Российские нанотехнологии, 2022, T. 17, № 4, стр. 532-540
Влияние типа углеродного материала на формирование теплопроводящего скелета в гранулах кобальтовых катализаторов синтеза Фишера–Тропша
К. О. Грязнов 1, *, Л. В. Синева 1, Д. А. Овсянников 1, Е. О. Наливайко 1, В. З. Мордкович 1
1 Технологический институт сверхтвердых и новых углеродных материалов
Троицк, Москва, Россия
* E-mail: gryaznovkirill@tisnum.ru
Поступила в редакцию 03.12.2021
После доработки 20.12.2021
Принята к публикации 07.01.2022
Аннотация
Приготовлена серия гранулированных композитных материалов, полученных на основе оксида алюминия и цеолита. Исследовано влияние введения углеродных материалов (терморасширенный графит, элементный графит, коллоидный графит, канальная сажа, углеродные нанотрубки) в состав композита на физико-химические и каталитические свойства полученных кобальтсодержащих систем. Показано, что формируемый материалами теплопроводящий скелет необходим для поддержания стабильной работы гранул катализатора при высоких нагрузках по исходному сырью.
ВВЕДЕНИЕ
Cинтез Фишера–Тропша (СФТ) – технология получения углеводородов для производства высококачественных моторных топлив из углеродсодержащего сырья ненефтяного происхождения (уголь, природный газ, биомасса). Основные проблемы, существенно ограничивающие промышленную реализацию процесса, – собственная низкая производительность классических катализаторов процесса, а также значительная экзотермичность реакций СФТ, сопряженная с высокой чувствительностью процесса к температуре его проведения [1]. Поэтому повышение производительности катализатора и катализаторного слоя на его основе – комплексная задача, сочетающая необходимость создания как высокоактивных центров основной реакции (гидрополимеризации CO) и вторичных превращений (крекинг, олигомеризация, изомеризация, гидрирование), так и развитой пористой системы для транспорта реактантов и продуктов синтеза, а также теплопроводящего скелета для эффективного отвода тепла реакции от активных центров. С этой точки зрения решение поставленной задачи приводит к концепции композитного катализатора, в котором на уровне гранул реализовано эффективное сочетание разнородных материалов, несущих отдельные либо взаимосвязанные функции и формирующих единую структурированную систему.
Для создания теплопроводящего катализаторного слоя чаще всего предлагают использовать структурированные катализаторы, например монолиты из алюминия или сплавов [2, 3], пены из алюминия или меди [4, 5], либо углеродные материалы: нановолокна, войлок и т.п. [6]. Основные недостатки данных каталитических систем заключаются в сложности равномерного закрепления активного в катализе компонента на металлической структуре монолитов, в ячейках пен, а также поверхности волокнистых углеродных материалов, возможности окисления либо собственной активности металлического компонента в реакциях с CO. Все это существенно усложняет и препятствует производству катализаторов такого типа в промышленном масштабе. Опубликовано небольшое количество работ, в которых теплопроводящая добавка является одним из компонентов в составе гранул катализатора [7, 8].
Цель настоящей работы – изучение возможности создания теплопроводящего скелета из различных углеродных материалов в гранулах кобальт-цеолитных катализаторов СФТ для повышения их коэффициента теплопроводности и, как следствие, увеличения производительности катализатора по жидким углеводородам.
МЕТОДЫ
Электронные микрофотографии исходных углеродных материалов, а также внутренней структуры гранул катализаторов были получены на сканирующем электронном микроскопе (СЭМ) TESCAN VEGA 3 SEM. Ускоряющее напряжение – 5 кВ. Внутренняя структура наноматериалов исследована с помощью просвечивающего электронного микроскопа (ПЭМ) JEM-2010. Ускоряющее напряжение – 160 кВ.
Информация об удельной поверхности и пористой структуре катализаторов получена методом низкотемпературной сорбции азота на приборе Quantachrome Nova Touch LX-2.
Сорбционную емкость по воде (влагоемкость) исследуемых катализаторов определяли гравиметрически, методика основана на результатах [9].
Исследование фазового состава проводили на приборе Empyrean Panalytical Diffractometer. Излучение – Kα, диапазон измерения 2θ – 10°–70°. Информация о средних размерах кристаллитов Co3O4 получена из расчета области когерентного рассеяния (ОКР) для пиков соответствующей фазы.
Коэффициент теплопроводности катализаторов рассчитывали из данных по изобарной теплоемкости (дифференциальный сканирующий калориметр DSC 8000 (Perkin Elmer)), коэффициенту температуропроводности (анализатор LFA 457/2/G MicroFlash (NETZSCH)) и данных кажущейся плотности гранул.
Катализаторы, исследованные в настоящей работе, были приготовлены в соответствии с методикой, описанной в патенте [10]. Носители представляют собой гранулы пористого структурированного композитного материала, состоящего из цеолита HB, связующего – бемита и теплопроводящей добавки. В качестве теплопроводящей добавки (рис. 1) использовали терморасширенный графит (ТРГ), углеродные нанотрубки (УНТ), канальную сажу (КС), элементный графит (ЭГ) и коллоидный графит (КГ). Микрофотографии теплопроводящих компонентов представлены на рис. 1.
Рис. 1.
СЭМ-изображения теплопроводящих добавок ТРГ (а), ЭГ (б), ТРГ+УНТ (в), КГ (г) и ПЭМ-изображение КС (д).
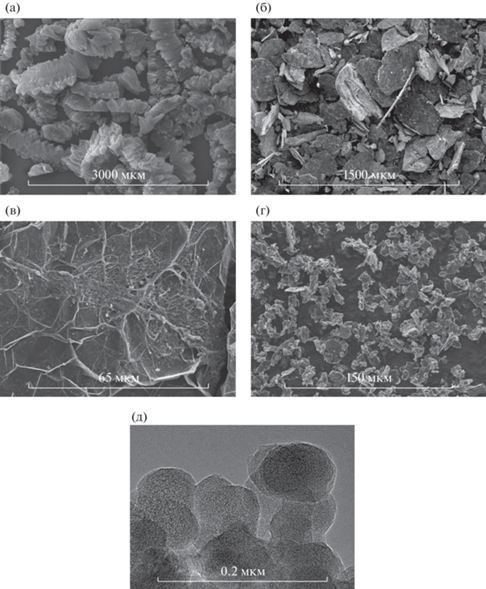
Носители готовили смешением порошков в жидкой фазе, представляющей собой смесь 9.4%-ной HNO3, триэтиленгликоля и С2Н5ОН. После достижения однородности пасту формовали с помощью поршневого экструдера через фильеру с отверстием диаметром 1.5 мм. Экструдаты высушивали, прокаливали и измельчали до цилиндрических гранул диаметром 1.0–1.25 мм и длиной 1.25–1.50 мм (рис. 2).
Название и состав носителей, рассчитанный на сухие исходные вещества, представлены в табл. 1.
Таблица 1.
Состав носителей на исходные сухие компоненты
Носитель | Содержание компонентов, мас. % | ||||||
---|---|---|---|---|---|---|---|
ТРГ | УНТ | КС | ЭГ | КГ | Цеолит | Бемит | |
ТРГ | 20 | 0 | 0 | 0 | 0 | 30 | 50 |
ТРГ+УНТ | 15 | 5 | 0 | 0 | 0 | 30 | 50 |
ТРГ+КС | 15 | 0 | 5 | 0 | 0 | 30 | 50 |
ТРГ+ЭГ | 15 | 0 | 0 | 5 | 0 | 30 | 50 |
КГ | 0 | 0 | 0 | 0 | 20 | 30 | 50 |
В качестве активного компонента СФТ использовали кобальт. Все катализаторы готовили методом двухстадийной пропитки соответствующего носителя водным раствором шестиводного нитрата кобальта (Со(NO3)2 · 6H2O) с прокаливанием после каждой пропитки в токе воздуха при 250°С в течение 1 ч. Содержание кобальта во всех катализаторах составляет 20 мас. %.
СФТ проводили в проточном кожухотрубном реакторе (внутренний диаметр – 10 мм) с неподвижным слоем гранулированного кобальтового катализатора. В реактор загружали 2.5 см3 катализатора. Перед синтезом катализатор восстанавливали в реакторе в токе водорода, подаваемого с объемной скоростью 3000 ч–1 при 400°С и 0.1 МПа в течение 1 ч.
После восстановления катализатор разрабатывали при 2 МПа в токе синтез-газа с мольным соотношением Н2:CO = 2 (в состав смеси вводили 5 мол. % N2 в качестве внутреннего стандарта), подаваемого с объемной скоростью 1000 ч–1, поднимая температуру от 170 до 215–228°С на 3–10°С каждые 6 ч в режиме пуск–остановка. Затем скорость синтез-газа поднимали с шагом 1000 ч–1, оптимизируя температуру при каждой объемной скорости. Оптимизацию проводили по соотношению производительность–селективность. Для этого температуру повышали до момента начала снижения производительности или селективности образования целевого продукта (углеводороды C5+).
Состав газообразных и жидких продуктов определяли хроматографически. Анализ исходной смеси и газообразных продуктов (СН4, СО2, углеводороды С2–С4) проводили с помощью газо-адсорбционной хроматографии. Детектор – катарометр. Газ-носитель – гелий, расход газа – 20 мл/мин. Для разделения СО и СН4 использовали колонку 3 м × 3 мм с молекулярными ситами СаА, для разделения СО2 и углеводородов С2–С4 – колонку с HayeSep тех же размеров 3 м × 3 мм. Режим – температурно-программированный (60–200°С, скорость нагрева – 10°С/мин).
Состав жидких углеводородов С5+ определяли методом газожидкостной хроматографии. Детектор – ПИД. Газ-носитель – гелий (расход газа – 30 мл/мин). Колонка – капиллярная, длиной 50 м, неподвижная фаза – DB-Petro. Режим – температурно-программированный (50–270°С, скорость нагрева – 4°С/мин).
РЕЗУЛЬТАТЫ И ИХ ОБСУЖДЕНИЕ
На рис. 3 представлены рентгеновские дифрактограммы исследованных катализаторов. Из рисунка видно, что фазовые составы катализаторов согласно рентгенофазовому анализу аналогичны друг другу, определены фазы оксида кобальта Co3O4, графита и цеолита HB. По ОКР рентгеновского излучения кристаллитов Co3O4 были вычислены их размеры (табл. 2).
Таблица 2.
Физико-химические свойства катализаторов
Катализатор | Удельная поверхность, м2/г | Объем пор по азоту, см3/г | Влагоемкость, см3/г | Коэффициент теплопроводности, Вт/(м К) | Размер кристаллитов Co3O4, нм |
---|---|---|---|---|---|
ТРГ | 193 | 0.20 | 0.35 | 8.99 | 12.1 |
ТРГ + УНТ | 216 | 0.21 | 0.32 | 8.50 | 17.0 |
ТРГ + КС | 243 | 0.20 | 0.47 | 10.67 | 10.0 |
ТРГ + ЭГ | 230 | 0.19 | 0.46 | 10.09 | 9.2 |
КГ | 247 | 0.20 | 0.23 | 4.23 | 12.0 |
Основные физико-химические свойства катализаторов представлены в табл. 2. Изотермы низкотемпературной сорбции азота исследованных катализаторов представлены на рис. 4.
Все катализаторы характеризовались схожими изотермами низкотемпературной сорбции азота. Согласно классификации ИЮПАК данная форма петли гистерезиса относится к типу H3 [11], характерной для материалов с доминирующей щелевой пористостью. В случае исследуемых катализаторов она образована частицами ТРГ либо КГ. Значительное количество поглощенного азота в области низких относительных давлений обусловлено наличием в составе катализаторов цеолита HB и γ-Al2O3 (образовавшегося из исходного бемита после термообработки экструдатов) с развитой структурой микропор. Отметим, что все катализаторы, за исключением ТРГ+УНТ, характеризуются близкими величинами сорбции азота при низких относительных давлениях P/P0. Причину этого рассмотрим ниже.
Из данных, представленных в табл. 2, видно, что катализаторы характеризуются близкими значениями удельной поверхности (метод Брунауэра–Эммета–Теллера), наибольшая величина характерна для катализатора КГ, наименьшая – ТРГ (247 и 193 м2/г соответственно).
Все исследуемые катализаторы характеризуются близкими значениями объема пор по азоту (0.19–0.21 см3/г), в то время как существенные различия наблюдаются по влагоемкости (0.23–0.47 см3/г). Наименьшей величиной влагоемкости характеризовался катализатор КГ (0.23 см3/г). Вероятно, это связано с тем, что размер его частиц не позволяет создать макропористую структуру, поэтому сорбционная емкость по воде и азоту сопоставима (0.20 и 0.23 см3/г соответственно), хотя по приготовлению его содержание в катализаторе аналогично ТРГ (20 мас. %). Это видно из сравнения электронных микрофотографий, представленных на рис. 5.
Из рис. 5 видно, что в катализаторе КГ частицы графита распределены отдельно в матрице из связующего, в то время как в катализаторе ТРГ частицы графита (волнистые и протяженные) сгруппированы, ориентированы и формируют развитую сеть транспортных макропор по всей грануле. Аналогичным образом можно объяснить и столь низкий коэффициент теплопроводности катализатора КГ (4.23 Вт/(м К)), связанный с тем, что частицы КГ изолированы друг от друга, их объемного содержания в матрице недостаточно для формирования сплошной теплопроводящей сети в грануле.
Близкими величинами влагоемкости и коэффициентами теплопроводности характеризовались катализаторы ТРГ и ТРГ + УНТ (0.35 и 0.32 см3/г соответственно). Это является неожиданным, так как согласно данным [11] УНТ уже при малом содержании способны существенно повысить коэффициент теплопроводности свыше 1 мас. %. На рис. 6 представлены микрофотографии сколов гранул носителя и катализатора ТРГ + УНТ.
Из рис. 6 видно, что в общем случае УНТ распределены в матрице связующего. Однако если в носителе они распределены кучно и равномерно по всему связующему, то в катализаторе они представлены отдельными фрагментами и визуально их очень мало. Согласно данным для многостенных УНТ [12] при термическом разложении нитрата кобальта происходит повреждение поверхности УНТ образующимися оксидами азота и кислородом, а также частицами оксида кобальта, которые способны проникать через образующиеся дефекты и внутрь УНТ. Поскольку в катализаторе ТРГ + УНТ были использованы двустенные УНТ, то их повреждение может быть значительным. Поскольку закрепление оксида кобальта на поверхности графита слабо, он склонен к миграции и агломерации в более крупные частицы, что подтверждается данными по ОКР (табл. 2). В результате окисления, по-видимому, количества оставшихся УНТ недостаточно для повышения коэффициента теплопроводности катализатора, поэтому по этой величине он аналогичен катализатору ТРГ (8.50 и 8.99 Вт/(м К) соответственно). Также наблюдаемое на рис. 3 отличие в изотерме сорбции связано именно с окислением УНТ в матрице связующего и образованием на их месте пустот, образующих более крупные мезопоры.
Наибольшими размерами пор, определенными по влагоемкости, характеризуются катализаторы ТРГ + КС и ТРГ+ЭГ (0.47 и 0.46 см3/г соответственно). В случае катализатора с элементным графитом этот эффект является ожидаемым, поскольку частицы ЭГ сопоставимы по размерам с частицами ТРГ и явно участвуют в формировании системы макропор. Они несколько крупнее их, сформированы из плоских агломератов графита, что, вероятно, приведет к частичному сохранению формы и после экструзии. Причина, по которой катализатор, содержащий канальную сажу, также имеет столь высокую величину влагоемкости, не очевидна. Возможно, в процессе приготовления катализатора она влияет на формирование матрицы связующего, что при экструзии приводит к перераспределению частиц ТРГ. Электронные микрофотографии внутренней структуры гранул катализаторов ТРГ + КС и ТРГ + ЭГ в различном масштабе представлены на рис. 7.
На рис. 7а видна внутренняя структура катализатора ТРГ + ЭГ, наблюдаются волнистые частицы ТРГ, частица ЭГ, ребро которой в результате экструзии сформовано в правильную ломаную линию, а также матрица связующего, скрепляющая все воедино. Похожим образом выглядит внутренняя структура катализатора ТРГ + КС (рис. 7в). Однако при большем увеличении видно, что морфология связующего различна: у катализатора ТРГ + ЭГ она визуально однородная, плотная и равномерно заполняет частицы графита (рис. 7б), а в случае ТРГ + КС – более рыхлая и пористая (рис. 7г).
Сравнение распределения агломератов частиц ТРГ в катализаторах ТРГ и ТРГ + КС представлено на рис. 8.
Из микрофотографий видно, что добавление КС влияет на характер распределения и размер агломератов ТРГ. В случае катализатора ТРГ (рис. 8а) они меньше и более равномерно распределены по грануле, в случае ТРГ + КС (рис. 8б) они представлены либо одиночными частицами графита, либо более крупными агломератами, чем у катализатора ТРГ. Таким образом, канальная сажа действительно влияет на формирование структуры гранул, вызывая перераспределение частиц ТРГ, что приводит к росту влагоемкости и коэффициента теплопроводности на уровне, сравнимом с введением в состав элементного графита.
Все катализаторы были активны в СФТ. Зависимость основных каталитических характеристик от объемной скорости синтез-газа представлена на рис. 9.
Рис. 9.
Каталитические показатели в зависимости от объемной скорости синтез-газа: а – конверсия CO, б – производительность по углеводородам C5+, в – селективность образования C5+, г – селективность образования CH4.
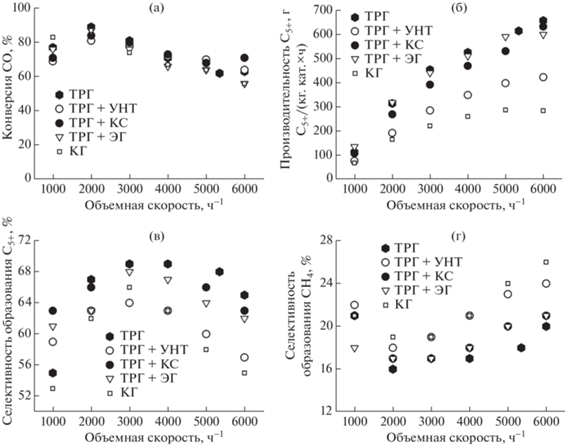
Конверсия CO (рис. 9а) возрастала с 70–80 до 80–90% в интервале 1000–2000 ч–1 и плавно снижалась до 60–80% при 6000 ч–1. Видно, что в области объемных скоростей 1000–5000 ч–1 катализаторы близки по величинам конверсии CO и лишь при 6000 ч–1 наблюдается заметный разброс значений (55–75%).
Производительность по углеводородам C5+ возрастала во всем интервале объемных скоростей. При сравнении катализаторов по данной характеристике заметный разброс значений наблюдается уже при 1000 ч–1 (70–130 г С5+/(кг кат. ч)) и с ростом объемной скорости разброс увеличивается (так, при 6000 ч–1 производительность углеводородов C5+ катализаторов ТРГ и КГ различалась в 2.6 раза, 650 и 250 г С5+/(кг кат. ч) соответственно).
Наблюдаемое изменение производительности углеводородов C5+ коррелирует с изменением величин селективностей образования углеводородов С5+. В общем случае она возрастала в интервале объемных скоростей синтез-газа 1000–3000 ч–1, а затем плавно снижалась (рис. 9в). При этом уже при 1000 ч–1 наблюдались существенные различия, а также характер изменения этой величины. Так, в диапазоне объемных скоростей синтез-газа 2000–6000 ч–1 наибольшими величинами характеризовались катализаторы ТРГ и ТРГ + КС (63–70%). Наименьшей селективностью образования углеводородов С5+ характеризовались катализаторы ТРГ + УНТ и КГ, для которых во всем диапазоне измерений эта величина не превышала 64 и 66% соответственно.
Противоположным образом с ростом объемной скорости синтез-газа изменялась селективность образования CH4. В общем случае изменение данной величины с ростом объемной скорости подачи синтез-газа имеет минимум при 2000 ч–1, а затем возрастает в интервале 3000–6000 ч–1 (рис. 9г). Наименьшей величиной селективности образования CH4 характеризовался катализатор ТРГ, она составила 16–21% во всем интервале объемных скоростей синтез-газа. Наибольшей величиной селективности образования CH4 характеризовались катализаторы КГ и ТРГ + УНТ, во всем интервале объемных скоростей синтез-газа она изменялась в диапазоне 19–27 и 18–24% соответственно.
ЗАКЛЮЧЕНИЕ
Применение терморасширенного графита в сочетании с другими углеродными материалами позволяет сформировать единый теплопроводящий скелет и структуру транспортных пор в гранулах кобальт-цеолитного катализатора СФТ. Отдельное применение коллоидного графита не привело к формированию аналогичной структуры в грануле катализатора, вероятно, в силу недостаточного количества контактов между теплопроводящими частицами. Интересно отметить, что сочетание наноразмерной канальной сажи с терморасширенным графитом в массовом соотношении 1:3 привело к получению композитного катализатора по свойствам, близкого к аналогу, содержащему макроразмерный элементный графит в аналогичном массовом соотношении. Показано, что частицы сажи повлияли на свойства связующего, что привело к получению более рыхлой структуры, а также формированию более крупных агломератов терморасширенного графита, распределенных в матрице связующего. С помощью метода сканирующей электронной микроскопии показано, что углеродные нанотрубки в процессе приготовления катализатора (при термолизе нитрата кобальта) практически полностью окисляются и не способны значимо повлиять на физические свойства катализатора.
Применение углеродных материалов различных размеров (как макро-, так и наноматериалов) способно значимым образом повлиять на итоговые свойства каталитической системы. Так, катализатор КГ с низким коэффициентом теплопроводности и объемом транспортных пор, определенным по влагоемкости, является наименее селективным и производительным в образовании жидких углеводородов. Катализатор ТРГ + КС, характеризующийся наибольшими значениями этих физических свойств, был наиболее селективным и производительным в условиях высоких объемных скоростей синтез-газа. Катализатор ТРГ + ЭГ, характеризующийся немного меньшим коэффициентом теплопроводности и сопоставимым объемом пор, был заметно менее селективным, а катализатор ТРГ мало отличался от ТРГ + КС по производительности и селективности, несмотря на значительно меньший коэффициент теплопроводности и величину влагоемкости. Поскольку содержание теплопроводящей добавки в готовом катализаторе достигает 16 мас. %, нельзя пренебрегать влиянием поверхности частиц углеродного материала на размер кристаллитов кобальта, образующихся при его нанесении из нитратного раствора с последующей термообработкой. Известно, что размер кристаллитов активного металла на поверхности катализатора влияет на показатели СФТ, в первую очередь на его селективность [14]. Наименьшая активность, производительность и селективность катализатора КГ связаны с недостаточным для массообмена объемом транспортных пор, а также низким коэффициентом теплопроводности [2, 15]. Таким образом, коэффициент теплопроводности, объем транспортных пор и размер кристаллитов кобальта являются определяющими факторами для стабильной эксплуатации катализатора при высоких объемных скоростях синтез-газа.
Авторы выражают благодарность И.А. Пережогину за проведение исследований в области просвечивающей электронной микроскопии и С.И. Жолудеву за проведение измерений в области рентгеновской дифракции и обработку полученных результатов.
Работа выполнена с использованием оборудования ЦКП ФГБНУ ТИСНУМ “Исследования наноструктурных, углеродных и сверхтвердых материалов”.
Список литературы
Maitlis P.M., de Klerk A. Greener Fischer–Tropsch Processes. Weinheim: Wiley–VCH, 2013. 372 p.
Merino D., Sanz O., Montes M. // Fuel. 2017. V. 210. P. 49. https://doi.org/10.1016/j.fuel.2017.08.040
Visconti C.G., Tronconi E., Groppi G. et al. // Chem. Eng. J. 2011. V. 171. № 3. P. 1294. https://doi.org/10.1016/j.cej.2011.05.014
Fratalocchi L., Visconti C.G., Groppi G. et al. // Chem. Eng. J. 2018. V. 349. P. 829. https://doi.org/10.1016/j.cej.2018.05.108
Park J.C., Roh N.S., Chun D.H. et al. // Fuel Proc. Tech. 2014. V. 119. P. 60. https://doi.org/10.1016/j.fuproc.2013.10.008
Fu T., Li Z. // Chem. Eng. Sci. 2015. V. 135. P. 3. https://doi.org/10.1016/j.ces.2015.03.007
Asalieva E., Gryaznov K., Kulchakovskaya E. et al. // Appl. Catal. A. 2015. V. 505. P. 260. https://doi.org/10.1016/j.apcata.2015.08.006
Wang D., Chen C., Wang J. et al. // Appl. Catal. A. 2016. V. 527. P. 60. https://doi.org/10.1016/j.apcata.2016.08.027
ГОСТ 17219-71. Угли активные. Метод определения суммарного объема пор по воде.
Мордкович В.З., Синева Л.В., Кульчаковская Е.В. и др. Катализатор для синтеза Фишера–Тропша и способ получения этого катализатора. Пат. 2685437 (Россия). 2017.
Карнаухов А.П. Адсорбция. Текстура дисперсных и пористых материалов. Новосибирск: Наука, 1999. 470 с.
Morishita T., Matsushita M., Katagiri Y. et al. // J. Mater. Chem. 2011. V. 21. P. 5610. https://doi.org/10.1039/c0jm04007j
Larrude D.G., Ayala P., da Costa M.E.H.M. et al. // J. Nanomater. 2012. V. 2012. P. 1. https://doi.org/10.1155/2012/695453
Rahmati M., Huang B., Mortensen M.K. et al. // J. Cat. 2018. V. 359. P. 92. doi: 14. https://doi.org/10.1016/j.jcat.2017.12.022
Ermolaev V., Gryaznov K., Mitberg E. et al. // Chem. Eng. Sci. 2015. V. 138. P. 1. https://doi.org/10.1016/j.ces.2015.07.036
Дополнительные материалы отсутствуют.
Инструменты
Российские нанотехнологии