Мембраны и мембранные технологии, 2022, T. 12, № 2, стр. 151-162
Осаждение на поверхности трековых мембран гидрофобных полимерных покрытий из активной газовой фазы
Л. И. Кравец a, *, В. А. Алтынов a, М. А. Ярмоленко b, Р. В. Гайнутдинов c, V. Satulu d, B. Mitu d, G. Dinescu d
a Объединенный институт ядерных исследований, Лаборатория ядерных реакций им. Г.Н. Флерова
141980 Дубна, Россия
b Гомельский государственный университет им. Ф. Скорины
246019 Гомель, Беларусь
c Федеральный научно-исследовательский центр “Кристаллография и фотоника” Российской академии наук
119333 Москва, Россия
d National Institute for Laser, Plasma and Radiation Physics
077125 Bucharest, Romania
* E-mail: kravets@jinr.ru
Поступила в редакцию 22.11.2021
После доработки 03.12.2021
Принята к публикации 07.12.2021
- EDN: SHLZNV
- DOI: 10.1134/S2218117222020079
Аннотация
Проведено исследование поверхностных свойств и химической структуры наноразмерных покрытий, осажденных на поверхности полиэтилентерефталатных трековых мембран с помощью методов полимеризации органических соединений в плазме, магнетронного распыления и электронно-лучевого диспергирования полимеров в вакууме. Показано, что применение данных методов при использовании в качестве исходных соединений для модифицирования, обладающих низкой поверхностной энергией, позволяет получать на поверхности мембран гидрофобные покрытия. Показано, что осаждение на поверхности трековых мембран покрытий методами плазмохимической полимеризации и магнетронного распыления ведет к сглаживанию структурных неоднородностей. Осаждение покрытий методом электронно-лучевого диспергирования полимеров, напротив, вызывает повышение поверхностной шероховатости. Наблюдаемые различия в морфологии поверхностного слоя композиционных мембран связаны с размерами осаждающихся полимерных наноструктур. Установлено, что химическая структура покрытий, осажденных методом электронно-лучевого диспергирования полимеров, в большей степени соответствует структуре исходных полимеров по сравнению с покрытиями, полученными методами плазмохимической полимеризации и высокочастотного магнетронного распыления.
ВВЕДЕНИЕ
Мембранные процессы, такие как газоразделение, обессоливание воды, первапорация, разделение и выделение индивидуальных компонентов растворов, очистка и концентрирование биологически активных веществ и т.п., широко применяются во многих областях науки и техники [1–3]. Среди многообразия мембран, используемых в этих процессах, важное место занимают полимерные мембраны. Однако свойства существующих мембран зачастую не соответствуют требованиям технологических процессов, так как круг полимеров, пригодных для их производства, ограничен. Для расширения сферы применения промышленно производимых полимерных мембран проводятся работы по модифицированию их свойств, под которым понимают целенаправленное изменение состава и структуры поверхностного слоя.
Существуют различные методы модифицирования свойств полимерных материалов, в том числе и мембран, на основе физических и химических воздействий [4, 5]. В большинстве случаев для придания полимерным мембранам большей полярности проводят гидрофилизацию поверхности, в процессе которой достигается радикальное вмешательство в природу поверхностного слоя полимера [4]. Такая обработка приводит к улучшению био- и гемосовместимости поверхности мембран, что позволяет применять гидрофилизированные мембраны для очистки и концентрирования биопрепаратов, вакцин и пр. [6], а также использовать модифицированные мембраны в медицине, например, в качестве высокоэффективного биосовместимого эксплантодренажа при хирургическом лечении рефрактерной глаукомы [7] и в качестве имплантатов в хирургическом лечении буллезной кератопатии [8].
К наиболее часто используемым методам гидрофилизации относят обработку полимеров травящими растворами или парами реагентов, тепловую (в частности, лазерохимическую) обработку, обработку в плазме или пламенем [9]. Одним из наиболее простых и часто используемых методов гидрофилизации поверхности является обработка химическими реагентами. Травление полимеров обычно приводит к образованию тонкого поверхностного модифицированного слоя с большим числом функциональных групп [4]. При проведении процесса гидрофилизации для каждого полимера подбирают соответствующий травящий раствор и оптимальные условия травления. Обработка полимерных материалов с помощью повышенных температур используется как для гидрофилизации поверхности изделий, так и для модифицирования их объема. При гидрофилизации поверхности полимеров путем воздействия высоких температур одновременно используют и воздействие других факторов: химически активных растворов, различных частиц, облучения [5, 9].
Одним из современных методов модифицирования мембран является метод радиационной прививочной полимеризации (РПП), который основан на генерировании активных центров радикальной и ионной природы под действием ионизирующего излучения с последующей прививкой разнообразных полимеров из газовой фазы или из растворов мономеров [10]. РПП в основном осуществляется двумя методами. Один их них заключается в облучении полимеров в присутствии мономера − это метод прямой прививки. В другом способе прививка полимера происходит путем контакта предварительно облученного полимера с мономером. Наиболее распространенным способом получения полимеров с модифицированной поверхностью является РПП по методу предоблучения с использованием низкоэнергетических ускорителей электронов. Недостатком РПП является необходимость использования дорогостоящих источников ионизирующих излучений.
Из физических методов воздействия с целью гидрофилизации поверхности полимеров наиболее широкое применение получил метод обработки в плазме неполимеризующихся в условиях разряда газов [11, 12], преимуществом которого является изменение незначительного по величине поверхностного слоя материала благодаря малой глубине проникновения активных частиц плазмы в его объем. Основная масса полимера при этом не изменяется, что чрезвычайно важно с точки зрения сохранения механических и физико-химических свойств модифицируемых материалов. В этой связи в ряде работ, опубликованных в последнее время, с целью модифицирования свойств проведено исследование влияния плазмы на полимерные мембраны [13–15], в том числе трековые [16, 17]. Результаты исследований показывают, что воздействие плазмы неполимеризующихся газов на различные по своей природе мембраны приводит к изменению целого ряда свойств: адсорбционных, селективных, а также транспортных. Так, при действии плазмы кислорода или воздуха на поверхность полимерных мембран появляются кислородсодержащие функциональные группы, в частности, карбонильные и карбоксильные, образование которых связано с окислением концевых групп, возникающих при разрыве химических связей [18]. Это приводит к существенной гидрофилизации поверхности мембран. Смачиваемость поверхности мембран при этом повышается. Например, если угол смачивания (Θ) на исходной трековой мембране из полипропилена составляет 120°, то воздействие плазмы азота приводит к снижению Θ до 75°, плазмы воздуха – до 65°, а плазмы кислорода – до 60° [17]. Повышение смачиваемости поверхности гидрофобных мембран способствует проникновению молекул воды в поры, в результате чего водопроницаемость обработанных в плазме мембран увеличивается. Так, было найдено, что исходная полипропиленовая трековая мембрана не проницаема для воды при перепаде давления до 105 Па, а введение в поверхностный слой мембраны полярных групп способствует переносу воды через мембрану – обработанные в плазме мембраны становятся водопроницаемыми.
Однако, в некоторых мембранных процессах таких как мембранная дистилляция [19, 20], гидрофобная первапорация [21, 22], а также в процессах с использованием мембранных контакторов газ-жидкость [23, 24] для предотвращения проникновения воды в поры мембран необходимо, чтобы их поверхность была гидрофобной. Поскольку получение мембран на основе высокогидрофобных полимеров из поливинилиденфторида (ПВДФ), политетрафторэтилена (ПТФЭ) и полипропилена (ПП) затруднено, то актуальным подходом создания гидрофобных мембран является гидрофобизация поверхности мембран, изготовленных на основе гидрофильных полимеров. Для получения мембран с гидрофобной поверхностью может быть использован метод нанесения на поверхность тонких полимерных покрытий [25–27]. Такое модифицирование приводит к образованию композиционных мембран (КМ), состоящих из пористой подложки − исходной мембраны и осажденного слоя полимера. Наибольший интерес представляет разработка методов создания двухслойных композиционных мембран (ДКМ), в которых один из слоев имеет гидрофильную основу, а второй тонкий слой обладает гидрофобными свойствами. Мембраны подобного образца, наряду с традиционно применяемыми гидрофобными мембранами из ПВДФ, ПТФЭ и ПП, находят применение в процессах мембранной дистилляции для опреснения морской воды. В публикациях последних лет показано, что использование тонкого гидрофобного слоя в сочетании с толстым гидрофильным подслоем позволяет повысить производительность данного процесса за счет снижения сопротивления массообмену [28–31].
Существуют различные подходы к созданию двухслойных КМ, одним из которых является осаждение на пористую подложку слоя полимера, синтезированного в плазме [11, 12, 15]. Использование плазмы обладает большими преимуществами: позволяет регулировать толщину осажденного слоя полимера, обеспечивает его высокую адгезию, характеризуется малым временем проведения процесса и возможностью применения в качестве прекурсоров широкого круга органических и элементорганических соединений. Свойства поверхности композиционных мембран, полученных методом плазмохимического модифицирования, зависят от природы плазмообразующего соединения. Использование этого метода в случае полимеризации органических соединений, содержащих функциональные группы, позволило получить на поверхности мембран полимерные слои гидрофильной природы [32].
Для нанесения гидрофобных полимерных покрытий на поверхность мембран может быть использован целый ряд современных методов модифицирования. Наибольший интерес представляют методы формирования покрытий из активной газовой фазы. Эта группа методов включает осаждение покрытий в результате протекания реакций полимеризации адсорбированных на поверхности твердых тел низкомолекулярных органических соединений (прекурсоров), активированных под воздействием электронов, ионов, УФ-излучения, или диспергированных в результате воздействия на мишень (полимер или олигомер) концентрированного потока энергии − электронов, ионов, лазерного излучения [33, 34]. Особенностью второго подхода является одновременное протекание двух основных стадий, а именно, стадии образования летучих продуктов и стадии их активации. Указанные методы являются высокотехнологичными и позволяют регулировать структуру и состав осаждаемых слоев. Для получения гидрофобных покрытий используют материалы с низкой поверхностной энергией. К таким материалам в первую очередь относятся соединения на основе кремния и фтора.
Целью настоящей работы является сравнительное исследование поверхностных свойств и химической структуры наноразмерных полимерных покрытий, осажденных на поверхности полиэтилентерефталатных трековых мембран (ПЭТФ ТМ) путем плазмохимической полимеризации (ПП) органических прекурсоров различной природы, а также методами ВЧ-магнетронного распыления (ВЧ МР) и электронно-лучевого диспергирования (ЭЛД) полимеров в вакууме, и установление преимуществ одного из них для получения высокогидрофобных покрытий для применения композиционных мембран разработанного образца в процессах мембранной дистилляции для опреснения морской воды.
ЭКСПЕРИМЕНТАЛЬНАЯ ЧАСТЬ
В экспериментах использовали ПЭТФ ТМ с эффективным диаметром пор от 65 до 250 нм, изготовленные на основе пленки Лавсан ГОСТ 24234-80 (Владимир, Россия) толщиной 10.0 мкм. Для получения мембран исходную пленку облучали ускоренными на циклотроне положительно заряженными ионами криптона с энергией ∼3 МэВ/нуклон. Флюенс ионов варьировали от 2 × 108 до 3 × 109 см–2. Химическое травление облученной ПЭТФ-пленки проводили при температуре 75°С в водном растворе гидроксида натрия с концентрацией 3 моль/л по методике [35]. До начала травления для увеличения избирательности процесса травления треков облученную пленку подвергали воздействию УФ-излучения с максимальной длиной волны спектра испускания 310–320 нм.
Прекурсорами для модифицирования мембран методом полимеризации в плазме служили гексаметилдисилоксан (ГМДС), гексаметилдисилазан (ГМДСЗ) и 1,1,1,2-тетрафторэтан (ТФЭ) производства Aldrich Chemical Co. (USA). Использовали плазмохимическую установку, осуществляющую ВЧ-разряд с частотой 13.56 МГц. Осаждение полимеров на поверхности мембран из ГМДС и ГМДСЗ проводили при давлении паров в вакуумной камере 0.7 Па и мощности разряда 100 Вт, а из ТФЭ при давлении пара 32 Па и мощности разряда 20 Вт. В качестве газа-носителя применяли аргон. Воздействию плазмы подвергалась только одна сторона мембран. Схема установки и процедура обработки мембран в плазме подробно описаны в [36].
Мишенями для нанесения покрытий методом электронно-лучевого диспергирования служили порошки сверхвысокомолекулярного полиэтилена (СВМПЭ) со средней молекулярной массой 5 × 106 г/моль (Foresight Global FZE, UAE), политетрафторэтилена, плотность которого составляла 2.15 г/см3 (Aldrich), изотактического полипропилена со средней молекулярной массой 9.7 × 104 г/моль и плотностью 0.91 г/см3 (Polypropylene Co., Japan), полиэтилена высокого давления (ПЭВД) ГОСТ 16337-77 (Россия) и полиметилфенилсилоксана (ПМФС) ТУ 6-02-946-79 (Россия). В качестве источника электронов использовали электронно-лучевую пушку с катодом прямого накала, позволяющую формировать пучки с энергией 0.8–1.6 кэВ и площадью сечения (5–10) × × 10−4 м2. Начальное давление остаточных газов в вакуумной камере составляло 4 × 10−3 Па, температура поверхности подложки ~300 К. Схема установки и методика осаждении покрытий методом ЭЛД подробно описаны нами в [37].
Осаждение покрытий на поверхность мембран методом магнетронного распыления полимеров в вакууме проводили при мощности разряда 80 Вт. Мишенями для этой цели служили пластины из СВМПЭ и ПТФЭ толщиной 2.5 см и размером 2.5 × 3.5 см. В качестве рабочего газа использовали аргон, скорость потока которого составляла 100 см3/мин. Предварительное вакуумирование рабочей камеры проводили до давления ∼10−2 Па, рабочее давление аргона составляло 6 × 10−1 Па. Схема установки и методика нанесения покрытия методом ВЧ МР подробно описаны в работе [38].
Характеристики исходной и модифицированных мембран определяли при помощи ряда методик. Газопроницаемость (поток воздуха, прошедший через мембрану) измеряли при определенном перепаде давления (ΔP) при помощи поплавкового расходомера. По величине газопроницаемости, исходя из уравнения Хагена–Пуазейля [39]:
где Q − расход воздуха, η − вязкость воздуха, l − толщина мембраны, S − площадь мембраны, d − диаметр пор, no − плотность пор (число пор на 1 см2), применяя соответствующую программу рассчитывали газодинамический (эффективный) диаметр пор.Морфологию поверхности мембран изучали методом атомно-силовой микроскопии (АСМ) с помощью прибора NTEGRA Prima (NT-MDT, Россия). Сканирование проводили в прерывисто-контактном режиме с использованием кремниевых зондов HA FM (Tipsnano, Estonia). Поле сканирования составляло 1 × 1 мкм2 с разрешением 512 × 512 точек на изображение. Основным определяемым параметром являлась поверхностная шероховатость (среднеквадратичное отклонение профиля поверхности от базовой поверхности) Rms, рассчитанная по всем точкам скана. Для того чтобы избежать влияния пор при определении поверхностной шероховатости, исследовали также сканы меньшей площадью, не содержащие пор.
Смачиваемость поверхности мембран характеризовали значениями краевых углов по воде, измеренными с помощью установки “Easy Drop DSA100” (KRUSS, Germany) и программного обеспечения Drop Shape Analysis V.1.90.0.14. Для измерений использовали бидистиллированную воду, точность измерений составляла ±1°.
Рентгеновские фотоэлектронные спектры (РФЭС) получали с помощью прибора K-Alpha “Thermo Scientific” (USA), оснащенного полусферическим анализатором. Для возбуждения фотоэлектронов использовали рентгеновское излучение алюминиевого анода (Al Kα = 1486.6 эВ) при напряжении на трубке 12 кВ и токе эмиссии 3 мА. Положение пиков калибровали по стандартному пику С1s (284.6 эВ) [40]. Обзорные спектры регистрировали при окне пропускания 100 эВ с шагом по спектру 0.5 эВ, региональные спектры – при окне пропускания 20 эВ с шагом 0.05 эВ. Регистрацию и обработку спектров проводили с помощью программы Avantage, форму пиков аппроксимировали сверткой Гауссовой и Лоренцевой функций.
РЕЗУЛЬТАТЫ И ИХ ОБСУЖДЕНИЕ
Результаты измерений характеристик исходной ПЭТФ ТМ с диаметром пор 250 нм и композиционных мембран, полученных путем нанесения на ее поверхность покрытий из ПТФЭ методами магнетронного распыления и электронно-лучевого диспергирования исходного полимера в вакууме, приведены в табл. 1. Формирование полимерных покрытий из СВМПЭ и ПТФЭ на поверхности мембраны с помощью данных методов иллюстрируют рис. 1 и 2, на которых представлены двумерные микрофотографии поверхностного слоя мембран, полученные методом АСМ. Из представленных данных следует, что по мере увеличения толщины осажденного слоя полимера происходит более значительное уменьшение диаметра пор на поверхности мембран. Поток воздуха и, как следствие, эффективный диаметр пор композиционных мембран, рассчитываемый из величины газопроницаемости, также уменьшается с увеличением толщины покрытия (табл. 1). Наибольшее уменьшение эффективного диаметра пор происходит при нанесении покрытия методом электронно-лучевого диспергирования. Так, при осаждении покрытия из ПТФЭ толщиной 100 нм, полученным магнетронным распылением, эффективный диаметр пор образующейся композиционной мембраны уменьшается до 240 нм. Осаждение покрытия толщиной 200 нм вызывает уменьшение эффективного диаметра пор до 215 нм. При осаждении покрытия из ПТФЭ толщиной 100 нм электронно-лучевым диспергированием эффективный диаметр пор исходной мембраны уменьшается до 225 нм, а осаждение покрытия ПТФЭ толщиной 300 нм вызывает уменьшение эффективного диаметра пор до 195 нм (табл. 1).
Таблица 1.
Изменение характеристик ПЭТФ ТМ с диаметром пор 250 нм при нанесении покрытий из ПТФЭ различной толщины на ее поверхность
Параметры | Исходная ПЭТФ ТМ | Метод нанесения и толщина покрытия | |||
---|---|---|---|---|---|
ВЧ МР, 100 нм | ВЧ МР, 200 нм | ЭЛД, 100 нм | ЭЛД, 300 нм | ||
Поток воздуха при ΔР = 104 Па, мл/мин ⋅ см2 |
300 | 265 | 185 | 215 | 130 |
Эффективный диаметр пор, нм | 250 | 240 | 215 | 225 | 195 |
Пористость, % | 9.8 | 9.0 | 7.3 | 7.2 | 6.0 |
Поверхностная шероховатость Rms, нм (площадь сканирования 1 × 1 мкм2) | 7.8 | 6.4 | 5.0 | 9.6 | 16.4 |
Поверхностная шероховатость Rms, нм (область без пор) | 5.4 | 4.5 | 4.2 | 7.9 | 12.5 |
Угол смачивания, град | 65 | 111 | 110 | 130 | 150 |
Рис. 1.
Изображения поверхности ПЭТФ ТМ с диаметром пор 95 нм, полученные методом АСМ, после нанесения покрытий из СВМПЭ толщиной 75 (а) и 100 нм (б) и покрытий из ПТФЭ толщиной 100 (в) и 200 нм (г) методом магнетронного распыления исходных полимеров.
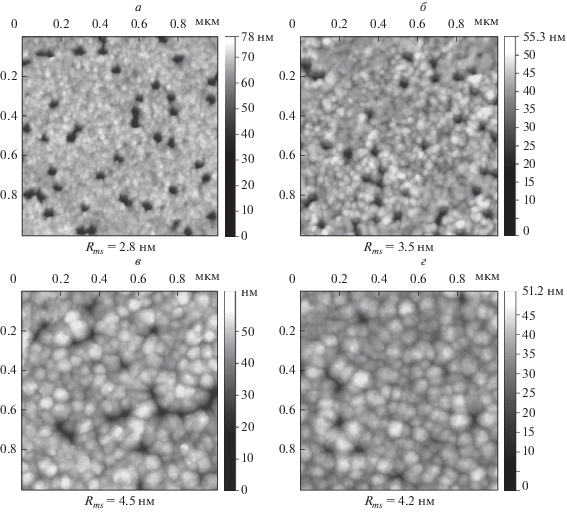
Рис. 2.
Изображения поверхности ПЭТФ ТМ с диаметром пор 250 нм, полученные методом АСМ, после нанесения покрытий из СВМПЭ толщиной 100 (а) и 200 нм (б) и покрытий из ПТФЭ толщиной 100 (в) и 300 нм (г) методом электронно-лучевого диспергирования исходных полимеров.
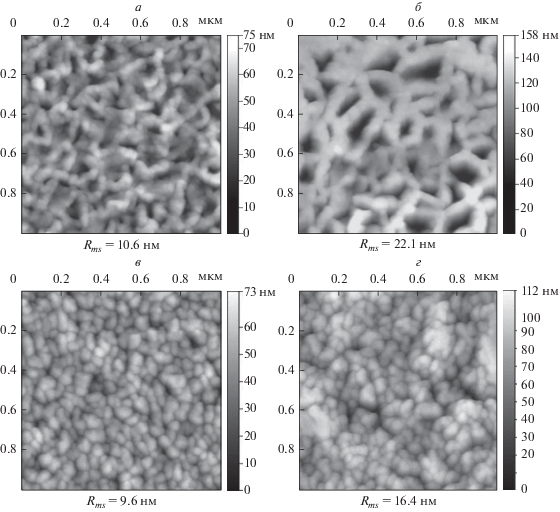
Вместе с этим, как показали экспериментальные данные, диаметр пор на обратной стороне мембран, остается неизменным. Это свидетельствует о том, что осаждение полимерных покрытий происходит лишь на стороне мембран, подвергнутых модифицированию. Нанесение на поверхность ПЭТФ ТМ покрытий методами магнетронного распыления и электронно-лучевого диспергирования полимеров в вакууме приводит, таким образом, к формированию композиционных мембран, имеющих асимметричную форму пор – диаметр пор на необработанной стороне мембран не изменяется, а на модифицированной стороне происходит его уменьшение. Аналогичные данные получены нами при исследовании модифицирования трековых мембран методом полимеризации в плазме [32].
Для практических целей при использовании мембран в процессах мембранной дистилляции при опреснении морской воды важно, чтобы осаждаемое покрытие не образовывало сплошного непористого слоя на поверхности исходной мембраны, так как это может привести к существенному снижению газопроницаемости композиционных мембран. Иными словами, композиционные мембраны должны обладать достаточной проницаемостью, сопоставимой с проницаемостью гидрофобных мембран из ПВДФ, ПТФЭ и ПП, традиционно применяемыми в процессах мембранной дистилляции. Анализ экспериментальных данных показывает, что при осаждении на поверхности ПЭТФ ТМ с эффективным диаметром пор 250 нм покрытия из ПТФЭ толщиной 100 нм, полученным магнетронным распылением и электронно-лучевым диспергированием исходного полимера, образующиеся композиционные мембраны обладают более высокой проницаемостью в сравнении с мембраной из ПВДФ с диаметром пор 0.22 мкм толщиной 50 мкм (Millipore, Germany), величина газопроницаемости которой при ΔР = 104 Па составляет 190 мл/мин ⋅ см2 [41]. Осаждение на поверхности ПЭТФ ТМ покрытий из ПТФЭ большей толщины вызывает заметное снижение проницаемости композиционных мембран (табл. 1). Данный факт следует учитывать при выборе длительности обработки ПЭТФ трековых мембран в разряде с целью гидрофобизации их поверхности. Вопрос выбора режимов обработки в разряде, таким образом, имеет два аспекта: с одной стороны, он связан с установлением длительности его воздействия, при котором изменения в поверхностном слое мембран приводили бы к заметному повышению угла смачиваемости, т.е. композиционные мембраны обладали бы высокогидрофобными свойствами. Толщина осажденного покрытия при этом должна быть достаточной для равномерного распределения по поверхности исходной мембраны. С другой стороны, необходимо выбирать длительность воздействия разряда, при которой в процессе обработки не происходило бы образования сплошного непористого слоя на поверхности исходной мембраны, значительно снижающего газопроницаемость композиционных мембран. Выбор оптимальных режимов обработки позволяет получать композиционные мембраны с гидрофобной поверхностью, обладающие достаточной проницаемостью. Это делает возможным использование их процессах мембранной дистилляции при опреснении морской воды.
Исследование морфологии поверхностного слоя КМ показывает некоторое различие процессов осаждения покрытий в зависимости от метода модифицирования. При изучении процесса нанесения полимерных покрытий плазмохимическим методом мы наблюдали сглаживание поверхностного слоя исходной мембраны [32]. Величина среднеквадратичного отклонения профиля поверхности, как показали наши исследования, уменьшается. Осаждение на поверхности трековой мембраны покрытий из СВМПЭ и ПТФЭ методом магнетронного распыления также приводит к сглаживанию структурных неоднородностей поверхностного слоя (рис. 1). Так, если для исходной мембраны с диаметром пор 65 нм величина Rms на участке беспоровой поверхности составляет 5.4 нм, то осаждение покрытия из СВМПЭ толщиной 75 нм (рис. 1а) вызывает уменьшение Rms до 2.8 нм. При увеличении толщины осажденного слоя до 100 нм (рис. 1б) величина поверхностной шероховатости равна 3.5 нм. Формирование на поверхности трековой мембраны покрытий из ПТФЭ толщиной 100 и 200 нм (рис. 1в и 1г) приводит к формированию композиционных мембран, поверхностная шероховатость которых соответственно равна 4.5 и 4.2 нм, т.е. и в этом случае значение Rms ниже чем у исходной мембраны. Следует отметить, что расчет поверхностной шероховатости по всем точкам скана площадью 1 × 1 мкм2 приводит к несколько большим значениям величины Rms, как для исходной, так и для модифицированных мембран (табл. 1). Обусловлен данный эффект наличием пор на поверхности мембраны. Уменьшение величины Rms в процессе осаждения на поверхности скана большей площадью свидетельствует, таким образом, о том, что полимерные покрытия имеют более гладкую поверхность по сравнению с поверхностью исходной мембраной.
Осаждение покрытий методом электронно-лучевого диспергирования полимеров, напротив, вызывает повышение шероховатости при возрастании их толщины (рис. 2). Так, при формировании покрытия из ПТФЭ толщиной 100 нм (рис. 2в) величина Rms составляет 9.6 нм. При увеличении толщины покрытия до 300 нм (рис. 2г) поверхностная шероховатость повышается и становится равной 16.4 нм. Осаждение покрытий из СВМПЭ толщиной 100 и 200 нм (рис. 2а и 2б) приводит к более заметному повышению поверхностной шероховатости. Соответствующие значения Rms равны 10.6 и 22.1 нм. Наблюдаемые различия в морфологии поверхностного слоя композиционных мембран, образующихся в процессе нанесения покрытий на поверхность исходной трековой мембраны, могут быть связаны, прежде всего, с размерами осаждающихся полимерных наноструктур. Наноструктуры, образующиеся на поверхности трековых мембран, при диспергировании полимеров под действием электронного пучка, имеют, как правило, существенно большие размеры, чем наноструктуры, формирующиеся при магнетронном распылении полимеров [42].
Исследование смачиваемости исходной трековой мембраны и композиционных мембран свидетельствует о некотором различии их поверхностных свойств (рис. 3). Если исходная мембрана характеризуется величиной угла смачивания по воде (Θ), равной 65°, то для ПЭТФ ТМ с покрытием из СВМПЭ толщиной 50 нм, осажденным ВЧ МР исходного полимера, значение Θ составляет 78°. Для мембраны со слоем СВМПЭ толщиной 75 нм Θ = 82°. Увеличение толщины нанесенного слоя полимера до 100 нм приводит к повышению угла смачивания до 94° (рис. 3а). Осаждение слоя полимера, полученного магнетронным распылением ПТФЭ приводит к более заметной гидрофобизации поверхности исходной мембраны. Величина угла смачивания поверхности композиционных мембран в этом случае в среднем составляет 111°. Обусловлено это более низкой поверхностной энергией ПТФЭ в сравнении со СВМПЭ. Так, для ПТФЭ поверхностная энергия составляет 18.3 мДж/м2, а для СВМПЭ эта величина равна 33.0 мДж/м2. Следует заметить, что значения краевых углов для данных покрытий ниже, чем для покрытий из СВМПЭ и ПТФЭ, полученных методом электронно-лучевого диспергирования (рис. 3б). Например, величина угла смачивания покрытия из СВМПЭ, сформированного под действием электронного пучка, в зависимости от его толщины, повышается от 92° до 125°, а для покрытия из ПТФЭ величина Θ изменяется от 130° до 155°. Такое изменение смачиваемости покрытий, обладающих гидрофобными свойствами, обусловлено ростом шероховатости их поверхности при увеличении толщины осажденного слоя полимера [43, 44]. Различие в смачиваемости покрытий, формируемых методами ВЧ МР и ЭЛД может быть также вызвано различием в химической структуре полимерных покрытий.
Рис. 3.
Изменение угла смачивания покрытий, полученных магнетронным распылением (а) и электронно-лучевым диспергированием (б) полимеров различной природы, при возрастании их толщины.
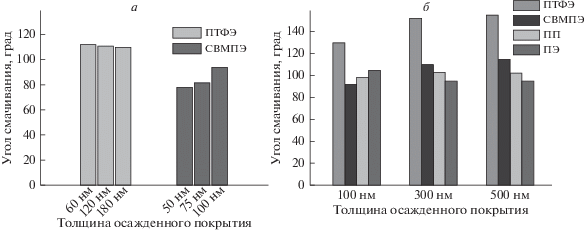
Для получения информации о химической структуре КМ были проведены исследования методом РФЭС. Анализ спектра поверхностного слоя исходной ПЭТФ ТМ показал присутствие линий, связанных с атомами углерода и кислорода, концентрация которых составляет 74.5 и 25.5%, соответственно. Разложение линии спектра C1s ПЭТФ ТМ на компоненты позволило сделать заключение, что он имеет сложный характер [37, 38]. Наиболее интенсивный компонент с максимумом энергии связи при 284.6 эВ, относительный вклад которого составляет 66.0%, соответствует углероду в составе связей С–С и С–Н. Компоненты с максимумами энергий связи при 286.3 и 288.7 эВ отвечают углероду в составе кислородсодержащих функциональных групп: C–О(H) с концентрацией 18.3% и O=C–О, концентрация которых составляет 15.7%. Значительная концентрация кислородсодержащих функциональных групп в поверхностном слое исходной ПЭТФ ТМ определяет гидрофильность ее поверхности.
Исследование методом РФЭС химической структуры покрытий из ПТФЭ, осажденных магнетронным распылением исходного полимера, показало присутствие пиков, связанных с атомами углерода и фтора, а также с незначительным содержанием кислорода и азота (табл. 2). Детальный анализ спектров C1s свидетельствует о значительном различии структуры исходного ПТФЭ и осажденных полимеров. В спектре исходного ПТФЭ (рис. 4а) присутствуют два компонента: интенсивный с максимумом энергии связи 292.1 эВ, отвечающий химическому состоянию углерода в составе групп CF2, и компонент малой интенсивности с максимумом энергии связи 284.5 эВ, который соответствует углероду в составе связей C–C. Парциальные концентрации этих состояний равны 98.5 и 1.5% соответственно. Для полимера, полученного методом магнетронного распыления ПТФЭ наблюдается уширение спектра, что свидетельствует о суперпозиции нескольких линий, соответствующих различным химическим состояниям атома углерода. Аппроксимация спектра выявила три дополнительных пика с энергией связи 286.6, 293.3 и 288.9 эВ, которые соответственно можно отнести к группам C*–CF, CF3 и связи C–F. Это свидетельствует о протекании процессов деструкции ПТФЭ, происходящих в разряде. Наличие в полимере групп CF3 указывает на присутствие макромолекул с короткими цепями [45]. Кроме этого, наличие пика, отвечающего энергии связи 286.6 эВ, может быть также обусловлено присутствием в полимерах кислородсодержащих групп C–OH и C–OR [46]. Это объясняет более низкую величину угла смачивания покрытий из ПТФЭ по сравнению с исходным полимером, для которого Θ = 120°. Концентрация групп в пленках ПТФЭ различной толщины колеблется незначительно (табл. 2).
Таблица 2.
Данные РФЭС по элементному составу полимерных покрытий
Полимер/прекурсор, применяемый для модифицирования | Метод осаждения и толщина покрытия | Содержание атомов, ат. % | ||||
---|---|---|---|---|---|---|
С | F | O | N | Si | ||
ТФЭ | ПП, 150 нм | 37.7 | 58.1 | 4.2 | – | – |
ГМДС | ПП, 150 нм | 50.5 | – | 23.4 | – | 26.1 |
ГМДСЗ | ПП, 150 нм | 54.2 | – | 15.9 | 6.0 | 23.9 |
ПП | ЭЛД, 300 нм | 98.5 | – | 1.5 | – | – |
ПЭ | ЭЛД, 300 нм | 98.3 | – | 1.7 | – | – |
СВМПЭ | ЭЛД, 300 нм | 98.7 | – | 1.3 | – | – |
СВМПЭ | ЭЛД, 500 нм | 98.4 | – | 1.6 | – | – |
ПТФЭ | ЭЛД, 100 нм | 66.9 | 33.1 | – | – | – |
ПТФЭ | ЭЛД, 300 нм | 64.5 | 35.5 | – | – | – |
СВМПЭ | ВЧ МР, 50 нм | 85.8 | – | 14.2 | – | – |
СВМПЭ | ВЧ МР, 100 нм | 84.9 | – | 15.1 | – | – |
ПТФЭ | ВЧ МР, 100 нм | 47.5 | 47.8 | 3.6 | 1.1 | – |
ПТФЭ | ВЧ МР, 200 нм | 45.7 | 49.8 | 3.4 | 1.1 | – |
Рис. 4.
Спектры РФЭС атомов С1s исходного ПТФЭ (а) и покрытий из ПТФЭ, осажденных магнетронным распылением (б) и электронно-лучевым диспергированием (в) исходного полимера.
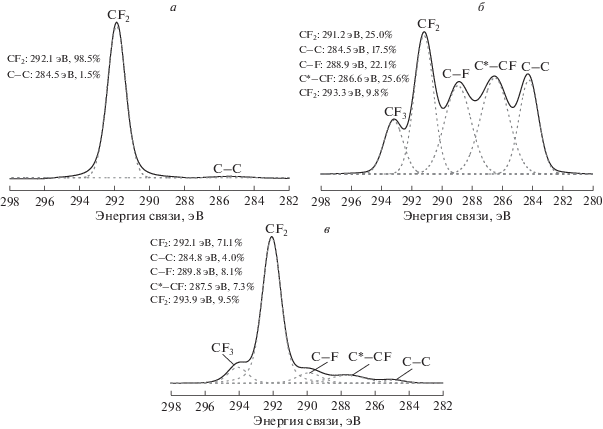
Изучение методом РФЭС химической структуры покрытий из ПТФЭ, осажденных под действием электронного пучка, показало присутствие пиков, связанных с атомами углерода и фтора (табл. 2). Данные полимеры не содержат атомов кислорода и азота, с присутствием которых связана более низкая величина угла смачивания у покрытий, осажденных методом магнетронного распыления. Детальный анализ спектра C1s покрытия из ПТФЭ, осажденного электронно-лучевым диспергированием (рис. 4в), свидетельствует о том что, он также имеет сложный характер, связанный с присутствием связей C–C (284.8 эВ) C–F (289.8 эВ) и групп CF2 (292.1 эВ), C*–CF (287.5 эВ), CF3 (293.9 эВ). Сравнение экспериментальных данных по исследованию структуры покрытий из ПТФЭ, осажденных методами ВЧ-магнетронного распыления и электронно-лучевого диспергирования ПТФЭ, показывает, что покрытия, полученные методом ЭЛД, по химическому составу более близки к исходному ПТФЭ. Для них наблюдается более высокая концентрация химических групп CF2 и значительно меньшие концентрации групп C*–CF, CF3 по сравнению с покрытиями, осажденными методом магнетронного распыления. Кроме того, на поверхности данных покрытий наблюдается значительно меньшая концентрация кислородсодержащих групп, чем на поверхности покрытий, полученных методом ВЧ МР.
Использование метода плазмохимической полимеризации с целью получения гидрофобных полимерных покрытий показало (табл. 2), что на их поверхности присутствует значительное количество кислородсодержащих, в том числе карбоксильных групп, образование которых связано с окислением при выносе образцов на воздух, а также с наличием остаточного кислорода в вакуумной реакционной камере [47]. Так, анализ спектра РФЭС слоя полимера, синтезированного в плазме 1,1,1,2-тетрафторэтана (ППТФЭ), свидетельствует о наличии пиков, связанных с атомами углерода, фтора и незначительным содержанием кислорода (табл. 2). Детальный анализ C1s спектра ППТФЭ показывает наличие химических связей C–C/C–H (284.2 эВ) и C–F (288.5 эВ), а также групп C*–CF (286.1 эВ), CF2 (291.2 эВ), содержание которых составляет 18.1, 53.9, 17.2, и 10.0% соответственно, а также незначительное количество групп CF3 (293.8 эВ), концентрация которых равна 0.8%. Следует отметить, что наличие пика, отвечающего энергии связи 286.1 эВ, может свидетельствовать о присутствии в полимере кислородсодержащих групп C–OH и C–OR. Анализ спектра F1s показывает присутствие в полимере групп CF2–CH2 (686.5 эВ), CF*–CF2 (687.4 эВ) и CF*–CF3 (690.2 эВ), концентрация которых составляет 88.7, 0.5 и 10.8% соответственно. Спектр O1s свидетельствует о присутствии карбонильных O=C (531.1 эВ) и карбоксильных групп O=C–O (533.7 эВ), содержание которых составляет 28.3, и 24.8% соответственно, а также ионов О2– (528.5 эВ), концентрация которых равна 46.9%. Это означает, что часть атомов углерода связана с кислородом.
В спектрах РФЭС покрытия, синтезированного в плазме гексаметилдисилозана (ППГМДСЗ), присутствуют пики, связанные с атомами углерода, кремния, азота и кислорода (табл. 2). Разложение спектра C1s свидетельствует о наличии в полимере связей C–Si (283.5 эВ), C–C/C–H (284.5 эВ), C–N, C–О (286.0 эВ), концентрация которых составляет 90.9, 6.1 и 3.0% соответственно. Анализ спектра Si2p показывает наличие связей Si–C (100.3 эВ), Si–N (101.6 эВ) и Si–O (102.4 эВ), концентрация которых равна 91.1, 6.2 и 2.7% соответственно. Присутствие групп С–О и Si–O означает, что часть атомов углерода и кремния находится в окисленном состоянии, что характерно для полимеров, полученных методом полимеризации в плазме. Именно с образованием кислородсодержащих групп в поверхностном слое осажденных полимеров связаны недостаточно высокие значения краевых углов. Угол смачивания поверхности осажденных покрытий при использовании в качестве прекурсоров кремний- и фторорганических соединений, как показали проведенные исследования, не превышает 100° (рис. 5).
ЗАКЛЮЧЕНИЕ
Суммируя полученные результаты, можно заключить, что нанесение на поверхность ПЭТФ ТМ покрытий путем полимеризации ГМДС, ГМДСЗ и ТФЭ в плазме, методом ВЧ-магнетронного распыления СВМПЭ и ПТФЭ, а также методом электронно-лучевого диспергирования СВМПЭ, ПТФЭ, ПП, ПЭ и ПМФС приводит к образованию композиционных мембран, состоящих из двух слоев, одним из которых является исходная полиэтилентерефталатная трековая мембрана, характеризующаяся средним уровнем гидрофильности. Второй слой имеет гидрофобную природу. Угол смачивания этого слоя, в зависимости от его толщины и используемого метода модифицирования, изменяется.
Исследование морфологии поверхностного слоя композиционных мембран показывает, что осаждение на поверхности трековых мембран покрытий методами плазмохимической полимеризации и магнетронного распыления ведет к сглаживанию структурных неоднородностей − величина среднеквадратичного отклонения профиля поверхности модифицированных мембран уменьшается. Осаждение покрытий методом электронно-лучевого диспергирования полимеров, напротив, вызывает повышение поверхностной шероховатости. Величина среднеквадратичного отклонения профиля поверхности модифицированных мембран в этом случае заметно возрастает, что обусловливает более значительное повышение угла смачивания поверхностного слоя композиционных мембран.
Изучение химической структуры покрытий показывает, что покрытия, осажденные методом электронно-лучевого диспергирования полимеров, в большей степени соответствуют структуре исходных полимеров по сравнению с покрытиями, полученными методами плазмохимической полимеризации и высокочастотного магнетронного распыления. Для покрытий, осажденных под воздействием электронного пучка, наблюдается более высокая концентрация химических групп, образующих исходные полимеры, и значительно меньшая концентрация кислородсодержащих групп.
Проведение сравнительного исследования поверхностных свойств и химической структуры наноразмерных полимерных покрытий, осажденных на поверхности полиэтилентерефталатных трековых мембран путем плазмохимической полимеризации, а также методами магнетронного распыления и электронно-лучевого диспергирования полимеров в вакууме, таким образом, показывает: наилучшими характеристиками обладают композиционные мембраны с покрытием, осажденным под воздействием электронного пучка. Осажденные покрытия такого образца обладают высокогидрофобными свойствами, химическая структура которых максимально приближена к структуре исходных полимеров.
В данной работе мы исследовали возможность создания полимерных композиционных мембран, состоящих из толстой гидрофильной основы и тонкого высокогидрофобного слоя. Мембраны такого типа обладают достаточной газопроницаемостью, сопоставимой с проницаемостью производимых промышленностью мембран из ПВДФ, ПТФЭ и ПП, и могут быть использованы в процессах мембранной дистилляции с целью опреснения морской воды. Проведение такого рода работ планируется в ближайшее время.
Список литературы
Ярославцев А.Б., Шельдешов Н.В., Заболоцкий В.И. и др. Мембраны и мембранные технологии. М.: Научный мир, 2013. 611 с.
Апель П.Ю., Бобрешова О.В., Волков А.В., Волков В.В., Никоненко В.В., Стенина И.А., Филиппов А.Н., Ямпольский Ю.П., Ярославцев А.Б. // Мембраны и мембранные технологии. 2019. Т. 9. № 2. С. 59.
Ulbricht M. // Polymer. 2006. V. 47. № 7. P. 2217.
Назаров В.Г. Поверхностная модификация полимеров. М.: МГУП, 2008. 474 с.
Modification of Polymer Properties / Ed. by Jasso-Gastinel C.F., Kenny J.M. Oxford (UK): William Andrew. 2016. 232 p.
Фатиянц Е.Х., Березкин В.В., Каграманов Г.Г. // Мембраны и мембранные технологии. 2013. Т. 3. № 1. С. 38.
Рязанцева Т.В., Кравец Л.И., Елинсон В.М. // Перспективные материалы. 2012. № 3. С. 41.
Филиппова Е.О., Карпов Д.А., Градобоев А.В., Сохорева В.В., Пичугин В.Ф. // Перспективные материалы. 2016. № 5. С. 1.
Garbassi F., Morra M., Ochiello E. Polymer surface: from physics to technology. N.Y.: John Wiley & Sons Inc, 1994. 594 p.
Кабанов В.Я. // Химия высоких энергий. 1998. Т. 38. № 2. С. 83.
Bryjak M., Gancarz I., Smolinska K. // Adv. Colloid Interface Sci. 2010. V. 161. № 1–2. P. 2.
Kravets L.I., Gilman A.B., Dinescu G. // Rus. J. Gener. Chem. 2015. V. 85. № 5. P. 1284.
Pegalajar-Jurado A., Mann M.N., Maynard M.R., Fisher E.R. // Plasma Process. Polym. 2016. V. 13. № 6. P. 598.
Shahkaramipour N., Tran T.N., Ramanan S., Lin H. // Membranes. 2017. V. 7. № 1. Article 13.
Wang J., Chen X., Reis R., Chen Zh., Milne N., Winther-Jensen B., Kong L., Dumee L.F. // Membranes. 2018. V. 8. № 3. Article 56.
Tompkins B.D., Dennison J.M., Fisher E.R. // J. Membr. Sci. 2013. V. 428. P. 576.
Kravets L., Gilman A., Yablokov M., Elinson V., Mitu B., Dinescu G. // Plasma Process. Polym. 2013. V. 10. № 7. P. 603.
Jaleh B., Parvin P., Wanichapichart P., Saffar A.P., Reyhani A. // Appl. Surf. Sci. 2010. V. 257. № 5. P. 1655.
Drioli E., Ali A., Macedonio F. // Desalination. 2015. V. 356. P. 56.
Eykens L., DeSitter K., Dotremont C., Pinoy L., Van der Bruggen B. // Sep. Purif. Technol. 2018. V. 193. P. 38.
Wu H., Zhang X., Xu D., Li B., Liang Z. // J. Membr. Sci. 2009. V. 337. P. 61.
Wang Q., Li N., Bolto B., Hoang M., Xie Z. // Desalination. 2016. V. 387. P. 46.
Баженов С.Д., Любимова Е.С. // Мембраны и мембранные технологии. 2018. Т. 6. № 33. С. 213.
Бильдюкевич А.В., Плиско Т.В., Усоский В.В., Овчарова А.А., Волков В.В. // Мембраны и мембранные технологии. 2018. Т. 8. № 2. С. 75.
Kochkodan V.M., Sharma V.K. // J. Environ. Sci. Health. Part A. 2012. V. 47. № 12. P. 1713.
Michelmore A., Steele D.A., Whittle J.D., Bradley J.W., Short R.D. // RSC Adv. 2013. V. 3. № 33. P. 13540.
Khelifa F., Ershov S., Habibi Y., Snyders R., Dubois P. // Chem. Rev. 2016. V. 116. № 6. P. 3975.
Essalhi M., Khayet M. // J. Membr. Sci. 2012. V. 417−418. P. 163.
Gancarz I., Bryjak M., Kujawski J., Wolska J., Kujawa J., Kujawski W. // Mater. Chem. Phys. 2015. V. 151. P. 233.
Korolkov I.V., Gorin Y.G., Yeszhanov A.B., Kozlovskiy A.L., Zdorovets M.V. // Mater. Chem. Phys. 2018. V. 205. P. 55.
Kravets L.I., Yarmolenko M.A., Yablokov M.Yu., Gainutdinov R.V., Altynov V.A., Lizunov N.E. // High Temp. Mater. Proc. 2020. V. 24. № 4. P. 239.
Кравец Л.И., Гильман А.Б., Satulu V., Mitu B., Dinescu G. // Перспективные материалы. 2017. № 9. С. 5.
Бильдюкевич А.В. // Полимерные материалы и технологии. 2017. Т. 3. № 4. С. 6.
Ярмоленко М.А., Рогачев А.А., Лучников П.А., Рогачев А.В., Джанг Сянь Хун. Микро- и нанокомпозиционные полимерные покрытия, осаждаемые из активной газовой фазы. / Под ред. Рогачева А.В. М.: Радиотехника, 2016. 424 с.
Apel P.Yu., Dmitriev S.N. // Adv. Natur. Sci.: Nanosci. Nanotechnol. 2011. V. 2. № 013002.
Lazea A., Kravets L.I., Dmitriev S.N., Dinescu G. // Romanian Reports in Physics. 2005. V. 57. № 3. P. 396.
Kravets L.I., Yarmolenko M.A., Rogachev A.A., Gainutdinov R.V., Altynov V.A., Lizunov N.E. // High Temp. Mater. Proc. 2019. V. 23. № 1. P. 77.
Satulu V., Mitu B., Pandele A.M., Voicu S.I., Kravets L., Dinescu G. // Appl. Surf. Sci. 2019. V. 476. P. 452.
Мулдер М. Введение в мембранную технологию. М.: Мир, 1999. 514 с.
Surface Analysis by Auger and X-Ray Photoelectron Spectroscopy / Eds by Briggs D., Grant J.T. Chichester: IM Publ. 2003. 505 p.
Dmitriev S.N., Kravets L.I., Sleptsov V.V., Elinson V.M., Potryasai V.V. // Heavy Ion Physics, FLNR Scientific Report 1999–2000. JINR Dubna, Russia. 2001. P. 225.
Kravets L., Gainutdinov R., Gilman A., Yablokov M., Satulu V., Mitu B., Dinescu G. // Plasma Phys. Technol. 2018. V. 5. № 3. P. 110.
Quere D. // Ann. Rev. Mater. Res. 2008. V. 38. P. 71.
Бойнович Л.Б., Емельяненко А.М. // Усп. хим. 2008. Т. 77. № 7. С. 619.
Bismarck A., Tahhan R., Springer J., Schulz A., Kla-potke T.M., Zell H., Michaeli W. // J. Fluor. Chem. 1997. V. 84. № 2. P. 127.
Yim J.H., Rodriguez-Santiago V., Williams A.A., Gougousi T., Pappas D.D., Hirvonen J.K. // Surf. Coat. Technol. 2013. V. 234. P. 21.
Friedrich J. // Plasma Process. Polym. 2011. V. 8. № 10. P. 783.
Дополнительные материалы отсутствуют.
Инструменты
Мембраны и мембранные технологии