Нефтехимия, 2019, T. 59, № 4, стр. 367-377
Закономерности совместных превращений вакуумных газойлей с растительными маслами на бицеолитных катализаторах крекинга
П. В. Липин 1, *, О. В. Потапенко 1, Т. П. Сорокина 1, В. П. Доронин 1
1 Институт проблем переработки углеводородов СО РАН
Омск, Россия
* E-mail: lipin@ihcp.ru
Поступила в редакцию 01.10.2018
После доработки 01.03.2019
Принята к публикации 14.03.2019
Аннотация
В последние годы активно изучается вопрос поиска и переработки природных веществ, выступающих в качестве альтернативы нефтяному сырью. В качестве возможных источников сырья для получения биотоплив рассматриваются растительные масла [1–4], жиры животного происхождения [5, 6], сахара [7], биомасса [8, 9] и др.
Одним из возможных способов получения таких биотоплив является крекинг растительных масел. В настоящее время использование в качестве сырья каталитического крекинга растительных масел экономически не обосновано, т.к. затраты на их получение выше, чем стоимость нефтяного сырья. Кроме того, авторами работы [10] было показано, что выходы целевых продуктов крекинга чистых растительных масел не достигают уровня значений, получаемых при переработке вакуумного газойля – традиционного сырья крекинга. Это обусловлено в первую очередь жирнокислотным составом растительных масел. Так, первичные продукты термического разложения исходных триглицеридов растительных масел обладают высокой реакционной способностью, что может отрицательно сказаться как на количестве, так и на качестве продуктов крекинга. В связи с этим целесообразно осуществлять совместный крекинг вакуумных газойлей и растительных масел. При этом необходимо учитывать, что групповой состав выбранного углеводородного сырья также будет во многом определять распределение целевых продуктов каталитического крекинга.
Помимо подбора сырья для совместного превращения вакуумных газойлей с растительными маслами в условиях крекинга важным аспектом остается выбор цеолитсодержащего катализатора. В случае нефтехимического варианта крекинга в состав катализатора в качестве активного компонента, помимо цеолита Y, вводится цеолит семейства пентасилов. Наибольшее распространение среди них получил цеолит ZSM-5. Он позволяет осуществлять вторичный крекинг бензиновой фракции при низкой активности реакций переноса водорода.
Большое значение имеет предварительное модифицирование цеолитов перед их включением в состав катализатора. Так, регулирование физико-химических свойств цеолитов, а также их кислотных характеристик может существенно повысить выход легких олефинов. Наиболее частым является модифицирование цеолитов фосфором [11–14], при введении которого снижается общая кислотность цеолита, что обусловливает образованием новых групп P–OH, кислотные свойства которых слабее, чем групп Al–OH [12]. Кроме того, введение фосфора ведет к изменению основных текстурных характеристик катализатора.
Цель настоящей работы – исследование закономерностей совместных превращений вакуумных газойлей, отличающихся групповым составом, и растительных масел различного жирнокислотного состава.
ЭКСПЕРИМЕНТАЛЬНАЯ ЧАСТЬ
При исследовании влияния состава смесевого сырья на состав продуктов в качестве сырья нефтяного происхождения использованы два вида вакуумных газойлей, отличающихся групповым составом (табл. 1). В качестве сырья растительного происхождения использовали подсолнечное и пальмовое масла. Жирнокислотный состав масел определен путем гидролиза исходных триглицеридов и анализом состава получаемых кислот (табл. 2). Соотношение нефтяного и растительного компонентов в модельных смесях составляло 95/5 и 90/10 мас. %/мас. % соответственно.
Таблица 1.
Основные характеристики вакуумных газойлей
Наименование показателя | Вакуумные газойли | |||
---|---|---|---|---|
остаток гидрокрекинга (ОГК) | гидроочищенный вакуумный газойль (ГВГ) | негидроочищенный вакуумный газойль (НГВГ) | ||
Плотность при 15°С, г/см3 | 0.858 | 0.903 | 0.9137 | |
Групповой состав, мас. %: | ||||
– парафино-нафтеновые углеводороды | 93.7 | 68.1 | 65.00 | |
– легкие ароматические углеводороды – средние ароматические углеводороды – тяжелые ароматические углеводороды – смолы |
$\left. \begin{gathered} \hfill \\ \hfill \\ _{{_{{_{{_{{_{{_{{}}}}}}}}}}}} \hfill \\ \end{gathered} \right\}$ | 6.3 | 15.4 3.3 9.7 3.5 | 10.90
5.80 16.10 2.20 |
Содержание серы, ppm | 13.7 | 558 | 8600 | |
Коксуемость, мас. % | 0.01 | 0.07 | 0.20 |
Таблица 2.
Основные характеристики растительных масел
Наименование показателя | Растительные масла | |
---|---|---|
пальмовое | подсолнечное | |
Плотность при 20°С, г/см3 | 0.912 | 0.894 |
Содержание кислорода, мас. % | 11.2 | 10.8 |
Жирнокислотный состав, мас. %: | ||
–пальмитиновая (С16:0) –стеариновая (С18:0) –олеиновая (С18:1) –линолевая (С18:2) |
19.3 13.2 13.5 6.0 |
6.9
1.9 19.7 71.3 |
Индекс непредельности | 1.2 | 9.0 |
Для характеристики непредельности жирных кислот предлагается использовать индекс непредельности – параметр, вычисляемый по формуле:
где, хi – молярная доля i-й жирной кислоты в масле; Nd.b.,i – количество двойных связей в i-й кислоте; NC,i – количество атомов углерода в i-той кислоте.
При исследовании влияния модифицирования цеолитов фосфором в качестве сырья использована смесь гидроочищенного вакуумного газойля (табл. 1) и подсолнечного масла. Соотношение нефтяного и растительного компонентов в модельной смеси составляло 90/10 мас. %/мас. % соответственно.
Для исследования были приготовлены катализаторы, которые содержали в своем составе цеолиты HРЗЭY, HZSM-5 и матрицу. В качестве компонентов матрицы использовались аморфный алюмосиликат (Al−Si, Na2O = 0.09 мас. %, Al2O3 = 10.80 мас. %), оксид алюминия (Al2O3) и бентонитовая глина – монтмориллонит (MM, Na2O = 0.12 мас. %). В табл. 3 приведен компонентный состав приготовленных образцов катализаторов.
Таблица 3.
Компонентный состав катализаторов
Катализатор | Цеолиты, мас. % | Матрица, мас. % | |||
---|---|---|---|---|---|
HРЗЭY | HZSM-5 | Al−Si | Al2O3 | MM | |
Образец 1 (HРЗЭY/HZSM-5) | 10.0 | 15.0 | 33.0 | 17.0 | 25.0 |
Образец 2 (P/HРЗЭY/HZSM-5) | |||||
Образец 3 (HРЗЭY/P/HZSM-5) |
Модифицирование цеолитов HРЗЭY (производства AO “Газпромнефть-ОНПЗ”) и цеолита HZSM-5 (производства фирмы Zeolyst International – марка CBV-3024E) фосфором осуществляли методом, приведенным ниже. Цеолиты пропитывали раствором (NH4)2HPO4. Модификацию осуществляли из расчета: 4.0 мас. % фосфора для цеолита Y с модулем 9 и 8.0 мас. % фосфора для ZSM-5 с модулем 30. Процесс пропитки проводили под вакуумом в течение 2 ч с последующей сушкой 24 ч при температуре 25°С. Далее осуществляли сушку при 100°С 12 ч и прокалку при 550°С в течение 3 ч.
Температурно-программируемую десорбцию (ТПД) аммиака проводили на прецизионном хемосорбционном анализаторе AutoChem-2920 “Micromeritics” в температурной области 100–600°С со скоростью нагрева измерительной ячейки с образцом 10°С/мин. Скорость потока через реактор с образцом составляла 30 см3 (STP)/мин.
Характеристики удельной поверхности и пористой структуры цеолитов определялись из анализа изотерм адсорбции-десорбции азота при 77.4 K, измеренных на объемной вакуумной статической установке ASAP-2020 фирмы “Micromeritics”. Перед проведением адсорбционных измерений все образцы вакуумировали при 300°С в течение 12 ч. Значения адсорбционного объема пор (Vадс, см3/г) определяли по величине адсорбции азота при Р/Р0 = 0.990. Для оценки величин удельной внешней поверхности (Sвн, м2/г ) и объема микропор (Vмикро-, см3/г) использовали сравнительный t-метод.
Все образцы катализаторов были подвергнуты предварительной гидротермальной обработке при температуре 788°C в течение 5 ч в среде 100%-ного водяного пара.
Крекинг смесевого сырья проводили на лабораторной установке проточного типа с неподвижным слоем катализатора в количестве 5 г при температуре 450°C и весовой скорости подачи сырья 30 ч–1. Сырье дозировали в течение 30 с. Реакторную систему продували азотом с расходом 30 мл/мин.
Состав газообразных продуктов крекинга (CO, СО2 и C1−C5+), а также содержание продувочного газа (N2) определяли хроматографически на приборе “Кристалл 5000.1”, оборудованном капиллярной колонкой GS-Alumina (50 м × 0.53 мм), стальной насадочной колонкой (3 м × 3 мм, адсорбент NaX фракции 45/60 меш), пламенно-ионизационным детектором и детектором по теплопроводности.
Количественный анализ жидких продуктов крекинга проводили в соответствии с методикой ASTM D 2887 (метод имитированной дистилляции) на газовом хроматографе GC-2010 Shimadzu c капиллярной колонкой Rtx-2887 (10 м × 0.53 мм × × 2.65 мкм) и пламенно-ионизационным детектором. К бензиновой фракции относили все жидкие УВ с температурой кипения менее 216°С.
Количество получаемой воды определяли из 1H ЯМР-спектров по соотношению пиков, соответствующих ацетону и воде. Ацетон вводили в смесь в известном количестве для гомогенизации получаемых жидких продуктов. Спектры 1Н ЯМР были записаны на ЯМР-спектрометре Аvance-400 фирмы Bruker c использованием широкополосного многоядерного датчика PARBO BB в стандартных ампулах (Ø5 мм), в ходе одноимпульсного эксперимента при следующих параметрах: частота Лармора 400 МГц для ядер 1H. В качестве эталона использован тетраметоксисилан.
Содержание коксовых отложений на катализаторе определяли по убыли массы образца после его прокаливания при 550°С.
РЕЗУЛЬТАТЫ И ИХ ОБСУЖДЕНИЕ
Совместный крекинг вакуумных газойлей и растительных масел
На рис. 1–5 приведены результаты каталитических испытаний на бицеолитном катализаторе крекинга, содержащем немодифицированные цеолиты. Из представленных данных видно, что при совместном превращении нефтяного и растительного сырья значения конверсии изменяются (рис. 1). Однако изменения конверсии во многом зависят от группового состава вакуумного газойля и жирнокислотного состава растительного масла. Так, при превращении смеси негидроочищенного вакуумного газойля с подсолнечным маслом конверсия повышается на 3.6 мас. % по сравнению с чистым негидроочищенным вакуумным газойлем, а в случае использования пальмового масла конверсия увеличивается на 4.6 мас. %. При использовании в качестве нефтяной компоненты смесевого сырья остатка гидрокрекинга растительные масла практически не оказывают промотирующего действия на крекинг нефтяной фракции.
Рис. 1.
Изменения значений конверсии при крекинге смеси нефтяного (90 мас. %) и растительного (10 мас. %) сырья (температура 450°С, катализатор : сырье – 4.0). Нефтяное сырье: остаток гидрокрекинга (ОГК), негидроочищенный вакуумный газойль (НГВГ).
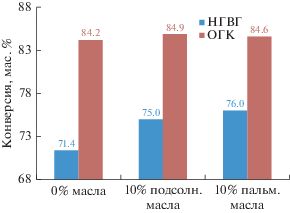
Рис. 2.
Изменения выхода бензина при крекинге смеси нефтяного (90 мас. %) и растительного (10 мас. %) сырья (температура – 450°С, катализатор : сырье – 4.0). Нефтяное сырье: остаток гидрокрекинга (ОГК), негидроочищенный вакуумный газойль (НГВГ).
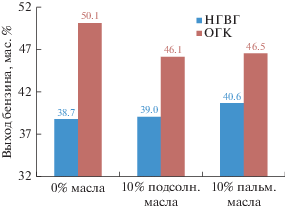
Рис. 3.
Изменения выхода кокса при крекинге смеси нефтяного (90 мас. %) и растительного (10 мас. %) сырья (температура – 450°С, катализатор : сырье – 4.0). Нефтяное сырье: остаток гидрокрекинга (ОГК), негидроочищенный вакуумный газойль (НГВГ).
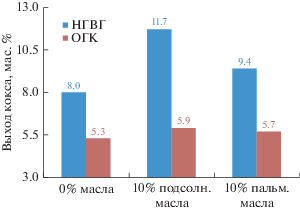
Рис. 4.
Изменения суммарного выхода пропан-пропиленовой и бутан-бутиленовой фракций при крекинге смеси нефтяного (90 мас. %) и растительного (10 мас. %) сырья (температура – 450°С, катализатор : сырье – 4.0). Нефтяное сырье: остаток гидрокрекинга (ОГК), негидроочищенный вакуумный газойль (НГВГ).
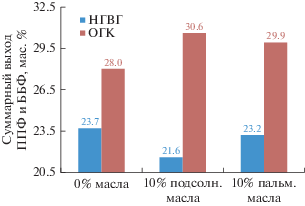
Рис. 5.
Изменения выхода олефинов С3 и С4 при крекинге смеси нефтяного (90 мас. %) и растительного (10 мас. %) сырья (температура – 450°С, катализатор : сырье – 4.0). Нефтяное сырье: остаток гидрокрекинга (ОГК), негидроочищенный вакуумный газойль (НГВГ).
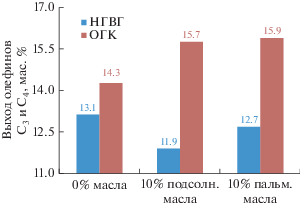
Ранее на примере моноцеолитного катализатора было показано, что при совместном крекинге растительное масло оказывает промотирующий эффект на превращение вакуумного газойля [3]. Данное действие обусловлено образованием олефинов при термическом разложении триглицеридов растительного масла, которые выступают в качестве акцептора водорода, а парафины и нафтены вакуумного газойля – в качестве донора. В результате образуются карбокатионы, которые легко и быстро сорбируются на кислотных центрах катализаторов. При этом наиболее заметно данный промотирующий эффект проявляется для газойлей с высоким содержанием ароматических УВ. Это связано с возникновением конкуренции в адсорбции на активной поверхности катализатора между образующимися карбокатионами и ароматическими УВ нефтяного сырья. При использовании вакуумного газойля, отличающегося высоким содержанием парафино-нафтеновой фракции (например, остаток гидрокрекинга), промотирующий эффект растительного масла в смеси практически не проявляется.
В нашем случае при анализе состава углеводородной части продуктов для смеси, содержащей остаток гидрокрекинга, установлено, что выход бензина (рис. 2) снижается с 50.1 мас. % (чистое нефтяное сырье) до 46.1 (смесь с подсолнечным маслом) и до 46.5 мас. % (смесь с пальмовым маслом). При использовании негидроочищенного вакуумного газойля выход бензиновой фракции, напротив, растет. Так, для смеси с подсолнечным маслом выход бензина увеличивается до 39.0 мас. %, а для смеси с пальмовым маслом до 40.6 мас. %. Кроме того, необходимо отметить, что при использовании подсолнечного масла наблюдается увеличение образования коксовых отложений на бицеолитном катализаторе, особенно для смеси с негидроочищенным вакуумным газойлем (рис. 3).
На рис. 4 и 5 показано влияние присутствия растительного масла в смесевом сырье крекинга на выход углеводородных газов крекинга. Из данных видно, что в смеси с остатком гидрокрекинга как подсолнечное, так и пальмовое масло способствуют увеличению суммарного выхода пропан-пропиленовой и бутан-бутиленовой фракций. При этом значение индекса непредельности растительного масла практически не влияет на выход данных газовых фракций. Аналогичные закономерности наблюдаются и для выхода олефинов С3 и С4.
При совместном крекинге негидроочищенного вакуумного газойля с маслом, имеющим низкий индекс непредельности (пальмовое масло), суммарный выход пропан-пропиленовой и бутан-бутиленовой фракций, а также выход легких олефинов практически не изменяется по сравнению с превращением чистого негидроочищенного вакуумного газойля. Для смеси негидроочищенного вакуумного газойля с маслом с высоким индексом непредельности (подсолнечное масло) наблюдается снижение как суммарного выхода ППФ и ББФ, так и олефинов С3 и С4. Вероятно, это связано с повышенным содержанием подсолнечного масла в смесевом сырье. Так, масла с высоким содержанием непредельных жирных кислот в составе исходных триглицеридов крекируются с преимущественным образованием высокореакционных олефинов. Данные непредельные УВ легко подвергаются циклизации с последующим дегидрированием, в результате чего образуются различные ароматические УВ при одновременном снижении выходов парафинов и олефинов. Таким образом, наличие в структуре подсолнечного масла триглицеридов с двумя или тремя двойными С=С-связями объясняет повышение выхода кокса.
При крекинге смесового сырья на моноцеолитном катализаторе [3] было показано, что чем выше содержание олефинов в органических продуктах термического разложения триглицеридов масла, тем более сильный промотирующий эффект оказывает растительное масло на превращение вакуумного газойля. Для бицеолитного катализатора наблюдается несколько иная ситуация. Так, смеси, содержащие 10 мас. % подсолнечного масла, при превращении на бицеолитных катализаторах отличаются повышенным выходом кокса при одновременном сниженном выходе бензиновой фракции по сравнению со смесями с пальмовым маслом. Вероятно, это связано с образованием высокореакционных олефинов с двумя и тремя двойными связями, что в итоге ведет к повышенному образованию коксовых отложений на катализаторе. Для минимизации данного эффекта были приготовлены смеси, содержащие 95 мас. % вакуумного газойля и 5 мас. % подсолнечного масла. В табл. 4 приведено сопоставление результатов каталитических испытаний для смесей с 5 и 10 мас. % растительного масла с высоким индексом непредельности.
Таблица 4.
Состав продуктов крекинга нефтяного сырья и смеси нефтяного сырья и растительного масла (температура 450°С, катализатор : сырье – 4.0)
Состав смесей | НГВГ/подсолнечное масло (95%/5%) | НГВГ/подсолнечное масло (90%/10%) | ОГК/подсолнечное масло (95%/5%) | ОГК/подсолнечное масло (90%/10%) |
---|---|---|---|---|
Конверсия | 73.9 | 75.0 | 84.2 | 84.9 |
Продукты, мас. % | ||||
Газообразные продукты | 26.0 | 24.0 | 30.3 | 32.6 |
СО + СО2 | 1.0 | 1.1 | 0.9 | 1.0 |
С1–С2 | 1.1 | 1.3 | 0.8 | 1.0 |
ППФ в т.ч. пропилена |
8.8 7.3 |
8.2 6.7 |
9.5 7.9 |
10.6 8.7 |
ББФ в т.ч. бутиленов |
15.1 6.1 |
13.4 5.2 |
19.1 7.2 |
20.0 7.0 |
Жидкие продукты | 65.9 | 64.3 | 64.2 | 61.5 |
вода | 0.2 | 0.3 | 0.2 | 0.3 |
бензин | 39.6 | 39.0 | 48.2 | 46.1 |
легкий газойль | 18.0 | 18.0 | 12.3 | 12.2 |
тяжелый газойль | 8.1 | 7.0 | 3.5 | 2.9 |
Кокс | 8.1 | 11.7 | 5.5 | 5.9 |
Селективность, % | ||||
Газы | 35.2 | 32.0 | 36.0 | 38.4 |
Вода | 0.3 | 0.4 | 0.3 | 0.4 |
Бензин | 53.6 | 52.0 | 57.2 | 54.3 |
Кокс | 10.9 | 15.6 | 6.5 | 6.9 |
Из приведенных данных видно, что при снижении содержания подсолнечного масла в смеси с негидроочищенным вакуумным газойлем уменьшается селективность образования кокса с 15.6 до 10.9%, а значения селективности образования газов и бензина повышаются на 3.2 и 1.6% соответственно. Для смеси с остатком гидрокрекинга при понижении содержания подсолнечного масла отмечается снижение значений селективности образования кокса на 0.4% и газов на 2.4%. При этом наблюдается повышение селективности образования бензиновой фракции на 2.9%.
По результатам каталитических испытаний можно выделить следующие закономерности. При превращении смеси с остатком гидрокрекинга, во-первых, присутствие растительного масла в смеси (как 5, так и 10 мас. %) практически не оказывает промотирующего действия на крекинг нефтяной фракции. Во-вторых, жирнокислотный состав растительного масла не влияет на распределение углеводородных продуктов крекинга. В-третьих, снижение содержания в смеси подсолнечного масла до 5 мас. % способствует увеличению образования бензиновой фракции по сравнению со смесью, содержащей 10 мас. %. При этом данные изменения происходят за счет снижения образования пропан-пропиленовой и бутан-бутиленовой фракций. Однако полученные значения выхода бензиновой фракции ниже, чем при крекинге чистого остатка гидрокрекинга.
Для негидроочищенного вакуумного газойля присутствие в смеси 10 мас. % растительного масла способствует увеличению конверсии. При этом установлено, что при использовании подсолнечного масла относительно высокое его содержание в смеси ведет к высокому выходу кокса. Это обусловлено образованием высокореакционных олефинов при термическом разложении растительного масла, которые активно вовлекаются в реакции циклизации с последующим дегидрированием. В результате, если снизить содержание подсолнечного масла в смеси до 5 мас. %, значение конверсии относительно превращения чистого негидроочищенного вакуумного газойля растет, выход бензина повышается, а значения выходов кокса сопоставимы.
Кислотные и текстурные характеристики образцов цеолитов, модифицированных фосфором
В табл. 5 приведены основные текстурные показатели исходных и модифицированных фосфором образцов цеолитов.
Таблица 5.
Основные текстурные и кислотные характеристики исследуемых образцов цеолитов из анализа изотерм адсорбции-десорбции азота
Образец | Удельная площадь поверхности, м2/г | Удельный объем пор, см3/г | Количество десорбирован-ного аммиака, мкмоль/г | |||
---|---|---|---|---|---|---|
SБЭТ | Sвн | Vадс | Vмезо-1 | Vмикро- | ||
HРЗЭY | 716 | 57 | 0.358 | 0.105 | 0.253 | 2131 |
P/HРЗЭY | 438 | 40 | 0.236 | 0.082 | 0.154 | 1460 |
HZSM-5 | 416 | 66 | 0.287 | 0.137 | 0.150 | 854 |
P/HZSM-5 | 127 | 10 | 0.103 | 0.057 | 0.046 | 282 |
В результате модификации как для цеолита Y, так и для ZSM-5 отмечается существенное изменение основных текстурных характеристик. Так, исходя из данных, представленных в табл. 5, модифицирование фосфором исходного HРЗЭY приводит к снижению значений удельной площади поверхности и удельного объема микропор. В то же время пористая структура ZSM-5 в ходе модифицирования претерпевает более существенные изменения. Так значения удельной площади поверхности и объема микропор уменьшаются более чем в 3 раза. Эти результаты согласуются с данными работы [15, 16], где авторы отмечали, что нанесение фосфора ведет к существенному снижению удельной площади поверхности и объема пор цеолита. Это происходит из-за формирования на внешней поверхности фосфатных соединений, которые частично блокируют входные окна каналов цеолитов. Необходимо отметить, что существенно большее относительное влияние фосфора на характеристики цеолита ZSM-5 связано с увеличенным мольным соотношением Р/Al данного цеолита по сравнению с цеолитом Y.
Введение фосфора в исходные цеолиты приводит к снижению их общей кислотности (табл. 5). Так, количество десорбированного аммиака для цеолита Y снижается в 1.5 раза, а для цеолита ZSM-5 в 3.0 раза при модификации фосфором. При этом необходимо учесть количество вводимого фосфора в цеолиты, как указывалось выше.
Совместный крекинг вакуумного газойля и подсолнечного масла на бицеолитных катализаторах, содержащих цеолиты, модифицированные фосфором
Результаты каталитических испытаний показывают, что модификация цеолитов фосфором ведет к снижению конверсии смесевого сырья с 75.6 мас. % для образца с исходными цеолитами до 67.1 мас. % для образца с цеолитным компонентом P/HРЗЭY/HZSM-5 и до 70.7 мас. % для образца с HРЗЭY/P/HZSM-5 (табл. 6). Это связано с тем, что при нанесении фосфора происходит уменьшение размера входных окон и каналов цеолитов из-за присутствия соединений фосфора. В результате это ведет к уменьшению вероятности проникновения больших молекул исходного сырья в поры цеолита и в итоге наблюдается падение конверсии.
Таблица 6.
Состав продуктов крекинга нефтяного сырья и смеси нефтяного сырья (90 мас. %) и растительного масла (10 мас. %) (температура – 450°С, катализатор : сырье – 4.0)
Продукты, мас. % | Образец 1 | Образец 2 | Образец 3 |
---|---|---|---|
HРЗЭY/HZSM-5 | P/HРЗЭY/HZSM-5 | HРЗЭY/P/HZSM-5 | |
Конверсия | 75.6 | 67.1 | 70.7 |
Газообразные продукты | 23.7 | 26.1 | 33.9 |
СО + СО2 | 1.1 | 0.9 | 1.2 |
С1−С2 | 1.0 | 0.9 | 2.5 |
ППФ в т.ч. пропилена |
8.1 6.6 |
9.5 8.3 |
12.6 10.5 |
ББФ в т.ч. бутиленов |
13.5 4.9 |
14.8 7.8 |
17.6 8.6 |
C3=/СумС3, % | 81.4 | 87.4 | 83.2 |
изо-С4/СумС4, % | 55.4 | 40.8 | 44.6 |
изо-С4=/СумС4=, % | 25.4 | 39.8 | 37.5 |
СумС4=/СумС4, % | 36.3 | 53.0 | 48.9 |
Жидкие продукты | 69.9 | 67.9 | 60.9 |
вода | 0.2 | 0.3 | 0.2 |
бензин | 45.3 | 34.7 | 31.4 |
легкий газойль | 18.7 | 19.7 | 18.3 |
тяжелый газойль | 5.7 | 13.2 | 11.0 |
Кокс | 6.4 | 6.0 | 5.2 |
Это обусловлено тем, что для бицеолитных катализаторов характерна следующая схема превращения сырья [17]: 1. матрица осуществляет первичный крекинг молекул исходного сырья; 2. крекинг на цеолите Y до углеводородов С7−С8; 3. вторичный крекинг бензиновой фракции на цеолите ZSM-5 до углеводородов С2−С4, где благодаря низкой активности реакций переноса водорода преобладают легкие олефины. Таким образом, для катализаторов, в состав которых входит модифицированный цеолит HРЗЭY, снижается возможность проникновения молекул, образовавшихся в результате первичного крекинга сырья на компонентах матрицы.
Одновременно со снижением конверсии смесевого сырья для образцов, содержащих модифицированные цеолиты, наблюдается снижение выхода бензина. Наиболее сильное уменьшение выхода бензиновой фракции отмечается для образца с цеолитом P/HZSM-5 – на 13.9 мас. %. В случае нанесения фосфора только на цеолит HРЗЭY выход бензина снижается на 10.6 мас. % по сравнению с немодифицированным образцом бицеолитного катализатора.
Анализ состава газов показывает, что при модифицировании цеолитов фосфором выход сухого газа увеличивается исключительно за счет повышения выхода этилена. Так выход этилена для бицеолитного образца с предварительно обработанным фосфором цеолитом HZSM-5 увеличивается с 0.5 до 1.9 мас. %. При этом необходимо отметить, что для образца с модифицированным только цеолитом HРЗЭY изменений в выходах как сухого газа, так и этилена практически не наблюдается.
Модифицирование цеолитов фосфором также влияет на суммарный выход пропан-пропиленовой и бутан-бутиленовой фракций. Для образца с модифицированным фосфором цеолитом HРЗЭY наблюдается увеличение суммарного выхода пропан-пропиленовой и бутан-бутиленовой фракций до 24.4 мас. %, т.е. на 2.8 мас. % по сравнению с немодифицированным образцом. Одновременно с этим отмечается увеличение доли олефинов в данных газовых фракциях. Так содержание пропилена в ППФ увеличивается до 87.4%, а содержание бутиленов в ББФ до 54.3%. В результате, несмотря на относительно небольшое повышение выхода ППФ и ББФ выход олефинов для данного образца бицеолитного катализатора увеличивается на 4.7 мас. %. Образец, содержащий цеолит ZSM-5 с нанесенным фосфором отличается увеличением выхода ППФ и ББФ: на 8.6 мас. %. Кроме того, отмечается увеличение содержания олефинов в данных фракциях, что ведет к росту выхода олефинов С3 и С4 с 11.5 (HРЗЭY/HZSM-5) до 19.1 мас. % (HРЗЭY/P/HZSM-5).
Снижение активности реакций переноса водорода в результате модификации цеолитов обуславливает увеличение выхода легких олефинов. Это связано с тем, что в результате введения фосфора снижается общая кислотность цеолита, а это в свою очередь ведет к уменьшению времени контакта между промежуточными соединениями и кислотными центрами (чем слабее кислотный центр, тем меньше время жизни карбений-иона для вторичных реакций, поэтому он быстро десорбируется в виде олефина [18]). Кроме того, диффузионные ограничения вызванные присутствием соединений фосфора в каналах цеолитов затрудняют протекание бимолекулярных реакций, к которым относятся реакции переноса водорода [15]. В результате этого наблюдается увеличение выхода легких олефинов.
Анализ данных табл. 7 показывает, что модификация только цеолита HРЗЭY в составе бицеолитного катализатора способствует повышению селективности образования пропилена и бутиленов. При этом значения селективности образования бензина снижаются. Как отмечалось выше, при модификации происходят изменения пористой структуры цеолитов, а также кислотных свойств, и как результат повышение селективности образования легких олефинов.
Таблица 7.
Значения селективности при крекинге смесевого сырья, %
Образцы катализаторов | Образец 1 | Образец 2 | Образец 3 |
---|---|---|---|
HРЗЭY/HZSM-5 | P/HРЗЭY/HZSM-5 | HРЗЭY/P/HZSM-5 | |
СО + СО2 | 1.4 | 1.3 | 1.7 |
С1–С2 | 1.3 | 1.3 | 3.5 |
ППФ в т.ч. пропилена |
10.7 8.7 |
14.2 12.4 |
17.8 14.9 |
ББФ в т.ч. бутиленов |
17.9 6.5 |
22.1 11.6 |
24.9 12.2 |
Вода | 0.3 | 0.4 | 0.3 |
Бензин | 59.9 | 51.8 | 44.4 |
Кокс | 8.5 | 8.9 | 7.4 |
Кроме того, необходимо отметить, что при модифицировании фосфором только цеолита HРЗЭY выход светлых продуктов снижается на 9.6 мас. % (рис. 6), а для образца, содержащего модифицированный цеолит HZSM-5, наблюдается снижение выхода светлых продуктов на 14.3 мас. %.
ЗАКЛЮЧЕНИЕ
Таким образом, при совместном превращении нефтяных фракций с растительными маслами не целесообразно использовать газойли с высоким содержанием парафино-нафтеновой фракции. В случае совместного крекинга вакуумных газойлей с высоким содержанием ароматических углеводородов содержание растительного масла с низким индексом непредельности (пальмовое масло) должно находиться в диапазоне 5–10 мас. %. При совместном крекинге вакуумного газойля с растительным маслом с высоким индексом непредельности (подсолнечное масло) его содержание в смеси не должно превышать 5 мас. %, т.к. при повышении его в смеси происходит повышение образования коксовых отложений на бицеолитном катализаторе при одновременном снижении выхода целевых продуктов крекинга.
Модифицирование цеолитов фосфором ведет к изменению их текстурных характеристик, в частности к снижению удельной площади поверхности, а также объема микропор. Это связано с частичной блокировкой входных окон и сужением каналов цеолитов из-за образующихся в результате модифицирования соединений фосфора. Кроме того, при нанесении фосфора отмечается снижение общей кислотности цеолитов.
При крекинге смеси гидроочищенного вакуумного газойля и подсолнечного масла определено, что модифицирование цеолитов ведет к повышению выхода олефинов С3 и С4 с 11.5 мас. %(образец с цеолитным компонентом HРЗЭY / HZSM-5) до 16.1 (P/HРЗЭY/HZSM-5) и 19.1 мас. % (HРЗЭY/P/HZSM-5). Это обусловлено, во-первых, тем, что при введении фосфора снижается сила кислотных центров цеолита, а чем слабее кислотный центр, тем меньше время жизни карбений-ионов для вторичных реакций, и они быстро десорбируются в виде олефинов. Во-вторых, диффузионные ограничения, возникающие от присутствия соединений фосфора в каналах цеолитов, препятствуют протеканию бимолекулярных реакций, к которым относятся реакции переноса водорода. При этом при пропитке фосфором цеолитов происходит снижение конверсии смесевого сырья. Наиболее сильное снижение отмечается для образца, содержащего цеолит P/HРЗЭY. Это связано с тем, что сужение пор при модифицировании фосфором приводит к снижению вероятности проникновения молекул, образовавшихся в результате первичного крекинга сырья на компонентах матрицы, в каналы цеолитов.
БЛАГОДАРНОСТИ
Работа выполнена в рамках государственного задания ИППУ СО РАН в соответствии с Программой фундаментальных научных исследований государственных академий наук на 2013–2020 годы по направлению V. 47, проект № V.47.1.3 (номер госрегистрации в системе ЕГИСУ НИОКТР AAAA-A17-117021450099-9).
Авторы выражают благодарность за помощь в выполнении данной работы сотрудникам Института проблем переработки углеводородов СО РАН Т.И. Гуляевой, В.П. Талзи и С.Н. Евдокимову.
Список литературы
Chew T.L., Bhatia S. // Bioresource Technology. 2009. V. 100. № 9. P. 2540.
Bielansky P., Reichhold A., Schönberger C. // Chemical Engineering and Processing. 2010. V. 49. № 8. P. 8730.
Doronin V.P., Potapenko O.V., Lipin P.V., Sorokina T.P. // Fuel. 2013. V. 106. P. 757.
Doronin V.P., Potapenko O.V., Lipin P.V., Sorokina T.P. // Catalysis in Industry. 2014. V. 6. № 1. P. 53.
Fan X., Burton R., Austic G. // Chemistry and Technology of Fuels and Oils. 2010. V. 46. № 5. P. 287.
Keshwani D.R., Cheng J.J. // Bioresource Technology. 2009. V. 100. № 4. P. 1515.
Guo F., Fang Z., Xu C.C., Smith Jr. R.L. // Progress in Energy and Combustion Science. 2012. V. 38. № 5. P. 672.
Заварухин С.Г., Стрельцов И.А., Яковлев В.А. // Кинетика и катализ. 2011. Т. 52. № 4. С. 510.
Сорокина К.Н., Яковлев В.А., Пилигаев А.В., Кукушкин Р.Г., Пельтек С.Е., Колчанов Н.А., Пармон В.Н. // Катализ в промышленности. 2012. № 2. С. 63.
Doronin V.P., Potapenko O.V., Lipin P.V., Sorokina T.P., Buluchevskaya L.A. // Petrol. Chemistry. 2012. T. 52. № 6. P. 392.
Blasco T., Corma A., Martínez-Triguero J. // J. Catal. 2006. V. 237. № 2. P. 267.
Rahimi N., Karimzadeh R. // Appl. Catal., A. 2011. V. 398. № 1–2. P. 1.
Ding J., Wang M., Peng L., Xue N., Wang Y., He M.-Y. // Appl. Catal., A. 2015. V. 503. P. 147.
Altynkovich E.O., Potapenko O.V., Sorokina T.P., Doronin V.P., Gulyaeva T.I., Talzi V.P. // Petrol. Chemistry. 2017. T. 57. № 3. P. 215.
van der Bij H.E., Weckhuysen B.M. // Chem. Society Reviews. 2015. V. 44. № 20. P. 7406.
Soh J.C., Chong S.L., Hossain Sk S., Cheng C.K. // Fuel Processing Technology. 2017. V. 158. P. 85.
Доронин В.П., Липин П.В., Потапенко О.В., Сорокина Т.П., Короткова Н.В., Горденко В.И. // Катализ в промышленности. 2014. № 5. С. 82.
Guisnet M., Gnep N.S., Aittaleb D., Doyemet Y.J. // Applied Catalysis A: General. 1992. V. 87. № 2. P. 255.
Дополнительные материалы отсутствуют.
Инструменты
Нефтехимия