Коллоидный журнал, 2021, T. 83, № 2, стр. 242-248
Стабилизация мезопористой структуры полиэтилентерефталата, деформированного по механизму Крейзинга
Л. М. Ярышева 1, *, А. К. Беркович 1, А. Ю. Ярышева 1, М. С. Аржаков 1, О. В. Аржакова 1, А. Л. Волынский 1
1 Московский государственный университет им. М.В. Ломоносова, химический факультет
119991 Москва, Ленинские горы 1–3, Россия
* E-mail: yarishev@gmail.com
Поступила в редакцию 30.09.2020
После доработки 05.10.2020
Принята к публикации 09.10.2020
Аннотация
Исследована деформация пленок аморфного стеклообразного полиэтилентерефталата (ПЭТФ) в жидких адсорбционно-активных средах (ААС) по механизму крейзинга. Показано, что крейзинг является эффективным способом формирования в полимере высокодисперсной мезопористой структуры. Разработан способ стабилизации структуры ПЭТФ, деформированного по механизму крейзинга, путем отжига в присутствии ААС в условиях, исключающих усадку. Рассмотрено влияние условий деформирования и отжига на пористость и паропроницаемость полученных материалов на основе ПЭТФ. Установлено, что стабильность сформированной мезопористой структуры ПЭТФ после отжига пленок в ААС связана с кристаллизацией полимера. Сформированная структура характеризуется анизотропией поверхностного рельефа и смачивания.
ВВЕДЕНИЕ
В жидких адсорбционно-активных средах (ААС) деформация аморфных стеклообразных и кристаллических полимеров происходит по механизму крейзинга и рассматривается как частный случай проявления эффекта Ребиндера [1–4]. Особенность данного вида деформации связана с формированием в полимере высокодисперсной фибриллярно-пористой структуры с мезопорами [2–4]. При растяжении полимеров в ААС деформирование может осуществляться по классическому или делокализованному (межкристаллитному) механизмам крейзинга. Характерный для аморфных стеклообразных полимеров классический крейзинг сопровождается возникновением и развитием в полимере локальных зон неупругой деформации (крейзов), чередующихся с участками недеформированного полимера. Делокализованный крейзинг реализуется в ААС для частично кристаллических полимеров. Формирование пористости при деформировании полимеров по механизму межкристаллитного крейзинга происходит в пространстве между ламелями, и поры однородно распределены по всему объему полимера.
Таким образом, крейзинг можно рассматривать как универсальный метод получения мезопористых материалов, которые могут быть использованы в качестве мембран, сорбентов и матриц нанокомпозиционных материалов [3]. Деформирование полимеров в жидких ААС, содержащих низко- или высокомолекулярные соединения, позволяет получать нанокомпозиты и полимер-полимерные смеси с высоким уровнем дисперсности компонентов и новыми функциональными свойствами, например, негорючестью, паропроницаемостью, ионной или электронной проводимостью, бактерицидными и фунгицидными свойствами, пролонгированным выделением полезной добавки и т.д. [5–15].
Преимущество использования крейзинга в качестве метода получения пористых материалов состоит в том, что морфологию и параметры пористой структуры можно регулировать за счет изменения природы полимера, ААС или условий деформирования (температуры, скорости и степени вытяжки). Однако высокодисперсная фибриллярно-пористая структура крейзов, как типичная коллоидная система с высокой удельной поверхностью, является термодинамически нестабильной и подвержена коагуляционным процессам [3]. Особенно заметные изменения в структуре деформированных полимеров происходят при релаксации напряжения, что проявляется в виде низкотемпературной усадки вплоть до полного “залечивания” пористости [3, 4, 16, 17]. Вследствие этого для получения и последующего применения мезопористых материалов на основе полимеров, деформированных по механизму крейзинга, актуальными являются исследования, направленные на разработку подходов к стабилизации сформированной структуры.
В качестве объекта исследования выбран аморфный стеклообразный полиэтилентерефталат (ПЭТФ), деформирование которого в ААС осуществляется по механизму классического крейзинга. Структура ПЭТФ, формирующаяся в процессе вытяжки в ААС, охарактеризована достаточно подробно [3, 18–21], однако известны лишь единичные исследования, направленные на поиск способов стабилизации структуры ПЭТФ, деформированного по механизму крейзинга, после удаления ААС. В работе [22] для стабилизации структуры ПЭТФ и устранения напряжений, связанных с действием капиллярных сил в результате резкого изменения межфазной поверхностной энергии при удалении среды, осуществляли замену ААС на воду, которую затем удаляли с помощью лиофильной сушки. Однако после лиофильной сушки наблюдали значительную усадку деформированных образцов и уменьшение пористости ПЭТФ. В работе [23] разрабатывался метод, основанный на регенерации пористой структуры ПЭТФ после вытяжки в ААС путем повторной вытяжки на воздухе, но эффективность его также оказалась невысокой.
Конечной стадией получения пористых материалов, так называемых хард-эластиков, при растяжении частично кристаллических полимеров на воздухе является их отжиг для фиксирования размеров деформированных образцов [24]. Этот подход был использован для стабилизации пористой структуры полиэтилена высокой плотности со специфической слоевой ламеллярной структурой, деформированного в ААС по механизму межкристаллитного крейзинга [7, 25].
Целью данной работы было исследование деформации пленок аморфного стеклообразного ПЭТФ в ААС по механизму крейзинга и изучение эффективности отжига как способа стабилизации сформированной пористой структуры этого полимера.
ЭКСПЕРИМЕНТАЛЬНАЯ ЧАСТЬ
В качестве объекта исследования были выбраны пленки аморфного стеклообразного ПЭТФ толщиной 100 мкм. В качестве ААС для деформирования ПЭТФ использовали изопропиловый спирт (ИЗП) и 40%-ный (по объему) водный раствор ИЗП.
Вытяжку ПЭТФ осуществляли при температуре 20°C со скоростью 5 мм/мин на динамометре Instron-1122. Размеры рабочей части пленок составляли 20 × 40 мм2.
Пористость пленок в процессе вытяжки в присутствии ААС (W) определяли по изменению геометрических размеров по формуле W = (Vt − V0)/V0, где V0 − исходный объем образца, Vt − объем образца после вытяжки. Пористость сухих образцов (Wc) после удаления ААС определяли гравиметрическим методом по привесу пленок после выдерживания их в полипропиленгликоле (ППГ) с молекулярной массой 400 Да и вычисляли по формуле Wc = (Vt − V0)/V0 = = (mt − m0)d/m0dППГ, где m0 – масса исходного образца, mt − масса образца с ППГ, d – плотность ПЭТФ (1.32 г/см3) и dППГ – плотность ППГ (1.01 г/см3).
Паропроницаемость пленок измеряли в ячейках, на дно которых наливали воду для создания 100%-ной влажности; ячейку помещали в эксикатор с хлористым кальцием для создания нулевой влажности, испарение воды происходило через исследуемую пленку. Коэффициент паропроницаемости определяли как K = (m0 − mt)/St, где m0 и mt – начальная масса ячейки с образцом и ее масса по истечении времени t, S – площадь образца.
Теплофизические свойства ПЭТФ исследовали методом дифференциальной сканирующей калориметрии (ДСК) с помощью калориметра DSC 402 Phoenix (Netzsch) в инертной атмосфере. Масса исследуемых образцов составляла 2−3 мг, скорость нагревания 10 град/мин.
Исследование структуры ПЭТФ проведено методом сканирующей электронной микроскопии (СЭМ) на приборе Hitachi S-520.
РЕЗУЛЬТАТЫ И ИХ ОБСУЖДЕНИЕ
Об эффективности влияния ААС на способность ПЭТФ к деформации по механизму крейзинга можно судить по изменению механических свойств полимера. На рис. 1 представлены динамометрические кривые растяжения пленок ПЭТФ на воздухе (1), в ИЗП (2) и в 40%-ном водном растворе ИЗП (3). По сравнению с деформированием полимера на воздухе вытяжка ПЭТФ в ИЗП и в его водном растворе происходит при меньшем уровне напряжения без изменения модуля упругости, что свидетельствует об отсутствии пластификации ПЭТФ в среде ИЗП.
При одинаковых условиях деформирования уровень снижения напряжения зависит от природы ААС и определяет эффективность крейзинга. Вода является инертной средой по отношению к ПЭТФ. Растяжение полимера в воде происходит аналогично растяжению на воздухе и не сопровождается образованием крейзов, поэтому по сравнению с растяжением в ИЗП вытяжка ПЭТФ в водно-спиртовом растворе происходит при более высоком уровне напряжения.
В отсутствие напряжения ПЭТФ практически не набухает в алифатических спиртах и водно-спиртовых растворах. Влияние таких жидкостей на механическое поведение ПЭТФ связано с понижением поверхностной энергии [3, 4].
На рис. 2 представлено СЭМ-изображение ПЭТФ, деформированного в ИЗП по механизму крейзинга. Как уже упоминалось выше, характерный для аморфных стеклообразных полимеров классический крейзинг сопровождается возникновением и развитием в полимере локальных зон неупругой деформации (крейзов). Однако после удаления ААС наноразмерная фибриллярно-пористая структура крейзов методом СЭМ не разрешается, и СЭМ-изображения дают только общее представление о структуре ПЭТФ, деформированного по механизму крейзинга. Видно, что наряду с крейзами (область 1 на рис. 2) в полимере присутствуют недеформированные области (2 на рис. 2). С увеличением степени вытяжки ширина крейзов увеличивается, в то время как протяженность областей недеформированного ПЭТФ уменьшается вплоть до полного перехода полимерного материала в крейзы.
Рис. 2.
СЭМ-изображение скола образца ПЭТФ, деформированного в ИЗП на 100%, направление вытяжки показано стрелкой; цифрой 1 на изображении указан участок с крейзами, цифрой 2 – участок блочного недеформированного полимера. Изображение получено после удаления ААС.
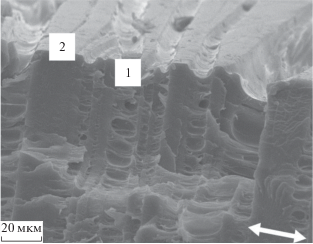
По данным низкотемпературной адсорбции азота размер пор в ПЭТФ, деформированном по механизму крейзинга, составил 11 нм при 100%-ной степени вытяжки и 8 нм – при 150%-ной, что соответствует по номенклатуре ИЮПАК мезопористым материалам.
Величина пористости является главной характеристикой с точки зрения практического использования полимеров, деформированных по механизму крейзинга. Как правило, жидкость, в большей степени снижающая напряжение вытяжки, является более эффективной для получения материалов с высокой пористостью. С увеличением степени вытяжки все большая часть полимера переходит в крейзы, что приводит к увеличению пористости. Однако величина пористости определяется не только условиями вытяжки, но и стабильностью формирующейся при вытяжке в ААС фибриллярно-пористой структуры.
На рис. 3 представлена зависимость объемной пористости ПЭТФ от степени вытяжки полимера в ИЗП (кривая 1) и в водном растворе ИЗП (кривая 2). Здесь же приведены теоретическая зависимость пористости от степени вытяжки, рассчитанная в предположении, что деформация происходит по механизму “идеального” крейзинга без коагуляционных процессов в структуре крейзов (кривая 3), а также зависимость пористости от степени вытяжки ПЭТФ в ИЗП и последующей усадки полимера (кривая 4).
Рис. 3.
Зависимость пористости от степени вытяжки ПЭТФ в ИЗП (1), в 40%-ном водном растворе ИЗП (2), теоретически вычисленная зависимость (3), после растяжения ПЭТФ в ИЗП и усадки (4).
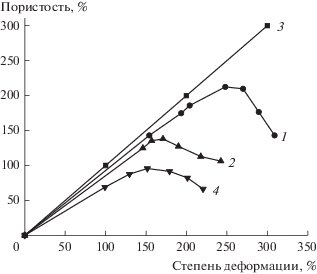
Согласно данным рис. 3 с увеличением степени вытяжки почти до 150% пористость возрастает для всех исследуемых условий растяжения, причем экспериментально измеренная пористость ПЭТФ (кривые 1, 2) близка к теоретически вычисленной (кривая 3). При степенях вытяжки больше 150% наблюдаются возрастающие отклонения от теоретической кривой, что свидетельствует о структурных перестройках фибриллярно-пористой структуры крейзов, которые приводят к уменьшению пористости. Интенсивность структурных превращений в виде коагуляционных процессов возрастает с увеличением степени вытяжки, то есть с увеличением ширины крейзов и длины фибрилл. Вода не является ААС, поэтому по сравнению с ИЗП водный раствор ИЗП является менее активной средой и в меньшей степени снижает поверхностную энергию ПЭТФ. В связи с этим пористость ПЭТФ, деформированного в водном растворе ИЗП, оказалась ниже, чем деформированного в ИЗП, при высоких степенях вытяжки (кривые 1, 2).
Таким образом, механические испытания, данные СЭМ и измерения объемной пористости позволяют сделать вывод, что деформация ПЭТФ в ИЗП происходит по механизму классического крейзинга и сопровождается формированием мезопористой структуры.
Усадка пленок ПЭТФ после растяжения приводит к уменьшению значений объемной пористости (кривая 4 рис. 3) по сравнению с пленками, которые после растяжения находятся в изометрических условиях (кривые 1 и 2 на рис. 3). Таким образом, очевидно, что стабилизацию структуры полимера, деформированного по механизму крейзинга, необходимо проводить в условиях, исключающих усадку. С этой целью отжиг деформированных образцов в ИЗП проводили при закреплении пленок в круговые рамки при температуре 75–80°C, близкой к температуре стеклования ПЭТФ (Tс = 81°C) и не превышающей температуру кипения ИЗП (82°C).
Результаты исследований паропроницаемости и пористости полученных пористых материалов на основе ПЭТФ, деформированного по механизму крейзинга, после отжига в ИЗП в изометрических условиях и удаления ИЗП представлены в табл. 1.
Таблица 1.
Коэффициент паропроницаемости (K) и объемная пористость (Wc) образцов ПЭТФ, деформированных до разной степени вытяжки (ε)
ε, % | K, г м–2 сутки–1 | Wc, % |
---|---|---|
0 | 0 | 0 |
100 | 575 | 20 |
125 | 680 | 27 |
150 | 730 | 32 |
200 | 460 | 23 |
Удаление летучей жидкой ААС (ИЗП) приводит к коагуляции фибрилл боковыми стенками, поэтому пористость полученных материалов оказалась значительно меньше пористости нативных образцов, определяемой до удаления ИЗП (рис. 3), однако отжиг позволил предотвратить усадку и сохранить открытопористую структуру ПЭТФ, проницаемую для паров волы. Согласно данным табл. 1 зависимость паропроницаемости и пористости полученных материалов от степени вытяжки ПЭТФ проходит через максимум. Максимальные значения паропроницаемости (730 г м–2 сутки–1) и пористости (32%) получены для ПЭТФ, деформированного на 150%.
Стабилизация структуры ПЭТФ, очевидно, обусловлена тем, что при отжиге в ААС происходит не только снятие внутренних напряжений в деформированном полимере, но и его кристаллизация. Для проверки этого предположения были проведены исследования структуры исходного ПЭТФ, ПЭТФ, деформированного в ИЗП на 150%, и ПЭТФ, отожженного после деформации на 150% в ИЗП, методом ДСК. Полученные термограммы представлены на рис. 4.
Рис. 4.
Термограммы исходного образца ПЭТФ (1), ПЭТФ, деформированного в ИЗП на 150% (2), ПЭТФ, деформированного в ИЗП на 150% и затем отожженного в ИЗП в изометрических условиях (3).
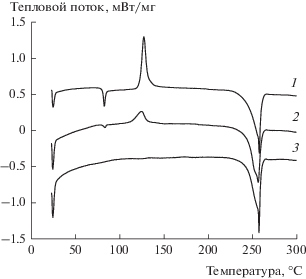
Исходный ПЭТФ является неориентированным аморфным полимером и способен к кристаллизации при температуре выше Tс полимера (79–81°C). Выше Tс на термограмме исходного полимера наблюдается экзотермический пик кристаллизации с максимумом при 130°C и последующий эндотермический пик плавления закристаллизованного полимера при 257°C (кривая 1 на рис. 4). На термограмме ПЭТФ, деформированного в ИЗП на 150%, присутствуют те же пики кристаллизации и плавления, что и для исходного ПЭТФ (кривая 2 на рис. 4), однако теплота кристаллизации оказалась ниже (табл. 2), что связано с изменением структуры ПЭТФ в результате деформации по механизму крейзинга. Поскольку в деформированном ПЭТФ присутствуют крейзы и области недеформированного полимера между ними (рис. 2), пик кристаллизации для этого образца, видимо, относится к кристаллизации участков аморфного ПЭТФ, расположенных между крейзами. Для образца ПЭТФ, отожженного после деформации в ИЗП, пик кристаллизации отсутствует (кривая 3 на рис. 4), однако теплоты плавления и соответственно степени кристалличности как образцов, закристаллизовавшихся в процессе нагревания при проведении ДСК-исследования, так и предварительно отожженного образца, оказались близки (табл. 2). Алгебраическая сумма площадей пиков плавления и кристаллизации позволила оценить степень кристалличности образцов ПЭТФ до кристаллизации в процессе проведения ДСК (табл. 2).
Таблица 2.
Теплота кристаллизации (ΔНкр), теплота плавления (ΔНпл) и степень кристалличности (χ) образцов ПЭТФ по данным ДСК
Для недеформированного аморфного ПЭТФ степень кристалличности составила 11%, что может быть связано как с присутствием отдельных локальных упорядоченных зон мезофазы, близкой по свойствам к кристаллической фазе [26], так и с условиями получения термограмм. Для ПЭТФ, деформированного по механизму крейзинга, степень кристалличности составила 23%, что соответствует представлениям о кристаллизации ориентированного полимера в крейзах и подтверждается данными рентгеноструктурного анализа [27, 28]. Отжиг вблизи температуры стеклования ПЭТФ позволил увеличить степени кристалличности деформированного полимера до 33% и сформировать кристаллический каркас, который способен удерживать и сохранять пористую структуру крейзов после снятия напряжения.
Таким образом, для аморфного стеклообразного ПЭТФ, деформированного по механизму крейзинга, эффективным способом сохранения пористой структуры является отжиг в условиях, предотвращающих усадку, в присутствии ААС. Стабилизация структуры крейзов обусловлена кристаллизацией ПЭТФ и снятием внутренних напряжений в деформированном полимере. Полученные методом крейзинга в ААС пленки ПЭТФ можно отнести к “дышащим” материалам с объемной пористостью до 32% и паропроницаемостью до 730 г м–2 сутки–1.
Классический крейзинг позволяет получить хорошо выраженную анизотропную структуру на поверхности ПЭТФ с крейзами в виде канавок (бороздок) шириной несколько микрон, прорастающих через всю толщу полимера в направлении, перпендикулярном оси вытяжки (рис. 5а). На оптических микрофотографиях видно, что капля воды принимает анизотропную форму – она вытянута вдоль бороздок крейзов. Исследование смачиваемости водой пленок ПЭТФ, деформированных по механизму классического крейзинга, показало, что анизотропия структуры вызывает анизотропию поверхностных свойств, в частности, анизотропию смачивания.
Рис. 5.
(а) Оптическая микрофотография капли воды на поверхности ПЭТФ, деформированного по механизму крейзинга. Направление вытяжки указано стрелкой. Измерение краевого угла с точки наблюдения 1 (б) и с точки 2 (в) на рисунке (а).
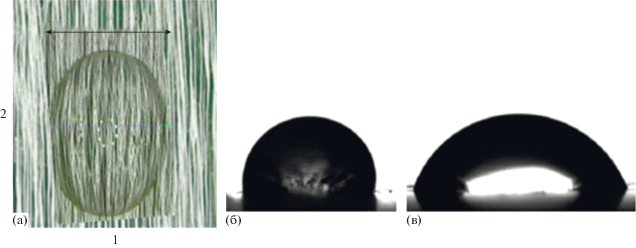
Краевой угол воды (θ) имеет разные значения при измерении вдоль и перпендикулярно оси вытяжки, т.е. зависит от направления крейзов (рис. 5б). θ, измеренный вдоль направления крейзов (вид с точки 1 на рис. 5а), оказался больше θ = 82° для исходного ПЭТФ и составил 95° при 150%-ной степени вытяжки. θ, измеренный перпендикулярно направлению крейзов (вид с точки 2 на рис. 5а), оказался равен 70°, то есть меньше, чем для исходного ПЭТФ. После кипячения ПЭТФ в ИЗП, возможно, вследствие присоединения гидроксильных радикалов угол смачивания исходного ПЭТФ уменьшился до 62°. Для деформированного на 150% по механизму крейзинга ПЭТФ после отжига в ИЗП θ, измеренный вдоль направления крейзов (вид с точки 1 на рис. 5а), оказался больше θ = 62° для исходного ПЭТФ и составил 70°. Значение θ, измеренного перпендикулярно направлению крейзов (вид с точки 2 на рис. 5а), составило 55°, то есть меньше, чем для исходного ПЭТФ.
Таким образом, крейзинг позволяет получать структуры с анизотропией рельефа поверхности, что в свою очередь приводит к анизотропии смачивания. Возможность стабилизации пористой структуры ПЭТФ, деформированного по механизму крейзинга, расширяет область его практического использования в качестве “дышащих” упаковочных и укрывных материалов, пористых мембран, матриц для создания нанокомпозитов и полимерных смесей, в том числе материалов с анизотропией поверхностных свойств.
Список литературы
Ребиндер П.А., Щукин Е.Д. // УФН. 1972. Т. 108. С. 3.
Kambour R.P. // J. Polym. Sci.: Macromol. Rev. 1973. V. 7. P. 1.
Волынский А.Л., Бакеев Н.Ф. Роль поверхностных явлений в структурно-механическом поведении полимеров. М.: Физматлит, 2014.
Волынский А.Л., Бакеев Н.Ф. // Физикохимия поверхности и защита материалов. 2013. Т. 49. С. 451.
Ярышева А.Ю., Полянская В.В., Рухля Е.Г., Дементьев А.И., Волынский А.Л., Бакеев Н.Ф. // Коллоид. журн. 2011. Т. 73. С. 565.
Yarysheva A.Y., Dolgova A.A., Yarysheva L.M., Arzhakova O.V. // Mendeleev Commun. 2020. V. 30. P. 507.
Yarysheva A.Y., Rukhlya E.G., Grokhovskaya T.E., Dolgova A.A., Arzhakova O.V. // J. Appl. Polym. Sci. 2019. V. 136. P. 48567.
Ярышева Л.М., Ярышева А.Ю., Волынский А.Л. // Журн. общей химии. 2019. Т. 89. С. 2092.
Goel P., Möller M., Weichold O. // Chem. Mater. 2009. V. 21. P. 3036.
Волынский А.Л., Никонорова Н.И., Волков А.В., Москвина М.А., Тунян А.А., Ярышев Н.Г., Аржакова О.В., Долгова А.А., Рухля Е.Г., Трофимчук Е.С., Абрамчук С.С., Ярышева Л.М., Бакеев Н.Ф. // Коллоид. журн. 2010. Т. 72. С. 458.
Gillanders R.S., Arzhakova O.V., Hempel A., Dolgova A., Kerry J.P., Yarysheva L.M., Bakeev N.F., Volynskii A.L., Papkovsky D.B. // Anal. Chem. 2010. V. 82. P. 466.
Go D., Takarada W., Aneja A., Kikutani T. // Mater. Today Commun. 2019. V. 19. P. 98.
Goldade V., Vinidiktova N. // ISJ Theor. Appl. Sci. 2017. V. 47. P. 178.
Andronova A.P., Popryadukhina S.I., Egorov I.A., Aleshicheva N.B. // Fibre Chem. 2011. V. 43. Article 86.
Kale R.D., Banerjee A., Katre G. // Fibers Polym. 2015. V. 16. P. 54.
Волынский А.Л., Бакеев Н.Ф. // Высокомолек. соед. А. 2009. Т. 51. С. 1783.
Yarysheva A.Yu., Bagrov D.V., Kechek’yan P.A., Rukhlya E.G., Bakirov A.V., Yarysheva L.M., Chvalun S.N., Volynskii A.L. // Polymer. 2019. V. 169. P. 234.
Аржакова О.В., Миронова А.А., Ярышева Л.М., Волынский А.Л., Бакеев Н.Ф. // Высокомолек. соед. А. 1996. Т. 38. С. 1166.
Миронова А.А., Аржакова О.В., Ярышева Л.М., Волынский А.Л., Бакеев Н.Ф. // Высокомолек. соед. А. 1996. Т. 38. С. 828.
Ефимов А.В., Щерба В.Ю., Озерин А.Н., Ребров А.В., Бакеев Н.Ф. // Высокомолек. соед. А. 1990. Т. 32. С. 456.
Yarysheva A.Yu., Arzhakova O.V., Yarysheva L.M., Volynskii A.L. // Polymer. 2018. V. 158. P. 243.
Синевич Е.А., Праздничный А.М., Бакеев Н.Ф. // Высокомолек. соед. А. 1995. Т. 37. С. 1521.
Синевич Е.А., Праздничный А.М., Ребров А.В., Бакеев Н.Ф. // Высокомолек. соед. А. 1994. Т. 36. С. 1499.
Himma N.F., Anisah N., Prasetya N., Wenten I.G. // J. Polym. Eng. 2016. V. 36. P. 329.
Arzhakova O.V., Dolgova A.A., Yarysheva L.M., Volynskii A.L., Bakeev N.F. // Inorg. Mater. Appl. Res. 2011. V. 2. P. 493.
Козлов Г.В., Новиков В.У. // УФН. 2001. Т. 171. С. 717.
Синевич Е.А., Праздничный А.М., Бакеев Н.Ф. // Высокомолек. соед. А. 1996. Т. 38. С. 276.
Ефимов А.В., Щерба В.Ю., Озерин А.Н., Ребров А.В., Бакеев Н.Ф. // Высокомолек. соед. А. 1990. Т. 32. С. 828.
Дополнительные материалы отсутствуют.
Инструменты
Коллоидный журнал