Нефтехимия, 2019, T. 59, № 3, стр. 246-255
Перспективы конверсии углеводородных газов в жидкие продукты на основе азотсодержащего синтез-газа (обзор)
В. С. Арутюнов 1, 2, 3, *, Л. Н. Стрекова 1, В. И. Савченко 2, И. В. Седов 2, А. В. Никитин 1, 2, О. Л. Елисеев 3, 4, М. В. Крючков 3, А. Л. Лапидус 3, 4
1 Институт химической физики им. Н.Н. Семенова РАН
Москва, Россия
2 Институт проблем химической физики РАН
Москва, Россия
3 Российский государственный университет нефти и газа им. И.М. Губкина
Москва, Россия
4 Институт органической химии им. Н.Д. Зелинского РАН
Москва, Россия
* E-mail: arutyunov@chph.ras.ru
Поступила в редакцию 01.08.2018
После доработки 15.10.2018
Принята к публикации 10.12.2018
Аннотация
Проанализированы перспективы создания малотоннажных технологий конверсии природных и попутных газов в жидкие углеродсодержащие продукты на основе использования дешевого азотсодержащего синтез-газа. Рассмотрены методы получения дешевого азотсодержащего синтез-газа и устойчивого высокопроизводительного синтеза жидких продуктов на его основе. Приведены данные по превращению содержащего азот синтез-газа в метанол, диметиловый эфир, высшие углеводороды (УВ). Отмечены основные преимущества использования азотсодержащего синтез-газа: возможность эксплуатации установок непосредственно в промысловых условиях, отсутствие необходимости в дорогостоящих криогенных аппаратах для разделения воздуха, снижение взрывоопасности производства.
Постепенное снижение доступных ресурсов жидких УВ, обеспечивающих подавляющую долю топлива, потребляемого современным транспортом, а также основного сырья для производства углеродсодержащих (нефтехимических) продуктов требует поиска адекватных путей долговременного решения этих проблем. Наблюдаемые колебания цен на нефть на мировых рынках, отражающие не столько даже состояние мировой экономики, сколько различные геополитические и биржевые процессы, не должны никого вводить в заблуждение: в долговременной перспективе нефть будет постоянно дорожать. Причины этого очевидны: ее ресурсы сокращаются, а себестоимость добычи растет по мере перехода на все более трудно извлекаемые виды сырья. Каждый следующий баррель добытой нефти, как и любых других природных ресурсов, объективно обходится мировой экономике дороже предыдущего.
Расчет на заметную роль в мировой энергетике возобновляемых источников, под которыми, в случае жидкого топлива подразумеваются различные виды биоресурсов, абсолютно несостоятелен, прежде всего, из-за реально доступного объема их производства [1]. Поэтому в среднесрочной перспективе, по крайней мере, до конца текущего столетия, практически единственным источником необходимого мировой экономике и энергетике объема УВ могут быть только различные виды природных газов и угля. Хотя оценки ресурсов природных газов сильно различаются [2, 3], они огромны и значительно превосходят ресурсы жидких УВ. Но наличие ресурсов газообразных УВ само по себе не решает проблемы обеспечения экономики углеводородным сырьем и топливом. Нужны эффективные технологии их конверсии в жидкие УВ, необходимые энергетике, транспорту и традиционной нефтехимии. Кроме того, без конверсии в жидкие УВ невозможно решить проблему практического использования и транспортировки на мировые рынки углеводородных ресурсов огромного числа малодебитных и нетрадиционных источников газа, доля которых будет постоянно возрастать.
Идеальным решением этих проблем могла бы стать конверсия любых газообразных УВ в жидкие продукты непосредственно в местах их добычи. Оценки показывают, что даже для традиционного газа при транспортировке на большие расстояния при уже существующем уровне газохимических технологий, его предварительная химическая конверсия в жидкие продукты может оказаться значительно выгоднее трубопроводной транспортировки или транспортировки в виде сжиженного газа (СПГ) [4]. Для малодебитных и нетрадиционных источников это практически единственное экономически приемлемое решение.
Современная газохимия – зрелая технологическая область, производящая более 200 млн т в год таких базовых продуктов, как аммиак, метанол, водород, жидкие УВ [5, 6]. Однако рентабельность газохимических предприятий, в том числе осуществляющих конверсию природного газа в жидкие моторные топлива, достигается в основном за счет гигантского объема производства, в первую очередь на так называемых предприятиях “мирового класса”, производящих более миллиона тонн продукции в год. В этих газохимических процессах первой и наиболее дорогостоящей стадией является конверсия природного газа в синтез-газ, на которую приходится до 60–70% всех затрат на получение конечных продуктов [7, 8]. Но ориентация на создание гигантских газохимических предприятий противоречит реальной тенденции к сокращению среднего объема ресурсов разрабатываемых и вновь открываемых месторождений и неизбежному в уже недалеком будущем преобладанию низкодебитных и рассредоточенных источников традиционного, а затем и нетрадиционного газового сырья.
Одним из решений проблемы создания технологии для использования низкодебитных источников газового сырья, таких как малоресурсные и низконапорные месторождения, попутный нефтяной газ, сланцевый газ и другие может стать использование более дешевого синтез-газа, получаемого парциальным окислением природного газа атмосферным воздухом.
В данной работе рассмотрены перспективные технологии получения дешевого азотсодержащего синтез-газа и возможность его использования для производства таких продуктов, как синтетические жидкие УВ (СЖУ) [9], метанол [10] и диметиловый эфир (ДМЭ) [11].
ПРИЧИНЫ ИНТЕРЕСА К ИСПОЛЬЗОВАНИЮ АЗОТСОДЕРЖАЩЕГО СИНТЕЗ-ГАЗА
Современные промышленные технологии конверсии углеводородных газов в синтез-газ основаны на процессах их паровой конверсии, парциального окисления или различных комбинациях этих процессов, включая автотермический риформинг [12, 13]. Эти технологии требуют больших затрат энергии на получение пара, либо сооружения криогенных воздухоразделительных установок, капитальные затраты на которые составляют около 40% от всех капитальных затрат на получение синтез-газа [14], либо и того и другого. Например, компания Shell в своем производстве СЖУ в Катаре получает синтез-газ сочетанием некаталитического парциального окисления природного газа и его паровой конверсии.
Необходимость использовать и при кислородной конверсии, и при автотермическом риформинге именно кислород связана в первую очередь с тем, что в противном случае синтез-газ будет содержать большое количество азота, примерно 45–50 об. %. До последнего времени использование разбавленного азотом синтез-газа считалось неприемлемым для производства метанола и СЖУ, поскольку по термодинамическим (метанол) и кинетическим (СЖУ) ограничениям конверсия монооксида углерода за проход далека от полной. Это означает необходимость возврата в реактор непревращенного газа, причем кратность рециркуляции может быть весьма высокой. При наличии в сырье значительного количества инертных примесей (азота) их содержание в рециркулируемом газе вырастет многократно, причем тем больше, чем выше заданная общая степень превращения СО. Соответственно растут затраты на компремирование рециркулируемого газа. Исключением для использования азотсодержащего синтез-газа является производство аммиака по наиболее распространенной двухступенчатой схеме: паровая конверсия природного газа на первой ступени и паровоздушная конверсия на второй. Азот, попадающий в продукт на этой стадии, является сырьем для получения азот-водородной смеси для синтеза аммиака.
Сложность, капиталоемкость и энергоемкость технологий получения не содержащего азот синтез-газа приводит к тому, что в настоящее время газохимические процессы производительностью ниже нескольких сотен тысяч тонн в год готовой продукции (СЖУ, метанол, ДМЭ) считаются нерентабельными. А высокие затраты на получение синтез-газа современными технологиями делают его настолько дорогим продуктом, что его потери экономически недопустимы, и необходимо обеспечить его максимальное срабатывание в целевом процессе.
Таким образом, в современных технологиях высокие капитальные и эксплуатационные затраты на производство не содержащего азот синтез-газа необходимы для того, чтобы снизить более высокие издержки на стадиях, потребляющих это сырье. И наоборот, попытка удешевить производство синтез-газа путем использования в качестве окислителя воздуха приводит к неприемлемому росту эксплуатационных расходов в производствах метанола и СЖТ.
Попытки создания более простых и дешевых технологий получения не содержащего азот синтез-газа ведутся многими исследовательскими группами и компаниями. Одно из популярных направлений, позволяющее обойтись без криогенных технологий, – использование высокотемпературных керамических мембран, проницаемых для кислорода. Однако несмотря на длительные усилия ряда известных американских компаний по их разработке [8, 15], из-за серьезных технологических проблем подобные установки промышленного уровня так и не появились. По этой же причине не завершились практической реализацией и попытки обойтись без воздухоразделительных установок за счет использования в качестве переносчика кислорода расплавов оксидов металлов, например свинца [16].
Для небольших по объему производств метанола, ДМЭ и синтетических УВ, по нашему мнению, более перспективным может стать использование дешевого азотсодержащего синтез-газа, получаемого некаталитическим парциальным окислением УВ атмосферным воздухом. При этом превращение такого синтез-газа в конечные продукты должно осуществляться на основе наиболее эффективных технологий с максимальной конверсией за проход. При необходимости может быть установлена серия последовательных реакторов (каскад реакторов), что обеспечит высокую степень превращения сырья без его рециркуляции. При этом даже неполная конверсия дешевого синтез-газа с использованием его небольшой оставшейся части для нужд собственной энергетики может быть экономически оправдана за счет резкого снижения затрат на процесс его получения.
Если речь идет о переработке углеводородных газов непосредственно в промысловых условиях (а актуальность этого становится все более очевидной), возникает еще один важный аспект в пользу технологий на основе синтез-газа, полученного с использованием в качестве окислителя атмосферного воздуха. В промысловых условиях большое значение приобретает не только экономическая эффективность, но и технологическая безопасность эксплуатации оборудования. По мнению большинства специалистов в области газодобычи, по условиям безопасности производства применение кислородных технологий в промысловых условиях с обилием горючих газов и жидкостей и недостатком высококвалифицированного персонала, подготовленного для работы с кислородным оборудованием, должно быть ограничено, если не исключено полностью. Это обстоятельство является серьезным аргументом в пользу технологий получения синтез-газа на основе парциального окисления воздухом и, соответственно, синтеза жидких продуктов на основе азотсодержащего синтез-газа.
ПЕРСПЕКТИВНЫЕ ТЕХНОЛОГИИ ПОЛУЧЕНИЯ АЗОТСОДЕРЖАЩЕГО СИНТЕЗ-ГАЗА
Ряд потенциальных технологий получения азотсодержащего синтез-газа рассматривается в [17]. Среди них – созданный при участии специалистов ИНХС РАН модифицированный дизельный или компрессионный двигатель, являющийся одновременно химическим реактором [17–19]. Процесс производит синтез-газ с содержанием азота 50–60%, и доведен до уровня установки производительностью 10 000 м3/ч. Другой разработкой с участием специалистов ИНХС РАН, не имеющей зарубежных аналогов, является генератор синтез-газа на основе ракетных технологий, который был реализован на уровне опытно-промышленной установки в Приморском НТЦ РКК “Энергия” [20]. В качестве еще одной возможной технологии получения синтез-газа на основе парциального окисления атмосферным воздухом можно отметить фильтрационное горение. Процесс может быть реализован, например, в варианте с периодическим переключением направления потока одного из реагентов и раздельной подачей второго реагента в центральную часть реактора [21].
Однако на данный момент наиболее перспективной технологией получения дешевого азотсодержащего синтез-газа, по нашему мнению, является конверсия природного газа атмосферным воздухом на основе проницаемых объемных матриц [22–25]. В [25] представлены результаты экспериментальных исследований матричной конверсии природного газа в синтез-газ, при которой автотермический процесс окисления протекает в режиме поверхностного горения внутри полости замкнутой объемной матрицы, выполненной из проницаемого для газа материала. Удельная объемная производительность таких конверторов в десятки раз превышает удельную объемную производительность традиционных типов конверторов при возможности превращать в синтез-газ углеводородные газы практически любого состава.
На демонстрационной установке с объемной матрицей, образованной двумя плоскопараллельными пластинами из пенометалла или прессованной металлической проволоки, при атмосферном давлении, расходах природного газа до 10 м3/ч и окислении воздухом с содержанием O2 21–26%, при значениях коэффициента избытка окислителя α = 0.34–0.36 был достигнут практически предельно возможный выход синтез-газа (рис. 1).
Рис. 1.
Зависимость концентрации продуктов конверсии реагентов от коэффициента избытка окислителя α при окислении атмосферным воздухом при постоянном расходе газовоздушной смеси 19.3 м3/ч (расход СН4 = 4.0–4.8 м3/ч) [22].
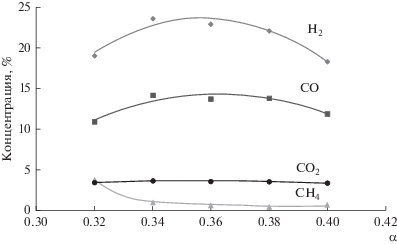
Максимальная концентрация компонентов синтез-газа достигается при α ≈ 0.34 (рис. 1). При начальной концентрации кислорода в атмосферном воздухе [О2] = 21% суммарное содержание компонентов синтез-газа достигало почти 40% с концентрацией [Н2] ~ 24% и концентрацией [СО] ~ 14% (табл. 1). Соотношение Н2/СО монотонно растет с уменьшением коэффициента избытка окислителя и при α = 0.34 достигает значения 1.67. Конверсия кислорода в исследуемом диапазоне почти не зависит от коэффициента избытка окислителя и находится на уровне 95%. Конверсия метана также не сильно зависит от коэффициента избытка окислителя и тоже находится на уровне 95%, что обуславливает низкую остаточную концентрацию метана в продуктах, на уровне всего 0.5–1%. Концентрация СО2 практически не зависит от изменения коэффициента избытка окислителя в исследуемом диапазоне и находится на уровне 3.6%, что, видимо, обеспечивает достаточный уровень тепловыделения для поддержания процесса конверсии. В области устойчивой работы конвертора изменение общего потока газовоздушной смеси через матрицу в 4 раза почти не влияло на параметры получаемого синтез-газа. Только при очень больших расходах газовой смеси, когда скорость потока через матрицу заметно превышала ламинарную скорость горения стехиометрической метановоздушной смеси, происходил срыв пламени. Параметры синтез-газа, получаемого в оптимальных условиях при окислении метана в матричном конверторе атмосферным воздухом, представлены в табл. 1.
Таблица 1.
Параметры синтез-газа, получаемого в оптимальных условиях при окислении метана в матричном конверторе воздухом и обогащенным воздухом [22]
Параметр | Значение | |
---|---|---|
эксперимент 1 | эксперимент 2 | |
Коэффициент избытка окислителя | 0.34 | 0.36 |
Конверсия метана, % | 94.3 | 96.6 |
Конверсия кислорода, % | 95.0 | 95.3 |
Концентрация Н2, % | 23.7 | 23.0 |
Концентрация СО, % | 14.2 | 14.4 |
Концентрация СО2, % | 3.7 | 3.6 |
Концентрация СН4, % | <1 | 0.6 |
Соотношение Н2/СО | 1.67 | 1.60 |
Селективность образования Н2, % | 71.3 | 67.2 |
Селективность образования СО, % | 85.4 | 84.1 |
Температура рабочей поверхности матрицы, °С | 955 | 996 |
Температура входной поверхности матрицы, °С | 642 | 664 |
Сравнение экспериментально показателей, представленных в табл. 1, с равновесным составом продуктов конверсии смесей метана с воздухом показывает, что достигнут практически предельный выход синтез-газа, который может быть получен при окислении природного газа атмосферным воздухом. Мольная доля азота в смеси, получаемой при парциальном окислении метана атмосферным воздухом, зависит от коэффициента избытка окислителя α, и может быть приближенно определена по формулам (1) или (2):
(1)
$\begin{gathered} {в с м е с и н а в ы х о д е и з к о н в е р т о р а :\;}\quad \\ {{С }_{{{{{\text{N}}}_{2}}}}} = {\text{ }}{{7.54\alpha } \mathord{\left/ {\vphantom {{7.54\alpha } {\left( {3 + 7.54\alpha } \right)}}} \right. \kern-0em} {\left( {3 + 7.54\alpha } \right)}}, \\ \end{gathered} $(2)
$\begin{gathered} {в р а с ч е т е н а с у х о й с и н т е з - г а з :\;} \hfill \\ {{С }_{{{{{\text{N}}}_{2}}}}} = {\text{ }}7.54\alpha {\text{/}}\left( {3.8 + 4.34\alpha } \right), \hfill \\ \end{gathered} $где 7.54α – количество молей азота на моль исходного метана при данном значении α, коэффициент 3 – количество молей получаемого синтез-газа на моль исходного метана, количество получаемой Н2О составляет ~0.8(4α – 1) моль на моль метана.
Таким образом, матричный конвертор атмосферного давления, описанный в [25], может рассматриваться как реальный прототип конверторов для работы в составе процессов получения метанола и продуктов синтеза Фишера–Тропша на основе каскадных схем синтеза. В случае необходимости получения синтез-газа с более низкой концентрацией азота, можно использовать в качестве окислителя обогащенный воздух. С экономической точки зрения целесообразнo использовать обогащенный воздух с концентрацией кислорода до ~45%, который может быть получен на относительно простых установках мембранного разделения воздуха.
Поскольку матричная конверсия протекает в газовой фазе во фронте пламени, имеющем протяженность всего несколько миллиметров, она позволяет достигать значительно более высокой удельной объемной производительности по сравнению с каталитическими конверторами, в которых слой катализатора, необходимый для завершения конверсии, может достигать нескольких метров. Помимо очевидных преимуществ, связанных с отсутствием катализатора и более низкими операционными затратами, это обеспечивает компактность матричных конверторов и значительно более низкие удельные капиталовложения. В связи с этим можно ожидать, что использование азотсодержащего синтез-газа, полученного парциальным окислением атмосферным воздухом в некаталитических матричных конверторах, создаст хорошие предпосылки для рентабельной малотоннажной конверсии природных и попутных газов в жидкие продукты непосредственно в промысловых условиях.
СИНТЕЗ УГЛЕВОДОРОДОВ ИЗ АЗОТСОДЕРЖАЩЕГО СИНТЕЗ-ГАЗА
Возможность использования азотсодержащего синтез-газа для получения СЖУ на протяжении ряда лет изучалaсь в Университете Карлсруэ [26–28]. Общая схема производства выглядит следующим образом (рис. 2). Природный газ проходит сероочистку и поступает на парциальное окисление воздухом в реактор с Ni-содержащим катализатором при температуре 1200°С и давлении 2.5 МПа. Реактор работает в автотермическом режиме, производя синтез-газ примерно следующего состава: 47% N2, 28% H2, 15% CO, 2% CH4, 3% CO2, 5% H2O [28]. При этом в отличие от используемой компанией Shell технологии некаталитического окисления, не образуется сажа. Далее синтез-газ без дополнительной компрессии поступает в трубчатый реактор, заполненный осажденным Fe-катализатором Hoechst-Ruhrchemie, аналогичным использованному в низкотемпературном синтеза УВ компании Sasol (ARGE-процесс). Полученные УВ поступают на разделение, остаточный газ используется в качестве топлива [28].
Рис. 2.
Блок-схема процесса конверсии природного газа в СЖУ на основе азотсодержащего синтез-газа [27].
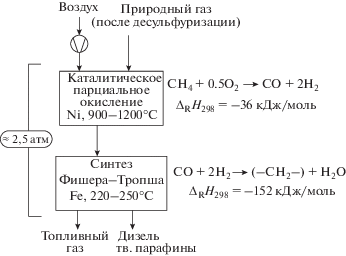
В пилотной установке для проведения синтеза УВ использовали серию из трех последовательно расположенных реакторов, каждый из которых представлял собой заполненную катализатором трубку по диаметру соответствующую используемым в промышленных мультитрубных реакторах. Реакторы охлаждались маслом. Жидкие продукты синтеза конденсировали и отделяли от газа после каждого реактора. Поддерживались следующие рабочие параметры: давление около 2.4 МПа, температура от 220 до 240°С. Период непрерывной работы установки составлял до нескольких недель.
Математическое моделирование реактора на основе полученных кинетических данных позволило рассчитать радиальный и аксиальный температурный профили реактора, а также сопоставить устойчивость работы на чистом и разбавленном синтез-газе. Увеличение температуры охлаждения ведет к росту максимальной температуры в реакторе, однако эта зависимость более плавная для разбавленного азотом синтез-газа (рис. 3). Авторы пришли к выводу, что при диаметре трубки реактора 70 мм устойчивая работа при оптимальной температуре 250°С для неразбавленного синтез-газа невозможна. При одинаковых температурах охлаждения, объемных скоростях и парциальных давлениях реагентов (СО и Н2) работа реактора на забалластированном азотом синтез-газе оказывается более устойчивой, чем на неразбавленном. Это объясняется следующими причинами [27, 28]:
Рис. 3.
Параметрическая чувствительность реактора синтеза Фишера–Тропша для неразбавленного и разбавленного азотом синтез-газа [28].
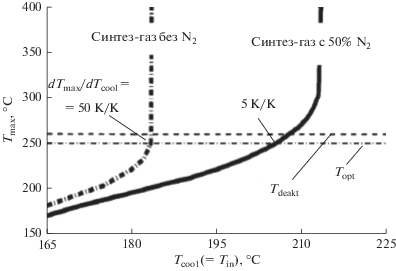
• азот поглощает часть тепла реакции;
• теплопроводность азотсодержащей смеси выше;
• коэффициент теплопередачи к стенке реактора у азотсодержащей смеси также выше.
Таким образом, если для устойчивой работы кожухотрубного реактора и предотвращения перегревов при работе на неразбавленном синтез-газе диаметр трубок ограничен 45 мм, то для синтез-газа, содержащего 50% азота, он может быть увеличен до 70 мм. Это означает уменьшение металлоемкости реактора и снижение капитальных затрат на его изготовление [27, 28].
В работе [28] представлена концепция низкозатратного производства СЖУ на базе процессов воздушно-каталитического окисления природного газа и последующего синтеза углеводородов мощностью по сырью 42 т/ч (340 тыс. т/год). Синтез-газ вырабатывается в реакторе парциального окисления, работающем под давлением 2.6 МПа, и поступает в кожухотрубные реакторы синтеза Фишера–Тропша, собранные в две параллельные нитки по два реактора в каждой. Диаметр реактора 7 м, высота 8 м, диаметр труб 70 мм. В каждом реакторе 4000 труб, что примерно вдвое меньше, чем в случае использования труб диаметром 40 мм, которые используются при работе с неразбавленным синтез-газом. Конверсия СО составляет 63%, производительность по жидким и твердым УВ 19 т/ч (150 тыс. т/год). Остаточный газ имеет низшую теплоту сгорания 4 МДж/м3 и может использоваться как топливо.
В работе [29] получение СЖУ из разбавленного синтез-газа на катализаторе Fe−Pd/ZSM-5 было исследовано в широком интервале температур (250–400°С), давлений (3.4–8.6 МПа) и объемных скоростей (500–3000 ч–1). Состав синтез-газа также варьировали, меняя в нем содержание азота, СО2 и метана. Образовывались в, основном, газообразные УВ состава С1–С4 и бензиновая фракция, содержащие до 23% олефинов и до 48% ароматических УВ. Рост температуры и давления способствовал повышению конверсии и образованию УВ. При этом селективность их образования достигала 70%, остальное количество СО превращалось в СО2.
Необходимо указать на существенный недостаток железных катализаторов, отмеченный в цитированных выше работах: в условиях синтеза Фишера–Тропша 25–30% СО расходуется на образование СО2 по реакции водяного газа. Кроме того, образующиеся в синтезе пары воды ингибируют превращение СО в УВ, из-за чего скорость реакции в нижних слоях железного катализатора падает [30]. Эти недостатки отсутствуют у кобальтовых катализаторов. Селективность образования СО2 на них в норме не превышает единиц процентов, а вода не оказывает влияние на кинетику. Более того, по некоторым данным, пары воды способствуют повышению селективности кобальтовых катализаторов по целевым высшим УВ [31].
Возможность получения СЖУ из азотсодержащего синтез-газа на кобальтовых катализаторах исследовали в работах [32, 33]. Для каталитических испытаний использовали модельную смесь состава CO : H2 : N2 = 1 : 2 : 5. Испытывали три образца катализаторов: 20% Со/Al2O3 (образец № 1), 20% Со–3% Zr/Al2O3 (образец № 2), 20% Со–3% Zr–3% Ce/Al2O3 (образец № 3). Катализаторы готовили пропиткой носителя γ-Al2O3 (Sуд 200 м2/г, фракция 0.18–0.4 мм) водными растворами Co(NO3)2, ZrO(NO3)2 и Ce(NO3)3 с последующим высушиванием и прокаливанием в токе воздуха при 450°С в течение 1 ч. Опыты проводили на лабораторной установке высокого давления проточного типа с интегральным трубчатым реактором диаметром 20 мм с фиксированным слоем катализатора. Результаты каталитических испытаний приведены в табл. 2.
Таблица 2.
Основные показатели синтеза углеводородов из сырья состава CO : H2 : N2 = 1 : 2 : 5 (Т = 200°С, об. скорость 1000 ч–1 [32])
Образец | Давление, МПа | Конверсия СО, % | Селективность, мольн.% | Выход С5+, г/м3 | ||
---|---|---|---|---|---|---|
C5+ | CH4 | CO2 | ||||
№ 1 | 0.5 | 35 | 88 | 8 | 5 | 23 |
1.0 | 12 | 97 | 3 | 1 | 9 | |
2.0 | 21 | 94 | 4 | 2 | 15 | |
№ 2 | 0.5 | 19 | 91 | 4 | 6 | 13 |
1.0 | 53 | 96 | 3 | 1 | 38 | |
2.0 | 87 | 90 | 7 | 1 | 59 | |
№ 3 | 0.5 | 53 | 90 | 8 | 2 | 36 |
1.0 | 57 | 91 | 5 | 4 | 39 | |
2.0 | 58 | 95 | 3 | 2 | 41 |
Все образцы показали высокую селективность по целевым УВ С5+, 88–97%, и низкую селективность по метану. Столь высокие показатели обусловлены, очевидно, исключением местных перегревов в слое катализатора благодаря разбавлению сырья инертным газом. Поэтому вклад “горячих точек” в общий выход метана оказывается минимальным.
Молекулярно-массовый состав продуктов с хорошей точностью соответствовал теоретическому распределению Андерсона–Шульца–Флори (АШФ). Показатель распределения α для всех образцов превышал 0.82, а его максимальное значение на образце 3 составило 0.89. Высокие значения показателя α коррелируют с высокой селективности по УВ С5+. Жидкие УВ состояли преимущественно из линейных алканов, что характерно для кобальтовых катализаторов. Массовая доля изоалканов и олефинов составляла 14–22%. Обращает на себя внимание высокая конверсия СО, достигавшая 87% для катализатора № 2 при давлении 2 МПа, что подтверждает реальность высокой степени использования синтез-газа даже при отказе от его рециркуляции (табл. 2).
Таким образом, показана перспективность получения СЖУ из разбавленного азотом синтез-газа на нанесенных кобальтовых катализаторах [32, 33]. Высокие значения конверсии СО в сочетании с высокой селективностью по СЖУ позволяют реализовать технологическую схему без рециркуляции газа.
Превращение азотсодержащего синтез-газа в СЖУ на катализаторе Co–Pt–ZrO2/Al2O3 исследовано в работе [34]. Синтез-газ получали парциальным окислением воздухом в сочетании с углекислотной конверсией метана. Показано благоприятное влияние повышенного давления на показатели синтеза. Так, при увеличении давления с 0.5 до 2.5 МПа конверсия СО возросла с 26.8 до 36.3%. Однако дальнейшее повышение давления уже слабо влияло на конверсию СО. В работе сделан вывод о пригодности синтез-газа с большим содержанием азота в качестве сырья для синтеза УВ и возможности достижения при этом высокой активности катализатора.
ИСПОЛЬЗОВАНИЕ АЗОТСОДЕРЖАЩЕГО СИНТЕЗ-ГАЗА ДЛЯ ПРОИЗВОДСТВА МЕТАНОЛА И ДИМЕТИЛОВОГО ЭФИРА
Одним из наиболее привлекательных жидких продуктов превращения природного газа в промысловых условиях, безусловно, является метанол. Помимо простой, малозатратной и хорошо отработанной технологии синтеза, получение метанола в районах промысла природного и попутных газов привлекательно также тем, что он широко используется на месторождениях в качестве ингибитора гидратообразования. Расходы метанола на эти цели достигают в России 500 тыс. т/год, а стоимость в районах удаленных промыслов, с учетом затрат на доставку, может в два-три раза превышать рыночную цену.
Синтез метанола из азотсодержащего синтез-газа с содержанием азота до 60% подробно рассмотрен в [17]. Эксперименты показали возможность эффективного синтеза метанола из синтез-газа с содержанием азота 40–60% на промышленных катализаторах производства компании Zud Chemie при объемной скорости подачи газа до 5000 ч–1. Однако оптимальные условия синтеза метанола требуют соотношение Н2/СО ≈ 2.5, превышающее стехиометрическое соотношение, и давление не ниже 5 МПа. При повышении содержания азота в сырье и отклонении отношения Н2/СО от оптимального значения конверсия СО заметно снижается (рис. 4, 5).
Рис. 4.
Зависимость конверсии СО и СО2 от содержания азота в синтез-газе при объемной скорости 3000 ч–1 и соотношении H2/CO =10.4 [17].

Рис. 5.
Зависимость выхода метанола и концентрации воды в продуктах синтеза от соотношения H2/CO при объемной скорости 3000 ч–1 и содержании азота в синтез-газе 40% [17].
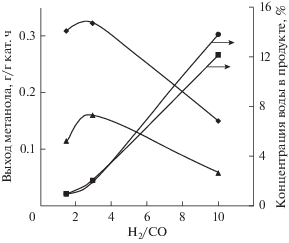
В обзоре [10] обобщены литературные и патентные данные по синтезу метанола в slurry-реакторах с использованием тонкодисперсных гетерогенных катализаторов, суспендированных в жидкостях. Показана возможность применения разбавленного азотом (50–56%) синтез-газа в условиях длительного пробега Cu–Zn–Al-катализатора. Активность оставалась неизменной в течение 600 ч работы. Однако конверсия СО при температуре 260°С, давлении 5 МПа и времени контакта 3 с не превышала 65% [10].
Более перспективным может оказаться получение ДМЭ, поскольку термодинамика этого процесса более благоприятна:
ДМЭ рассматривается в качестве перспективного дизельного топлива, он является промежуточным продуктом производства УВ бензиновой фракции (процесс компании Mobil) и пропилена (процесс MTP компании Lurgi). Наконец, ДМЭ легко может быть превращен в метанол.
Важным преимуществом получения ДМЭ является то, что оптимальное соотношение Н2/СО для его синтеза близко к 1, в отличие от синтеза метанола, где оно (точнее, значение функционала) равно 2. Это обстоятельство особенно существенно при использовании в качестве источника синтез-газа автотермических процессов парциального окисления природного газа, при которых это соотношение обычно находится на уровне 1.6–1.7. То есть такой синтез-газ более удобен для превращения в ДМЭ, чем в метанол. Отметим также, что экономические оценки дают себестоимость получения ДМЭ на 5–20% ниже себестоимости получения метанола [7].
Получение ДМЭ может быть осуществлено без рециркуляции синтез-газа при ориентации на максимальное превращение за проход через реактор или каскад реакторов и последующее дожигание остаточного газа. Такой вариант обеспечивает минимальные инвестиции при почти полном последующем превращении ДМЭ в бензин с селективностью образования 80–90%. Даже при большом содержании азота в исходном синтез-газе 67–68% и высокой объемной скорости 6000 ч–1 степень превращения монооксида углерода превышает 50% [7].
В работе [35] для синтеза ДМЭ использовали осажденный Cu–Zn–Al-катализатор синтеза метанола, смешанный с цеолитом HZSM-5. Последний сообщает каталитической системе необходимую дегидратирующую функцию. Синтез-газ получали на промотированном La и Mg катализаторе Ni/α-Al2O3 парциальным окислением жирного газа (86% метана, остальное алканы С2–С4) воздухом. Однако парциальное окисление вели при относительно низких температурах, 800–850°С. В этих условиях полная конверсия метана не достигалась: при атмосферном давлении она была равна 96.2% и снижалась до 73.4% при давлении 1.1 МПа. Кроме того, катализатор сильно закоксовывался. Снизить коксоообразование и повысить конверсию оказалось возможным введением в поток сырья водяного пара.
Продуктовый газ, использованный в синтезе ДМЭ, после удаления водяных паров имел следующий состав: 41% H2, 19.8% CO, 0.59% CH4, 7.06% CO2 и 31.5% N2. С повышением давления конверсия СО постепенно возрастала при практически неизменной селективности по ДМЭ около 75%. Таким образом, повышение давления благоприятствует выходу ДМЭ (рис. 6).
Рис. 6.
Влияние давления на показатели синтеза ДМЭ при Т = 234°С и объемной скорости подачи газа 1000 ч–1 [35].
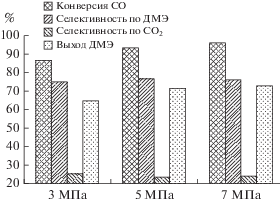
Зависимость показателей реакции от температуры более сложная. Максимальная конверсия СО в 96% достигается при температурах 230–235°С (давление 7 МПа) и с дальнейшим ростом температуры снижается вплоть до 80% при 290°С. При этом селективность по ДМЭ почти не зависит от температуры и составляет 76–78% в температурном диапазоне 210–290°С. В результате, максимальный выход ДМЭ в 75% достигается при температуре 235°С [35].
Авторы [35] утверждают, что катализатор синтеза ДМЭ сохраняет стабильные показатели в течение как минимум 450 ч работы. Отходящий газ после выделения ДМЭ содержит 56% N2, 19.4% H2 и 20% CO2. Авторы предлагают использовать его для выработки энергии в турбине, далее выделять СО2, а остаток использовать как топливо. Отметим, что описанная в работе схема предполагает проведение стадии получения синтез-газа при невысоком давлении и затем дожим газа компрессором перед подачей в реактор синтеза ДМЭ. Возможно, с экономической точки зрения это не самое удачное решение.
Аналогичный по составу катализатор Cu–Zn–Al/HZSM-5 использовали для демонстрации возможности получения ДМЭ из азотсодержащего синтез-газа в [36]. Соотношение H2/CO в синтез-газе было равно 1.5, содержание азота составляло 26%. Конверсия СО за проход составила 75% при селективности образования ДМЭ 66.7% при следующих условиях: Т = 260°С, Р = 4 МПа. Катализатор сохранял эти показатели в течение 150 ч работы [36].
ЗАКЛЮЧЕНИЕ
Анализ литературных данных показывает, что парциальное окисление природного газа воздухом с последующим превращением получаемого азотсодержащего синтез-газа в СЖУ, метанол или ДМЭ может стать удачным решением использования ресурсов удаленных малодебитных газовых месторождений. Поскольку подключение таких месторождений к газопроводной системе требует слишком высоких затрат, экономически более оправдано превращение добытого газа прямо на месте в жидкие продукты, более удобные для транспортировки. К тому же один из таких продуктов – метанол – широко востребован в России как раз в местах добычи природного газа как ингибитор гидратообразования. Однако используемые технологии должны быть максимально просты, дешевы и не требовать для обслуживания многочисленного высококвалифицированного персонала.
Одной из перспективных опций является получение азотсодержащего синтез-газа на основе матричных конверторов, использующих в качестве окислителя атмосферный воздух. Объемная производительность таких конверторов в десятки раз превышает таковую в традиционных типах конверторов при возможности превращать в синтез-газ углеводородные газы практически любого состава. Другим вариантом может быть парциальное каталитическое окисление природного газа воздухом. Использование воздуха в качестве окислителя позволяет отказаться от дорогостоящих и небезопасных в эксплуатации криогенных установок разделения воздуха.
Использование азотсодержащего синтез-газа на этапе его превращения в жидкие продукты требует его высокой конверсии за проход с тем, чтобы исключить рецикл остаточного газа. Наибольшая степень превращения, около 90%, в настоящее время достигается в синтезе ДМЭ на комбинированных Cu–Zn–Al-цеолитных катализаторах. Превращение в метанол или УВ (синтез Фишера–Тропша) по разным причинам протекает с меньшей конверсией и требует каскада из двух или трех реакторов. Однако благодаря разбавлению синтез-газа азотом удельное тепловыделение в каталитическом слое снижается, что, как было установлено, позволяет использовать кожухотрубные реакторы синтеза Фишера–Тропша с увеличенным диаметром трубок. Таким образом, капитальные затраты на изготовление двух реакторов, оптимизированных для разбавленного азотом синтез-газа, могут оказаться не выше, чем на изготовление одного реактора, работающего на неразбавленном азотом синтез-газе.
Наличие в России большого числа удаленных газовых месторождений делает разработку низкозатратных технологий конверсии природного газа в жидкие продукты — метанол, диметиловый эфир и синтетические жидкие углеводороды, весьма актуальной для отечественной газовой отрасли.
Список литературы
Арутюнов В. // Нефть XXI. Мифы и реальность альтернативной энергетики. М.: Эксмо, 2016. 208 с.
Kvenvolden K.A. // Chem. Geol. 1988. V. 71. P. 41.
Boswell R., Collett T.S. // Energy & Environmental Science. 2011. V. 4. P. 1206.
Левинбук М.И., Котов В.Н. // Мир нефтепродуктов. 2013. № 9. С. 3.
Брагинский О.Б. // Нефтегазовый комплекс мира. М.: Издательство “Нефть и газ” РГУ нефти и газа им. Губкина, 2006. 640 с.
Савченко В.И., Макарян И.А., Арутюнов В.С. // Мир нефтепродуктов. Вестник нефтяных компаний. 2013. № 11. С. 3.
Розовский А.Я. // Российский химический журнал (Журнал Российского химического общества им. Д.И. Менделеева). 2003. Т. 47. № 6. С. 53.
Арутюнов В.С. // Окислительная конверсия природного газа. М.: КРАСАНД, 2011. 640 с.
Хаджиев С.Н., Сагитов С.А., Лядов А.С., Куликова М.В., Крылова А.Ю. // Нефтехимия. 2014. Т. 54. № 2. С. 88.
Хаджиев С.Н., Колесниченко Н.В., Ежова Н.Н. // Нефтехимия. 2016. Т. 56. № 2. С. 95.
Ионин Д.А., Колесниченко Н.В., Букина З.М., Хаджиев С.Н. // Нефтехимия. 2015. Т. 55. № 2. С. 119.
Aasberg-Petersen K., Hansen J.-H. Bak, Christensen T.S., Dybkjaer I., Christensen P. Seier, Nielsen C. Stub, Madsen S.E.L. Winter, Rostrup-Nielsen J.R. // Applied Catalysis A: General. 2001. V. 221. P. 379.
Rostrup-Nielsen J.R. // Catalysis Today. 2002. V. 71. P. 243.
Елисеев О.Л. // Российский химический журнал (Журнал Российского химического общества им. Д.И. Менделеева). 2008. Т. 52. № 6. С. 53.
Chen C.M., Bennett D.L., Carolan M.F., Foster E.P., Schinski W.L., Taylor D.M. // ITM syngas ceramic membrane technology for synthesis gas production. In: Proceedings of the 7th Natural Gas Conversion Symposium, June 6–10, Dalian, China. Studies in Surface Science and Catalysis. V. 147. Natural Gas Conversion VII. Bao X. and Xu Y. (Editors). Amsterdam et al.: Elsevier, 2004. P. 55.
Spangler M.J. // Patent US 5478370A. 1994.
Lishchiner I.I., Malova O.V., Tarasov A.L., Maslennikov V.M., Vyskubenko Yu.A., Tolchinskii L.S., Dolinskii Yu.L. // Catalysis in Industry. 2010. V. 2. № 4. P. 368.
Грунвальд В.Р., Долинский Ю.Л., Пискунов С.Е., Толчинский Л.С., Платэ Н.А., Колбановский Ю.А. // Патент РФ № 2096313. 1997.
Генкин В.Н., Генкин М.В., Заборских Д.В., Колбановский Ю.А. // Патент РФ № 2120913. 1998.
Загашвили Ю.В., Левихин А.А., Кузьмин А.М. // НефтеГазоХимия. 2017. № 4. С. 9.
Dorofeenko S.O., Polianczyk E.V. // Chem. Eng. J. 2016. V. 292. P. 183.
Arutyunov V.S., Shmelev V.M., Sinev M.Yu., Shapovalova O.V. // Chem. Eng. J. 2011. V. 176–177. P. 291.
Arutyunov V.S., Shmelev V.M., Rakhmetov A.N., Shapovalova O.V. // Ind. Eng. Chem. Res. 2014. V. 53. P. 1754.
Shapovalova O.V., Young Nam Chun, Arutyunov V.S., Shmelev V.M. // Int. J. Hydr. Energy. 2012. V. 37. P. 14040.
Арутюнов В.С., Савченко В.И., Седов И.В., Шмелев В.М., Никитин А.В., Фокин И.Г., Эксанов С.А., Шаповалова О.В., Тимофеев К.А. // ЖПХ. 2016. Т. 89. № 11. С. 1450.
Hedden K., Jess A., Kuntze T. // Oil Gas European Magazine. 1994. № 20. P. 42.
Jess A., Popp R., Hedden K. // Appl. Catal. A. 1999. V. 186. P. 321.
Jess A., Hedden K., Popp R. // Chem. Eng. Technol. 2001. V. 24. P. 27.
Yan. Q, Yu F., Cai Z., Zhang J. // Biomass and Bioenergy. 2012. V. 47. P. 469.
Dry M.E. // Catal. Lett. 1990. V. 7. P. 241.
Borg Ø., Eri S., Blekkan E.A., Storsæter S., Wigum H., Rytter E., Holmen A. // J. Catal. 2007. V. 248. P. 89.
Лапидус А.Л., Елисеев О.Л., Крючков М.В. // Технологии нефти и газа. 2011. № 5. С. 9.
Лапидус А.Л., Каторгин Б.И., Елисеев О.Л., Крючков М.В., Крейнин Е.В., Волков А.С. // Химия твердого топлива. 2011. № 3. С. 26.
Xu D., Duan H., Li W., Xu H. // Energy & Fuels. 2006. V. 20. P. 955.
Jia M., Li W., Xu H., Hou S., Ge Q. // Applied Catalysis A: General. 2002. V. 233. P. 7.
Wang T., Chang J., Fu Y., Zhang Qi, Li Y. // Korean J. Chem. Eng. 2007. V. 24. P. 181.
Дополнительные материалы отсутствуют.