Кристаллография, 2021, T. 66, № 6, стр. 993-999
Разработка программного обеспечения для определения параметров распределения пор и сегрегаций легирующих элементов в сталях аустенитного класса после ионного облучения
А. С. Фролов 1, *, Е. В. Алексеева 1, Е. А. Кулешова 1, 2
1 Национальный исследовательский центр “Курчатовский институт”
Москва, Россия
2 Национальный исследовательский ядерный университет “МИФИ”
Москва, Россия
* E-mail: frolov_as@nrcki.ru
Поступила в редакцию 09.06.2020
После доработки 15.07.2020
Принята к публикации 18.07.2020
Аннотация
Разработаны программные пакеты SwellingProfile и ElementProfile для построения профилей распухания при обработке изображений поперечных срезов, полученных методом просвечивающей растровой электронной микроскопии. Программы также позволяют рассчитывать профили распределения химических элементов вблизи границ вакансионных пор и вдоль траектории ионного облучения материалов до сравнительно больших повреждающих доз. Пакеты были применены для анализа вакансионного распухания при облучении стали 08Х18Н10Т ионами никеля (с предварительной имплантацией гелия) при температуре 625°С до пиковых значений повреждающей дозы ∼300 сна. В результате на построенном профиле распухания выявлены два максимума, обусловленные формированием двух систем пор разного размера. Сравнительный анализ показал, что полученный профиль имплантации никеля хорошо коррелирует с расчетами, проведенными с помощью SRIM-2008.
ВВЕДЕНИЕ
Одним из методов, позволяющих проводить качественную сравнительную оценку радиационной стойкости сталей и сплавов в процессе их эксплуатации в составе различных энергетических установок, является имитационное (ионное) облучение [1–3]. Однако существуют определенные методические аспекты, которые необходимо учитывать при интерпретации получаемых данных о микроструктурных изменениях в материалах, подвергшихся такому облучению [4].
Во-первых, качественное сравнение радиационной стойкости сталей и сплавов после имитационного облучения возможно только по ограниченному набору микроструктурных параметров, например по распуханию. Однако даже в этом случае необходимо учитывать смещение максимума на температурной зависимости распухания [4–7] для каждого типа облучения (ионами или нейтронами). Применение ионного облучения для анализа эволюции вторых фаз, как показывают многочисленные исследования, является нетривиальной задачей, поскольку, как правило, изменение фазового состава при ионном и нейтронном облучении различно [8, 9].
Во-вторых, профиль концентрации ионов (повреждающая доза) вдоль нормали к облучаемой поверхности не является линейной функцией [10, 11], что необходимо учитывать при построении дозовых зависимостей различных микроструктурных параметров.
В-третьих, необходимо учитывать тип и энергию бомбардирующих частиц. Чаще всего ионное облучение проводят теми же элементами, которые составляют основу химического состава исследуемого материала, либо выбирают наиболее близкие по массе и размеру ионы11. Глубина и степень повреждаемости (модифицирования) приповерхностного слоя зависят как от температуры облучения, так и от общей накопленной повреждающей дозы, а также энергии бомбардирующих частиц. В случае металлических материалов, например сталей аустенитного класса, для проведения имитационного облучения используют, как правило, ионы железа или никеля с энергией несколько МэВ. Несмотря на относительно небольшую глубину имплантации ионов (которая обычно составляет 1–3 мкм [1, 12]), распределение структурных элементов в приповерхностном слое крайне неоднородно, что в значительной мере затрудняет обработку результатов.
Тем не менее применение ионного облучения может быть обосновано с позиции сравнительной оценки радиационной стойкости [13] (по определенным параметрам) группы материалов с целью снижения затрат на этапе предварительного выбора некоторых из них для проведения дальнейших натурных испытаний.
Как упоминалось ранее, интерпретация результатов воздействия ионного облучения на эволюцию микроструктуры, кроме всего прочего, затрудняется вследствие неоднородности распределения изменений в приповерхностном слое, особенно при сравнительно больших повреждающих дозах (100 сна и более) [1, 12]. Поэтому в настоящей работе предложены алгоритмы и разработано программное обеспечение для расчета профилей распухания вдоль нормали к облучаемой поверхности, а также анализа сегрегационных процессов на границах раздела пора–матрица и построения профилей распределения имплантированных ионов, которые использовали для облучения.
1. МАТЕРИАЛЫ И МЕТОДЫ ИССЛЕДОВАНИЯ
В качестве тестового объекта исследования для апробации разработанного программного пакета выбрана сталь 08Х18Н10Т аустенитного класса после облучения ионами никеля с энергией 11.5 МэВ (с предварительной имплантацией гелия22 до ∼30 мд) на ускорителе Tandetron при температуре 625°С до пиковых значений повреждающей дозы ∼300 сна.
Образцы (ламели) для исследований методами просвечивающей электронной микроскопии (ПЭМ) изготавливали из приповерхностного (толщиной до 5 мкм) слоя мишеней методом сфокусированного ионного пучка с использованием двухлучевой станции Helios NanoLab 650 (FEI, США). Распределение пор, а также сегрегационные процессы на их границах и высокоугловых границах аустенитных зерен исследовали методами ПЭМ и энергодисперсионной рентгеновской спектроскопии с использованием высокоразрешающего микроскопа Titan 80-300 (FEI, США).
2. ПОСТРОЕНИЕ ПРОФИЛЯ РАСПУХАНИЯ
2.1. Подготовка исходных изображений. Для расчета профиля распухания проводили цифровую обработку изображений образцов, полученных с помощью просвечивающей растровой электронной микроскопии (ПРЭМ) [14]. На рис. 1а приведено типичное ПРЭМ-изображение образца из стали 08Х18Н10Т после облучения ионами никеля.
Рис. 1.
ПРЭМ-изображение участка образца (а) и его итоговая маска (б). Крупные (d > h) и мелкие (d < h) поры показаны разными цветами.
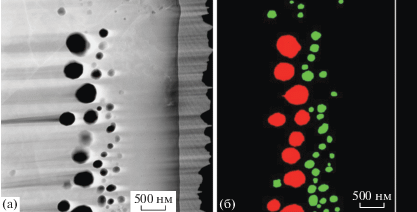
Область съемки выбирали в соответствии с распределением пор по глубине. Для каждой ламели (поперечного среза) получали серию ПРЭМ-изображений, покрывающих не менее 8 мкм по длине ламели. Далее с использованием программного комплекса SIAMS [15] строили панорамное изображение, объединяющее все изображения одного поперечного среза.
2.2. Алгоритм расчета интегрального профиля распухания. Для цифровой обработки изображения входными данными были карты интенсивности сигнала. Их обработка осложнялась тем, что не все локальные минимумы соответствуют порам и, кроме того, уровни локальных минимумов сильно различаются. Поэтому, применяя фильтры и пороговую сегментацию изображения, с помощью комплекса SIAMS создавали обратную бинарную маску, интенсивные области на которой соответствуют положениям пор на ПРЭМ-изображении. Из рис. 1а видно, что области пор на исходном изображении имеют различную интенсивность, что связано с тем, что часть пор (диаметр d которых меньше толщины ламели h) не проходит образец насквозь, поэтому внутри контура поры остается часть матричного материала, дающего ненулевой сигнал на ПРЭМ-изображении.
Толщина исследуемого участка определяется по отношению интегральной интенсивности к интенсивности пика нулевых потерь в спектре энергетических потерь электронов на каждом исследуемом участке [16–21]:
где ${{\lambda }}$ – длина свободного пробега электрона в железе при соответствующем ускоряющем напряжении, ${{I}_{T}}$ и ${{I}_{0}}$ – интегральная интенсивность и интенсивность пика нулевых потерь в спектре энергетических потерь электронов соответственно. Рассчитанная в соответствии с [17, 21] длина свободного пробега электронов в исследуемом образце при ускоряющем напряжении 200 кВ составляет ∼68 нм (угол сбора в ПЭМ-режиме с самой большой объективной апертурой составлял ∼170°).Для корректной обработки изображений все поры разделяли на “крупные” (d > h) и “мелкие” (d < h) путем фильтрации по среднему внутреннему диаметру с помощью комплекса SIAMS. В качестве выходных данных формировали новую бинарную маску с разделенными на две системы порами (рис. 1б).
Дальнейшую цифровую обработку полученной маски проводили с помощью разработанного в рамках настоящей работы программного пакета SwellingProfile. После загрузки изображения маски в этот программный пакет происходит ее разбиение в виде сетки с заданным шагом. Затем осуществляются послойное считывание и обработка маски, в результате которой подсчитывается суммарная площадь, занятая порами, т.е. количество элементов сетки, попадающих на поры (закрашенных разными цветами в данном слое), и полученное значение записывается в массив, имеющий размерность и шаг ранее выбранной сетки. В случае попадания элемента сетки на “крупные” поры, проходящие ламель насквозь, соответствующий элемент массива принимается равным единице, а в случае попадания на “мелкие” – $\frac{{h - \bar {d}}}{h}$, где $\bar {d}$ – средний внутренний диаметр “мелких” пор, $h$ – толщина образца. В остальных случаях элементам массива присваиваются нулевые значения. Затем полученный двумерный массив преобразуется в одномерный путем суммирования его элементов (строк либо столбцов – в зависимости от направления ионного пучка по отношению к плоскости облучения образца) с последующей нормировкой на число элементов в строке/столбце. Схематично данный алгоритм преобразования массива показан на рис. 2.
Для усреднения и сглаживания полученных профилей распухания осуществлялась обработка не менее трех ламелей общей длиной не менее 24 мкм. Для сглаживания профиля проводилось усреднение по нескольким слоям для каждой ламели.
3. МЕТОДИКА ОБРАБОТКИ ИЗОБРАЖЕНИЙ ДЛЯ РАСЧЕТА ПРОФИЛЯ РАСПРЕДЕЛЕНИЯ ЭЛЕМЕНТОВ
Для расчета профилей распределения имплантированных элементов по глубине образца методом энергодисперсионного рентгеновского анализа получали карты распределения элементов на участках размером 4.5 × 3.0 мкм. Шаг при построении такой карты составлял 30 нм в обоих направлениях. Из рис. 3а видно, что на картах распределения внутри контура пор имеются отдельные участки с относительно высоким содержанием этих элементов (яркие точки внутри пор), что является артефактом, возникающим из-за ошибки определения химического состава участков, которым соответствует сигнал малой интенсивности. Для устранения артефактов применяли фильтрацию данных участков с использованием ранее полученных масок для пор (рис. 3в).
Рис. 3.
Графическое отображение карты Ni (а), бинарная маска (б), графическое отображение карты Ni с учтенными порами (в).
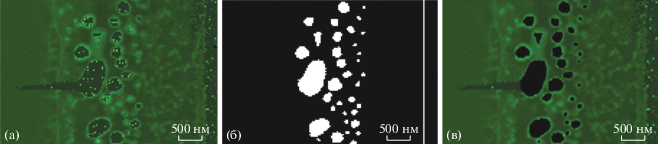
Для цифровой обработки карт использовали созданный в рамках работы программный пакет ElementProfile [22]. Входными данными для программы являлся массив концентраций элементов в каждой точке карты, представленный в виде текстового файла, а также изображение бинарной маски для фильтрации, описанной выше.
3.1. Построение профилей имплантации элементов по глубине образца. Для построения профилей распределения имплантированных элементов по глубине образца программный пакет ElementProfile осуществляет для каждого элемента отдельно построчное/постолбцовое считывание и обработку массива. Для каждого столбца/строки проводится подсчет общего содержания выбранного химического элемента, а затем нормировка на число элементов столбца/строки аналогично алгоритму построения профиля распухания, описанному выше.
В дальнейшем подобная обработка проводилась для нескольких карт по каждому из четырех элементов Fe, Ni, Cr, Ti, а также усреднение значений по картам для каждого элемента.
3.2. Построение профилей распределения элементов вблизи поры. Для построения профилей распределения элементов вблизи пор программный пакет ElementProfile после заполнения массива данными о содержании элементов в каждой точке с учетом бинарной маски проводит построение отдельных профилей, проходящих через пору. Для этого на карте распределения химических элементов выделяется прямоугольная область, внутри которой содержится только одна пора, с указанием ее центра. Затем выбираются точки из массива с координатами X, Y, соответствующими каждой линии профиля. Условием выбора точек является, во-первых, нахождение координат X, Y в пределах выделенной прямоугольной области и, во-вторых, связь координаты Y с координатой X соотношением, соответствующим уравнению секущей, проведенной через обозначенный центр поры под углом к оси X:
где xi, yi – координаты точки на текущей прямой, xbubble, ybubble – координаты центра поры, n – количество профилей, i – номер текущей прямой.4. РЕЗУЛЬТАТЫ И ИХ ОБСУЖДЕНИЕ
На рис. 4 представлено типичное ПРЭМ-изображение, совмещенное с профилем распухания, поверхности образца стали 08Х18Н10Т аустенитного класса после облучения ионами никеля с энергией 11.5 МэВ (с предварительной имплантацией гелия33 до ∼30 мд) на ускорителе Tandetron при температуре 625°С до пиковых значений повреждающей дозы ∼300 сна. Видно, что профиль распухания имеет два выраженных максимума (рис. 4, сплошная кривая), что связано с двумя системами пор, образующимися в результате ионного облучения. Пики были разделены с помощью функции Гаусса44.
Рис. 4.
Типичное ПРЭМ-изображение образца стали 08Х18Н10Т после ионного облучения, совмещенное с соответствующим профилем распухания (сплошная линия), и результаты моделирования процесса ионного облучения с помощью программного комплекса SRIM-2008 (штриховая линия).
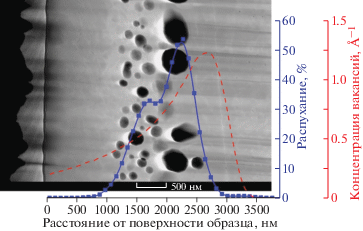
Сравнение экспериментальных данных с результатами моделирования процесса ионного облучения с помощью программного комплекса SRIM-2008 и в рамках приближения Кинчина–Пиза показало, что используемое во многих исследованиях стационарное решение задачи без учета динамических эффектов игнорирует реальную структуру, формирующуюся в процессе ионного облучения в исследуемом материале, температуру ионного облучения, а также влияние легирования (в частности влияние никеля) на порообразование. Поэтому расчетные данные несколько отличаются от экспериментального профиля распухания в исследованном образце (рис. 4, штриховая кривая): наблюдается смещение профилей распухания относительно расчетов c использованием SRIM-2008 в сторону поверхности образца, поскольку образующиеся поры являются эффективными стоками вакансий.
Анализ распределения пор по размерам показал, что для исследованного образца характерно наличие двух систем пористости, которые при построении профиля распухания были условно разделены по размеру на “крупные” поры со средним внутренним диаметром более 250 нм и “мелкие” поры со средним внутренним диаметром менее 250 нм. Из рис. 4 видно, что “мелкие” поры залегают ближе к поверхности образца, а “крупные” – наоборот, на большей глубине. Такое разделение может быть связано с наличием “инкубационного” периода в процессе порообразования, поскольку зависимость концентрации вакансий от глубины по результатам расчетов SRIM-2008 можно использовать как качественное представление дозовой зависимости. Следовательно, при достижении определенной дозы облучения DКР начинают образовываться зародыши будущих крупных пор в области, близкой к области с максимальным повреждением. В дальнейшем эти поры, увеличиваясь в размерах и являясь эффективными стоками вакансий, оказывают непосредственное влияние на распределение вакансий в облучаемом материале. Вторая система “мелких” пор, по-видимому, образуется на меньшей глубине при достижении в данной области дозы облучения DКР. Кроме того, на процесс порообразования оказывает влияние предварительная имплантации гелия, так как при облучении ионами гелия формирующиеся поры имеют малый размер и высокую плотность и являются эффективными стоками для возникающих при облучении ионами никеля вакансий.
В соответствии с методикой, описанной в разд. 3.2, была проведена оценка изменения элементного состава вблизи поверхности пор (рис. 5). Видно, что на краю пор наблюдаются области, обогащенные никелем, шириной ∼150 нм. В соответствии с методикой, описанной в разд. 3.1, были построены профили распределения имплантированного никеля. На рис. 6 приведены для сравнения расчетный концентрационный профиль имплантированного никеля, полученный при помощи программного пакета SRIM-2008, и экспериментальные данные. Видно, что экспериментальная максимальная глубина имплантации никеля довольно точно описывается расчетными моделями программного пакета SRIM-2008 и составляет для образца стали 08Х18Н10Т ∼2900 нм от поверхности образца.
ЗАКЛЮЧЕНИЕ
Разработан программный пакет SwellingProfile для построения профилей распухания при обработке ПРЭМ-изображений поперечных срезов материалов после ионного облучения до сравнительно больших повреждающих доз. Данный пакет был применен для анализа вакансионного распухания при облучении стали 08Х18Н10Т ионами никеля с энергией 11.5 МэВ (с предварительной имплантацией гелия до ∼30 мд) на ускорителе Tandetron при температуре 625°С до пиковых значений повреждающей дозы ∼300 сна. В результате на построенном профиле распухания выявлены два максимума, обусловленные формированием двух систем пор разного размера.
Кроме того, разработан программный пакет ElementProfile, позволяющий рассчитывать профили распределения химических элементов вблизи границ вакансионных пор, а также вдоль траектории ионного облучения материалов на основе постобработки соответствующих карт, полученных методом энергодисперсионной рентгеновской спектроскопии. Данный пакет был применен для анализа сегрегационных процессов в стали 08Х18Н10Т после ионного облучения (с указанными выше параметрами), в результате которого были количественно определены концентрации элементов на поверхности вакансионных пор, а также построен профиль распределения имплантированного никеля. Сравнительный анализ показал, что полученный профиль хорошо коррелирует с расчетами, проведенными с помощью SRIM-2008.
Таким образом, разработанные программные пакеты могут быть использованы для анализа процесса порообразования и различных сегрегационных процессов при ионном облучении различных материалов.
Список литературы
Sun C., Malerba L., Konstantinovic M.J. // Miner. Met. Mater. Ser. 2019. № 1. P. 669. https://doi.org/10.1007/978-3-030-04639-2_43
Was G.S. // J. Mater. Res. 2015. V. 30. № 9. P. 1158. https://doi.org/10.1557/jmr.2015.73
Bryk V., Borodin O., Kalchenko A. // Proc. 11th Int. Top. Meet. Nucl. Appl. Accel. Bruges, Belgium, 5–8 August 2013. P. 1.
Kalchenko A.S., Bryk V.V., Lazarev N.P. // J. Nucl. Mater. 2010. V. 399. № 1. P. 114. https://doi.org/10.1016/j.jnucmat.2010.01.010
Terasawa M., Nakahigashi S., Koyama M. // J. Nucl. Sci. Technol. 1983. V. 20. № 11. P. 929. https://doi.org/10.1080/18811248.1983.9733490
Abromeit C. // J. Nucl. Mater. 1994. V. 216. № C. P. 78. https://doi.org/10.1016/0022-3115(94)90008-6
Loomis B.A. // J. Nucl. Mater. 1986. V. 141–143. № 2. P. 690. https://doi.org/10.1016/0022-3115(86)90075-9
Ribis J., Bordas E., Trocellier P. // J. Mater. Res. 2015. V. 30. № 14. P. 2210. https://doi.org/10.1557/jmr.2015.183
Pareige C., Kuksenko V., Pareige P. // J. Nucl. Mater. 2015. V. 456. P. 471. https://doi.org/10.1016/j.jnucmat.2014.10.024
Bhattacharya A., Meslin E., Henry J., Décamps B. // Mater. Res. Lett. 2018. V. 6. № 7. P. 372. https://doi.org/10.1080/21663831.2018.1462266
Stoller R.E., Toloczko M.B., Was G.S. // Nucl. Instrum. Methods Phys. Res. B. 2013. V. 310. № 9. P. 75. https://doi.org/10.1016/j.nimb.2013.05.008
Gigax J.G., Chen, T., Kim H. // J. Nucl. Mater. 2016. V. 482. № 8. P. 257. https://doi.org/10.1016/j.jnucmat.2016.10.003
Swenson M.J., Wharry J.P. // J. Nucl. Mater. 2015. V. 467. P. 97. https://doi.org/10.1016/j.jnucmat.2015.09.022
Williams D., Carter A. Transmission Electron Microscopy. New York: Springer, 2009. 760 p. 10. https://doi.org/1007/978-1-61779-415-5_23
Козерчук А.Л., Петров М.С. // Оптический журнал. 2011. V. 78. № 1. С. 77.
Синдо Д., Оикава Т. Аналитическая просвечивающая электронная микроскопия. М.: Техносфера, 2006. 256 с.
Malis T., Cheng S.C., Egerton R.F. // J. Electron Microsc. Tech. 1988. V. 8. № 2. P. 193. https://doi.org/10.1002/jemt.1060080206
Yang Y.Y., Egerton R.F. // Micron. 1995. V. 26. № 1. P. 1. https://doi.org/10.1016/0968-4328(94)00039-S
Zhang H.-R., Egerton R.F., Malac M. // Micron. 2012. V. 43. № 1. P. 8. https://doi.org/10.1016/j.micron.2011.07.003
Egerton R.F., Cheng S.C. // Ultramicroscopy. 1987. V. 21. № 3. P. 231. https://doi.org/10.1016/0304-3991(87)90148-3
Iakoubovskii K., Mitsuishi K., Nakayama Y. // Microsc. Res. Tech. 2008. V. 71. № 8. P. 626. https://doi.org/10.1002/jemt.20597
Алексеева Е.В., Фролов А.С., Сафонов Д.В. Программа для построения и обработки ЕDХ-профилей распределения химических элементов “EIementProfile”. Свидетельство о государственной регистрации программы для ЭВМ № 2019613187. от 12.03.2019.1 с.
Дополнительные материалы отсутствуют.
Инструменты
Кристаллография