Коллоидный журнал, 2021, T. 83, № 5, стр. 595-601
Экспериментальная оценка воздействия жидкометаллических адсорбционно-активных сред на металлы
1 Военная академия войсковой противовоздушной обороны Вооруженных Сил Российской Федерации им. Маршала Советского Союза А.М. Василевского
214027 Смоленск, ул. Котовского, 2, Россия
* E-mail: planeta-registr.com@rambler.ru
Поступила в редакцию 13.04.2021
После доработки 15.05.2021
Принята к публикации 17.05.2021
Аннотация
В статье предлагается новый способ определения длительной прочности металлов в условиях воздействия сильнодействующих адсорбционно-активных сред. Оригинальность работы, заключается в предложенном способе определения характеристик поверхностного слоя образцов, ослабленного совместным механическим и физико-химическим воздействием агрессивной среды с использованием оптической регистрации момента образования поверхностной трещины и разрушения образца. Описано устройство электронно-оптического стенда, реализующего предложенный способ.
ВВЕДЕНИЕ
Общий научный подход к объяснению эффекта Ребиндера был предложен еще в двадцатых годах прошлого столетия [1], однако современные представления о теории и механизмах его протекания все еще нуждаются в уточнении и развитии [2, 3]. По-прежнему не до конца изучено явление жидкометаллического охрупчивания (ЖМО) металлов, которое является одной из форм проявления эффекта Ребиндера. В частности, остаются невыясненными механизмы избирательного действия жидкометаллических составов (ЖМС) на металлы в широких диапазонах температуры и давления. Нуждаются в детальном исследовании вопросы взаимодействия жидкого и твердого металлов на атомном уровне, а также взаимосвязи процессов адсорбции, диффузии, капиллярного течения жидкого металла, роли дислокаций и напряжений при деформации и разрушении.
Остаются актуальными вопросы прогнозирования главных проявлений ЖМО в металлических конструкциях – пластической деформации и трещинообразования. Их наличие является характерным признаком потери работоспособности металлических изделий, свидетельствующим об опасности внезапного катастрофического разрушения в процессе эксплуатации.
Наличие проблем в области теории повышает значение экспериментальных исследований, которые служат важнейшим источником достоверных знаний об изучаемых явлениях. Развитие экспериментальной физико-химической механики материалов сложилось таким образом, что испытание металлов на длительную прочность стало одним из основных способов исследования явления ЖМО [4–7]. При его использовании рельефно проявляются главные закономерности процесса ЖМО, а получаемые результаты отличаются наибольшей наглядностью и точностью [4].
Появление новых знаний о теории и практике экспериментальных исследований явления ЖМО создало ряд предпосылок для их дальнейшего развития.
1. В настоящее время складывается общий подход к исследованию материалов, подверженных влиянию агрессивных сред, в соответствии с которым твердое тело рассматривается как гетерогенная система, состоящая из двух разнородных материалов [4, 7–9]. Такой подход позволяет сосредоточить внимание на поведении приповерхностных областей твердого тела, непосредственно контактирующих с ЖМС.
2. Установлена ключевая роль атомного механизма в разрушении материала образца на микроуровне [4, 10, 11]. Одним из показателей разрыва межатомных связей при ЖМО является время раскрытия хрупкой трещины. Однако отсутствие количественных данных о кинетике роста трещин, которая контролируется процессами разрыва межатомных связей в вершине, не позволяет предложить корректное теоретическое описание атомного механизма ЖМО.
В целях повышения точности, информативности и достоверности проводимых испытаний целесообразно использовать прямое наблюдение за процессами разрушения с применением оптических, рентгенографических и других бесконтактных методов регистрации.
3. Существует практическая потребность применения дозированного нанесения ЖМС на образцы в малых количествах. Подавляющее большинство существующих способов микромеханических исследований предполагают испытание образцов в условиях полного погружения в ЖМС, что не всегда целесообразно и экономически оправдано. Например, в некоторых случаях разрушение твердых образцов происходит уже на стадии погружения в жидкий металл. Кроме того, многолетний опыт показал, что сопоставление результатов, полученных в воздушной и изучаемой средах, малоэффективно и труднореализуемо.
4. Анализ накопленных экспериментальных данных свидетельствует о необходимости разработки унифицированных способов испытаний, проводимых по единой типовой схеме, позволяющих выявить и сопоставить влияние различных факторов на прочность металлов: материалов и температуры образцов и ЖМС, механических нагрузок. Например, создание системы исходных данных по уязвимости металлов и сплавов к воздействию ЖМС в различных условиях их эксплуатации может значительно ускорить процесс разработки машин и механизмов уже на этапе предварительного проектирования.
С учетом состояния и перспектив развития экспериментальной физико-химической механики в работе предложен новый способ испытаний металлов на длительную прочность в условиях воздействия сильнодействующих ЖМС. Цель разработки – повышение точности измерений времени разрушения материалов, достоверности и информативности наблюдений, обеспечение возможности дозированного нанесения ЖМС в малых количествах на испытываемые образцы, а также расширение научных представлений о физикохимии поверхностных явлений, имеющих место при ЖМО.
ЭКСПЕРИМЕНТАЛЬНАЯ ЧАСТЬ
Общие подходы к исследованию длительной прочности образцов, имеющих модифицированный поверхностный слой, ранее были рассмотрены в работах [4, 7–9].
Схема нагружения плоского образца при испытании на растяжение показана на рис. 1. ЖМС наносится на правую грань выбранного участка образца. С момента нанесения ЖМС начинается его проникновение вглубь образца, вследствие чего в процесс деформирования вовлекаются материалы областей 1 и 2 (рис. 2). В качестве объектов испытаний рассматривались плоские образцы, близкие по размерам к стандартным. Выбор плоской формы образцов сделан с целью устранения нелинейной зависимости концентрации жидкого металла от глубины его проникновения.
Рис. 1.
Схема нагружения образца в условиях воздействия ЖМС: P – полное усилие растяжения, Pf и Ps – усилия в областях, не модифицированных и модифицированных ЖМС соответственно.
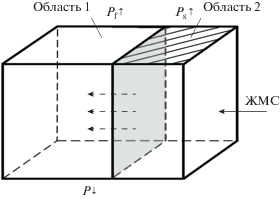
Рис. 2.
Схема действия внутренних напряжений: ${{{{\sigma }}}_{{\text{0}}}}$ – приложенное напряжение, ${{{{\sigma }}}_{{{\text{if}}}}}$– напряжение в области 1, ${{{{\sigma }}}_{{{\text{is}}}}}$– напряжение в области 2, $h$ – глубина внедрения ЖМС.
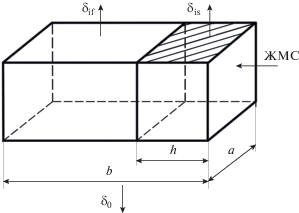
Область 1 не содержит жидкометаллических включений и является упругопластической основой образца. Область 2, модифицированная жидким металлом, является местом протекания сложных физико-химико-механических процессов [10], которые завершаются резким повышением хрупкости и понижением предела прочности материала до предела прочности при хрупком разрушении ${{{{\sigma }}}_{{\text{s}}}}$. В области 2, представляющей собой хрупкую оболочку на поверхности образца, происходит зарождение и развитие магистральной трещины. Время до образования трещины является периодом замедленного разрушения образца.
Напряженно-деформированные состояния в этих областях существенно различаются [4, 7–9]. Имеет место соотношение dσ1/dε1 > dσ2/dε2, где σ1 и σ2 – напряжения растяжения, ε1 и ε2 – деформации материала соответственно в областях 1 и 2. Допускается, что ширина границы разупрочнения, разделяющей области 1 и 2, бесконечно мала. Допущение сделано на основе результатов рентгенографических исследований глубины проникновения изотопов жидкого галлия в алюминиевый сплав, которые показали, что зависимость концентрации жидкого металла от пройденного расстояния носит пороговый характер.
На рис. 2 показано распределение внутренних напряжений в прямоугольном сечении образца с размерами a × b на участке нанесения ЖМС.
Для принятых схем нагружения (рис. 1) имеем [7]
Из уравнения (1) и рис. 2 получаем [8]
Граница разупрочнения, в силу особенностей физико-химического действия ЖМС и напряженного состояния образца, продвигается в направлении, перпендикулярном вектору внешней нагрузки. В процессе ее перемещения при увеличении $h$ происходит непрерывное перераспределение внутренних напряжений с области 2 на область 1 (см. уравнение (2)). Поскольку ${{{{\sigma }}}_{{\text{s}}}}$< σy, то в определенный момент времени наступает хрупкое разрушение материала области 2 с образованием магистральной трещины. Поступление ЖМС в вершину трещины прекращается, и дальнейшее разрушение образца происходит без его участия. При достижении предела текучести материала на участке $b$–${{h}_{{\text{s}}}}$ области 1 происходит вязкое течение металла вплоть до полного разрушения образца.
Полное разрушение наступает при выполнении условий σif = σy и ${{{{\sigma }}}_{{{\text{is}}}}}$ = ${{{{\sigma }}}_{{\text{s}}}}$. В итоге из уравнения (2) получаем
Определение σs осуществляется экспериментально, путем последовательного подбора на одинаковых образцах такого неразрушающего режима испытаний, при котором выполняется условие σs = σ0min.
Для реализации предложенного способа испытаний был разработан экспериментальный стенд, оснащенный электрооптической системой регистрации времени образования трещины ${{t}_{{\text{s}}}}$ и времени полного разрушения образца tc (рис. 3). Стенд включает в себя устройство для нагружения образцов, систему регистрации динамики их разрушения, контактор, систему изменения и измерения температуры наносимого ЖМС.
Рис. 3.
Схема испытательного стенда для исследования характеристик материалов в условиях влияния ЖМС: 1 – генератор светового потока, 2, 3 – световоды, 4 – образец, 5 – ЖМС, 6 – контактор, 7 – нагреватель (охладитель), 8 – воздушный редуктор с трубопроводами, 9 – баллон со сжатым воздухом, 10 – место нанесения ЖМС.
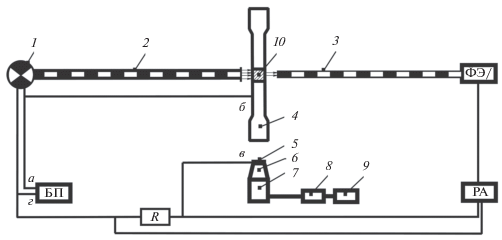
Устройство для нагружения образцов может быть представлено разрывной машиной, рычажным или иным устройством в зависимости от цели испытания. Максимальное растягивающее усилие должно создаваться в пределах проявления эффекта ЖМО и не превышать величину ${{{{\sigma }}}_{{\text{s}}}}$. В состав стенда можно включить любое растягивающее устройство, удовлетворяющее указанному требованию (в ряде случаев ЖМО может наступить и при отсутствии нагрузки по истечении достаточно длительного времени).
Система регистрации динамики разрушения образца включает генератор светового потока 1, световоды 2 и 3, блок фотоэлектронного умножителя (ФЭУ), блок регистрирующей аппаратуры (РА), блок питания (БП), систему коммутирующих проводов. В состав блока РА входят электронно-счетный частотомер и универсальный запоминающий осциллограф.
Контактор 6 служит для нанесения ЖМС 5 на образец 4 на участке 10 (на рис. 3 он заштрихован). Контактор должен иметь непроницаемую рабочую поверхность, смачиваемую ЖМС и инертную по отношению к нему. Это обеспечивает сохранность контактора, предотвращает неконтролируемый расход ЖМС и обеспечивает его удобное нанесение и точное дозирование. Контактор позволяет наносить тонкую пленку жидкого металла, которой вполне достаточно для испытания сильнодействующего ЖМС.
Система нанесения и изменения температуры ЖМС состоит из контактора 6, скрепленного с головкой нагревателя (охладителя) 7, воздушного редуктора 8, баллона высокого давления 9 со сжатым воздухом и системы подводящих воздухопроводов. Изменение температуры ЖМС осуществляется посредством контактора 6, нагреваемого или охлаждаемого от блока 7, который конструктивно совмещает в себе электроподогреватель и воздушный охладитель дроссельного типа, включающий в себя воздушный редуктор 8 и баллон высокого давления 9. Электрический нагреватель позволяет доводить температуру образца и ЖМС до 200°C, а охладитель – до –40°C.
ЖМС может наноситься как при постоянном, так и при переменном нагружении образца. В общем случае поверхность контактора может быть произвольной формы, как может быть произвольным и способ подведения контактора в зависимости от цели испытания.
Практика показала, что закономерность распространения трещины в направлении, перпендикулярном вектору растягивающей силы, особенно явно проявляется в условиях ЖМО. Эта особенность формирования трещины была использована для оптической регистрации процесса разрушения образца путем расположения в профиль по обе стороны от него светоизлучающего и светопринимающего устройств (см. рис. 3), объединенных в общую контрольно-измерительную цепь.
В исходном состоянии блоки ФЭУ и РА работают в режиме ожидания. Корпус образца препятствует проникновению света из передающего световода 2 в принимающий световод 3, поэтому сигнал на входе блока ФЭУ отсутствует. Цепь абвг разомкнута, напряжение на нагрузке R отсутствует, и, следовательно, отсутствует сигнал “запуск” на блоке РА.
После нанесения ЖМС 5 на поверхность контактора 6 последний прикладывается к образцу 4 в месте предполагаемого разрушения на участ-ке 10. Цепь абвг замыкается, и напряжение, снимаемое с нагрузки R, поступает на блок РА. Начинают работать электронно-счетный частотомер и запоминающий осциллограф, точно фиксируя момент начала воздействия ЖМС на поверхность образца. Спустя период замедленного разрушения в образце под воздействием ЖМС и растягивающей нагрузки раскрывается трещина на глубину ${{h}_{{\text{s}}}}$ (см. рис. 4), через которую световой поток попадает на блок ФЭУ. Электронно-счетный частотомер вырабатывает сигнал и подает его на осциллограф, регистрируя тем самым момент образования трещины ts. Запоминающий осциллограф в это время продолжает работать, поскольку предварительно настраивается на останов от заднего фронта сигнала. После скачкообразного раскрытия трещины происходит резкое перераспределение нагрузки по сечению. Как следствие, значительно ускоряется течение металла в образовавшейся шейке (см. рис. 4б) с последующим окончательным разрушением образца в момент времени tc.
Рис. 4.
Схемы прохождения светового потока в процессе испытания. (а) Фронтальный вид образца в период развития трещины; (б) профильный вид образца в момент образования хрупкой трещины.
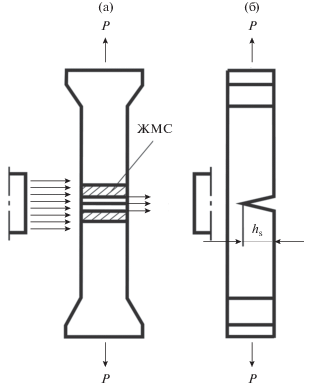
Таким образом, динамика разрушения образца фиксируется при нарушении его сплошности по изменению светового потока, проходящего через образующуюся трещину.
Температурный режим воздействия ЖМС на образец изменяется посредством контактора, сопряженного с головкой подогревателя (охладителя) 7. Его применение дает возможность локально изменять температуру наносимого ЖМС и соответствующего участка поверхности образца, что позволяет существенно динамичнее изменять температурный режим испытаний, а также получать информацию о динамике разрушения в зависимости от величины и характера изменения температуры наносимого ЖМС в месте контакта.
Для измерения температуры образцов и ЖМС предусмотрено применение бесконтактных датчиков температуры. Заметим, что один из самых простых используемых пирометров Fluke 51 позволяет измерять температуру в пределах от ‒250°C до 1370°C.
Образцы для испытаний целесообразно выполнять однообразными по форме и размерам, что позволяет избежать переналадки оборудования от опыту к опыту и значительно облегчить сравнение результатов испытаний образцов, выполненных из различных материалов.
Рекомендуется применять плоские образцы толщиной 0.5–5 мм, длиной 150–200 мм, имеющие ширину плоской части для нанесения ЖМС 10–20 мм. Указанные размеры позволяют, с одной стороны, свести к минимуму расход материалов на их изготовление и расход ЖМС, а с другой – обеспечить удобство и высокую скорость выполнения однотипных операций. Полное время, необходимое для проведения отдельного эксперимента, составляет примерно 6 минут.
Потенциальные возможности нового способа, как правило, окончательно определяется после достаточно длительного периода его использования. В настоящее время установлены пределы его применимости, соблюдение которых гарантирует высокое качество экспериментальных исследований.
РЕЗУЛЬТАТЫ И ИХ ОБСУЖДЕНИЕ
В качестве примера на рис. 5–8 показаны некоторые результаты испытания образцов, выполненных из сплава Д16 АТ. В качестве ЖМС использовался жидкометаллический состав с температурой плавления 13.5°C. Температура образцов, ЖМС, контактора и окружающего воздуха составляла 20°C.
Рис. 6.
Типичная осциллограмма скорости изменения светового потока, проходящего через профиль разрушающегося образца. Разрешение шкалы по горизонтали 1 деление/с.
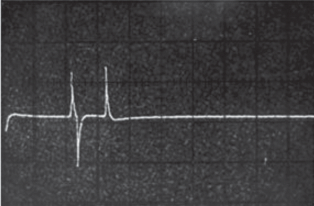
Рис. 7.
Типичная осциллограмма изменения мощности светового потока, проходящего через профиль разрушающегося образца. Разрешение шкалы по горизонтали 1 деление/с.
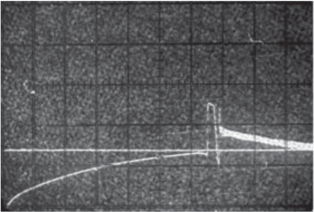
Рис. 8.
Пример экспериментальной оценки длительной прочности образцов толщиной 2.86 мм. Плотность поверхностного нанесения ЖМС – 3 кг/м2.
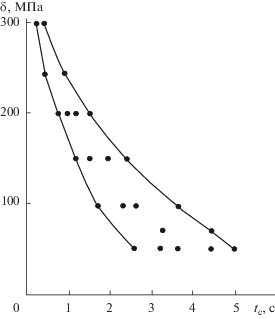
Типичные осциллограммы сигналов, несущих информацию о разрушении металлических пластин, представлены на рис. 6 и 7. На рис. 8 приведен пример определения длительной прочности для одного из металлических образцов. Анализ полученных результатов позволил выявить некоторые закономерности быстропротекающих процессов разрушения при ЖМО.
1. Процесс разрушения носит двухстадийный характер. На первой стадии протекает замедленное разрушение модифицированного слоя образца. Образуется “хрупкий след” (потенциальная трещина) по ходу продвижения ЖМС. Стадия завершается появлением магистральной трещины. На рис. 6 время ts прихода сигнала об образовании трещины зафиксировано в виде первого “всплеска”.
На второй стадии происходит вязкое разрушение оставшейся шейки. Разрушение происходит без участия ЖМС, что подтверждается путем визуального осмотра излома: поверхность, соответствующая раскрывшейся трещине, оказывается хорошо смоченной жидким металлом. На оставшейся части излома следы ЖМС отсутствуют.
Время окончания вязкого разрушения образца tc фиксируется на осциллограмме в виде второго “всплеска”. Промежуток времени между поступлениями сигналов характеризуется течением металла шейки. Время замедленного разрушения составляет 2.2 с, время полного – 3.2 с.
Таким образом, времена разрушения поверхностного слоя и окончательной фрагментации конструкций при воздействии ЖМС могут не совпадать. Это обстоятельство требует уточнения понятия разрушения в зависимости от цели испытаний и функционального предназначения металлических конструкций.
2. На протяжении всего времени контакта образца с жидким металлом вплоть до его разрушения отмечается непрерывное течение металла в месте контакта с ЖМС. На рис. 7 приведена осциллограмма, снятая при испытаниях другого образца. На ней отчетливо видно постепенное увеличение светового потока, поступающего на ФЭУ. Это свидетельствует об уменьшение толщины образца, которое начинается практически сразу же после прикладывания контактора. При отводе контактора от образца течение прекращалось. Подтверждаются высказываемые ранее мнения о том, что текучесть предшествует любому хрупкому разрушению при ЖМО.
3. Наличие растягивающих усилий значительно ускоряет процесс проникновения ЖМС в структуру металлов. Визуально можно наблюдать характерную картину поглощения поверхностью нагруженного образца жидкого металла: металлический образец ведет себя подобно обычной губке, буквально на глазах впитывая ЖМС. Очевидно, что подобное явление возможно только при образовании внутри образца большого количества микронесплошностей.
4. На рис. 8 приведены результаты испытаний образцов в виде зависимости σ0(tс). Наблюдается определенный разброс опытных данных, границы которого показаны тонкими линиями. Очевидно, он обусловлен в первую очередь физико-химическими свойствами материалов образцов и используемого ЖМС. Причины разброса могут быть различными: термофлуктуационная природа деформации и разрушения твердого тела, вероятностный характер распределения микродефектов в структуре образцов и др. Разброс значений времени разрушения возрастает при увеличении толщины образцов и уменьшении растягивающих напряжений. Таким образом, получаемые результаты нуждаются в тщательной статистической обработке, учитывая их важность для теоретического объяснения эффекта ЖМО.
ЗАКЛЮЧЕНИЕ
Предложенный способ испытаний может быть использован для исследования следующих перечисленных ниже основных факторов, влияющих на физикохимию поверхностных явлений в процессе ЖМО.
1. Химический состав ЖМС и твердого тела.
2. Тип кристаллической решетки или ближний порядок ЖМС и металла.
3. Величины атомных радиусов химических элементов ЖМС и металла.
4. Электроотрицательность, валентность элементов, входящих в состав ЖМС и металла.
5. Атомные массы элементов, входящих в состав ЖМС.
6. Коэффициент диффузии ЖМС в металле.
7. Температура ЖМС и металла.
8. Величина и скорость приложения внешней нагрузки, наличие деформаций.
9. Наличие микро- и макродефектов на поверхности и внутри твердого тела.
10. Размер зерна металла, наличие и строение границ зерен и межзеренных прослоек.
11. Наличие примесей в ЖМС.
12. Размер и форма испытываемых конструкций.
13. Масса, концентрация и условия нанесения ЖМС.
14. Вид и величина лучевого воздействия на образцы.
15. Комбинирование механического, физико-химического и лучевого воздействий при ЖМО.
Способ испытаний может быть приспособлен для исследования свойств неметаллических материалов, подверженных воздействию адсобционно-автивных сред различной физической природы.
ВЫВОДЫ
1. Экспериментально доказана адекватность модели ЖМО металлического тела как двухкомпонентной гетерогенной системы. Предложенный подход к исследованию явления ЖМО позволяет определять характеристики разрушения модифицированных слоев металла, непосредственно контактирующих с ЖМС, а также глубину модифицированного слоя в момент раскрытия магистральной трещины. Установлена новая закономерность ЖМО металлов, главная особенность которой состоит в наличии двух стадий разрушения.
2. Показана эффективность оптического метода регистрации времени разрушения образца по изменению светового потока, проходящего через образующуюся хрупкую трещину. Точность измерений, полученная с применением обычного осциллографа, составляет 0.2 с. Она может быть значительно повышена путем использования измерительной аппаратуры с более высоким разрешением по времени.
3. Разработан и апробирован способ дозированного нанесения ЖМС на испытываемые образцы, что в совокупности с высокой точностью измерений дает возможность испытывать металлы в условиях воздействия малых доз (до сотых долей грамма) сильнодействующих ЖМС.
4. Предложенный экспериментальный стенд экономичен, прост, удобен при эксплуатации и доступен для реализации в условиях лабораторий со средним уровнем технического оснащения.
Таким образом, предложенный способ испытаний может рассматриваться в качестве основы для разработки унифицированного средства решения широкого круга исследовательских задач.
Список литературы
Ребиндер П.А. “VI съезд русских физиков”. М.: ОГИЗ, 1928. С. 29.
Малкин А.И. // Коллоид. журн. 2012. Т. 74. С. 239.
Щукин Е.Д., Перцов А.В., Амелина Е.А. Коллоидная химия. М.: Юрайт, 2012.
Локошенко А.М. Ползучесть и длительная прочность металлов в агрессивных средах. М.: МГУ им. М.В. Ломоносова, 2000.
Иванова Н.И., Горюнов Ю.В., Перцов Н.В., Щукин Е.Д. // Физико-химическая механика материалов. 1967. № 1. С. 16.
Никитин В.И. // Физико-химическая механика материалов. 1968. Т. 4. № 1. С. 13.
Савенко В.И., Щукин Е.Д. // Физико-химическая механика материалов. 1985. Т. 21. № 3. С. 78.
Дмуховская И.Г., Попович В.В. // Физико-химическая механика материалов. 1982. Т. 18. № 6. С. 5.
Локошенко А.М. Ползучесть и длительная прочность металлов. М.: Физматгиз, 2016.
Щукин Е.Д. // Физико-химическая механика и лиофильность дисперсных систем. 1981. Вып. 13. С. 46.
Kelley M.J., Stoloff N.S. // Metall. Trans. A. 1975. V. 6. P. 159.
Дополнительные материалы отсутствуют.
Инструменты
Коллоидный журнал