Кристаллография, 2022, T. 67, № 2, стр. 216-226
Исследование механизма влияния коррозии под напряжением на развитие макропластических неустойчивостей алюминий-магниевого сплава
А. А. Шибков 1, *, С. С. Кочегаров 1, А. А. Денисов 1, А. Е. Золотов 1, М. Ф. Гасанов 1, А. В. Шуклинов 1
1 Тамбовский государственный университет им. Г.Р. Державина
Тамбов, Россия
* E-mail: shibkov@tsu.tmb.ru
Поступила в редакцию 29.04.2021
После доработки 14.05.2021
Принята к публикации 16.05.2021
- EDN: GOILJS
- DOI: 10.31857/S0023476122020187
Аннотация
Комплексом высокоскоростных методов исследования динамики деформационных полос и прерывистой деформации обнаружены и исследованы макроскопические скачки пластической деформации амплитудой несколько процентов на кривых ползучести алюминий-магниевого сплава, вызванные локальным воздействием на поверхность сплава концентрированного раствора соляной кислоты. Представлены результаты компьютерного моделирования процесса формирования фрактальной морфологии коррозионного фронта и полей упругих напряжений в условиях стресс-коррозии. Показано, что в сложной структуре коррозионной границы, включающей “полуострова” и “фьорды”, локальные напряжения в вершинах фьордов на ~1–1.5 порядка превышают уровень приложенного напряжения, что может привести к коллективному срабатыванию большого количества дислокационных источников и развитию макроскопической дислокационной лавины, вызывающей скачок деформации на кривой ползучести.
ВВЕДЕНИЕ
Многие промышленные сплавы на основе алюминия, меди, титана, никеля и некоторые стали демонстрируют пластические неустойчивости на макроскопическом уровне – “зуб текучести”, прерывистая (скачкообразная) деформация и образование шейки перед разрывом. Прерывистая деформация проявляется в трех ситуациях в зависимости от условий деформирования: появление скачков напряжения при деформировании с заданной скоростью ${{\dot {\varepsilon }}_{0}}$ = const (эффект Портевена–Ле Шателье [1]), появление скачков деформации при нагружении материала с заданной скоростью ${{\dot {\sigma }}_{0}}$ = const (эффект Савара–Массона [2]) и появление скачков на кривых ползучести (“лестничная” ползучесть [3]). Несмотря на почти двухвековую историю исследования прерывистой деформации, начатой еще в первой половине XIX века, природа этого явления остается неясной [4]. Высокоскоростные исследования динамики полос макролокализованной деформации, вызывающие прерывистую деформацию, показывают, что эти полосы зарождаются у поверхности металла [5]. Однако роль состояния поверхности в развитии прерывистой деформации недостаточно изучена экспериментально и теоретически. Практически важной и актуальной является проблема влияния на прерывистую деформацию коррозии под напряжением, которая изменяет состояние поверхности деформируемого материала.
Коррозия под напряжением (стресс-коррозия), как известно, является одним из наиболее опасных видов коррозии. Исследование взаимосвязи коррозии и пластической деформации до настоящего времени проводилось по двум основным направлениям: оценка влияния интенсивной пластической деформации на скорость коррозии и изучение связи стресс-коррозии с деградацией механических свойств. В частности, было установлено, что коррозионное воздействие способствует локализации пластической деформации и снижает сопротивление разрушению ряда алюминиевых сплавов [6, 7], а питтинги на поверхности сплава являются концентраторами напряжения, которые ускоряют разрушение и уменьшают остаточную прочность [8, 9]. В [10] подчеркивалась актуальность проблемы изучения синергизма коррозионного и механического воздействий.
В поликристаллических металлических сплавах коррозия под напряжением, как предполагается, происходит в основном по механизмам межкристаллитной и транскристаллитной коррозии. В промышленных сплавах системы Al–Mg межкристаллитная коррозия включает селективное растворение частиц вторичной β(Al3Mg2)-фазы, выделяющихся по границам зерен [11], распространение трещин в зоне, обедненной магнием вдоль границ зерен [12, 13] или в результате водородного охрупчивания [14, 15]. Транскристаллитная коррозия в этих сплавах происходит вследствие выноса атомов магния на поверхность дислокационными скоплениями [16] за счет динамического деформационного старения дислокаций [17]. Вместе с тем динамическое деформационное старение дислокаций и их взаимодействие с малыми преципитатами являются основными обсуждаемыми механизмами развития прерывистой деформации [17–22]. Систематические исследования взаимосвязи стресс-коррозии и прерывистой пластической деформации до настоящего времени не проводились. В настоящей работе экспериментально обнаружено влияние стресс-коррозии на развитие макропластической неустойчивости алюминий-магниевого сплава в условиях прерывистой ползучести и проведены компьютерные исследования формирования фрактальной границы коррозионного фронта и ее влияния на спектр поверхностных концентраторов напряжения, способных спровоцировать потерю механической устойчивости деформируемого сплава на макроскопическом уровне.
МЕТОДИКА
Исследуемым материалом являлся промышленный алюминий-магниевый сплав АМг6 (Al–6.15 мас. % Mg–0.65 мас. % Mn–0.25 мас. % Si–0.21 мас. % Fe), проявляющий прерывистую деформацию в жестких и мягких деформационных машинах [23–25]. Плоские образцы в форме двухсторонних лопаток с размерами рабочей части 6 × 3 × 0.5 мм вырезали машинным способом из холоднокатаной полосы вдоль направления прокатки, отжигали при 450°С в течение 1 ч и закаливали на воздухе. После термообработки средний размер зерна составил 10 мкм. Перед механическим испытанием образцы подвергали электролитической полировке в течение минуты при 20°С в растворе, состоящем из 20%-ной хлорной кислоты HClO4, 10% глицерина и 70% этилового спирта; U = 18 В, I = 0.5 А/см2. Комплекс высокоскоростных методов регистрации деформации, нагрузки и исследования динамики деформационных полос, сопровождающих деформационные скачки, описаны в [5, 23]. Микроструктурные исследования поверхности проводили с помощью электронного зондового микроскопа di Innova SPM.
РЕЗУЛЬТАТЫ И ИХ ОБСУЖДЕНИЕ
Влияние стресс-коррозии на прерывистую ползучесть сплава АМг6
Испытания проводили в горизонтальной мягкой деформационной машине. Образцы нагружали одноосным растяжением в две последовательные стадии: нагружения со скоростью 1.5 МПа/с до момента времени, соответствующего приложенному напряжению σ0 ≈ 200 МПа, и ползучести при напряжении σ0 = const. Спустя ~30 с на рабочую поверхность деформируемого образца с помощью шприца наносили каплю 30%-ного раствора соляной кислоты, которая, растворяя оксидную поверхностную пленку Al2O3, активно реагирует с алюминием в соответствии с реакцией $2{\text{Al}} + 6{\text{HCl}} \to {\text{2AlC}}{{{\text{l}}}_{3}} + 3{{{\text{H}}}_{2}}$. В результате химического растворения локального участка поверхности площадью ~10 мм2 через временной интервал ~10 с деформируемый образец теряет механическую устойчивость, и на его поверхности развивается сложная структура деформационных полос (типичная для прерывистой ползучести [23]), которая сопровождается макроскопическим скачком пластической деформации – ступенью на кривой ползучести амплитудой 1–3% (рис. 1). Предварительные эксперименты показали, что при заданном уровне приложенного напряжения деформационный скачок спонтанно происходит обычно через ~100 c после приложения нагрузки.
Рис. 1.
Скачок деформации Δε (а) и соответствующий силовой отклик σ (б), инициированный химическим воздействием капли 30%-ного раствора HCl на поверхность деформируемого в условиях ползучести сплава АМг6. На вставке показана первичная полоса деформации на поверхности сплава. Стрелкой отмечен момент нанесения капли 30%-ного раствора HCl.
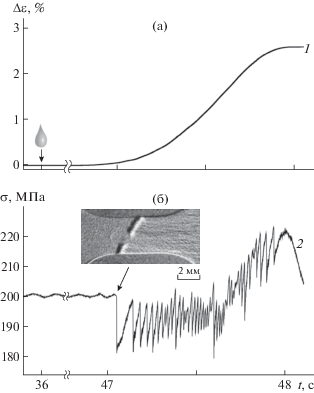
Таким образом, экспериментально установлено, что химический процесс растворения локального участка поверхности деформируемого алюминиевого сплава в условиях ползучести вызывает развитие макроскопической неустойчивости в виде скачка пластической деформации амплитудой несколько процентов. Естественно предположить, что процесс образования коррозионного пятна связан с формированием геометрических концентраторов напряжения и, следовательно, большого количества активных поверхностных дислокационных источников, способных спровоцировать зарождение макроскопической дислокационной лавины, которая вызывает развитие деформационной ступени на кривой ползучести.
Исследования in situ процесса формирования структуры коррозионного повреждения поверхности сплава связаны со значительными техническими трудностями, поэтому в работе проведены компьютерные исследования растворения поликристаллического алюминиевого сплава в растворе концентрированной соляной кислоты для оценки роли стресс-коррозии в развитии макроскопической неустойчивости.
Модель растворения поликристаллического металла в жидкой среде
В предлагаемой модели учитывали следующие структурные и физико-химические факторы. Структуру поликристаллического сплава задавали при помощи многоугольников Вороного, каждый из которых разбивали на более мелкие расчетные ячейки. Каждой ячейке приписывали коррозионную прочность, зависящую в основном от кристаллографической ориентации зерна. Травящий раствор характеризуется активностью, определяемой концентрацией частиц кислоты в растворе. Вероятность растворения ячейки твердого тела зависит от активности травителя и коррозионной прочности ячейки. В ходе травления активность травителя снижается вследствие уменьшения его концентрации, что приводит к затуханию и остановке химической реакции. Предполагается, что диффузионный перенос частиц кислоты к фазовой границе раствор–металл происходит значительно быстрее процесса растворения металла, поэтому концентрация раствора остается постоянной во временном интервале, соответствующем одной итерации расчета. Рассмотрена двумерная модель растворения в жидкой коррозионной среде поликристаллического металла без учета капиллярных явлений, связанных с эффектом Ребиндера и кривизной фазовой границы, а также без учета внутренних напряжений и возможного наличия активных центров коррозии в местах выхода дислокаций на поверхность.
На первом этапе расчетную область размером 500 × 500 мкм разбивали на многоугольники Вороного [26] следующим образом. Исследуемую область покрывали конечным числом окружностей с пуассоновским распределением их диаметров и математическим ожиданием, равным среднему размеру зерна. Внутри каждой окружности случайным образом выбирали точку, находящуюся в расчетной области. На основе выбранных точек при помощи встроенной в MATLAB функции строили диаграмму Вороного. В результате получали сетку из многоугольников Вороного. На втором этапе всю расчетную область покрывали равномерной квадратной сеткой. Среднее количество квадратных расчетных ячеек, приходящееся на одно зерно поликристалла, обозначим $k$. Как показали расчеты, при k > 390 результаты моделирования перестают зависеть от коэффициента разбиения k. Таким образом, принимая k = 400 и средний диаметр зерна равным 10 мкм, получаем размер расчетной ячейки 0.5 мкм (в $\sqrt k $ раз меньше размера зерна).
Каждая расчетная ячейка характеризуется безразмерной величиной ${{w}_{j}}$ – прочностью по отношению к травлению. Этот параметр показывает относительное время, которое требуется для коррозионного разрушения ячейки при постоянной активности травящего раствора: чем выше параметр ${{w}_{j}}$, тем большее время необходимо для разрушения конкретной ячейки. Величина ${{w}_{j}}$ зависит от нескольких факторов. Во-первых, известно, что для зерен с различной кристаллографической ориентацией скорость коррозионного разрушения может различаться в несколько раз [26–28]. Во-вторых, структура индивидуальных зерен неоднородна (наличие включений в сплавах Al–Mg, блочной структуры в отожженных сплавах, неоднородной дислокационной структуры в зонах локализованной пластической деформации и другие факторы). Другой случайной величиной является распределение на поверхности образца микроразрывов оксидной пленки, образовавшихся в результате коррозионного разрушения. На поверхности поликристаллического сплава эти структурные особенности расположены хаотично, поэтому предполагалось, что коррозионная прочность ${{w}_{j}}$ является случайной величиной с гауссовым статистическим распределением. Конечные значения ${{w}_{j}}$ были нормированы в диапазоне 0 ≤ ${{w}_{j}}$ ≤ 1. Таким образом, была получена структура, изображенная на рис. 2а, где оттенками серого тона показана различная коррозионная прочность ячеек твердого тела: чем светлее область, тем больше коррозионная прочность, и наоборот.
Рис. 2.
Временна́я эволюция поверхности в процессе коррозионного разрушения. “Кадры” получены после 100 (а), 500 (б), 1500 (в), 2500 (г) итераций расчета. Черным цветом показан раствор кислоты. На рис. 2г стрелкой отмечен лидирующий фьорд. На рис. 2д представлено фронтальное РЭМ-изображение реального коррозионного фронта, полученного травлением сплава АМг6 30%-ным раствором HCl.
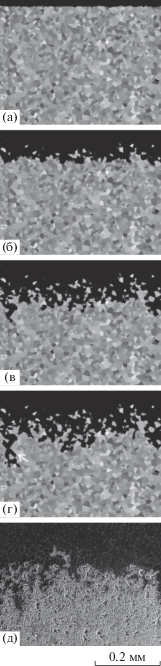
Будем полагать, что активность травителя $A$ – безразмерная величина, в любой момент времени $t$ линейно зависящая только от концентрации частиц кислоты: At = γCt, где Ct – концентрация кислоты, равная отношению количества частиц кислоты ${{N}_{t}}$ к объему раствора (в двумерном случае – площади), а γ – коэффициент с размерностью площади. В случае растворения на $t$-й итерации ${{n}_{t}}$ ячеек твердого тела количество частиц кислоты снижается на такое же количество. Таким образом, к $t$-й итерации остается ${{N}_{t}} = {{N}_{0}} - \sum\nolimits_{i = 1}^t {{{n}_{i}}} $ активных частиц кислоты, и активность раствора на следующей итерации расчета может быть выражена как
(1)
$\begin{gathered} {{A}_{{t + 1}}} = \gamma {\text{ }}{{C}_{t}} = {{\gamma }}{{N}_{t}}{\text{/}}V = {{\gamma }}\left( {{{N}_{0}} - \sum\limits_{i = 1}^t {{{n}_{i}}} } \right){\text{/}}V = \\ \, = {{A}_{0}}\left( {1 - \sum\limits_{i = 1}^t {{{n}_{i}}} {\text{/}}{{N}_{0}}} \right), \\ \end{gathered} $Как известно, химическая реакция растворения металла в кислоте является термоактивационным процессом, поэтому для его моделирования будем использовать вероятностный подход. Обозначим через ${{S}_{t}}$ множество ячеек разбиения, занятых твердым телом и контактирующих (имеют общую сторону) как минимум с одной ячейкой раствора кислоты на $t$-й итерации расчета. Ячейки этого множества образуют границу коррозионного фронта и потенциально могут быть растворены в ходе химической реакции. Среднее количество итераций расчета, необходимых для полного растворения j-й ячейки из множества ${{S}_{t}}$, обозначим τj. Тогда вероятность растворения этой ячейки на каждой итерации расчета (при неизменной активности кислоты) будет равна pj = = 1/τj. Эта вероятность, зависящая от активности раствора травителя $A$ и коррозионной прочности ячейки ${{w}_{j}}$, задавалась функцией ошибок
Так как на квадратной сетке ячейка твердого тела может быть окружена максимально четырьмя ячейками кислоты, а химическая реакция между ячейками проходит независимо, то верхний предел вероятности растворения ограничен величиной 0.25. Поэтому считали, что в зависимости от разности $A - {{w}_{j}}$ вероятность ${{p}_{j}}$ может принимать значения в диапазоне 0 ≤ ${{p}_{j}}$ ≤ 0.25. Параметр λ в формуле (2) характеризует скорость затухания химической реакции. Чем выше λ, тем быстрее затухает химическая реакция при снижении концентрации раствора кислоты. В предельном случае, при λ → ∞, выражение (2) превращается в ступеньку Хевисайда высотой 0.25. Это приводит к тому, что кислота растворяет только те ячейки твердого тела, коррозионная прочность которых ниже активности раствора кислоты, т.е. $A > {{w}_{j}}$. Описанный выше алгоритм численного расчета процесса коррозионного разрушения был реализован при помощи программного кода, написанного на языке MATLAB. Для количественной характеризации морфологии коррозионного фронта рассчитывали его фрактальную размерность ${{d}_{f}}$ (размерность Хаусдорфа–Безиковича) с помощью метода “бокс каунтинг” по формуле [29]:
где N(ε) – минимальное количество “боксов” (квадратов) со стороной ε, покрывающих данный контур.Морфологический переход от евклидовой к фрактальной морфологии коррозионного фронта
Временная эволюция коррозионного фронта представлена на рис. 2. Черные клетки представляют собой раствор кислоты, серые – поликристаллический сплав, где оттенками, как и ранее, отражена коррозионная прочность. Рисунки 2а–2г представляют морфологию промежуточных состояний коррозионного фронта. С течением времени активность раствора кислоты снижается из-за протекающей химической реакции, что приводит к замедлению процесса растворения твердого тела и образованию шероховатой границы коррозионного фронта. Конечная граница, полученная через 2500 итераций расчета, представляет собой фрактальную структуру (рис. 2г).
Процесс травления рассматривается как стохастический процесс отрыва ячеек и/или их агрегатов от границы твердого тела и перехода их в раствор, где они исчезают (растворяются) через некоторое количество итераций, т.е. спустя случайный временной интервал. Моделирование показывает, что в ходе коррозионного процесса вблизи поверхности алюминиевого образца в растворе кислоты формируются сложные пространственные структуры твердых островков с широким распределением по линейным размерам – от размера ячейки (0.5 мкм) до максимального размера агрегата из нескольких зерен (~30 мкм), средний размер ~7 мкм. В результате множественных отрывов этих островков образуется ломанная береговая линия твердого тела, которая включает множество впадин (“фьордов”) с соответствующим широким распределением их размеров и площадей (рис. 2). Расчеты по формуле (3) бокс-размерности показывают, что на любой итерации (т.е. в любой момент времени) при $t$ > 100 эта береговая линия представляет собой фрактал.
Зависимость от времени t (количества итераций) размерности ${{d}_{f}}$ коррозионного фронта представлена на рис. 3. Как видно из рис. 2 и 3, при травлении происходит морфологический переход от евклидовой формы (исходно гладкой) поверхности сплава к фрактальной форме с дробной размерностью ${{d}_{f}}$, которая сначала возрастает в активной фазе коррозионного процесса, а по мере его затухания вследствие истощения конечного объема травителя выходит на уровень ~1.3. Скачки на графике фрактальной размерности в большинстве случаев связаны с отделением от фазовой границы кластеров из зерен, коррозионная прочность которых превышала среднюю. Конечная фрактальная размерность коррозионного фронта, как показали расчеты, равна ${{d}_{f}}$ = 1.323 $ \pm $ $ \pm $ 0.002. Для сравнения по формуле (3) рассчитывали бокс-размерность реальной границы коррозионного фронта, полученного травлением поверхности сплава АМг6 30%-ным раствором соляной кислоты (рис. 2д). Полученное значение ${{d}_{f}}$ = 1.32 $ \pm $ 0.02, с одной стороны, хорошо согласуется с результатами компьютерного моделирования, а с другой – совпадает с размерностью фронта градиентной перколяции, равной 4/3 [30].
Рис. 3.
Временна́я зависимость фрактальной размерности коррозионного фронта. Конечное значение фрактальной размерности ${{d}_{f}}$ = 1.323 ± 0.002.
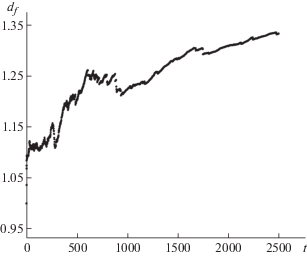
На оптическом уровне морфологический переход от евклидовой к фрактальной форме коррозионного фронта выглядит как переход в процессе травления от оптически гладкой к шероховатой поверхности алюминиевого образца. Действительно, примерно до $t \approx $ 30 глубина впадин на береговой линии не превышает 0.8 мкм, что соизмеримо с длиной волны видимой области спектра. Поэтому на начальной стадии поверхность еще оптически гладкая. С ростом количества итераций среднеквадратичная ширина коррозионного фронта возрастает и выходит на насыщение на последней, затухающей стадии процесса до максимального значения ~30 мкм. Поэтому конечная фрактальная морфология соответствует оптически шероховатой поверхности.
Важно подчеркнуть, что в ходе формирования фрактального коррозионного фронта в его структуре спонтанно образуется лидирующий, “гигантский” фьорд, размер которого на несколько порядков (в рассматриваемом случае на 2.5 порядка) превышает размер ячейки травления и более чем на порядок средний размер зерна. Действительно, на рис. 2г в конечной структуре наблюдается фьорд глубиной около 150 мкм, что в 300 раз превышает размер ячейки травления и значительно превышает (в разы) размеры самых крупных твердых островков, отделившихся в жидкий раствор. Рост лидирующего фьорда постепенно падает, уступая ускоренному росту соседних фьордов. Проблема формирования лидирующих фьордов особенно важна в условиях коррозии под напряжением как концентраторов максимальных внутренних напряжений в твердом теле, способных вызвать внезапное разрушение корродирующей конструкции или изделия. В зависимости от уровня приложенного напряжения локальные напряжения вблизи вершины лидирующего фьорда могут превысить напряжения срабатывания дислокационного источника или напряжения зарождения микротрещины. В первом случае возрастает вероятность формирования дислокационной полосы деформации, а во втором – развитие магистральной трещины. Формирование гигантского фьорда свидетельствует о перколяционной природе рассматриваемого процесса и является предметом отдельного исследования, выходящего за рамки настоящей работы.
Пространственное распределение концентраторов напряжения
В рассматриваемой модели плоский образец с коррозионным пятном подвергался одноосному растяжению приложенным напряжением σ0 = = const (режим ползучести). Поле упругих напряжений в сплаве с фрактальной поверхностью, образованной в результате коррозионного воздействия кислоты, рассчитывали с помощью метода конечных элементов. Исследуемую область покрывали неравномерной треугольной сеткой, которая сгущалась вблизи границы. Минимальный размер сетки оценивали на основе микроструктурных данных, полученных с помощью растровой электронной микроскопии (РЭМ) реального коррозионного фронта. РЭМ-изображения фрагментов при разных увеличениях показаны на рис. 4а, 4б. Анализ ~100 изображений показал, что минимальный радиус кривизны коррозионной границы составляет ~20 нм, который принимали за минимальный размер ячейки треугольной сетки. Ее фрагмент показан на рис. 4в. Поле упругих напряжений рассчитывали по формуле Мизеса [31]:
(4)
${{\sigma }_{M}} = {{\{ [{{({{{{\sigma }}}_{1}} - {{{{\sigma }}}_{2}})}^{2}} + {{({{{{\sigma }}}_{2}} - {{{{\sigma }}}_{3}})}^{2}} + {{({{{{\sigma }}}_{1}} - {{{{\sigma }}}_{3}})}^{2}}]{\text{/}}2\} }^{{1{\text{/}}2}}},$Рис. 4.
РЭМ-изображение фрагментов коррозионного фронта при различных увеличениях (а, б), пример построения расчетной сетки для вычисления упругих напряжений методом конечных элементов (в) и типичная расчетная картина полей напряжений вблизи фрактальной поверхности коррозионного фронта (г).
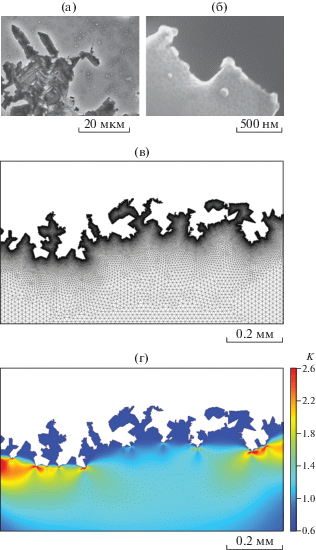
На рис. 4г показана типичная картина пространственного распределения упругих напряжений вблизи фрактальной поверхности деформируемого образца. Как и ожидалось, выступающие фьорды являются концентраторами напряжений в материале. В то же время “полуострова” оказываются разгруженными, т.е. σM < σ0, вследствие их экранирования фьордами; поэтому коэффициенты концентрации K = σM/σ0 в вершинах полуостровов меньше единицы, а в вершинах фьордов – больше единицы. Очевидно, представляет интерес расчет значений K в вершинах фьордов для оценки пространственного распределения потенциальных дислокационных источников и микротрещин. Распределение расчетных коэффициентов K вдоль длины L фрактальной границы деформируемого материала представлено на рис. 5а. Как видно, структура зависимости K(L) имеет внешние признаки фрактальности и самоподобия.
Рис. 5.
Пространственное распределение локальных концентраторов напряжения с коэффициентом концентрации напряжения K(L) вдоль границы коррозионного фронта в условиях коррозии под растягивающим напряжением (а). Результаты расчета показателя Херста (б, в).
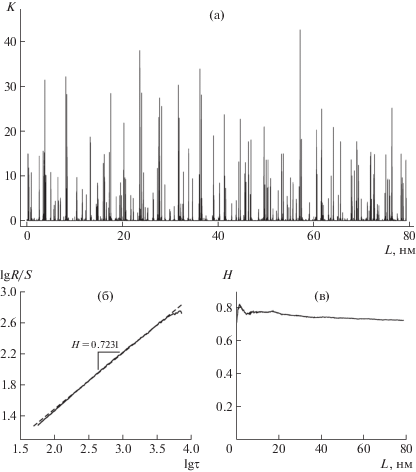
Исследование скрытых корреляций в пространственной структуре внутренних напряжений проводили методами фрактального и статистического анализа. Фрактальную размерность зависимости K(L) (“сигнала”) вычисляли, используя R/S-анализ методом нормированного размаха [30] с помощью выражения
где R(τ) = Ymax – Ymin – накопленное отклонение (размах) зависимости K(L) от среднего на отрезке τ вдоль береговой линии, а накопленное отклонение определяется какНа рис. 5б показана зависимость нормированного размаха R/S от величины τ [мкм] в двойных логарифмических координатах. Линейная аппроксимация этой зависимости дает среднее значение показателя Херста $\bar {H}$ = 0.72 и среднюю фрактальную размерность ${{\bar {d}}_{f}}$ = 1.28. Степень мультифрактальности оценивали согласно [32] как размах фрактальной размерности ${{d}_{{f\max }}} - {{d}_{{f\min }}}$. Для этого длину границы коррозионного фронта разбивали на части и по формуле (5) рассчитывали локальные показатели Херста. Пространственные вариации локального показателя Херста представлены на рис. 5в, из которого следует, что размах ${{d}_{f}}_{{\max }} - {{d}_{f}}_{{\min }}$ = 0.05. Таким образом, зависимость K(L) имеет почти монофрактальную структуру с размерностью ${{d}_{f}}$ = 1.28 $ \pm $ 0.05 и степенью мультифрактальности ~4%.
Отметим, что для случайного процесса показатель Херста Н = 0.5. Значение Н ≈ 0.72 указывает на то, что статистика коэффициентов напряжения значительно отличается от гауссовой. Стохастические процессы с Н > 0.5 являются, как известно, персистентными, т.е. процессами с сохраняющейся тенденцией [30]. Это означает, что процесс формирования коррозионного фронта в условиях стресс-коррозии является персистентным стохастическим процессом, в котором наблюдается взаимосвязь между тенденциями изменения коэффициентов корреляции в ходе формирования коррозионной границы. Если в некотором интервале наблюдается тенденция к росту среднего значения $\bar {K}$, то следует ожидать сохранения этой тенденции в последующем таком интервале и т.д. Действительно, результаты компьютерного моделирования показывают, что крупные фьорды, образовавшиеся на последних стадиях травления, являются источниками наиболее интенсивных локальных напряжений (K ~ ~ 20–40). В то же время мелкие фьорды и неровности с K ~ 1 образуются в ходе всего процесса травления, включая локальные участки с низкой скоростью травления, которые несут информацию о предшествующих стадиях травления. Как видно из рис. 5б, пространственные распределения коэффициентов интенсивности напряжений K(L) являются фракталом со скейлингом более двух порядков по линейной шкале и около двух порядков по величине нормированного размаха.
Другим признаком масштабной инвариантности зависимости K(L) является близость к гиперболическим формам гистограмм дискретных значений K и отрезков $\Delta L$ между ними (рис. 6а, 6б). В двойных логарифмических координатах статистическая функция распределения $D(s) = {{N}^{{ - 1}}}dN{\text{/}}ds$ нормированного коэффициента интенсивности напряжений $s = K{\text{/}}\bar {K}$ является приблизительно линейной с коэффициентом наклона к s-оси, равным –1.04 (здесь N – общее количество концентраторов напряжения, dN – количество концентраторов, коэффициенты концентрации которых попадают в узкий интервал s – δs/2, s + δs/2 [33], $\bar {K}$ – среднее значение K для всей выборки). Это означает, что функция распределения концентраторов напряжения вблизи фрактальной поверхности подчиняется степенному закону
с показателем α = 1.04 (рис. 6а).Рис. 6.
Гистограмма коэффициентов концентраций упругих напряжений K вдоль границы L коррозионного фронта (а), гистограмма отрезков $\Delta L$ между концентраторами (б) и “спектр мощности” Sp(ν) концентраторов напряжения (в). На вставках показаны плотности статистического распределения нормализованного коэффициента концентрации s и расстояния $\Delta L$ между концентраторами. Штриховыми линиями обозначены отрицательные склоны этих распределений, которые равны –1.04 и –0.5264 для распределений s и $\Delta L$ соответственно и –0.3163 и –1.5586 для “спектра мощности” в области больших и малых частот соответственно.
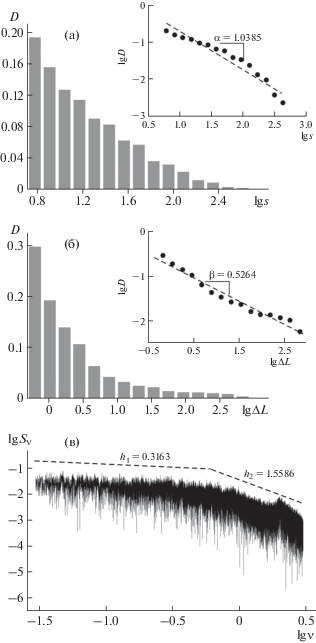
Статистическое распределение отрезков $\Delta L$ (“интервалов”) между позициями на фрактальной границе, где K > 1, также демонстрирует скейлинговую форму
с показателем степени β = 0.5264 (рис. 6б).По аналогии со спектром мощности временного ряда Sp(ν) можно рассматривать “спектр мощности” концентраторов напряжения как зависимость $\left\langle {{{K}^{2}}} \right\rangle $ на единичном отрезке береговой линии от “частоты” ν = 1/ΔL. Как видно из рис. 6в, “спектр мощности” Sp(ν) также демонстрирует степенную функцию
c показателями ${{h}_{1}}$ = 0.3163 для малых частот (большие интервалы между концентраторами напряжения) и ${{h}_{2}}$ = 1.5586 для больших частот (малые интервалы $\Delta L$). Известно, что в отсутствие корреляций в стохастическом сигнале $h$ = 0 (белый шум), а условие $h$ ~ 1 характерно для фликкер-шумовой структуры сигнала, что свидетельствует о наличии в нем долговременных корреляций.Скейлинговые законы (6)–(8) указывают на состояние самоорганизующейся критичности, которое характеризуется дальнодействующими корреляциями между большим числом локальных объектов [34, 35], в рассматриваемом случае – концентраторов упругих напряжений. Согласно [35] для сложных систем с состоянием самоорганизующейся критичности соблюдается скейлинговое соотношение между показателями степенных законов спектра мощности (8) и интервалов (7):
Подставляя в (9) β = 0.5264, получим $h$ = 1.4736, что близко к расчетному значению ${{h}_{2}}$ = 1.5586 и дополнительно подтверждает вывод о состоянии самоорганизующейся критичности, в которое эволюционирует структура концентраторов напряжения в ходе формирования фрактальной поверхности в условиях стресс-коррозии.Таким образом, в деформируемом поликристаллическом металле вблизи фрактальной границы коррозионного фронта образуется сложная мозаика упругих розеток с широким спектром хаотично распределенных концентраторов напряжения. Результаты моделирования показывают, что локальные напряжения в вершинах фьордов превышают на 1–1.5 порядка уровень приложенного напряжения. Это означает, что даже если напряжение ползучести в разы меньше условного предела текучести σ0.2 поликристаллического сплава, то в условиях стресс-коррозии локальные напряжения в приповерхностном слое коррозионного пятна могут значительно превышать предел текучести и напряжения срабатывания дислокационных источников, что может привести к пластической релаксации в области коррозионного пятна. Однако дислокационные скопления, генерируемые концентраторами напряжения, не смогут распространяться в объем материала, где σ ≈ σ0 < σ0.2. Если напряжение ползучести σ0 > > σ0.2, как в экспериментах с прерывистой ползучестью, то коллективное срабатывание большого количества дислокационных источников в вершинах фьордов в области коррозионного пятна может при определенных условиях привести к развитию макроскопической дислокационной лавины в сплавах, проявляющих прерывистую деформацию.
Как отмечалось, для этих сплавов характерно динамическое деформационное старение, поэтому дислокационная лавина в объеме материала может распространяться в случае, если скорость дислокации превысит скорость диффузионного потока атомов примеси к дислокациям по механизму восходящей диффузии. Анализ процесса взаимодействия примесных атомов и малых преципитатов с дислокациями, приводящего к развитию прерывистой деформации, выходит за рамки настоящей работы; в течение многих лет он является предметом дискуссии о природе прерывистого течения металлических сплавов [17–22]. Отметим, что выявленные методом компьютерного моделирования дальнодействующие корреляции во фрактальной структуре концентраторов напряжения должны привести к корреляции активности дислокационных источников. Срабатывание источника в вершине острого фьорда может активизировать соседние (не только ближние) источники, что может объяснить начальную стадию формирования дислокационной лавины. Далее роль концентраторов напряжения должна перейти к вершинам дислокационных скоплений, активных и/или заторможенных препятствиями (преципитатами и границами зерен) и т.д. Поэтому можно ожидать, что по мере продвижения фронта дислокационной лавины в объем материала роль поверхностных концентраторов напряжения в области коррозионного пятна будет падать.
ЗАКЛЮЧЕНИЕ
Развитие макроскопических неустойчивостей в виде деформационных полос, как известно, начинается от поверхностных источников дислокаций, что указывает на связь топологического и физико-химического состояния поверхности металлического сплава с механизмами его механической неустойчивости на макроуровне. В настоящей работе этот вопрос исследовался в контексте смежной практически важной проблемы влияния коррозии под напряжением на прерывистую деформацию. В этой ситуации поверхность деформируемого сплава в ходе коррозионного воздействия меняется от оптически гладкой до шероховатой (фрактальной), что провоцирует развитие макроскопического скачка деформации, как показали экспериментальные исследования на примере локального воздействия концентрированной соляной кислоты на поверхность алюминий-магниевого сплава АМг6, деформируемого в условиях ползучести. Это явление, видимо, следует рассматривать как новый пример механохимического эффекта, в котором процесс (химический) на атомно-молекулярном уровне вызывает механичную неустойчивость металла на макроуровне, что представляет самостоятельный объект исследования.
С помощью разработанной компьютерной модели растворения поликристаллического металла в жидкой агрессивной среде показано, что в процессе коррозионного воздействия реализуется морфологический переход от евклидовой (оптически гладкой) к фрактальной (шероховатой) границе коррозионного фронта с размерностью df = = 1.323 + 0.002, согласующейся по результатам микроструктурных исследований с размерностью фронта травления алюминий-магниевого сплава АМг6 концентрированным раствором соляной кислоты.
Проведены расчеты структуры полей упругих напряжений вблизи фрактальной поверхности коррозионного пятна в условиях коррозии под напряжением. Выявлены степенные законы статистических распределений локальных коэффициентов концентрации и интервалов между концентраторами, которые указывают на наличие дальнодействующих корреляций между большим числом концентраторов напряжения. Этот вывод дополнительно подтверждается результатами фрактального анализа пространственной структуры концентраторов методом нормированного размаха Херста. Наличие дальнодействующих корреляций, как предполагается, может спровоцировать коллективное срабатывание дислокационных источников и развитие макроскопической дислокационной лавины, вызывающей скачок деформации на деформационной кривой при напряжении ползучести, превышающем условный предел текучести поликристаллического сплава.
Экспериментальная часть исследования выполнена при поддержке Российского фонда фундаментальных исследований (РФФИ) (грант № 19-08-00395) на оборудовании Центра коллективного пользования ТГУ им. Г.Р. Державина при частичной поддержке Министерства науки и высшего образования Российской Федерации в рамках проекта по соглашению № 075-15-2021-709 (уникальный идентификатор проекта RF—2296.61321X0037), компьютерные исследования − при поддержке РФФИ (грант № 19-38-90145 “Аспиранты”).
Список литературы
Portevin A., Le Chatelier F. // C.R. Acad. Sci. Paris. 1923. V. 176. P. 507.
Savart F. // Ann. Chim. Fhys. 1837. V. 65. P. 337.
Andrade E.N. da C. // Proc. Roy. Soc. A. 1910. V. 84. P. 1.
Белл Дж.Ф. Экспериментальные основы механики деформируемых твердых тел. Ч. 2. М.: Наука, 1984. 432 с.
Shibkov A.A., Lebyodkin M.A., Lebedkina T.A. et al. // Phys. Rev. E. 2020. V. 102. P. 043003. https://doi.org/10.1103/PhysRevE.102.043003
Дубинин В.В., Рудзей Г.Ф. // Коррозия: материалы, защита. 2013. № 12. С. 19.
Григоренко В.Б., Морозова Л.В., Жегина И.П., Фомина М.А. // Тр. ВИАМ. 2016. Т. 7. № 43. С. 3. https://doi.org/10.18577/2307-6046-2016-0-7-1-1
Chlistovsky R., Heffeman P., Duquesnay D. // Int. J. Fatigue. 2007. V. 29. № 9–11. P. 1941. https://doi.org/10.1016/j.ijfatigue.2007.01.010
Jones K., Hoeppner D.W. // Corros. Sci. 2006. V. 48. № 10. P. 3109. https://doi.org/10.1016/j.corsci.2005.11.008
Каблов Е.Н., Старцев О.В., Медведев И.М., Панин С.В. // Коррозия: материалы, защита. 2013. № 12. С. 6.
Reboul M., Baroux B. // Mater. Corros. 2011. V. 62. P. 215. https://doi.org/10.1002/maco.201005650
Yukama H., Murata Y., Morinaga M. et al.// Acta Metall. Mater. 1995. V. 43. P. 681. https://doi.org/10.1016/0956-7151(94)00266-K
Searles J.L. // Metall. Mater. Trans. A. 2001. V. 32. P. 2859. https://doi.org/10.1007/s11661-001-1036-3
Argade G.R., Kumar N., Mishra R.S. // Mater. Sci. Eng. A. 2013. V. 565. P. 80. https://doi.org/10.1016/j.msea.2012.11.066
Vargel C. Corrosion of Aluminium. Oxford: Elsevier Ltd., 2004. 658 p.
Swann P.R., Pickering H.W. // Corrosion. 1963. V. 19. P. 369t. https://doi.org/10.5006/0010-9312-19.11.369
Cottrell A.H. // Philos. Mag. 1953. V. 44. № 355. P. 829. https://doi.org/10.1080/14786440808520347
Estrin Y., Kubin L.P. // Spatial Coupling and Propagative Plastic Instabilities / Continuum Models for Materials with Microstructure / Ed. Muhlhaus H.-B. New York: Wiley & Sons, 1995. P. 395.
Yilmaz A.J. // Sci. Technol. Adv. Mater. 2011. V. 12. P. 16. https://doi.org/10.1088/1468-6996/12/6/063001
Brechet Y., Estrin Y. // Scripta Metall. Mater. 1994. V. 31. P. 185. https://doi.org/10.1016/0956-716X(94)90172-4
Brechet Y., Estrin Y. // Acta Metall. Mater. 1995. V. 43. № 3. P. 955. https://doi.org/10.1016/0956-7151(94)00334-E
Kubin L.P., Fressengeas C., Ananthakrishna G. // Dislocations in Solids. V. 11 / Ed. Nabarro F.R.N., Hirth J.P. Elsevier Science, 2001.
Shibkov A.A., Gasanov M.F., Zheltov M.A. et al. // Int. J. Plast. V. 86. 2016. P. 37. https://doi.org/10.1016/j.ijplas.2016.07.014
Шибков А.А., Золотов А.Е. // Письма в ЖЭТФ. 2009. Т. 90. № 5. С. 412.
Shibkov A.A., Zheltov M.A., Gasanov M.F. et al. // Crystallography Reports. 2020. V. 65. № 6. P. 836. https://doi.org/10.1134/S1063774520060310
Madrigal-Canoa M., Hallena J.M., Arce-Estradaa E.M., Tu Le Manha // Comput. Mater. Sci. 2019. V. 161. P. 394. https://doi.org/10.1016/j.commatsci.2019.02.016
Brewick P.T., Kota N., Lewis A.C. et al. // Corrosion Sci. 2017. V. 129. P. 54. https://doi.org/10.1016/j.corsci.2017.09.009
Brewick P.T., DeGiorgi V.G., Geltmacher A.B., Qidwai S.M. // Corrosion Sci. 2019. V. 158. P. 108111. https://doi.org/10.1016/j.corsci.2019.108111
Edgar G. Classics on Fractals. Boulder: Westview Press, 2004.
Федер Е. Фракталы. М.: Мир, 1991. 230 с.
Хилл Р. Математическая теория пластичности. М.: Гостехиздат, 1956. 410 с.
Ivanov P.Ch., Amaral L.N., Goldberger A.L. et al. // Nature. 1999. V. 399. № 3. P. 461. https://doi.org/10.1038/20924
Lebedkina T.A., Lebyodkin M.A. // Acta Mater. 2008. V. 56. P. 5567. https://doi.org/10.1016/j.actamat.2008.07.025
Jensen H.J. Self-Organized Criticality. Cambridge: Cambridge University Press, 1998.
Bak P., Tang C., Wiessenfeld K. // Phys. Rev. A. 1988. V. 38. № 1. P. 364. https://doi.org/10.1103/PhysRevA.38.364
Дополнительные материалы отсутствуют.
Инструменты
Кристаллография