Мембраны и мембранные технологии, 2022, T. 12, № 4, стр. 223-234
Влияние режимов формования на структуру и свойства половолоконных ультрафильтрационных мембран из полиэфирсульфона
А. В. Бильдюкевич a, Т. А. Глевицкая a, *, Т. Н. Невар a
a ГНУ “Институт физико-органической химии НАН Беларуси”
220072 Минск, ул. Сурганова, 13, Республика Беларусь
* E-mail: hlyavitskaya1706@gmail.com
Поступила в редакцию 17.01.2022
После доработки 22.03.2022
Принята к публикации 08.04.2022
- EDN: XLNZXB
- DOI: 10.31857/S2218117222040022
Аннотация
Изучено влияние основных параметров процесса формования половолоконных (ПВ) мембран на основе полиэфирсульфона (ПЭС) методом свободного прядения. Проанализировано влияние скорости дозирования полимерного раствора, внутреннего осадителя, высоты воздушного зазора и температуры внутреннего осадителя на геометрические размеры, структуру и транспортные свойства мембран. Показано, что варьирование указанных параметров формования позволяет в широких пределах регулировать транспортные свойства получаемых мембран: производительность по дистиллированной воде в пределах 120–950 л/м2 ч, коэффициент задерживания по ПВП К-30 в интервале 20–93%. Установлено, удельная производительность ПЭС ПВ мембран линейно возрастает с увеличением фильерной вытяжки (ФВ) волокна независимо от того, варьированием какого параметра процесса формования это достигается. Методами СЭМ и АСМ показано, что увеличение ФВ приводит к росту доли взаимосвязанных пор на селективной поверхности ПЭС ПВ мембран и трансформации формы пор от круглой к щелевидной. Проведен сравнительный анализ структуры и свойств половолоконных и плоских мембран, полученных из одного и того же состава формовочной композиции. Показано, что для плоских мембран характерна анизотропная губчатая структура, в то время как в случае полых волокон дренажный слой пронизан пальцеобразными вакуолями (макровоидами). Сделан вывод, что формирование макровоидов, а также на порядок более высокая производительность ПВ обусловлены нарушением целостности (микроразрывами) формирующегося селективного слоя в результате вытяжки волокна в воздушном зазоре.
ВВЕДЕНИЕ
Современные установки очистки воды методом низконапорной тупиковой ультрафильтрации комплектуются, как правило, мембранами в виде полого волокна (ПВ). Это объясняется достаточно высокой механической прочностью ПВ, что не требует использования опорных материалов и прокладок, как в плоскорамных модулях или сепарационных сеток в спиральных модулях. Важным преимуществом ПВ мембран является большая удельная площадь, а также плотность их упаковки (отношение активной поверхности мембран, участвующих в фильтрации, к объему модуля) в мембранном аппарате. Так, удельная площадь плоских мембран в плоскорамных модулях не превышает 300 м2/м3, удельная площадь плоских мембран в спиральных модулях не превышает 2000 м2/м3, в то время как использование полых волокон позволяет достичь удельной площади мембран до 20 000 м2/м3 [1].
Основной способ получения половолоконных мембран – сухо-мокрый метод формования [2]. Принципиальные отличия данного метода от мокрого способа получения листовых мембран заключаются в следующем: образование мембранной структуры происходит при контакте как с внутренним осадителем, так и с внешней коагуляционной ванной, объем внутреннего осадителя (модуль) лимитируется геометрией формирующегося первичного гелеобразного каркаса; вследствие чего формование мембран происходит в более “мягких” условиях за счет разбавления внутреннего осадителя растворителем. Как правило, для получения ПВ используют высоковязкие формовочные композиции (η > 10 Па с) с повышенной концентрацией полимера и высокими значениями степени насыщения (α*) [3–6]. Высокие значения степени насыщения формовочного раствора обеспечивают высокую скорость фазового разделения, а повышенная вязкость формовочных растворов придает дополнительную механическую прочность первичному гелеобразному каркасу, предотвращает порывы волокна и тем самым гарантирует непрерывность процесса формования.
Необходимо отметить, что при получении ПВ мембран методом свободного прядения, экструдируемый полимерный раствор подвергается дополнительной деформации под действием внешней растягивающей силы (силы тяжести и/или растягиванию волокна в результате изменения скорости вращения приемного барабана). Как правило, удлинение, индуцированное в процессе формования волокна, является причиной изменения конформации цепей полимера, и приводит к изменению их ориентации, что также должно отражаться на свойствах получаемых ультрафильтрационных мембран. Однако этому аспекту в литературе не уделено должного внимания за исключением отдельных работ, посвященных, в основном, получению половолоконных мембран для газоразделения [7, 8].
Для оценки степени вытяжки волокна в результате внешней растягивающей силы используется такой параметр как кратность вытяжки мембран φ [9]. Кратность вытяжки мембран рассчитывают как отношение площади кольцевого отверстия фильеры, через которое подается полимерный раствор к площади поперечного сечения стенок волокна:
(1)
$\varphi = \frac{{{{{\left( {d_{{{\text{наруж}}}}^{2} - d_{{{\text{внутр}}}}^{2}} \right)}}_{{{\text{фильеры}}}}}}}{{{{{\left( {d_{{{\text{наруж}}}}^{2} - d_{{{\text{внутр}}}}^{2}} \right)}}_{{{\text{ПВ}}}}}}}.$Следует отметить, что этот подход, справедливый при формовании химических волокон, по нашему мнению, не совсем применим к получению полых волокон. Как будет показано ниже, наружный и внутренний диаметр волокна существенно зависит от скорости подачи в фильеру внутреннего осадителя и раствора полимера при постоянной скорости формования. С другой стороны, при формировании пористых структур методом инверсии фаз протекают усадочные явления. Так, при получении плоских мембран путем нанесения формовочного раствора щелевой фильерой на полированную подложку с последующим погружением в коагуляционную ванну толщина сформированной пленки, как правило, существенно меньше, чем зазор фильеры, хотя в данном случае вытяжка отсутствует. При формировании структуры полого волокна в воздушном зазоре только под действием силы тяжести (метод свободного прядения), вытяжка волокна невелика и вместо этого используют фильерную вытяжку (ФВ) или степень вытяжки (drawing ratio, DR), по сути представляющие собой отношение одних и тех де величин [10–12]. ФВ представляет собой отношение разности между линейной скоростью формования волокна (v) и скоростью истечения формовочного раствора из кольцевого отверстия фильеры (v1) к скорости истечения раствора (v1):
Степень вытяжки волокна определяют, как отношение линейной скорости формования волокна к скорости истечения прядильного раствора из фильеры:
Литературные данные о влиянии вытяжки на размер пор, структуру поддерживающего слоя и производительность мембран весьма противоречивы [9, 13–17]. Авторы [9] установили, что при высоких значениях кратности вытяжки мембран (φ > 15) полые волокна, полученные из системы ПЭС-диэтиленгликоль-НМП (соотношение компонентов 23 : 36 : 41) обладают полностью губчатой структурой. К сожалению, авторы работы не приводят данных о влиянии вытяжки мембран на их транспортные свойства. В [13] на примере мембран из поливинилиденфторида установлено, что увеличение высоты воздушного зазора с 1 до 20 см или скорости намотки сформованной нити на бобину с 3.5 до 10 м/мин подавляет образование макровоидов в структуре поддерживающего слоя мембран, приводит к уменьшению размера пор на селективной поверхности мембран, а также к сужению распределения пор по размерам. Наблюдаемые явления авторы работы связывают с усадочными явлениями формирующегося волокна. Уменьшение размера пор с увеличением скорости приема полого волокна зарегистрировано и в работе [14]. Авторы предполагали, что повышение скорости приемки волокна приводит к увеличению степени ориентации макромолекул ПВДФ и формированию менее пористой мембранной структуры. С другой стороны, в работе [15] на примере мембран из ацетата целлюлозы регистрировали увеличение среднеквадратичной и среднеарифметической шероховатости внутренней поверхности мембран, увеличение размера пор на селективной поверхности, а также возрастание производительности при увеличении скорости приемки полых волокон. Авторы [15] считают, что такое изменение свойств мембран происходит под действием напряжения растяжения, вызванного увеличением скорости приемки полых волокон на бобину.
Целью данной работы являлось установить влияние режимов формования на структуру и транспортные свойства на примере ПЭС ПВ мембран, получаемых методом свободного прядения. Новизна данного исследования заключается в том, что регулирование ФВ осуществляли путем изменения величины воздушного зазора, скорости дозирования полимерного раствора и внутреннего осадителя, а также его температуры (Твн ос). Дополнительно проанализированы различия в структуре и свойствах половолоконных и плоских мембран, полученных из одного и того же состава.
ЭКСПЕРИМЕНТАЛЬНАЯ ЧАСТЬ
Для получения мембран использовали полиэфирсульфон марки Ultrason E 6020P (Mw = = 58 000 г/моль, BASF, Германия), N,N-диметилацетамид (ДMАА, BASF, Германия), в качестве порообразователей использовали смесь глицерина (ГОСТ 6259-75) и полиэтиленгликоля ПЭГ-400 (❬Mn❭ = 400 г/моль, BASF, Германия). В качестве внутреннего осадителя использовали дистиллированную воду.
Приготовление формовочного раствора состава ПЭС/нерастворитель/растворитель осуществляли на лабораторном стенде, включающем термостатированный реактор из нержавеющей стали и верхнеприводную мешалку (IKARW 20 Digital, Германия). Температура приготовления формовочного раствора составляла 90 ± 2°С, время приготовления – 4 ч, скорость перемешивания – 1000 об. мин–1. Концентрация ПЭС в формовочном растворе составляла 25%. В качестве нерастворителя, введенного в формовочный раствор использовали смесь ПЭГ-400 и глицерина с числом осаждения 1% раствора ПЭС в ДМАА 135 г/дл [18], в количестве, обеспечивающем степень насыщения формовочного раствора – 0.94 согласно методике, описанной в [18].
Мембраны получали методом инверсии фаз путем мокрого (листовые мембраны) или сухо-мокрого формования (в форме полого волокна). Для получения плоских мембран формовочный раствор наносили на стеклянную подложку или подложку из нетканого полиэфира с помощью щелевой фильеры с толщиной зазора 200 µm. Температура коагуляционной ванны составляла 20, 39 или 85°C.
Сформованные мембраны отмывали от остатков растворителя в течении 24 ч, после чего импрегнировали 30% водным раствором глицерина для предотвращения контракции пор.
Получение половолоконных мембран осуществляли на стендовой установке Института физико-органической химии НАН Беларуси, внешний вид которой представлен на рис. 1. Оборудование для получения ПВ мембран включает систему термостатируемых приемно-подающих емкостей и патрубков для формовочного раствора (1, рис. 1) и осадителя (2, рис. 1), стойку с фильерным узлом (3, рис. 1) и приемную ванну с водопроводной водой, T = 15°C (4, рис. 1). Подача в фильеру формовочной композиции и внутреннего осадителя (воды) осуществляется сжатым воздухом, давление которого контролируется манометрами (5, рис. 1). В системе отсутствует сматывающее устройство, волокно формуется под действием силы тяжести.
Рис. 1.
Установка для получения половолоконных мембран, где 1 – емкость для формовочного раствора; 2 – емкость для внутренней осадительной ванны; 3 – фильера; 4 – приемная ванна; 5 – манометры 6 – датчик температуры внутреннего осадителя; 7 – термостат.
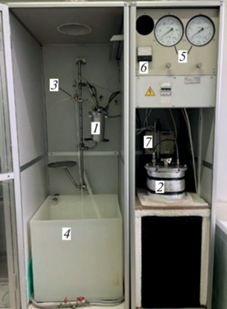
Формование полых волокон осуществлялось при различных режимах: скорость дозирования раствора полимера варьировали в диапазоне 3.44–6.0 г/мин, давление осадителя – 30–60 кПа, температуру внутреннего осадителя – 20–85°С, температура приемной (внешней коагуляционной) ванны – 15°С, высота воздушного зазора от фильеры до приемной ванны –15–100 см.
Поскольку в используемом методе формования отсутствовало дозирующее оборудование (насос подачи прядильного раствора) и приемная бобина, то для определения линейной скорости формования волокна определяли длину волокна, сформованного за 1 мин при фиксированном расстоянии от фильеры до приемной ванны. Для этого поступали следующим образом: формующееся волокно отрезали на границе раздела воздух – приемная коагуляционноя ванна с интервалом 1 мин и измеряли длину сформованного волокна. Таким образом определяли линейную скорость формования волокна, которая адекватна скорости приема сформованной нити на бобину в традиционном процессе формования химических волокон.
где l – длина волокна, сформованного за 1 мин, м; t – время, мин.Т.к. в качестве движущей силы для подачи формовочного раствора использовался сжатый воздух при определенном давлении, а не дозирующий насос, то для определения скорости истечения прядильного раствора из отверстий фильеры поступили следующим образом. Измеряли массу сформованного высушенного волокна за единицу времени. Затем, зная плотность и концентрацию раствора, определяли его объем и скорость его дозирования
где m – масса высушенного волокна, г; ρ – плотность, г/см3.Скорость истечения прядильного раствора из отверстий фильеры (v1) рассчитывали по формуле
где S – площадь поперечного сечения кольцевого отверстия фильеры (м2) расчитывали по формуле: где D – наружный диаметр канала фильеры, м; d – внутренний диаметр канала фильеры, м.Далее по формуле (2) рассчитывали ФВ.
Удельную производительность мембран (J0, л/м2 ч) вычисляли по формуле:
где V – объем фильтрата, л; S – площадь рабочей поверхности мембраны, м2; t – время фильтрации, ч.Коэффициент задерживания вычисляли по формуле:
где Сф – концентрация калибранта в фильтрате, г/л; Сисх – концентрация калибранта в исходном растворе, г/л. В качестве калибранта использовали 0.3% водный раствор поливинилпирролидона марки К-30 (Fluka, Германия).Изучение геометрических размеров и морфологии мембран проводили на растровом электронном микроскопе Phenom Pro (Thermo Fisher Scientific), осуществляя предварительную пробоподготовку методом криогенного разлома в жидком азоте, с последующим нанесением слоя золота посредством катодного распыления в вакуумной установке Vac Coat DSR1 (Иран).
Структуру внешней поверхности селективного слоя мембран изучали методом атомно-силовой микроскопии (NT-206, Mikrotest mashines, Belarus) с использованием стандартных кремниевых кантилеверов NSC35 (Mikromasch, Estonia) с радиусом кривизны зонда не более 10 нм и жесткостью 3.5 N/m (согласно паспорту производителя).
РЕЗУЛЬТАТЫ И ОБСУЖДЕНИЕ
Как уже отмечалось выше, управлять структурой и свойствами полых мембран возможно путем варьирования следующих переменных: величиной воздушного зазора, скоростью дозирования полимерного раствора и внутреннего осадителя и его температуры (Твн ос). Экспериментальные данные по влиянию указанных переменных на характеристики получаемых половолоконных мембран приведены в табл. 1–4.
Таблица 1.
Зависимость свойств половолоконных мембран от высоты воздушного зазора. Скорость дозирования формовочного раствора – 4.04 г/мин, давление подачи внутреннего осадителя – 45 кПа, Твн ос – 39°С
Н, см | Скорость формования волокна, м/мин | ФВ, % | Dвнутр, мм | L, мм | J0, л/м2 ч | RПВП,% |
---|---|---|---|---|---|---|
15 | 3.16 | 46.2 | 1.23 | 0.25 | 300 | 45.9 |
30 | 3.25 | 55.3 | 1.17 | 0.25 | 350 | 43.4 |
40 | 3.26 | 56.7 | 1.15 | 0.25 | 363 | 37.9 |
50 | 3.30 | 57.5 | 1.13 | 0.24 | 445 | 36.4 |
60 | 3.32 | 64.6 | 1.12 | 0.24 | 492 | 37.6 |
70 | 3.34 | 71.6 | 1.10 | 0.23 | 492 | 40.4 |
80 | 3.40 | 72.1 | 1.09 | 0.23 | 541 | 35.8 |
90 | 3.46 | 73.9 | 1.00 | 0.22 | 530 | 43.4 |
100 | 3.52 | 84.4 | 0.92 | 0.22 | 579 | 34.0 |
Таблица 2.
Зависимость свойств половолоконных мембран от скорости дозирования формовочного раствора (VФР). Давление подачи внутреннего осадителя – 50 кПа, величина воздушного зазора – 70 см, Твн ос – 39°С
VФР, г/мин | Скорость формования волокна, м/мин | ФВ, % | D, мм | L, мм | J0, л/м2 ч | RПВП,% |
---|---|---|---|---|---|---|
3.44 | 3.24 | 66.7 | 1.04 | 0.23 | 570 | 51 |
4.04 | 3.83 | 67.8 | 1.01 | 0.24 | 520 | 52 |
4.64 | 4.25 | 62.1 | 1.02 | 0.25 | 540 | 55 |
5.20 | 4.57 | 55.6 | 1.12 | 0.25 | 480 | 57 |
6.00 | 4.83 | 42.5 | 1.05 | 0.25 | 445 | 60 |
Таблица 3.
Зависимость свойств половолоконных мембран от давления подачи внутреннего осадителя. Скорость дозирования формовочного раствора – 4.04 г/мин, величина воздушного зазора – 70 см, Твн ос – 39°С
Рвн ос, кПа | Скорость формования волокна, м/мин | ФВ, % | D, мм | L, мм | J0, л/м2ч | RПВП,% |
---|---|---|---|---|---|---|
30 | 3.47 | 50.5 | 0.98 | 0.26 | 350 | 67 |
40 | 3.73 | 66.7 | 1.00 | 0.23 | 420 | 59 |
50 | 3.83 | 67.8 | 1.01 | 0.24 | 520 | 52 |
60 | 4.02 | 76.1 | 1.10 | 0.20 | 605 | 43 |
Таблица 4.
Зависимость свойств половолоконных мембран от температуры внутреннего осадителя. Величина воздушного зазора – 70 см, давление подачи внутреннего осадителя – 50 кПа
ТВН ОС, °С | VФР, г/мин | Скорость формования волокна, м/мин | ФВ, % | D, мм | L, мм | J0, л/м2 ч | RПВП,% |
---|---|---|---|---|---|---|---|
20 | 3.00 | 2.2 | 29.8 | 0.99 | 0.24 | 120 | 93 |
39 | 4.64 | 4.25 | 62.1 | 1.02 | 0.25 | 520 | 52 |
57 | 5.20 | 5.13 | 74.6 | 1.13 | 0.23 | 560 | 45 |
70 | 5.48 | 5.78 | 100.7 | 1.12 | 0.22 | 730 | 24 |
85 | 6.08 | 6.94 | 102.0 | 1.15 | 0.25 | 920 | 20 |
Зависимость величины ФВ, а также свойств мембран от высоты воздушного зазора (Н) приведена в табл. 1. Как видно, увеличение высоты воздушного зазора с 15 до 100 см при прочих фиксированных условиях формования (температура внутреннего осадителя, скорость дозирования формовочного раствора, давление подачи внутреннего осадителя) приводит к возрастанию ФВ с 46.2 до 84.4% и оказывает существенное влияние на геометрические размеры ПВ мембран. С увеличением ФВ регистрируется как уменьшение внутреннего диаметра, так и толщины стенки волокна. С увеличением высоты воздушного зазора происходит увеличение удельной производительности мембран по воде, при этом коэффициент задерживания мембран по ПВП варьируется в достаточно узком диапазоне 34.0–45.9%.
На рис. 2 приведены структуры поперечного сечения ПЭС мембран в зависимости от высоты воздушного зазора. Мембраны имеют ярко выраженную анизотропную структуру: в канале волокна расположен тонкий селективный слой (скин-слой), за которым следуют пенообразный переходный слой и высокопористый дренажный. Дренажный слой пронизан большим количеством пальцеобразных вакуолей (макровоидов). При этом с увеличением высоты воздушного зазора регистрируется постепенное возрастание общей ширины переходного слоя мембран, уменьшается количество и размер макровоидов в поддерживающем слое, увеличивается их ширина, а также увеличивается ширина перегородок между макровоидами (рис. 2), что хорошо согласуется с литературными данными [13, 14]. Установлено, что селективная поверхность ПЭС ПВ мембран имеет четко выраженную ориентацию в направлении оси волокна, при этом с увеличением фильерной вытяжки форма пор на поверхности селективного слоя изменяется от круглой (диаметр пор не превышает 0.3–0.5 мкм) до щелевидной (продольный размер пор достигает 1.0–1.2 мкм), см. рис. 2. Полученные результаты хорошо согласуются с данными АСМ-микроскопии, приведенными на рис. 3. Как видно, структурные элементы на поверхности селективного слоя имеют четко выраженную ориентацию в направлении оси волокна, при этом с увеличением фильерной вытяжки регистрируется незначительное уменьшение площади щелеобразных углублений [14].
Рис. 2.
Электронные микрофотографии поперечных сколов и внутренней селективной поверхности ПВ ПЭС мембран, полученных при различной величине воздушного зазора: (а) 15 см (ФВ = 46.2%); (б) 40 см (ФВ = 56.7%); (в) 70 см (ФВ = 71.6%); (г) 100 см (ФВ = 84.4%).
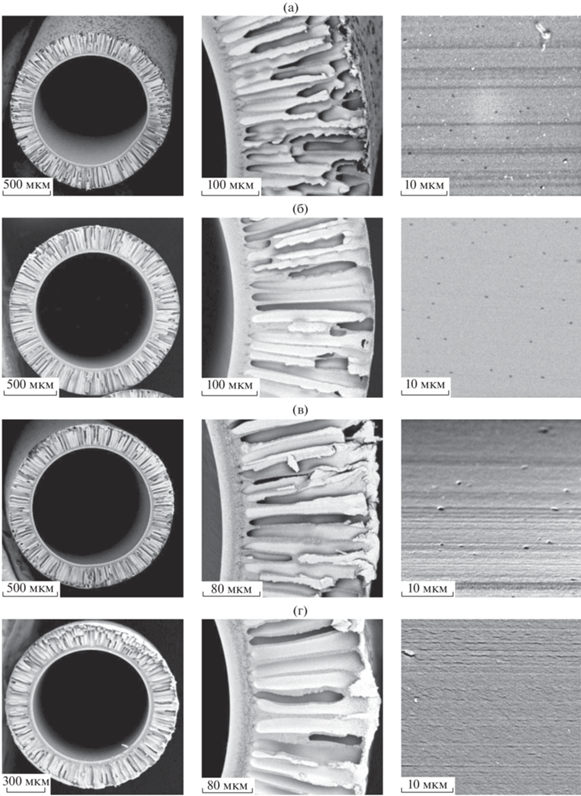
Рис. 3.
АСМ изображения селективной поверхности ПЭС мембран, полученных при различной величине воздушного зазора: (а) 40 см (ФВ = 46.2%); (б) 60 см (ФВ = 64.6%); (в) 100 см (ФВ = 84.4%).
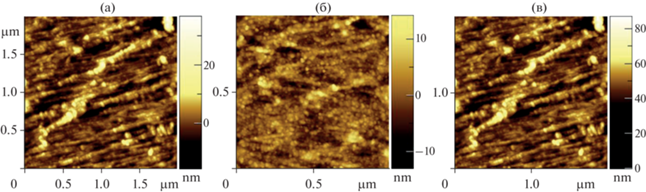
В табл. 2 представлена зависимость геометрических размеров и транспортных свойств ПЭС мембран от скорости дозирования формовочного раствора (VФР) при прочих фиксированных условиях формования (температура раствора полимера, температура и давление внутреннего осадителя, величина воздушного зазора и др.). Увеличение скорости дозирования формовочного раствора с 3.44 до 6.00 г/мин приводит к снижению производительности мембран с 570 до 445 л/м2 ч, при этом коэффициент задерживания мембран по ПВП К-30, внутренний диаметр (D) и толщина стенок волокна (L) варьируются в достаточно узких пределах: R = 51–60%, D = 1.01–1.12 мм, L = 0.23–0.25 мм соответственно.
Увеличение давления подачи внутреннего осадителя (Рвн ос) с 30 до 60 кПа, наоборот, приводит к достаточно резкому повышению производительности мембран по дистиллированной воде с 350 до 605 л/м2 ч, уменьшению коэффициента задерживания мембран по ПВП, увеличению внутреннего диаметра волокна, а также к снижению толщины его стенки (табл. 3), что связано с блокированием усадочных явление полого волокна в процессе формования.
Влияние температуры внутреннего осадителя на свойства мембран продемонстрировано данными табл. 4. Как видно, повышение температуры внутреннего осадителя при прочих фиксированных параметрах приводит к увеличению удельной производительности по воде и снижению селективности мембран. Наиболее резкий рост удельной производительности мембран по воде со 120 до 520 л/м2 ч наблюдается при повышении температуры с 20 до 39°С, далее в интервале температур 39–57°С производительность мембран практически постоянна, а последующее существенное возрастание производительности мембран с 560 до 920 л/м2 ч происходит при повышении Твн ос до 85°С. Такое изменение транспортных характеристик мембран при увеличении температуры внутреннего осадителя можно объяснить возрастанием скорости массообменных процессов при фазовом разделении [10]. Следует отметить, что в используемом методе формования полых волокон дозирование внутреннего осадителя в фильеру осуществляется под действием давления. Повышение температуры внутреннего осадителя (воды) с 20 до 85°С приводит к уменьшению его вязкости с 1.005 до 0.336 мПа с и, соответственно, при фиксированном давлении подача внутреннего осадителя в фильеру возрастает [19]. Именно это является одной из причин увеличения удельной производительности по воде и уменьшения задерживания. Этим же объясняется возрастание внутреннего диаметра волокна, однако, следует отметить, что при этом не наблюдается уменьшения толщины стенок волокна. В данном случае, наряду с возрастанием подачи внутреннего осадителя, одновременно существенно возрастает и скорость дозирования формовочного раствора (табл. 4) в результате его локального разогрева в фильере и уменьшения вязкости. Так вязкость используемого формовочного раствора при 25°С составляет 45 Па с, при 45°С – 22.4 Па с, а при 60°С – 6.4 Па с.
Электронные микрофотографии поперечных сколов, внутренней и наружной поверхностей ПЭС ПВ мембран приведены на рис. 4. С увеличением температуры внутреннего осадителя с 20 до 85°С наблюдается снижение количества и длины пальцеобразных вакуолей в субструктуре мембран, возрастание толщины переходного слоя, что особенно проявляется при изменении температуры внутреннего осадителя с 20 до 39°С, что связано с возрастанием скорости массообменных процессов при фазовом разделении и увеличением ФВ с 29.8 до 102.0% [13, 14]. С увеличением ФВ в результате повышения температуры внутреннего осадителя также изменяется форма пор на поверхности селективного слоя от круглой (для ФВ = 29.8–62.1%) до щелевидной (для ФВ = = 100.7–102.0%). Обращает на себя внимание резкое изменение топологии селективного слоя при увеличении температуры внутреннего осадителя с 70 до 85°С, что обуславливает резкий рост производительности мембран по дистиллированной воде.
Рис. 4.
Электронные микрофотографии поперечных сколов (1, 2), внутренней селективной (3) и наружной (4) поверхностей ПВ ПЭС мембран, в зависимости от температуры внутреннего осадителя: (а) 20°С (ФВ = 29.8%); (б) 39°С (ФВ = 62.1%); (в) 70°С (ФВ = 100.7%); (г) 85°С (ФВ = 102.0%).
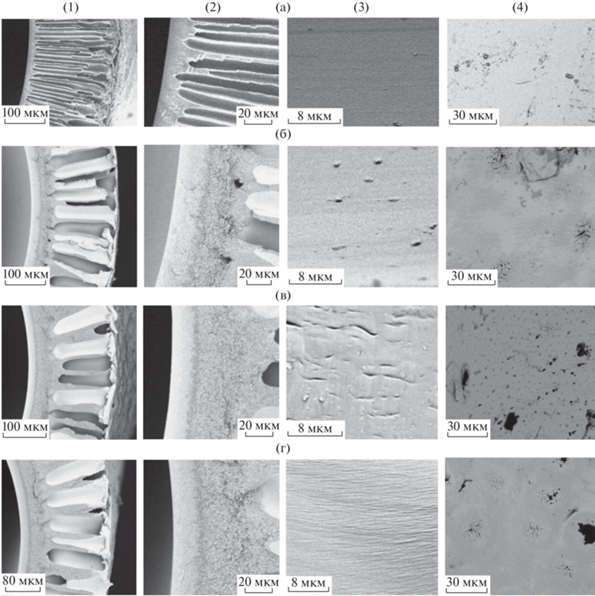
Таким образом, варьируя режимы формования возможно в широких пределах регулировать как геометрические характеристики, так и транспортные свойства половолоконных мембран. При этом указанные характеристики определяются совместным влиянием высоты воздушного зазора, скорости дозирования внутреннего осадителя, формовочного раствора, а также температурой внутреннего осадителя. При этом наиболее эффективным параметром, определяющим свойства мембран, является температура внутреннего осадителя. Как следует из табл. 4 и рис. 5 изменение данного параметра позволяет в широких пределах варьировать транспортные характеристики мембран. Анализ полученных результатов показал, что удельная производительность ПЭС ПВ мембран линейно возрастает с увеличением фильерной вытяжки (рис. 5), независимо от того, варьированием какого параметра формования ПВ достигается изменение ФВ. На наш взгляд, это связано с тем, что результате подачи внутреннего осадителя в фильеру под давлением [10, 20] блокируются усадочные явления, а при вытяжке волокна в воздушном зазоре происходит частичное разрушение формирующегося полимерного каркаса и прежде всего, микроразрывы формирующегося селективного слоя, сопровождающееся увеличением доли взаимосвязанных пор, трансформации формы пор от круглой к щелевидной и, соответственно, возрастанием производительности мембран. Данное положение хорошо согласуется с результатами СЭМ, представленными на рис. 2 и рис. 4. Увеличение ФВ с 29.8 до 62.1% приводит к увеличению размера пор в продольном направлении на селективном слое мембран с 0.1–0.3 до 0.8–1.2 мкм (см. рис. 4а, 4б), последующее увеличение ФВ (до 100.7–102.0%) приводит к тому, что селективная поверхность ПЭС ПВ мембран представлена большим количеством щелевидных пор, связанных между собой, (см. рис. 4в, 4г).
Рис. 5.
Зависимость производительности ПЭС ПВ мембран от ФВ, для различных переменных: (H) – высота воздушного зазора, (VФР) – скорость дозирования формовочного раствора, (Pвн ос) – давление подачи внутреннего осадителя, (Tвн ос) – температура внутреннего осадителя.
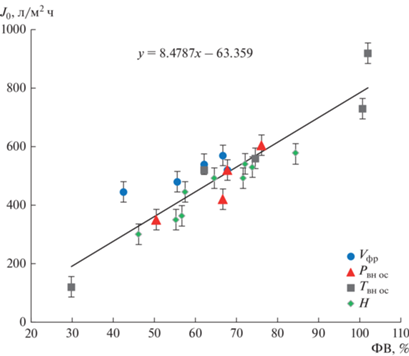
Обращает на себя внимание тот факт, что несмотря на высокое значение степени насыщения формовочного раствора (α* = 0.94) поддерживающий (дренажный) слой ПЭС ПВ мембран пронизан большим количеством макрвоидов (рис. 2 и рис. 4). Согласно [18, 21–26] мембраны, полученные из формовочных растворов с высокими значениями степени насыщения, обычно обладают выраженной губчатой структурой т.е. характеризуются отсутствием макровоидов в поддерживающем слое, что не наблюдается в случае мембран в виде полых волокон. Это может быть связано с тем, что, по мнению авторов [27], имеется некоторая критическая высота воздушного зазора, ниже которой невозможно получить структуру без макровоидов. В случае же исследуемых систем высота воздушного зазора при формовании полых волокон варьировалась в достаточно широких пределах, тем не менее, даже при максимальной высоте (100 см) фиксировали образование макровоидов в субструктуре мембран (рис. 2г). Для сравнения на рис. 6 приведены структуры поперечных сколов плоских ПЭС мембран, полученных по мокрому способу формования из этого же формовочного раствора с использованием подложки из полированного стекла при трех различных температурах коагуляционной ванны (20, 39 и 85°С). Установлено, что поперечное сечение мембран, полученных из ОВ с температурой 25 и 39°С, имеет губчатую асимметричную структуру, состоящую из селективного, переходного и дренажного слоев. При этом увеличение температуры ОВ с 25 до 39°С приводит к снижению толщины селективного и переходного слоев с 2.8 до 1.9 мкм и с 10.7 до 7.8 мкм соответственно, а также разрыхлению структуры поддерживающего слоя. Для мембран, полученных при температуре ОВ 85°С толщина селективного слоя составляет менее 50 нм, переходный слой отсутствует, а структура дренажного слоя является более однородной и пористой. При этом плоские ПЭС мембраны обладают крайне низкой производительностью по дистиллированной воде: J0 = 3 л/м2 ч (ТОВ = = 20°С), J0 = 12 л/м2 ч (ТОВ = 39°С) и 15 л/м2 ч (ТОВ = 85°С) по сравнению с полыми волокнами.
Рис. 6.
Микрофотографии поперечных сколов плоских ПЭС мембран, полученных при различных температурах осадительной ванны: (а) 20°С, (б) 39°С, (в) 85°С.
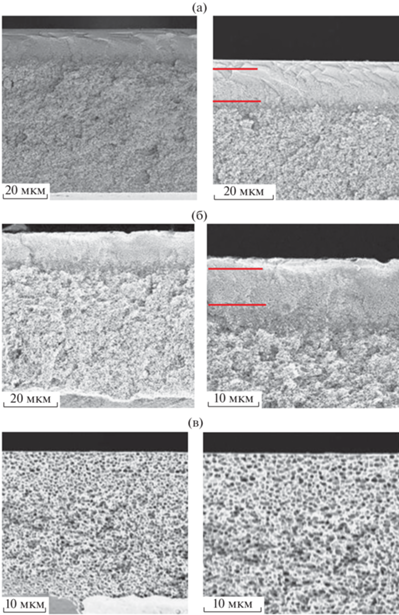
Известно, что изменяя химическую природу и рельеф поверхности подложки или армирующего материала, можно в широких пределах варьировать свойства плоских мембран [28, 29]. При переходе от подложки из полированного стекла, к нетканому армирующему материалу на основе полиэфира губчатая структура плоских мембран сохранялась, при этом производительность мембран по дистиллированной воде резко возрастает: J0 = 96 л/м2 ч (ТОВ = 20°С), J0 = 128 л/м2 ч (ТОВ = = 39°С) и 135 л/м2 ч (ТОВ = 85°С). Такое увеличение производительности связано с блокированием усадочных явлений селективного слоя мембран. Армирующая подложка создает дополнительные внутренние напряжения в свежесформованной мембране, которые и влекут изменения в структуре селективного слоя. Таким образом, более высокую производительность ПЭС ПВ мембран (120–950 л/м2 ч в зависимости от режимов формования) можно объяснить подачей внутреннего осадителя под давлением, что препятствует протеканию усадочных явлений и частичным разрушением (деформацией) формирующегося полимерного каркаса при вытяжке волокна в воздушном зазоре, что приводит к увеличением доли взаимосвязанных пор и трансформации формы пор от круглой к щелевидной.
ЗАКЛЮЧЕНИЕ
На основании полученных результатов можно сделать вывод, что как геометрические характеристики, так и транспортные свойства половолоконных мембран определяются совместным влиянием основных параметров формования методом свободного прядения (высота воздушного зазора, скорость дозирования формовочного раствора, давление подачи и температура внутреннего осадителя). Показано, что варьирование указанных параметров формования позволяет в широких пределах регулировать транспортные свойства получаемых мембран: производительность по дистиллированной воде в пределах 120–950 л/м2 ч и коэффициент задерживания по ПВП К-30 в интервале 20–93%. Установлено, удельная производительность ПЭС ПВ линейно возрастает с увеличением фильерной вытяжки (ФВ) волокна независимо от того, варьированием какого параметра процесса формования это достигается. Методами СЭМ и АСМ показано, что увеличение ФВ приводит к росту доли взаимосвязанных пор на селективной поверхности ПЭС ПВ мембран и трансформации формы пор от круглой к щелевидной. Проведен сравнительный анализ структуры и свойств половолоконных и плоских мембран, полученных из одного и того же состава формовочной композиции. Показано, что для плоских мембран характерна анизотропная губчатая структура, в то время как в случае полых волокон дренажный слой пронизан пальцеобразными макровоидами. Сделан вывод, что формирование макровоидов, а также на порядок более высокая производительность ПВ обусловлено блокированием усадочных явлений путем подачи внутреннего осадителя под давлением и нарушением целостности (микроразрывами) формирующегося селективного слоя в результате вытяжки волокна в воздушном зазоре.
Список литературы
Bodík I., Blšt'Áková A., Dančová L., Sedlìček S. // Polish J. Environmental Studies. 2009. V. 18. № 3. P. 331–340.
Alsalhy Q.F., Salih H.A., Simone S., Zablouk M., Drioli E., Figoli A. // Desalination. 2014. V. 345. P. 21–35.
Zhang H., Li B., Sun D., Miao X., Gu Y. // Desalination. 2018. V. 429. P. 33–43.
Joorabloo A., Khorasani M.T., Adeli H., Mansoori-Moghadam Z., Moghaddam A. // J. Industrial and Engineering Chemistry. 2019. V. 70. P. 253–263.
Bildyukevich A.V., Hliavitskaya T.A., Melnikova G.B. // Membranes and Membrane Technologies. 2020. V. 2. № 5. P. 283–295.
Bildyukevich A., Hliavitskaya T., Melnikova G. // J. Membrane Science and Research. 2021. V. 7. № 1. P. 45–54.
Ahmad A.L., Otitoju T.A., Ooi B.S. // J. Industrial and Engineering Chemistry. 2019. V. 70. P. 35–50.
Mubashir M., Yeong Y.F., Chew T.L., Lau K.K. // J. Applied Membrane Science & Technology. 2018. V. 22. № 2. P. 101–108.
Wang K.Y., Li D.F., Chung T.S., Chen S.B. // Chemical engineering science. 2004. V. 59. № 21. P. 4657–4660.
Бильдюкевич А.В., Плиско Т.В., Усоский В.В. // Мембраны и мембранные технологии. 2016. Т. 6. № 2. С. 113–137.
Ren J., Wang R. Preparation of polymeric membranes // Membrane and desalination technologies. Humana Press, Totowa, NJ, 2011. P. 47–100.
McKelvey S.A., Clausi D.T., Koros W.J. // J. Membrane Science. 1997. V. 124. № 2. P. 223–232.
Sukitpaneenit P., Chung T.S. // J. Membrane Science. 2011. V. 374. № 1–2. P. 67–82.
Loh C.H., Wang R. // J. Membrane Science. 2014. V. 466. P. 130–141.
Chou W.L., Yang M.C. // J. Membrane Science. 2005. V. 250. № 1–2. P. 259–267.
Zhang B., Lu C., Liu Y., Zhou P., Yu Z., Yuan S. // Polymer. 2019. V. 179. P. 121618.
Huang Y., Xiao C., Huang Q., Liu H., Zhao J. // Chemical Engineering J. 2021. V. 403. P. 126295.
Бильдюкевич А.В., Глевицкая Т.А., Мельникова Г.Б. // Мембраны и мембранные технологии. 2020. Т. 10. № 5. С. 295–308.
Pigott J.S. The Viscosity of Water at High Pressures and High Temperatures: A Random Walk through a Subduction Zone. The Ohio State University, 2011.
Матвеев Д.Н., Василевский В.П., Борисов И.Л., Волков В.В., Волков А.В. // Журн. прикладной химии. 2020. Т. 93. № 4. С. 545–555.
Ren J., Li Z., Wong F.S. // J. Membrane Science. 2004. V. 241. № 2. P. 305–314.
Liu Y., Koops G.H., Strathmann H. // J. Membrane Science. 2003. V. 223. P. 187–199.
Aroona M.A., Ismail A.F., Montazer-Rahmati M.M., Matsuuraa T. // Sep. Purif. Technol. 2009. V. 72. P. 194–202.
Kim I.-Ch., Lee K.-H. // J. Membrane Science. 2004. V. 230. P. 183–188.
Wang Z., Ma J. // Desalination. 2012. V. 286. P. 69–79.
Machado P.S.T., Habert A.C., Borges C.P. // J. Membrane Science. 1999. V. 155 P. 171–183.
Peng N., Chung T.S., Wang K.Y. Macrovoid evolution and critical factors to form macrovoid-free hollow fiber membranes // Hollow Fiber Membranes. Elsevier, 2021. P. 141–161.
Pratsenko S.A., Bildyukevich A.V., Kober K. Tshmel A. // J. Appl. Polym. Chem. 1996. V. 59. P. 1525–1528.
Lohokare H.R., Bhole Y.S., Kharul U.K. // J. Applied Polymer Science. 2006. V. 99. № 6. P. 3389–3395.
Дополнительные материалы отсутствуют.
Инструменты
Мембраны и мембранные технологии