Нефтехимия, 2019, T. 59, № 4, стр. 378-387
Способы модифицирования цеолита типа ZSM-5 для изменения активности системы реакций переноса водорода при крекинге низших алифатических спиртов
Е. О. Алтынкович 1, *, К. С. Плехова 1, О. В. Потапенко 1, В. П. Талзи 1, Т. П. Сорокина 1, В. П. Доронин 1
1 Федеральное государственное бюджетное учреждение науки Институт проблем
переработки углеводородов СО РАН
Омск, Россия
* E-mail: aneevgen@mail.ru
Поступила в редакцию 02.11.2018
После доработки 01.03.2019
Принята к публикации 14.03.2019
Аннотация
В работе исследовано влияние щелочной обработки цеолитов ZSM-5 с модулем 30 в пределах мольного отношения NaOH : SiO2 0–230, а также модифицирование цеолита ZSM-5 фосфором в пределах 0–8 мас. % на физико-химические свойства и активность в реакциях переноса водорода при превращении алифатических спиртов. Щелочная обработка цеолита приводит к снижению модуля цеолита и росту коэффициента переноса водорода при превращении алифатических спиртов. Модифицирование цеолита фосфором эквивалентно повышению модуля цеолита, что приводит к уменьшению коэффициента переноса водорода.
В настоящее время нефть и продукты на ее основе являются одними из основных видов топлива и сырья для нефтехимии. Однако все чаще появляются сообщения об ограниченности запасов нефти. В связи с этим непрерывно продолжается поиск альтернативных видов сырья, одними из которых могут выступать алифатические спирты. Последние могут быть получены при переработке растительного сырья или, в частности метанол, получены из синтез-газа [1]. Также в качестве альтернативного сырья для нефтехимии рассматриваются углеводородные фракции, содержащие большое количество олефинов С4–С8 [2].
По видам направлений переработки можно говорить об универсальности спиртов как сырья. Процесс MTO (methanol to olefins) позволяет получать из метанола олефины, тем самым все больше привлекая внимание промышленников из-за обострившегося спроса на низшие олефины [3]. Для получения моторных топлив метанол перерабатывают по направлению MTG (methanol to gasoline), где бензин получают за счет дегидратаций и наращивания длины углеродной цепи [4]. Также существует процесс MTA (methanol to aromatics) для получения ароматических углеводородов, которые могут использоваться как сырье для нефтехимии, так и служить добавкой к моторным топливам [5]. В вышеперечисленные процессы можно вовлекать спирты с большей молекулярной массой (этанол, пропанол, бутанол и т.д). Основным преимуществом их вовлечения, несмотря на относительно высокую стоимость, является больший удельный выход углеводородов (УВ) по сравнению с метанолом [6].
Основным активным компонентом катализатора для этих процессов служит цеолит типа ZSM-5. Умеренная кислотность, микропористая структура, препятствующая значительному отложению кокса, термостабильность, приводят к высокой селективности в образовании олефинов и ароматических углеводородов [7, 8].
Большое влияние на каталитические свойства, состав и распределение продуктов оказывает модуль цеолита (SiO2/Al2O3). При увеличении отношения SiO2/Al2O3 снижается количество кислотных центров, препятствуя протеканию реакций переноса водорода. В результате растет селективность по отношению к легким олефинам. Если же существует необходимость в получении ароматических УВ, то снижая модуль цеолита, можно значительно увеличить их выход [9].
Модифицируя цеолит ZSM-5 различными элементами можно существенно влиять на его свойства. В работе [10] для изменения селективности катализатора к легким олефинам при превращении этанола использовали модифицирующие добавки на основе Cr, Fe, La, Ce, Zr и W. В последние годы многие исследователи неоднократно обращали внимание, что модифицирование цеолита ZSM-5 фосфором значительно повышает выходы алкенов С2–С4 за счет частичной нейтрализации фосфором кислотных центров [11].
Прямые каналы цеолита ZSM-5 пересекаются с зигзагообразными каналами, образуя трехмерную структуру узких каналов с размерами 5.1–5.6 Å. Такое строение обуславливает с одной стороны избирательность цеолита, а с другой – диффузионные ограничения, которые приводят к невысокой каталитической активности [1]. Одним из способов увеличения активности катализатора в превращении спиртов в жидкие УВ бензинового ряда является щелочная обработка цеолита. В качестве десилицирующего агента используются гидроксид натрия [1, 12], гидроксид тетрапропиламмония [7, 13]. В результате происходит частичное удаление атомов кремния из решетки, что с одной стороны приводит к образованию мезопор в цеолите, тем самым способствуя увеличению каталитической активности, а с другой – к повышению кислотности за счет снижения модуля цеолита. Высокая концентрация кислотных центров приводит к росту реакций переноса водорода и, следовательно, к большему выходу парафиновых и ароматических углеводородов [13].
Таким образом, модифицирование цеолита ZSM-5 позволяет изменять его физико-химические свойства (концентрацию и силу кислотных центров, пористую структуру). Модифицирование цеолита щелочами или соединениями фосфора оказывает существенное влияние на соотношение Si/Al в готовом цеолите, что позволяет рассматривать данные обработки эквивалентные изменению модуля цеолита.
Цель работы – исследование изменения физико-химических свойств цеолита ZSM-5, эквивалентных изменению модуля, в зависимости от отношения NaOH : SiO2 щелочной обработки и содержания фосфора при модифицировании дигидрофосфатом аммония, а также выявление закономерности изменения активности полученных катализаторов в реакциях крекинга и переноса водорода при превращении алифатических спиртов, содержащих 1–5 атомов углерода.
ЭКСПЕРИМЕНТАЛЬНАЯ ЧАСТЬ
Исходные реактивы. В качестве исходного активного компонента катализатора щелочной обработки и модифицирования фосфором использовали цеолит типа ZSM-5 (Zeolyst International, CBV 3024E) с модулем 30 без дополнительной обработки. В состав матрицы катализатора входили бентонитовая глина и оксид алюминия.
Для исследования каталитических свойств образцов катализаторов использовали спирты: метанол, этанол, пропанол-2, 2-метилпропанол-2, 3-метилбутанол-1 с содержанием основного компонента более 98% (АО “ЭКОС-1”).
Щелочная обработка. Обработка цеолита щелочью происходила по следующей схеме. В коническую колбу к навеске исходного цеолита приливали раствор щелочи (NaOH) с концентрацией 0.2 н и температурой 60°С. Для изменения глубины обработки варьировали объем модифицирующего раствора щелочи. Было получено четыре образца (ЩЕЛ-0, ЩЕЛ-25, ЩЕЛ-100, ЩЕЛ-230) с мольным отношением NaOH : SiO2 = 0, 25, 100, 230. После обработки цеолит промывали дистиллированной водой, проводили серию ионных обменов нитратом аммония. Далее цеолит сушили при комнатной температуре на воздухе, при 100°С в течение 10 ч и прокаливали в муфельной печи при 600°С в течение 5 ч.
Нанесение фосфора. Получение цеолита, модифицированного фосфором, осуществляли путем пропитки цеолита НZSM-5 (с модулем 30) раствором дигидрофосфата аммония (ООО “ЕвроХим”). Затем пропитанный цеолит отделяли от маточного раствора, сушили сутки на воздухе при комнатной температуре, затем при 100°С в течение 10 ч, прокаливали при 600°С в течение 5 ч. В результате было получено 5 образцов с содержанием фосфора в цеолите 0, 2.9, 4.1, 7.0, 8.0 мас. %.
Приготовление катализатора. Полученный цеолит смешивали с компонентами матрицы, оксидом алюминия и бентонитовой глиной в соотношении 2 : 1 : 1 до получения водной гомогенной суспензии. Затем суспензию отфильтровывали от воды, а полученную пасту отправляли на формовку в экструдер. Далее катализатор сушили при комнатной температуре, при 100°С и прокаливали в муфельной печи при 600°С.
Исследование катализатора. Содержание фосфора в цеолите определяли путем разложения образцов в минеральных кислотах с последующим анализом методом атомно-эмиссионной спектрометрии с индуктивно-связанной плазмой на спектрометре Varian 710-ES (Австралия).
Параметры пористой структуры катализаторов исследовали на приборе ASAP-2020 (Micromeritics). Координационное состояние алюминия и кремния в цеолитах исследовали методом MAS ЯМР на ядрах 27Al и 29Si на приборе Advance 400 (Bruker).
Определение кислотности образцов проводили методом температурно-программируемой десорбцией аммиака на прецизионном хемосорбционном анализаторе AutoChem-2920 Micromeritics. В экспериментах использовали смесь 6 об. % аммиака в гелии. Перед ТПД-экспериментом образцы продували гелием при 600°C в течение 1 ч, затем охлаждали в токе гелия до температуры 100°C. Аммиак адсорбировался при этой же температуре в течение 1 ч, затем продувался гелием в течение 1 ч для удаления физически адсорбированного аммиака.
Эксперименты по изучению каталитических свойств цеолитов проводили на лабораторной установке с неподвижным слоем катализатора. Катализатор в количестве 3 г загружали в реактор. Температура процесса во всех экспериментах составляла 450°С и WHSV – 2.5 ч–1. В качестве характеристики переноса водорода использован коэффициент переноса водорода (hydrogen transfer coefficient, HTC), рассчитываемый как отношение выходов насыщенных и ненасыщенных С4-углеводородов [27, 28].
Анализ газообразных продуктов осуществляли на хроматографе “ГХ-1000” с капиллярной колонкой (SiO2, 30 м × 0.32 мм) и пламенно-ионизационным детектором для определения состава углеводородных газов. Для определения состава жидких продуктов применяли хромато-масс-спектрометр SHIMADZU GCMS-2010.
Содержание кокса на катализаторе определяли по убыли массы при прокаливании образца катализатора до 600°С.
РЕЗУЛЬТАТЫ И ИХ ОБСУЖДЕНИЕ
Исследование физико-химических свойств катализатоов. Химический состав цеолитов, полученных в результате щелочной обработки, представлен в табл. 1.
Таблица 1.
Физико-химические свойства цеолитов
Параметр | ЩЕЛ-0 | ЩЕЛ-25 | ЩЕЛ-100 | ЩЕЛ-230 |
---|---|---|---|---|
Содержание, мас. % | ||||
Na2O | 0.12 | 0.16 | 0.14 | 0.69 |
Al2O3 | 4.59 | 4.99 | 5.55 | 13.82 |
SiO2 | более 95 | более 94 | более 93 | более 85 |
Количество десорб. аммиака, мкмоль/г | 1188 | 1304 | 1613 | 1948 |
Площадь поверхности БЭТ, м2/г | 416 | 425 | 425 | 596 |
Площадь микропор t-Plot, м2/г | 365 | 371 | 368 | 550 |
Объем микропор, см3/г | 0.154 | 0.145 | 0.155 | 0.211 |
Общий объем пор, см3/г | 0.217 | 0.226 | 0.264 | 0.307 |
Средний диаметр пор, нм | 2.15 | 2.13 | 2.50 | 2.06 |
После щелочной обработки наблюдается увеличение площади поверхности цеолита с 416 до 596 м2/г (см. табл. 1). Это связано с образованием мезопор за счет экстрагирования кремния из решетки цеолита. При увеличении отношения NaOH : SiO2 до 100 объем микропор не изменяется и составляет 0.154–0.155 см3/г, что, вероятно, связано с недостаточной глубиной щелочной обработки, которая не затрагивает микропоры. В то же время наблюдается рост общего объема пор цеолита. Авторы [14, 15] отмечают, что использование слабых десилицирующих агентов (алюминат натрия, гидроксид тетрапропиламмония) позволяет повышать площадь поверхности при незначительном уменьшении объема микропор. Более глубокая обработка приводит к частичному разрушению структуры цеолита с образованием микро- и мезопористой структуры. В связи с этим у образца ЩЕЛ-230 увеличивается объем микропор и площадь поверхности.
С увеличением концентрации щелочи при обработке наблюдается постепенное повышение кислотности цеолита ZSM-5 с 1188 до 1948 мкмоль/г (табл. 1). При этом растет концентрация как слабых, так и сильных кислотных центров (рис. 1). У образцов ЩЕЛ-25 и ЩЕЛ-100 не происходит изменений в силе кислотных центров. Температуры пиков слабых и сильных кислотных центров находятся в пределах 200 и 410°С соответственно. Однако, у образца 4 наблюдается снижение концентрации сильных кислотных центров и смещение пика в более низкотемпературную область. В то же время, значительно увеличивается пик, соответствующий слабым кислотным центрам. Глубокая обработка цеолита ЩЕЛ-230 в значительной степени увеличивает относительную концентрацию алюминия (до 13.82 мас. %) по сравнению с другими образцами (табл. 1). Это приводит к образованию групп Si 4Al, которые являются наиболее слабой кислотой Бренстеда, а также вызывает частичный переход сильных кислотных центров в слабые.
На рис. 2 представлены 29Si ЯМР-спектры цеолитов до и после обработки щелочью. На спектре исходного цеолита (рис. 2а) при –109 ppm наблюдается интенсивный пик, соответствующий координации 4Si 0Al. Неразделенный пик в области –98...–103 ppm относится к координации 3Si 1Al. После щелочной обработки (рис. 2б, 2в) не происходит значительного изменения координации атомов алюминия. Авторами [12, 16] высказано предположение, что отрицательно заряженные тетраэдры AlO4 могут препятствовать гидролизу связей Si–O–Al при щелочной обработке, поэтому образование координации 2Si 2Al маловероятно. Обработка щелочью при высоких значениях NaOH : SiO2 привела к значительному увеличению интенсивности пиков в области –76…–103 ppm (рис. 2г). Это связано с удалением кремния из решетки цеолита и образованию новых связей Si–O–Al (3Si 1Al, 2Si 2Al).
На рис. 3 представлен ЯМР-спектр 27Al исходного и обработанного щелочью цеолита. У исходного ZSM-5 наблюдается два пика при 58 и 3 ppm, соответствующие тетраэдрической и октаэдрической координации атомов алюминия. После обработки щелочью на спектрах не наблюдается пик в области 0 ррm, что указывает на отсутствие алюминия в октаэдрической координации. При этом не наблюдается снижения интенсивности сигнала тетраэдрической пика (рис. 3б, в). Это означает, что слабая обработка цеолита щелочью удаляет в первую очередь неструктурный алюминий, не затрагивая атомы алюминия в решетке. Асимметричность и уширение пика на рис. 3г (ЩЕЛ-230) вызвана образованием неизоморфных структур алюминия [17].
Физико-химические свойства образцов цеолитов, модифицированных фосфором представлены в табл. 2. Содержание оксида натрия в полученных образцах не превышало 0.12 мас. %. Данные анализа ТПД-NH3 образцов катализаторов показали снижение кислотности цеолитов при добавлении фосфора с 1188 до 401 мкмоль/г. При этом у образцов, содержащих фосфор, отсутствует пик соответствующий сильным кислотным центрам. В работе [18] утверждают, что фосфор включается в структуру цеолита с образованием катиона ${\text{P}}({\text{OH}})_{4}^{ + }$ при протонировании ортофосфорной кислоты кислотными центрами Бренстеда. После прокалки фосфор находится главным образом в состоянии пиро- или полифосфатов, что приводит к частичной нейтрализации кислотных центров Бренстеда, при более высокой нейтрализации сильных центров. Это также подтверждается данными 31Р ЯМР. В спектре был обнаружен пик 5 ppm, который соответствует ортофосфорной кислоте. Три неразделенных пика в области –5…–50 ppm с вершинами –6, –20, –28 ppm относятся к пирофосфорной кислоте, малым полифосфатам, присоединенных к атому алюминия, средним полифосфатам соответственно [19, 20].
Таблица 2.
Физико-химические свойства цеолитов типа ZSM-5, модифицированных фосфором
Цеолит типа ZSM-5 | Содержание фосфора, мас. % | ||||
---|---|---|---|---|---|
Параметр | 0 | 2.8 | 4.1 | 7.0 | 8.0 |
Количество десорб. аммиака, мкмоль/г | 1188 | 556 | 401 | 292 | 347 |
Площадь поверхности БЭТ, м2/г | 416 | 335 | 224 | 182 | 112 |
Площадь микропор t-Plot, м2/г | 365 | 290 | 209 | 163 | 102 |
Объем микропор, см3/г | 0.154 | 0.115 | 0.083 | 0,063 | 0.040 |
Общий объем пор, см3/г | 0.217 | 0.235 | 0.118 | 0.139 | 0.087 |
Средний диаметр пор, нм | 2.1 | 2.8 | 2.1 | 3.0 | 3.1 |
Анализ пористой структуры показал уменьшение площади поверхности, площади микропор, общего объема и объема микропор образцов цеолита, модифицированных фосфором (табл. 2). Это связано с образованием полифосфатов внутри пор цеолита, которые приводят к их частичной блокировке [21].
Был проведен ЯМР-анализ цеолитов, модифицированных фосфором на ядрах 27Al. У исходного образца (рис. 4а) максимальную интенсивность имеет пик в области 40–70 ррm, соответствующий тетраэдрической координации алюминия. После введения фосфора в количестве 2.8% наблюдается рост интенсивности пика с вершиной –8 ppm, соответствующего образованию связей типа AlOoct–O–P. Дальнейшее повышение содержания фосфора до 8.0% приводит к снижению доли алюминия, находящегося в тетраэдрической координации, что соответствует выходу атомов Al из решетки цеолита. Таким образом, введение фосфора вызывает деалюминирование цеолита [22]. В то же время, уменьшение суммарной площади пиков при увеличении количества фосфора (рис. 4г, д) может указывать на образование связей A–O–P [23].
Рис. 4.
27Al ЯМР спектры фосформодифицированных цеолитов: (а) 0%, (б) 2.8%, (в) 4.1%, (г) 7.0%, (д) 8.0%.
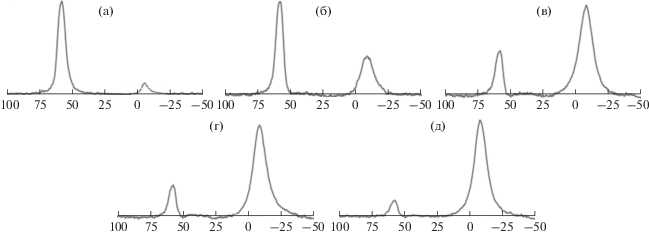
Исследование активности обработанных цеолитов и катализаторов на их основе в превращении спиртов. Было поведено исследование превращения различных видов спиртов на цеолитсодержащем катализаторе с модулем 30, при температуре 450°С и весовой скорости подачи сырья равной 2.5 ч–1 (табл. 3).
Таблица 3.
Состав продуктов превращения спиртов
Выход, % на углеводородную часть | Метанол | Этанол | Пропанол-2 | 2-Метилпро-панол-2 | 3-Метилбута-нол-1 |
---|---|---|---|---|---|
С1 | 2.2 | 0.7 | 0.6 | 0.5 | 0.8 |
С2 | 5.1 | 3.9 | 3.0 | 2.5 | 3.2 |
С3 | 37.2 | 40.1 | 44.3 | 43.0 | 38.6 |
С4 | 25.9 | 22.3 | 27.8 | 28.1 | 23.5 |
Жидкие УВ (в т.ч. С5) | 25.6 | 28.7 | 20.7 | 22.5 | 30.9 |
Кокс | 4.0 | 4.3 | 3.6 | 3.4 | 3.0 |
Выход водной части, мас. % | 55.7 | 38.8 | 30.5 | 25.3 | 21.4 |
При превращении этанола, пропанола-2, 2-метилпропанола-2 наблюдаются характерные высокие выходы УВС2, С3, С4, что указывает на дегидратацию спиртов с образованием олефинов и их последующим превращением в насыщенные или конденсированные продукты. Продукты конверсии метанола содержат наибольшее количество метана, этана и этилена, которые являются продуктами распада и дегидратации диметилового эфира.
Превращение спиртов может проходить через два возможных механизма с образованием эфиров или олефинов [24]. При этом с увеличением молекулярной массы спирта количество получаемых эфиров снижается. Анализ жидких продуктов и водной части методом хромато-масс-спектрометрии показал отсутствие содержания эфиров и других кислородсодержащих соединений, что возможно связано с более высокой температурой (450°С) конверсии спиртов, в то время как для получения эфиров приемлемый температурный интервал 200–300°С [25].
Также при конверсии спиртов наблюдается линейное уменьшение содержания УВ С1–С2 в ряду от метанола к 2-метилпропанолу-2, а при превращении 3-метилбутанола-1 их доля снова возрастает с одновременным снижением количества УВ С3–С4. Таким образом, превращение спиртов может быть рассмотрено в рамках двухстадийного превращения – дегидратация спирта + каталитический крекинг легкого непредельного УВ.
Исследование каталитических свойств модифицированных образцов цеолита ZSM-5 выполнено с использованием в качестве сырья 3-метилбутанола-1. При этом образующийся в случае дегидратации 3-метилбутанола-1 изопентен будет обладать максимальной активностью по сравнению с другими олефинами, получаемыми из других спиртов.
Влияние щелочной обработки цеолитов в превращение спиртов изучалось при температуре 450°С и WHSV = 2.5 ч–1. Распределение и выход продуктов представлены в табл. 4.
Таблица 4.
Состав продуктов превращения 3-метилбутанола-1 на цеолитах, обработанных щелочью
Выход, % на углеводородную часть | ЩЕЛ-0 | ЩЕЛ-25 | ЩЕЛ-100 | ЩЕЛ-230 |
---|---|---|---|---|
Алканы С1–С4 | 61.4 | 64.7 | 62.2 | 58.3 |
Олефины С2–С4 | 4.7 | 3.3 | 1.6 | 1.5 |
Жидкие УВ (в том числе С5) | 30.9 | 28.9 | 32.8 | 29.8 |
Кокс | 3.0 | 3.1 | 3.4 | 10.4 |
НТС4 | 15.7 | 24.4 | 31.7 | 60.8 |
Арены | 23.2 | 23.5 | 28.2 | 22.5 |
Состав жидких продуктов, % | ||||
н-парафины | 0.2 | 0.6 | 0.1 | 0.6 |
изо-парафины | 0.9 | 1.4 | 0.7 | 3.2 |
олефины | 0.7 | 0.4 | 0.3 | 0.2 |
нафтены | 1.0 | 0.6 | 0.6 | 0.5 |
арены | 96.9 | 97.0 | 98.3 | 95.5 |
С повышением глубины обработки цеолита щелочью увеличивается концентрация кислотных центров. Это, с одной стороны, приводит к снижению выхода олефинов С2–С4 с 4.7 до 1.5%, а с другой, – к росту коэффициента переноса водорода (рис. 5). По сравнению с исходным образцом цеолита ZSM-5 коэффициент переноса водорода вырос в 4 раза и составил 60.8. При этом зависимость выхода олефинов от глубины обработки имеет гиперболический вид, где сначала происходит резкое снижение выхода с 4.7 до 1.6%, а затем постепенное уменьшение до 1.5%, в то время как, отношение NaOH : SiO2 увеличилось со 100 до 230 (более чем в 2 раза). Данное явление может быть связано с дезактивацией кислотных центров коксовыми отложениями, выход которых на образце ЩЕЛ-230 составил 10.4%.
Рис. 5.
Влияние щелочной обработки цеолита на (а) выход олефинов С2–С4 и (б) изменение коэффициента переноса водорода при крекинге 3-метилбутанола-1.
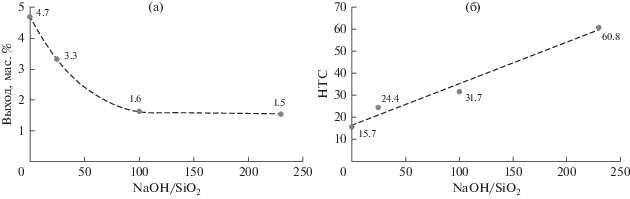
Жидкий продукт состоит более чем на 95% из ароматических УВ. При этом с повышением отношения NaOH : SiO2 наблюдается тенденция равномерного снижения количества олефинов и нафтенов при одновременном увеличении содержания аренов, что также указывает на рост вклада реакций переноса водорода. Однако, низкое содержание аренов в жидком продукте образца ЩЕЛ-230 вероятно связано с частичным переходом ароматических углеводородов в кокс.
Исследование влияния фосфора на состав и выход продуктов при превращении 3-метилбутанола-1 проводилось при температуре 450°С и WHSV = 2.5 ч–1 (табл. 5).
Таблица 5.
Состав продуктов превращения 3-метилбутанола-1 на фосфорсодержащих цеолитах типа ZSM-5
Выход, % на углеводородную часть | Содержание фосфора, мас. % | ||||
---|---|---|---|---|---|
0 | 2.8 | 4.1 | 7.0 | 8.0 | |
Алканы С1–С4 | 61.4 | 61.0 | 61.0 | 51.6 | 31.8 |
Олефины С2–С4 | 4.7 | 6.3 | 6.7 | 12.4 | 32.2 |
Жидкие УВ (в том числе С5) | 30.9 | 30.1 | 29.8 | 32.8 | 33.0 |
Кокс | 3.0 | 2.6 | 2.5 | 3.2 | 3.0 |
НТС4 | 15.7 | 13.9 | 11.5 | 6.2 | 1.4 |
Арены | 23.2 | 20.7 | 20.8 | 16.6 | 11.1 |
Состав жидких продуктов, % | |||||
н-парафины | 0.2 | 0.3 | 0.5 | 0.9 | 2.1 |
изо-парафины | 0.9 | 1.7 | 2.2 | 3.0 | 4.0 |
олефины | 0.7 | 0.7 | 0.7 | 3.8 | 16.0 |
нафтены | 1.0 | 1.6 | 1.4 | 5.7 | 13.6 |
арены | 96.9 | 95.6 | 95.3 | 86.5 | 64.3 |
При увеличении содержания фосфора от 0 до 4.1% наблюдается постепенное увеличение выхода олефинов С2–С4 с 4.7 до 6.7% (рис. 6а). При повышении концентрации фосфора в цеолите до 7.0% выход олефинов вырос более чем в 2.5 раза по сравнению с первоначальным, а при концентрации фосфора 8.0% – более чем в 6.5 раз и составил 32.2 мас. %. Для коэффициента переноса водорода наблюдается закономерная зависимость от количества фосфора в цеолите: постепенно снижение коэффициента до концентрации фосфора 4.1% и резкое падение в интервале 7.0–8.0% (рис. 6б). Высокое содержание фосфора подавляет сильные кислотные центры цеолита, отвечающие за перенос водорода, способствуя высокому выходу легких олефинов.
Рис. 6.
Влияние фосфора в цеолите на (а) выход олефинов С2–С4 и (б) изменение коэффициента переноса водорода при крекинге 3-метилбутанола-1.
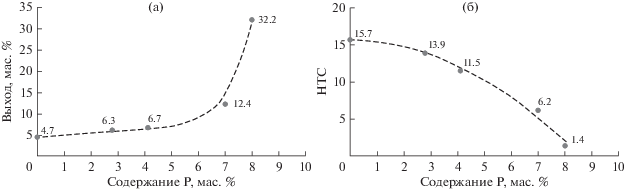
Анализ жидких продуктов показал, что при содержании фосфора в цеолите более 4.1% происходит резкий рост олефиновых и нафтеновых соединений. Доля ароматических углеводородов уменьшилась с 96.9 до 64.3%, что указывает на снижение вклада реакций переноса водорода, вследствие подавления фосфором кислотных центров [26].
ЗАКЛЮЧЕНИЕ
В работе были проведены исследования физико-химических и каталитических свойств цеолитов, прошедших щелочную обработку и модифицирование фосфором, и катализаторов на их основе. Обработка щелочью позволяет изменять пористую структуру цеолитов, увеличивая площадь поверхности, общий объем пор, за счет образования мезопор, а при глубокой обработке за счет дополнительного образования микропор.
Щелочная обработка цеолита ZSM-5 способствует увеличению общей кислотности, причем обработка при отношении NaOH : SiO2 более 100 приводит к снижению концентрации сильных кислотных центров, при одновременном росте количества слабых центров. Данные ЯМР анализа показали, что при увеличении соотношения NaOH : SiO2 наблюдается увеличение групп 2Si 2Al и 1Si 3Al. Рост кислотности и увеличение размера пор модифицированных щелочью цеолитов оказывает положительное влияние на протекание реакций переноса водорода. При превращении 3-метилбутанола-1 на катализаторе, содержащем обработанный щелочью цеолит (NaOH : SiO2 = 230), коэффициент переноса водорода составил 60.8. Выход олефинов уменьшился с 4.7% (немодифицированый образец) до 1.5%.
Модифицирование цеолитов фосфором, в противоположность щелочной обработке, вызывает снижение общей кислотности цеолита. При этом число сильных кислотных центров снижается значительнее. Также данные ЯМР анализа 27Al показывают переход из тетраэдрической координации в октаэдрическую, что происходит при деалюминировании цеолита. При содержании фосфора в цеолите 8.0%, коэффициент переноса водорода при превращении 3-метилбутанола-1 был снижен до 1.4 и достигнут максимальный выход олефинов С2-С4 32.2 мас. %
Обработка цеолита типа ZSM-5 щелочью приводит к увеличению площади поверхности, объема пор и кислотности цеолита. Наблюдается рост коэффициента переноса водорода. Таким образом, обработка цеолита щелочью эквивалента снижению модуля цеолита. Модифицирование цеолита типа ZSM-5 фосфором приводит к снижению площади поверхности, объема пор и кислотности цеолита. При этом происходит уменьшение коэффициента переноса водорода. Таким образом, модифицирование цеолита фосфором эквивалентно уменьшению модуля цеолита.
БЛАГОДАРНОСТИ
Работа выполнена в рамках государственного задания ИППУ СО РАН в соответствии с Программой фундаментальных научных исследований государственных академий наук на 2013–2020 годы по направлению V.46, проект № V.46.2.4 (номер госрегистрации в системе ЕГИСУ НИОКТР AAAA-A17-117021450095-1).
Авторы выражают благодарность сотрудникам Института проблем переработки углеводородов СО РАН С.Н. Евдокимову, Т.И. Гуляевой, Р.Р. Измайлову, А.В. Бабенко и Т.В. Киреевой за помощь при подготовке статьи.
Список литературы
Bjørgen M., Joensen F, Holm M.S., Olsbye U., Lillerud K.-P., Svelle S. // Applied Catalysis A: General. 2008. № 345. P. 43.
Zhang R., Wang Z. // Chinese J. of Chemical Engineering. 2015. № 23. P. 1131.
Mores D., Stavitski E., Kox M., Kornatowski J., Olsbye U., Weckhuysen B.M. // Chem. Eur. J. 2008. № 14. P. 11320.
Ilias S., Bhan A. // J. of Catalysis № 290. 2012. P. 186.
Ji H., Zhang Q., Wang B., Li C., Shan H. // Catal. Lett. 2014. № 144. P. 1860.
Mentzel U.V., Shunmugavel S., Hruby S.L., Christensen C.H., Holm M.S. // J. Am. Chem. Soc. 2009. № 131. P. 17009.
Rownaghi A.A., Hedlund J. // Ind. Eng. Chem. Res. 2011. № 50. P. 11872.
Liu Z., Wu D., Ren S., Chen X., Qiu M., Liu G., Zenga G., Sun Y. // RSC Adv. 2016. № 6. P. 15816.
Liu J., Zhang C., Shen Z., Hua W., Tang Y., Shen W., Yue Y., Xu H. // Catalysis Communications. 2009. № 10. P. 1506.
Inoue K., Okabe K., Inaba M., Takahara I., Murata K. // Reac. Kinet. Mech. Cat. 2010. № 101. P. 477.
Yaripour F., Shariatinia Z., Sahebdelfar S., Irandoukht A. // Microporous and Mesoporous Materials. 2015. № 203. P. 41.
Xin H., Li X., Fang Y., Yi X., Hu W., Chu Y., Zhang F., Zheng A., Zhang H., Li X. // J. of Catalysis. 2014. № 312. P. 204.
Yingping H., Min L., Chengyi D., Shutao X., Yingxu W., Zhongmin L., Xinwen G. // Chinese J. of Catalysis. 2013. № 34. P. 1148.
Abello S., Bonilla A., Perez-Ramırez J. // Applied Catalysis A: General. 200. № 364. P. 191.
Caicedo-Realpe R., Perez-Ramırez J. // Microporous and Mesoporous Materials. 2010. № 128. P. 91.
Gil B., Mokrzyckib L., Sulikowskib B., Olejniczakc Z., Walasa S. // Catalysis Today. 2010. № 152. P. 24.
Sadowska K., Wach A., Olejniczak Z., Kustrowski P., Datka J. // Microporous and Mesoporous Materials. 2013. № 167. P. 82.
Takahashi A., Xia W., Nakamura I., Shimada H., Fujitani T. // Applied Catalysis A: General. 2012. № 423–424. P. 162.
Cabral de Menezes S.M., Lam Y.L., Damodaran K., Pruski M. // Microporous and Mesoporous Materials. 2006. № 95. P. 286.
Lee Y.-J., Kim J.M., Bae J.W., Shin C.-H., Jun K.-W. // Fuel. 2009. № 88. P. 1915.
Liua D., Choi W.C., Leea C.W., Kanga N.Y., Leea Y.J., Shinc C.-H., Park Y.K. // Catalysis Today. 2011. № 164. P. 154.
Zhao G., Teng J., Xie Z., Jin W., Yang W., Chen Q., Tang Y. // J. of Catalysis. 2007. № 248. P. 29.
Ramesh K., Jie C., Han Y.-F., Borgna A. // Ind. Eng. Chem. Res. 2010. № 49. P. 4080.
Phillips C.B., Datta R. // Ind. Eng. Chem. Res. 1997. № 36. P. 4466.
Ramasamya K.K., Wang Y. // Catalysis Today. 2014. № 237. P. 89.
Songa Z., Takahashi A., Nakamuraa I., Fujitani T. // Applied Catalysis A: General. 2010. № 384. P. 201.
Park S., Biligetu T., Wang Y., Nishitoba T., Kondo J. N., Yokoi T. // Catalysis Today. 2018. № 303. P. 64.
Mehla S., Kukade S., Kumar P., Rao P. V. C., Sriganesh G., Ravishankar R. // Fuel. 2019. 242. P.487.
Дополнительные материалы отсутствуют.