Коллоидный журнал, 2019, T. 81, № 6, стр. 742-749
Формирование структуры, морфологии и фракционного состава композиционных порошков “Al–2B” в процессе механоактивации
А. И. Малкин 1, *, В. А. Клюев 1, А. А. Рязанцева 1, В. И. Савенко 1
1 Институт физической химии и электрохимии им. А.Н. Фрумкина РАН
119071 Москва, Ленинский проспект, 31, Россия
* E-mail: mlkn@list.ru
Поступила в редакцию 10.06.2019
После доработки 24.06.2019
Принята к публикации 25.06.2019
Аннотация
Исследована эволюция структурно-морфологических характеристик и фракционного состава композиционного порошка “Al–2B” в процессе синтеза методом механического легирования. Получены данные о величине внутренних напряжений, удельной площади межфазной поверхности и статистических характеристиках фракционного состава в зависимости от продолжительности обработки порошковой смеси. Обсуждаются механизмы формирования состава и структуры композиционного порошка.
ВВЕДЕНИЕ
Одним из перспективных направлений в области создания новых энергетических материалов является использование в их составе борсодержащих наполнителей, в частности, композиционных порошков системы “Al–2B”, получаемых методом самораспространяющегося высокотемпературного синтеза (СВС-композиции). По теплоте сгорания в расчете на единицу массы и объема такие композиции соответственно не уступают и значительно превосходят углеводородные топлива. Однако значимый эффект от применения композиционных порошков “Al–2B” может быть достигнут лишь при рациональных кинетических параметрах воспламенения и горения. Последние существенно зависят от фракционного состава и структурно-морфологических характеристик порошков, таких, как распределение композиционных частиц по размерам, форма и состояние поверхности частиц, степень однородности состава, удельная площадь межфазной поверхности между компонентами.
Наиболее простой и доступный метод изготовления композиционных порошков “Al–2B” основан на совместной механической обработке компонентов в охлаждаемых шаровых мельницах-активаторах [1–3]. Характеристики конечного продукта определяются технологическим режимом – интенсивностью и продолжительностью обработки, интенсивностью охлаждения, составом размольной среды, размерами частиц и физико-механическими свойствами исходных порошков.
Качественная картина синтеза является универсальной для процессов механического легирования, используемых при изготовлении дисперсно-упрочненных композиционных материалов [3]. В ходе совместной механоактивации происходит интенсивное внедрение твердых субмикронных частиц бора в приповерхностные слои относительно крупных и пластичных частиц алюминия и, в дальнейшем, композиционных частиц. Одновременно протекают два конкурирующих процесса – разрушение и “холодная сварка” композиционных частиц. Следствием чередования этих процессов является гомогенизация состава частиц: по мере увеличения продолжительности обработки распределение компонентов в их объеме становится все более однородным. В итоге формируется композиционный порошок с максимально возможной величиной удельной площади межфазной поверхности между компонентами, причем при механоактивации в защитной размольной среде межфазная поверхность образуется в очищенном от оксидных пленок состоянии. Многократное интенсивное механическое воздействие на порошковую смесь приводит к формированию высокодефектной, далекой от равновесия атомной структуры композиционных частиц.
Хотя метод механического синтеза композиционных порошков – механическое легирование – много лет применяется в технологиях порошковой металлургии, для создания композиционных энергетических материалов он стал использоваться сравнительно недавно. Специфика синтеза энергетических композитов состоит в необходимости выявления режимов обработки, исключающих появление заметного количества нежелательных продуктов химических превращений в процессе изготовления и, вместе с тем, обеспечивающих требуемые физико-химические свойства и кинетические характеристики превращений конечного продукта, включая его взаимодействие с окислительными средами.
Следует отметить, что исследование влияния механоактивации на кинетику превращений энергетических конденсированных систем представляет собой быстро развивающееся направление химической физики горения и взрыва. К настоящему времени опубликовано большое количество оригинальных работ и обзоров, посвященных исследованию свойств механоактивированных СВС-композиций [4, 5], пиротехнических [6] и взрывчатых [7, 8] составов. Установлен ряд общих закономерностей, таких, как резкое снижение температуры самовоспламенения и повышение полноты превращения. Широко обсуждаются гипотетические механизмы влияния механоактивации на кинетику превращений, связь характеристик воспламенения и горения с надатомной структурой материалов [5, 9]. Тем не менее, существующий уровень понимания этих механизмов нельзя признать удовлетворительным. Представления о зависимости “технология–структура–свойства” механоактивированных энергетических материалов ограничиваются преимущественно общими соображениями и нуждаются в экспериментальном обосновании.
Применительно к рассматриваемой в настоящей работе СВС-композиции “Al–2B” в первую очередь необходимо установить характеристики порошковой смеси в зависимости от режима обработки и сформулировать детальный количественный сценарий формирования композиционного порошка. Детализация этого процесса путем выявления количественных характеристик эволюции состава и структуры композиционного порошка представляет не только академический интерес. Практическая сторона вопроса заключается в обосновании рациональных параметров технологии синтеза. Технология должна обеспечивать отсутствие в конечном продукте заметного количества боридов алюминия и продуктов реакции с компонентами размольной среды, минимальное содержание свободного бора и требуемый фракционный состав порошка. В связи с этим возникает проблема управления характеристиками продукта за счет выбора технологических параметров. Ниже представлены результаты исследования влияния продолжительности механоактивации на структуру, морфологию и фракционный состав композиционных порошков “Al–2B”.
МАТЕРИАЛЫ И МЕТОДЫ
В экспериментах использовались порошки алюминия марки АСД-1 и аморфного бора марки Б-99В. Обработка порошковых смесей осуществлялась в лабораторной планетарно-центробежной мельнице-активаторе с водяным охлаждением АГО-2У при загрузке смеси 10 г, шаровой загрузке – 100 г шаров диаметром 6 мм из сплава ШХ-15, скорости вращения барабанов 1061.5 об./мин. Продолжительность обработки составляла от 3 до 21 мин. В качестве размольной среды использовался химически чистый гексан. Смешение порошков алюминия и бора в соотношении 55/45 (мас. %) осуществлялось в течение 20 мин в вибромельнице без шаровой загрузки.
Структурно-морфологические исследования проводились методами электронной микроскопии, рентгеноспектрального микроанализа и рентгеновской дифрактометрии. Использовался электронный микроскоп JSM-6460LA с приставкой для энергодисперсионного рентгеноспектрального микроанализа (EDAX). Энергия первичного электронного пучка составляла 15 кэВ, ток на образце – 1 нА, угол между поверхностью образца и детектором – 40°. При определении объемной концентрации элементов использовалась программа ZAF-коррекции. Исследовались образцы порошковых проб двух типов: таблетки толщиной около 1 мм, изготовленные на ручном прессе, и россыпь частиц на проводящей липкой ленте.
Для установления характера распределения частиц бора в объеме композиционных частиц и количественной оценки содержания бора в них изготавливались специальные образцы: композиционные порошки смешивались с порошком полимера, смесь прессовалась и отверждалась при повышенной температуре, после чего проводилась шлифовка и травление аншлифов потоком ионов аргона.
Дифрактометрические измерения проводились на рентгеновском дифрактометре EMPYREAN (Cu-Kα-излучение) в диапазоне углов 5°–140°. При расчетах учитывались две длины волны, 1.5406 и 1.5444 Å, с соотношением интенсивностей в спектре 2 : 1. Для всех дифрактограмм проводилось полнопрофильное уточнение результатов их расчета методом Ритвельда.
Фракционный состав порошков определялся на жидкофазном лазерном дифрактометрическом анализаторе высокого разрешения Microtrac S3500. Для устранения слабосвязанных агрегатов порошковые пробы подвергались ультразвуковому диспергированию в течение 3 мин.
Перед проведением серийных экспериментов было выполнено исследование морфологии, фракционного и химического состава порошков алюминия и бора в состоянии поставки и тех же порошков, подвергнутых механоактивации в среде гексана.
Форма частиц алюминиевого порошка АСД-1 близка к сферической. Средний размер частиц, вычисленный по распределению их относительного числа, составляет 3.89 мкм, удельная площадь поверхности – 0.33 м2/г, 90% массы порошка сосредоточено в частицах размером от 2.4 до 18.0 мкм. Содержание основного вещества – 99.5%, характерная толщина оксидного слоя на поверхности частиц принадлежит интервалу 12– 15 нм.
Исходный порошок аморфного бора Б-99В содержит изометричные частицы неправильной формы. Среднечисленный размер частиц равен 0.56 мкм, удельная поверхность, вычисленная в рамках модели сферических частиц, составляет 1.19 м2/г, реальная удельная поверхность не превышает 2.5 м2/г. Содержание основного вещества – не менее 99%. Частицы исходного порошка состоят из наноразмерных кристаллитов с характерным размером около 5 нм. Они содержат около 0.07% хлора, незначительное количество металлических примесей и кристаллического гидроксида бора. Основная масса порошка сосредоточена в частицах размером от 0.2 до 10 мкм, причем крупные частицы представляют собой хорошо различимые агрегаты.
ЭВОЛЮЦИЯ ФРАКЦИОННОГО СОСТАВА И МОРФОЛОГИИ
На рис. 1 представлено распределение относительного объема, занимаемого частицами порошка, по размеру частиц. По мере увеличения продолжительности обработки изначально бимодальное распределение, обусловленное большим различием в размерах частиц алюминия и бора, трансформируется в одномодальное. Одновременно происходит значительное укрупнение частиц. Субмикронная фракция, содержащая преимущественно свободный, не внедренный в алюминий, бор и составляющая в исходной смеси около 6% общего объема частиц, практически полностью исчезает при продолжительности обработки более 7 мин. С другой стороны, в порошковой системе появляется заметное количество крупных частиц, отсутствовавших в исходной смеси.
Рис. 1.
Эволюция распределения относительного объема по размеру частиц при времени механоактивации 3 (а), 9 (б), 21 мин (в).
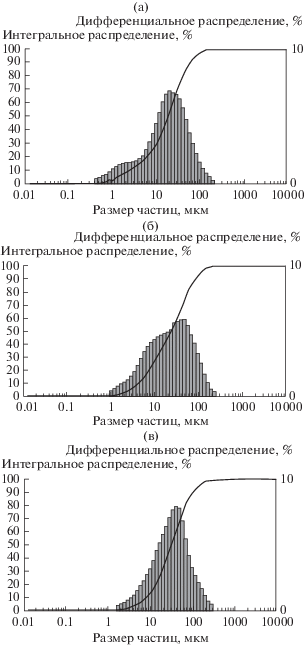
Кинетику укрупнения иллюстрируют представленные на рис. 2, 3 основные статистические характеристики порошковой системы в зависимости от времени обработки. Как видно из приведенных зависимостей, средние размеры частиц, вычисленные по распределениям относительного объема, площади поверхности и числа частиц, ширина и медиана распределения относительного объема на начальной стадии механоактивации, при продолжительности обработки 3–7 мин, быстро возрастают. При этом удельная площадь поверхности порошка, вычисленная в рамках модели сферических частиц, резко снижается.
Рис. 2.
Зависимость статистических средних и медианы от продолжительности обработки: 1 – среднеобъемный, 2 – среднеповерхностный, 3 – среднечисленный размер частиц, 4 – медиана распределения относительного объема.
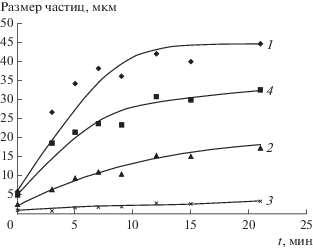
Рис. 3.
Зависимость удельной площади поверхности композиционного порошка от продолжительности обработки.
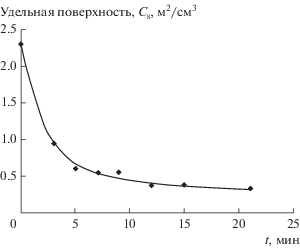
Процесс синтеза композиционного порошка имеет ярко выраженный двухстадийный характер. С увеличением его продолжительности процесс укрупнения тормозится, временной масштаб эволюции фракционного состава резко возрастает. На второй стадии изменение основных статистических параметров фракционного состава оказывается немонотонным. Немонотонная зависимость от времени механической обработки имеет место не только для средних значений, но и для стандартных отклонений и медиан распределений относительного объема, площади поверхности и числа частиц композиционного порошка.
Результаты морфологических исследований также свидетельствуют о двухстадийности процес-са синтеза. При продолжительности обработки 3–7 мин значительную объемную долю порошковой смеси составляют частицы анизометричной пластинчатой формы. С увеличением продолжительности доля таких частиц резко снижается. При обработке в течение 9 мин и более основной объем порошковой системы представлен изометричными частицами с остроугольным габитусом.
Для прояснения причин двухстадийного характера процесса выполнены исследования эволюции фракционного состава и морфологии частиц индивидуального порошка алюминия. На рис. 4 представлены электронные микрофотографии, иллюстрирующие качественное различие формы и размеров частиц чистого алюминия и системы “Al–2B” после 9 мин обработки. Порошок чистого алюминия содержит крупные частицы пластинчатой формы, тогда как частицы композиционного порошка являются изометричными и имеют многократно меньшие размеры. С увеличением продолжительности механоактивации различие в форме и размерах становится еще больше.
ЭВОЛЮЦИЯ СОСТАВА И СТРУКТУРЫ КОМПОЗИЦИОННЫХ ЧАСТИЦ
Результаты рентгеноспектрального микроанализа прессованных образцов в зависимости от продолжительности обработки представлены на рис. 5.
Рис. 5.
Результаты рентгеноспектрального микроанализа прессованных образцов порошковой смеси в зависимости от продолжительности обработки.
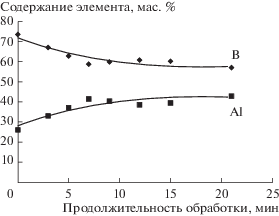
Необходимо пояснить, что полученные на прессованных образцах формальные значения относительного содержания компонентов ни в коей мере не соответствуют усредненным по объему порошкового образца величинам, вне зависимости от времени обработки характеризуемым их стехиометрическим массовым соотношением 55% Al/45% B для всех образцов. Приведенные зависимости в действительности отражают кинетику внедрения бора в алюминий и гомогенизацию состава частиц композиционного порошка. На начальной стадии обработки система содержит большое количество свободного бора, порошок которого имеет низкую насыпную плотность, занимает большой относительный объем и обладает значительно меньшим коэффициентом поглощения рентгеновского излучения, чем алюминий. В результате усредненное по поверхности аншлифа содержание бора значительно превышает реальное. С увеличением продолжительности обработки количество свободного бора снижается, так что процентное содержание бора в объеме композиционных частиц приближается к стехиометрическому.
Содержание оксидов в обработанных порошковых смесях оценивалось по величине атомной доли кислорода. Полученные значения оказались несколько выше, чем в исходных порошках. Последнее объясняется окислением в процессе приготовления образцов для аналитических исследований и обусловлено повышенной химической активностью механоактивированных алюминия и бора. Оксидные фазы, по данным рентгеновской дифрактометрии, находятся в рентгеноаморфном состоянии. Однако при продолжительности обработки 5–7 мин порошкограммы содержат небольшой диффузный пик при угле 2θ = 33.05°, отвечающий фазе Fe2O3. Появление незначительного количества этой фазы связано с износом мелющих тел и стенок барабана активатора.
Из результатов дифрактометрических исследований следует также вывод об отсутствии в составе композиционных порошков заметного количества кристаллических боридов алюминия, карбидных и нитридных фаз. Тем не менее, нельзя исключить возможность незначительного содержания таких фаз в аморфизованном состоянии. Отметим также, что узкий и малоинтенсивный пик малой при угле 2θ = 28.10°, наблюдавшийся на порошкограмме исходной смеси и отвечающий кристаллическому гидроксиду бора, полностью исчезает уже при минимальной продолжительности обработки 3 мин.
Частицы бора, как исходного, так и в соста-ве композиционных порошков, находятся в аморфном состоянии. Отвечающие кристаллическому бору рефлексы на всех порошкограммах отсутствуют. Зависимости основных характеристик микроструктуры алюминиевой составляющей композиционных порошков от продолжительности обработки представлены в табл. 1. На начальной стадии обработки размеры области когерентного рассеяния (ОКР) и величина постоянной решетки резко снижаются, а микродеформации 2-го рода, характеризующие напряжения в субзернах и блоках мозаики, возрастают. С увеличением продолжительности изменение параметров микроструктуры приобретает осциллирующий характер. Корреляция во временной зависимости параметров сохраняется.
Таблица 1.
Характеристики микроструктуры алюминиевой матрицы в зависимости от продолжительности обработки
№ | Продолжительность обработки, мин | Размер ОКР, мкм | Постоянная решетки, Å* | Микродеформация, %* |
---|---|---|---|---|
1 | 0 | 0.1150 | 4.0494 (1) | 0.03 (1) |
2 | 3 | 0.1085 | 4.0487 (4) | 0.16 (4) |
3 | 5 | 0.0395 | 4.0451 (2) | 0.12 (3) |
4 | 7 | 0.0392 | 4.0441 (2) | 0.13 (2) |
5 | 9 | 0.0619 | 4.0475 (5) | 0.22 (7) |
6 | 12 | 0.0848 | 4.0474 (5) | 0.26 (7) |
7 | 15 | 0.0502 | 4.0470 (6) | 0.22 (5) |
8 | 21 | 0.0434 | 4.0482 (4) | 0.17 (1) |
ОБСУЖДЕНИЕ РЕЗУЛЬТАТОВ
Полученные результаты позволяют сформулировать количественную картину формирования фракционного состава, структуры и морфологии композиционного порошка “Al–2B”. Кинетика изменения компонентного и фракционного состава композиционного порошка определяется соотношением скоростей трех взаимозависимых процессов: внедрением бора в алюминий, разрушением частиц и их агрегацией за счет “холодной сварки” частиц малого размера. На начальной стадии, при продолжительности обработки 3–7 мин, преобладает укрупнение частиц за счет внедрения высокодисперсного бора в алюминий и “холодной сварки”. Плотность распределения относительного объема по размеру частиц сдвигается вправо (рис. 1).
С возрастанием продолжительности и увеличением доли крупных фракций процесс укрупнения, как видно на рис. 2, 3, тормозится. Стабилизация содержания бора в объеме композиционных частиц и основных статистических характеристик фракционного состава происходит практически одновременно. При этом частицы анизометричной пластинчатой формы полностью исчезают. Морфология частиц композиционного порошка свидетельствует о квазихрупком характере разрушения. Сравнение морфологии механоактивированных частиц чистого алюминия и композиционного порошка позволяет сделать вывод, что причина заключается в насыщении композиционных частиц бором.
Увеличение содержания бора в композиционных частицах влечет за собой повышение предела текучести – дисперсионное упрочнение, обусловленное увеличением концентрации барьеров, препятствующих скольжению дислокаций. Для грубой качественной оценки можно воспользоваться соотношением [10]
(1)
$\Delta {{{\sigma }}_{{0.2}}} \cong {{1.7Gb} \mathord{\left/ {\vphantom {{1.7Gb} {\sqrt {{\lambda }d} }}} \right. \kern-0em} {\sqrt {{\lambda }d} }},$С другой стороны, увеличение содержания бора должно приводить к снижению предела прочности композиционного материала из-за низкой прочности адгезионных контактов алюминий–бор, обусловленной наличием оксидной пленки на поверхности частиц бора, а также адсорбцией на межфазной поверхности компонентов рабочей среды. В пренебрежении адгезией предел прочности можно оценить по соотношению [11]
(2)
${{\sigma }_{{\text{в}}}} \cong {{\sigma }_{{\text{m}}}}\left( {1{\text{ }}--\beta {{\alpha }^{{{2 \mathord{\left/ {\vphantom {2 3}} \right. \kern-0em} 3}}}}} \right),$Эволюция блочной структуры алюминиевой составляющей композиционного порошка определяется конкуренцией процессов фрагментации зерен и динамической рекристаллизации. На начальной стадии обработки резкое снижение размеров ОКР сопряжено с появлением в объеме частиц больших сжимающих напряжений, проявляющихся в снижении постоянной решетки. Максимум сжимающих напряжений реализуется при продолжительности процесса механоактивации, равной 7 мин, и минимальном размере ОКР. Оценка максимального напряжения в предположении, что материал находятся в состоянии равномерного всестороннего сжатия, дает величину около 240 МПа. На стадии немонотонного изменения параметров структуры, при продолжительности обработки 9–21 мин, напряжения изменяются в интервале 50–100 МПа, что отвечает удельной энергии упругой деформации 12.5–25.0 Дж/г.
В избыточную свободную энергию частиц композиционного порошка вносят вклад также дефекты в объеме кристаллитов Al, межфазные и межкристаллитные границы. Вкладом дефектов в объеме наноразмерных кристаллитов обычно можно пренебречь, поскольку высокие напряжения в процессе формирования блочной структуры приводят к выдавливанию подвижных дефектов в межкристаллитные границы. Применительно к композиционным порошкам “Al–2B” это подтверждается относительно низкими значениями фактора Дебая–Валлера, характеризующего среднеквадратичное смещение атомов кристаллической решетки алюминия из положения равновесия.
Для оценки максимальных значений удельной энергии межфазных границ в частицах композита можно, в пренебрежении адгезией, использовать величину суммы поверхностных энергий алюминия и бора. При среднем размере частиц бора 0.5 мкм, что согласуется с данными электронной микроскопии, это приводит к величине порядка 5 Дж/г при продолжительности обработки более 7 мин. При малом содержании свободного бора в системе вклад энергии межфазных границ должен быть практически постоянным.
Полученные экспериментальные данные не позволяют дать непосредственную оценку свободной энергии межкристаллитных границ. Можно, однако, оценить величину поверхностных напряжений – механическое поверхностное натяжение [13]. Положим, что алюминиевая матрица имеет регулярную ячеистую структуру, каждая ячейка которой содержит кристаллит размером, равным размеру ОКР, окруженный тонким слоем зернограничной фазы. Из условия механического равновесия следует, что нормальные напряжения на границе ячейки равны нулю, а напряжения в плоскости границы непрерывны. В рамках такой модельной схемы давление в кристаллите и поверхностное напряжение связаны формулой Лапласа. Соответствующие оценки дают максимальное значение поверхностных напряжений 2.3 Н/м при 7-минутной обработке, значения в интервале 1.3–1.8 Н/м при обработке в течение 9–15 мин и 0.8 Н/м при времени обработки 21 мин, причем указанная временнáя зависимость не является монотонной. По-видимому, высокий уровень поверхностных напряжений при промежуточных временах обработки обусловлен главным образом неравновесным состоянием границ. Релаксация напряжений с увеличением времени связана со снижением степени неравновесности в процессе динамической рекристаллизации.
С другой стороны, удельная площадь поверхности межкристаллитных границ, достигающая максимума в 30 м2/г при обработке продолжительностью t = 7 мин, принимает минимальное значение 14 м2/г при t = 12 мин и вновь возрастает до 28 м2/г при t = 21 мин. Таким образом, первая стадия завершается формированием предельно измельченной, сильно неравновесной блочной структуры алюминиевой компоненты. В дальнейшем площадь границ, как и поверхностные напряжения, изменяется немонотонно. При максимальной продолжительности обработки измельчение структуры сопряжено со снижением поверхностных напряжений, что можно объяснить возрастанием доли низкоэнергетичных малоугловых границ в процессе вторичной фрагментации зерен.
Следует также отметить, что значения свободной энергии большеугловых границ зерен в поликристаллах алюминия обычно принадлежат интервалу 0.5–0.7 Дж/м2 [14], так что вклад границ в общую избыточную энергию композиционных частиц не превышает 20 Дж/г. При этом доля атомов в зернограничной фазе весьма велика: при ширине границ 1 нм и характерной для большеугловых границ зерен в поликристаллах алюминия величине относительного свободного объема 6% [15] она составляет несколько процентов.
Приведенные оценки не могут претендовать на точное количественное описание эволюции механических свойств и структуры композиционных частиц. Они лишь позволяют прояснить причины и взаимосвязь процессов, в результате которых формируется внутренняя структура частиц и фракционный состав композиционного порошка. Что касается энергетических характеристик, то полная избыточная энергия порошка на два порядка меньше теплоты реакции между алюминием и бором и не может играть заметной роли в энергетическом балансе превращения. Однако величина избыточной энергии дефектной структуры является показателем повышения химической активности и изменения теплофизических характеристик алюминиевой компоненты. В частности, оценка температуры плавления алюминия в составе композиционного порошка дает ее снижение более чем на 100 К.
ЗАКЛЮЧЕНИЕ
Методом механического легирования синтезированы композиционные порошки СВС состава “Al–2B”. Исследованы структурно-морфологические характеристики и фракционный состав порошковой смеси в зависимости от продолжительности обработки. Установлено, что процесс синтеза имеет ярко выраженный двухстадийный характер. На первой стадии происходит интенсивное внедрение твердых высокодисперсных частиц бора в алюминий, укрупнение частиц и измельчение блочной структуры алюминиевой компоненты. В дальнейшем основные статистические параметры фракционного состава, параметры блочной структуры и связанная с ними избыточная энергия композиционного порошка изменяются немонотонно.
Фракционный состав формируется в результате установления баланса между скоростями дробления и “холодной сварки”. Соотношение скоростей этих процессов контролируется степенью насыщения частиц бором и, в меньшей степени, параметрами блочной структуры. В свою очередь, эволюция блочной структуры обусловлена конкуренцией процессов фрагментации зерен и динамической рекристаллизации, скорости которых также зависят от содержания бора и размера кристаллитов. На начальной стадии уменьшение размера ОКР сопряжено с возникновением в объеме кристаллитов больших сжимающих напряжений. На второй стадии напряжения релаксируют, но остаются весьма значительными. Оценки величины избыточной энергии свидетельствуют о возможности значительного увеличения реакционной способности композиционного порошка и снижения температуры плавления алюминиевой матрицы.
Список литературы
Gilman P.S., Benjamin J.S. // Ann. Rev. Mater. Sci. 1983. V. 13. P. 279.
Gilman P.S., Nix W.D. // Met. Trans. A 1983. V. 12. P. 813.
Кузьмич Ю.В., Колесникова И.Г., Серба В.И., Фрейдин Б.М. Механическое легирование. М.: Наука, 2005.
Bernard F., Gaffet E. // Int. J. SHS. 2001. V. 10. P. 109.
Рогачев А.С., Мукасьян А.С. Горение для синтеза материалов: введение в структурную макрокинетику. М.: Физматлит, 2013.
Reddy B.S.B., Das S. // J. Mater. Sci. 2007. V. 42. P. 9366.
Долгобородов А.Ю., Махов М.Н., Колбанев И.В., Стрелецкий А.Н., Фортов В.Е. // Письма в ЖЭТФ. 2005. Т. 81. С. 395.
Долгобородов А.Ю., Махов М.Н., Стрелецкий А.Н., Колбанев И.В., Гогуля М.Ф., Фортов В.Е. // Химическая физика. 2004. Т. 33. № 9. С. 85.
Рогачев А.С., Кочетов Н.А., Курбаткина В.В., Левашов Б.А., Гримчук П.С., Рабинович О.С., Сачкова В.Н., Бернар Ф. // Физика горения и взрыва. 2006. Т. 42. № 4. С. 61.
Штремель М.А. Прочность сплавов. М.: МИСИС, 1999.
Баженов С.Л., Берлин А.А., Кульков А.А., Ошмян В.Г. Полимерные композиционные материалы. Прочность и технология. Долгопрудный: Издательский дом “Интеллект”, 2010.
Физические величины. Справочник / Под ред. Григорьева И.С., Мейлихова Е.З. М.: Энергоатомиздат, 1991.
Русанов А.И. Термодинамические основы механохимии. СПб.: Наука, 2006.
Hasson G., Gou C. // Scr. Met. 1971. V. 5. P. 889.
Чувильдеев В.Н. Неравновесные границы зерен в металлах. Теория и приложения. М.: Физматлит, 2004.
Дополнительные материалы отсутствуют.
Инструменты
Коллоидный журнал