Кинетика и катализ, 2023, T. 64, № 1, стр. 109-118
Синтез и исследование каталитических свойств структурированного Rh-содержащего катализатора конверсии дизельного топлива в синтез-газ
В. А. Шилов a, b, *, В. Н. Рогожников a, Д. И. Потемкин a, b, П. В. Снытников a
a ФГБУН Институт катализа им. Г.К. Борескова СО РАН
630090 Новосибирск, просп. Акад. Лаврентьева, 5, Россия
b ФГАОУ ВО Новосибирский национальный исследовательский государственный университет
630090 Новосибирск, ул. Пирогова, 2, Россия
* E-mail: sva@catalysis.ru
Поступила в редакцию 26.08.2022
После доработки 03.10.2022
Принята к публикации 04.10.2022
- EDN: KIURFI
- DOI: 10.31857/S0453881123010070
Аннотация
В представленной работе была усовершенствована методика нанесения активного оксида Ce0.75Zr0.25O2 – δ на структурированную подложку из сплава FeCrAl. Суть метода заключается в соосаждении оксидов церия и циркония на фехралевую сетку из водного раствора их нитратов Ce(NO3)3·6H2O и ZrO2(NO3)2·7–8H2O при гомогенном гидролизе аммиаком. Методом рентгенофазового анализа было показано, что в образце катализатора, полученного соосаждением, образуется больше фазы церий-циркониевого оксида, к тому же ее дисперсность выше, чем при нанесении методом пропитки по влагоемкости. Данный метод способствует формированию покрытия с большей удельной поверхностью. Разработанный катализатор обладает высокой активностью в условиях автотермической конверсии дизельного топлива. В ходе ресурсных испытаний в течение 200 ч было выявлено, что зауглероживание катализатора со скоростью 8.6 мгсажи${\text{г}}_{{{\text{кат}}}}^{{ - 1}}$ ч–1, а также накопление серы не сказываются на удельной производительности катализатора по синтез газу, которая составила ~8 м3${\text{л}}_{{{\text{кат}}}}^{{ - 1}}$ ч–1.
ВВЕДЕНИЕ
Для перехода к экологически чистой и ресурсосберегающей энергетике разрабатываются альтернативные системы преобразования энергии, в основе которых заложены процессы получения и использования водорода, который выступает в роли энергоносителя. Перспективными устройствами для выработки электроэнергии являются электрохимические генераторы на топливных элементах, которые по своим техническим и эксплуатационным характеристикам превосходят коммерчески доступные энергоустановки на основе двигателей внутреннего сгорания. Одной из основных проблем, сдерживающих внедрение электрохимических генераторов в повседневную жизнь, пока остается их стоимость и доступность водорода из-за слаборазвитой инфраструктуры [1–3]. Для решения этой проблемы предлагается на начальном, “переходном” этапе задействовать привычное для потребителей углеводородное топливо, например, дизельное, инфраструктура которого широко развита и отлажена логистика, в том числе и в труднодоступных районах Российской Федерации. В этом случае энергоустановку необходимо оснастить дополнительным устройством – топливным процессором, позволяющим конвертировать дизельное топливо в пригодный для питания топливных элементов водородсодержащий газ.
Большое число проводимых исследований (лабораторных экспериментов, испытаний макетов и опытных образцов) направленно на разработку катализатора конверсии коммерческих марок дизельного топлива [4–25]. Основные трудности связаны с многокомпонентностью, а также наличием в дизеле, полученном из нефтяного сырья, серосодержащих соединений, являющихся даже в небольших количествах каталитическим ядом. Присутствие ди- и полиароматических соединений, конверсия которых вызывает наибольшие затруднения [8, 16, 19], приводит к зауглероживанию катализатора и его дезактивации. Деградационные процессы также возникают из-за спекания активного компонента в условиях довольно высоких реакционных температур (750–1000°С). Все эти факторы усложняют создание эффективного катализатора и, соответственно, топливного процессора.
Конверсию дизельного топлива в синтез-газ можно осуществить тремя способами: парциальным окислением (I), паровым (II) и автотермическим риформингом (III), из которых последний является наиболее предпочтительным:
(I)
${{{\text{C}}}_{n}}{{{\text{H}}}_{m}} + \frac{n}{2}{{{\text{O}}}_{2}} \to n{\text{CO}} + \frac{m}{2}{{{\text{H}}}_{2}},\,\,\,\,\Delta H < 0;$(II)
${{{\text{C}}}_{n}}{{{\text{H}}}_{m}} + n{{{\text{H}}}_{{\text{2}}}}{\text{O}} \to n{\text{CO}} + \left[ {\frac{m}{2} + n} \right]{{{\text{H}}}_{2}},\,\,\,\,\Delta H > 0;$(III)
$\begin{gathered} {{{\text{C}}}_{n}}{{{\text{H}}}_{m}} + \frac{n}{4}{{{\text{O}}}_{2}} + \frac{n}{2}{{{\text{H}}}_{{\text{2}}}}{\text{O}} \to \\ \to n{\text{CO}} + \left[ {\frac{m}{2} + \frac{n}{2}} \right]{{{\text{H}}}_{2}},\,\,\,\,\Delta H \leqslant 0. \\ \end{gathered} $В условиях реакции автотермического риформинга дизеля должна обеспечиваться высокая теплопроводность слоя катализатора для передачи тепла из лобовой зоны (где преимущественно протекают процессы полного окисления с экзотермическим эффектом), в хвостовую зону (где превалируют эндотермические реакции паро- и углекислотной конверсии углеводородов). Исследования показывают, что недостаток тепла в хвостовой зоне катализатора играет ключевую роль в снижении конверсии топлива [17].
Решением этой проблемы может стать использование в качестве подложки структурированного носителя с высокой теплопроводностью, например, из жаропрочного фехралевого сплава [17, 18, 25]. Однако, поскольку коэффициент термического расширения (КТР) высокотемпературных металлических сплавов вдвое превышает КТР оксидных покрытий, при нагреве зачастую наблюдается их растрескивание и разрушение, что решается путем нанесения игольчатого покрытия вместо сплошного каталитического слоя [25, 26]. Такое покрытие является “гибким” – отдельные элементы оксидного слоя способны смещаться относительно друг друга при нагреве/охлаждении и расширении/сжатии металлической подложки, что предотвращает деградацию каталитического слоя.
Целью настоящей работы была разработка модифицированного метода синтеза структурированного Rh-содержащего катализатора конверсии дизельного топлива в синтез-газ. Была усовершенствована методика нанесения активного оксида Ce0.75Zr0.25O2 – δ на структурированную подложку. Представлены результаты исследований катализатора различными физико-химическими методами и изучены его каталитические свойства, включая ресурсные испытания при работе на коммерческом дизельном топливе.
ЭКСПЕРИМЕНТАЛЬНАЯ ЧАСТЬ
Приготовление катализатора и его физико-химические характеристики
В качестве носителя использовали металлическую сетку из нержавеющей фехралевой стали (марка стали – “Х23Ю5Т”, размер ячейки – 0.5 мм, диаметр проволоки – 0.25 мм, ЗАО “НПО Союзнихром”, Россия). Сталь содержала, вес. %: Cr – 22.15, Al – 5.1, сумма C, Ni, S, P, Ti, Mn, Si – 1.0, остальное – Fe. В экспериментах применяли блоки сотового типа, состоящие из гофрированных и плоских сеток, скрученных в спираль Архимеда. Для увеличения адгезии и площади поверхности на металлическую сетку (далее обозначена как FeCrAl) наносили слой ϴ-Al2O3 по модифицированной методике Байера, описанной в [25].
Использованный ранее способ нанесения слоя активного оксида Ce0.75Zr0.25O2 – δ на поверхность блока заключался в смачивании поверхности подложки раствором нитратов церия и циркония с последующими сушкой, разложением нитратов металлов до их оксидов при 700–800°С и прокаливанием конечного образца при 800°С на воздухе [17–19]. Покрытие ϴ-Al2O3 было пропитано насыщенным раствором Се(NO3)3·6Н2О и ZrO(NO3)2·2Н2O (мольное соотношение Ce/Zr = 3) в течение 7 последовательных стадий с промежуточной термической обработкой при 800°С в течение 5 мин и окончательным прокаливанием при той же температуре в течение 30 мин. Таким образом был получен структурированный носитель Ce0.75Zr0.25O2 – δ–ϴ-Al2O3/FeCrAl, обозначенный далее, как CZ/FCA.
Усовершенствованная методика нанесения активного оксида Ce0.75Zr0.25O2 – δ на структурированную подложку заключалась в соосаждении на поверхность структурированного блока оксидов церия и циркония из водного раствора их нитратов Ce(NO3)3·6H2O и ZrO2(NO3)2·7–8H2O при гомогенном гидролизе аммиаком. Для этого структурированный блок с нанесенным защитным слоем оксида алюминия пропитывали водным раствором нитратов церия и цирконила с концентрациями 0.75 и 0.25 М, далее избыток раствора отделяли с помощью центрифуги, блок помещали в водный раствор аммиака с весовым содержанием 12.5 вес. % на 2 мин, после чего высушивали в сушильном шкафу при 80°C для удаления избыточной воды в течение 5 мин. Эти операции по пропитке и осаждению повторяли в общей сложности 7–8 раз до привеса в 7 вес. %. При последней пропитке блок оставляли в растворе осадителя для дальнейшего старения в течение 24 ч. Далее образец промывали дистиллированной водой до нейтрального pH, сушили при 80°C и прокаливали при 800°C в течение 1 ч. Таким образом был получен модифицированный структурированный носитель Ce0.75Zr0.25O2 – δ–ϴ-Al2O3/FeCrAl, обозначенный далее, как CZ/FCA-mod.
Нанесение активного компонента осуществляли методом сорбционно-гидролитического осаждения [24, 27]. Раствор RhCl3 смешивали с Na2CO3 в соотношении Na : Cl = 1. При комнатной температуре приготовленный раствор является метастабильным по отношению к гомогенному осаждению гидроксида родия. Затем смесь приводили в контакт со структурированными подложками CZ/FCA и CZ/FCA-mod при Т = = 75°C. Добавление структурированного носителя в смесь реагентов инициировало гидролиз, который приводил к равномерному осаждению частиц родия на поверхности носителя. Количественное протекание реакции осаждения родия проверяли по реакции фильтрата с NaBH4 (наличие ионов родия в растворе дает серое опалесцирующее окрашивание пробы вследствие образования золя металла). После окончания процедуры осаждения (т.е. когда реакция раствора с NaBH4 не наблюдалась) блоки промывали горячей водой путем декантации, высушивали на воздухе и восстанавливали в смеси 10 об. % H2 в N2 при 250°С в течение 30 мин. На рис. 1 представлена схема синтеза каталитических блоков.
Полученные катализаторы были охарактеризованы методами просвечивающей электронной микроскопии высокого разрешения (ПЭМ-ВР), сканирующей электронной микроскопии (СЭМ), совмещенной с энергодисперсионным рентгеновским анализом, рентгенофазового анализа (РФА), температурно-программированного окисления (ТПО). В табл. 1 представлены размеры приготовленных каталитических блоков и их состав.
Таблица 1.
Размеры и состав катализаторов
Катализатор | Диаметр, мм | Длина, мм | Масса катализатора, г | Состав, вес. % | |||
---|---|---|---|---|---|---|---|
Rh | Ce0.75Zr0.25O2 – δ | Ѳ-Al2O3 | FeCrAl | ||||
Rh/CZ/FCA | 17 | 50 | 10.83 | 0.24 | 6.4 | 3.6 | Остальное |
Rh/CZ/FCA-mod | 17 | 50 | 10.80 | 0.24 | 6.5 | 3.8 | Остальное |
Удельную поверхность образцов (Sуд) определяли методом БЭТ по низкотемпературной адсорбции азота на анализаторе ASAP 2400 (“Mic-romeritics”, США). Удельную поверхность измеряли непосредственно на сетке FeCrAl с нанесенным каталитическим слоем.
Рентгенограммы образцов на сетке были получены с использованием CuKα-излучения (λ = = 1.5418 Å). Измерения проводили на приборе Thermo ARL X’tra (“Thermo Fisher Scientific”, США) с геометрией фокусировки θ–θ в сканирующем режиме в диапазоне углов 2θ = 5°–75° с шагом 0.05°.
Морфологию поверхности и микроструктуру образцов изучали с помощью просвечивающей электронной микроскопии высокого разрешения и сканирующей просвечивающей электронной микроскопии. Исследования осуществляли с применением электронного микроскопа Themis Z (“Thermo Fisher Scientific”, США).
Для количественного определения скорости образования углерода в ходе каталитических экспериментов использовали метод ТПО. Для этого каталитические блоки после проведения реакции помещали в кварцевый проточный реактор и подавали смесь 8 об. % O2 в Ar со скоростью 100 см3 мин–1. Температуру линейно повышали от 30 до 800°С со скоростью 10°С мин–1. Количество углерода на поверхности катализатора определяли по концентрации CO2, которую отслеживали в режиме реального времени с помощью масс-спектрометра QMC-200 (“Stanford Research Systems”, США).
Каталитические эксперименты
Автотермический риформинг модельной смеси, состоящей из 75 вес. % н-гексадекана, 20 вес. % о-ксилола и 5 вес. % 1-метилнафталина (99.5%, ООО “Компонент-Реактив”, Россия), и дизельного топлива зимней марки (“Газпромнефть”, Россия), соответствующего стандарту EN 590, проводили в проточном реакторе с неподвижным слоем катализатора при температуре печи 750°С и атмосферном давлении. Условия экспериментов приведены в табл. 2. Конверсию топлива (Х) определяли гравиметрически каждый час по следующему уравнению:
где t – время сбора пробы, ч; V – массовый расход топлива на входе в реактор, г ч–1; m – масса непрореагировавшего топлива, г.Таблица 2.
Условия каталитических экспериментов на катализаторах Rh/CZ/FCA и Rh/CZ/FCA-mod
Катализатор | Тип топлива | Подача реагентов | Н2О/С | O2/C | GHSV, ч–1 | Т, °С |
||
---|---|---|---|---|---|---|---|---|
топливо, г/ч | Н2О, г/ч | воздух, л/ч | ||||||
Rh/CZ/FCA | 75 вес. % гексадекан + + 20 вес. % о-ксилол + + 5 вес. % 1-метил-нафталин | 28.9 | 99 | 120 | 2.65 | 0.5 | 20 300 | 750 |
Rh/CZ/FCA-mod | 28.9 | 99 | 144 | 2.65 | 0.6 | 22 200 | 750 | |
Зимнее дизельное топливо | 30 | 72 | 168 | 1.95 | 0.7 | 21 600 | 750 |
Во время ресурсных испытаний катализатор подвергали окислительной регенерации в потоке воздуха каждые 10 ч при 750°С в течение 30–60 мин.
Состав газа на выходе анализировали с помощью газового хроматографа ГХ-1000 (“Хромос”, Россия), оборудованного пламенно-ионизационным детектором (ПИД) с блоком метанатора и детектором по теплопроводности (ДТП). Перед анализом газовой смеси воду конденсировали. ДТП служил для нахождения концентраций Н2 и N2, разделенных в колонке CaA с газом-носителем Ar. Углеводороды СО, СО2, СН4 и С2–С5 разделяли в колонке Porapak Q и количественно определяли с использованием ПИД. Термодинамически равновесные составы для конверсии модельного бленда рассчитывали в программном пакете HSC Chemistry 7.0. Эти данные использовали для сравнения с экспериментальными результатами.
РЕЗУЛЬТАТЫ И ИХ ОБСУЖДЕНИЕ
Методом рентгенофазового анализа показано, что в образце Rh/CZ/FCA-mod, полученном соосаждением, образуется больше фазы смешанного церий-циркониевого оксида, чем в образце Rh/CZ/FCA, к тому же она более дисперсная (рис. 2). Это согласуется с результатами предыдущей работы [26], где было обнаружено, что носитель Ce0.75Zr0.25O2, приготовленный методом соосаждения в виде порошка, преимущественно состоит из высокодисперсной (DОКР = 5 нм) фазы смешанного оксида с кубической решеткой. Определить параметр элементарной ячейки с достаточной точностью после нанесения смешанного оксида на поверхность сетки не представлялось возможным.
Согласно результатам измерения физической адсорбции азота удельная поверхность катализатора Rh/CZ/FCA, полученного пропиткой по влагоемкости c последующим термическим разложением нитратов предшественников, составляла 1.3 м2/г, в то время как для Rh/CZ/FCA-mod она была 3.7 м2/г.
На микрофотографиях ПЭМ (рис. 3) видно, что частицы родия в образце Rh/CZ/FCA-mod имели средний диаметр менее 1 нм и находились в более дисперсном состоянии, чем в образце Rh/CZ/FCA.
Результаты испытаний обоих приготовленных катализаторов в автотермическом риформинге модельной смеси при разных соотношениях О2/С демонстрирует рис. 4, где представлены сравнительные распределения продуктов реакции после 3 ч в потоке. Стоит отметить, что во всех экспериментах наблюдали полную конверсию топлива (маслянистый остаток на выходе из реактора отсутствовал). Однако на катализаторе Rh/CZ/FCA-mod удавалось достигать большей производительности по синтез-газу, а содержание побочных продуктов конверсии, углеводородов С2–С4, было в несколько раз ниже, чем на Rh/CZ/FCA. Основным требованием к составу реформата перед подачей в твердооксидный топливный элемент (ТОТЭ) является минимальное содержание углеводородов с длиной цепи ≥2, поскольку их присутствие может способствовать образованию углерода на поверхности анода.
Рис. 4.
Сравнение активности катализаторов Rh/CZ/FCA и Rh/CZ/FCA-mod в автотермическом риформинге модельной смеси.
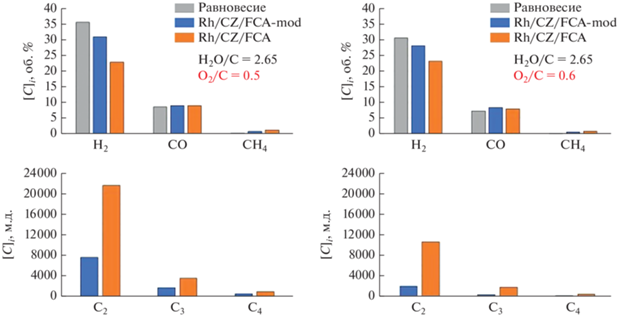
Таким образом, образец Rh/CZ/FCA-mod был выбран для дальнейших ресурсных испытаний на коммерческом дизельном топливе стандарта ЕВРО-5. В ходе реакции в лобовой части катализатора температура составляла 960°С, а в хвостовой части – 790°С. Конверсия топлива на протяжении 200 ч была близка к 100%, образование маслянистого остатка на выходе из реактора не наблюдали (рис. 5).
Рис. 5.
Автотермический риформинг дизельного топлива на катализаторе Rh/CZ/FCA-mod: конверсия дизельного топлива Х и концентрации Н2, N2, CO, CO2 в пересчете на сухой газ (а); концентрации СH4 и углеводородов С2, С3 (б).
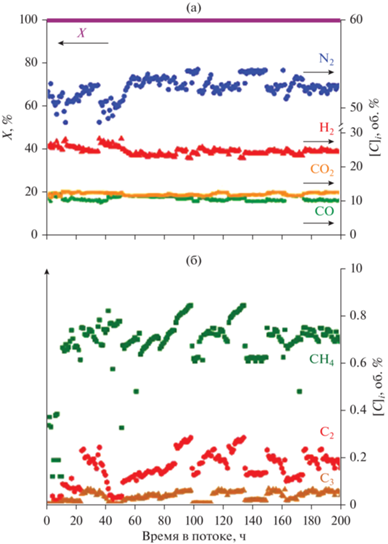
Стоит отметить, что, несмотря на высокую конверсию топлива, на выходе из реактора были обнаружены следы сажи, свидетельствующие о протекании процессов углеродообразования из побочных продуктов конверсии – углеводородов C2–C3. Из рис. 5б видно, что образуется около 0.2 об. % углеводородов С2, преимущественно этилена. Легкие газообразные углеводороды формируются в результате крекинга более сложных углеводородов, входящих в состав дизельного топлива. Кроме этого, в нем содержатся небольшие количества полиароматических соединений (<1 вес. %), конверсия которых протекает достаточно медленно [19]. Вероятно, их наличие в реакционной смеси также способствует формированию углерода на поверхности катализатора.
По результатам проведения ТПО катализатора после 10 ч в потоке скорость образования углерода на поверхности катализатора составила 8.6 мгсажи${\text{г}}_{{{\text{кат}}}}^{{ - 1}}$ ч–1. Визуально было выявлено, что сажа преимущественно образуется в лобовой части катализатора. Возможно, это также обусловлено протеканием гомогенных процессов крекинга и пиролиза в зоне смешения реагентов, расположенной перед катализатором. В связи с этим необходимы дальнейшие исследования, направленные на снижение влияния этих побочных процессов.
После проведения ресурсных испытаний катализатор Rh/CZ/FCA-mod был исследован методом ПЭМ и СЭМ, результаты были частично сопоставлены с полученными в работе [14]. На рис. 6 представлены СЭМ-микрофотографии катализаторов Rh/CZ/FCA (рис. 6а, 6б) [14] и Rh/CZ/FCA-mod (рис. 6в, 6г). В обоих случаях повреждение каталитического покрытия не выявлено. Наблюдается изменение морфологии поверхности катализатора при модификации методики нанесения. Из сравнения рис. 6б и 6г видно, что в случае Rh/CZ/FCA-mod носитель Ce0.75Zr0.25O2 обволакивает игольчатые кристаллы Al2O3, образуя объемное покрытие, скрывающее острые грани кристаллов. Масса блока Rh/CZ/FCA-mod после ресурсных испытаний составила 10.65 г (при начальной массе 10.80 г). Таким образом, значимого изменения массы каталитического покрытия в течение 200 ч работы и 20 циклов пуск/останов не произошло.
По данным ПЭМ после длительной работы частицы носителя CexZr1 – xO2 укрупнились и стали более окристаллизованными (рис. 7). Размер частиц Rh определить не удалось. Однако карта распределения родия в образце показывает, что он достаточно равномерно распределен по частицам носителя. Кроме того, было обнаружено накопление в образце остаточной серы из серосодержащих соединений дизельного топлива.
ЗАКЛЮЧЕНИЕ
В работе был получен и исследован структурированный Rh-содержащий катализатор конверсии дизельного топлива в синтез-газ. Использование метода соосаждения позволило нанести на поверхность структурированного блока покрытие из смешанного церий-циркониевого оксида. В отличие от покрытия, приготовленного методом пропитки, оно характеризовалось составом, близким к однофазному, и меньшим размером частиц, что, соответственно, приводило к увеличению удельной поверхности. При нанесении родия методом сорбционно-гидролитического осаждения на носителе формировались частицы размером менее 1 нм. Это дало возможность повысить активность Rh-содержащего катализатора в реакции автотермической конверсии модельной углеводородной смеси и снизить образование побочных продуктов.
В ходе ресурсных испытаний модифицированного Rh/Ce0.75Zr0.25O2 – δ/Ѳ-Al2O3/FeCrAl катализатора в реакции автотермической конверсии коммерческого дизельного топлива достигалась полная конверсия жидких углеводородов. При этом было зафиксировано образование сажи, преимущественно в лобовой части катализатора. Наиболее вероятно, это вызвано протеканием побочных гомогенных процессов крекинга и пиролиза в зоне смешения реагентов. Скорость образования углерода на поверхности катализатора составила 8.6 мгсажи ${\text{г}}_{{{\text{кат}}}}^{{ - 1}}$ ч–1. Тем не менее, каталитическое покрытие на было подвержено деградации, а образовавшиеся углеродные отложения можно удалять окислительной обработкой на воздухе при 600°С. Из полученных в ходе ресурсных испытаний результатов можно заключить, что модифицированный Rh-содержащий катализатор демонстрировал стабильную работу и обеспечивал производительность по синтез-газу ~8 м3${\text{л}}_{{{\text{кат}}}}^{{ - 1}}$ ч–1.
Список литературы
Бадмаев С.Д., Беляев В.Д., Собянин В.А. // Кинетика и катализ. 2022. Т. 63. № 3. С. 394.
Горлова А.М., Симонов П.А., Стонкус О.А., Пахарукова В.П., Снытников П.В., Потемкин Д.И. // Кинетика и катализ. 2021. Т. 62. № 6. С. 773.
Юсенко М.В., Беляев В.Д., Демин А.К., Бронин Д.И., Саланов А.Н., Собянин В.А., Снытников П.В., Потемкин Д.И. // Кинетика и катализ. 2022. Т. 63. № 1. С. 138.
Shigarov A.B., Kireenkov V.V., Kuzmin V.A., Kuzin N.A., Kirillov V.A. // Catal. Today. 2009. V. 144. № 3–4. P. 341.
Alvarez-Galvan M.C., Navarro R.M., Rosa F., Briceño Y., Gordillo Alvarez F., Fierro JL.G. // Int. J. Hydrogen Energy. 2008. V. 33. № 2. P. 652–663.
Bae J., Lee S., Kim S., Oh J., Choi S., Bae M., Kang I., Katikaneni S.P. // Int. J. Hydrogen Energy. 2016. V. 41. № 44. P. 19990.
Bae M., Cheon H., Oh J., Kim D., Bae J., Katikaneni S.P. // Int. J. Hydrogen Energy. 2021. V. 46. № 52. P. 26575.
Ju D.G., Jo S.B., Ha D.S., Kim T.Y., Jung S.Y., Chae H.J., Lee S.C., Kim J.C. // Catalysts. 2019. V. 9. № 7. P. 573.
Karatzas X., Jansson K., Dawody J., Lanza R., Pettersson L.J. // Appl. Catal. B: Env. 2011. V. 101. № 3–4. P. 226.
Karatzas X., Dawody J., Grant A., Svensson E.E., Pettersson L.J. // Catal. Today. 2011. P. 515.
Kim D., Choi S., Jeong S., Bae M., Katikaneni S.P., Bae J., Heo S., Lee J.H. // Chem. Eng. J. 2021. V. 424. P. 130 564.
Pasel J., Samsun R.C., Meißner J., Tschauder A., Peters R. // Int. J. Hydrogen Energy. 2019. V. 11. P. 137.
Rogozhnikov V.N., Kuzin N.A., Snytnikov P.V., Potemkin D.I., Shoynkhorova, T.B., Simonov P.A., Shilov V.A., Ruban N.V., Kulikov A.V., Sobyanin V.A. // Chem. Eng. J. 2019. V. 374. P. 511.
Rogozhnikov V.N., Potemkin D.I., Ruban, N.V., Shilov V.A., Salanov A.N., Kulikov A.V., Simonov P.A., Gerasimov E.Y., Sobyanin V.A., Snytnikov P.V. // Mater. Lett. 2019. V. 257. P. 126715.
Samsun R.C., Prawitz M., Tschauder A., Meißner J., Pasel J., Peters R. // Appl. Energy. 2020. V. 279. P. 115882.
Shekhawat D., Gardner T.H., Berry D.A., Salazar M., Haynes D.J., Spivey J.J. // Appl. Catal. A: Gen. 2006. V. 311. № 1–2. P. 8.
Shilov V.A., Rogozhnikov V.N., Zazhigalov S.V., Potemkin D.I., Belyaev V.D., Shashkov M.V., Zagoruiko A.N., Sobyanin V.A., Snytnikov P.V. // Int. J. Hydrogen Energy. 2021. V. 46. № 72. P. 35866.
Shilov V.A., Rogozhnikov V.N., Ruban N.V., Potemkin D.I., Simonov P.A., Shashkov M.V., Sobyanin V.A., Snytnikov P.V. // Catal. Today. 2021. V. 379. P. 42.
Shilov V.A., Rogozhnikov V.N., Potemkin D.I., Belyaev V.D., Shashkov M.V., Sobyanin V.A., Snytnikov P.V. // Int. J. Hydrogen Energy. 2022. V. 47. № 21. P. 11316.
Younis M.N., Malaibari Z.O., Ahmad W., Ahmed S. // Energy and Fuels. 2018. V. 32. № 6. P. 7054.
Zazhigalov S.V., Rogozhnikov V.N., Snytnikov P.V., Potemkin D.I., Simonov P.A., Shilov V.A., Ruban N.V., Kulikov A.V., Zagoruiko A.N., Sobyanin V.A. // Chem. Eng. Process. Process Intensif. 2020. V. 150. P. 107876.
Zazhigalov S.V., Shilov V.A., Rogozhnikov V.N., Potemkin D.I., Sobyanin V.A., Zagoruiko A.N., Snytnikov P.V. // Catal. Today. 2021. V. 378. P. 240.
Zazhigalov S.V., Shilov V.A., Rogozhnikov V.N., Potemkin D.I., Sobyanin V.A., Zagoruiko A.N., Snytnikov P.V. // Chem. Eng. J. 2022. V. 442. P. 136160.
Симонов П.А., Шойнхорова Т.Б., Снытников П.В., Потемкин Д.И., Беляев В.Д. Патент RU 2653360 C1, 2017.
Porsin A.V., Kulikov A.V., Rogozhnikov V.N., Serkova A.N., Salanov A.N., Shefer K.I. // Catal. Today. 2016. V. 273. P. 213.
Rogozhnikov V.N., Potemkin D.I., Pakharukova V.P., Belyaev V.D., Nedolivko V.V., Glotov A.P., Sobyanin V.A., Snytnikov P.V. // Int. J. Hydrogen Energy. 2021. V. 46. № 72. P. 35853.
Shoynkhorova T.B., Simonov P.A., Potemkin D.I., Snytnikov P.V., Belyaev V.D., Ishchenko A.V., Svintsitskiy D.A., Sobyanin V.A. // Appl. Catal. B: Env. 2018. V. 237. P. 237. 1.
Дополнительные материалы отсутствуют.
Инструменты
Кинетика и катализ