Кинетика и катализ, 2023, T. 64, № 1, стр. 97-108
Влияние стехиометрии и способа синтеза порошкообразного прекурсора Cu–Fe–Al на стабильность и активность керамометаллов CuFeAlO/CuFeAl в реакции среднетемпературной паровой конверсии СО
С. Ф. Тихов a, *, К. Р. Валеев a, С. В. Черепанова a, А. Н. Саланов a, А. А. Сараев a, В. В. Каичев a, Т. П. Минюкова a
a ФГБУН ФИЦ Институт катализа им. Г.К. Борескова СО РАН
630090 Новосибирск, просп. Акад. Лаврентьева, 5, Россия
* E-mail: tikhov@catalysis.ru
Поступила в редакцию 08.08.2022
После доработки 01.09.2022
Принята к публикации 02.09.2022
- EDN: KJDHAM
- DOI: 10.31857/S0453881123010100
Аннотация
Керамометаллические катализаторы CuFeAlO/CuFeAl, полученные из различных порошкообразных прекурсоров Cu–Fe–Al, отличающихся стехиометрией и способом приготовления, охарактеризованы физико-химическими методами и исследованы в реакции паровой конверсии СО (СО + + Н2О ⇌ СО2 + Н2). Катализаторы представляют собой единый пористый композит, в котором металлические частицы покрыты оксидной оболочкой. Показано, что наиболее стабилен образец со стехиометрией Cu : Fe : Al = 45 : 22 : 33 ат. %, синтезированный из порошкообразного прекурсора в две стадии. На первой стадии проводили механохимическое сплавление порошков железа и меди, а на второй – механохимическую обработку полученного продукта, смешанного с алюминием. Это позволило обеспечить более равномерное распределение компонентов в прекурсоре. Методами рентгеновской дифракции, сканирующей электронной микроскопии и рентгеновской фотоэлектронной спектроскопии исследованы образцы керамометаллических катализаторов до и после реакции при 400°С. Выявлено, что наиболее активные при 350°С катализаторы имеют после обработки в восстановительной среде восстановленные центры Cu1+ и Fe3+. Наименее активные катализаторы восстанавливаются полностью до Cu0 и частично до Fe0. Обнаружено что активность в области температур 330–400°С определяется не только железными, но и медными активными центрами на поверхности катализаторов или их совместным действием. Двухстадийная мехактивация, по-видимому, приводит к более глубокому химическому взаимодействию компонентов – Fe и Cu, что обеспечивает более высокую активность бесхромовых CuFeAl керамометаллических катализаторов.
ВВЕДЕНИЕ
Паровая конверсия СО является важнейшей стадией в процессе получения водорода по реакции паровой конверсии метана [1, 2]. Процесс паровой конверсии СО проводят в два этапа. На первом (среднетемпературном) реакция осуществляется при 320–450°С, на втором (низкотемпературном) – при 150–250°С [1]. Для среднетемпературной конверсии СО используются преимущественно катализаторы на основе смешанных оксидов железа и хрома [3–5]. Однако хром является токсичным компонентом, поэтому многими исследователями предпринимаются попытки заменить его другими промоторами, позволяющими повысить стабильность при сохранении активности [6–11].
Поиску оптимального соотношения компонентов и методов приготовления стабильных и активных не содержащих хром катализаторов среднетемпературной паровой конверсии СО посвящены многочисленные исследования. По литературным данным [7] наиболее активен смешанный оксид с соотношением Cu : Fe : Al = 1 : 1 : 1. Согласно [8, 11] максимальной активностью обладает нанесенная на мезопористый оксид алюминия Cu-Fe-шпинель при соотношении Cu : Fe = = 1 : 1. По результатам работы [10] самым активным является феррит с весовым отношением Fe/Al = 10 и Fe/Cu = 5. Среди методов приготовления катализаторов наиболее высокое качество катализаторов обеспечивает метод соосаждения [7, 10, 12], имеющий существенные технологические недостатки. Этих недостатков лишен метод мехактивации и последующей гидротермальной обработки, которым получают керамометаллические катализаторы. Механохимическая активация в последние годы рассматривается как перспективный экологически чистый метод приготовления катализаторов, в том числе композитных [13, 14]. В результате мехактивации предшественников повышается дисперсность материалов и образуются дефекты структуры в объеме и на поверхности, что позволяет модифицировать каталитические свойства [15].
Паровая конверсия СО – экзотермическая реакция, а теплопроводность традиционных оксидных катализаторов является недостаточной для предотвращения разогрева катализаторного слоя [16]. Для гранул, обычно используемых в промышленных условиях, характерно внутридиффузионное торможение, поскольку в них слабо развиты транспортные поры [17]. С этой точки зрения перспективными оказываются высокопористые керамометаллические катализаторы [18, 19], которые показали достаточно значительную активность единицы объема в низкотемпературной паровой конверсии CO из-за развитой полидисперсной пористой структуры и хорошую теплопроводность благодаря большому содержанию частиц металла. Эти материалы обладают высокой насыпной плотностью каталитического слоя. Ранее были изучены СuFeAl керамометаллические катализаторы в низкотемпературной паровой конверсии СО [19, 20]. Однако по сравнению с традиционными оксидными системами образцы оказались недостаточно стабильны. Целью настоящей работы было исследование факторов, способствующих повышению активности и стабильности керамометаллических CuFeAl-катализаторов в восстановительной реакционной среде среднетемпературной паровой конверсии СО.
ЭКСПЕРИМЕНТАЛЬНАЯ ЧАСТЬ
Керамометаллы синтезировали, используя в качестве исходного сырья алюминиевую пудру марки ПАП-2 (ГОСТ 5494-95), порошкообразную медь марки ПМС-1 (ГОСТ 4960-75) и порошкообразное железо марки ПЖВ 1.17.28 (ГОСТ 9849-86) в различных атомных отношениях (Сu45Fe22Al33, Cu28Fe22Al50, Cu24Fe20Al56). Синтез предусматривал несколько стадий:
а) механохимическое сплавление (МА) в одну стадию смесей порошков Cu, Fe, Al в планетарной мельнице АПФ-2 (ИХТМС СО РАН, Россия) при ускорении 20 g (стальные шары диаметром 5 мм при весовом соотношении 1 : 20) осуществляли в течение 12 мин. Двухстадийный синтез проводили дополнительно для образца Сu45Fe22Al33-24. На первой стадии механохимическое сплавление выполняли для смеси Cu + Fe в течение 90 мин аналогично [21]. На второй стадии полученный порошок смешивали с алюминиевой пудрой и проводили механохимическое сплавление в течение 24 мин [21];
б) гидротермальную обработку (ГТО) порошкообразного продукта МА, предварительно засыпанного в специальную пресс-форму из нержавеющей стали, осуществляли в течение 4 ч при ~100°С. Гидротермальная обработка приводила к частичному окислению алюминия и гидролизу, что обеспечивало цементирование металлических частиц в монолит;
в) после извлечения керамометаллического монолита из пресс-формы его сушили и прокаливали при 550°С на воздухе.
Фазовый состав предварительно размолотых образцов керметов до и после реакции исследовали методом порошковой рентгеновской дифракции (РД) на рентгеновском дифрактометре D8 Advance (“Bruker”, Германия) с фокусировкой по Брэггу–Брентано. Рентгенограммы были записаны с использованием излучения CuKα (длина волны λ = 1.5418 Å) в интервале углов 2θ от 25° до 85° c шагом 0.05°. Фазы идентифицировали с помощью баз данных PDF-2 и PDF-4 (ICDD-JCPDS). Оценку весовых соотношений содержания фаз, а также уточнение параметров элементарной ячейки для каждой фазы производили методом Ритвельда с применением программы TOPAS. Для определения области когерентного рассеяния (ОКР) использовали формулу Шеррера.
Морфологию поверхности материалов анализировали с помощью сканирующего электронного микроскопа JSM-6460 LV (“Jeol”, Япония). Исследовали рельеф поверхности керамометаллов на изломе гранул, а также микроструктуру полированной поверхности керамометалла.
Для определения удельной поверхности (Sуд) катализаторов записывали изотермы адсорбции азота при температуре 77 К с использованием автоматизированного прибора ASAP-2400 (“Micromeritics”, США). Удельную поверхность рассчитывали методом Брунауера–Эммета–Теллера (БЭТ).
Химический состав поверхности катализаторов после каталитических измерений оценивали методом рентгеновской фотоэлектронной спектроскопии (РФЭС). Исследования проводили на рентгеновском фотоэлектронном спектрометре, оснащенном полусферическим энергоанализатором PHOIBOS-150 и источником рентгеновского характеристического излучения XR-50 с двойным Al/Mg анодом (“SPECS Surface Nano Analysis GmbH”, Германия). Для записи спектров применяли немонохроматизированное излучение AlKα (hν = 1486.61 эВ). Обработку данных производили с помощью пакета программ CasaXPS. Для учета эффекта зарядки образцов использовали пик Al2p с энергией связи 74.5 эВ, соответствующий оксиду алюминия. Фон неупруго рассеянных электронов аппроксимировали функцией Ширли. Отличительной особенностью спектрометра является наличие ячейки высокого давления, предназначенной для обработки катализаторов в смесях газов при различных температурах и последующего их переноса в аналитическую камеру спектрометра без контакта с атмосферой воздуха [22]. Перед измерениями катализаторы обрабатывали в кислороде, а затем в водороде. В обоих случаях обработку осуществляли при атмосферном давлении при температуре 330°С в течение 1 ч. Запись спектров производили в сверхвысоком вакууме при комнатной температуре. Более детально методика эксперимента описана в работе [19].
Каталитические измерения в реакции паровой конверсии СО (СО + Н2О ⇌ СО2 + Н2) проводили в проточном реакторе, анализ состава реакционной смеси выполняли газохроматографическим методом. Катализаторы активировали в смеси 5% Н2 в гелии при 350°С, объемной скорости подачи 3000–4000 ч–1, скорость подъема температуры 2 град/мин. Активность измеряли при атмосферном давлении, при температурах 330, 350, 400, 350°С. Состав реакционной смеси: СО : Н2О : Н2 = = 5.5 : 50 : 44.5; отношение пар : газ = 1.0, время контакта – 0.06 с. Измерения осуществляли в кинетической области на фракции образцов 0.14–0.25 мм, навеске 0.5 г. Активность оценивали по величине константы скорости прямой реакции, рассчитанной в приближении первого порядка по СО.
РЕЗУЛЬТАТЫ И ИХ ОБСУЖДЕНИЕ
Активность и стабильность CuFeAlO/CuFeAl керамометаллов в паровой конверсии СО
Как видно из табл. 1 начальная активность катализаторов при 330°С существенно различается. Катализаторы с меньшим содержанием меди и бóльшим содержанием алюминия (Cu28Fe22Al50 и Cu24Fe20Al56) имеют активность ниже, чем катализаторы Сu45Fe22Al33 и Сu45Fe22Al33-24, хотя их удельная поверхность заметно выше. Достаточно значительная удельная поверхность, несмотря на то что размер частиц металлических порошков после МА составляет десятки мкм, обусловлена высокой удельной поверхностью оксидного слоя. Этот слой формируется в процессе ГТО и прокаливания. Развитая поверхность этого слоя хорошо видна на снимках СЭМ (рис. 1).
Таблица 1.
Активность керамометаллических катализаторов до и после перегрева при 400° в реакционной среде
Образец | Активность, k | Sуд, м2/г |
КА, 350°, после испытаний, с–1 ${{{\text{м}}}_{{{\text{C}}{{{\text{u}}}^{{2 - }}}}}}$ | ||||||
---|---|---|---|---|---|---|---|---|---|
с–1 | с–1/м2 | исходный | после испытаний | ||||||
до испытаний | после испытаний | ||||||||
330°C | 350°C | 400°C | 350°C | 330°С | 350°С | ||||
Сu45Fe22Al33 | ~1.4 | Дезактивация | 0.04 | <0.001 | 22.7 | 17.0 | $ \ll $0.001 | ||
Сu45Fe22Al33-24 | 2.3 | 2.1 | 3.2 | 1.4 | 0.43 | 0.28 | 10.7 | 7.2 | 0.7 |
Cu28Fe22Al50 | 0.8 | 0.6 | 0.9 | 0.4 | 0.05 | 0.04 | 29.7 | 27.0 | 0.4 |
Cu24Fe20Al56 | 0.1 | 0.1 | 0.3 | 0.2 | ~0.003 | ~0.008 | 30.4 | 30.0 | 0.1 |
Примечание. КА – удельная активность, отнесенная к содержанию поверхностных атомов меди, оцененному по данным РФЭС (см. табл. 4).
Рис. 1.
Изображение СЭМ поверхности керамометаллического катализатора (a) и шлифа керамометаллического катализатора (б): 1 – металлическое ядро, 2 – оксидная оболочка.
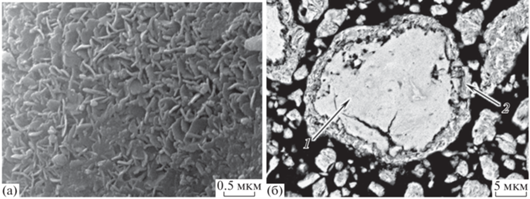
После пребывания в реакционной среде при 400°С активность при 350°С существенно падает. Одной из причин этого является уменьшение удельной поверхности катализаторов Сu45Fe22Al33 и Сu45Fe22Al33-24. Однако для катализаторов Cu28Fe22Al50 и Cu24Fe20Al56, имеющих крайне низкую начальную активность, сокращение удельной поверхности незначительно (табл. 1). Сравнивая активности, отнесенные к единице поверхности катализаторов, до и после выдерживания при 400°С, можно сделать вывод что активность и стабильность активных центров на поверхности катализаторов значительно различаются у разных катализаторов. Наиболее перспективным представляется образец Сu45Fe22Al33-24, полученный при мехактивации в две стадии.
Особенности структуры и микроструктуры керамометаллических катализаторов
Для выяснения причин различия удельной активности был проведен детальный рентгенофазовый анализ образцов до и после реакции при 400°С (рис. 2, 3, табл. 2, 3). Почти для всех керамометаллических катализаторов до испытаний характерно наличие металлических фаз Cu, Fe и Al (Al, PDF#04-0787, Cu, PDF#04-0836, Fe, PDF#06-0696), твердого раствора алюминия в меди Cu1 – xAlx, а также интерметаллида Al4Cu9 (PDF#24-0003) (табл. 2, рис. 2). В образце Cu45Fe22Al33-24 отсутствует фаза металлического алюминия. В образцах Cu24Fe20Al56, Cu28Fe22Al50 и Cu45Fe22Al33-24 присутствует интерметаллид Al7Cu2Fe (PDF#25-112). Обнаружены также оксидные фазы: СuO (PDF#05-0661) у всех, кроме Cu24Fe20Al56, а также фаза со структурой шпинели у всех катализаторов. Параметр шпинели у образцов Cu24Fe20Al56 и Cu28Fe22Al50 промежуточный между параметром Fe3O4 (8.396 Å, PDF#19-0629) и CuFe2O4 (8.349 Å, PDF#25-0283). Параметр Cu45Fe22Al33-24 ближе к таковому чистой шпинели CuFe2O4. Параметр Cu45Fe22Al33 заметно меньше (8.320 Å) и ближе к шпинели Fe2AlO4 (8.273 Å, PDF#01-089-7408). Необходимо отметить, что для тройной системы (Fe, Cu, Al) по параметру решетки шпинели состав определить сложно.
Рис. 2.
Рентгенограммы образцов керамометаллических катализаторов до испытаний: 1 – Cu24Fe20Al56, 2 – Cu28Fe22Al50, 3 – Cu45Fe22Al33-24, 4 – Cu45Fe22Al33.
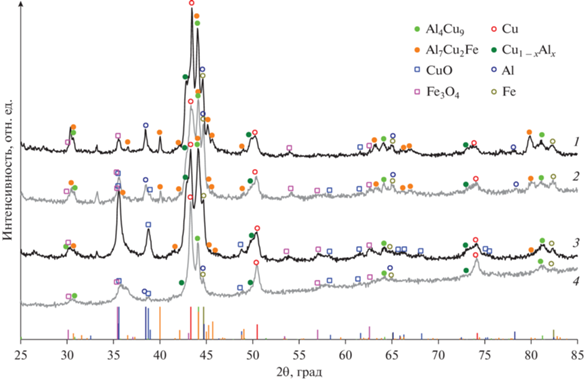
Рис. 3.
Рентгенограммы образцов керамометаллических катализаторов после каталитических испытаний: 1 – Cu24Fe20Al56, 2 – Cu28Fe22Al50, 3 – Cu45Fe22Al33-24, 4 – Cu45Fe22Al33.
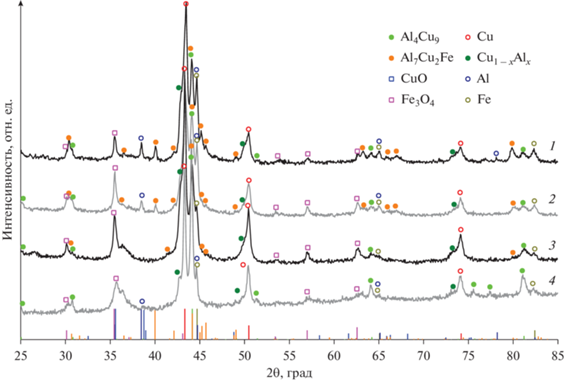
Таблица 2.
Данные рентгенофазового анализа керамометаллических катализаторов до испытаний
Образец | Параметры РСА | Cu | Cu1 – xAlx | Al | Fe | Al4Cu9 | Al7Cu2Fe | CuO | Шпинель |
---|---|---|---|---|---|---|---|---|---|
Cu24Fe20Al56 | ОКР, нм | 27 | 16 | 22 | 30 | 14 | 40 | н/o | 20 |
Содержание, мас. % | 20 | 18 | 9 | 6 | 28 | 12 | н/o | 6 | |
Параметр решетки, Å | н/о | 3.649(2) х = 0.08 |
н/о | н/о | н/о | н/о | н/о | 8.374(2) | |
Cu28Fe22Al50 | ОКР, нм | 10 | 24 | >100 | 23 | 18 | 45 | 40 | 16 |
Содержание, мас. % | 39 | 5 | 7 | 11 | 21 | 3.5 | 1.5 | 12 | |
Параметр решетки, Å | н/о | 3.658(2) х = 0.10 |
н/о | н/о | н/о | н/о | н/о | 8.360(2) | |
Cu45Fe22Al33-24 | ОКР, нм | 21 | 13 | н/o | 22 | 13 | 13 | 30 | 13 |
Содержание, мас. % | 26 | 10 | н/o | 3 | 25 | 2 | 10 | 24 | |
Параметр решетки, Å | н/о | 3.653(2) х = 0.09 |
н/о | н/о | н/о | н/о | н/о | 8.354(2) | |
Cu45Fe22Al33 | ОКР, нм | 40 | 11 | 13 | 13 | 28 | н/o | 18 | 13 |
Содержание, мас. % | 14 | 28 | 16 | 6 | 14 | н/o | 20 | 2 | |
Параметр решетки, Å | н/о | 3.617(2) х = 0.01 |
н/о | н/о | н/о | н/о | н/о | 8.320(2) |
Таблица 3.
Данные рентгенофазового анализа керамометаллических катализаторов после каталитических испытаний
Образец | Параметры РСА |
Cu | Cu1 – xAlx | Al | Fe | Al4Cu9 | Al7Cu2Fe | CuO | Шпинель |
---|---|---|---|---|---|---|---|---|---|
Cu24Fe20Al56 | ОКР, нм | 24 | 17 | 50 | 22 | 17 | 40 | н/o | 30 |
Содержание, мас. % | 28 | 15 | 5 | 12 | 21 | 12 | н/o | 8 | |
Параметр решетки, Å | н/о | 3.647(2) х = 0.07 |
н/о | н/о | н/о | н/о | н/о | 8.383(2) | |
Cu28Fe22Al50 | ОКР, нм | 13 | 23 | >100 | 20 | 17 | 45 | н/o | 22 |
Содержание, мас. % | 43 | 4 | 3 | 10 | 20 | 5 | н/o | 15 | |
Параметр решетки, Å | н/о | 3.658(2) х = 0.10 |
н/о | н/о | н/о | н/о | н/о | 8.382(2) | |
Cu45Fe22Al33-24 | ОКР, нм | 40 | 12 | н/o | 19 | 13 | 13 | н/o | 17 |
Содержание, мас. % | 33 | 12 | н/o | 4 | 25 | 2 | н/o | 24 | |
Параметр решетки, Å | н/о | 3.649(2) х = 0.08 |
н/о | н/о | н/о | н/о | н/о | 8.384(2) | |
Cu45Fe22Al33 | ОКР, нм | 40 | 25 | 13 | 35 | 32 | н/o | н/o | 13 |
Содержание, мас. % | 25 | 5 | 15.5 | 4.5 | 29 | н/o | н/o | 21 | |
Параметр решетки, Å | н/о | 3.661(2) х = 0.11 |
н/о | н/о | н/о | н/о | н/о | 8.344(2) |
Сравнение активности и фазового состава исходных катализаторов можно проводить только для оксидной части, которая сконцентрирована в поверхностном слое керамометаллов (рис. 1б). При сопоставлении структурных параметров с активностью единицы поверхности при 330°С можно сделать вывод, что самый высокий вклад в активность дает шпинель CuFe2O4, содержание которой максимально именно у наиболее активного образца Cu45Fe22Al33-24, а также оксид меди (табл. 1, 2). В состав менее активных, но сопоставимых между собой образцов входит либо достаточно большое количество шпинели (Cu28Fe22Al50), либо большое количество оксида меди (Cu45Fe22Al33), которая после активации переходит в активную металлическую медь. Самый неактивный образец (Cu24Fe20Al56) оксида меди не содержат вообще, а шпинель по параметру решетки ближе к Fe3O4, менее активной в высокотемпературной паровой конверсии СО [12].
После испытаний по данным рентгенофазового анализа ряд количественных изменений наблюдается в металлических ядрах, несмотря на то что они закрыты оксидной оболочкой. Так, содержание алюминия заметно падает во всех образцах, где он регистрировался до испытаний (табл. 2, 3). По-видимому, это обусловлено его окислением водой, имеющейся в реакционной среде. Содержание фазы железа у образцов Cu28Fe22Al50, Cu45Fe22Al33-24 примерно постоянно, у образца Cu45Fe22Al33 немного снижается, а у Cu24Fe20Al56 растет с 6 до 12 мас. % (табл. 2,3). Сложно ведут себя интерметаллические соединения: концентрация твердого раствора Cu1 – xAlx заметно уменьшается в образце Cu45Fe22Al33 с 29 до 5 мас. %, а в остальных катализаторах его концентрация примерно постоянна. Также неоднозначно поведение интерметаллида Al4Cu9: существенное увеличение концентрации наблюдается именно в образце Cu45Fe22Al33-24. В остальных керамометаллических катализаторах его концентрация примерно постоянна. Можно полагать, что интерметаллид Al4Cu9 образуется в реакционной среде из твердого раствора Cu1 – xAlx, поскольку избыточное количество алюминия концентрируется на межзеренных границах [23]. Таким образом, восстановительная реакционная среда заметно влияет на металлические ядра, находящиеся в объеме керамометаллических катализаторов.
Достаточно очевидно меняются содержания CuO и Cu0 до и после испытаний. В отработанных катализаторах оксид меди отсутствует, а содержание металлической меди после восстановительной активации и восстановительной реакционной среды возрастает (табл. 2, 3). Количество фазы шпинели в катализаторах Cu24Fe20Al56 и Cu28Fe22Al50 немного повышается, в Cu45Fe22Al33-24 не изменяется, а в Cu45Fe22Al33 растет с 2 до 21 мас. %. Во всех случаях увеличивается и параметр шпинели. У образцов Cu24Fe20Al56, Cu28Fe22Al50 и Cu45Fe22Al33-24 он приближается к параметру Fe3O4, у Cu45Fe22Al33 – к таковому шпинели CuFe2O4. Учитывая слабую интенсивность и достаточно большое уширение пиков (рис. 2, 3), оценка параметров шпинели весьма приблизительна.
Ранее для реакции низкотемпературной паровой конверсии СО была выявлена тенденция повышения активности с увеличением содержания интерметаллида Al4Cu9 [20]. В нашем случае при сравнении активности образцов при 350°С после пребывания в реакционной среде при 400°С можно сделать вывод об отсутствии какой-либо однозначной связи с фазовым составом оксидной оболочки керамометаллов, а также концентрацией и дисперсностью металлической меди (табл. 3). Последнее является следствием того, что металлическая медь существует не только на поверхности оксидной оболочки, но и в объеме катализаторов, в металлических ядрах. Поэтому для выявления факторов, влияющих на активность и стабильность керамометаллических катализаторов, было проведено исследование свойств поверхности выгруженных катализаторов методом РФЭС.
Исследование химического состава поверхностного слоя катализаторов CuFeAl после испытаний методом РФЭС
На рис. 4 представлены спектры Fe2p катализаторов после обработки в кислороде (O2) и после последующей обработки в водороде (O2/H2). Спектры Fe2p вследствие спин-орбитального взаимодействия представляют собой дублет Fe2p3/2–Fe2p1/2, интегральные интенсивности компонент которого соотносятся как 2 : 1 (рис. 4). Как правило, для определения состояния железа используют как положение основной линии Fe2p3/2, так и форму спектра Fe2p, а именно интенсивность и относительное положение сателлитов, обусловленных проявлением многоэлектронных процессов. Высокое значение энергии связи (Есв) Fe2p3/2 (711.1 эВ) и наличие ярко выраженных сателлитов в районе 719.8 эВ свидетельствуют, что в окисленных катализаторах железо находится в состоянии Fe3+ [19, 24]. Восстановительная обработка образцов Cu45Fe22Al33 и Cu45Fe22Al33-24 не ведет к каким-либо изменениям спектров Fe2p, т.е. химическое состояние железа не меняется. В то же время в спектрах катализаторов Cu28Fe22Al50 и Cu24Fe20Al56 появляется дополнительный дублет Fe2p3/2–Fe2p1/2 с энергией связи Fe2p3/2, равной 707.2 эВ. Столь низкое значение энергии связи Fe2p3/2 характерно для железа в металлическом состоянии [25]. Следовательно, железо частично восстанавливается в катализаторах Cu28Fe22Al50 и Cu24Fe20Al56 в атмосфере водорода при 330°С. Доля железа в металлическом состоянии составляет 30 и 60% соответственно. Результаты анализа РФЭ-спектров приведены в табл. 4.
Рис. 4.
Спектры Fe2p исследованных катализаторов: а – после обработки в кислороде (${{P}_{{{{{\text{O}}}_{{\text{2}}}}}}}$ = 1 бар; Т = 330°С); б – после последующей обработки в водороде (${{P}_{{{{{\text{H}}}_{{\text{2}}}}}}}$ = 1 бар; Т = 330°С). Спектры нормированы на суммарную интегральную интенсивность соответствующих спектров Al2p, Cu2p и Fe2p.
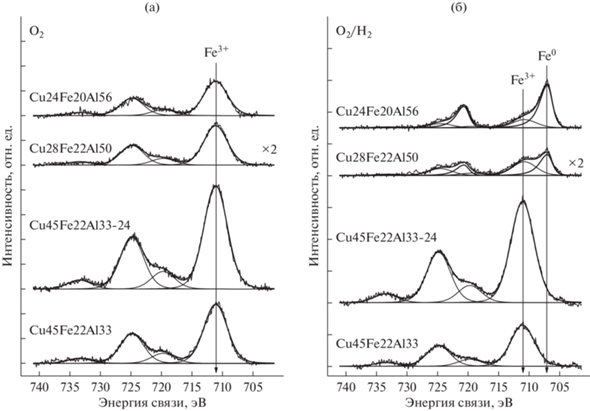
Таблица 4.
Значения энергий связи Cu2p3/2, Fe2p3/2 и Оже-параметра α (эВ) исследованных катализаторов*
Образец | Тренировка | Cu2p3/2 | α | Состояние | Fe2p3/2 | Состояние | Cu/(Cu + Fe + Al) |
---|---|---|---|---|---|---|---|
Cu45Fe22Al33 | O2 | 933.7 | 1851.3 | Cu2+ (100%) | 711.1 | Fe3+ | 0.41 |
O2/H2 | 932.7 | 1851.1 | Cu0 (90%) | 711.1 | Fe3+ | 0.44 | |
934.8 | н/о | Cu1+ (10%) | |||||
Cu45Fe22Al33-24 | O2 | 933.7 | 1851.3 | Cu2+ (100) | 711.1 | Fe3+ | 0.30 |
O2/H2 | 932.7 | 1851.1 | Cu0 (90%) | 711.1 | Fe3+ | 0.40 | |
934.2 | н/о | Cu1+ (10%) | |||||
Cu28Fe22Al50 | O2 | 933.7 | 1851.3 | Cu2+ (100%) | 711.1 | Fe3+ | 0.13 |
O2/H2 | 932.7 | 1851.1 | Cu0 (100%) | 707.2 | Fe0 (30%) | 0.10 | |
711.1 | Fe3+ (70%) | ||||||
Cu24Fe20Al56 | O2 | 933.7 | 1851.3 | Cu2+ (100%) | 711.1 | Fe3+ | 0.09 |
O2/H2 | 932.7 | 1851.1 | Cu0 (100%) | 707.2 | Fe0 (60%) | 0.07 | |
711.1 | Fe3+ (40%) |
Спектры Cu2p катализаторов после обработки в кислороде (O2) и после последующей обработки в водороде (O2/H2) представлены на рис. 5. Спектры Cu2p также представляют собой дублет Cu2p3/2–Cu2p1/2, интегральные интенсивности компонент которого соотносятся как 2 : 1. Форма спектров позволяет утверждать, что в приповерхностном слое катализаторов после обработки в кислороде медь находиться преимущественно в состоянии Cu2+. В пользу этого свидетельствуют высокая энергия связи Cu2p3/2, равная 933.7 эВ, а также наличие интенсивных сателлитов, характерных исключительно для Cu2+ [19, 24]. Обработка в водороде приводит к существенному изменению спектров. Так, спектры Cu2p катализаторов Cu28Fe22Al50 и Cu24Fe20Al56 содержат только два узких пика Cu2p3/2 и Cu2p1/2. Отсутствие сателлитов и низкая энергия связи Cu2p3/2, равная 932.7 эВ, указывают на то, что медь находится в состоянии Cu1+ и/или Cu0. Оба состояния меди характеризуются близкой энергией связи Cu2p3/2. Для того, чтобы их отличить, были записаны дополнительно рентген-индуцированные Оже-спектры CuLMM и рассчитан так называемый Оже-параметр α. В данном случае Оже-параметр равен сумме энергии связи Cu2p3/2 и положения максимума Оже-спектра CuLMM на шкале кинетических энергий электронов. В соответствии с литературными данными, значения Оже-параметра для массивных образцов металлической меди, Cu2O и CuO составляют 1851.0–1851.4, 1848.7–1849.3 и 1851.4–1851.7 эВ соответственно [19, 24]. Для восстановленных катализаторов Cu28Fe22Al50 и Cu24Fe20Al56 Оже-параметр равен 1851.1 эВ, что характерно для меди в металлическом состоянии (табл. 4). Следовательно, обработка в водороде этих катализаторов приводит не только к частичному восстановлению Fe3+ → Fe0 (рис. 5б), но и к полному восстановлению меди Cu2+ → Cu0.
Рис. 5.
Спектры Cu2p исследованных катализаторов: а – после обработки в кислороде (${{P}_{{{{{\text{O}}}_{{\text{2}}}}}}}$ = 1 бар; Т = 330°С); б – после последующей обработки в водороде (${{P}_{{{{{\text{H}}}_{{\text{2}}}}}}}$ = 1 бар; Т = 330°С). Спектры нормированы на суммарную интегральную интенсивность соответствующих спектров Al2p, Cu2p и Fe2p.
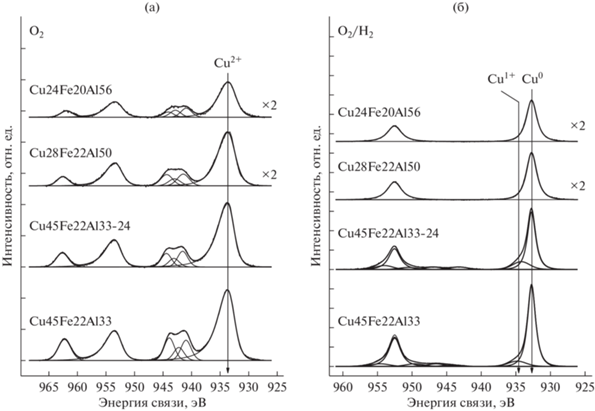
Спектры Cu2p восстановленных катализаторов Cu45Fe22Al33 и Cu45Fe22Al33-24 имеют более сложную форму (рис. 5б). Основной пик Cu2p3/2 состоит из двух пиков: интенсивного асимметричного в районе 932.7 эВ и низкоинтенсивного симметричного в области больших энергий связи. Для интенсивного пика Оже-параметр равен 1851.1 эВ (табл. 4), что соответствует меди в металлическом состоянии. Для второго пика определить Оже-параметр не представляется возможным. Однако положение этого пика (934.2–934.8 эВ) характерно для меди в окисленном состоянии Cu2+.
Таким образом, поверхностный слой керамометаллических катализаторов после пребывания при 400°С в реакционной среде и тренировки в кислороде находится в окисленном состоянии; железо и медь присутствуют преимущественно в состояниях Fe3+ и Cu2+ (табл. 4). Последующая обработка в водороде проявляет различия в химических свойствах поверхностного слоя. Для образцов с невысоким содержанием меди (Cu28Fe22Al50 и Cu24Fe20Al56) характерна легкая восстанавливаемость до состояния Cu0 и частичное восстановление до состояния Fe0 без образования каких-либо промежуточных состояний (Fe2+, Fe1+). В то же время для катализаторов с большим содержанием меди и меньшим – железа (Cu45Fe22Al33, Cu45Fe22Al33-24) после тренировки в водороде в поверхностном слое наблюдается стабильное состояние Fe3+. Оксид меди (Cu2+) исчезает. Однако окисленные соединения меди не полностью восстанавливаются до Cu0. Часть меди имеет степень окисления Cu2+ (табл. 4).
Ранее методом РФЭС были исследовали оксидные CuFeAl-системы, полученные различными способами [12]. Предварительно образцы вакуумировали при комнатной температуре. Даже после такой мягкой предобработки на поверхности помимо центров Cu2+ в CuO были выявлены восстановленные центры Cu+(Cu0) без детального анализа их природы. Обнаружено, что активность в среднетемпературной паровой конверсии СО пропорциональна концентрации этих легко восстанавливающихся центров. Для шпинели CuFe2O4, нанесенной на оксид алюминия [8], после вакуумирования при комнатной температуре, также было показано, что в самой активной шпинели состава Cu1.5Fe1.5Ox концентрация легко восстанавливающихся центров Cu+(Cu0) тоже наибольшая. Дополнительно выявлено, что в активном образце отношение Fe2+/Fe3+ минимальное, т.е. устойчивость оксида железа к восстановлению максимальная. В работе [26] было продемонстрировано, что для системы CuFeOx в реакционной среде концентрация восстановленной меди снижается с повышением температуры. Позднее в [27] было обнаружено, что в зависимости от условий приготовления смешанного оксида CuFeOx концентрация восстановленных центров меди в реакционной среде может снижаться с повышением температуры от 188 до 376°С либо, наоборот, расти. Различаются и химические свойства восстановленных центров. У образца CuFeOx, активного в высокотемпературной области паровой конверсии СО, в реакционной среде, содержащей помимо водорода СО и воду (in situ), при 311°С преобладают центры Cu+ [26], а у образцов CuFeOx, более активных в низкотемпературной области, в реакционной среде при 250°С – центры Cu0 [8].
В работе [28] было показано существенное уменьшение концентрации меди после восстановления в водороде. Полученные данные объяснили формированием слоя оксида железа поверх частиц металлической меди. Этот вывод можно рассматривать как гипотезу, требующую дополнительного подтверждения, поскольку прямые данные просвечивающей электронной микроскопии свидетельствуют об обратном – в восстановительной среде на поверхности оксида железа формируются частицы металлической меди [26, 27]. В целом метод РФЭС применяли для исследования исходных, окисленных при высоких температурах катализаторов, для восстановленных систем и для изучения поверхности катализаторов в реакционной среде in situ при общем давлении компонентов газовой смеси в пределах нескольких Торр.
В настоящей работе мы исследовали катализаторы именно после измерений каталитической активности при существенно большем парциальном давлении компонентов. Такие испытания приводят к заметным изменениям фазового состава (табл. 2, 3) и удельной поверхности (табл. 3) катализаторов в согласии с литературными данными [12]. Оценка активности, отнесенной к суммарной концентрации восстановленных центров Cu+(Cu0), показала, что она существенно различается для разных керамометаллических образцов. Можно полагать, что у изученных катализаторов имеются как минимум два типа высокоактивных центров в высокотемпературной паровой конверсии СО: металлическая медь, образовавшаяся из оксида меди, и кластеры [26], сформировавшиеся при восстановлении смешанного оксида СuFeOx. Свойства последних существенно зависят от взаимодействия металл–носитель, структуры и размера частиц меди [27].
Взаимосвязь способа приготовления и состава прекурсоров со свойствами оксидной пленки в керамометаллах и стабильностью активных центров
Как видно из сопоставления данных табл. 1 и 4 наиболее активный и стабильный катализатор Cu45Fe22Al33-24 после обработки в водороде характеризуется наличием восстановленных центров меди Cu+ и Cu0. При этом оксид железа не восстанавливается. Аналогичными свойствами обладает образец Cu45Fe22Al33 (табл. 4). Возможно, что такое поведение (восстановление окисленных состояний меди и отсутствие восстановления оксида железа) характерно для шпинели CuFe2O4, обнаруженной в исходных образцах Cu45Fe22Al33-24 и Cu45Fe22Al33. Однако Cu45Fe22Al33 крайне малостабилен (табл. 1). Низкую активность и стабильность имеют образцы Cu28Fe22Al50 и Cu24Fe20Al56, которые легко восстанавливаются (до Cu0 и, частично, до Fe0) (табл. 4). К сожалению, сопоставление данных об активности меди, полученных в настоящей работе, с результатами других авторов не представляется возможным. Сведений об удельной активности меди в температурном режиме реакции среднетемпературной конверсии у нас нет.
Для образцов Cu28Fe22Al50 и Cu24Fe20Al56 характерно высокое содержание алюминия, который в процессе синтеза может формировать шпинели с железом, например, Fe2AlO4 [PDF#01-089-7408]. Восстановление таких шпинелей способно приводить к их распаду с образованием металлического железа и оксида алюминия, что и наблюдается после обработки в водороде. С другой стороны, образeц Cu45Fe22Al33, имеющий низкую стабильность, получен гидротермальным окислением продуктов механохимической активации порошков Cu, Fe и Al в одну стадию [27]. В этом случае в продуктах МА помимо смешанных сплавов преобладают продукты раздельного взаимодействия алюминия с медью и железом [29]. При синтезе керамометаллов из них формируется оксидный слой, содержащий отдельно смешанные оксиды алюминия и железа и смешанные оксиды алюминия и меди. Последние преимущественно активны в низкотемпературной области, но нестабильны, поэтому разрушаются после высокотемпературных испытаний.
Образец Cu45Fe22Al33-24 был приготовлен из прекурсора, синтезированного в две стадии [21]. На первой стадии осуществляли механохимическое сплавление меди и железа. Оно было затруднено из-за различия кристаллических решеток: кубической гранецентрированной – у меди, и кубической объемно-центрированной – у железа, поэтому процесс проводили долго, в течение 90 мин, до полного исчезновения рефлексов железа в дифрактограммах. Затем полученный продукт подвергали механохимическому сплавлению с алюминием. Хотя полного взаимодействия меди и железа достичь не удалось, их взаимодействие и более равномерное перемешивание по сравнению с одностадийным синтезом было реализовано [21]. По-видимому, этот метод позволяет синтезировать относительное большее количество смешанной шпинели CuFeOx, которую отличает повышенная активность и стабильность в высокотемпературном процессе конверсии СО [30].
ЗАКЛЮЧЕНИЕ
Исследовано влияние метода приготовления и стехиометрии порошкообразного прекурсора Cu–Fe–Al на активность и стабильность керамометаллических катализаторов CuFeAlO/CuFeAl в реакции среднетемпературной паровой конверсии СО. Катализаторы представляют собой металлические частицы, покрытые оксидной оболочкой, которая скрепляет частицы в единый пористый композит. Показано, что наиболее активен и стабилен образец Cu45Fe22Al33-24 с соотношением Cu : Fe : Al = 45 : 22 : 33, синтезированный из порошкообразного прекурсора в две стадии. На первой стадии проводили механохимическое сплавление порошков железа и меди, а на второй – механохимическую обработку полученного продукта, смешанного с алюминием. Методами РФА, сканирующей электронной микроскопии, РФЭС исследованы образцы керамометаллических катализаторов до и после реакции при 400°С. Обнаружено, что активность в области температур 330–400°С определяется не только железными, но и медными активными центрами на поверхности катализаторов или их совместным действием. Двухстадийная мехактивация, по-видимому, приводит к более глубокому химическому взаимодействию компонентов – Fe и Cu, что обеспечивает бóльшую активность бесхромовых CuFeAl керамометаллических катализаторов. Полученные катализаторы имеют хороший потенциал практического применения, если будет решен вопрос повышения их стабильности. Их высокая теплопроводность и механическая прочность, развитая пористая структура, а также значительная насыпная плотность делают их очень привлекательными для использования в компактных устройствах для производства водорода и для создания структурированного катализаторного слоя.
Список литературы
Baraj E., Ciahotný K., Hlinčík T. // Fuel. 2021. V. 288. P. 119817.
Zhu M., Wachs I.E. // ACS Catal. 2016. V. 6. P. 722.
Damma D., Smirniotis P.G. // Curr. Opin. Chem. Eng. 2018. V. 21. P. 103.
Хасин А.А., Минюкова Т.П., Демешкина М.П., Баронская Н.А., Плясова Л.М., Кустова Г.Н., Зайковский В.И., Юрьева Т.М. // Кинетика и катализ. 2009. Т. 50. № 6. С. 871.
Khassin A.A., Minyukova T.P., Plyasova L.M., Filonenko G.A., Yurieva T.M. / Catalysts Based on the Nanodispersed Metastable Iron Oxyhydroxide, 2-Line Ferrihydrite. Ch. 8 in: Advances in Nanotechnology. V. 2. Eds. Z. Bartul and J. Trenor. Nova Publishers, 2010. P. 347. ISBN: 978-1-60876-199-9.
Zhu M., Wachs I.E. // Catal. Today. 2018. V. 311. P. 2.
Bao Z., Ding W., Li Q. // Int. J. Hydrog. Eng. 2012. V. 37. I. 1. P. 951.
Jeong D.-W., Jha A., Jang W.-J., Han W.-B., Roh H.-S. // Chem. Eng. J. 2015. V. 265. P. 100.
Zhu M., Yalçına Ö., Wachs I.E. // Appl. Catal. B: Env. 2018. V. 232. P. 205.
Meshkani F., Rezaei M. // Renew. Eng. 2015. V. 74. P. 588.
Jeong D.-W., Subramanian V., Shim J.-O., Jang W.-J., Seo Y.-C., Roh H.-S., Gu J.H., Lim Y.T. // Catal. Lett. 2013. V. 143. P. 438.
Na H.-S., Jeong D.-W., Jang W.-J., Shim J.-O., Roh H.-S. // Int. J. Hydrog. Eng. 2015. V. 40. I. 36. P. 122 68.
Фирсова А.А., Морозова О.С., Воробьева Г.А., Леонов А.В., Кухаренко А.И., Чолах С.О., Курмаев Э.З., Корчак В.Н. // Кинетика и катализ. 2018. Т. 59. № 2. С. 188.
Морозова О.С., Фирсова А.А., Тюленин Ю.П., Воробьева Г.А., Леонов А.В. // Кинетика и катализ. 2020. Т. 61. № 5. С. 741.
Краснякова Т.В., Юрчило С.А., Моренко В.В., Носолев И.К., Глазунова Е.В., Хасбулатов С.В., Вербенко И.А., Митченко С.А. // Кинетика и катализ. 2020. Т. 61. № 3. С. 359.
Palma V., Ruocco C., Cortese M., Martino M. // Catalysts. 2019. V. 9. P. 991.
Tikhov S.F., Minyukova T.P., Reshetnikov S.I., Valeev K.R., Vernikovskaya N.V., Salanov A.N., Cherepanova S.V., Sadykov V.A. // Chem. Eng. J. 2019. V. 374. P. 405.
Tikhov S.F., Minyukova T.P., Valeev K.R., Cherepanova S.V., Salanov A.N., Bakina O.V., Pervikov A., Yakovlev I.V., Lapina O.B., Sadykov V.A. // ACS Omega. 2020. V. 5. P. 19928.
Tikhov S.F., Minyukova T.P., Valeev K.R., Cherepanova S.V., Saraev A.A., Kaichev V.V., Aidakov E.E., Smorygo O.L., Vazhnova A.I., Mikutski V.A. // Int. J. Hydr. Energy. 2022.
Tikhov S.F., Minyukova T.P., Valeev K.R., Cherepanova S.V., Salanov A.N., Shtertser N.V., Sadykov V.A. // Mater. Chem. Phys. 2019. V. 221. P. 349.
Tikhov S.F. Valeev K.R., Cherepanova S.V., Zaikovskii V.I., Salanov A.N., Sadykov V.A., Dudina D.V., Lomovsky O.I., Petrov S.A., Smorygo O.L., Gokhale A. // Materials. 2022. V. 15. I. 6. P. 2087.
Kaichev V.V., Chesalov Y.A., Saraev A.A., Tsapina A.M. // J. Phys. Chem. C. 2019. V. 123. P. 19668.
Dudina D.V., Lomovsky O.I., Valeev K.R., Tikhov S.F., Boldyreva N.N., Salanov A.N., Cherepanova S.V., Zaikovskii V.I., Andreev A.S., Lapina O.B., Sadykov V.A. // J. Alloys Comp. 2015. V. 629 P. 343.
Fedorov A.V., Saraev A.A., Kremneva A.M., Selivanova A.V., Vorokhta M., Šmíd B., Bulavchenko O.A., Yakovlev V.A., Kaichev V.V. // ChemCatChem 2020. V. 12. № 19. P. 4911.
McIntyre N.S., Zetaruk D.G. // Anal. Chem. 1977. V. 49. P. 1521.
Hou M., Ma L., Ma H., Yue M. // J. Mater. Sci. 2017. V. 53. P. 1065.
Ma L., Ma H., Han D., Qiu M., Guan Y., Hu Y. // Catalysts. 2018. V. 8. P. 415.
Ye Y., Wang L., Zhang, S., Zhu Y., Shan F., Tao F. // Chem. Commun. 2013. V. 49. P. 4385.
Tikhov S.F., Valeev K.R., Salanov A.N., Cherepanova S.V., Boldyreva N.N., Zaikovskii V.I., Sadykov V.A., Dudina D.V., Lomovsky O.I., Romanenkov V.E., Pyatsyushik E.E. // J. Alloy. Comp. 2018. V. 736. P. 289.
Kameoka S., Tanabe T., Tsai A.P. // Appl. Catal. A: Gen. 2010. V. 375. P. 16.
Дополнительные материалы отсутствуют.
Инструменты
Кинетика и катализ