Российские нанотехнологии, 2020, T. 15, № 3, стр. 316-322
ДИЗАЙН КАТАЛИТИЧЕСКИХ ПОЛИФУНКЦИОНАЛЬНЫХ НАНОМАТЕРИАЛОВ ДЛЯ ПРОЦЕССОВ ПОЛУЧЕНИЯ ВОДОРОДА
Д. И. Потемкин 1, 2, 3, *, П. В. Снытников 1, 2, С. Д. Бадмаев 1, 2, С. И. Усков 1, 2, А. М. Горлова 1, 2, В. Н. Рогожников 1, 4, А. А. Печенкин 1, 4, А. В. Куликов 1, В. А. Шилов 1, 2, Н. В. Рубан 1, 2, В. Д. Беляев 1, 2, В. А. Собянин 1
1 Институт катализа им. Г.К. Борескова СО РАН
Новосибирск, Россия
2 Новосибирский государственный университет
Новосибирск, Россия
3 Новосибирский государственный технический университет
Новосибирск, Россия
4 Российский государственный университет нефти и газа им. И.М. Губкина
Москва, Россия
* E-mail: potema@catalysis.ru
Поступила в редакцию 03.06.2020
После доработки 14.08.2020
Принята к публикации 14.08.2020
Аннотация
Процессы получения водорода из различных видов ископаемых и возобновляемых топлив являются энергонапряженными многомаршрутными химическими реакциями, для эффективного проведения которых необходимо применение селективных и высокопроизводительных катализаторов, которые бы совмещали в себе высокие активность, теплопроводность, коррозионную и термическую стойкость. Изложена общая стратегия дизайна каталитических систем для процессов получения водорода, которая заключается в использовании композитных катализаторов типа “наночастицы металлов/наночастицы активного оксида/структурный оксидный компонент/структурированная металлическая подложка” и описан подход для их направленного синтеза. Структурированная металлическая подложка обеспечивает эффективный отвод/подвод тепла для экзо-/эндотермических реакций, обладает хорошими гидродинамическими характеристиками и облегчает масштабный переход. Структурный оксидный компонент (оксид алюминия) обеспечивает термическую и коррозионную устойчивость и высокую удельную поверхность каталитического покрытия, выполняя защитную функцию для металлической подложки. Активный оксидный компонент (преимущественно оксиды церия-циркония) повышает устойчивость к зауглероживанию за счет кислородной подвижности и поддерживает высокую дисперсность активного компонента за счет сильного взаимодействия металл–носитель. Наночастицы металлов размером 1–2 нм участвуют в активации молекул-субстратов. В качестве теплопроводящей подложки использованы фехралевые (FeCrAl) сетки, сформованные в цилиндрические блоки заданных размеров. Путем контролируемого отжига с формированием микронного слоя α-Al2O3 и последующего нанесения слоя η-Al2O3 по методу Байера (через гидроксид алюминия) на поверхность фехрали нанесен структурный слой η-Al2O3 с “дышащей” игольчатой морфологией, на который далее методами пропитки и/или осаждения был нанесен каталитически активный компонент. Эффективность предложенной стратегии показана на примере катализаторов Rh/Ce0.75Zr0.25O2 – δ–η-Al2O3/FeCrAl три-реформинга метана и Cu–CeO2 – δ/η-Al2O3/FeCrAl-катализаторов паровой конверсии диметоксиметана.
ВВЕДЕНИЕ
Несмотря на рост производства и потребления энергии за счет возобновляемых ресурсов (солнечно-ветровой энергетики, использование биомассы), активному распространению и внедрению различных соответствующих устройств генерации и аккумулирования энергии прогнозируется, что еще на многие десятилетия ископаемые ресурсы (в первую очередь нефть и природный газ) будут составлять основу мирового энергопотребления. Увеличение эффективности использования углеводородного сырья при улучшении эксплуатационных характеристик (немаловажный фактор для конечного потребителя) связывается с применением топливных элементов (ТЭ) и технологий хранения водорода для нужд распределенной энергетики [1, 2]. Поэтому ТЭ, которые позволяют с высоким КПД преобразовывать энергию химических связей в электрическую даже для компактных и мобильных систем, являются одной из наиболее динамично развивающихся отраслей энергетики.
В большинстве научно-исследовательских работ, выполненных за последние 20–25 лет, ожидалось, что на момент начала массового использования ТЭ инфраструктура по снабжению топливом (водородом) в основном будет создана, отлажена логистика: будет доступно достаточное количество водородных заправок, решены проблемы по длительному хранению необходимых (с точки зрения конечного потребителя) количеств водорода. Но эти прогнозы, к сожалению, оказались чрезмерно оптимистичными. Использование имеющейся и активно развиваемой инфраструктуры транспортировки и потребления природного газа на данный момент оказывается недостаточно для удовлетворения нужд массового потребления.
Именно поэтому интерес к использованию основных логистических топлив с высокой энергетической плотностью, удобных для хранения и транспортировки (бензин, пропан-бутан, авиационный керосин и дизельное топливо), проявляют все мировые научно-исследовательские центры, занимающиеся разработкой энергоустановок на основе ТЭ. Более того, по сравнению с другими доступными на сегодняшний день технологиями хранения водорода у органических топлив на единицу объема содержится наибольшее количество водорода [3]. Поэтому для ТЭ актуально использование жидких или легко сжижаемых органических топлив с высокой энергетической плотностью. Прямое окисление таких топлив в анодном пространстве ТЭ способствует зауглероживанию электрода, что ведет к выходу ТЭ из строя. Чтобы этого избежать, топливо сначала подвергают конверсии в водородсодержащий газ, который далее окисляется в ТЭ [4]. В зависимости от назначения, типа ТЭ, выбранной общей схемы преобразования топлива и интеграции между частями энергоустановки получение водородсодержащего газа проводят путем паровой конверсии (ПК), автотермического реформинга (АТР), парциального окисления (ПО), углекислотной конверсии (УК) или три-реформинга (ТР), которые по сути основаны на процессе ПК нафты, применяемом с 60-х годов прошлого века в нефтехимической промышленности и в производстве аммиака с целью получения синтез-газа и водорода [5].
Процессы ПК, АТР, ПО, УК и ТР являются энергонапряженными многомаршрутными химическими реакциями, для эффективного проведения которых необходимо применение селективных и высокопроизводительных катализаторов. В работе изложена общая стратегия дизайна каталитических систем для процессов конверсии ископаемых, синтетических и возобновляемых топлив в водородсодержащие смеси для питания ТЭ, основанная на применении композитных катализаторов типа “наночастицы металлов/наночастицы активного оксида/структурный оксидный компонент/структурированная металлическая подложка”.
ЭКСПЕРИМЕНТАЛЬНАЯ ЧАСТЬ
В качестве основы для металлического структурированного блока использовали фехралевую сетку (FeCrAl) производства АО “НПО СОЮЗНИХРОМ” с параметрами ячейки 0.5 × 0.25 мм (проходное сечение ячейки на диаметр проволоки). Из фехралевой сетки изготавливали структурированный блок путем скручивания в Архимедову спираль двух наложенных друг на друга лент из сетки – гофрированной и гладкой. Таким образом получили структурированный металлический блок длиной 60 мм и диаметром 18 мм. Далее на металлический структурированный блок нанесли промежуточный защитный слой η-Al2O3 согласно методике, описанной в [6].
При приготовлении 0.24 мас. % Rh/6 мас. % Ce0.75Zr0.25O2 – δ–6 мас. % η-Al2O3/FeCrAl (далее Rh/Ce0.75Zr0.25O2 – δ–η-Al2O3/FeCrAl) катализатора после формирования промежуточного защитного слоя η-Al2O3 на структурированный блок нанесли слой Ce0.75Zr0.25O2 – δ. В качестве предшественников церия и циркония использовали нитрат церия(III) и нитрат цирконила(IV), из которых был получен пропиточный раствор. Необходимое количество пропиточного раствора с мольным соотношением Ce : Zr = 3 : 1 использовали для пропитки металлического структурированного блока с нанесенным слоем оксида алюминия. Путем нескольких последовательных пропиток с промежуточной термической обработкой при 800°C в течение 5 мин и финальной прокалкой при 800°C в течение 30 мин был получен металлический структурированный блок Ce0.75Zr0.25O2 – δ/η-Al2O3/FeCrAl. Далее на блок наносили наночастицы Rh размером 1–2 нм методом сорбционно-гидролитического осаждения [7].
Порошковый 10 мас. % CuO–5 мас. % CeO2/Al2O3 (далее Cu–CeO2 – δ/γ-Al2O3) и структурированный 10 мас. % CuO–5 мас. % CeO2/Al2O3 (далее Cu–CeO2 – δ/ƞ-Al2O3/FeCrAl) катализаторы готовили пропиткой гранул γ-Al2O3 (0.25–0.5 мм) и блока η-Al2O3/FeCrAl соответственно раствором азотнокислых солей меди и церия, взятых в заданном соотношении. Полученные образцы сушили и затем в течение 2 ч прокаливали при 400°С.
Cu–CeO2 – δ/γ-Al2O3/- и Cu–CeO2 – δ/η-Al2O3/FeCrAl-катализаторы исследовали в реакции паровой конверсии диметоксиметана (ДММ). Эксперименты проводили в проточном реакторе при атмосферном давлении в интервале температур 150–350°С. Реактор представлял собой U-образную кварцевую трубку. После процедуры восстановления катализатора при температуре 350°С в потоке смеси 5 об. % Н2/N2 в реактор подавали реакционную смесь состава (об. %): 10 ДММ, 45Н2О и 45N2, объемная скорость подачи реагентов в реактор составляла 20–30 л ${\text{г}}_{{{\text{кат}}}}^{{ - 1}}$ ч–1 (в случае катализатора Cu–CeO2 – δ/η-Al2O3/FeCrAl скорость потока рассчитывали с учетом массы каталитического покрытия, т.е. Cu–CeO2 – δ/η-Al2O3). Температуру измеряли термопарой, помещенной в середину слоя катализатора (блока). Состав и концентрации компонентов реакционной смеси определяли с помощью газового хроматографа “Хромос ГХ-1000” (Россия), снабженного двумя детекторами теплопроводности.
Три-реформинг метана на катализаторе Rh/Ce0.75Zr0.25O2 – δ–η-Al2O3/FeCrAl изучали в проточном реакторе из нержавеющей стали при атмосферном давлении и температуре стенок реактора 730°С. Катализатор предварительно восстанавливали в токе 5 об. % Н2/N2 при 600°С. После чего повышали температуру и в реактор подавали реакционную смесь состава (об. %): 24.3CH4, 12.8O2, 9.9H2O, 4.7CO2, 48.3N2. Объемную скорость подачи смеси варьировали в интервале 10 000–40 000 ч–1. Температуру на входе и выходе из блока измеряли термопарами по центральной оси блока. Состав и концентрации компонентов реакционной смеси определяли с помощью газового хроматографа “Хромос ГХ-1000” (Россия), снабженного детектором теплопроводности и пламенно-ионизационным детектором с метанатором. “Холостой” эксперимент, без катализатора, показал, что при используемых объемных скоростях потока протекание реакции на стенках реактора не существенно и может не учитываться при анализе результатов.
Расчеты равновесного распределения продуктов реакций паровой конверсии ДММ и три-реформинга метана в приближении идеальных газов проводили в программе HSC Chemistry 7.1.
Морфологию каталитического покрытия контролировали методом сканирующей электронной микроскопии (СЭМ) на приборе SM-6460 LV (JEOL Ltd., Japan). Для проведения анализов параллельно с основным блоком по аналогичной процедуре готовили небольшие фрагменты композитного катализатора на плоской сетке.
Микроструктуру покрытия в катализаторах и после реакции исследовали методом просвечивающей электронной микроскопии (ПЭМ) на приборе JEM-2010 с разрешением 1.4 Å, снабженном спектрометром с Si(Li)-детектором (разрешение по энергиям 130 эВ) для энергодисперсионного анализа (ЭДА). Для проведения анализов материал каталитического покрытия соскабливали с FeCrAl-подложки.
РЕЗУЛЬТАТЫ И ИХ ОБСУЖДЕНИЕ
Процессы паровой конверсии и УК углеводородов, метанола и других топлив [8, 9] являются сильно эндотермическими реакциями, требующими подвода большого количества тепла (рис. 1а). Производительность процесса зачастую ограничивается скоростью теплопередачи в крупных реакторах. Одним из эффективных подходов к увеличению производительности катализаторов паровой конверсии и УК является использование тонких каталитических покрытий (рис. 1б), нанесенных на стенки реактора или поверхность металлических структурированных блоков, обладающих более высокой теплопроводностью по сравнению с гранулами катализатора [9].
Процессы АТР, парциального окисления и ТР характеризуются сочетанием экзо- и эндотермических реакций. Во фронтальной части реактора протекают быстрые реакции полного окисления с выделением тепла, которое далее потребляется по длине слоя катализатора при протекании эндотермических процессов паровой и углекислотной конверсии углеводородов. Поэтому при проведении процессов АТР, парциального окисления и ТР для уменьшения перегревов лобового слоя и чрезмерного охлаждения хвостовой части реактора катализатор должен обеспечивать эффективную передачу тепла между ними (рис. 2). Традиционные гранулированные керамические катализаторы обладают низкой теплопроводностью и плохо подходят для проведения этих процессов. Кроме того, для снижения перепада давления в реакторе необходимо использовать гранулы катализатора достаточно больших размеров (1 см и более), что приводит к низкому коэффициенту использования зерна катализатора в условиях быстро протекающих реакций АТР, парциального окисления и ТР.
Рис. 1.
Схематичное изображение радиального распределения температуры при протекании эндотермической реакции в трубчатом реакторе со слоем гранулированного катализатора (а) и структурированного катализатора, нанесенного на металло-сетчатый носитель (б).
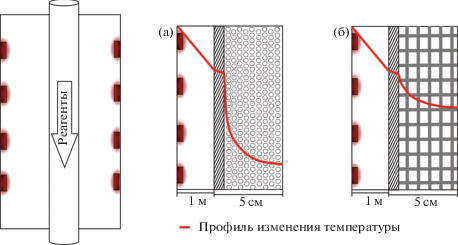
Рис. 2.
Схематичное изображение аксиального профиля температуры при протекании реакций автотермического реформинга, парциального окисления и три-реформинга углеводородов.
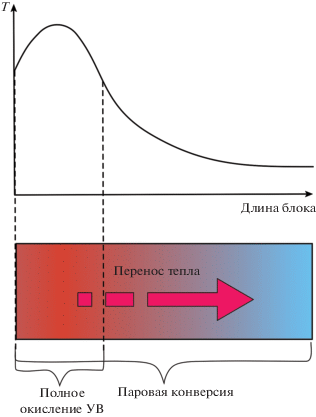
Для эффективного проведения таких процессов было предложено использовать композитные каталитические системы типа “наночастицы металлов/наночастицы активного оксида/структурный оксидный компонент/структурированная металлическая подложка”. Структурированная металлическая подложка, в частности из фехралевого сплава [10], обеспечивает быстрый отвод/подвод теплоты для экзо-/эндотермических реакций, обладает хорошими гидродинамическими характеристиками, позволяет изготавливать изделия различной геометрической формы и облегчает масштабирование. Структурный оксидный компонент (оксид алюминия) обеспечивает термическую устойчивость, высокую удельную поверхность и увеличивает механическую прочность для наносимого каталитического покрытия, выполняя защитную функцию для металлической подложки. Активный оксидный компонент (преимущественно использовали оксид церия, смешанные церий-циркониевые оксиды со структурой флюорита) участвует в активации молекул воды и кислорода, повышает устойчивость к зауглероживанию за счет высокой кислородной подвижности и поддерживает высокую дисперсность активного компонента за счет сильного взаимодействия металл–носитель. Наночастицы металлов размером 1–2 нм участвуют в активации молекул углеводородов.
Одним из основных затруднений при дизайне таких композитных катализаторов является отслойка каталитического покрытия при нагревании вследствие разницы коэффициентов температурного расширения металлической положки и оксидного покрытия. Решить эту проблему удалось за счет подбора режима отжига фехралевой подложки для формирования на ее поверхности микронного слоя α-Al2O3 и последующего нанесения слоя η-Al2O3 по методу Байера (через гидроксид алюминия) [6] с “дышащей” игольчатой морфологией (рис. 3). Далее методом многократной пропитки формировалось покрытие активного оксида, например смешанного оксида церия-циркония Ce0.75Zr0.25O2 – δ. После чего в порах сформированного каталитического покрытия формировались наночастицы активного металла. Медь наносили методом пропитки, а платиновые металлы (Pt, Pd, Rh) – сорбционно-гидролитическим осаждением из метастабильных растворов хлоридов металлов в условиях преобладания гетерогенного зародышеобразования, что позволяло получать наночастицы платиновых металлов размером 1–2 нм (рис. 3).
Рис. 3.
Схема синтеза композитных катализаторов на примере Rh/Ce0.75Zr0.25O2 – δ–η-Al2O3/FeCrAl-блока и данные о морфологии и микроструктуре блока на различных стадиях синтеза.
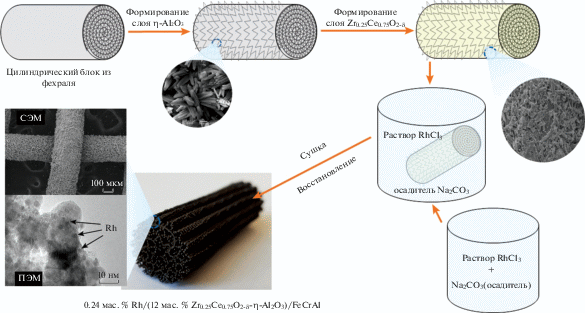
Ранее было продемонстрировано [7, 11], что приготовленный по данной методике композитный Rh/Ce0.75Zr0.25O2 – δ–η-Al2O3/FeCrAl-катализатор был высокоэффективным в автотермической конверсии дизельного топлива, проявляя высокую каталитическую активность, стабильность, низкую склонность к зауглероживанию, обладая при этом механической прочностью при термоциклировании. В настоящей работе исследованы его свойства в три-реформинге метана. Процесс ТР метана активно исследуется в последнее десятилетие как метод получения синтез-газа [12], который позволяет одновременно утилизировать диоксид углерода. Основными проблемами процесса являются стабильность катализаторов в условиях высоких температур и зауглероживание катализаторов. На рис. 4 представлены зависимости выходных концентраций H2, N2, CO, CO2, CH4 и температуры на входе (Tвход) и выходе (Tвыход) из каталитического блока от скорости потока реакционной смеси при ТР метана на катализаторе Rh/Ce0.75Zr0.25O2 – δ–η-Al2O3/FeCrAl. Видно, что при всех потоках распределение продуктов близко к равновесному при 700°С. Температура на выходе из блока изменялась от 693 до 730°С, т.е. была близка к 700°С, что объясняет близость распределения продуктов к равновесному. Температура на входе в катализатор превышала температуру стенок реактора (730°С) и температуру выхода, что связано с протеканием экзотермичной реакции полного окисления метана. Температура выхода, наоборот, не превышала температуры стенок реактора, что обусловлено протеканием эндотермических реакций паровой и углекислотной конверсии метана. При этом с увеличением скорости потока Tвход уменьшалась, а Tвыход увеличивалась. Это, по-видимому, связано увеличением мощности тепловыделения на катализаторе и с растягиванием зоны, в которой протекает полное окисление метана (рис. 2), при увеличении нагрузки на катализатор, что обусловлено внешнедиффузионным лимитированием скорости окисления метана [13]. Свойства катализатора были постоянны в течение 30 ч эксперимента в ходе четырех циклов запуска/останова. Масса блока в ходе эксперимента не изменилась, повреждений (отслойки) каталитического покрытия зарегистрировано не было. Таким образом, катализатор Rh/Ce0.75Zr0.25O2 – δ–η-Al2O3/FeCrAl показал стабильную работу в условиях ТР метана и обеспечивал при нормальных условиях производительность по синтез-газу (Н2 + СО) 28 м3${\text{л}}_{{{\text{кат}}}}^{{ - 1}}$ ч–1.
Рис 4.
Зависимости выходных концентраций H2, N2, CO, CO2, CH4 и температуры на входе (Tвход) и выходе (Tвыход) из каталитического блока от скорости потока реакционной смеси при три-реформинге метана на Rh/Ce0.75Zr0.25O2 – δ–η-Al2O3/FeCrAl-катализаторе. Также на графике обозначена температура стенок реактора (Tреактора), которая поддерживалась постоянной в ходе эксперимента. Точки – экспериментальные данные; сплошные линии – измеренные температуры; пунктирные линии – равновесные концентрации при 700°С.
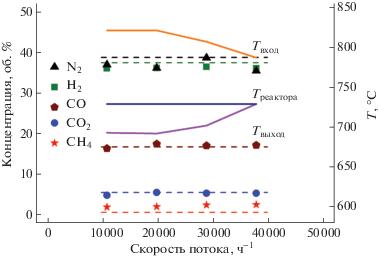
Метанол, диметиловый эфир и ДММ являются перспективными синтетическими топливами для получения водорода [14, 15]. В настоящей работе исследовали ПК диметоксиметана на катализаторе Cu–CeO2 – δ/η-Al2O3/FeCrAl. Поскольку паровая конверсия ДММ является высокоэндотермической реакцией, использование традиционных гранулированных катализаторов может вызывать образование градиента температуры вдоль оси реактора, что приводит к снижению эффективности катализатора. Чтобы решить эту проблему, использовали композитный катализатор, нанесенный на FeCrAl-сетку. При этом за счет сниженного по сравнению с катализатором Rh/Ce0.75Zr0.25O2 – δ–η-Al2O3/FeCrAl количества нанесенного CeO2 слой η-Al2O3 выполнял не только роль структурного компонента, но и выступал в качестве активного компонента катализатора: кислотные центры на поверхности оксида алюминия были активны в реакции гидролиза ДММ [16, 17]:
Поверхность наночастиц металлической меди выступала в качестве активных центров для протекания реакций дегидрирования и ПК метанола и формальдегида:
Роль оксида церия заключалась в стабилизации частиц меди в высокодисперсном состоянии. В табл. 1 представлены данные о каталитических свойствах композитного Cu–CeO2 – δ/η-Al2O3/FeCrAl-катализатора и гранулированного катализатора Cu–CeO2/γ-Al2O3. Отметим, что для обоих катализаторов при всех температурах конверсия ДММ составляла 100%. Видно, что на катализаторе Cu–CeO2 – δ/η-Al2O3/FeCrAl достигаются более высокие производительности по водороду (${{Y}_{{{{{\text{H}}}_{2}}}}}$), а в продуктах реакции содержится меньше нежелательных побочных продуктов: СО, метанол, диметиловый эфир. По-видимому, эффект достигается за счет более равномерного температурного поля по слою катализатора благодаря его более высокой теплопроводности. Свойства катализатора Cu–CeO2 – δ/η-Al2O3/FeCrAl были стабильны в течение не менее 20 ч эксперимента в нескольких циклах повышения/снижения температуры. Изменения массы и повреждения каталитического покрытия не наблюдали. Таким образом, катализатор Cu–CeO2 – δ/η-Al2O3/FeCrAl показал стабильную работу в условиях паровой конверсии ДММ и обеспечивал при нормальных условиях производительность по синтез-газу (Н2 + СО) 17.6 м3${\text{л}}_{{{\text{кат}}}}^{{ - 1}}$ ч–1.
Таблица 1.
Свойства катализаторов в паровой конверсии диметоксиметана
Катализатор | Поток, л ${\text{г}}_{{{\text{кат}}}}^{{ - 1}}$ ч–1 | T, °C | ${{Y}_{{{{{\text{H}}}_{2}}}}}$, л ${\text{г}}_{{{\text{кат}}}}^{{ - 1}}$ ч-1 | Селективность по С-содержащим продуктам, % | |||
---|---|---|---|---|---|---|---|
CO2 | CO | ДМЭ | CH3OH | ||||
Гранулированный Cu–CeO2 – δ/γ-Al2O3 | 20 | 280 | 12 | 79 | 1.2 | 3.8 | 16 |
300 | 15 | 88 | 4 | 4 | 4 | ||
Композитный Cu–CeO2 – δ/ƞ-Al2O3/FeCrAl | 30 | 275 | 20 | 88 | 1 | 0.4 | 10.5 |
300 | 22 | 97 | 2.2 | 0.6 | 0.1 |
ВЫВОДЫ
Изложена общая стратегия дизайна каталитических систем для процессов получения водорода, которая заключается в использовании композитных катализаторов типа “наночастицы металлов/наночастицы активного оксида/структурный оксидный компонент/структурированная металлическая подложка”, и описан подход для их направленного синтеза. На примере катализатора Rh/Ce0.75Zr0.25O2 – δ–η-Al2O3/FeCrAl три-реформинга метана и катализатора паровой конверсии диметоксиметана Cu–CeO2 – δ/η-Al2O3/FeCrAl показана высокая эффективность и стабильность катализаторов.
Работа выполнена при финансовой поддержке Российского фонда фундаментальных исследований в рамках проекта № 19-33-60008 (Д.И. Потемкин) в части исследования три-реформинга метана.
Список литературы
Ren J., Musyoka N.M., Langmi H.W. et al. // Int. J. Hydrogen Energy. 2017. V. 42. P. 289. https://doi.org/10.1016/j.ijhydene.2016.11.195
Zhang F., Zhao P., Niu M., Maddy J. // Int. J. Hydrogen Energy. 2016. V. 41. P. 14535. https://doi.org/10.1016/j.ijhydene.2016.05.293
Speight J.G. // Fuel Cells Technol. Fuel Process. Ch. 3. Fuels for Fuel Cells / Eds. Shekhawat D. et al. Amsterdam: Elsevier, 2011. P. 29. https://doi.org/10.1016/B978-0-444-53563-4.10003-3
Song C. // Catal. Today. 2002. V. 77. P. 17. https://doi.org/10.1016/S0920-5861(02)00231-6
Rostrup-Nielsen J.R., Christensen T., Dybkjaer I. // Recent Adv. Basic Appl. Asp. Ind. Catal. 1998. V. 113. P. 81.
Porsin A.V., Rogozhnikov V.N., Kulikov A.V. et al. // Cryst. Growth Des. 2017. V. 17. P. 4730. https://doi.org/10.1021/acs.cgd.7b00660
Shoynkhorova T.B., Simonov P.A., Potemkin D.I. et al. // Appl. Catal. B. 2018. V. 237. P. 237. https://doi.org/10.1016/j.apcatb.2018.06.003.14
Zhang H., Li X., Zhu F. et al. // Chem. Eng. J. 2017. V. 310. P. 114. https://doi.org/10.1016/j.cej.2016.10.104
Wismann S.T., Engbæk J.S., Vendelbo S.B. et al. // Science. 2019. V. 364. P. 756. https://doi.org/10.1126/science.aaw8775
Pauletto G., Vaccari A., Groppi G. et al. // Chem. Rev. 2020. V. 120. P. 7516. https://doi.org/10.1021/acs.chemrev.0c00149
Shoynkhorova T.B., Rogozhnikov V.N., Ruban N.V. et al. // Int. J. Hydrogen Energy. 2019. V. 44. P. 9941. https://doi.org/10.1016/j.ijhydene.2018.12.148
Pan W. // Catal. Today. 2004. V. 98. P. 463. https://doi.org/10.1016/j.cattod.2004.09.054
Kirillov V.A., Shigarov A.B., Kuzin N.A. et al. // Catalysis in Industry. 2020. V. 12. P. 66. https://doi.org/10.1134/S2070050420010080
Álvarez A., Bansode A., Urakawa A. et al. // Chem. Rev. 2017. V. 117. P. 9804. https://doi.org/10.1021/acs.chemrev.6b00816
Schemme S., Breuer J.L., Köller M. et al. // Int. J. Hydrogen Energy. 2020. V. 45. P. 5395. https://doi.org/10.1016/j.ijhydene.2019.05.028
Pechenkin A.A., Badmaev S.D., Belyaev V.D., So-byanin V.A. // Appl. Catal. B. 2015. V. 166–167. P. 535. https://doi.org/10.1016/j.apcatb.2014.12.008
Thattarathody R., Katheria S., Sheintuch M. // Ind. Eng. Chem. Res. 2019. V. 58. P. 21382. https://doi.org/10.1021/acs.iecr.9b04483
Дополнительные материалы отсутствуют.
Инструменты
Российские нанотехнологии