Российские нанотехнологии, 2022, T. 17, № 4, стр. 547-554
САМОРАСПРОСТРАНЯЮЩИЙСЯ ВЫСОКОТЕМПЕРАТУРНЫЙ СИНТЕЗ КОМПОЗИТА Ti–Si–С С ИСПОЛЬЗОВАНИЕМ ФУЛЛЕРИТОВ
Р. М. Никонова 1, *, Н. С. Ларионова 1, В. И. Ладьянов 1
1 Научный центр металлургической физики и материаловедения
Удмуртского федерального исследовательского центра УрО РАН
Ижевск, Россия
* E-mail: rozamuz@udman.ru
Поступила в редакцию 03.12.2021
После доработки 03.12.2021
Принята к публикации 10.12.2021
Аннотация
Методом самораспространяющегося высокотемпературного синтеза получен композиционный материал 3Ti–Si–2C, где в качестве углерода использован фуллерит С60/70. Методами рентгеноструктурного анализа, растровой электронной микроскопии исследованы его фазовый состав и структура. Показано, что в результате синтеза сформирован композит, содержащий карбид TiC, карбосилицид Ti5Si3Cx, MAX-фазу Ti3SiC2, а также следы силицида титана TiSi2. Структура образцов неоднородна и содержит области, состоящие одновременно из нескольких фаз.
ВВЕДЕНИЕ
Одной из основных задач современного материаловедения является создание новых материалов, отвечающих постоянно возрастающим требованиям к их функциональным свойствам. Это приводит к развитию существующих и созданию новых технологий получения материалов различного конструкционного назначения. Одним из таких перспективных научно-технологических направлений является самораспространяющийся высокотемпературный синтез (СВС) [1]. СВ-синтез позволяет получать самые разнообразные материалы, обладающие уникальными физическими и механическими свойствами: однофазные карбиды, нитриды, оксиды, силициды, твердые растворы, интерметаллиды (TiC, TiCN, Al2O3 и др.) и различные многофазные материалы (высокотемпературная керамика, высокоэнтропийные сплавы и др.) [1–6].
В основе СВС лежит процесс экзотермического взаимодействия двух или нескольких химических элементов или соединений, протекающий с выделением тепла в режиме направленного горения. Он является многофакторным процессом, при котором скорость распространения фронта горения реагирующего слоя и температура реакции зависят от многих параметров. К ним относятся состав смеси, теплопроводность смеси порошков, теплота образования химического соединения, форма и размер частиц, дефектность структуры частиц порошков и др. Главные преимущества СВС-технологий получения материалов состоят в том, что синтез идет за счет тепла химических реакций и не требует дополнительной энергии, в высокой скорости горения (10–30 мм/с), высокой чистоте получаемых материалов (примеси разлагаются и/или улетучиваются в процессе синтеза), в возможности получения материалов в одну стадию непосредственно в волне горения [1–6].
Появляются работы, в которых рассматривается возможность применения СВС-технологии для получения тройных соединений системы Ti–Si–С [7–9]. В последнее время эта система привлекает особое внимание исследователей как перспективный материал высокотемпературной керамики. Одно из возможных соединений этой системы (Ti3SiC2) является типичным представителем семейства МАХ-фаз, отвечающих общей формуле Mn + 1AXn, где М – переходный металл, А – элемент А-подгруппы таблицы Менделеева, Х – углерод или азот. Отличительной особенностью МАХ-фаз является слоистость структуры с гексагональной плотной упаковкой, в которой карбидные/нитридные блоки разделены монослоями атомов А (Al, Si и др.) [10, 11]. Показана возможность получения Ti3SiC2 методами in-situ горячего прессования (наиболее часто используемый метод) [10, 12, 13], механосинтеза с последующим отжигом [14], искрового плазменного спекания [15], магнетронного распыления [16], спекания в импульсном разряде [17]. СВС в настоящее время остается менее изученным методом получения МАХ-фаз.
Применяют различные подходы при осуществлении синтеза Ti–Si–С. В качестве исходной реакционной смеси используются как чистые порошки Ti/Si/C, так и смеси с карбидами Ti/C/SiC [12–14] и Ti/Si/TiC [15–18]. При этом основная проблема при получении МАХ-фаз путем СВС заключается в присутствии в конечных продуктах синтеза примесных фаз. Примесными фазами, образующимися в процессе синтеза, могут быть TiC, TiSi2, SiC, Ti5Si3, Ti5Si3Cx, которые оказывают существенное влияние на свойства получаемого композита. Главной причиной фазовой неоднородности при синтезе МАХ-фаз является многостадийность процессов высокотемпературного гетерогенного взаимодействия компонентов порошковой смеси.
На последовательность реакций в процессе синтеза может оказывать структура используемого углерода. Как правило, применяют сажу или измельченный графит [19]. При использовании сажи и графита в результате СВС-реакции формируется 71.5 и 82.5 об. % Ti3SiC2 соответственно, при этом независимо от используемого углерода добавление карбида SiC приводит к выходу ~85 об. % Ti3SiC2 [19]. В [20] показано, что использование высокоактивного углерода и мелкодисперсного графита повышает выход Ti3SiC2, при избытке углерода в продуктах синтеза увеличивается количество TiC, а при недостатке помимо карбида формируется Ti5Si3. О влиянии активированного угля и графита на синтез Ti3SiC2 указывается в работе [12], в которой использовался другой наиболее часто применяемый метод получения Ti3SiC2 – метод горячего прессования. Показана возможность формирования 98 и 87 мас. % Ti3SiC2 при использовании угля и графита соответственно.
Уникальные свойства фуллерита, существенно отличающегося от других углеродных материалов своей структурой, позволяют использовать его в различных направлениях [21]. Сравнительные исследования [22, 23] показали, что кинетика формирования структурно-фазового состава механокомпозитов Fe–С и Cu–С с использованием графита и фуллерита зависит от формы углерода и определяется его деформационной стабильностью. В [24, 25] показана возможность применения фуллерита в качестве дисперсно-упрочняющей фазы в металломатричных материалах. В [26] показано, что использование фуллерита препятствует рекристаллизации нанофрагментированных материалов. Исследования формирования MAX-фазы Ti3SiC2 с применением в качестве источника углерода фуллерита не проводились.
В настоящей работе представлены результаты исследований композита Ti–Si–С, полученного методом СВС с использованием фуллерита.
МЕТОДЫ
Для приготовления исходных шихтовых заготовок использовали смесь порошков титана марки ПТМ-1 (99%), кремния марки Кр-00 (99%) и углерода в стехиометрическом соотношении 3Ti–Si–2C. В качестве углерода использовали смесь фуллерита С60/70. Фуллериты С60/70 получены методом электродугового испарения графитовых стержней с последующей экстракцией фуллеренов из фуллеренсодержащей сажи кипящим толуолом в приборе “Сокслет” и дальнейшей кристаллизацией фуллерита из раствора в ротационном испарителе. Смесь С60/70, согласно данным жидкостной хроматографии, содержит преимущественно С60 и С70 (82.18 и 14.08 мас. % соответственно). В качестве примесей присутствуют 2.81 мас. % оксидов С60О, С60О2 и С70О; 0.93 мас. % высших фуллеренов С76, С78, С82, С84. Содержание остаточного толуола в образце, согласно термогравиметрическому анализу, составляет 1.1 мас. %.
Исходные порошки предварительно сушили при температуре 150°С в течение 2 ч. Механическое перемешивание исходных компонент осуществляли в смесителе со скоростью вращения 19 об./мин в течение 2 ч. Далее смесь засыпали в тигель диаметром 48 мм и высотой 49 мм. Процесс СВС проводили в реакторе РВС-10 объемом 10 л, изготовленном в НЦ МФМ УдмФИЦ УрО РАН, в атмосфере аргона при РAr = 105 атм. Волну послойного горения реакционной смеси инициировали раскаленной вольфрамовой спиралью.
Фазовый состав полученных образцов анализировали с использованием метода рентгеноструктурного анализа (РСА) (дифрактометр ДРОН-6, CuKα-излучение). Поверхность изломов образцов исследовали на растровом электронном микроскопе (РЭМ) Termo Fisher Scientific Quattro S с возможностью энергодисперсионного микроанализа на основе спектрометра EDAX Octane Elect Plus EDS System.
РЕЗУЛЬТАТЫ И ИХ ОБСУЖДЕНИЕ
Изображения исходных порошков Ti, Si и C60/70 приведены на рис. 1. Порошки титана размером 5–15 мкм имеют неправильную (иррегулярную), сглаженную форму и развитую поверхность частиц (рис. 1а, 1б). Порошки кремния имеют камневидную форму размером 150–200 мкм (рис. 1в). Порошок фуллерита C60/70 представляет собой частицы размером ~60–200 мкм (рис. 1г). Частицы имеют плоскую форму (в плоскости размером менее 10 мкм, рис. 1е), рыхлые внутри, состоящие из более мелких частиц ~1–4 мкм (рис. 1д).
В результате СВС-реакции получен образец, общий вид которого представлен на рис. 2а, вид в срезе – 2б. Образец – цилиндр диаметром 48 мм. Из рисунка видно, что образец пористый. На ощупь – твердый, не рассыпается. Для дальнейших исследований выбраны три различных участка – с поверхности, середины и края образца (рис. 2б).
Исследования показали, что в результате СВ-синтеза сформирован композит, характеризующийся наличием нескольких фаз. По данным РСА исходные компоненты Ti, Si и фуллерит отсутствуют (рис. 3). Фазовый состав на краю, поверхности и середине образца (дифрактограммы 1, 2 и 3 соответственно) характеризуется наличием карбида TiC, фаз Ti5Si3Cx, Ti3SiC2, а также силицида TiSi2. При этом их количественное соотношение различно (табл. 1). На дифрактограмме с поверхности образца кристаллические пики уширены, что может быть обусловлено большей дисперсностью фаз. В отличие от края и поверхности на дифрактограмме середины образца наряду с рефлексами фаз TiC, Ti5Si3Cx, Ti3SiC2 наблюдается интенсивный рефлекс вблизи 2θ ~ 50°. В указанной области находится линия силицида TiSi2. Однако соотношение интенсивности его линий не соответствует равновесному состоянию TiSi2 – наиболее интенсивная линия на дифрактограмме находится вблизи 2θ = 50°, тогда как должна быть вблизи 38° (вставка на рис. 3). Перераспределение интенсивности рефлексов TiSi2 может быть обусловлено наличием текстуры в образце вследствие очень высоких скоростей формирования фаз при СВС.
При количественном анализе учет TiSi2 не дает адекватного описания экспериментальной дифрактограммы. Поэтому при расчетах силицид титана TiSi2 не учитывали. Результаты расчетов представлены в табл. 1. Из анализа таблицы видно, что на различных участках образца количество карбида TiC варьируется в пределах – 34–57%, MAX-фазы Ti3SiC2 – 20–35%, фазы Ti5Si3Cx от 7 до ~50%. Последняя фаза – силикокарбид Ti5Si3Cx, не имеющий определенной стехиометрии по углероду, является промежуточной при формировании Ti3SiC2 [7, 19, 20]. Значительные отличия количественного фазового состава середины края и поверхности образца, вероятно, объясняются неоднозначностью определения силицида TiSi2.
Исследования, выполненные методом растровой электронной микроскопии, показали, что полученный композит сформирован плотными глобулами размером более 300 мкм (рис. 4а). При детальном анализе микроструктуры видно, что указанные глобулы имеют неоднородное строение. Обнаружены плотные пакеты (рис. 4б–4д) и частицы округлой формы (рис. 4е), имеющие слоистую структуру, характерную для МАХ-фаз. Частицы округлой формы имеют сильно сглаженный, “оплавленный” вид (рис. 4е). Согласно дисперсионному анализу эти участки (рис. 4б–4д) могут соответствовать МАХ-фазе Ti3SiC2 и/или промежуточной фазе – Ti5Si3Cx (рис. 5, спектры 1–3). Имеются локальные участки, в которых присутствуют частицы правильной геометрической формы с ровными гранями (рис. 4ж, 4з), соответствующие карбиду SiC (рис. 5, спектр 5). На рентгеновских дифрактограммах рефлексы карбида SiC не обнаружены (рис. 3), что указывает на незначительное его количество или точечное распределение. Локально присутствует непрореагировавший углерод (рис. 4ж, 4з; рис. 5, спектр 4).
Рис. 5.
Энергодисперсионные спектры, полученные с отдельных локальных участков (в соответствии с текстом).
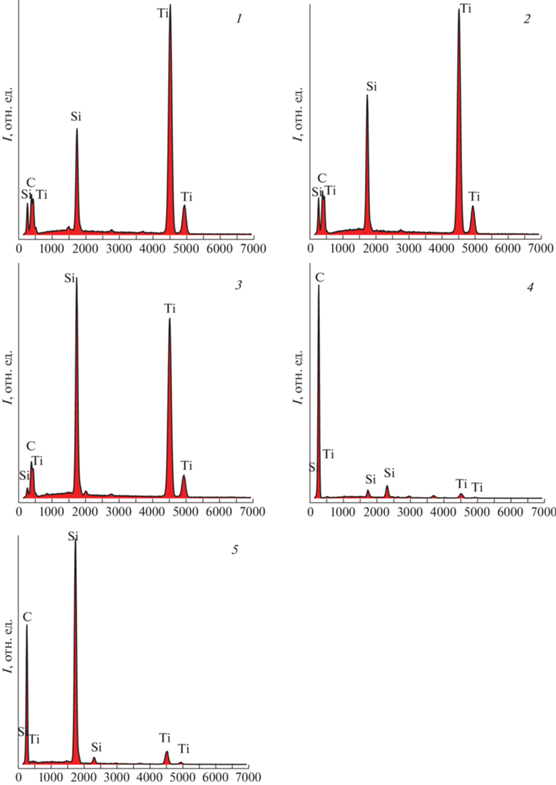
Наличие различных по форме зерен со слоистой структурой, вероятно, объясняется многоступенчатым характером процесса их образования и последующего роста. Установление механизмов их формирования, а также проведение сравнительных исследований с использованием в качестве углерода традиционно используемых сажи и графита, выполненных в одинаковых экспериментальных условиях, являются предметом дальнейших исследований.
ЗАКЛЮЧЕНИЕ
Методом СВС получены композиционные материалы 3Ti–Si–2C с использованием фуллерита С60/70. Показано, что в результате СВС-реакции формируются карбид TiC, МАХ-фаза Ti3SiC2 и переходная фаза – карбосилицид Ti5Si3Cx. Кроме того, обнаружены следы силицида титана TiSi2. Показано, что структура неоднородна и содержит области, состоящие одновременно из нескольких фаз.
Авторы выражают благодарность ведущему инженеру В.А. Кареву за получение образцов.
При выполнении исследований использовано оборудование Центра коллективного пользования “Центр физических и физико-химических методов анализа, исследования свойств и характеристик поверхности, наноструктур, материалов и изделий” УдмФИЦ УрО РАН.
Список литературы
Мержанов А.Г. Самораспространяющийся высокотемпературный синтез: теория и практика. Черноголовка: Территория, 2001. 432 с.
Концепция развития СВС как области научно-технического прогресса / Под ред. Мержанова А.Г. Черноголовка: Территория, 2003. 368 с.
Мержанов А.Г., Мукасьян А.С. Твердопламенное горение. М.: Торус Пресс, 2007. 336 с.
Сычев А.Е., Мержанов А.Г. // Успехи химии. 2004. Т. 73. № 2. С. 157.
Рогачев А.С., Мукасьян А.С. Горение для синтеза материалов: введение в структурную макрокинетику. М.: Физматлит, 2012. 400 с.
XV International Symposium on Self-Propagating High-Temperature Synthesis. 16–20 September 2019, Moscow, Chernogolovka: IPCP RAS, 2019. 594 p.
El Saeed M.A., Deorsola F.A., Rashad R.M. // Int. J. Refr. Met. Hard Mater. 2012. V. 35. P. 127.https://doi.org/10.1016/j.ijrmhm.2012.05.001
Afanasyev N.I., Lepakova O.K., Kitler V.D. // J. Phys.: Conf. Ser. 2020. V. 1459. P. 012008. https://doi.org/10.1088/1742-6596/1459/1/012008
Vadchenko S.G., Sytschev A.E., Kovalev D.Yu. et al. // Nanotechnologies in Russia. 2015. V. 10 № 1–2. P. 67.https://doi.org/10.1134/S1995078015010206
Barsoum M.W. // Prog. Solid St. Chem. 2000. V. 28. P. 201.
Андриевский Р.А. // Успехи физ. наук. 2017. Т. 187. № 3. С. 296. Doi: https://doi.org/10.3367/UFNr.2016.09.037972
Yong-Ming L., Wei P., Shuqin L. et al. // Ceram. Int. 2002. V. 28. P. 227.
Gao N.F., Miyamoto Y., Zhang D. // Mater. Lett. 2002. V. 55. P. 61.https://doi.org/10.1016/S0167-577X(01)00620-6
Li J.-F., Matsuki T., Watanabe R. // J. Am. Ceram. Soc. 2002. V. 85. № 4. P. 1004.https://doi.org/10.1111/j.1151-2916.2002.tb00210.x
Gao N.F., Li J.T., Zhang D. et al. // J. Eur. Ceram. Soc. 2002. V. 22. P. 2365.https://doi.org/10.1016/S0955-2219(02)00021-3
Emmerlich J., Music D., Eklund P. et al. // Acta Mater. 2007. V. 55. P. 1479.https://doi.org/10.1016/j.actamat.2006.10.010
Zhang Z.F., Sun Z.M., Hashimoto H. // J. Alloys Compd. 2003. V. 352. P. 283.https://doi.org/10.1016/S0925-8388(02)01171-4
Istomin P.V., Istomina E.I., Nadutkin V. et al. // Refr. Ind. Ceram. 2019. V. 60. № 3. P. 264.https://doi.org/10.1007/s11148-019-00349-3
Yeh C.L., Shen Y.G. // J. Alloys Compd. 2008. V. 461. P. 654.https://doi.org/10.1016/j.jallcom.2007.07.088
Meng F., Liang B., Wang M. // Int. J. Refr. Met. Hard Mater. 2013. V. 41. P. 152.https://doi.org/10.1016/j.ijrmhm.2013.03.005
Kadish K.M., Ruoff R.S. Fullerenes: chemistry, physics, and technology. New York: John Wiley & Sons. Inc., 2000. 968 p.
Larionova N.S., Nikonova R.M., Ladyanov V.I. // Adv. Powder Technol. 2018. V. 29. № 2. P. 399.https://doi.org/org/10.1016/j.apt.2017.11.027
Ларионова Н.С., Никонова Р.М., Ульянов А.Л. и др. // Физика металлов и металловедение. 2021. Т. 122. № 7. С. 745. https://doi.org/10.31857/S0015323021050089
Robles Hernandez F.C. // J. Metallurgy. 2004. V. 10. № 2. P. 107.
Popov M., Medvedev V., Blank V. et al. //J. Appl. Phys. 2010. V. 108. P. 094317. https://doi.org/10.1063/1.3505757
Medvedev V.V., Popov M.Y., Mavrin B.N. et al. // Appl. Phys. A. 2011. V. 105. P. 45. https://doi.org/10.1007/s00339-011-6544-4
Дополнительные материалы отсутствуют.
Инструменты
Российские нанотехнологии