Российские нанотехнологии, 2022, T. 17, № 1, стр. 79-88
КАТАЛИТИЧЕСКИЕ КОМПОЗИЦИИ, ПОЛУЧЕННЫЕ В МАГНЕТРОНЕ ИЗ КОМПОЗИТНЫХ МИШЕНЕЙ ДЛЯ ЭЛЕКТРОДОВ ТОПЛИВНЫХ ЭЛЕМЕНТОВ И ЭЛЕКТРОЛИЗЕРОВ С ПРОТОНООБМЕННОЙ МЕМБРАНОЙ
С. И. Нефедкин 1, *, М. А. Климова 1, А. В. Рябухин 1, А. В. Чижов 1, И. И. Левин 2
1 Национальный исследовательский университет “МЭИ”
Москва, Россия
2 ООО “Ионтек-Нано”
Москва, Россия
* E-mail: snefedkin@mail.ru
Поступила в редакцию 05.06.2020
После доработки 25.02.2021
Принята к публикации 25.02.2021
Аннотация
Представлены результаты исследования каталитических покрытий, полученных в магнетроне из композитных мишеней для электродов топливных элементов и электролизеров с полимерной протонообменной мембраной. Благородные металлы (платина, иридий) используются как вставки в основные мишени на основе графита, молибдена, титана, никеля. Исследовано влияние различных параметров процессов нанесения в магнетроне на электрохимические и структурные характеристики каталитических композиций. Показана высокая каталитическая активность покрытий. Обсуждается возможность использования магнетронного напыления для создания тонких наноструктурных каталитических композиций в качестве промышленной технологии для топливных элементов и электролизеров с протонообменной мембраной с низким содержанием благородных металлов.
ВВЕДЕНИЕ
Низкотемпературные топливные элементы с полимерной протоноoбменной мембраной (ПОМТЭ) и электролизеры разложения воды с полимерной протоноoбменной мембраной (ПОМЭВ) занимают лидирующие позиции как на рынке топливных элементов (ТЭ), так и на рынке электролизеров [1]. Мировой рынок компонентов мембранных электродных блоков (MЭБ) ПОМТЭ должен составить 2.6 млрд. долларов США к 2022 г. по сравнению с 766 млн. долларов США в 2017 г. И если лидерство ПОМТЭ на рынке ТЭ наметилось достаточно давно, то тенденция постепенного вытеснения электролизеров с щелочным раствором электролита электролизерами с ПОМ уже становится заметной, в том числе в классе высокопроизводительных электролизеров. Электрохимические устройства с ПОМ более компактны и удобны в эксплуатации по сравнению со всеми типами ТЭ и электролизеров. Однако использование платины в коммерческих электрокатализаторах электродов ПОМТЭ, а также иридия в ПОМЭВ остается обязательным, так как они обеспечивают высокую активность электрохимических процессов на электродах и необходимый ресурс. Тем не менее работы в области электрокатализа с целью снижения содержания Pt-металлов в электродах этих устройств, повышения их ресурса и снижения стоимости остаются актуальными.
Современные ПОМТЭ продемонстрировали чрезвычайно высокую плотность мощности и десятки тысяч часов непрерывного срока службы. Если ориентироваться на параметры, объявленные в энергетическом модуле (ЭМ) автомобиля Toyota Mirai-2 (2017 г.), то удельная закладка Pt в катализаторе Pt–Co на катоде составляет 0.1 мг/см2, а в катализаторе анода – Pt–С 0.025 мг/см2 при плотности мощности МЭБ с тонкой ПОМ (14 мкм) 1.1 Вт/см2, Р = 2.5 бар, U = = 0.663, i = 1.65 А/см2 [2]. Таким образом, можно реализовать высокую плотность мощности электрохимических процессов на супертонких наноструктурированных каталитических слоях на основе Pt без ограничений в процессах массопереноса веществ и ионов. Однако стоимость катализатора в ЭМ составляет около 50%, поэтому задача снижения закладки Pt при сохранении высокой удельной мощности ТЭ остается актуальной [1].
Наметились два подхода в электрокатализе ПОМТЭ:
– разработка относительно активных смешанных катализаторов, не содержащих металлов Pt-группы, но с иономером в их составе. Обнадеживающие результаты по использованию композиций Co–N–С, Fe–N–С с иономером получены в [3]. Однако они не достигли уровня Pt-катализаторов по активности и ресурсу;
– синтез тонких наноструктурированных каталитических структур, содержащих Pt и сформированных на новых высокодисперсных носителях. Здесь в качестве носителя и функционального компонента дисперсной Pt могут выступать новые формы углерода, переходные металлы, а для их формирования можно использовать физические методы нанесения, например магнетронный [4]. Важно, что такой электрокаталитический слой формируется на границе пористого газодиффузионного электрода (ГДЭ) и ПОМ фактически в одну технологическую стадию, что значительно упрощает технологию изготовления.
Каждый из электрохимических процессов на электродах ПОМТЭ и ПОМЭВ имеет свои особенности и требует подобранных электрокатализаторов. Например, в качестве катализатора катодной реакции выделения водорода (РВВ) в ПОМЭВ исследовались неплатиновые композиции на основе переходных металлов, в частности на основе вольфрама WC [5], WSx [6], Cu1 –xNixWO4 [7], а также молибдена и кобальта MoS2 [8], MoS2/CoSe2 [9], Mo2C [10], MoSe2 [11], CoP [12]. Однако Pt-содержащие катализаторы имеют лучшую кинетику в РВВ. Так, ток обмена РВВ в 0.5 М H2SO4 для электрокатализатора Pt/C составляет j0 = 0.7 мА см–2, что на порядок выше, чем у самой активной неплатиновой системы MoS2/CoSe2 [9]. Загрузка Pt-катализатора 0.05 мг/см2 с использованием обычного Pt/C-катализатора достаточна для поддержания плотности тока 2 А/см2 [13]. Стратегия сокращения закладки Pt включает в себя ее легирование более дешевыми компонентами, например сообщается о каталитических системах Pt–Ru [14], Pt–Cu, Pt–Pd [15]. Сократить количество Pt можно с помощью структуры катализатора типа ядро–оболочка.
Каталитическая система Pt/C остается основной как для катода ПОМЭВ, так и для анода ПОМТЭ. С использованием магнетронного метода нанесения катализатора в вакууме на поверхность сажевого слоя ГДЭ или пористого титана можно в одном технологическом процессе формировать тонкие наноструктурированные пленки Pt-катализаторов. Ранее было показано, что каталитические черни платины, полученные в магнетроне, проявляют высокую активность на аноде ПОМТЭ даже без использования иономера в каталитическом слое [16–18]. Проблема заключается катодном катализаторе реакции восстановления кислорода (РВК) ПОМТЭ, который требует расширенной трехфазной границы электрохимической реакции и введения в катализатор иономера. Тем не менее в [4] показано, что предварительное азотирование сажи и последующее нанесение в магнетроне дисперсного слоя оксида церия позволяют создать ультратонкие пленки Pt-катализатора, проявляющего высокую активность на катоде ПОМТЭ и без использования иономера. Подобные ультратонкие структуры на основе Pt формировались магнетронным методом с использованием наноструктурированной подложки [19, 20]. Также предложены смешанные катализаторы, например Pt–Ni и Pt–Co, полученные химическим восстановлением компонентов из раствора на углеродном носителе [21–24].
В качестве катализаторов анода в реакции выделения кислорода ПОМЭВ в кислой среде активны композиции оксида иридия с рядом металлов (Ru, Mo, W, V) [25], например Ir0.6V0.4O2. Перспективной добавкой для анода ПОМЭВ может быть молибден [26], в [27] была исследована каталитическая система Ir0.4Ru0.6MoxOy, синтезированная модифицированным методом Aдамса.
В настоящей работе исследованы каталитические композиции, полученные в магнетроне путем распыления в вакууме композитных мишеней для электродов ПОМТЭ и ПОМЭВ. Благородные металлы (платина, иридий) использованы как вставки в основные мишени на основе молибдена, титана, графита, никеля. Основная цель – показать возможности формирования в одном технологическом процессе активных смешанных катализаторов с минимальной закладкой благородных металлов.
ЭКСПЕРИМЕНТАЛЬНАЯ ЧАСТЬ
Каталитические композиции на основе Pt получены на магнетронной установке Краудион-М-11/1 (ООО “Ионтек-Нано”). В тороидальной зоне распыления DC-магнетрона в поле постоянного тока создается низкотемпературная плазма. Под воздействием бомбардировки ионами плазмообразующего газа (Ar+) материал мишени распыляется на подложку. В качестве подложки для исследования катализаторов использовали поверхность микропористого сажевого слоя (МПС) ГДЭ Freudenberg H24C3, а также поверхность титановой фольги марки ВТ-1-0. Для удаления оксида с поверхности титановую фольгу обрабатывали в 50%-ной H2SO4 при температуре 100°С до момента появления газовыделений с последующей отмывкой водой. Мишень магнетрона представляла собой диск диаметром 100 мм из графита, титана, платины, молибдена, циркония и никеля. На основе этих мишеней составляли композитные мишени. Для этого на основной мишени на одинаковом расстоянии друг от друга закрепляли радиальные вставки из платины (иридия) в виде полосок шириной 5 мм, их число менялось от 2 до 8. Дистанция от подложки до мишени (графитовой, титановой, молибденовой, никелевой) составляла 100 мм. Такое расстояние обеспечивало равномерность осаждения композитного покрытия по поверхности подложки. После создания с помощью турбомолекулярного насоса в камере магнетрона высокого вакуума вводили плазмообразующий газ аргон и поддерживали его давление в диапазоне PAr = 4–20 Па. Также с помощью контроля давления изменяли долю реактивного газа кислорода в среде аргона. Для этого использовали параметр ${{\gamma }_{{{{{\text{O}}}_{2}}/({{{\text{O}}}_{2}} + {\text{Ar}})}}}$, который изменялся в пределах ${{\gamma }_{{{{{\text{O}}}_{2}}/({{{\text{O}}}_{2}} + {\text{Ar}})}}}$ = 0–0.75. Распыление мишени проводили при частоте магнетрона 13.56 МГц. Ток магнетрона варьировали в пределах 0.04–0.15 А при напряжении 440–450 В. Массу покрытия определяли взвешиванием на аналитических весах АВ600М-1х. Для оценки удельного содержания компонентов ms в каталитической композиции при распылении составной мишени использовали параметр α – доля площади компонента от общей площади зоны распыления составной мишени, а также параметр kPt – индивидуальный коэффициент распыления компонента, например платины. Для исследований были приготовлены катализаторы из композитной мишени при различном количестве вставок Pt или Ir (2, 4, 6, 8) в основную мишень (С, Ti, Mo, Ni). Доля площади Pt (Ir) α в площади зоны распыления композитной мишени составляла α = 0.06, 0.13 (0.19, 0.26).
Для исследования структуры и элементного состава каталитических композиций использовали сканирующий электронный микроскоп (СЭМ) JSM–6390 LA (JEOL USA, Inc.) с приставкой для энергодисперсионного анализа Oxford. Для микроанализа использовали дифрактометр Rigaku D/Max RC (CuKα-излучение, графитовый кристалл-анализатор, фокусировка по Бреггу–Брентано) в шаговом режиме с шагом Δ2q = 0.05° в интервале углов 2q = 20°–125°.
Электрохимические исследования синтезированных катализаторов проводили в трехэлектродной электрохимической ячейке. В качестве вспомогательного электрода применяли Pt-проволоку, в качестве электрода сравнения – Ag/AgCl-электрод 4M KCl. Рабочий раствор электролита – 0.5 М раствор Н2SO4 – готовили из очищенной ионным обменом воды и серной кислоты (х.ч.). При измерении циклических вольтамперограмм (ЦВА) раствор электролита насыщали аргоном. Все значения потенциалов в работе приведены относительно обратимого водородного электрода (ОВЭ). Активную электрохимическую поверхность (ЭХАП) каталитических композиций на основе Pt определяли на подложке из гладкой титановой фольги по токам окисления водорода на ЦВА, снятой в диапазоне в 0.0–1.2 В (ОВЭ) в 0.5 М H2SO4 при Т = 25°С. Использовали потенциостат Solartron 1287a, скорость развертки потенциала составляла 0.025 В/с. Электрохимическую активность катализаторов, сформированных на поверхности МПС ГДЭ, в реакции восстановления кислорода ПОМТЭ определяли в ячейке (полутопливный элемент из фторопласта) по поляризационным кривым, снятым со скоростью изменения потенциала 1 мВ/с от равновесного значения в область катодных потенциалов. Воздух подавали микрокомпрессором с тыльной части ГДЭ, а со стороны катализатора использовали раствор 0.5 М H2SO4 при температуре 25°С.
РЕЗУЛЬТАТЫ И ИХ ОБСУЖДЕНИЕ
На первом этапе исследований были определены индивидуальные скорости распыления монолитных мишеней, изготовленных из различных материалов. При распылении монолитной мишени в плазме аргона образуются потоки атомного пара материала мишени, который перемещается в направлении подложки. Процесс роста пленки и ее структура на поверхности подложки зависят от энергии частиц, процесс проходит в два этапа. На первом образуются зародыши на поверхности подложки, на втором они растут и объединяются в мелкие кластеры. Возможен островковый механизм роста пленки, когда осаждаемые атомы взаимодействуют между собой сильнее, чем с атомами подложки. Послойный механизм роста пленки преобладает при образовании больших по площади двумерных зародышей на поверхности подложки вследствие того, что атомы напыляемого материала имеют более сильную связь с атомами подложки, чем связь между собой. Послойно-островковый механизм роста пленки возникает, когда островки начинают расти после того, как сформируется пленка толщиной в несколько атомных монослоев. Таким образом, структурные характеристики и свойства пленки определяются условиями и продолжительностью процесса ее формирования. Если в камере магнетрона кроме инертного плазмообразующего газа аргона будет находиться реактивный газ, то он может образовывать химическую связь с атомами распыляемого материала в процессе его движения к подложке, образуя при этом более сложные структуры.
Были исследованы каталитические структуры, полученные из монолитных мишеней, и определены индивидуальные коэффициенты распыления используемых материалов.
Система Pt/C(Ti). Согласно [16, 26, 28] при распылении Pt добавление кислорода в состав плазмообразующего газа аргона приводит к формированию на подложке наноструктурированной “черни” платины с высокой удельной поверхностью и высокой электрохимической активностью. При этом можно предположить, что при малых скоростях напыления в среде кислорода частицы Pt высаживаются по послойно-островковому механизму в вертикальном направлении в виде столбчатых структур. На рис. 1 показана структура платиновой черни, полученная в магнетроне на титановой подложке в одном технологическом процессе при распылении Pt. Видим структуру “куста коралла” с расстоянием между веточками 0.5–2 мкм, а сами веточки осадка Pt имеют более тонкую наноструктуру. Такой Pt-катализатор интересен для процессов выделения водорода в ПОМЭВ, так как сочетает высокую электрохимическую поверхность и каналы для подвода–отвода газообразных реагентов.
Рис. 1.
СЭМ-изображение каталитического осадка Pt, полученного в магнетроне в атмосфере кислорода на поверхности титановой фольги.
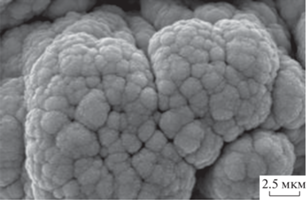
Для выделения кислорода более активным является катализатор на основе иридия, имеющий свои индивидуальные особенности распыления. В связи с этим для различных условий распыления определены индивидуальные скорости распыления различных материалов, в первую очередь Pt.
На рис. 2а показано влияние доли реактивных газов γ (кислорода и ацетилена) в плазмообразующем газе аргоне на скорость распыления Pt. Как видно, повышение γ приводит к снижению скорости распыления Pt. Оксид на поверхности Pt-мишени не имеет сильной связи с поверхностью, поэтому скорость ее распыления высокая уже при малых токах (в данном случае 40 мА). Поскольку реакция Pt с кислородом не приводит к образованию летучих продуктов, можно предположить, что вся Pt доходит до подложки в виде оксида. По данным рентгеновской дифрактометрии обнаружено, что при доле кислорода γ = 0.25 получается пленка с высокой степенью окисления платины (PtO1.5) без каких-либо ее следов в виде неокисленного металла.
Рис. 2.
Скорость распыления платины в плазме аргона при различном содержании реактивных газов – кислорода и ацетилена (γ = 0.6): 1 – кислород; 2 – ацетилен (а). Скорость распыления платины при токе I = 0.1 А в плазме аргона и кислорода (γ = 0.6) от давления в камере магнетрона (б).
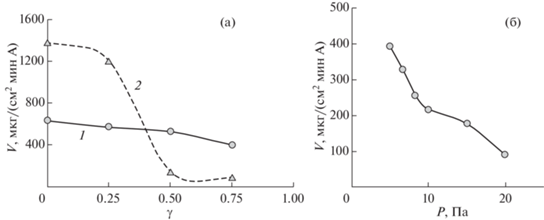
Влияние присутствия ацетилена в аргоне на скорость распыления Pt-мишени более сильное и неоднозначное (рис. 2а, кривая 2). При γ ~ 0.5 до поверхности подложки доходит незначительное количество напыляемого вещества. Это может быть связано как с влиянием ацетилена на процесс образования плазмы аргона и выход атомного пара, так и с химическим взаимодействием атомного пара распыляемого материала с молекулами ацетилена. Возможно образование атомных потоков Pt и C (который образуется из ацетилена в плазме), что также может снижать плотность осадков. Напротив, при увеличении содержания кислорода в плазме аргона скорость распыления Pt плавно линейно снижается (рис. 2а, кривая 1). Поэтому в качестве реактивного газа использовали кислород. Выбор диапазона рабочего давления аргона в камере магнетрона, с одной стороны, ограничен его минимальной плазмообразующей концентрацией, а с другой, снижением скорости распыления материала. Для распыления Pt такая зависимость представлена на рис. 2б. Как видно, повышение давления в камере магнетрона снижает скорость распыления, так как возрастает количество взаимодействий атомного пара распыляемого материала с аргоном и кислородом. В [30] обнаружен эффект снижения размера частиц напыляемого палладия при увеличении давления аргона в камере. Как будет показано далее, при увеличении давления аргона можем также констатировать снижение размера осаждаемых частиц Pt.
СистемаPt/(TiOx)/C. Другой подход заключается в нанесении тонкого нанодисперсного подслоя, например, на основе титана на поверхность основного электрода-носителя (микропористого слоя ГДС или пористого титана). В этом случае можно сформировать нанодисперсную структуру промежуточного слоя носителя для повышения адгезии самого катализатора и коррозионной устойчивости основного носителя [29]. Для сажи Vulcan, на базе которой изготавливается МПС ГДЭ, проблема коррозионной устойчивости существенна и актуальна. После нанесения дисперсных пленок на основе Pt-катализатора с подслоем дисперсного титана их исследовали на предмет активной каталитической поверхности по токам окисления адсорбированного водорода, также исследовалась структура. Тонкий слой титана (~30 нм) предварительно наносили при различном содержании кислорода в аргоновой плазме (γ = 0–1.0). После нанесения дисперсных пленок Pt-катализатора в виде черни (ms = 0.03 мг/см2) c добавкой реактивного газа кислорода (γ = 0.75) были сняты ЦВА. На рис. 3 представлены ЦВА каталитической системы Pt на подслое оксида титана. Как видно, введение кислорода в плазму при нанесении титана приводит к повышению активной поверхности Pt-катализатора примерно на 30%. Однако нанесение титана при γ = 1.0 приводит к снижению активности, видимо, за счет повышения омического сопротивления подслоя полностью окисленного титана (рис. 3, кривая 4). Таким образом, при содержании кислорода в аргоновой плазме (γ ~ 0.75) формируется оптимальная структура подслоя титана, на которой высаживается дисперсная Pt.
Рис. 3.
ЦВА платинового дисперсного катализатора на титановой фольге с подслоем дисперсной пленки диоксида титана (~30 нм); (γ): 1 – 0 (без кислорода), 2 – 0.5, 3 – 0.75, 4 – 1. Раствор электролитa 0.5 М H2SO4; Т = 25°С; msPt = 0.02 мг/см2; V = 0.025 В/c.
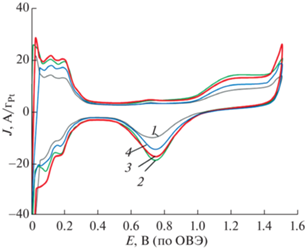
Рис. 4.
Увеличенные СЭМ-изображения катализатора C–Pt, полученного на поверхности сажевого микропористого слоя ГДЭ при магнетронном распылении композитной мишени.
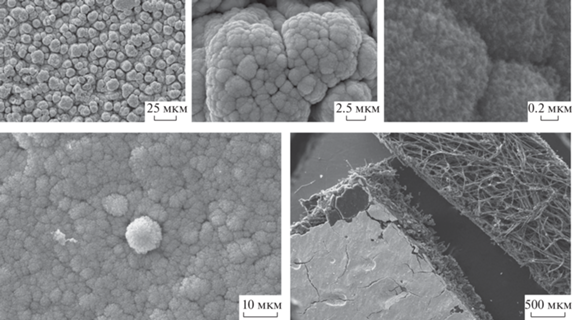
Для исследования активности катализатора в РВК его наносили на МПС ГДЭ Freudenberg H24C3. На рис. 4 показаны увеличенные изображения ГДЭ с нанесенным катализатором. Как видно, частицы каталитической композиции представляют собой тонкодисперсную структуру, которая покрывает тонким слоем частицы сажи МПС ГДЭ. Они имеют форму, близкую к сферической, а их размер составляет 5–15 мкм.
В табл. 1 представлены катодные токи электродов на основе дисперсной Pt с подслоем титана (около 30 нм), снятые при потенциале Е = = 0.7 В (относительно хлор-серебряного электрода сравнения) в полуэлементе (Т = 25°С, 0.5 М Н2SO4). Анализ таблицы показывает, что максимальная электрохимическая активность достигается при содержании 50% кислорода в плазме при нанесении дисперсного подслоя диоксида титана, а также 50% кислорода в плазме уже при нанесении дисперсного слоя Pt (образец 4). Увеличение кислорода в плазме при нанесении подслоя титана уже не повышает активность катализатора. Таким образом, параметр γ оказывает заметное влияние на формирование тонких нанодисперсных структур катализатора и носителя и определяет активность катализатора.
Таблица 1.
Активность каталитических композиций Pt/(TiOx)/C в реакции катодного восстановления кислорода при различных значениях γ при сформировании Pt-катализатора и Ti-подслоя
Pt/(TiOx)/C ($m_{s}^{{{\text{Pt}}}}$ = 0.02 мг/см2) |
γPt | γTi | I, А/мг (Pt) |
---|---|---|---|
1 | 0.75 | 0.75 | 0.8 |
2 | 0.5 | 0.75 | 0.12 |
3 | 0.75 | 0.5 | 0.26 |
4 | 0.5 | 0.5 | 0.34 |
Магнетронное напыление углерода, титана, никеля. Графитовая мишень является самой доступной, однако имеет свои особенности при магнетронном распылении, если использовать добавки реактивного газа кислорода в плазмообразующий газ. Известно, что доминирующим продуктом кислородной реакции в плазме является СО, практически не зависящий от энергии ионов и температуры мишени [30]. При термическом воздействии на графит в присутствии кислорода газ СО образуется лишь при Т более 1000 К. Однако при бомбардировке графита ионами Ar и О2 в магнетроне возможно образование СО, при этом образование СО2 незначительно. Таким образом, углерод в зоне распыления графитовой мишени частично превращается в газообразный продукт, который не доходит до подложки [30]. Как видно из рис. 7б, доля газообразного продукта при распылении графитовой мишени (СО) заметно падает при γ > 0.25 при общем давлении Р = 4 Па. Также обнаружено, что скорости распыления C и Pt на единицу массы различаются в сотни раз (табл. 2). Однако если такие скорости привести к атомной массе, то физические потоки атомов Pt и C в плазме аргона и при небольших добавках кислорода (γ < 0.2) соизмеримы. Этот факт интересен с практической точки зрения и будет использован при синтезе смешанных С–Pt-катализаторов, а также других композитных каталитических систем.
Таблица 2.
Индивидуальные скорости распыления ряда материалов при различном содержании кислорода в плазме аргона ${{\gamma }_{{{{{\text{O}}}_{2}}/({{{\text{O}}}_{2}} + {\text{Ar}})}}}$
Ток магнетрона, А | 0.04 | 0.04 | 1 | 0.15 |
---|---|---|---|---|
${{\gamma }_{{{{{\text{O}}}_{2}}/({{{\text{O}}}_{2}} + {\text{Ar}})}}}$ | Скорость распыления, мкг/А см2 мин | |||
Pt | С | Ti | Ni | |
0 | 630 | 52 | 20.3 | 11.1 |
0.25 | 570.65 | 10.4 | 1.45 | 6.67 |
0.5 | 525.36 | 8.68 | 1.38 | 4.44 |
0.75 | 398.55 | 5.5 | 1.3 | 3.3 |
Атомная масса | 195.09 | 12 | 47.9 | 58.71 |
${{\gamma }_{{{{{\text{O}}}_{2}}/({{{\text{O}}}_{2}} + {\text{Ar}})}}}$ | Скорость распыления, отнесенная к атомной массе | |||
Pt | С | Ti | Ni | |
0 | 3.23 | 4.33 | 0.42 | 0.19 |
0.25 | 2.93 | 0.87 | 0.03 | 0.11 |
0.5 | 2.69 | 0.72 | 0.03 | 0.08 |
0.75 | 2.04 | 0.46 | 0.03 | 0.06 |
ПОЛУЧЕНИЕ КАТАЛИЗАТОРОВ ИЗ КОМПОЗИТНЫХ МИШЕНЕЙ
Система (PtNix)/C. Для практического использования наиболее интересны смешанные катализаторы, полученные при распылении в магнетроне композитных мишеней. Такая мишень состоит из основной мишени из более дешевого и доступного материала (графит, титан, никель, цирконий, молибден) и вставок из благородных металлов, например Pt и Ir. В этом случае возникают более сложные взаимодействия, так как каждый материал имеет свои индивидуальные особенности и скорости при магнетронном распылении (табл. 2). Для системы (PtNix)/C было приготовлено 16 образцов катализаторов и изучено влияние на их активность давления аргона в камере магнетрона Р и доли площади платины в составной мишени αPt/(Pt + Ni). Как видно из табл. 3, высокую активность (катодные токи, измеренные в полуэлементе) имеют образцы, полученные при Р = 4–6 Па и минимальном содержании Pt в мишени αPt/(Pt + Ni) = 0.06. То есть максимальное количество Pt в составе композитной мишени Pt–Ni не приводит к максимальной активности катализатора Pt–Ni. ЭХАП (Sm), определенная по токам окисления адсорбированного водорода ЦВА, коррелирует с этими данными, и, как видно из таблицы, повышение давления плазмообразующего газа аргона в камере магнетрона приводит к увеличению как удельной поверхности катализатора, так и удельной активности катализатора в РВК.
Таблица 3.
Зависимость тока восстановления кислорода i и удельной поверхности катализатора PtNiхSm от параметра αPt/(Pt + Ni) и давления аргона в камере магнетрона
αPt/(Pt + Ni) | PAr, Па | ||||
---|---|---|---|---|---|
0.5 | 2 | 4 | 6 | ||
Sm, м2/г Pt | 0.06 | 19.1 | 8.92 | 9.89 | 13.39 |
0.13 | 13.6 | 11.75 | 5.9 | 17.13 | |
0.19 | 13.1 | 16 | 14.89 | 29.95 | |
0.26 | 16.25 | 18.63 | 19.98 | 37.01 | |
i, А/г(Ni + Pt) | 0.06 | 4.81 | 14.2 | 23.25 | 27.1 |
0.13 | 4 | 24.6 | 30.98 | 21.45 | |
0.19 | 6.28 | 19.15 | 28.5 | 35.2 | |
0.26 | 6.24 | 12.3 | 19.28 | 28.3 |
Система Рt–С/C. Каталитическая система Рt–С/C для ПОМТЭ является коммерчески доступной. Она реализована с использованием синтеза наночастиц Pt в многостадийном технологическом процессе путем химического восстановления из раствора ее соли на частицах сажи [22]. Такой коммерческий катализатор в составе каталитических чернил наносится на поверхность МПС ГДС или мембрану и используется на аноде и катоде ПОМТЭ или на катоде ПОМЭВ. В принципе систему Рt–С можно реализовать в одну стадию в магнетроне при распылении композитной С–Рt-мишени. В этом случае катализатор Рt–С формируется сразу на поверхности сажевого МПС ГДЭ.
Серия экспериментов, проведенная для 16 образцов, показала влияние параметров αPt/(Pt + Ti) и ${{\gamma }_{{{{{\text{O}}}_{2}}/({{{\text{O}}}_{2}} + {\text{Ar}})}}}$ на каталитическую активность в РВВ и их структуру. Микроструктурный анализ образцов выявил несколько общих тенденций. При γ = 0 введение углерода резко снижает средний размер доменов. Наименьший размер домена обнаружен для α = 0.19, образец, который содержит как платину, так и оксид платины, явное проявление одновременных процессов образования твердых и летучих продуктов Pt, PtOx и CO в смешанной плазме. Когда α уменьшается, больше кислорода потребляется для производства CO, поэтому рост PtOx неблагоприятен, и размер домена становится больше. На рис. 5 видим, что высокий ток в РВВ при малой закладке Pt может быть результатом взаимодействия двух эффектов при формировании каталитической C–Pt-структуры: снижение крупных пор в структуре катализатора на основе оксида Pt и увеличение количества более мелких частиц под влиянием реакционного газа кислорода. Известно, что при выделении водорода на электроде растущие пузырьки могут блокировать узкие поры. Хотя такая поверхность может быть доступна для адсорбции водорода, а для выделения может быть затруднена. Оказалось (точка α = 0.06, γ = 0.25), что рост плотных частиц углерода и оксида платины приводит к образованию более плотных пленок, эффект блокирования нейтрализуется, а перенапряжение выделения водорода снижается.
Рис. 5.
Ток выделения водорода, измеренный при Е = = –0.08 В (ОВЭ). Значения нормированы на истинную площадь поверхности.
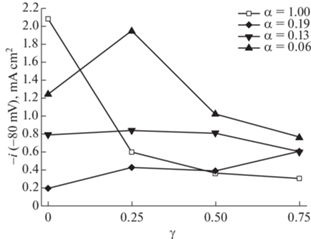
Рис. 6.
Увеличенные (×20 000) СЭМ-изображения катализатора Ir–Mo/Ti при α = 0.19 и различной доле кислорода в плазме аргона: γ = 0 (а), 0.25 (б), 0.5 (в), 0.75 (г).

Система Ir–Mo/Ti. Анодный катализатор для процесса выделения кислорода является наиболее проблемным в ПОМЭВ. Катализатор Ir–Mo/Ti, синтезированный в магнетроне при распылении Mo–Ir-мишени на пористый Ti-коллектор, показал высокую каталитическую активность и коррозионную устойчивость [26]. Также обнаружено, что с увеличением γ размеры сферических частиц уменьшаются с 800–1000 нм при α = 0.19, γ = 0 до 100–200 нм при α = 0.19, γ = 0.75 (рис. 6). При этом сам катализатор приобретает характерный черный цвет.
Предварительное окисление катализатора является необходимым условием его устойчивости. Это достигается как при высоких γ в магнетроне, так и при последующем термическом окислении на воздухе.
Формирование каталитического слоя в одном технологическом процессе. Наиболее распространенной является технология, включающая в себя синтез Pt-содержащего катализатора путем химического восстановления Pt из раствора платиноидов на носитель (например, сажу), получения на его основе каталитических чернил и формирования ультразвуковым напылением каталитических покрытий на поверхности ГДЭ. Процесс является многостадийным и требует использования большого количества оборудования, материалов, реактивов (которые также требуют отдельного синтеза) и воды с высокой степенью очистки. Однако металлическая платина остается как исходным, так и конечным веществом данной технологии, изменяются лишь ее состояние и характерные размеры частиц.
Процесс нанесения C–Pt-катализатора на поверхность ГДЭ можно сделать одностадийным, если использовать физический метод нанесения, например метод магнетронного напыления в вакууме. Приведем пример для катализатора C–Pt, который является востребованным для многих электрохимических процессов (рис. 7). С–Pt-катализатор в виде наноструктурированного слоя наносится на подложку (например, МПС ГДЭ) в одном процессе из исходной металлической платины и графита, которые составляют композитную мишень магнетрона. Углерод в данном случае остается носителем и функциональным разбавителем для платины, который не только снижает стоимость каталитического покрытия, но и придает ему дополнительные свойства.
Физические методы получения каталитических покрытий для технологии ПОМТЭ представляют практический интерес, в том числе, в качестве промышленных технологий. В частности, получение дисперсных катализаторов из композитных мишеней с использованием технологии магнетронного распыления металла упрощает изготовление электродов и делает процесс более технологичным и воспроизводимым. В промышленных магнетронах в одну стадию можно получить электроды с общей площадью поверхности около 2 м2, что соответствует батарее ТЭ мощностью 1 кВт.
ЗАКЛЮЧЕНИЕ
Проведены исследования каталитических покрытий, полученных в магнетроне из композитных мишеней для электродов ПОМТЭ и ПОМЭВ. Благородные металлы (платина, иридий) использовались как вставки в основные мишени на основе молибдена, титана, графита, никеля. Исследовано влияние различных параметров процесса нанесения на электрохимические и структурные характеристики каталитических композиций. Показано, что для электродов ПОМТЭ и ПОМЭВ могут быть получены каталитически активные наноструктурные композиции с низкой закладкой платины или иридия в одностадийном процессе магнетронного напыления, на основе которого может быть освоена промышленная технология.
Авторы выражают благодарность Э.Е. Левину (Центр квантовых технологий МГУ им. М.В. Ломоносова) за помощь и выполнение микроструктурных исследований.
Список литературы
Papageorgopoulos D. U.S. Department of energy. Fuel Cell Technologies Office. 2019 Annual Merit Review and Peer Evaluation Meeting. Fuel Cell R&D Overview April 29. 2019. hydrogenandfuelcells.energy.gov
Thompson S.T., Brian D.J., Huya-Kouadio J.M. et al. // J. Power Sourc. 2018. V. 399. P. 304. https://doi.org/10.1016/j.jpowsour.2018.07.100
Wan X., Liu X., Shui J. // Prog. Natural Sci: Materials International. 2020 V. 30. № 6. P. 721. https://doi.org/10.1016/j.pnsc.2020.08.010
Ostroverkh A., Johánek V., Dubau M. et al. // Int. J. Hydrogen Energy. 2019. V. 44. № 35. P. 19344. https://doi.org/10.1016/j.ijhydene.2018.12.206
Nikiforov A., Petrushina I., Christensen E. et al. // Int. J. Hydrogen Energy. 2012. V. 37. № 24. P. 18591.
Voiry D., Yamaguchi H., Li J. et al. // Nature Mater. 2013. V. 12 (9). P. 850. https://doi.org/10.1038/nmat3700
Selvan R.K., Gedanken A. // Nanotechnology. 2009. V. 20 (5). P. 1176. https://doi.org/10.1039/C0GC00516A
Karunadasa H.I. // Science. 2012. V. 335. № 6069. P. 698.
Gao M.R., Liang J.-X., Zheng Y.R. et al. // Nature Commun. 2015. V. 6. P. 1. https://doi.org/10.1038/ncomms6982
Ma R., Zhou Y., Chen Y. et al. // Angew. Chem. Int. Ed. 2015. V. 54 (49). P. 14723.
Huang Y.A., Lu H., Gu H. et al. // Nanoscale. 2015. V. 7 (44). P. 18595. https://doi.org/10.1039/C5NR05739F
Popczun E.J., Read C.G., Roske C.W. et al. // Angew. Chem. Int. Ed. 2014. V. 53 (21). P. 5427. https://doi.org/10.1002/anie.201506727
Lewinski K.A., van der Vliet D., Luopa S.M. // ECS Trans. 2015. V. 69 (17). P. 893.
Ayers K.E., Renner J.N., Danilovic N et al. // Catal. Today. 2016. V. 262. P. 121.
Tymoczko J., Calle-Vallejo F., Schuhmann W., Bandarenka A.S. // Nat. Commun. 2016. V. 7. P. 10990.
Nefedkin S.I., Kholichev O.V., Pavlov V.I. et al. // Russ. J. Electrochem. 2014. V. 50 (7). P. 617. https://doi.org/10.1134/S102319351407009X
Quiñones C., Vallejo W., Mesa F. // Appl. Surf. Sci. 2011.V. 257 (17). P. 7545. https://doi.org/10.1016/j.apsusc.2011.03.121
Fedotov A.A., Grigoriev S.A., Lyutikova E.K. et al. // Int. J. Hydrogen Energy. 2013. V. 38 (1). P. 426. https://doi.org/10.1016/j.ijhydene.2012.09.121
Stevens D.A., Mehrotra R., Sanderson J. et al. //J. Electrochem. Soc. 2011. V. 158. P. B905. https://doi.org/10.1149/1.3595747
Debe M.K. // Catalysts J. Electrochem. Soc. 2013. V. 160 (6). P. 522. https://doi.org/10.1149/2.049306jes
Kamitaka Y., Taguchi N., Morimoto Y., Assessing. // Catalysts. 2018. V. 8. P. 258.
Alekseenko A.A., Guterman V.E., Belenov S.V. et al. // Int. J. Hydrogen Energy. 2018. V. 43. P. 3676.
Cortés-Escobedo C.A., Gonzalez-Huerta R.G., Bolarin-Miroet A.M. // Int. J. Hydrogen Energy. 2014. V. 39 (29). P. 16722. https://doi.org/10.1016/j.ijhydene.2014.03.025
Емец В.В., Тарасевич М.Р., Бусев С.А. // Электрохимия. 2011. Т. 47. № 3. С. 367.
Takasu Y., Yoshinaga N., Sugimoto W. // Electrochem. Commun. 2008. V. 10. P. 668.
Нефедкин С.И., Климова М.А., Коломейцева Е.А. и др. // Электрохимия. 2017. Т. 53. № 3. С. 1.
Cheng J., Zhang H., Ma H. et al. // Int. J. Hydrogen Energy. 2009. V. 34. P. 6609.
Nefedkin S.I., Shaposhnikov D.Y., Nefedkina A.V. US Patent № US 10.654.034 B2 Date of patent: May 19, 2020.
Alexeeva O.K., Fateev V.N. // Int. J. Hydrogen Energy. 2016. V. 41 (5). P. 3373. https://doi.org/10.1016/j.ijhydene.2015.12.147
Vietzke E., Tanabe T., Philippset V. et al. // J. Nucl. Mater. 1987. V. 145. P. 425. https://doi.org/10.1016/0022-3115(87)90374-6
Дополнительные материалы отсутствуют.
Инструменты
Российские нанотехнологии