Мембраны и мембранные технологии, 2022, T. 12, № 4, стр. 286-293
Формование многослойных мембран из одного полимера с использованием обработки ИК-излучением
А. А. Юшкин a, *, А. В. Балынин a, М. Н. Ефимов a, Д. Г. Муратов a, Г. П. Карпачева a, А. В. Волков a
a Институт нефтехимического синтеза имени А.В. Топчиева
Москва, Россия
* E-mail: Halex@ips.ac.ru
Поступила в редакцию 15.03.2022
После доработки 05.04.2022
Принята к публикации 08.04.2022
- EDN: UNDWBM
- DOI: 10.31857/S2218117222040113
Аннотация
В работе предложен новый метод послойного формования мембран из одного и того же полимера. Подход основан на использовании модификации полиакриланитрила (ПАН) под действием ИК-излучения для перевода полимера в нерастворимую форму с целью нанесения последующих слоев. Предложенный подход позволяет независимо регулировать структуру и характеристики отдельных слоев мембраны для достижения высоких эксплуатационных характеристик. Важной особенностью ИК модификации является то, что размер пор и проницаемость мембран не изменяется в результате модификации. Это позволило использовать различные условия для формирования отдельных слоев мембраны. Мембраны имели губчатую структуру поверхностного слоя и пальцевидные поры в объеме мембраны. Порог отсечения по молекулярной массе (МWСО) для мембран составил 1800 г/моль при проницаемости 38.7 л/(м2 ч атм). Размер пор полученных мембран составил 3.7 нм.
1. ВВЕДЕНИЕ
Большинство фильтрационных мембран представляют собой асимметричные по структуре материалы с тонким селективным слоем с узкими порами и макропористым подложечным слоем. В случае полимерных мембран, такая асимметрия пористой структуры формируется в процессе инверсии фаз при контакте раствора полимера с осадителем (нерастворителем) (NIPS) [1–4]. Метод NIPS является наиболее распространенным методом получения полимерных мембран [5–10]. Для обеспечения заданных разделительных характеристик мембраны вместе с хорошей механической прочностью подложечного слоя требуется проведение процесса формования мембраны при одновременном контроле многих параметров, включая состав и температуру формовочного раствора и осадительной ванны, влажность, время экспозиции и др. [1].
Так как пористая структура селективного и подложечного слоя формируется одновременно, то при очевидной технологичности (одностадийный процесс) имеются существенные ограничения этого подхода при направленном и контролируемом создании требуемой толщины и морфологии тонкопористого разделительного слоя, обеспечивающего ключевые функциональные свойства мембраны в целом – селективность и проницаемость.
Другой тип асимметричных мембран – композиционные мембраны [11–13]. В этом случае селективный и подложечный слой формируются независимо и, как правило, из разных материалов. Большинство коммерчески доступных ультрафильтрационных, нанофильтрационных и обратноосмотических мембран относятся к композиционному типу. В этом случае встает вопрос адгезии селективного слоя к материалу подложки, так как недостаточная связь между подложкой и селективным слоем может привести к разрушению целостности мембраны в процессе эксплуатации. Для решения этой проблемы при создании полимерных мембран используют различные методы модификации, такие как функционализирование поверхности подложки перед нанесением селективного слоя [14, 15], сшивка материала подложки и селективного слоя после нанесения [12, 16] и другие методы [11–13]. Это усложняет процесс получения мембран, а широкая номенклатура используемых реагентов существенно затрудняет процесс очистки и утилизации образующихся отходов такого производства по сравнению с одностадийным процессом получения мембран по методу инверсии фаз.
Целью данной работы является демонстрация возможности получения монополимерных мембран послойным формованием с использованием одного растворителя. Такой подход позволяет уменьшить количество используемых реагентов, и одновременно расширить возможности по оптимизации структуры мембраны. Использование одного полимера также уменьшает проблемы адгезии между слоями мембраны. Последовательное формование позволяет задавать на каждом этапе необходимые условия для создания оптимальной пористой структуры.
В качестве модельной системы предлагается использовать полиакрилонитрил (ПАН). Данный полимер является вторым по распространенности мембранным материалом для создания микро- и ультрафильтрационных мембран [17, 18]. Мембраны на его основе отличаются высокой прочностью, хорошей стойкостью к растворителям, термической и химической стабильностью, а также низкой стоимостью [17, 19]. По сравнению с другими мембранными материалами, например, поливинилиденфторидом, полисульфоном и полиэфирсульфоном, ПАН более гидрофилен и менее склонен к загрязнению [20–24]. Для получения мембран из ПАН обычно используют апротонные растворители, такие как диметилсульфоксид (ДМСО), н-метил-2-пирролидон (НМП), диметилформамид (ДМФА) и диметилацетамид (ДМАА) в которых данный полимер хорошо растворим.
Для перевода ПАН в нерастворимую форму, может быть использован нагрев образцов инфракрасным (ИК) излучением по методике, ранее разработанной авторами работы [6, 25–27]. Данная методика заключается в воздействии на образец ИК-излучением в течение непродолжительного времени, что приводит к нагреву образца до заданной температуры. В результате в полимерной цепи развиваются процессы циклизации, дегидрогенизации и сшивки полимерных цепей [6], которые делают материал нерастворимым. Протекающие под воздействием ИК-излучения процессы аналогичны процессам, протекающим в ПАН при традиционном конвективном нагреве, однако модификация происходит значительно быстрее и при более низких температурах [26–29]. Было показано, что нагревание мембран из ПАН до температуры 120–170°С ИК-излучением, позволяет за 5 мин обработки добиться устойчивости материала к апротонным растворителям [6]. Использование данного подхода позволяет наносить следующий слой из того же материала и растворителя, что использовались для получения первого слоя. Кроме того, данный метод модификации отличается от других методов тем, что он является безреагентным и, соответственно, минимизируются стоки, для которых необходимо использование дорогостоящих методов регенерации или утилизации.
2. ЭКСПЕРИМЕНТАЛЬНАЯ ЧАСТЬ
В работе использовали апротонные растворители (ДМСО, НМП, ДМФА и ДМАА) произведенные компанией Химмед (Россия). Указанные растворители задействованы в исследовании процесса фильтрации. ДМСО также использовали в качестве растворителя для приготовления мембран. Использованные в работе в качестве импрегнирующих агентов полиэтиленгликоль (ПЭГ) с молекулярной массой 400 г/моль, и деканол были поставлены компанией Sigma Aldrich (Германия). Растворенные вещества лизоцим (Mw = 14 кг/моль) и ПЭГ с различной молекулярной массой также произведены Sigma Aldrich. Использованные в работе изобутанол, 1-пропанол и гептан поставлены компанией Химмед.
Для синтеза полимера в работе использовали акрилонитрил производства Fluka (Швейцария). Синтез полиакрилонитрила проводили в водной среде в присутствии окислительно-восстановительной системы из пероксодисульфата аммония ((NH4)2S2O8) и дитионита натрия (Na2S2O4) в качестве инициаторов. Для этого в колбу Эрленмейера, содержащую 300 мл бидистиллированной воды последовательно добавляли серную кислоту и мономер: [H2SO4] = 1.9 × 10–2 моль/л, [акрилонитрил] = 1.27 моль/л. Инициаторы добавляли одновременно в концентрациях: [(NH4)2S2O8] = 5.88 × 10–3 моль/л, [Na2S2O4] = = 2.52 × 10–3 моль/л. Колбу взбалтывали и помещали в термостат на 40 мин при 60°C. Затем к имеющейся эмульсии добавляли 100 мл водного раствора серной кислоты и мономера с концентрациями: [H2SO4] = 1.9 × 10–2 моль/л, [акрилонитрил] = 0.66 моль/л, после чего реакция продолжалась в течение 4 ч. Выбор концентрации компонентов раствора базируется на результатах предварительных исследований по выбору оптимальных условий синтеза. В частности, чем выше концентрация инициаторов, тем меньше молекулярная масса. Уменьшение молекулярной массы полимера позволяет использовать для получения мембран более концентрированные растворы полимера, что позволяет получать мембраны с меньшим размером пор.
Исследование молекулярно-массовых характеристик полученного полимера было проведено методом ГПХ на хроматографе GPC-120 фирмы “PolymerLabs”. Анализ проводили при 50°С в ДМФА. Средняя молекулярная масса синтезированного ПАН Mw = 118 800.
Необходимые для получения формовочного раствора компоненты помещали в колбу, после чего смесь обрабатывали в ультразвуковой ванне Сапфир ТТЦ (РМД) в течение 30 мин. Далее полученную смесь перемешивали на магнитной мешалке (IKA C-MAG HS 10) в течение 72 ч со скоростью 50 об./мин при комнатной температуре (20–25°С). После истечения указанного времени на мешалке включали нагрев до 50°С и оставляли до полного растворения полимера. Для дегазации готового раствора его повторно помещали в ультразвуковую ванну на 30 мин. Полученный раствор хранился при комнатной температуре и влажности не более 25%.
Полимерный раствор с помощью ракли наносили на полированное предварительно очищенное ацетоном стекло слоем толщиной 200 мкм при температуре 20°С и влажности 20%. Далее стекло с нанесенным раствором погружали в дистиллированную воду (температура воды составляла 20°С). Полученную таким образом мембрану выдерживали в осадительной ванне в течение 5 мин после чего переносили в отмывочную ванну, заполненную дистиллированной водой и оставляли на 24 ч. Далее мембрану помещали в 1-пропанол не менее чем на 24 ч, после которого мембрану еще на 24 ч помещали в гептан. Вымоченный в гептане образец сушили в вытяжном шкафу при комнатной температуре и влажности 20%. Гептан имеет низкое поверхностное натяжение, что позволяет предотвратить схлопывание пор мембраны в процессе высушивания.
Высушенный образец помещали в лабораторную установку импульсного ИК-излучения [6]. В качестве источника некогерентного ИК-излучения использовали галогеновые лампы КГ-220 с максимумом излучения в области 0.9–1.2 мкм. 22 лампы располагались параллельно друг другу с шагом 1.5 см. Обработку проводили в атмосфере азота. Интенсивность ИК-излучения контролировали по температуре разогрева образца, измеряемой с помощью термопары хромель-алюмель, размещенной непосредственно под образцом. Блок управления обеспечивал подъем и снижение интенсивности ИК-излучения по заданной программе. Скорость нагрева до данной температуры составляла 1°С/с. После достижения максимальной температуры интенсивность излучения снижалась таким образом, чтобы поддерживать постоянную температуру образца в течение заданного времени. Как ранее было показано, для получения нерастворимой в ДМСО мембраны необходима температура обработки 170°С при времени обработки без учета нагрева и охлаждения – 5 мин [6]. После истечения указанного времени ИК-лампы выключали и образец остывал до комнатной температуры.
Для нанесения второго слоя сформированный подложечный слой мембраны приклеивали к стеклу с помощью клейкой ленты. После этого образец смачивали импрегнирующим агентом. В качестве импрегнирующих агентов были рассмотрены вода, ПЭГ, ДМСО и деканол. Вода и ПЭГ в данном случае являются осадителями для ПАН, и при этом смешиваются с полимерным раствором, причем ПЭГ имеет существенно большую вязкость. ДМСО является растворителем для ПАН и его присутствие может предотвратить преждевременное осаждение раствора в процессе нанесения, а деканол не смешивается с полимерным раствором и имеет высокую вязкость, что позволяет полностью исключить затекание полимерного раствора в поры мембраны. Для импрегнирования пор перед нанесением второго слоя первый слой полностью смачивался выбранным агентом. Излишки импрегнирующего агента удаляли с поверхности с помощью фильтровальной бумаги. Также были проведены эксперименты по нанесению второго слоя без импрегнирования.
Вторым слоем наносили 20% раствор ПАН в смеси ДМСО/ацетон 50/50. Нанесение осуществляли с помощью ракли с толщиной зазора 50 мкм. Нанесение раствора выполнялось перпендикулярно направлению формования первого слоя, что было связано с техническими особенностями используемого оборудования. После этого мембрану погружали в дистиллированную воду, далее отмывали и сушили по методике, аналогичной высушиванию первого слоя.
Размер пор в мембранах определяли на приборе POROLIQ 1000 ML. Принцип действия прибора основан на вытеснении смачивающей жидкости несмачивающей. Смачивающая и не смачивающая жидкости представляли собой насыщенные растворы воды в изобутаноле и изобутанола в воде соответственно, полученные путем расслаивания смеси воды и изобутанола в соотношении 1 : 4 при температуре проведения измерений (20°С). Межфазное поверхностное натяжение в использованной системе составляет 2 дин/см. Из мембраны вырезали образцы диаметром 2.5 см, которые помещали в изобутанол, насыщенный водой, на время не менее 12 ч. Далее образец помещали в ячейку, после чего запускали измерение, в ходе которого трансмембранное давление пошагово увеличивалось от 0 до тех пор, пока на графике зависимости потока от приложенного давления не возникала характерная S-образная кривая, свидетельствующая об открытии всех пор мембраны. На каждом шаге по давлению измерение проводилось до тех пор, пока поток не стабилизировался на одном уровне с точностью ±1 мкл/мин в течение 30 с, либо ±100 мкл/мин для потоков больше 1 мл/мин. Основным параметром, используемым в данной работе, являлся средний размер пор по потоку (Mean flow pore size – MFP). MFP определялся как такой размер пор, что 50% потока проникает через поры большего размера и 50% потока проникает через поры меньшего размера. Данный показатель выше среднечисленного размера пор, так как учитывает, что более крупные поры вносят больший вклад в общий поток через мембрану. Величина MFP рассчитывается для давления, при котором величина проницаемости равна 50% от максимального значения для данного измерения.
Также в работе определяли размер наибольшей поры, который рассчитывался для давления, при котором поток через мембрану превышал 5 мкл/мин, что чуть выше погрешности, но существенно ниже потока, наблюдавшегося через полностью смоченные мембраны (обычно – 0.3–10 мл/мин).
Разделительные характеристики мембран исследовали в тупиковом режиме фильтрации. Для снижения эффекта концентрационной поляризации в процессе фильтрации осуществлялось постоянное перемешивания раствора над мембраной с помощью системы перемешивания с магнитным приводом при скорости 600 об./мин. В качестве привода использовали магнитные мешалки (Heidolph MR Hei-Mix S). Активная площадь мембраны составляла 7.9 см2. Объем жидкости, заливаемой в ячейку составлял 900 мл. Трансмембранное давление в процессе фильтрации поддерживали на уровне 5 атм. Для всех образцов мембран фильтрацию проводили до тех пор, пока объем пермеата не достигал 90% от объема исходной смеси для чистых жидкостей и 50% для растворов.
В качестве значения проницаемости мембраны брали среднее из значений проницаемости измеренных после завершения периода начальной релаксации мембраны. Разброс значений, полученных в ходе одного эксперимента не превышал 5%, а разброс характеристик разных образцов, полученных в идентичных условиях не превышал 9%. Для первичной оценки проницаемости и сравнения мембран в качестве фильтруемой жидкости использовали воду. Также в работе исследовали проницаемость мембран по апротонным растворителям: НМП, ДМСО, ДМФА и ДМАА. В качестве разделяемой смеси для оценки разделительных свойств – раствор лизоцима (молекулярная масса 14 кг/моль) в воде с концентрацией 10 мг/л. Концентрацию лизоцима измеряли на спектрофотометре ПЭ-5400УФ на длине волны 280 нм.
Для определения величины молекулярного веса отсечения (MWCO) использовали растворы ПЭГ с молекулярной массой 1, 2, 5 и 10 кг/моль в воде с концентрацией 1 г/л. Концентрация ПЭГ в пробах определялась по методу сухого остатка. Для этого определенное количество раствора наливали в пробирку известной массы, после чего высушивали при температуре 80°С до постоянного веса.
Производительность мембраны (J), рассчитывали следующим образом:
где m – масса пермеата (г) прошедшего через мембрану с площадью S (м2) в течение времени Δt (ч), ρ – плотность жидкости (г/см3). Проницаемость мембраны (P) рассчитывали как отношение производительности мембраны (J) к приложенному трансмембранному давлению (Δp):Задерживающая способность мембраны (R) определяли исходя из концентрации компонента в ячейке (сf) и пермеате (сp):
Измерения толщины проводились на микрометре Mitutoyo 273 Quick Step с точностью ±3 мкм.
Исследования механических характеристик пленок проводили с помощью разрывной машины TT-1100 (Cheminstruments, США) при комнатной температуре (25°С). Скорость перемещения траверсы составляла 3.8 см/мин. Образцы представляли собой куски пленок прямоугольной формы длиной около 40 мм и шириной 10 мм, закрепленных двумя концами между зажимами. Начальное расстояние между зажимами составляло 30 мм. Расчет напряжений вели на начальное сечение образца. Для каждой мембраны испытанию на прочность было подвергнуто не менее 5 образцов.
Для характеризации структуры и морфологии мембран был использован метод сканирующей электронной микроскопии (CЭМ). СЭМ проводилась на установке “Thermo Fisher Phenom XL G2 Desktop SEM” (США). Сколы мембран получали после предварительной пропитки мембран в изопропаноле и последующего разламывания их в среде жидкого азота. С помощью настольного магнетронного напылителя “Cressington 108 auto Sputter Coater” (Великобритания) на подготовленные образцы в вакуумной камере (~0.01 мбар) наносили тонкий (5–10 нм) слой золота. Ускоряющее напряжение при съемке микрофотографий составляло 15 кэВ. Определение средней толщины селективного слоя по полученным микрофотографиям проводилось с помощью программного обеспечения Gwyddion (ver. 2.53).
3. РЕЗУЛЬТАТЫ И ОБСУЖДЕНИЕ
В качестве первого слоя в работе были получены мембраны из 15% растворов ПАН в ДМСО. Проницаемость данных мембран по воде составляла 220 л/(м2 ч атм), размер пор, измеренный по методу вытеснения жидкость-жидкость составлял 36 нм. Задерживание лизоцима составляло 28%. Предел прочности при испытаниях образцов на разрыв составлял 10.4 МПа (табл. 1). Следует отметить, что размер наибольшей поры в таких образцах был существенно выше по сравнению со средним размером пор. Присутствие в мембране пор с размером в 5 раз больше среднего негативно сказывается на селективности таких мембран.
Таблица 1.
Характеристики полученных в работе однослойных мембран
Образец | h, мкм | σ, МПа | MFP, нм | rmax, нм | P, л/(м2 ч атм) | R, % |
---|---|---|---|---|---|---|
15% ПАН/ДМСО | 110 ± 5 | 10.4 ± 1.6 | 36 ± 4 | 166 ± 50 | 220 ± 10 | 28 |
20% ПАН/ДМСО + Ацетон | 130 ± 5 | 11.6 ± 1.2 | 3.9 ± 0.5 | 6.5 ± 0.9 | 15.8 ± 3.4 | 99 |
Помимо мембран из 15% раствора ПАН в ДМСО, в работе были получены мембраны из 20% раствор ПАН в смеси ДМСО/ацетон 50/50. Данный раствор использовали в работе для нанесения второго слоя, поэтому для сопоставления полученных характеристик из него были получены однослойные мембраны (табл. 1). Ацетон, является плохим растворителем ПАН. В то же время, благодаря высокой подвижности ацетон быстро удаляется из полимерной пленки при формовании, что способствует образованию более плотной структуры и узких пор. Мембраны, полученные с добавлением ацетона, имели существенно меньший средний размер пор и при этом размер наибольшей поры для таких мембран был ненамного больше величины MFP. Благодаря небольшому размеру пор, такие мембраны демонстрировали хорошее задерживание, но их проницаемость была ниже.
Мембраны из 15% раствора ПАН в ДМСО обрабатывали ИК-излучением при температуре 170°С в течение 5 мин для перевода материала в нерастворимую форму. После модификации средний размер пор мембран составил 35 нм, а проницаемость 216 л/(м2 ч атм), что в пределах погрешности совпадает с характеристиками мембраны до обработки. Предел прочности для модифицированных образцов при испытаниях на разрыв составлял 8.7 МПа. Для модифицированной мембраны были определены значения проницаемости апротонных растворителей (рис. 1). Полученные значения хорошо коррелируют с вязкостью фильтруемых жидкостей, что вполне ожидаемо с учетом размера пор мембран. Так, наиболее вязкие растворители ДМСО и НМП демонстрируют самую низкую проницаемость, в то время как вода, ДМФА и ДМАА в 1.7–1.9 раза менее вязкие и во столько же раз их проницаемость оказалась выше по сравнению с ДМСО и НМП.
Как и в работе [6], в результате модификации размер пор и проницаемость мембран практически не изменялась. Разница в размере пор и проницаемости мембран по сравнению с работой [6] обусловлена меньшей молекулярной массой используемого полимера, что приводит к меньшей вязкости формовочного раствора и способствует формированию более крупных пор.
Полученные результаты свидетельствуют, что модифицированные мембраны сохраняют стабильность при длительном контакте с апротонными растворителями. Это делает возможным нанесение второго слоя полимера. В случае нанесения второго слоя на сухой образец, полученные мембраны имели низкую проницаемость по воде – 0.7 л/(м2 ч атм). Из этого был сделан вывод, что в процессе нанесения происходит затекание формовочного раствора в поры первого слоя, в результате чего происходит их закупоривание. Для предотвращения этого явления были рассмотрены несколько вариантов импрегнирования пор в процессе нанесения второго слоя.
При использовании воды и ПЭГ в качестве импрегнирующих агентов проницаемость мембран составила 3.5 и 4.7 л/(м2 ч атм), что хоть и выше чем для неимпрегнированных мембран, однако также недостаточно. Кроме того, в случае воды процесс осаждения начинался еще при нанесении полимерного раствора, что приводило к формированию неоднородностей на поверхности мембраны. В случае ПЭГ такого эффекта не наблюдалось, что по всей видимости связано с высокой вязкостью данного вещества.
При использовании в качестве импрегнирующего агента ДМСО проницаемость мембран составила 17.0 л/(м2 ч атм), а размер пор мембраны – 3.6 нм, что сопоставимо с параметрами мембраны полученной в одну стадию из раствора с ацетоном. Полученные значения выше чем в других вариантах импрегнирования. В то же время, проницаемость оказалась ниже ожидаемой с учетом меньшей толщины зазора используемой ракли. Из этого был сделан вывод, что некоторое затекание полимерного раствора второго слоя в поры все же происходит.
Для предотвращения данного эффекта в качестве импрегнирующего агента был использован деканол. Данный компонент не смешивается с ДМСО и при этом имеет высокую вязкость, которая позволяет ему удерживаться в порах мембраны в процессе нанесения. Данный компонент также не смешивается с водой, но в то же время смешивается с 1-пропанолом. Таким образом, вымывание деканола из пор происходило на стадии отмывки мембран в 1-пропаноле. Деканол оказался наиболее удобным компонентом из исследованных, так как при его использовании не происходило проскальзывание полимерного раствора в процессе нанесения.
При использовании деканола в качестве импрегнирующего агента были получены двухслойные мембраны со средним размером пор MFP равным 3.7 нм и проницаемостью по воде 38.7 л/(м2 ч атм), что является наилучшим показателем среди рассмотренных вариантов импрегнирования пор при нанесении второго слоя. Предел прочности при испытаниях образцов на разрыв составлял 10.7 МПа при толщине мембраны 120 мкм. Размер наибольшей поры в таких мембранах составлял 6.5 нм, что позволяет говорить о бездефектности полученной мембраны. При фильтрации растворов Лизоцима мембрана задерживала более 99% растворенного вещества. Полученные значения размеров пор и задерживающей способности хорошо согласуются с результатами, полученными при одностадийном формовании мембран из аналогичного раствора, при этом проницаемость двухслойных мембран была более чем в 2 раза выше.
Исследование полученных мембран методом сканирующей электронной микроскопии показало, что наблюдается хорошее зацепление между отдельными слоями мембраны (рис. 2). Толщина второго слоя по данным СЭМ составила 17 мкм. Можно ожидать, что дальнейшее снижение толщины верхнего слоя может позволить повысить проницаемость мембраны без потери ее разделительных свойств. Полученные мембраны имеют выраженный губчатый слой на поверхности, наличие которого снижает вероятность появления дефектов, негативно влияющих на разделительные свойства. А пальцевидные поры в подложечном слое создают минимальное сопротивление при высокой проницаемости.
Для полученной мембраны было определено значение молекулярного веса отсечения (MWCO) с использованием растворов ПЭГ в воде (рис. 3). В результате экстраполяции полученных данных на величину задерживания равную 90% была получена оценка величины MWCO, которая составила 1800 г/моль. Такое сочетание молекулярного веса отсечения и проницаемости сопоставимо с имеющимися в открытых источниках характеристиками ультрафильтрационных мембран с близкими значениями MWCO. Согласно [30] ультрафильтрационные мембраны из полиэфирсульфона производства Microdyn Nadir с MWCO = 4000 г/моль имеют проницаемость 32.6 л/(м2 ч атм). Ультрафильтрационная мембрана Alfa Laval GR95PP с MWCO 2000 г/моль имеет проницаемость 6 кг/(м2 ч атм) [31, 32]. А композиционная мембрана Desal GK с MWCO 2000 г/моль в работе [33] продемонстрировала проницаемость 10.62 кг/(м2 ч атм).
Рис. 3.
Задерживание двухслойной ПАН мембраной растворенных веществ в зависимости от молекулярного веса.
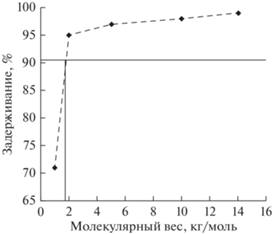
Следует отметить, что значительная часть существующих мембран с молекулярным весом отсечения менее 10 кг/моль изготавливаются из полиэфирсульфона и полисульфона [34–36], которые существенно уступает ПАН по своей устойчивости к органическим растворителям. А возможность обработки полученных мембран ИК-излучением, позволяет добиться их устойчивости к апротонным растворителям, что дополнительно расширяет область применения. Таким образом, полученные мембраны обладают уникальным сочетанием разделительных свойств, которые сложно получить с использованием одностадийного процесса осаждения.
4. ЗАКЛЮЧЕНИЕ
В рамках работы был предложен новый метод послойного формования монополимерных мембран. Разработанный метод позволяет независимо регулировать структуру и характеристики отдельных слоев мембраны для достижения высоких эксплуатационных свойств. Для получения нерастворимого подложечного слоя была использована ранее разработанная методика модификации ПАН под действием ИК-излучения. Важной особенностью модификации ИК-излучением является то, что размер пор и проницаемость мембраны не изменяется в процессе модификации.
Основная задача подложечного слоя – обеспечивать механическую прочность при сохранении высокой проницаемости. В то же время, второй слой обеспечивает разделительные свойства мембран, поэтому для получения верхнего слоя мембран необходимо использовать условия, обеспечивающие наименьший размер пор при сохранении хорошей проницаемости, что было реализовано в рамках данной работы.
Полученные мембраны имели выраженный губчатый слой на поверхности и пальцевидные поры в оставшейся части объема мембраны. Это позволило получить мембраны, сочетающие низкий молекулярный вес отсечения MWCO равный 1800 г/моль и неплохую проницаемость 38.7 л/(м2 ч атм). Размер пор полученных мембран составил 3.7 нм. Полученное сочетание молекулярного веса отсечения и проницаемости превосходит характеристики коммерческих ультрафильтрационных мембран с близкими значениями MWCO. Таким образом, мембраны продемонстрировали уникальное сочетание свойств, которое сложно получить с использованием одностадийного процесса осаждения.
Список литературы
Vandezande P., Gevers L.E.M., Vankelecom I.F.J. // Chem. Soc. Rev. 2008. V. 37. P. 365–405.
Guillen G.R., Pan Y., Li M., Hoek E.M. // Industrial & Engineering Chemistry Research. 2011. V. 50. № 7. P. 3798–3817.
Wang H.H., Jung J.T., Kim J.F., Kim S., Drioli E., Lee Y.M. // J. Membrane Science. 2019. V. 574. P. 44–54.
Garcia J.U., Iwama T., Chan E.Y., Tree D.R., Delaney K.T., Fredrickson G.H. // ACS Macro Letters. 2020. V. 9. № 11. P. 1617–1624.
Anokhina T.S., Ignatenko V.Y., Kostyuk A.V., Ilyin S.O., Volkov A.V., Antonov S.V. // Membranes and Membrane Technologies. 2020. V. 2. № 3. P. 149–158.
Yushkin A.A., Efimov M.N., Malakhov A.O., Karpacheva G.P., Bondarenko G.P., Marbelia L., Vankelecom I.F.J., Volkov A.V. // Reactive and Functional Polymers. 2021. V. 158. P. 104793.
Pérez-Manríquez L., Aburabi’e J., Neelakanda P., Peinemann K.V. // Reactive and Functional Polymers. 2015. V. 86. P. 243–247.
Bildyukevich A.V., Hliavitskaya T.A., Pratsenko S.A., Melnikova G.B. // Membranes and Membrane Technologies. 2021. V. 3. № 1. P. 24–35.
Plisko T.V., Liubimova A.S., Bildyukevich A.V., Penkova A.V., Dmitrenko M.E., Mikhailovskii V.Y., Melnikova G.B., Semenov K.N., Doroshkevich N.V., Kuzminova A.I. // J. Membrane Science. 2018. V. 551. P. 20–36.
Dibrov G., Kagramanov G., Sudin V., Grushevenko E., Yushkin A., Volkov A. // Membranes. 2020. V. 10. № 11. P. 356.
Lau W.J., Ismail A.F., Misdan N., Kassim M.A. // Desalination. 2012. V. 287. P. 190–199.
Hermans S., Mariën H., Van Goethem C., Vankelecom I.F. // Current Opinion in Chemical Engineering. 2015. V. 8. P. 45–54.
Li D., Wang H. // J. Mater. Chem. 2010. V. 20. P. 4551–4566.
Li J., Hu M., Pei H., Ma X., Yan F., Dlamini D.S., Cui Z., He B., Li J., Matsuyama H. // J. Membrane Science. 2020. V. 595. P. 117547.
Nasef M.M., Shamsaei E., Saidi H., Ahmad A., Dahlan K.Z.M. // J. Applied Polymer Science. 2013. V. 128. № 1. P. 549–557.
Lv Z., Hu J., Zheng J., Zhang X., Wang L. // Industrial & Engineering Chemistry Researchю. 2016. V. 55. № 16. P. 4726–4733.
Scharnagl N., Buschatz H. // Desalination. 2001. V. 139. № 1. P. 191–198.
Kumar M., Shevate R., Hilke R., Peinemann K.V. // Chem. Eng. J. 2016. V. 301. P. 306–314.
Tran T.D., Mori S., Suzuki M. // Thin Sol. Film. 2007. V. 515. № 9. P. 4148–4152.
Marbelia L., Mulier M., Vandamme D., Muylaert K., Szymczyk A., Vankelecom I.F. // Algal Res. 2016. V. 19. P. 128–137.
Guillen G.R., Pan Y., Li M., Hoek E.M. // Ind. Eng. Chem. Res. 2011. V. 50. № 7. P. 3798–3817.
Cornelissen E.R., Van den Boomgaard T., Strathmann H. // Coll. Surf. A. 1998. V. 138. № 2. P. 283–289.
Lohokare H., Bhole Y., Taralkar S., Kharul U. // Desalination. 2011. V. 282. P. 46–53.
Klaysom C., Hermans S., Gahlaut A., Van Craenenbroeck S., Vankelecom I.F. // J. Membrane Science. 2013. V. 445. P. 25–33.
Lee W.H., Bae J.Y., Yushkin A., Efimov M., Jung J.T., Volkov A., Lee Y.M. // J. Membrane Science. 2020. V. 613. P. 118477.
Yushkin A.A., Efimov M.N., Vasilev A.A., Ivanov V.I., Bogdanova Yu.G., Dolzhikova V.D., Karpacheva G.P., Bondarenko G.N., Volkov A.V. // Polymer Science, Series A. 2017. V. 59. № 6. P. 880–890.
Yushkin A.A., Efimov M.N., Vasilev A.A., Bogdanova Yu.G., Dolzhikova V.D., Karpacheva G.P., Volkov A.V. // Petroleum Chemistry. 2017. V. 57. № 4. P. 341–346.
Renschler C.L., Sylwester A.P., Salgado L.V. // J. Mater. Res. 1989. V. 4. № 2. P. 452–457.
Chernikova E.V., Poteryaeva Z.A., Shlyakhtin A.V., Prokopov N.I., Gerval’d A.Yu., Nikolaev A.Yu., Duflot V.R., Dubova E.A., Kostina Yu.V., Rodionov A.S., Efimov M.N., Cherevan’ A.S., Bondarenkod G.N. // Polymer Science B. 2013. V. 55. № 1–2. P. 1–13.
Cifuentes-Cabezas M., Carbonell-Alcaina C., Vincent-Vela M.C., Mendoza-Roca J.A., Álvarez-Blanco S. // Process Safety and Environmental Protection. 2021. V. 149. P. 724–734.
Cassano A., Conidi C., Ruby-Figueroa R., Castro-Muñoz R. // International J. Molecular Sciences. 2018. V. 19. № 2. P. 351.
Giacobbo A., Oliveira M., Duarte E.C., Mira H.M., Bernardes A.M., de Pinho M.N. // Separation Science and Technology. 2013. V. 48. № 3. P. 438–444.
Conidi C., Cassano A., Caiazzo F., Drioli E. // J. Food Engineering. 2017. V. 195. P. 1–13.
Zhao C., Xue J., Ran F., Sun S. // Progress in Materials Science. 2013. V. 58. № 1. P. 76–150.
Matveev D.N., Kutuzov K.A., Vasilevsky V.P. // Membranes and Membrane Technologies. 2020. V. 2. № 6. P. 351–356.
Bildyukevich A.V., Hliavitskaya T.A., Melnikova G.B. // Membranes and Membrane Technologies. 2020. V. 2. № 5. P. 283–295.
Дополнительные материалы отсутствуют.
Инструменты
Мембраны и мембранные технологии