Российские нанотехнологии, 2022, T. 17, № 3, стр. 333-340
Синтез субмикронного карбида бора безвакуумным методом с косвенным подводом тепловой энергии дугового разряда постоянного тока
Р. С. Мартынов 1, *, А. Я. Пак 2, Г. Я. Мамонтов 2
1 АО “НПЦ “Полюс”
Томск, Россия
2 Томский политехнический университет
Томск, Россия
* E-mail: rsm6@tpu.ru
Поступила в редакцию 11.01.2021
После доработки 11.01.2021
Принята к публикации 29.05.2021
Аннотация
Изложены результаты экспериментальных исследований, демонстрирующие возможность получения порошка карбида бора путем обработки смеси углерода и аморфного бора, содержащего незначительное количество оксида бора, плазмой дугового разряда постоянного тока. Особенностью применяемого безвакуумного электродугового метода синтеза карбида бора является его реализация в открытой воздушной среде благодаря достижению эффекта экранирования реакционной зоны газообразными оксидом и диоксидом углерода. При этом исходные реагенты нагреваются до необходимых температур плазмой дугового разряда постоянного тока, горящего в непосредственной близости от смеси исходных материалов в полости графитового тигля. В полученном материале присутствуют частицы карбида бора размером субмикронного диапазона, которые характеризуются структурой типа “оболочка–ядро”. Описанная в работе схема разрядного контура лабораторного реактора с горизонтальным расположением электродов и косвенным подводом тепловой энергии к исходным реагентам позволяет существенно повысить содержание фазы карбида бора и снизить содержание примесной фазы графита.
ВВЕДЕНИЕ
Карбид бора является широко известным сверхтвердым веществом, применяемым в различных отраслях [1–3]. Материалы на основе карбида бора характеризуются комплексом важных свойств, среди которых можно выделить высокую температуру плавления (около 2620–2740°С) и микротвердость (до 4950 кг/мм2) при относительно низкой плотности (2.46–2.52 г/см3) [4, 5]. Существует несколько подходов к получению таких материалов.
Одним из основных считается карботермическое восстановление оксида бора в диапазоне температур от 1500 до 2300°С в инертной газовой среде в течение нескольких часов с использованием различных прекурсоров, содержащих бор и углерод [6–8]. Известным подходом к синтезу карбида бора является метод самораспространяющегося высокотемпературного синтеза [9]. Также кристаллические фазы карбида бора получают путем размола исходных материалов в шаровых мельницах в течение длительного времени (до нескольких дней) [10], воздействием потоков энергии высокой плотности, в частности электронными пучками [11]. Объемные керамические материалы на основе карбида бора получают методами искрового плазменного спекания [12, 13] и горячего прессования [14]. Одним из перспективных методов синтеза карбида бора является электродуговой [15, 16], который последние годы развивается в направлении упрощения и удешевления используемого оборудования, в частности, за счет реализации в инертной газовой среде нормального атмосферного давления или на открытом воздухе [17–19]. Ранее была показана возможность синтеза ультрадисперсного карбида бора в плазме дугового разряда постоянного тока, инициированного в открытой воздушной среде [20]. Метод основан на достижении эффекта самоэкранирования реакционного объема от кислорода воздуха продуктами горения дугового разряда на графитовых электродах, а именно, газами монооксида углерода и диоксида углерода. Данный метод требует оптимизации для синтеза карбида бора, так как исходная смесь бора (и оксида бора) с углеродом характеризуется низкой электропроводностью, что затрудняет надежное инициирование дугового разряда. Кроме того, продукт синтеза существенно загрязнен катодным депозитом графитового анода, поскольку исходное сырье загружается непосредственно в зону инициирования и горения дугового разряда. Решением этой проблемы может послужить реализация такой схемы разрядного контура, при которой исходная смесь находится за пределами указанной зоны, а осаждение эродированного графита осуществляется не в зоне нахождения исходных реагентов. В настоящей работе изложены результаты экспериментальных исследований, в ходе которых был реализован синтез субмикронных кристаллов карбида бора при косвенном нагреве исходной смеси частиц, содержащей аморфный бор (с примесями оксида бора B2O3) и рентгеноаморфный углерод C (сажу), атмосферной плазмой дугового разряда постоянного тока.
МЕТОДЫ ИССЛЕДОВАНИЯ
Серию экспериментов проводили на лабораторном электродуговом реакторе. В качестве источника тока использовали управляемый выпрямительно-инверторный преобразователь, настраиваемый предварительно на силу постоянного тока 160 А. Вольт-амперные характеристики дугового разряда регистрировали при помощи двухканального цифрового осциллографа марки Rigol DS1052E, а также омического делителя напряжения и датчика тока. Катод располагался неподвижно, а анод перемещали при помощи винтовой передачи. В первой серии экспериментов в качестве катода использовали графитовый стакан высотой 30 мм с диаметром полости 21 мм, на дно которого закладывали исходную смесь рентгеноаморфного углерода (сажи) и аморфного бора (с примесями оксида бора). В полость катода вертикально опускали цилиндрический графитовый анод, после этого инициировали дуговой разряд. Согласно второй схеме два графитовых стержня располагали горизонтально, соосно, образуя разрядный промежуток [21]. Смесь, содержащую бор (с примесью оксида бора) и углерод, помещали на дно графитового тигля, который располагали таким образом, чтобы над его дном на расстоянии 10 мм горел дуговой разряд. Исходная смесь содержала 22 мас. % углерода и 78 мас. % аморфного бора (с примесью оксида бора B2O3), в каждом эксперименте использовалось 0.3 ± 0.03 г исходной смеси. Дуговой разряд поддерживали до 20 с, в результате чего в реакционной зоне выделялось до 90 кДж энергии; длительность поддержания дугового разряда изменяли в серии экспериментов. Температуру внешней стенки графитового стакана (тигля) фиксировали высокотемпературным пирометром Benetech GM1850.
Полученные материалы собирали со дна и стенок графитового стакана и анализировали методом рентгеновской дифрактометрии (Shimadzu XRD 7000s, CuKα-излучение), просвечивающей электронной микроскопии (ПЭМ) (JEOL JEM 2100F). Для проведения качественного анализа рентгеновских дифрактограмм использовали стандартное программное обеспечение фирмы Shimadzu, а также базу данных PDF4+. Для проведения количественного рентгенофазового анализа применяли программу Powder Cell 2.4. Для анализа результатов ПЭМ служило программное обеспечение Gatan Digital Micrograph версии 1.8.
РЕЗУЛЬТАТЫ И ИХ ОБСУЖДЕНИЕ
На рис. 1 представлены типичные рентгеновские дифрактограммы полученных продуктов синтеза. Во всех продуктах идентифицируются три кристаллические фазы: графит gC, оксид бора B2O3, карбид бора B4C и рентгеноаморфная компонента. Данная компонента представляет собой остатки непереработанных в процессе синтеза бора и углерода. Формирование графита в рассматриваемой системе – это естественно согласно известным диаграммам состояний углерода. Образование фазы карбида бора также является ожидаемым ввиду ранее проведенных экспериментов, показывающих возможность получения карбидов металлов и неметаллов рассматриваемым безвакуумным электродуговым методом [22].
Рис. 1.
Типичные рентгеновские дифрактограммы продуктов синтеза в системе углерод–бор: 1 – полученного при вертикальном расположении электродов с прямым воздействием дугового разряда на исходную смесь, энергия дуги до 35 кДж; 2 – полученного при вертикальном расположении электродов с прямым воздействием дугового разряда на исходную смесь, энергия дуги до 90 кДж; 3 – полученного при горизонтальном расположении электродов с косвенным нагревом исходной смеси дуговым разрядом, энергия дуги до 35 кДж; 4 – полученного при горизонтальном расположении электродов с косвенным нагревом исходной смеси дуговым разрядом, энергия дуги до 90 кДж.
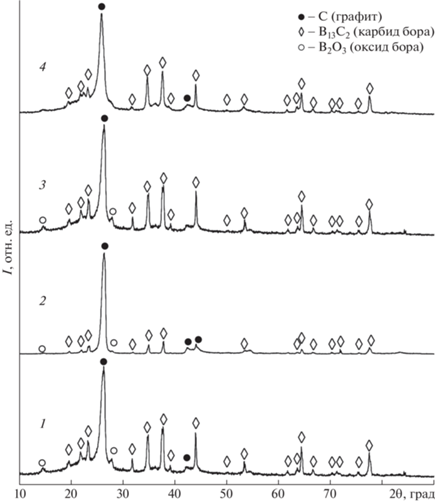
Согласно рентгеновским дифрактограммам 1 и 2 (рис. 1) при использовании вертикальной схемы расположения электродов с увеличением энергии дуги от 35 до 90 кДж существенно снижается интенсивность дифракционных максимумов оксида бора и карбида бора; практически полностью исчезает рентгеноаморфная компонента. При этом значительно возрастает интенсивность дифракционных максимумов графита. Проводя анализ ряда рентгеновских дифрактограмм продуктов, полученных при закладке исходных реагентов непосредственно в зону инициирования дугового разряда (т.е. при схеме с вертикальным расположением электродов), можно заметить, что для полной переработки исходного бора и его оксида требуется длительное воздействие дугового разряда (до 20 с при силе тока 160 А). При этом эродированная масса графита анода, расходуемая частично на формирование газовой среды СО и СО2 и попадающая частично в продукт синтеза, может составлять до 0.8–0.9 г. В результате доля графита в продукте синтеза составляет не менее 75 об. %. Соответственно, содержание фазы карбида бора в этом случае не может превышать 25 об. %.
Применение горизонтальной схемы расположения электродов с косвенным подводом тепловой энергии дугового разряда к исходной смеси позволяет минимизировать загрязнение продукта синтеза эродированным графитом. На рис. 1 представлены рентгеновские дифрактограммы 3, 4 типичных продуктов синтеза, полученных при горизонтальном расположении электродов с энергией дугового разряда до 35 и 90 кДж соответственно. Анализ серии рентгеновских дифрактограмм показывает, что увеличение энергии дугового разряда позволяет минимизировать содержание исходного кристаллического оксида бора. Кроме того, степень кристалличности с ростом энергии дуги возрастает с 45 до 56%. Провести полную переработку исходных рентгеноаморфных бора и углерода в данной серии экспериментов не удалось, по-видимому, по причине снижения плотности потока энергии при переходе от вертикальной схемы электродной системы к горизонтальной. Кроме того, известно, что при горении дугового разряда постоянного тока между графитовыми электродами создается тепловое поле с высоким градиентом температуры и максимумом до 10 000 К в зоне инициирования разряда и снижением температуры примерно на 1000 К при удалении на 1–2 мм центра дуги; таким образом, переход к системе с горизонтальным расположением электродов ведет к интегральному снижению температуры процесса синтеза. При этом до 55% массы эрозии анода осаждается на поверхности катода, что позволяет избежать значительного роста доли фазы графита с увеличением количества подведенной энергии путем увеличения продолжительности синтеза. Такой подход обеспечил рост доли карбида бора (в составе кристаллической основы продукта) не менее чем до 54 об. %. Очевидно, что для полной переработки исходного сырья требуется увеличение количества подведенной энергии. В рассматриваемой серии экспериментов температура графитового тигля, в котором располагалась смесь исходных реагентов, поднималась до 800°С при поддержании дугового разряда в течение 20 с. Для преодоления этого барьера в дальнейшем будут рассмотрены варианты повышения силы тока разрядного контура и, соответственно, уменьшения расстояния между исходными материалами и зоной инициирования и горения разряда.
Для проведения ПЭМ был выбран образец с наибольшим содержанием карбида бора в рассматриваемой серии. Пробу готовили путем нанесения спиртовой суспензии полученного порошка, обработанной в ультразвуковой ванне, на стандартную медную сетку, покрытую аморфным углеродным слоем.
Согласно результатам ПЭМ продукта, полученного безвакуумным электродуговым методом с горизонтальным расположением электродов, в типичном продукте синтеза можно идентифицировать четыре основных типа объектов. Согласно данным энергодисперсионного анализа скопление основных типов различных объектов (рис. 2) состоит из 22.2 ат. % бора, 72.5 ат. % углерода, 4.8 ат. % кислорода и 0.5 ат. % прочих элементов. По данным рентгеновской дифрактометрии наличие бора и углерода представляется естественным в силу доминирования в продукте синтеза фаз карбида бора и графита. Содержание 4.8 ат. % кислорода может свидетельствовать о наличии некоторого количества в продукте оксида бора, имеющегося в составе исходного сырья, а также адсорбированного кислорода. По картам распределения химических элементов (рис. 2б–2д) видно, что форма скопления частиц коррелирует с картами распределения бора и углерода и не коррелирует с картой распределения кислорода. Следовательно, отдельные частички в составе продукта, форма которых соответствует карте распределения кислорода, не были выделены.
Рис. 2.
Снимки скопления частиц в составе продукта синтеза: а – светлопольный снимок, б – темнопольный снимок, снятый в режиме сканирующей–просвечивающей электронной микроскопии, в – карта распределения бора, г – углерода, д – кислорода.
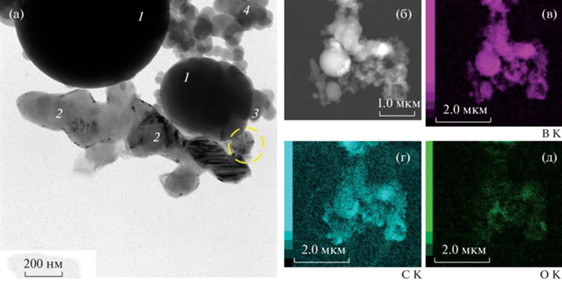
Объекты первого типа представляют собой относительно крупные, не просвечивающиеся электронным пучком (вероятно, сферические) частицы размерами от 0.5 до 1 мкм. Судя по картам распределения химических элементов, объекты первого типа состоят из бора и углерода.
Объекты второго типа также представляют собой частицы, содержащие бор и углерод (рис. 3). Данные частицы характеризуются размерами около 100 нм, в них просматривается неоднородная структура (в частности, видна оболочка, которая более четко различима на снимках в режиме высокого разрешения).
Рис. 3.
Снимки скопления объектов первого и второго типов в составе продукта синтеза: а – светлопольный, снятый в режиме сканирующей–просвечивающей электронной микроскопии, б – карта распределения бора, в – углерода.
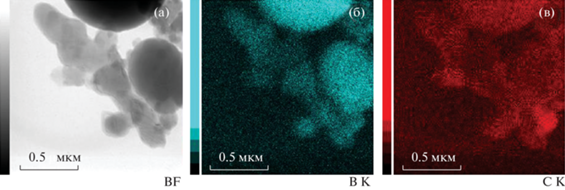
Отдельную область частиц второго типа, полученную при помощи просвечивающего электронного микроскопа, можно увидеть на рис. 4а. По картине дифракции электронов (рис. 4б) можно идентифицировать множество межплоскостных расстояний, соответствующих структуре данных частиц. Для удобства данные анализа двух типичных картин электронной дифракции представлены в табл. 1 в сравнении с эталонными. Отметим, что в международной базе данных PDF 4+ имеется множество эталонных карточек фаз карбида бора различной стехиометрии, преимущественно B4C и B13C2. Подобные структуры различаются по размерам элементарной ячейки незначительно. Соответственно, в табл. 1 представлены данные из карточки № 00-026-0233, которая соответствует одной из типичных структур карбида бора. Видно, что экспериментально определенные межплоскостные расстояния 4.45, 4.00, 3.72, 2.50, 2.31, 1.86, 1.64, 1.45, 1.37 и 1.25 Å достаточно точно в пределах возможных погрешностей соответствуют эталонным межплоскостным расстояниям карбида бора. Несоответствующие фазе карбида бора межплоскостные расстояния, определенные экспериментально: 3.52, 2.14, 2.00, 1.54 и 1.18 Å, соответствуют структуре графита. Для фазы графита вычисленное межплоскостное расстояние 3.52 Å несколько больше эталонного d002 = 3.41 Å, это может быть связано с результатом допирования кристаллической структуры примесными атомами, такое явление нередко характерно и для графитоподобных 2D-материалов [23].
Рис. 4.
Результаты ПЭМ высокого разрешения частиц второго типа: а – светлопольный снимок отдельной частицы, б – соответствующая картина дифракции электронов, в – снимок ядра частицы в режиме прямого разрешения, г – снимок оболочки частицы в режиме прямого разрешения.
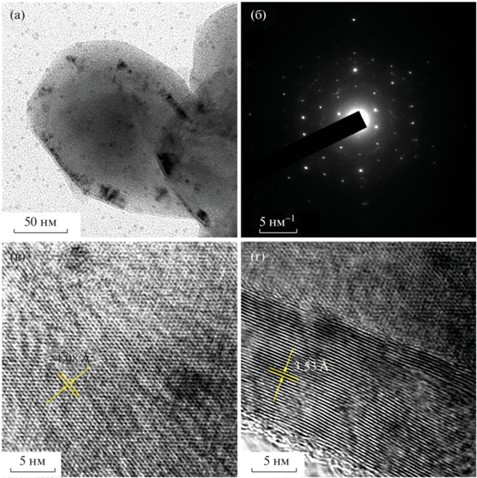
Таблица 1.
Экспериментально определенные межплоскостные расстояния по картинам дифракции электронов в сравнении с эталонными
Межплоскостные расстояния согласно картине дифракции электронов 1 (рис. 4б) | Межплоскостные расстояния согласно картине дифракции электронов 2 (не представлен на рисунке) | Эталонные межплоскостные расстояния фазы B13С2 (PDF4+) |
---|---|---|
4.45 | 4.44 | 4.50 |
4.00 | 4.03 | |
3.72 | 3.77 | |
3.56 | 3.52 | |
2.50 | 2.50 | 2.57 |
2.31 | 2.31 | |
2.14 | 2.17 | |
2.00 | ||
1.86 | 1.86 | 1.82 |
1.64 | 1.68 | 1.63 |
1.52 | 1.54 | |
1.45 | 1.46 | |
1.37 | 1.36 | 1.34 |
1.25 | 1.27 | 1.26 |
1.19 | 1.18 |
Снимки в режиме прямого разрешения позволяют идентифицировать структуру частиц второго типа как “оболочка–ядро” (рис. 4). Толщина оболочки составляет до 20 нм, в теле оболочки отчетливо идентифицируются межплоскостные расстояния с d = 3.53 ± 0.03 Å, что, как отмечалось ранее, соответствует структуре графита. В ядре частицы просматриваются хорошо упорядоченная структура и межплоскостные расстояния с d = 4.08 ± 0.02 Å. Таким образом, объекты второго типа можно идентифицировать как кристаллы карбида бора в графитовой оболочке.
Объекты третьего типа представляют собой фазу так называемого полиэдрического графита, отличающегося характерной морфологией [24] (рис. 5а). Средний размер частиц третьего типа составляет 100–200 нм. По соответствующей типичной картине дифракции электронов (рис. 5б) можно идентифицировать межплоскостные расстояния 3.60, 2.16, 1.79 и 1.29 Å. Формирование данного морфологического типа графита в условиях горения дугового разряда считается возможным при конденсации испаренного углерода [25].
Объекты четвертого типа представляют собой аморфные сферические частицы размерами 100–200 нм (рис. 5в). Данные частицы, вероятно, могут являться фазой аморфного бора, не переработанного в процессе синтеза, что коррелирует с картиной дифракции электронов (рис. 5г).
По совокупности представленных данных можно сделать вывод о возможности синтеза субмикронных частиц карбида бора разрабатываемым безвакуумным электродуговым методом. Частицы карбида бора характеризуются размерами ~100–200 нм и структурой типа “оболочка–ядро”. Характерной особенностью применяемой в серии экспериментов схемы разрядного контура является горизонтальное расположение электродов, обеспечивающее косвенный нагрев исходной смеси, содержащей бор и углерод, плазмой дугового разряда. При используемой схеме исходная смесь с низкой электрической проводимостью не включается в силовую цепь, чем обеспечивается стабильное горение дугового разряда по сравнению с ранее используемой вертикальной схемой расположения электродов. Кроме того, данная схема позволяет минимизировать загрязнение продукта синтеза материалом эрозии графитового анода, так как продукт синтеза формируется не на поверхности катода в составе разрядного контура, а в графитовом тигле с нулевым потенциалом под зоной инициирования и горения разряда. При этом в рамках проведенной серии экспериментов не удалось полностью переработать исходные рентгеноаморфные реагенты. Для решения этой проблемы в будущем будут проведены исследования по зависимости величины силы тока разрядного контура, а также расстояния смеси исходных реагентов от дугового разряда.
Исследование выполнено в рамках программы развития Томского политехнического университета, а также в рамках Государственного задания вузам (FSWW-0022-2020). Просвечивающая электронная микроскопия проведена на базе Наноцентра Томского политехнического университета.
Список литературы
Domnich V., Reynaud S., Haber R.A. et al. // J. Am. Ceram. Soc. 2011. V. 9. № 11. P. 3605. https://doi.org/10.1111/j.1551-2916.2011.04865.x
Sasaki S., Takeda M., Yokoyama K. et al. // Sci. Technol. Adv. Mater. 2005. V. 6. № 2. P. 181. https://doi.org/10.1016/j.stam.2004.11.010
LaSalvia J.C., Leavy R.B., Houskamp J.R. et al. // Ceram. Eng. Sci. Proc. 2009. V. 30. № 5. P. 45.
Андриевский Р.А. // Успехи химии. 2012. Т. 81. Вып. 6. С. 549.
Косолапова Т.Я. Карбиды. М.: Металлургия, 1968. 300 с.
Thevenot F. // J. Eur. Ceram. Soc. 1990. V. 6. № 4. P. 205. https://doi.org/10.1016/0955-2219(90)90048-K
Kakiage M., Tominaga Y., Yanase I. et al. // Powder Technol. 2012. V. 221. P. 257. https://doi.org/10.1016/j.powtec.2012.01.010
Rao M.P.L.N., Gupta G.S., Manjunath P. et al. // Int. J. Refract. Met. Hard Mater. 2009. V. 27. № 3. P. 621. https://doi.org/10.1016/j.ijrmhm.2008.10.004
Zhang F., Fu Z., Zhand J. et al. // Ceram. Int. 2010. V. 36. № 4. P. 1491. https://doi.org/10.1016/j.ceramint.2010.02.013
Mortensen M.W., Sorensen P.G., Bjordahl O. et al. // Appl. Radiat. Isot. 2006. V. 64. № 3. P. 315. https://doi.org/10.1016/j.apradiso.2005.08.003
Pasquale F.L., Kelber J.A. // Appl. Surf. Sci. 2012. V. 258. № 7. P. 2639. https://doi.org/10.1016/j.apsusc.2011.10.110
Hayun S., Kalabukhov S., Ezersky V. et al. // Ceram. Int. 2010. V. 36. № 2. P. 451. https://doi.org/10.1016/j.ceramint.2009.09.004
Hayun S., Paris V., Dariel M.P. et al. // J. Eur. Ceram. Soc. 2009. V. 29. № 16. P. 3395. https://doi.org/10.1016/j.jeurceramsoc.2009.07.007
Roszeitis S., Feng B., Martin H.-P. et al. // J. Eur. Ceram. Soc. 2014. V. 34. № 2. P. 327. https://doi.org/10.1016/j.jeurceramsoc.2013.08.013
Zhou D., Seraphin S., Withers J. C. // Chem. Phys. Lett. 1995. V. 234. № 1–3. P. 233. https://doi.org/10.1016/0009-2614(95)00039-7
Tu R., Li N., Li Q. et al. // J. Eur. Ceram. Soc. 2016. V. 36. № 16. P. 3929. https://doi.org/10.1016/j.jeurceramsoc.2016.06.049
Joshi R., Engstler J., Nair P.K. et al. // Diamond Relat. Mater. 2008. V. 17. № 6. P. 913. https://doi.org/10.1016/j.diamond.2008.01.004
Zhao J., Wei L., Yang Z. et al. // Phys. E. Low-dimen. Syst. Nanostruct. 2012. V. 44. № 7–8. P. 1639. https://doi.org/10.1016/j.physe.2012.04.010
Arora N., Sharma N.N. // Diamond Relat. Mater. 2014. V. 50. P. 135. https://doi.org/10.1016/j.diamond.2014.10.001
Pak A.Ya., Mamontov G.Ya. // Tech. Phys. Lett. 2018. V. 44. P. 615. https://doi.org/10.1134/S1063785018070234
Мартынов Р.С., Пак А.Я., Мамонтов Г.Я. Устройство для получения порошка на основе карбида бора // Патент России № 2019111857. 2019. Бюл. № 26.
Pak A.Ya., Shanenkov I.I., Mamontov G.Y., Kokorina A.I. // Int. J. Refract. Met. Hard Mater. 2020. V. 93. P. 105343. https://doi.org/10.1016/j.ijrmhm.2020.105343
Hou B.H., Wang Y.Y., Lu H.Y. et al. // Electrochim. Acta. 2018. V. 268. P. 323. https://doi.org/10.1016/j.electacta.2018.02.105
Thinius S., Islam M.M., Bredow T. // Surf. Sci. 2016. V. 649. P. 60. https://doi.org/10.1016/j.susc.2016.01.027
Song X., Liu Y., Zhu J. // Mater. Lett. 2007. V. 61. № 26. P. 4781. https://doi.org/10.1016/j.matlet.2007.03.032
Дополнительные материалы отсутствуют.
Инструменты
Российские нанотехнологии