Мембраны и мембранные технологии, 2023, T. 13, № 1, стр. 33-41
Практика изготовления асимметричной газоразделительной мембраны в виде полого волокна из поли(2,6-диметилфениленоксида-1,4)
А. В. Варежкин *
Российский химико-технологический университет им. Д.И. Менделеева
Москва, Россия
* E-mail: ale-varezhkin@yandex.ru
Поступила в редакцию 16.09.2022
После доработки 06.10.2022
Принята к публикации 07.10.2022
- EDN: HITMGO
- DOI: 10.31857/S2218117223010078
Аннотация
Проведено исследование закономерностей получения газоразделительной асимметричной мембраны в виде полого волокна из поли(2,6-диметилфениленоксида-1,4) (ПФО) методом фазовой инверсии. Характеристики мембраны получены с помощью определения газопроницаемости. Показано, что более высокие сепарационные и газотранспортные характеристики мембраны из ПФО получаются при использовании “мокрого” метода формования. В системе кислород–азот получена идеальная селективность 4.8 ± 0.4 при удельной проницаемости по кислороду (20°C) – $\left( {P{\text{/}}l} \right)$(790 ± ± 82) × 10–9 [м3(н.у.) м–2 с–1 кПа]. Разработанные мембраны перспективны для использования в системах получения азота и воздуха, обогащенного кислородом.
1. ВВЕДЕНИЕ
Асимметричная газоразделительная половолоконная мембрана представляет наукоемкий продукт, при изготовлении которого требуется учет массы нюансов. Геометрия полого волокна обеспечивает высокую плотность упаковки в мембранном аппарате, но, по мере уменьшения внешнего диаметра мембраны, существенно увеличивается трудоемкость изготовления, как самой мембраны, так и мембранного модуля [1, 2].
Работы по созданию технологии производства мембран в виде полых волокон при переработке полимера через раствор, хотя и ведутся на протяжении много лет, но в силу того, что детали такого рода исследований, обычно, имеют закрытый характер, то при решении конкретных задач необходимо самостоятельно выполнить серьезный объем экспериментов. Как правило, в работах изложены, безусловно, важные, но отдельные аспекты формования мембран. Например, влияние характеристической вязкости полимера [3] и состава коагуляционных ванн [4], конструкции фильеры [6], или постфильерной вытяжки [8] на функциональные свойства мембраны. Большее число работ посвящено пористым мембранам и водным формовочным системам [5, 7, 8]. Цель данной работы – получение оптимального режима изготовления газоразделительной мембраны с учетом наиболее важных параметров проведения формования.
Поли(2,6-диметилфениленоксид-1,4) (ПФО) один из наиболее перспективных материалов для мембранного разделения воздуха с точки зрения хороших газотранспортных и термомеханических характеристик [9, 10]. Структурная формула мономерного звена представлена на рис. 1.
2. ЭКСПЕРИМЕНТАЛЬНАЯ ЧАСТЬ
2.1. Формование половолоконных мембран
В качестве полимера использовался поли(2,6-диметилфениленоксид-1,4) (далее ПФО) PPO6130-11-0-15 (Sabic Innovative plastics/US LLC).
Для определения молекулярно-массового распределения использован метод гель проникающей хроматографии: высокотемпературный хроматограф “GPCV 2000” (Waters), оснащенный рефрактометрическим детектором и колонкой Styrogel HT 6E. Растворитель N-метилпирролидон, температура 80°C. Калибровку системы проводили с помощью полистирольных стандартов.
Результаты средних значений массы представлены в табл. 1.
Таблица 1.
Значение средних молекулярных масс PPO6130-11-0-15
Образец | Среднечисленная молекулярная масса, Mn, г/моль | Средневесовая молекулярная масса, Mw, г/моль | Mw/Mn | Z-средняя молекулярная масса, Mz, г/моль |
---|---|---|---|---|
PPO 6130 | 12 510 | 91 100 | 7.3 | 251 000 |
Мембрана изготавливалась методом фазовой инверсии. Рассмотрены варианты сухо-мокрого и мокрого формования (метод двойной коагуляционной ванны). Принципиальная схема процесса показана на рис. 2.
Рис. 2.
Принципиальная схема установки формования мембран в виде полых волокон: 1, 11 – баллон со сжатым азотом; 2, 10 – редуктор; 3 – емкость с опорным давлением для подачи нерастворителя во внутреннее пространство фильеры; 4 – фильера; 5 – фиксирующая ванна; 6 – емкость дозирования полимерного раствора; 7 – поршень; 8 – пневмоцилиндр; 9 – термостат; 12 – ведомый ролик; 14 – ведущий ролик; 13 – намоточный узел с электродвигателем и приемным колесом; 15 – промывочная ванна; 16 – емкость с внешним нерастворителем; 17 – шестеренный насос; 18 – переключатель; 19 – фильтр.
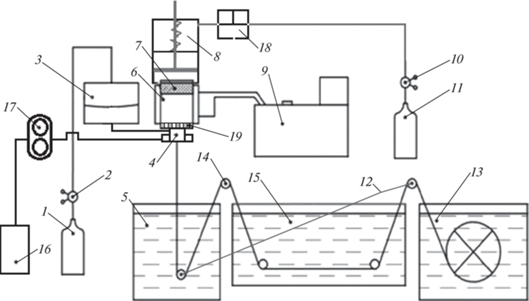
Полимерный раствор (ПР) готовился отдельно в стеклянной колбе при температуре водяной бани 70°С. Для перемешивания использовалась мешалка с верхним приводом. После полного растворения полимера колбу вынимали из водяной бани и помещали в ультразвуковую ванну для дегазации ПР. После этого ПР переливали в емкость 6 (рабочий объем в данной схеме – 160 мл), в которую предварительно устанавливали поршень 7, и термостатировали ее до температуры, при которой осуществлялось приготовление ПР. После заполнения емкости 6 ее соединяли с пневмоциллиндром 8, в который из баллона 11 подавался сжатый азот. Давление в пневмоциллиндре регулировали редуктором 10 и переключателем потока газа 18. На емкость 6 устанавливали трехкамерную фильеру 4 и разогревали ее промышленным феном до операционной температуры. После этого подавали газ в пневмоцилиндр и устанавливали операционное давление над поршнем для появления сплошной струи ПР на выходе из фильеры. Массовый расход ПР определяли на электронных весах (AND LK2000) с точностью 0.1 г и регулировали с помощью редуктора 10. Фильтр ПР 19 установлен непосредственно в емкости 6 перед фильерой 4. В режиме мокрого формования внешний нерастворитель подавали во внешнюю камеру фильеры 4 из емкости 16 с помощью шестеренного насоса 17.
После установки нужного массового расхода ПР во внутреннюю камеру фильеры подавался нерастворитель из подмембранного пространства емкости с опорным давлением 3. Опорное давление над мембраной устанавливалось сжатым азотом из баллона 1 с помощью редуктора 2.
На выходе из фильеры ПР приобретает форму полого цилиндра и в режиме пуска под воздействием силы тяжести перемещается вниз. Одновременно с этим запускаются шаговые двигатели, которые осуществляют вращение ведущего ролика 14 и колеса намоточного узла 13. Волокно проводится через первый из ведомых роликов 12, ведущий ролик 14, ведомые ролики промывочной ванны 15, второй ведомый ролик 12 и закрепляется на колесе намоточного узла 13.
После этого проводится корректировка скоростей вращения ведущего ролика 14 и колеса намоточного узла 13.
Установка позволяет изменять высоту так называемого “воздушного промежутка” h, то есть расстояние между нижней плоскостью фильеры 4 и поверхностью жидкости фиксирующей ванны 5. В случае использования режима сухо-мокрого формования ПР из фильеры вытекает непосредственно на воздух и находится там некоторое время до поступления в фиксирующую ванну 5. В случае режима мокрого формования в наружную камеру фильеры 4 из емкости 16 шестеренным насосом 17 подается нерастворитель, который в воздушном промежутке h обтекает волокно с наружной поверхности и предотвращает контакт ПР с воздухом.
В данном эксперименте использована фильера с внешним диаметром иглы 230 мкм и внешним диаметром кольцевого отверстия, через которое выходит ПР, 600 мкм. В зависимости от прочих условий формования, внешний диаметр изготовленных мембран находился в диапазоне 490–550 мкм.
2.2. Модель формирования селективного слоя
В качестве рабочей была принята модель формирования асимметричной структуры мембраны, которая представлена на рис. 3.
В момент выхода ПР (гомогенный однофазный раствор, золь 1) из фильеры, начинаются 2 типа его взаимодействия с окружающей технологической средой. Со стороны внутренней поверхности мембраны, куда поступает жесткий нерастворитель НР1, имеет место мгновенный фазовый распад, который приводит к образованию гетерогенного раствора молекулярных агрегатов (золь 2) в направлении от центра цилиндра к периферии. Со стороны наружной поверхности происходит либо испарение растворителя (сухо-мокрое формование), либо обмен растворителя ПР на нерастворитель НР2 (мокрое формование). Фазовый распад не происходит, то есть раствор остается в состоянии золь 1 (запаздывающий фазовый распад), но за время прохождения ПР в воздушном промежутке h имеет место увеличение концентрации полимера с наружной поверхности и начинается процесс гелеобразования, что типично для ПФО [11]. При достижении струи ПР жидкости фиксирующей ванны с НР1 происходит мгновенный фазовый распад и со стороны наружной поверхности, но концентрация полимера на поверхности выше исходной. По этой причине на поверхности более вероятно образование плотной структуры, то есть плотного селективного слоя [11, 12].
В соответствии с данной моделью очевидно, что эффективная толщина селективного слоя определяется интенсивностью вывода растворителя с наружной поверхности струи ПР за время прохождения им воздушного промежутка h. Этот процесс контролируется рядом параметров: типом растворителя и характером его взаимодействия с окружающей технологической средой в воздушном промежутке h, температурой ПР и временем пребывания полого волокна в воздушном промежутке h.
Предполагалось, что основной процесс, который приводит к снижению концентрации растворителя на внешней поверхности струи ПР – диффузия растворителя в воздух (сухо-мокрое формование), либо в жидкость внешнего нерастворителя НР2 (мокрое формование). Вклад в изменение концентрации растворителя в ПР за счет диффузии нерастворителя НР2 предполагался незначительным в силу высокой вязкости полимерного раствора.
2.3. Теоретический подбор растворителей и нерастворителей (осадителей)
Круг возможных растворителей для ПФО выбирали расчетным путем на основании сравнения параметров растворимости полимера и растворителя, исходя из того, что самопроизвольное растворение полимера происходит в том случае, если эти параметры не различаются на величину, превышающую ±2 (кал/см3)0.5 [13].
Параметр растворимости ПФО рассчитывался на основании уравнения Смолла:
(1)
${{\delta }_{{\text{п}}}} = \frac{{{{{{\rho }}}_{{\text{п}}}}\sum {{{{\gamma }}}_{i}}}}{{{{M}_{0}}}},$Значения констант взаимодействия атомных группировок взяты из [13].
Параметры растворимости растворителей и нерастворителей рассчитаны с помощью уравнения
(2)
${{\delta }_{{\text{р}}}} = {{\left[ {\frac{{\left( {{{L}_{e}} - RT} \right)}}{{{{V}_{M}}}}} \right]}^{{0.5}}},$Результаты расчетов представлены в табл. 2.
Таблица 2.
Расчетные значения параметров растворимости полимера и растворителей
№ п.п. | Вещество | Параметр растворимости, δр, (кал/см3)0.5 |
---|---|---|
1 | ПФО | 10.8 |
2 | N-метилпирролидон (N-МП), С5H9NO | 11.4 |
3 | Хлороформ (ХФ), СHCl3 | 9.05 |
4 | Трихлорэтилен (ТХЭ), С2HCl3 | 9.2 |
Как видно из представленных данных все растворители, для которых проведены расчеты, теоретически могли обеспечить самопроизвольное растворение ПФО, так как их параметры растворимости укладываются в диапазон 10.8 ± 2 (кал/см3)0.5.
Для ХФ был проведен теоретический расчет коэффициента диффузии в воздух по уравнению (3) [14]. В качестве приближения, приемлемого для технических расчетов, рассматривалась модель ХФ1 – азот2.
(3)
${{D}_{{12}}} = 0.001858{{T}^{{3/2}}}{{\left[ {\left( {{{M}_{1}} + {{M}_{2}}} \right){\text{/}}{{M}_{1}}{{M}_{2}}} \right]}^{{1/2}}}/P\sigma _{{12}}^{2}{{{{\Omega }}}_{D}},$где D12 – коэффициент диффузии, см2/с;
σ12 – характеристическое расстояние, A;
ΩD – интеграл столкновений для диффузии, безразмерный;
${{M}_{i}}$ – молекулярные массы компонентов;
P – давление, атм;
Т – температура, К.
Для рассмотренной системы было получено следующее значение коэффициента диффузии:
Расчет коэффициентов диффузии растворителя в нерастворитель проведен на основе корреляции Шайбеля [14] по уравнению
(4)
$D_{{12}}^{0} = \frac{{KT}}{{{{\mu }_{2}}V_{1}^{{1{\text{/}}3}}}};\,\,\,\,K = 8.2 \times {{10}^{{ - 8}}}\left[ {1 + {{{\left( {\frac{{3{{V}_{2}}}}{{{{V}_{1}}}}} \right)}}^{{2{\text{/}}3}}}} \right],$μ2 – вязкость нерастворителя, сПз;
Vi – мольный объем жидкости при нормальной температуре кипения.
Результаты расчетов коэффициентов диффузии растворителя в вещество коагуляционной ванны по уравнению (4) представлены в табл. 3.
Таблица 3.
Коэффициент диффузии растворителя полимерного раствора в нерастворитель (коагулянт) при 25°C
№ | Растворитель1 | Нерастворитель2, НР2 | $D_{{12}}^{0}$, см2/с | ||
---|---|---|---|---|---|
1 | Хлороформ | СHCl3 | Метанол Этанол Этиленгликоль Глицерин |
СH3ОН С2H5ОН С2H2(ОН)2 С3H5(ОН)3 |
2.1 × 10–5 1.3 × 10–5 1.1 × 10–5 5.2 × 10–6 |
2 | Трихлорэтилен | С2HCl3 | Метанол Этанол Этиленгликоль Глицерин |
СH3ОН С2H5ОН С2H2(ОН)2 С3H5(ОН)3 |
1.9 × 10–5 1.1 × 10–5 1.0 × 10–5 4.7 × 10–6 |
3 | N-метилпирролидон | С5H9NO | Вода Метанол Этанол Глицерин |
Н2О СH3ОН С2H5ОН С3H5(ОН)3 |
8.7 × 10–6 16.2 × 10–6 8.5 × 10–6 0.02 × 10–6 |
2.4. Измерение газопроницаемости половолоконных мембран
Газопроницаемость (P/l) половолоконных мембран определяли по объемному расходу пермеата при постоянном трансмембранном давлении и измеряли в единицах [м3(н.у.) м–2 с–1 кПа–1].
Расчет газопроницаемости мембран проводился по уравнению
гдеP – коэффициент газопроницаемости мембраны, м3(н.у.) м/(м2 с кПа);
l – толщина мембраны, м;
Q – объемный расход пермеата, м3(н.у.)/с;
р – трансмембранное давление, кПа;
F – площадь поверхности мембраны, м2.
Селективность (α) определяли по проницаемости индивидуальных компонентов:
(6)
$\alpha \left( {{{{{{\text{O}}}_{{\text{2}}}}} \mathord{\left/ {\vphantom {{{{{\text{O}}}_{{\text{2}}}}} {{{{\text{N}}}_{{\text{2}}}}}}} \right. \kern-0em} {{{{\text{N}}}_{{\text{2}}}}}}} \right) = \frac{{{P \mathord{\left/ {\vphantom {P {l~\left( {{{{\text{O}}}_{{\text{2}}}}} \right)}}} \right. \kern-0em} {l~\left( {{{{\text{O}}}_{{\text{2}}}}} \right)}}}}{{{P \mathord{\left/ {\vphantom {P {l~\left( {{{{\text{N}}}_{{\text{2}}}}} \right)}}} \right. \kern-0em} {l~\left( {{{{\text{N}}}_{{\text{2}}}}} \right)}}}}.$Для измерения газовой проницаемости. собирали мембранные элементы из 20–30 полых волокон длинной 0.2–0.3 м. Газ подавали с наружной поверхности полых волокон, величину трансмембранного давления варьировали в диапазоне 0.3–1.0 МПа.
При расчетах точности измерений был использован эмпирический стандарт [15]:
(7)
$S = \sqrt {\frac{1}{{n - 1}}\sum\limits_{i = 1}^n {{{{\left( {{{x}_{i}} - \bar {x}} \right)}}^{2}}} } ,$где
n – количество независимых равноточных измерений;
xi – результат измерения без грубых и систематических ошибок;
$\bar {x}$ – среднее арифметическое значение результатов измерений.
При этом доверительная оценка принимает вид:
где множитель t (коэффициент Стьюдента) зависит как от доверительной вероятности Р, так и от числа измерений n (k = n – 1 – число степеней свободы). Распределение Стьюдента, то есть функция t = t(P; k) табулирована [15].Средняя ошибка в определении потока газа при заданной надежности 95% составила 10%, а селективности – 11%. При уменьшении надежности до 90% ошибка уменьшается соответственно до 8 и 10%.
3. РЕЗУЛЬТАТЫ И ИХ ОБСУЖДЕНИЕ
3.1. Практический подбор растворителя и нерастворителя (осадителя)
Сравнение коэффициентов диффузии нерастворителей в окружающую технологическую среду показывает, что в случае использования летучих растворителей их удаление с поверхности полимерного раствора в воздух будет происходить значительно быстрее, чем в случае мокрого осаждения: значение коэффициента диффузии хлороформа в воздухе на 4–5 порядков выше этого параметра в жидкости. В общем случае более низкое значение этого коэффициента диффузии упрощает процесс регулировки параметров формования мембраны.
Для приготовления газоразделительной мембраны с необходимыми характеристиками было исследовано несколько различных параметров и режимов формования.
Для всех формовочных режимов использовался ПР следующего состава: ПФО – 22%, Растворитель – 71%, Нерастворитель – 7%. Нерастворитель добавляли для приближения состава формовочного раствора к бинодали, с целью уменьшения времени доступного для роста фаз в ПР растворе золь2.
В качестве растворителей для приготовления ПР были использованы: N-МП, ТХЭ и ХЛФ.
1) Для получения первого образца мембран в качестве растворителя использовался N-МП (tкип = 206°С). В этом случае имеется возможность использования, в качестве реагента внутренней и внешней коагуляционной ванны, воды, что является значительным преимуществом перед другими нерастворителями.
Однако, в ходе предварительных экспериментов было установлено, что температура, при которой была возможность получить раствор нужной концентрации полимера, составляла выше 85°С. Это существенным образом осложняло процесс формования, так как формовочная установка не была рассчитана на данный уровень температур, и полимер, кристаллизуясь на более холодных стенках фильеры, постоянно блокировал подачу ПР.
2) Для получения второго образца волокна растворителем выступал использовался ТХЭ (tкип = 86.7°С). В этом случае ПР готовили при 50°С. При использовании этанола в качестве НР1, были сформованы мембраны при разном времени пребывания волокна в воздушном промежутке h. Результаты измерения сепарационных и газотранспортных характеристик, полученных образцов представлены в табл. 4.
Таблица 4.
Сепарационные и газотранспортные характеристики мембран с использованием ТХЭ в качестве растворителя
№ образца | Время пребывания на воздухе*, с | Проницаемость по О2, (м3(н.у.) м–2 с–1 кПа) × 109 |
Селективность |
---|---|---|---|
1.1 | 0.36 | 65.0 ± 6.6 | 4.80 ± 0.53 |
1.2 | 0.36 | 87.0 ± 8.8 | 4.80 ± 0.53 |
1.3 | 0.36 | 60.0 ± 6.0 | 4.70 ± 0.52 |
2.1 | 0.18 | 208.0 ± 20.8 | 4.70 ± 0.52 |
2.2 | 0.18 | 187.0 ± 18.7 | 4.60 ± 0.51 |
2.3 | 0.18 | 206.0 ± 20.6 | 4.60 ± 0.51 |
3.1 | 0.04 | 310.0 ± 31.0 | 4.50 ± 0.50 |
3.2 | 0.04 | 326.0 ± 32.6 | 4.70 ± 0.52 |
3.3 | 0.04 | 296.0 ± 29.6 | 4.70 ± 0.52 |
4.1 | 0.02 | 3720 ± 373 | 1.00 ± 0.11 |
4.2 | 0.02 | 3890 ± 389 | 1.00 ± 0.11 |
Как видно из представленных данных, для мембран 1.1–3.3 селективность, независимо от времени пребывания на воздухе, оставалась одинаковой в пределах погрешности измерения, т.е. с наружной стороны волокна концентрация полимера увеличивалась настолько, что гарантированно образовывался плотный бездефектный селективный слой.
По мере уменьшения времени пребывания на воздухе, уменьшается эффективная толщина селективного слоя, что приводит к росту газопроницаемости мембраны. Однако, при сокращении времени пребывания на воздухе менее 0.04 с (высота воздушного промежутка – 6.5 мм), мембрана полностью теряет селективность, а ее проницаемость резко увеличивается. Данное явление можно описать следующим образом: экструдируемый из фильеры ПР сразу попадает в среду насыщенных паров НР1, вследствие чего с внешней стороны волокна индуцируется процесс мгновенного фазового распада и образование плотного селективного слоя не происходит.
Таким образом метод сухо-мокрого формования при использовании летучего растворителя имеет определенные ограничения в плане повышения проницаемости мембраны путем сокращения времени пребывания в воздушном промежутке.
3) Для получения следующего образца в качестве растворителя был использован ХЛФ с tкип = = 61.2°С. Рабочий раствор также готовился при 50°С. Мембраны были изготовлены при условиях, идентичных условиям формования в случае использования ТХЭ. Результаты измерения сепарационных и газотранспортных характеристик представлены в табл. 5.
Таблица 5.
Сепарационные и газотранспортные характеристики мембран с использованием ХЛФ в качестве растворителя
№ образца | Время пребывания на воздухе, с |
Проницаемость по О2, (м3(н.у.) м–2 с–1 кПа) × 109 |
Селективность |
---|---|---|---|
5.1 | 0.36 | 250.0 ± 24.9 | 4.90 ± 0.54 |
5.2 | 0.36 | 260.0 ± 25.7 | 4.60 ± 0.51 |
5.3 | 0.36 | 236.0 ± 23.6 | 4.70 ± 0.52 |
6.1 | 0.18 | 370.0 ± 37.0 | 4.70 ± 0.52 |
6.2 | 0.18 | 373.0 ± 37.97 | 4.60 ± 0.51 |
6.3 | 0.18 | 387.0 ± 38.7 | 4.60 ± 0.51 |
7.1 | 0.04 | 502.0 ± 50.2 | 4.70 ± 0.51 |
7.2 | 0.04 | 532.0 ± 53.9 | 4.20 ± 0.46 |
7.3 | 0.04 | 510.0 ± 51.0 | 4.70 ± 0.52 |
7.4 | 0.04 | 463.0 ± 46.3 | 4.80 ± 0.53 |
Характер зависимостей аналогичен случаю с ТХЭ, однако абсолютные значения проницаемости для ХЛФ выше, чем для ТХЭ. В соответствии с принятой моделью формирования структуры мембраны, в силу более низкого значения коэффициента диффузии растворителя (ТХЭ) в этанол (НР1), формирование структуры мембраны от центра к периферии занимает больше времени, чем в случае ХЛФ. Это приводит к формированию более совершенных плотных структур, что, в конечном итоге, ухудшает взаимосвязь между порами в слое – подложке и увеличивает сопротивление диффузии газа через стенку мембраны.
Таким образом для дальнейших экспериментов в качестве базового растворителя был выбран ХЛФ. В качестве внутреннего нерастворителя НР1, для формирования высокопористой подложки мембраны, рассматривались этанол и метанол. По данным табл. 4 коэффициенты диффузии ХЛФ в рассматриваемые нерастворители составляют
$D_{{12}}^{0}$ (ХЛФ–этанол) = 1.3 × 10–5 см2/с;
$D_{{12}}^{0}$ (ХЛФ–метанол) = 2.1 × 10–5 см2/с.
Очевидно, что диффузия хлороформа в метанол протекает быстрее, следовательно, метанол является более “жестким” нерастворителем для выбранной системы.
Сепарационные и газотранспортные характеристики мембран, сформованных при различных внутренних нерастворителях приведены в табл. 6.
Таблица 6.
Сепарационные и газотранспортные характеристики мембран, полученных с пребыванием на воздухе 0.04 с при различных внутренних нерастворителях
№ образца | Внутренний нерастворитель НР1 | Проницаемость по О2, (м3(н.у.) м–2 с–1 кПа) × 109 |
Селективность |
---|---|---|---|
7.1 | Этанол | 502.0 ± 50.2 | 4.70 ± 0.52 |
7.2 | Этанол | 532.0 ± 53.2 | 4.20 ± 0.46 |
7.3 | Этанол | 510.0 ± 51.0 | 4.70 ± 0.52 |
7.4 | Этанол | 463.0 ± 46.3 | 4.80 ± 0.53 |
8.1 | Метанол | 614.0 ± 61.4 | 4.70 ± 0.52 |
8.2 | Метанол | 548.0 ± 54.8 | 4.40 ± 0.48 |
8.3 | Метанол | 570.0 ± 57.0 | 4.80 ± 0.53 |
8.4 | Метанол | 589.0 ± 59.0 | 4.50 ± 0.50 |
Чтобы оценить влияние внутреннего нерастворителя на проницаемость мембраны, оба режима формования были идентичны – в качестве растворителя в ПР использовался ХЛФ, время пребывания на воздухе было минимальным допустимым. Видно, что при использовании метанола, проницаемость волокна была выше, нежели в случае этанола. Это объясняется более интенсивным взаимодействием хлороформа с метанолом, по сравнению этанолом, что приводит к более быстрому переходу золя в гель, который фиксирует образование открытой микропористой структуры [11.
3.2. Подбор состава внешней коагуляционной ванны
Как указывалось выше, при уменьшении высоты воздушного промежутка ниже 6.5 мм управлять процесс формования мембраны не удается. Исходя из принятой модели формирования асимметричной структуры мембраны, был рассмотрен вариант мокрого формования с использованием внешней ванны с подбором соответствующих нерастворителей, в которых величина коэффициента диффузии ХЛФ меньше, чем величина коэффициента диффузии ХЛФ в воздух.
Для внешней ванны были испытаны три варианта жидкости внешней ванны: глицерин, этиленгликоль и этанол. Как следует из результатов расчетов табл. 2, также из расчета коэффициента диффузии ХЛФ в воздухе:
$D_{{12}}^{0}$ (ХЛФ–этанол) = 1.3 × 10–5 см2/с;
$D_{{12}}^{0}$ (ХЛФ–этиленгликоль) = 1.1 × 10–5 см2/с;
$D_{{12}}^{0}$ (ХЛФ–глицерин) = 5.2 × 10–6 см2/с;
${{D}_{{12}}}$ (ХЛФ–азот) = 0.249 см2/с.
Коэффициент диффузии растворителя в воздух и в нерастворители отличается на несколько порядков, что указывает на очевидный механизм управления толщиной селективного слоя мембраны: при использовании мокрого способа формования скорость увеличения концентрации полимера на поверхности полого волокна будет существенно ниже. С этой точки зрения ожидалось, что лучшие результаты должны быть получены для глицерина.
Для полученных образцов волокон были также измерены сепарационные и газотранспортные характеристики – табл. 7.
Таблица 7.
Сепарационные и газотранспортные характеристики мембран, полученных при различном составе внешней коагуляционной ванны. Время контакта с внешней ванной 1.2 с
№ образца | Внешняя ванна | Проницаемость по О2, (м3(н.у.) м–2 с–1 кПа) × 109 |
Селективность |
---|---|---|---|
9.1 | Глицерин | 4630 ± 462 | 1.00 ± 0.11 |
9.2 | Глицерин | 6590 ± 659 | 0.90 ± 0.01 |
10.1 | Этиленгликоль | 5580 ± 558 | 1.00 ± 0.11 |
10.2 | Этиленгликоль | 5350 ± 535 | 1.00 ± 0.11 |
11.1 | Этанол | 581 ± 58 | 5.20 ± 0.57 |
11.2 | Этанол | 896 ± 90 | 4.80 ± 0.53 |
11.3 | Этанол | 768 ± 77 | 4.80 ± 0.53 |
11.4 | Этанол | 842 ± 84 | 4.90 ± 0.54 |
Как следует из представленных данных, вопреки ожиданиям, глицерин и этиленгликоль не сработали – зафиксирована полная потеря селективности. Предполагается, что это вызвано появлением механических проникающих дефектов в селективном слое мембраны из-за высокой плотности внешних нерастворителей, что в процессе стекания этих реагентов по внешней поверхности мембраны приводит к образованию мелких разрывов.
В случае использования этанола получена селективная мембрана, причем с более высокой проницаемостью по кислороду, по сравнению с тем, что было получено, при прочих равных условиях, для сухо-мокрого формования.
ВЫВОДЫ
Исследовано влияние на свойства мембраны типа растворителя, составов внешней и внутренней ванны, а также темпера туры ПР и времени пребывания волокна во внешней ванне. В рамках данного исследования лучшим растворителем является хлороформ. Показано, что с этим растворителем в процессе “сухо-мокрого” формования оптимальная величина времени пребывания волокна на воздухе составляет 0.04 с. При этом во всех случаях достигается селективность, которая соответствует собственной селективности полимера для пары газов кислород–азот. В качестве внутреннего нерастворителя был выбран метанол: как более “жесткий” нерастворитель для данной полимерной системы он обеспечивал более открытую пористую структуру с внутренней поверхности полого волокна. Для варианта сухо-мокрого формования лучший результата по суммарному показателю селективность – проницаемость кислорода составил 4.80 ± 0.51 и (580 ± ± 60) × 10–9 (м3(н.у.) м–2 с–1 кПа). Лучший результат по суммарному показателю селективность-проницаемость составил 4.93 ± 0.54 (760 ± 77) × × 10–9 (м3(н.у.) м–2 с–1 кПа) получен в случае “мокрого” формования при использовании этанола в качестве жидкости внешней коагуляционной ванны.
Список литературы
Волков В.В., Мчедлишвили Б.В., Ролдугин В.И., Иванчев С.С., Ярославцев А.Б. // Российские нанотехнологии. 2008. Т. 3. № 11–12. С. 67.
Baker R.W. Membrane technology and applications. Chichester: John Wiley & Sons Ltd, 2012. 545 c.
Smid J., Albers J.H.M., Kusters A.P.M. // J. Membr. Sci. 1991. V. 64. P. 121.
Иванов М.В., Варежкин А.В. // Успехи химии и химической технологии. 2015. Т. ХХIX. № 6. С. 53.
Майборода А.Б., Петров Д.В., Кичик В.А., Стариков Е.Н. // Мембраны и мембранные технологии. 2014. Т. 10. № 6. С. 373.
Ivanov M.A., Dibrov G.A., Loyko A.V., Varezhkin A.V., Kagramanov G.G. // Theor. Found. Chem. Eng. 2016. V. 50. P. 316.
Бельдюкевич А.В., Плиско Т.В. // Мембраны и мембранные технологии. 2016. Т. 2. № 2. С. 113.
Матвеев Д.Н., Кутузов К.А., Василевский В.П. // Мембраны и мембранные технологии. 2020. Т. 10. № 6. С. 373.
Polyphenylene Oxide and Modified Polyphenylene Oxide Membranes / Ed. by Chowdhury G., Kruczek B., Matsuura T. N.Y.: Springer N.Y., 2001. 224 p.
Алентьев А.Ю., Чирков С.В., Никифоров Р.Ю., Левин И.А., Кечекьян А.С., Кечекьян П.А., Белов Н.В. // Мембраны и мембранные технологии. 2022. Т. 12. № 1. С. 3.
Мулдер М. Введение в мембранную технологию. М.: Мир, 1999. 514 с.
Khayet M., Matsuura T. Membrane distillation principles and applications. Amsterdam: Elsevier, 2011. 478 p.
Геллер Б.Э., Геллер А.А., Чиртулов В.Г. Практическое руководство по физикохимии волокнообразующих полимеров. М.: Химия, 1996. 432 с.
Рид Р., Праусниц Д., Шервуд Т. Свойства газов и жидкостей. Л.: Химия, 1982. 592 с.
Румшинский Л.З. Математическая обработка результатов эксперимента. М.: Наука, 1971. 192 с.
Дополнительные материалы отсутствуют.
Инструменты
Мембраны и мембранные технологии