Нефтехимия, 2019, T. 59, № 4, стр. 466-471
Особенности модифицирования цинком цеолитного катализатора конверсии диметилового эфира в синтетические жидкие углеводороды
З. М. Матиева 1, *, Н. В. Колесниченко 1, Ю. М. Снатенкова 1, С. Н. Хаджиев 1
1 Институт нефтехимического синтеза им. А.В. Топчиева РАН
Москва, Россия
* E-mail: mzm@ips.ac.ru
Поступила в редакцию 12.03.2019
После доработки 13.03.2019
Принята к публикации 14.03.2019
Аннотация
В присутствии катализаторов на основе цеолитов Zn-HZSM-5, полученных способами пропитки, ионного обмена из водного раствора азотнокислого цинка и in situ, осуществлен синтез жидких углеводородов (УВ) с пониженным содержанием ароматических соединений из диметилового эфира (ДМЭ) в среде водорода при температуре 340°С и давлении 10 МПа. Показано, что модифицирование цеолита H-ZSM-5 цинком вызывает уменьшение общего числа кислотных центров (КЦ) с повышением доли сильных льюисовских КЦ в общем спектре кислотности. Введение Zn в цеолит H-ZSM-5 методом in situ приводит к повышению доли мезопор, что позволяет устранить диффузионные затруднения. Эти факторы позволяют существенно повысить селективность по жидким УВ, содержание изо-алканов в их составе и значительно повысить стабильность работы катализатора на основе Zn-HZSM-5, полученного методом in situ.
Конверсия метанола и ДМЭ в УВ легла в основу создания процессов преобразования источников углерода в УВ и является одним из основополагающих процессом глубокой переработки природного газа, попутного нефтяного газа (ПНГ) и угля в моторное топливо и другие ценные нефтехимические продукты [1, 2]. Современные технологии превращения природного и попутного нефтяного газа в легко транспортируемые жидкие продукты позволяют перевести эти источники углерода в универсальный энергоресурс [3–7].
В последние годы в ИНХС РАН успешно разрабатывается процесс переработки синтез-газа любого состава в ДМЭ в одну стадию с последующим его превращением в смесь синтетических жидких УВ. Состав и технические характеристики получаемых из ДМЭ синтетических УВ определяются свойствами применяемого цеолитного катализатора и условиями проведения процесса, в т.ч. составом синтез-газа. Направленное регулирование кислотных свойств цеолитов со структурой MFI и состава исходного синтез-газа [8–10] позволяет получать по технологии ИНХС из метанола и ДМЭ продукты заданного качества – базовый компонент автобензина (высокооктановый продукт с ОЧИ не менее 90) и легкую бессернистую синтетическую нефть (смесь жидких УВ с низким содержанием ароматических соединений). Последний продукт пригоден по составу для транспортировки вместе с добываемой нефтью по трубопроводу, что позволяет решать проблему утилизации попутного нефтяного газа. Вместе с тем при смешении с высокооктановыми компонентами эта смесь может также использоваться в качестве автобензина.
Известно, что кислотные свойства цеолитов зависят от природы обменных катионов [11–20] и способа их введения [12, 14, 21–25].
В данной работе было изучено влияние способа введения катионов цинка (пропитка, ионный обмен, in situ) в состав цеолитного катализатора на его физико-химические и каталитические свойства в конверсии ДМЭ в смесь жидких УВ с низким содержанием ароматических соединений и повышенным содержанием изо-парафиновых УВ.
ЭКСПЕРИМЕНТАЛЬНАЯ ЧАСТЬ
Приготовление катализаторов. Для синтеза катализаторов получения из ДМЭ смеси жидких УВ с низким содержанием ароматических соединений был использован цеолит Н-ZSM-5 производства компании Zeolyst Int. (СBV 3024, мольное отношение SiO2/Al2O3 = 30). Катионы цинка вводили в состав цеолита из водного раствора (0.2 Н) азотнокислого цинка различными способами: ионным обменом при 80–90°C и пропиткой при комнатной температуре в течение 3 ч. Обработанные цеолиты высушивали и прокаливали в атмосфере воздуха при 500°С в течение 4 ч. В работе также использован образец Zn/ZSM-5, предоставленный компанией Zeolyst Int. (ZD 16025, мольное отношение SiO2/Al2O3 = 36), в котором катионы цинка введены в структуру цеолита на стадии его синтеза (in situ). Для получения экструдатов порошок модифицированного цеолита смешивали со связующим (оксид алюминия) в количестве 30% от массы катализатора (в расчете на абс. сухое вещество), после чего экструдаты провяливали на воздухе в течение 12 ч, сушили при 100°С в течение 12 ч и прокаливали при 500°С в течение 4 ч.
Характеристика катализаторов. Содержание цинка в образцах катализаторов определено с помощью элементного рентгеноспектрального флуоресцентного анализа (РСФА) на спектрометре Hirox EAGLE II.
Размер кристаллов определяли на основании снимков, полученных на сканирующем электронном микроскопе Hitachi TM3030, режимы съемки указаны на снимках. Перед съемкой на поверхность образцов наносили слой золота методом напыления в вакууме.
Дифрактограммы получены с помощью рентгеновского источника с вращающимся медным анодом Rotaflex RU-200 (Rigaku, Япония), режим работы источника 50 кВ–160 мА. Источник был оснащен горизонтальным широкоугольным гониометром Rigaku D/Max-RC, θ–2θ сканирование производилось по схеме Брэгга–Брентано. Диапазон измерения углов дифракции – 3°–50° по 2θ, измерение вели в режиме непрерывного сканирования со скоростью 1°/мин и шагом 0.04°. В качестве детектора дифрагированного рентгеновского излучения выступал сцинтилляционный счетчик, падающее на него излучение монохроматизировалось с помощью вторичного (т.е. стоявшего на отраженном от образца пучке) фокусирующего монохроматора – изогнутого монокристалла графита. Длина волны монохроматизированного излучения составляла 1.542 Å. Расчет степени кристалличности проводили по уравнению Шеррера [26].
Методом низкотемпературной адсорбции−десорбции молекулярного азота изучены текстурные свойства цеолитов. Исследование осуществляли на установке Autosorb-1-MP (Quantachrome Instruments). Предварительно все образцы были вакуумированы при температуре 300°С до 4 × 10–1 Па. Адсорбцию N2 проводили при температуре 77 K. Удельную поверхность рассчитывали по БЭТ при относительном парциальном давлении Р/Р0 = 0.2; распределение размера пор – по десорбционной кривой методом BJH (Баррета–Джойнера–Халенды); общий объем пор определяли методом BJH при относительном парциальном давлении Р/Р0 = 0.95. Для определения удельной площади и объема микропор использовали метод Астахова–Дубинина.
Кислотные свойства цеолитов изучены методом термопрограммированной десорбции аммиака (ТПД-NH3) на приборе УСГА-101 производства компании “УНИСИТ”. Предварительно прокаленный на воздухе образец в количестве 100 мг помещали в кварцевый реактор. Его прогревали в токе гелия при температуре 500°С в течение 1 ч. После охлаждения образца до температуры 60°С проводили его насыщение в токе аммиака в смеси с азотом в течение 15 мин. Удаление слабо связанного аммиака проводили при 70°С в токе сухого гелия в течение 1 ч, после чего образец быстро охлаждали до комнатной температуры, и, пропуская через образец ток гелия (30 мл/мин), регистрировали кривые ТПД-NH3 в режиме линейного подъема температуры до 800°С со скоростью 8°/мин. В качестве детектора использовался катарометр.
Для исследования природы кислотных центров использован метод ИК-спектроскопии пиридина. ИК-спектры регистрировали на ИК-Фурье спектрометре PE100. Образцы дегидратировали при 400°С в течение 3 ч в вакууме 1.33 × 10–3 Па. Адсорбцию пиридина проводили при комнатной температуре путем напуска через систему кранов на образец в течение 15 мин. Затем образец продували гелием при 150°С в течение 0.5 ч. Десорбцию пиридина проводили при температуре 150–400°С и регистрировали ИК-спектры оставшегося на поверхности пиридина.
Относительное количество КЦ Бренстеда и Льюиса оценивали в диапазоне 1400–1600 см–1 ИК-спектров, используя интегральные молярные коэффициенты поглощения, представленные в [27]. Полосы при 1450 и 1540 см–1 соотносят к пиридину, адсорбированному на льюисовских и брестедовских центрах соответственно.
Методика проведения испытаний. Синтез жидких УВ проводили в непрерывном режиме в течение 72 ч на микропилотной проточно-циркуляционной установке при температуре 340°С, давлении 10 МПа и массовой скорости подачи ДМЭ (WДМЭ) 2.7 ч–1 в среде водорода согласно методике, приведенной в [28]. Анализ отходящих газов и смеси жидких УВ, а также расчет конверсии ДМЭ и селективности по жидким УВ проводили согласно [29].
Настоящая работа проводится в рамках разрабатываемого процесса переработки синтез-газа любого состава в ДМЭ с последующим его превращением в смесь синтетических жидких УВ. Процесс осуществляется на микропилотной установке высокого давления, состоящей из двух реакторов – синтеза оксигенатов из синтез-газа и синтеза УВ из оксигенатов; давление процесса 10 МПа. При этом реакторы могут работать, как в автономном режиме, независимо друг от друга, так и совместно в едином циркуляционном контуре. В зависимости от источника и способа получения (паровой риформинг или парциальное окисление метана ПНГ, производство биогаза) синтез-газ, поступающий на стадию синтеза ДМЭ, характеризуется различным соотношением Н2/СО. При использовании на стадии получения ДМЭ синтез-газа с отношением Н2/СО ≥ 3.5 (соответствует составу газа, получаемому паровым риформингом метана) на стадию синтеза жидких УВ поступает парогазовая смесь с отношением Н2/СО ≥ 90, поэтому для удобства при проведении процесса получения из ДМЭ жидких УВ в качестве сопутствующего газа был использован водород.
РЕЗУЛЬТАТЫ И ИХ ОБСУЖДЕНИЕ
В табл. 1 представлены данные по содержанию цинка в образцах цеолитных катализаторов, степени их кристалличности и текстурным характеристикам. По данным низкотемпературной адсорбции азота показано, что введение цинка приводит к незначительному уменьшению активной поверхности в большей степени для образцаов, полученного методом пропитки и прямого синтеза, что может быть связано с меньшей доступностью внутренней поверхности микропор из-за большего содержания цинка в пропиточном образце и возможного расположения катионов цинка в каналах цеолита для образца, полученного прямым синтезом. Наибольшие величины общего объема пор и объема мезопор показал образец, полученный прямым синтезом. Полученные данные согласуются с результатами адсорбции бензола. Судя по значению предельной величины адсорбции бензола, наибольшей адсорбционной емкостью обладает образец, полученный введением катионов цинка в структуру цеолита in situ.
Таблица 1.
Данные адсорбции азота образцов Zn-HZSM-5
Образец | [Zn], мас. % (РСФА) | Степень кристал- личности, % (РФА) | SВЕТ, м2/г | Vпор, см3/г | Vмикропор, см3/г | VмезопорBJH, см3/г | Адсорбция бензола ±10 мкмоль/г |
---|---|---|---|---|---|---|---|
Исходный | – | 99 | 321 | 0.257 | 0.127 | 0.130 | 125 |
Пропитка | 2.00 | 99 | 303 | 0.227 | 0.114 | 0.113 | 109 |
Ионный обмен | 1.96 | 97 | 313 | 0.250 | 0.117 | 0.133 | 121 |
in situ | 2.03 | 98 | 309 | 0.260 | 0.113 | 0.143 | 129 |
По данным СЭМ (микрофотографии представлены на рис. 1), частицы порошкообразных цеолитов Zn-HZSM-5, полученных in situ и ионным обменом, практически не отличаются по размеру кристаллов (800–1000 нм).
Рис. 1.
Микроснимки использованных цеолитов: (a) Zn-HZSM-5, полученный in situ; (б) Zn-HZSM-5, полученный ионным обменом.
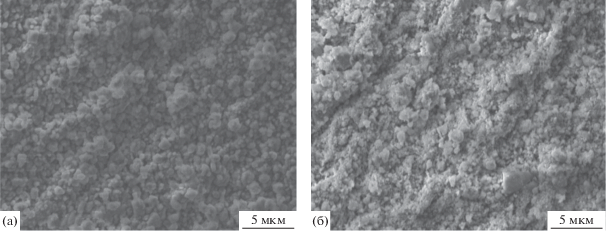
Результаты исследования кислотных свойств образцов катализаторов приведены в табл. 2 и 3. По данным ТПД-NH3 (табл. 2), позволяющей получить информацию об общем количестве кислотных центров и их распределении по силе, для всех образцов введение цинка в цеолит приводит к снижению общего числа адсорбционных центров за счет центров обоих типов. При этом отмечено повышение доли слабых и средних по силе кислотных центров в общем спектре кислотности.
Таблица 2.
Кислотные характеристики Zn-HZSM-5
Образец | N∑, мкмоль/г | Tmax1, °С | Tmax2, °С | N, мкмоль/г | NII /NI | |
---|---|---|---|---|---|---|
NI | NII | |||||
Исходный | 1130 | 200 | 415 | 589 (52%) | 541 (48%) | 0.91 |
Пропитка | 920 | 210 | 415 | 500 (54%) | 420 (46%) | 0.84 |
Ионный обмен | 825 | 215 | 418 | 485 (59%) | 340 (41%) | 0.70 |
in situ | 815 | 210 | 422 | 430 (53%) | 385 (47%) | 0.89 |
Таблица 3.
Данные ИК-спектров пиридина
Образец | БКЦ, мкмоль/г | ЛКЦ, мкмоль/г | ЛКЦ/ БКЦ | ЛКЦ + + БКЦ | ||||||
---|---|---|---|---|---|---|---|---|---|---|
всего | слабые | средние | сильные | всего | слабые | средние | сильные | |||
Исходный | 113.4 | 17.3 | 6.7 | 89.4 | 9.1 | 5.9 | 2.0 | 1.2 | 0.1 | 122.5 |
Пропитка | 69.6 | 6.6 | 13.0 | 50.0 | 43.5 | 17.7 | 7.9 | 17.8 | 0.6 | 113.1 |
Ионный обмен | 59.9 | 5.6 | 13.8 | 40.5 | 51.7 | 16.2 | 10.9 | 24.6 | 0.9 | 111.6 |
in situ | 16.2 | 6.2 | 5.4 | 4.5 | 70.9 | 20.4 | 22.9 | 27.6 | 4.4 | 87.1 |
Полученные данные согласуются с результатами ИК-спектроскопии адсорбированного пиридина (табл. 3), согласно которым при введении цинка в HZSM-5 происходит понижение общего количества кислотных центров от 122.5 до 87.1 мкмоль/г. По данным ИК-спектроскопии пиридина, позволяющей различать природу КЦ, введение цинка в HZSM-5 приводит к уменьшению концентрации бренстедовских КЦ (БКЦ), при взаимодействии с которыми катионы цинка генерируют [ZnOH]+–льюисовские КЦ (ЛКЦ). Отмечено. что характер распределения КЦ различных типов в общем спектре кислотности и их соотношение находится в зависимости от метода введения цинка. Образец, полученный прямым синтезом, отличается равномерным распределением слабых, средних и сильных бренстедовских и льюисовских КЦ и максимальным значением отношения ЛКЦ к БКЦ. Результаты опытов согласуются с литературными данными [21, 22, 30, 31].
Катализаторы, полученные на основе модифицированных цеолитов, были испытаны в конверсии ДМЭ в жидкие УВ на микропилотной установке. Результаты испытаний (табл. 4) показали высокую активность (более 98%) и селективность (более 80 мас. % от суммы УВ) для всех модифицированных образцов. Введение цинка в состав цеолита приводит к повышению содержания изо-парафиновых УВ в составе получаемого продукта. Наиболее эффективным оказался катализатор, в состав которого цинк был введен на стадии синтеза цеолита. Образец показал селективность по жидким УВ (SC5+) более 91 мас. % и повышенное содержание изо-алканов (78.5 мас. %) в составе жидких УВ. На этом образце также отмечено минимальное содержание ароматических соединений в составе получаемого продукта (не более 5.0 мас. %, в т.ч. дурола, нежелательного компонента любого топлива, не более 0.4 мас. %). Аналогичные результаты получены в работах [21, 22, 30–32], согласно которым образцы, полученные введением цинка ионным обменом и на стадии синтеза цеолита в сравнении с образцами, полученными пропиткой, показывают более высокие значения по конверсии метанола и селективности по жидким УВ.
Таблица 4.
Влияние способа введения катионов цинка в состав катализатора на конверсию ДМЭ в жидкие УВ. Данные приведены для испытаний катализатора в течение 24 ч
Образец | SC5+, мас. % | Состав бензина, мас. % | ||||
---|---|---|---|---|---|---|
изо-алканы | н-алканы | нафтены | олефины | арены (в т.ч. дурол) | ||
Исходный | 73.5 | 65.5 | 15.0 | 11.5 | 1.5 | 6.5 (0.7) |
Пропитка | 79.5 | 71.0 | 10.5 | 9.0 | 1.0 | 7.5 (0.7) |
Ионный обмен | 85.5 | 74.0 | 8.5 | 9.0 | 1.0 | 7.5 (0.5) |
in situ | 91.5 | 78.5 | 6.0 | 9.5 | 1.0 | 5.0 (0.4) |
Сопоставление физико-химических и каталитических свойств Zn-содержащих катализаторов (табл. 5) показывает, что образование цинк-содержащих центров приводит к повышению активности в образовании жидких УВ. При этом на катализаторе, полученном in situ, понижается содержание н-алканов и ароматических соединений. Как известно из литературы [21, 22, 30–32], при введении цинка на стадии синтеза цеолита повышается доля [ZnOH]+– сильных ЛКЦ, что приводит к уменьшению содержания н-алканов в составе получаемой смеси жидких УВ. Как полагают авторы, это происходит в связи с уменьшением скорости реакции переноса водорода между карбокатионами и алкенами.
Таблица 5.
Сопоставление кислотных и каталитических свойств
Образец | Адсорбция пиридина, мкмоль/г | SC5+, мас. % | Состав бензина, мас. % | ||||||
---|---|---|---|---|---|---|---|---|---|
БКЦ + ЛКЦ | БКЦ | ЛКЦ | ЛКЦ/ БКЦ | сильные/ средние (ЛКЦ) | изо-алканы | н-алканы | аром. УВ | ||
Исходный | 122.5 | 113.4 | 9.1 | 0.1 | 0.5 | 73.5 | 65.5 | 15.0 | 6.5 |
Пропитка | 113.1 | 69.6 | 43.5 | 0.6 | 2.25 | 79.5 | 71.0 | 10.5 | 7.5 |
Ионный обмен | 111.6 | 59.9 | 51.7 | 0.9 | 2.3 | 85.5 | 74.0 | 8.5 | 7.5 |
in situ | 87.1 | 16.2 | 70.9 | 4.4 | 1.2 | 91.5 | 78.5 | 6.0 | 5.0 |
Таким образом, полученные результаты показали, что введение цинка in situ в состав катализатора приводит не только к повышению объема мезопор, снимающее диффузионные затруднения, но и обусловливает изменение кислотных свойств с перераспределением кислотных центров, что сказывается на активности и селективности катализаторов.
Для определения перспективности промышленного использования катализаторов в химическом процессе наряду с основными показателями необходима оценка стабильности активного компонента и всего контакта на микропилотных, лабораторных и пилотных установках. Определение стабильности гетерогенных катализаторов, в конечном счете, определяется в результате длительной эксплуатации на промышленной установке, приводящей обычно к необратимой дезактивации. На лабораторном уровне выявить процессы дезактивации катализатора легче всего при высокотемпературной обработке водяным паром, т.к. при такой обработке в максимальной степени проявляется изменение структуры и фазового состояния цеолитного компонента [33].
Для определения стабильности каталитических свойств образец, полученный прямым синтезом, был подвергнут термопаровой обработке при 500°С в течение 4-х ч. Результаты испытания показали. что катализатор после процедуры ускоренного старения сохраняет основные показатели своей работы (рис. 2).
Таким образом, полученные результаты показали, что введение цинка in situ в состав катализатора позволяет существенно повысить селективность по жидким УВ и содержание изо-алканов в их составе. При этом катализатор обладает высокой стабильностью работы.
ЗАКЛЮЧЕНИЕ
В присутствии катализаторов на основе цеолитов Zn-H-ZSM-5, полученных способами пропитки, ионного обмена из водного раствора азотнокислого цинка и прямого синтеза in situ, осуществлен синтез жидких УВ с пониженным содержанием ароматических соединений из ДМЭ в среде водорода при температуре 340°С и давлении 10 МПа. Показано, что введение Zn в цеолит H-ZSM-5 методом прямого синтеза приводит к повышению доли мезопор, что позволяет устранить диффузионные затруднения. Модифицирование цеолита H-ZSM-5 цинком вызывает уменьшение общего числа КЦ для всех образцов с повышением доли слабых КЦ и КЦ средней силы в общем спектре кислотности. При этом отмечено повышение в спектре доли кислотности, образовавшихся в результате модифицирования сильных ЛКЦ в образцах, полученных методом пропитки и ионного обмена. Введение цинка in situ в состав катализатора позволяет существенно повысить селективность по жидким УВ и содержание изо-алканов в их составе и значительно повысить стабильность его работы.
Список литературы
Wood D. // Oil & Gas J. 2007. № 12. P. 20.
Арутюнов В.С. // Катализ в промышленности. 2008. № 1. С. 51.
Simonetti D.A., Carr R.T., Iglesia E. // J. of Catalysis. 2012. № 285. P. 19.
Hazari N., Labinger J.A., Scott V.J. // J. of Catalysis. 2009. № 263. P. 266.
Ahn J. H., Temel B., Iglesia E. // Angewandte Chemie. 2009. № 121. P. 3872.
Simonetti D.A., Ahn J.H., Iglesia E. // J. of Catalysis. 2011. №. 277. P. 173.
Хаджиев С.Н., Магомедова М.В., Пересыпкина Е.Г. // Нефтехимия. 2016. Т. 56. № 3. С. 198.
Букина З.М., Ионин Д.А., Колесниченко Н.В., Куоумбегов Н.В., Маркова Н.А., Хаджиев С.Н. // Пaтeнт PФ № 2442650. 2012.
Букина З.М., Графова Г.М., Ионин Д.А., Колесниченко Н.В., Лин Г.И., Маркова Н.А., Хаджиев С.Н. // Пaтeнт PФ № 2442767. 2012.
Пaтeнт PФ № 2616981. 2017.
Conte M. // Catalysis Science and Technology. 2012. № 2. P. 105.
Lee K.Y., Lee S.W., Ihm S.K. // J. of Industrial and Engineering Chemistry. 2014. № 53. P. 10072.
Mentzel U.V. // Applied Catalysis A: General. 2012. № 417–418. P. 290.
Meng F., Wang X., Wang S., Wang Y. // Catalysis Today. 2017. № 298. P. 226.
Bjørgen M., Joensen F., Holm M.S., Olsbye U. // Applied Catalysis A: General. 2008. № 345. P. 43.
Rac V., Rakic V., Miladinovic Z. // Thermochimica Acta. 2013. № 567. P. 73.
Van der Bij H.E., Aramburo L.R., Arstad B. // ChemPhysChem. 2014. № 15. P. 283.
Rahmani F., Haghighi M., Estifaee P. // Microporous and Mesoporous Materials. 2014. № 185. P. 213.
Zaidi H.A., Pant K.K. // Korean J. of Chemical Engineering. 2005. № 22. P. 353.
Zaidi H.A., Pant K.K. // Catalysis Today. 2004. № 96. P. 155.
Niu X., Gao J., Miao Q., Dong M. // Microporous and Mesoporous Materials. 2014. № 197. P. 252.
Ono Y., Adachi H., Senoda Y. // J. of the Chemical Society, Faraday Transactions. 1988. №1. V. 84. P. 109.
Ni Y., Sun A., Wu X., Hai G. // Microporous and Mesoporous Materials. 2011. № 143. P. 435.
Centi G., Perathoner S., Arrigo R., Giordano G. // Applied Catalysis A: General. 2006. № 307. P. 30.
Palin L., Lamberti C., Kvick A., Testa F. // J. of Physical Chemistry B. 2003. № 107. P. 4034.
Song W., Justice R.E., Jones C.A., Grassian V.H., Larsen S.C. // Langmuir. 2004. № 20. P. 8301.
Emeis C.A. // J. of Catalysis. 1993. № 141. P. 347.
Колесниченко Н.В., Букина З.М., Китаев Л.Е., Курумов С.А., Пересыпкина Е.Г., Хаджиев С.Н. // Нефтехимия. 2016. Т. 56. № 6. С. 621.
Ke Zhang, Курумов С.А., Xiaofang Su, Снатенкова Ю.М., Букина З.М., Колесниченко Н.В., Wei Wu, Хаджиев С.Н. // Нефтехимия. 2017. Т. 57. № 6. С. 656.
Wang Z., He T., Qin J. // Fuel. 2015. № 150. P. 386.
Asaftei I., Bilba N., Birsa L.M. // Acta Chemica IASI. 2009. № 17. P. 5.
Pinilla-Herrero I., Borfecchia E., Mentzel U.V., Olsbye U. // J. of Catalysis. 2018. № 362. P. 146.
Кубасов А.А., Горелик Д.Б., Гайрбекова С.М., Хаджиев С.Н., Топчиева К.В. // Журн. физ. химии. 1976. Т. 50. № 4. С. 1062.
Дополнительные материалы отсутствуют.