Кинетика и катализ, 2023, T. 64, № 1, стр. 22-30
Новые молибденсодержащие мезопористые катализаторы для быстрого окисления серосодержащих субстратов
О. О. Гуль a, *, П. Д. Поликарпова a, **, А. В. Акопян a, А. В. Анисимов a
a Московский государственный университет им. М.В. Ломоносова, кафедра химии нефти и органического катализа, химический факультет
119991 Москва, ГСП-1, Ленинские горы, 1-3, Россия
* E-mail: lesi00gul@gmail.com
** E-mail: polikarpova@petrol.chem.msu.ru
Поступила в редакцию 17.06.2022
После доработки 05.09.2022
Принята к публикации 26.09.2022
- EDN: KGESVN
- DOI: 10.31857/S0453881123010021
Аннотация
Впервые показана возможность использования молибденсодержащих катализаторов на основе SBA-15, синтезированных в одну стадию методом совместной конденсации, в процессе окисления различных сероорганических соединений. Состав и структура полученных материалов подтверждены набором современных физико-химических методов, таких как низкотемпературная адсорбция/десорбция азота, рентгеноспектральный флуоресцентный анализ, рентгенофазовый анализ, ПЭМ, ИК-спектроскопия. Исследовано влияние количества активной фазы и условий проведения процесса на окисление модельной смеси дибензотиофена. Показано, что полученный катализатор работает как минимум в течение 4 циклов без значительной потери активности. Образец, содержащий 5 мас. % молибдена, позволяет достичь 100%-ной конверсии дибензотиофена за 5 мин в следующих условиях: 0.5 мас. % катализатора 5%Mo-SBA-15, мольное соотношение H2O2 : S = 6 : 1, T = 80°C.
ВВЕДЕНИЕ
В настоящее время поиск новых эффективных методов очистки топлив от серы представляет собой актуальную задачу в связи с тем, что сернистые соединения, такие как сероводород, меркаптаны, тиоэфиры, дисульфиды, дибензотиофены и их производные, являются источниками загрязнения экосистем, а также оказывают значительное влияние на здоровье человека [1–3]. Окислительное обессеривание – один из альтернативных гидроочистке методов удаления сернистых соединений из различных нефтяных фракций, который позволяет в мягких условиях при атмосферном давлении и температуре не выше 120°C в присутствии окислителя удалять гетероароматические соединения серы, превращая их в соответствующие сульфоксиды и сульфоны без разрушения связь углерод–сера [4]. Так как в процессе окислительного обессеривания неполярные серосодержащие соединения превращаются в полярные, они могут быть легко извлечены из смеси углеводородов методами экстракции или адсорбции [5]. Наибольшее распространение в качестве окислителей получили пероксид водорода [2], кислород [6], озон [7], органические пероксиды [8]. Пероксид водорода представляет широкий интерес для исследователей, так как единственный побочный продукт, образующийся в ходе реакции окисления – вода [9], при этом окисление пероксидом водорода протекает уже при 20–80°С в отличие от кислорода, в присутствии которого необходимо нагревать реакционную смесь выше 130°С.
В литературе описано применение как гомогенных [10], так и гетерогенных [11] катализаторов пероксидного окислительного обессеривания, однако использование гомогенных систем вызывает трудности в связи со сложностями регенерации каталитической системы и отделения ее от реакционной смеси.
Как гетерогенные катализаторы окислительного обессеривания, хорошо изучены оксиды переходных металлов, таких как молибден [12], вольфрам [13] и ванадий [14]. В присутствии окислителя оксиды образуют активные пероксокомплексы, которые за счет нуклеофильной атаки атома серы окисляют серосодержащий субстрат до соответствующего сульфона [15]. Применение чистых оксидов металлов в качестве катализаторов окисления сернистых соединений имеет свои недостатки: низкие значения площади поверхности оксидов, что ведет к длительному времени проведения процесса; агрегация частиц в присутствии пероксида водорода [16], приводящая к уменьшению количества доступных активных центров; высокий расход оксида металла. В связи с этим оксиды металлов необходимо диспергировать по поверхности носителя.
В литературных источниках описано использование мезопористых материалов [17], цеолитов [18], пористых ароматических каркасов (PAF) [19], оксидов переходных металлов, таких как молибден, вольфрам, ванадий [20], углеродных материалов [21], металлоорганических каркасов (MOF) [22], силикоалюмофосфатов (SAPO) [23], модифицированного медицинского камня (MMS) [24] в роли носителей для катализаторов окислительного обессеривания. Известно, что микропористая структура цеолитов препятствует транспорту объемных ароматических сероорганических соединений в реакциях окислительного обессеривания, что ограничивает их применение в процессах удаления сернистых соединений [25]. Таким образом, популярность приобретают мезопористые носители, такие как HMS [26], SBA-15 [27], MCM-41 [28], а также кубический мезопористый KIT-6 [29], имеющие диаметр пор, соответствующий размеру молекул сероорганических соединений.
Ранее нами было показано, что SBA-15 может быть эффективным носителем для катализаторов окислительного обессеривания [30]. Однако нанесение оксида молибдена методом пропитки требует дополнительной стадии синтеза, что повышает стоимость катализатора.
Известно, что молибденсодержащий катализатор на основе SBA-15 можно получить в одну стадию методом соконденсации [31]. В настоящей работе, посвященной окислительному обессериванию модельных смесей серосодержащих соединений, были синтезированы и исследованы молибденсодержащие катализаторы на основе SBA-15, приготовленные вышеуказанным методом. Синтезированный катализатор обеспечивает высокую скорость окисления сероорганических соединений, таких как ДБТ и его производные. В присутствии 5%Mo-SBA-15 требуется всего 5 мин (условия окисления: 0.5 мас. % катализатора, мольное отношение H2O2 : S = 6 : 1, T = 80°С) для достижения полной конверсии модельной смеси на основе ДБТ с использованием в качестве окислителя пероксида водорода.
ЭКСПЕРИМЕНТАЛЬНАЯ ЧАСТЬ
Для синтеза мезопористого носителя SBA-15 и молибденсодержащих катализаторов применяли следующие реагенты: тетраэтоксисилан (ТЭОС, 98%, “Sigma-Aldrich”), симметричный триблок-сополимер Pluronic Р123, (EO20PO70EO20, “Sigma-Aldrich”), соляная кислота (HCl, 37%, “Сигма-Тэк”), гептамолибдат аммония ((NH4)6[Mo7O24]·4H2O, 99%, “Sigma-Aldrich”). В качестве окислителя был использован пероксид водорода (H2O2, 50%, “Prime-Chemicals-Group”).
Модельные смеси состояли из метилфенилсульфида (MeSPh, 98%, “Sigma-Aldrich”), дибензотиофена (ДБТ, 98%, “Sigma-Aldrich”), бензотиофена (БТ, “Sigma-Aldrich”), 4-метилдибензотиофена (МеДБТ, 96%, “Sigma-Aldrich”), 4,6-диметилдибензотиофен (Ме2ДБТ), растворенных в додекане (99%, “Sigma-Aldrich”). Содержание серы в модельных смесях – 500 ppm.
Синтез мезопористых носителей и катализаторов
Синтез SBA-15 проводили по стандартной методике, описанной в работе [30].
Синтез катализатора 5%Mo/SBA-15 методом пропитки. Нанесение оксида молибдена на SBA-15 осуществляли методом пропитки по влагоемкости. При перемешивании к раствору гептамолибдата аммония (0.04632 г) добавляли 1 г носителя. Смесь перемешивали на роторном испарителе в течение 2 ч при 60°С, затем сушили при температуре 80–110°С в течение 16 ч. Образец переносили в муфельную печь и прокаливали при 550°С в течение 5 ч при скорости нагрева 5°С/мин.
Синтез катализатора Х%Mo-SBA-15 методом соконденсации. Mo-SBA-15 был синтезирован аналогично методике, представленной в [31]. 3 г Pluronic-123 было растворено в 100 г дистиллированной воды, содержащей 6.1 г 35 мас. % HCl, при температуре 40°C и постоянном перемешивании в течении 1 ч. Затем к приготовленному раствору добавляли 0.1081–0.4908 г водного раствора гептамолибдата аммония (NH4)6[Mo7O24]·4H2O. Полученный раствор перемешивали 3 ч. Затем в реакционную смесь прикапывали 8.5 г ТЭОС. После перемешивания при 40°C в течение 24 ч смесь переносили в автоклав и выдерживали при 100°C в течение 24 ч. На этом этапе окраска раствора изменялась с желтого на голубой, что указывает на частичное восстановление молибдена. Полученный осадок промывали, фильтровали, сушили в температурном интервале 80–110°С в течение 16 ч и прокаливали в муфельной печи при 550°C в течение 5 ч при скорости нагрева 5°С/мин.
Аналитическое оборудование
Содержание молибдена в синтезированных образцах определяли методом рентгеноспектрального флуоресцентного анализа (РСФА) на рентгеновском флуоресцентном волновом спектрометр ARL PERFORM’X (“Thermo Fisher Scientific”, New Wave, США).
ИК-спектры полученных образцов регистрировали на ИК-Фурье спектрометре Nicolet IR200 (“Thermo Scientific”, США) в диапазоне частот 4000–500 см–1 методом нарушенного полного внутреннего отражения (НПВО) при использовании кристалла ZnSe.
Исследование пористой структуры катализаторов проводили на анализаторе Gemini VII 2390 (V1.02 t) (“Micromeritics”, США) при 77 К. В течение 12 ч образцы дегазировали при температуре 350°C и давлении 3 × 10–3 атм. По модели БЭT (Брунауэра–Эммета–Теллера) при относительном парциальном давлении P/P0 = 0.2 была определена удельная поверхность образцов. Общий объем пор был рассчитан по модели BJH (Баррет–Джойнер–Халенда) при относительном давлении P/P0 = 0.95.
Просвечивающую электронную микроскопию (ПЭМ) выполняли на микроскопе JEM-2100 (“JEOL”, Япония) с напряжением электронной трубки 200 кВ.
Рентгенофазовый анализ осуществляли на рентгеновском дифрактометре: рентгеновский источник Rotaflex RU-200, широкоугольный гониометр D/MAX-B (“Rigaku”, Япония). Режим работы источника – 50 кВ 100 мА, съемку вели в геометрии Брэгга–Брентано в режиме непрерывного θ–2θ сканирования в угловом диапазоне 0.5°–5° по 2θ с шагом 0.04° и скоростью 2°/мин.
Методика окисления модельных смесей
Активность синтезированных катализаторов была исследована в процессе окислительного обессеривания модельных смесей различного состава в стеклянных реакторах при атмосферном давлении в интервале температур от 40 до 80°C в течение 5–30 мин. В качестве модельных смесей были использованы растворы сероорганических соединений, таких как метилфенилсульфид, бензотиофен, дибензотиофен, 4-метилдибензотиофен и 4,6-диметилдибензотиофен в додекане. К 5 мл модельной смеси добавляли 0.0094–0.0375 г (0.25–1 мас. % от массы реакционной смеси) катализатора и 0.007–0.02 мл 50%-ного раствора пероксида водорода, полученную смесь перемешивали со скоростью 700 об/мин. После окисления модельную смесь отделяли от окислительно-каталитической смеси декантированием и анализировали продукты реакции методом газовой хроматографии на приборе Кристалл-2000М (“Хроматэк”, Россия; пламенно-ионизационный детектор; колонка Zebron; L = 30 м; d = 0.32 мм; жидкая фаза ZB-1) при программировании температуры от 150 до 250°C (газ-носитель – азот). Хроматограммы записывали и анализировали с помощью программы Chromatech Analytic 1.5.
Реакции окисления с целью получения достоверного результата проводили по три раза. Погрешность эксперимента не превышала 5%.
РЕЗУЛЬТАТЫ И ИХ ОБСУЖДЕНИЕ
Физико-химические характеристики
Для сравнения влияния способа синтеза молибденсодержащих катализаторов на их активность в окислительном обессеривании в настоящей работе было использовано два способа нанесения оксида молибдена на SBA-15 – традиционным методом пропитки (обозначен в работе 5%Mo/SBA-15) и путем соконденсации на стадии синтеза мезопористого носителя (обозначены в работе Х%Mo-SBA-15, где Х – массовое содержание молибдена).
Пористая структура синтезированных молибденсодержащих катализаторов на основе SBA-15 была охарактеризована методом низкотемпературной адсорбции/десорбции азота. Из полученных данных (рис. 1) видно, что нанесение оксида молибдена методом пропитки не ведет к существенным изменениям структуры катализатора. Изотерма N2 синтезированных носителей и катализаторов в области между 0.4 и 0.8 отражает стадию капиллярной конденсации, характерную для мезопористых структур. В случае катализаторов, приготовленных соконденсацией, при увеличении содержания молибдена в структуре изменяется форма и ширина петли гистерезиса, что, по-видимому, является следствием незначительного искажения структуры катализатора.
Удельная площадь поверхности катализатора, полученного методом пропитки, уменьшается по сравнению с чистым носителем SBA-15 (табл. 1), так как в этом случае поверхность мезопористого носителя экранируется оксидом молибдена. При нанесении 2.2 и 5 мас. % металла в виде оксида методом соконденсации получаются сравнимые площади поверхности катализатора и чистого носителя SBA-15. Такой подход к синтезу катализатора позволяет сохранить высокую площадь поверхности, что в свою очередь также способствует повышению эффективности диффузии субстрата и окислителя к активным центрам катализатора. При повышении количества молибдена до 10 мас. % площадь поверхности 10%Mo-SBA-15 уменьшается и достигает 483 м2/г, что может быть связано с забивкой пор оксидом молибдена [31].
Таблица 1.
Экспериментальные параметры носителя и синтезированных катализаторов
Образец | Содержание металла, мас. % | Sуд, м2/г |
Vпор, см3/г |
Dпор, Å |
---|---|---|---|---|
SBA-15 | 0 | 682 | 0.68 | 48 |
5%Mo/SBA-15 | 4.91 | 643 | 0.65 | 43 |
2.2%Mo-SBA-15 | 2.18 | 737 | 0.71 | 50 |
5%Mo-SBA-15 | 4.85 | 715 | 0.68 | 52 |
10%Mo-SBA-15 | 10.72 | 483 | 0.48 | 44 |
Молибденсодержащие катализаторы и носитель SBA-15 были исследованы методом НПВО ИК-Фурье спектроскопии (рис. 2а). Интенсивность полосы поглощения, отвечающей за связь Si–O–H (1200 см–1), уменьшается в присутствии молибдена, что свидетельствует об экранировании поверхности носителя оксидом молибдена. Полосы поглощения, обнаруженные в областях 1050 и 805 см–1, соответствуют симметричным и асимметричным колебаниям Si–O–Si [32]. Органический темплат, используемый в синтезе, был полностью удален, что подтверждается отсутствием пиков в ИК-спектрах при 3000 см–1 [33].
Рис. 2.
ИК-Фурье спектры катализаторов на основе SBA-15 (а), РФА-спектры катализаторов SBA-15 и 5%Mo-SBA-15 (б).
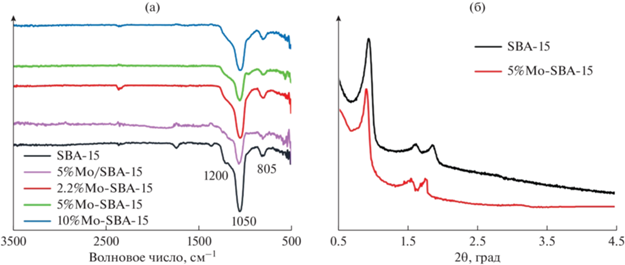
Метод РФА применяли для подтверждения отсутствия отдельной фазы оксида молибдена (VI) в структуре катализатора. На дифрактограмме РФА на низких углах (рис. 2б) присутствует сильный характерный дифракционный пик около 1.5°, который связан с типом симметрии P6mm гексагональной решетки пор в SBA-15 [34]. Сравнение дифрактограммы чистого SBA-15 и модифицированного образца подтверждает, что SBA-15 был функционализирован без деформирования.
Катализаторы 5%Mo/SBA-15 и 5%Mo-SBA-15 были также исследованы методом ПЭМ (рис. 3). Полученные микрофотографии свидетельствуют о сохранении у образцов высокоупорядоченной мезопористой структуры и сети параллельных каналов.
Окисление модельных смесей
Синтезированные катализаторы исследовали в процессе окисления модельной смеси, представляющей собой раствор ДБТ в додекане, с содержанием серы 500 ppm. В результате окисления ДБТ превращается в соответствующий сульфон (схема 1 ). В работе образование одного продукта реакции – сульфона – подтверждено методом газовой хроматографии.
Схема 1 . Схема окисления ДБТ.
Сравнение каталитических свойств синтезированных образцов (рис. 4а) показало, что катализаторы, полученные соконденсацией, активнее приготовленных методом пропитки. Наибольшая конверсия ДБТ зафиксирована в присутствии 5%Mo-SBA-15. Содержание молибдена 2.2 мас. % оказывается недостаточным для достижения конверсии ДБТ более 89% в выбранных условиях. При увеличении количества молибдена до 10 мас. % конверсия падает. Это может быть связано с тем, что в присутствии молибдена скорость разложения пероксида водорода растет, и, как следствие, скорость окисления ДБТ снижается.
Рис. 4.
Влияние метода синтеза катализаторов (а) и температуры и времени реакции (б) на конверсию ДБТ. Условия окисления: H2O2 : S = 6 : 1, T = 80°C, 0.5 мас. % катализатора, 10 мин (а); H2O2 : S = 6 : 1, 0.5 мас. % катализатора (б).
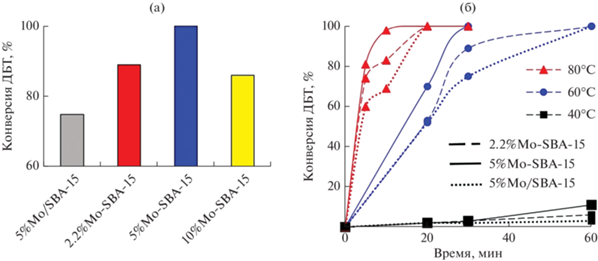
Из рис. 4б видно, что при повышении температуры от 40 до 60°С конверсия ДБТ резко увеличивается из-за возрастания скорости диффузии субстрата к активным центрам катализатора, что согласуется с литературными данными [35]. При 60°С за 30 мин катализаторы позволяют достичь 100%-ной конверсии ДБТ. При дальнейшем повышении температуры до 80°С реакция резко ускоряется, и за 10 мин в присутствии 0.5 мас. % катализатора 5%Mo-SBA-15 удается практически полностью окислить ДБТ. Важно отметить, что образец, полученный путем пропитки, проявляет меньшую активность по сравнению с теми, что были синтезированы методом соконденсации, независимо от температуры реакции.
На рис. 5а показано, как количество пероксида водорода влияет на конверсию ДБТ в присутствии катализаторов с различным содержанием активной фазы. Наибольшей степени окисления ДБТ возможно достичь за 20 мин при 6-ти кратном избытке окислителя. При большем добавлении пероксида водорода конверсия ДБТ снижается, поскольку при таком количестве воды, которое содержится в 50%-ном растворе пероксида водорода, гидрофильный катализатор начинает слипаться, что препятствует дальнейшему протеканию реакции [35]. В отсутствие пероксида водорода наблюдается небольшая конверсия ДБТ, связанная с сорбцией дибензотиофена в порах катализатора. Методом газовой хроматографии также подтверждено, что в данных условиях, когда окислитель отсутствует, окисления ДБТ до оксида или сульфона не происходит.
Рис. 5.
Влияние количества пероксида водорода (а) и катализатора 5%Mo-SBA-15 (б) на конверсию ДБТ. Условия окисления: T = 60°C, 0.5 мас. % катализатора, 20 мин (a); H2O2 : S = 6 : 1, T = 80°C, 5 мин (б).
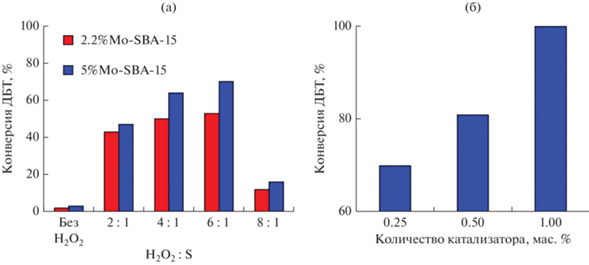
Уменьшение количества катализатора приводит к снижению конверсии (рис. 5б), что может быть связано с недостатком пероксокомплексов, образующихся в окислительно-каталитической системе в течение 5 мин. При увеличении содержания катализатора до 1 мас. % конверсия ДБТ достигает 100% уже за 5 мин реакции. Это дает возможность сделать вывод о получении эффективного катализатора окислительного обессеривания.
Активность катализаторов 2.2%Mo-SBA-15 и 5%Mo-SBA-15 изучена в процессе окисления модельных смесей, в состав которых входят сероорганические соединения различного строения: метилфенилсульфид (MeSPh), бензотиофен (БТ), дибензотиофен (ДБТ), 4-метилдибензотиофен (MeДБТ) и 4,6-диметилдибензотиофен (Me2ДБТ). Показано, что она падает в ряду MeSPh > ДБТ > MeДБТ > Me2ДБТ > БТ (рис. 6а). Самая низкая конверсия была достигнута при окислении бензотиофена, в молекуле которого электронная плотность на атоме серы наименьшая [36], что является решающим фактором в окислении.
Рис. 6.
Конверсия сероорганических соединений различного строения в присутствии катализаторов 2.2%Mo-SBA-15 и 5%Mo-SBA-15 (а); стабильность работы катализатора в реакции окисления ДБТ в течение нескольких циклов реакции–регенерации (б). Условия окисления: H2O2 : S = 6 : 1 (а), T = 80°C, 1 мас. % катализатора, 5 мин (а); H2O2 : S = = 6 : 1, T = 80°C, 0.5 мас. % катализатора, 5 мин (б).
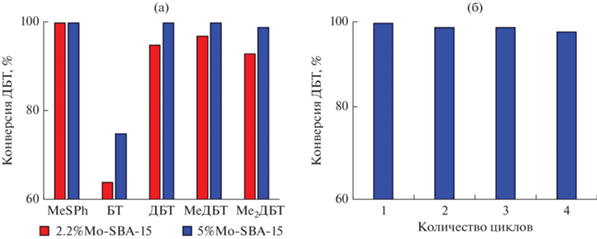
Известно, что сульфоны, образующиеся в процессе окисления, могут сорбироваться в порах катализатора [37]. С целью предотвращения дезактивации сульфонами катализатор 5%Mo-SBA-15 регенерировали путем отделения от реакционной смеси с последующим отжигом при 550°С для удаления сульфонов. В течение 4 циклов активность катализатора оставалась практически неизменной (рис. 6б).
В табл. 2 приведены сравнительные данные об активности различных катализаторов, содержащих оксид молибдена, в окислительном обессеривании. Основным преимуществом катализатора, синтезированного в настоящей работе, является высокая скорость реакции в его присутствии. Уже за 5 мин окисления удается добиться 100%-ной конверсии ДБТ. Кроме того, его приготовление происходит в отсутствие стадии нанесения оксида металла на носитель, поскольку оксид молибдена вносится напрямую методом соконденсации в процессе синтеза SBA-15, что позволяет получать катализатор в одну стадию.
Таблица 2.
Сравнение активности катализаторов в окислительном обессеривании модельной смеси на основе ДБТ
Катализатор | Окислитель | [O]/S (мольн.) | T, °C | mкат (г)/Vмод.см.(мл) | t, мин | Конверсия, % | Ссылки |
---|---|---|---|---|---|---|---|
Mo/MCM-41 | H2O2 | 10 : 1 | 60 | 0.008 | 120 | 100 | [20] |
Mo/SAPO-11 | H2O2 | 10 : 1 | 60 | 0.003 | 240 | >99 | [23] |
Mo/MMS | CYHPOа | 3 : 1 | 103 | 0.025 | 62 | 98 | [24] |
Mo/SBA-15 | H2O2 | 6 : 1 | 60 | 0.008 | 30 | 100 | [30] |
MoO2/g-C3N4-550 | TBHPб | 3 : 1 | 80 | 0.007 | 60 | 100 | [38] |
Mo-SBA-15 | H2O2 | 6 : 1 | 80 | 0.008 | 5 | 100 | Настоящая работа |
ЗАКЛЮЧЕНИЕ
В настоящей работе впервые в окислении сернистых соединений были использованы молибденсодержащие катализаторы на основе SBA-15, полученные путем одностадийного синтеза методом соконденсации. Методом низкотемпературной адсорбции/десорбции азота доказано, что молибденсодержащие катализаторы, синтезированные путем совместной конденсации, не уступают по своим текстурным характеристикам материалам на основе SBA-15, приготовленным традиционным способом. Изучено влияние на конверсию дибензотиофена в реакции его окисления таких параметров, как способ получения катализатора, температура и время реакции, количество окислителя и катализатора. Выбраны оптимальные условия для полного превращения ДБТ в сульфон в присутствии синтезированного катализатора 5%Mo-SBA-15: 5 мин, 0.018 г катализатора (0.5 мас. %), мольное соотношение H2O2 : S = 6 : 1, 80°С. Показано, что наиболее активный катализатор 5%Mo-SBA-15 работает как минимум в течение 4 циклов без значительной потери активности.
Список литературы
Liu W., Jiang W., Zhu W., Zhu W., L, H., Guo T. // J. Mol. Catal. A: Chem. 2016. V. 424. P. 261.
Ahmed G.S., Jarullah A.T., Al-tabbakh B.A. // J. Clean. Prod. 2020. V. 257. P. 120436.
Bhutto A.W., Abro R., Gao S., Abbas T., Chen X., Y., G.J. // Taiw. Inst. Chem. Eng. 2016. V. 62. P. 84.
Mjalli F.S., Ahmed O.U., Al-Wahaibi T., Al-Wahaibi Y., AlNashef I.M. // Rev. Chem. Eng. 2014. V. 30. № 4. P. 337.
Li X., Zhang J., Zhou F., Wang Y., Yuan X., Wang H. // Mol. Catal. 2018. V. 452. P. 93.
Gao Y., Gao R., Zhang G., Zheng Y., Zhao J. // Fuel. 2018. V. 224. P. 261.
Акопян А.В., Григорьев Д.А., Поликарпова П.Д., Есева Е.А., Литвинова В.В., Анисимов А.В. // Нефтехимия. 2017. Т. 57. № 5. С. 582.
Zhang Y., Li G., Kong L., Lu H. // Fuel. 2018. V. 219. P. 103.
Liu W., Li T., Yu G., Wang J., Zhou Z., Ren Z. // Fuel. 2020 V. 265. P. 116967.
Ding J., Zhang Y., Wang R. // New J. Chem. 2019. V. 43. № 19. P. 7363.
Брыжин А.А., Буряк А.К., Гантман М.Г., Зеликман В.М., Шилина М.И., Тарханова И.Г. // Кинетика и Катализ. 2020. Т. 61. № 5. С. 688.
Deng C., Wu P., Zhu L., He J., Tao D.J., Lu L., He M., Hua M., Li H., Zhu W. // Appl. Mater. Today. 2020. V. 20. P. 100680.
Zhang M., Liao W., Wei Y., Wang C., Fu Y., Gao Y., Zhu L., Zhu W., Li H. // ACS Appl. Nano Mater. 2021. V. 4. № 2. P. 1085.
Piscopo C.G., Granadeiro C.M., Balula S.S., Bošković D. // ChemCatChem. 2020. V. 12. № 19. P. 4721.
Rivoira L., Martínez M.L., Anunziata O., Beltramone A. // Micropor. Mesopor. Mater. 2017. V. 254. P. 96.
Wang C., Chen Z., Yao X., Jiang W., Zhang M., Li H., Liu H., Zhu W., Li H. // RSC Adv. 2017. V. 7. № 62. P. 39 383.
Shen D., Dai Y., Han J., Gan L., Liu J., Long M. // Chem. Eng. J. 2018. V. 332. P. 563.
Du Q., Guo Y., Wu P., Liu H., Chen Y. // Micropor. Mesopor. Mater. 2019. V. 275. P. 61.
Kulikov L.A., Akopyan A.V., Polikarpova P.D., Zolotukhina A.V., Maximov A.L., Anisimov A.V., Karakhanov E.A. // Ind. Eng. Chem. Res. 2019. V. 58. № 45. P. 20 562.
Polikarpova P., Akopyan A., Shigapova A., Glotov A., Anisimov A., Karakhanov E. // Energy Fuels. 2018. V. 32. № 10. P. 10898.
Dizaji A.K., Mokhtarani B., Mortaheb H.R. // Fuel. 2019. V. 236. P. 717.
Zhang X. min, Zhang Z., Zhang B., Yang X., Chang X., Zhou Z., Wang D.H., Zhang M.H., Bu X.H. // Appl. Catal. B: Env. 2019. V. 256. P. 117804.
Yang G., Zhang X., Yang H., Long Y., Ma J. // J. Colloid Interface Sci. 2018. V. 532. P. 92.
Qiu L., Cheng Y., Yang C., Zeng G., Long Z., Wei S., Zhao K., Luo L. // RSC Adv. 2016. V. 6. № 21. P. 17036.
Yang G., Han J., Liu Y., Qiu Z., Chen X. // Chin. J. Chem. Eng. 2020. V. 28. № 9. P. 2227.
Wang F., Xiao K., Shi L., Bing L., Han D., Wang G. // React. Chem. Eng. 2021. V. 6. № 2. P. 289.
Ribeiro S.O., Duarte B., de Castro B., Granadeiro C.M., Balula S.S. // Materials (Basel). 2018. V. 11. № 7. P. 1196.
Pham X.N., Pham T.D., Nguyen B.M., Tran H.T., Pham D.T. // J. Chem. 2018. V. 2018. P. 841860.
Wang B., Dai B., Kang L., Zhu M. // Fuel. 2020. V. 265. P. 117029.
Akopyan A., Polikarpova P., Gul O., Anisimov A., Karakhanov E. // Energy Fuels. 2020. V. 34. № 11. P. 14611.
Lin C., Tao K., Yu H., Hua D., Zhou S. // Catal. Sci. Technol. 2014. V. 4. № 11. P. 4010.
Melero J.A., Iglesias J., Arsuaga J.M., Sainz-pardo J. // Appl. Catal. A: Gen. 2007. V. 331. P. 84.
Anirudhan T.S., Varghese S., Manjusha V. // Int. J. Biol. Macromol. 2021. V. 192. P. 950.
Eseva E.A., Lukashov M.O., Cherednichenko K.A., Levin I.S., Akopyan A.V. // Ind. Eng. Chem. Res. 2021. V. 60. № 39. P. 14154.
Akopyan A.V., Polikarpova P.D., Arzyaeva N.V., Anisimov A.V., Maslova O.V., Senko O.V., Efremenko E.N. // ACS Omega. 2021. V. 6. № 41. P. 26932.
Houda S., Lancelot C., Blanchard P., Poinel L., Lamonier C. // Catalysts. 2018. V. 8. № 9. P. 344.
Estephane G., Lancelot C., Blanchard P., Toufaily J., Hamiye T., Lamonier C. // RSC Adv. 2018. V. 8. № 25. P. 13714.
Chen K., Zhang X.M., Yang X.F., Jiao M.G., Zhou Z., Zhang M.H., Wang D.H., Bu X.H. // Appl. Catal. B: Env. 2018. V. 238. P. 263.
Дополнительные материалы отсутствуют.
Инструменты
Кинетика и катализ