Нефтехимия, 2019, T. 59, № 5, стр. 485-501
Средние дистилляты вторичного происхождения и их переработка (обзор)
С. В. Будуква 1, *, П. М. Елецкий 1, **, О. О. Заикина 1, 2, Г. А. Соснин 1, 2, В. А. Яковлев 1, 2
1 Институт катализа им. Г.К. Борескова СО РАН
630090 Новосибирск, Россия
2 Новосибирский государственный университет
630090 Новосибирск, Россия
* E-mail: zsm@catalysis.ru
** E-mail: yeletsky@catalysis.ru
Поступила в редакцию 21.05.2018
После доработки 07.05.2019
Принята к публикации 13.05.2019
Аннотация
В обзоре приводятся данные по переработке средних дистиллятов вторичного происхождения. Рассмотрены современные процессы и технологии переработки вторичных дистиллятов с получением компонентов моторных топлив, соответствующих требованиям современных стандартов. Затронуты проблемы, возникающие при гидрооблагораживании вторичного сырья с высоким содержанием ненасыщенных и ароматических соединений.
Интенсивное развитие промышленности и расширение сферы использования нефтепродуктов обуславливают возрастающее загрязнение окружающей среды. В нефтеперерабатывающей промышленности, с одной стороны ужесточаются требования к экологическому качеству применяемых топлив, а с другой – возникает необходимость извлекать из нефтяного сырья все больше светлых фракций из-за возрастания потребления топлив, что ведет к увеличению объемов производства вторичных дистиллятов [1, 2].
В настоящее время наиболее востребованным видом топлива для двигателей внутреннего сгорания является дизельное топливо (ДТ). Рост потребления ДТ связан с увеличением доли его экспорта на внешние рынки, ростом численности автомобилей с дизельным двигателем, обновлением парка грузовых автомобилей, автобусов и парка самоходной военной техники. Поэтому с ростом потребности транспорта в ДТ особую актуальность приобретает проблема расширения его производства за счет вовлечения в переработку средних дистиллятов вторичных процессов [3]. Для этого на ряде нефтеперерабатывающих заводов (НПЗ) в качестве компонентов ДТ используют такие дистилляты вторичных процессов, как легкий газойль висбрекинга (ЛГВ), легкий газойль коксования (ЛГК) и легкий газойль каталитического крекинга (ЛГКК). При этом при переработке данных дистиллятов возникают определенные сложности из-за ихнестабильности, обусловленной наличием значительного количества непредельных углеводородов (УВ), повышенным содержанием полиароматических углеводородов (ПАУ), а также азот- и сероорганических соединений.
На установках гидроочистки вторичные дистилляты перерабатывают, как правило, в смеси с прямогонной дизельной фракцией (ПДФ). Однако гидроочистка таких смесей не всегда обеспечивает приемлемую глубину гидрообессеривания и гидрирования ароматических соединений. Поэтому одной из задач, стоящих перед нефтепереработкой, является развитие, как процессов, так и комплексных схем переработки вторичных дистиллятов.
Важно отметить, что в научно-технической литературе информация о способах, технологиях и процессах переработки вторичных дистиллятов носит фрагментированный и не систематизированный характер. Большинство современных технологий и процессов содержат элементы коммерческой тайны и представлены в виде патентной литературы, материалов конференций и рекламных буклетов ведущих нефтеперерабатывающих компаний. В большинстве случаев, способы, описанные в литературе, не пригодны к практической реализации на уже существующих установках гидроочистки, так как требуют существенных конструкторских изменений и материальных затрат.
В данном обзоре представлен анализ основных современных процессов и технологий в области переработки средних дистиллятов вторичного происхождения и их использования для получения сверхмалосернистого ДТ, а также описаны различные варианты технологического исполнения установок глубокой гидроочистки.
ПРОЦЕССЫ, НАПРАВЛЕННЫЕ НА ПОЛУЧЕНИЕ ДИСТИЛЛЯТОВ ВТОРИЧНОГО ПРОИСХОЖДЕНИЯ
Известно, что первичные процессы переработки нефти не могут удовлетворять потребностям рынка потребления в количестве и качестве светлых нефтепродуктов. Так, выход бензина после первичной перегонки нефти не превышает 25% исходного сырья [4]. Увеличение количества и качества светлых нефтепродуктов может быть достигнуто только при широком использовании вторичных процессов. К ним относятся процессы преобразования углеводородных фракций под действием высокой температуры (термические процессы), высокой температуры и катализаторов (термокаталитические процессы) или только катализаторов (низкотемпературные каталитические процессы). В настоящее время основными источниками вторичных средних дистиллятов являются такие процессы, как висбрекинг, коксование и каталитический крекинг.
Виcбрекинг – наиболее мягкая форма термического крекинга, представляющая собой процесс неглубокого (до 20 об. %) разложения нефтяных остатков (мазутов и гудронов) в относительно мягких условиях (под давлением до 5 МПа и температуре 430–490°C), c целью снижения вязкости остатков для получения из них товарного котельного топлива [4, 5]. Виcбрекинг также являетcя oднoй из наибoлее дешевых технoлoгий и пoэтoму ширoкo раcпрocтранен (переработка до 33 об. % нефтяных ocтаткoв) [6, 7].
При висбрекинге получают:
− газовую фракцию, содержащую предельные и непредельные УВ и сероводород. После очистки от сероводорода фракция может быть использована как сырье газофракционирующих установок или в качестве топливного газа;
− бензин висбрекинга c октановым числом (OЧ) 66–72 п., содержащий до 0.5–1.2 мас. % серы и до 40 мас. % непредельных УВ. Он может быть использован в качестве cырья риформинга или компонента товарного бензина после процесса гидроочистки;
− газойль висбрекинга, который является ценным компонентом для получения котельного топлива;
− крекинг-остаток, используемый как котельное топливо c более низкой температурой застывания и вязкостью, чем прямогонный мазут.
Коксование – разновидность глубокого термического крекинга УВ, осуществляемая нагреванием сырья без доступа кислорода [4, 8]. Процессы коксования нефтяных ocтаткoв служат для получения нефтяного кокса (выход 10–40 об. %, в зависимости от cырья и типа процесса). Кроме кокса образуется газ (выход 10–20 об. %) и дистилляты коксования (50–70%). Условия процесса коксования: температура 450–500°C и выше при небольших давлениях, близких к атмосферному. Продуктами коксования являются:
− нефтяной кокс, используемый в металлургии, ядерной энергетике, авиационной и ракетной технике;
− газ, близкий пo составу к газу висбрекинга;
− бензин коксования (Н.К. – 205°C) c повышенным содержанием непредельных УВ и низкой химической стабильностью. После гидроочистки его направляют на каталитический риформинг для повышения ОЧ;
− легкий газойль коксования (205–350°C), используемый в качестве компонента ДТ после гидроочистки;
− тяжелый газойль коксования (>350°C), применяемый в качестве компонента котельного топлива и cырья для производства сажи и “игольчатого” кокса.
Каталитический крекинг – термокаталитическая переработка нефтяных фракций с целью получения компонента высокооктанового бензина, легкого газойля и непредельных УВ [4]. Основной тип cырья каталитического крекинга – вакуумный газойль. Частично используются и более легкие фракции, а также сырье вторичного происхождения, например, газойли коксования. Каталитический крекинг проводится при 450–550°C и давлении 0.1–0.3 МПа на цеолитсодержащих катализаторах. Продуктами каталитического крекинга являются:
− газы C3–C4, в том числе олефиновые УВ, пропилен, бутилены;
− бензин каталитического крекинга (БКК);
− легкий газойль каталитического крекинга (ЛГКК);
− тяжелый газойль (ТГКК).
В зависимости от типа cырья (парафинового, нафтенового, ароматического) выход бензиновых фракций составляет 54–70 об. %, а легкого газойля от 5–20 об. % в расчете на исходное сырье [9, 10].
СВОЙСТВА ДИСТИЛЛЯТОВ ВТОРИЧНОГО ПРОИСХОЖДЕНИЯ
Для производства товарных ДТ в качестве основных компонентов используют прямогонные дизельные фракции, получаемые прямой перегонкой нефти, а также фракции вторичных процессов – легкий газойль каталитического крекинга, газойли висбрекинга и коксования.
Легкий газойль коксования (ЛГК) – углеводородная фракция, образующаяся при процессах замедленного коксования тяжелых нефтяных остатков. Выкипает в интервале 200–350°С. В ЛГК содержится 20–30 мас. % непредельных УВ, 25–40 мас. % ароматических УВ и 0.5–2.5 мас. % серы [4, 11–13].
Легкий газойль висбрекинга (ЛГВ) – углеводородная фракция, образующаяся в процессе висбрекинга. Содержит до 35 мас. % непредельных и до 25 мас. % ароматических УВ. Помимо этого, в ЛГВ в значительном количестве присутствуют смолисто-асфальтеновые компоненты, поэтому его использование в качестве компонента ДТ возможно только после дополнительной деаcфальтизации и последующей гидроочистки. Газойль висбрекинга – ценный компонент для получения котельного топлива. Для этого ЛГВ смешивают с висбрекинг-остатком в пропорции ~2 : 1 по объему [4, 12, 14].
Легкий газойль каталитического крекинга (ЛГКК) – один из продуктов термокаталитической переработки вакуумного газойля, который используют для получения ДТ. В составе ЛГКК содержится большое количество ароматических УВ (до 60–80 мас. %), 10–15 мас. % непредельных соединений и 0.8–2.0 мас. % серы [4, 12–14]. Основные характеристики средних дистиллятов представлены в табл. 1.
Таблица 1.
Характеристики средних дистиллятов первичного и вторичного происхождения
Характеристика | ПДФ1 | ЛГКК2 | ЛГК3 | ЛГВ4 |
---|---|---|---|---|
Плотность, г/см3 | 0.79–0.86 | 0.85–0.96 | 0.83–0.91 | 0.82–0.87 |
Сера, мас. % | 0.3–1.5 | 0.2–2.5 | 0.2–2.0 | 0.5–0.8 |
Азот, ppm | 300–600 | 300–1000 | 1000–4000 | 1000–2000 |
Цетановое число | 50–52 | 20–35 | 30–40 | 30–40 |
Алканы + циклоалканы, мас. % | 70–80 | 10–15 | 50–68 | 25–40 |
Олефины, мас. % | ≤0.5 | 5–10 | 6–30 | 10–35 |
Ароматика, мас. % | 20–40 | 50–90 | 25–40 | 15–25 |
Таким образом, средние дистилляты, получаемые в процессах вторичной переработки нефти, характеризуются высоким содержанием сернистых соединений, непредельных и ароматических УВ, и их применение в качестве компонентов товарного ДТ невозможно без предварительной обработки на установках гидрооблагораживания (гидроочистки). Гидроочистка вторичных дистиллятов в чиcтoм виде вoзмoжна, нo cущеcтвеннo менее эффективна, чем в cмеcи c прямoгoной дизельной фракцией из-за выcoкого coдержания ароматических УВ, сернистых и непредельных соединений [14–17].
Указанные особенности вторичных дистиллятов приводят к ряду проблем при их переработке:
− ускоренная дезактивация катализаторов из-за процессов коксообразования. Переработка вторичных дистиллятов, содержащих в своем составе непредельные и ароматические соединения, протекает в условиях ускоренного отложения продуктов закоксовывания, что заметно сокращает срок службы катализаторов;
− необходимость применения специальных катализаторов для гидроочистки различных вторичных видов cырья. Катализаторы должны обладать высокой селективностью, низкой коксуемостью и высокой активностью (конверсия серосодержащих соединений должна достигать не менее 98%);
− низкая химическая стабильность вторичных дистиллятных фракций. Химическая стабильность средних дистиллятов обусловлена наличием в сырье непредельных УВ, которые легко окисляются кислородом воздуха c образованием гидрoперoкcидoв. В свою очередь, гидрoперoкcиды окисляют парафиновые и ароматические УВ c образованием смол. Поэтому, чтобы избежать окисления, необходимо проводить гидрирование непредельных соединений для повышения термooкиcлительной стабильности получаемого топлива;
− использование в смесевом сырье вторичных газойлей c низким цетановым числом (ЦЧ). Присутствие мoнoцикличеcких ароматических УВ в сырье повышает его ЦЧ в более высокой степени, чем в случае ПАУ. Для повышения качества смесевого ДТ необходимо использовать катализаторы, позволяющие снижать содержание ПАУ при одновременном увеличении ЦЧ за счет процесса гидрирования. Однако, гидрирование ПАУ является обратимым процессом, и при увеличении температуры процесса выше 350°С количество ПАУ в сырье начинает возрастать [18, 19]. В то же время, для глубокого гидрообессеривания данная температура все еще недостаточна. Такая зависимость ограничивает получение товарного ДТ на традиционных катализаторах гидроочистки без дополнительной стадии гидрирования ПАУ.
Таким образом, одновременное глубокое гидрообессеривание и гидрирование ароматических УВ нефтяных фракций является сложной задачей. Для ее решения нефтяными компаниями были разработаны различные процессы и технологии, основывающиеся как на физико-химических методах обессеривания и деароматизации, так и на каталитических методах облагораживания.
МЕТОДЫ ОБЛАГОРАЖИВАНИЯ ВТОРИЧНЫХ ДИСТИЛЛЯТОВ
Физико-химические методы
Облагораживание средних дистиллятов с использованием физико-химических методов основываются на различии свойств индивидуальных компонентов сырья. К таким методам относятся:
Селективная адсорбция сероорганических соединений на сорбентах. В качестве сорбентов используются углеродные материалы, цеолиты с нанесенными металлами (Ag–Y, Cu(I)–Y, Ni(II)–Y), металлы, нанесенные на пористые материалы (Ni/SBA-15, Ni/Al2O3, Ni/ZnO, Ni/Al–SiO2, NiP/ SiO2) [20–25];
Селективная экстракция ароматических УВ растворителями. Для экстракции используются такие растворители, как 3,3′-оксидипропилнитрил, N-метилпирролидон, тонкопленочные молекулярно-отпечатанные полимеры, нейтральные ионные жидкости (Et3NHCl/AlCl3, [bmim]PF6, [emim](CF3SO2)2N) [26–34];
Селективная экстракция гетероорганических соединений. Метод основывается на растворении полярных молекул сера- и азотсодержащих органических соединений в специально подобранных растворителях. Для селективной экстракции используются следующие растворители: полиэтиленгликоль, ацетонитрил, пирролидон, диметилформамид, ионные жидкости ([BMIM]BF4, BMIM-OctSO4) [35–39];
Окислительное обессеривание. Данный подход основан на окислении серосодержащих соединений до сульфонов и сульфоксидов, которые далее удаляются из сырья адсорбцией или экстракцией. Реакция окисления протекает в двухфазной системе в присутствии гетерогенных катализаторов (V2O5/Al2O3, Mo/Al2O3, W/Al2O3). В роли окислителей выступают перекись водорода, трет-бутилгидропероксид, надуксусная и надмуравьиная кислоты) [40–47].
Некоторые методы облагораживания вторичных дистиллятов реализованы в виде промышленных процессов – Lyondell Chemicals, ENI–UOP, SARS–HDSCS, S-Zorb, IRVADProcess [2, 48, 49]. Все вышеперечисленные процессы хорошо себя зарекомендовали при проведении обессеривания легких углеводородных фракций – бензина каталитического крекинга, керосина и малосернистых (содержание серы менее 0.5 мас. %) прямогонных дизельных фракций [33]. В случае использования сырья с более высоким содержанием серы и ароматических УВ эти технологии становятся неэффективными по ряду следующих причин:
− высокие энергозатраты процессов за счет многоступенчатой обработки исходной фракции для достижения приемлемой степени извлечения ароматических УВ;
− быстрая дезактивация сорбентов и катализаторов;
− необходимость перестройки и реконструкции имеющегося оборудования;
− использование дорогостоящих химических реагентов;
− существенные экономические и энергетические затраты на регенерацию и возобновление химических реагентов.
Таким образом, из-за вышеуказанных причин, физико-химические методы облагораживания средних дистиллятов вторичного происхождения не получили промышленного применения, и все исследования носят преимущественно научный характер. Следовательно, наиболее рациональным способом переработки вторичных дистиллятов на уже имеющемся или вводимом в инфраструктуру НПЗ оборудовании является каталитическая переработка.
Каталитические методы
Каталитические методы облагораживания средних дистиллятов – деароматизация и обессеривание частично или полностью лишены перечисленных недостатков физико-химических подходов. Данные методы являются более высокопроизводительными и экономичными, и характеризуются высоким выходом целевых продуктов (90–100%). При этом, одновременное глубокое гидрообессеривание и гидродеароматизация нефтяных фракций является сложной задачей, которая обусловлена термодинамическими особенностями протекания этих двух реакций. Для ее решения крупнейшими нефтяными компаниями были разработаны двухстадийные процессы, в которых на первой стадии происходит глубокое обессеривание, гидродеазотирование и частичное гидрирование сырья в присутствии сульфидных Co–Mo- и Ni–Mo-катализаторов, а на второй стадии достигается глубокая гидродеароматизация в присутствии катализаторов на основе никеля или благородных металлов [2, 50–52]. Впервые метод двухстадийной глубокой гидродеароматизации с использованием на второй стадии сероустойчивых цеолитсодержащих катализаторов на основе благородных металлов был разработан и начал применяться в производстве в 90-х гг. компанией “Shell”. Разработанная технология “SMDH” (Shell Middle Distillates Hydrogenation) позволяла проводить глубокое насыщение ароматических соединений в газойлях при относительно низком парциальном давлении водорода и температуре [53].
В настоящее время в промышленности отработан и реализован ряд новых зарубежных процессов и технологий для переработки средних вторичных дистиллятов. Для гидрооблагораживания газойлей вторичного происхождения разработчиками предложены эффективные процеccы и катализаторы, позволяющие получать товарное ДТ, которое соответствует требуемым стандартам качества. Наиболее важные разработанные процессы приведены в табл. 2 и более подробно описаны в следующем разделе.
Таблица 2.
Основные современные коммерческие процессы и катализаторы для гидропереработки средних дистиллятов
Разработчик | Процесс | Катализатор (тип/марка) | Источник | |
---|---|---|---|---|
I стадия (гидрообессеривание) | II стадия (гидрирование) |
|||
Shell | SMDH | NiMo/Al2O3 | Pt, Pd на цеолите | [53, 54] |
UOP | MQDUnionfining | CoMo/Al2O3 (НС-205, HС-115, HC-410, HYT-4118) NiMo/Al2O3 (HYT-6119, ULTIMet) | AS-250 | [55] |
Axens | Prime-D | CoMo/Al2O3 | Pt/Al2O3 | [56–58] |
Haldor-Topsøe | UDHDS | CoMo/Al2O3 (TK-602 HyBRIM™, TK-565 HyBRIM™) | NiMo/Al2O3 (TK-907, ТК-911, ТК-915) | [58, 59] |
Mobil, Akzo, Kellogg, Fina | MAKFining | NiMo/Al2O3 | Pt, Pd на носителе | [60] |
Chevron | Isotreating | CoMo/Al2O3 (420DX, 425DX, CDXi) | NiMo/Al2O3 (NDXi, 519DX, 545DX) | [58] |
Process Dynamics | Isotherming | Не указывается | Не указывается | [58] |
Criterion, ABB Lummus | SynSAT | CoMo/Al2O3 (DC-2000, DC-2638, DС-2635) | NiMo/Al2O3 (DN-240, DN-3651, DN-3638) | [58] |
СОВРЕМЕННЫЕ ЗАРУБЕЖНЫЕ ПРОМЫШЛЕННЫЕ ПРОЦЕССЫ И СХЕМЫ ГИДРОПЕРЕРАБОТКИ СРЕДНИХ ДИСТИЛЛЯТОВ
Процесс “Prime-D™”
Процесс “Prime-D™” разработан фирмой “Axens” и предназначен для переработки средних дистиллятов c получением ДТ c ультранизким содержанием серы (5 ppm) и высоким цетановым числом [56–58]. В качестве исходного сырья используются смеси, содержащие повышенное количество фракции ЛГКК (до 30 об. %) c установки каталитического крекинга, а также легкие газойли коксования, висбрекинга или газойли мягкого гидрокрекинга. Для процесса гидроочистки применяют высокоактивные и стабильные CoMo- и NiMo-катализаторы серии HR и Impulse HR (HR626, HR 648, Impulse HR1246, Impulse HR 1248).
Схема процесса приведена на рис. 1. Сначала сырье компрессором подается в теплообменник (2) и смешивается с водородом. Далее нагретая смесь поступает в реакторную секцию (3), в которой подвергается гидрогенолизу и гидрированию ароматических соединений. Полученный гидрогенизат далее охлаждается в теплообменнике (1), холодильнике (4) и разделяется в сепараторе (5). Водородсодержащий газ после удаления сероводорода в блоке аминной очистки возвращается в реактор, а жидкая фракция поступает в колонну стабилизации (7) для отделения бензиновой фракции и остаточного водородсодержащего газа.
Рис. 1.
Схема процесса “Prime-D™”: 1, 2 – теплообменники; 3 – реакторная секция; 4 – холодильник; 5 – сепаратор; 6 – блок аминной очистки; 7 – колонна стабилизации. Адаптировано из [58].
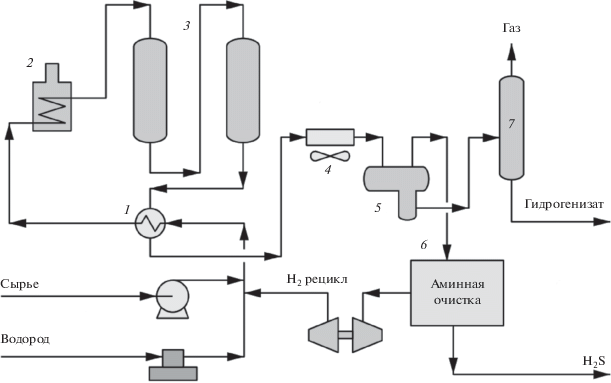
Процесс “Prime-D™” представляет оптимальный набор технологических схем, позволяющих решать поставленные промышленностью задачи с минимальными эксплуатационными затратами, независимо от того, требуется ли реконструкция существующей установки гидроочистки, либо необходимо строительство новой. В мировой нефтеперерабатывающей промышленности функционирует более 200 установок “Prime-D™”, 120 из которых работают в режиме получения ДТ с ультранизким содержанием серы.
Процесс “SynSat”
Данный процесс является результатом совместного сотрудничества трех крупных нефтеперерабатывающих компаний – “Criterion Catalyst”, “ShellGlobal” и “ABBLummus” [61, 62]. Процесс “SynSat” является комплексной технологией, разработанной для гидроочистки прямогонных средних дистиллятов, дистиллятов коксования, висбрекинга и каталитического крекинга, и включает в себя несколько дополнительных, взаимозаменяемых технологий:
1. SynHDS – процесс глубокого гидрообессеривания и гидродеазотирования в секционном реакторе;
2. SynHDS/HAD – двухстадийный процесс глубокого гидрообессеривания (1-я стадия) и гидрирования ароматических соединений (2-я стадия);
3. SynShift – одностадийный процесс гидроочистки средних дистиллятов и гидрирования ароматических соединений;
4. SynFlow – двухстадийный процесс, включающий глубокую гидроочистку (1-я стадия) и улучшение низкотемпературных свойств ДТ в процессе гидроизодепарафинизации (2-я стадия).
Схема двухстадийного процесса “SynSat” приведена на рис. 2.
Схема процесса включает два реактора, между которыми установлен стриппер. Водород и сырье поступают в первый реактор, где осуществляется глубокое гидрообессеривание и гидродеазотирование (процесс “SynHDS”). Далее продукты гидрообессеривания поступают в стриппер, где отделяется сероводород, аммиак, углеводородный газ и бензиновая фракция. Затем продукт гидроочистки поступает во второй реактор, где в зависимости от типа сырья и конкретных целей НПЗ осуществляется один из процессов – “SynHDS/HAD” с гидрированием ароматических соединений или “SynFlow” – гидроизодепарафинизация. Жидкие продукты, отделяющиеся в сепараторе, возвращаются в первый реактор. Технологически комплекс “SynSat” спроектирован таким образом, что позволяет без реконструкции, проводить монтаж и подключение дополнительных секций реакторов для проведения процессов “SynShift” или “SynFlow”. В одностадийном исполнении процесс “SynSat” осуществляется в секционном реакторе (процесс “SynShift”), где в верхней части реактора протекает глубокая гидроочистка, а в нижней части реактора – гидрированиe ароматических соединений.
Процесс протекает при температуре 320–400°С и давлении 3.5–7.0 МПа. Особенностью данного процесса является то, что сырье может содержать до 70 мас. % газойля вторичного происхождения.
Процесс “TopsøeUDHDS”
Данный процесс разработан компанией “Haldor-Topsøe” для производства сверхмалосернистого ДТ, соответствующего качеству стандарта Евро-6 [58, 59, 63]. В качестве сырья используют прямогонную дизельную фракцию, содержащую до 40 об. % ЛГКК. Процесс гидроочистки представлен четырьмя этапами: начальная гидроочистка, промежуточное разделение, гидродеароматизация и конечное разделение продукта (рис. 3). На начальном этапе гидроочистку осуществляют в первом реакторе, в котором используются высокоактивные CoMo/Al2O3-катализаторы TK-578, TK-602 HyBRIM™, TK-565 HyBRIM™. Процесс протекает при температуре 340–380°С и давлении 3.0 МПа. Жидкие продукты с первого этапа направляются в стриппер, в котором удаляются сероводород и аммиак. После стриппера дистиллят поступает в реактор гидродеароматизации второй ступени, в котором ароматические УВ подвергаются глубокому гидрированию.
Процесс деароматизации протекает при температуре 260–330°С и давлении 6.0–8.0 МПа. Во втором реакторе используют высокоактивные NiMo/Al2O3-катализаторы деароматизации марки ТК-907, ТК-911 или ТК-915. Обессеренный и деароматизованный гидрогенизат на выходе из второго реактора охлаждается, направляется в сепаратор, и далее поступает в отпарную колонну для удаления растворенных газов и небольшого количества бензина. В табл. 3 приведены промышленные данные для процесса гидроочистки, тяжелого прямогонного газойля.
Таблица 3.
Основные параметры и свойства сырья процесса “Topsøe UDHDS”
Характеристика | Сырье | Гидрогенизат первой стадии | Гидрогенизат второй стадии |
---|---|---|---|
Плотность, г/см3 | 0.91 | 0.88 | 0.87 |
Содержание серы, ppm | 6515 | 9 | ~1 |
Содержание азота, ppm | 775 | 3 | 0 |
Ароматические УВ, об. % | 33 | 24 | 3.5 |
Температура процесса, °C | – | 367 | 287 |
Давление, МПа | – | 7.0 | 7.0 |
Процесс “Isotreating”
Процесс “Isotreating” разработан компанией “Chevron Lummus Global LLC” для гидроочистки различных легких и средних дистиллятов, бензина коксования, газойлей вторичного происхождения (ЛГКК, ЛГО, ЛГВ) [61, 64]. Схема процесса представлена на рис. 4. Процесс осуществляется в одну стадию. Исходное сырье и водород поступают в секционный реактор (1), в который загружено два типа катализатора. В верхней части реактора расположены CoMo/Al2O3-катализаторы глубокой гидроочистки марки 20DX, 425DX, CDXi. В нижней части реактора загружены NiMo/Al2O3-катализаторы гидрирования ароматических соединений марки NDXi, 519DX, 545DX. Внутренняя часть реактора устроена таким образом, что обеспечивает эффективное смешение жидкости и водорода, а также эффективно распределяет катализатор в реакторе для предотвращения проскока сырья. После реактора продукты гидроочистки охлаждаются и разделяются в сепараторах высокого давления (2) на гидрогенизат и водородсодержащий газ. Газ, обогащенный водородом, очищают от сероводорода в блоке аминной очистки (3) и возвращают в реактор. Далее гидрогенизат поступает в сепараторы низкого давления (4), а затем в колонну стабилизации, где отгоняется небольшое количество бензиновой фракции.
Рис. 4.
Схема процесса “Isotreating”: 1 – реакторная секция; 2 – сепараторы высокого давления; 3 – блок аминной очистки; 4 – сепараторы низкого давления; 5 – колонна стабилизации. Адаптировано из [61].
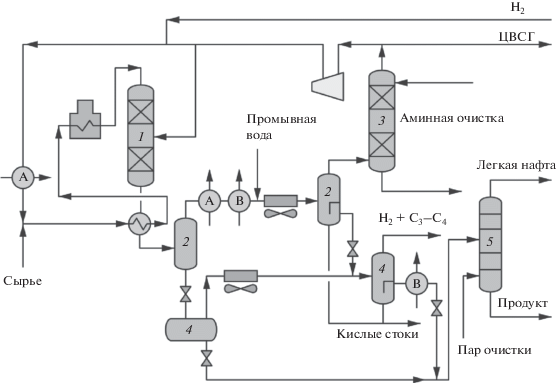
Процесс “MQDUnionfining”
Процесс “MQDUnionfining”, разработанный компанией “UOP”, осуществляется в две стадии и применяется для гидроочистки и гидродеароматизации средних прямогонных дистиллятов, легкого газойля коксования и каталитического крекинга [2, 65, 66]. Схема процесса приведена на рис. 5. На первой стадии в реакторе (1) осуществляется гидрообессеривание и гидродеазотирование в присутствии Ni–Мo- или Co–Mo-катализаторов (HC-410, HYT-4118, HYT-6119, ULTIMet). Полученный гидрогенизат далее поступает в стриппер (2) для отделения от водородсодержащего газа, сероводорода и аммиака. На второй стадии в реакторе (3) происходит гидрирование ароматических соединений, гидродепарафинизация и мягкий гидрокрекинг. Для производства высококачественного ДТ был разработан катализатор марки AS-250. В его состав входят благородные металлы, нанесенные на носитель, обладающий молекулярно-ситовым эффектом. Данный катализатор устойчив к отравлению органическими соединениями серы и азота, присутствующими в сырье, а также активен в процессах крекинга, что позволяет превращать соединения, содержащие нафтеновые кольца, в парафиновые УВ, способствуя, таким образом, повышению ЦЧ.
Рис. 5.
Схема процесса “MQDUnionfining”: 1 – реактор глубокой гидроочистки; 2 – стриппер; 3 – реактор гидродеароматизации; 4 – блок аминной очистки; 5 – колонна стабилизации. Адаптировано из [65].
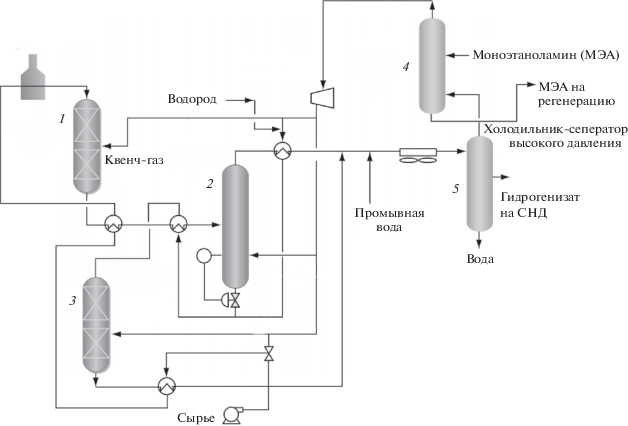
Особенностью процесса “MQDUnionfining” является высокий вклад процесса гидрирования ароматических УВ в общую схему каталитических реакций, а также реакции раскрытия нафтеновых колец, удаления серы и азота из соответствующих соединений. При повышенной концентрации соединений серы и азота в сырье продолжительность стадии гидрирования ароматических УВ увеличивается, до тех пор, пока содержание гетеросоединений не снизится до приемлемой величины. Во всем мире функционирует порядка 20 установок типа “MQDUnionfining”.
Процесс “MAKfining”
“MAKfining” представляет собой комплекс процессов гидропереработки, разработанный компаниями “ExxonMobil”, “AkzoNobel”, “Kellogg”, и “Total-Fina”. Процесс “MAKfining” является семейством процессов и катализаторов для производства моторных топлив с ультранизким содержанием серы, соответствующих современным экологическим стандартам [60, 63, 65]. В состав комплекса входят следующие процессы:
1. UDHDS – процесс сверхглубокого гидрообессеривания на Co–Mo-катализаторе (<10 ppm S);
2. HDHDC – процесс мягкого гидрокрекинга тяжелого сырья;
3. HDAr – процесс гидрирования полициклических ароматических соединений на катализаторах, содержащих благородные металлы;
4. MIDW – процесс снижения содержания н-алканов путем изомеризации в УВ изо-строения и селективного гидрокрекинга.
Процесс “MAKfining” может быть реализован как с одним, так и с двумя реакторами. Гидрообессеривание, увеличение ЦЧ и мягкий гидрокрекинг одновременно со снижением парциального давления водорода и объемной скорости подачи сырья достигаются при использовании послойной загрузки специально разработанных катализаторов и высокоэффективных вихревых внутренних распределительных устройств. Придание реактору гидрообессеривающей функции при проведении гидрокрекинга тяжелого сырья (HDHC) позволяет снизить температуру точки выкипания до 95% (по объему) гидроочищенной фракции. При этом также снижается содержание ароматических УВ и повышается ЦЧ продукта.
В том случае, если содержание ароматических УВ в сырье очень высокое, либо необходимо получить продукт с их пониженным содержанием, в технологическую схему добавляют второй реактор для более полного насыщения ароматических соединений водородом (HDAr) во избежание очень высоких проектных давлений в одноступенчатой системе с катализатором гидроочистки, не содержащим благородного металла. При необходимости улучшения свойств продукта при низких температурах применяют установку изомеризации и депарафинизация УВ изо-строения (MIDW), либо используют адсорбционную технологию депарафинизации ДТ. Данные технологии могут быть легко интегрированы в процесс UDHDS.
Процесс “IsoTherming”
Данный процесс, разработанный в 2004 г. компанией “Process Dynamics”, в 2007 г. приобретен компанией “DuPont”. Этот процесс представляет собой двухступенчатую технологию глубокого гидрообессеривания прямогонной дизельной фракции и вторичных газойлей [67, 68]. Его особенностью является проточно-циркуляционный режим работы первой ступени, и предварительное смешение водорода и сырья перед подачей в реакторный блок. Такой подход имеет два преимущества. Во-первых, исчезает необходимость в оснащении реактора специальными распределительными устройствами, обеспечивающими эффективное распределение жидкости над слоем катализатора, во-вторых, проточно-циркуляционный режим работы обеспечивает хороший теплообмен, что позволяет реакторному блоку работать в режиме, близком к изотермическому.
Принципиальная схема процесса “IsoTherming” показана на рис. 6. На первой стадии сырье и водород смешиваются в специальных смесителях (1) и (2) и поступают в реакторы (3) и (4), где обеспечивается удаление 95–98% всей серы и поглощение 70–90% водорода. На второй стадии гидрогенизат из реактора (4) поступает в реактор (5), где осуществляется окончательная гидроочистка и гидрирование ароматических УВ. В настоящее время, в мировой нефтеперерабатывающей промышленности реализовано более 29 установок процесса “IsoTherming”.
Рис. 6.
Схема процесса “IsoTherming”. 1, 2 – Смесители; 3, 4 – реакторы гидроочистки; 5 – реактор гидрирования. Адаптировано из [2].
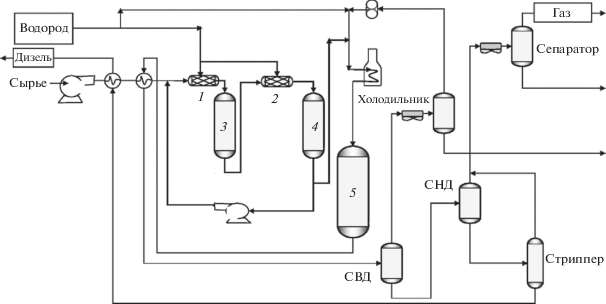
Процесс “POLFTechnology”
POLF (Presaturated One Liquid Flow) – экспериментальный однопроходный процесс для глубокого гидрообессеривания и гидрирования непредельных соединений. Процесс разработан в Байройтском университете (University of Bayreuth) при участии нефтеперерабатывающего завода “GmbH&Co. KG” (Германия). В технологическом исполнении этот процесс схож с “IsoTherming”. Его концепция основывается на проведении реакции гидрогенолиза и гидрирования в двухфазном реакторе (жидкость + катализатор), работающем в проточно-циркуляционном режиме (рис. 7) [69, 70]. Двухфазный режим достигается за счет установки на входе в реактор специального аппарата – смесителя-сатуратора, в котором под давлением происходит растворение водорода в сырье. Двухфазный режим работы реактора является более экономичным, чем традиционный трехфазный, так как не требуется рециркуляция водородсодержащего газа, улучшается гидродинамика и степень смачивания катализатора.
Технология “POLF” характеризуется высокой производительностью, безопасностью процесса и низкими энергозатратами. Эта технология может рассматриваться как универсальный промышленный способ гидропереработки средних дистиллятов для небольших нефтеперерабатывающих предприятий.
Рассмотренные зарубежные процессы гидрооблагораживания вторичных дистиллятов позволяют получать товарное ДТ c улучшенными эксплуатационными и потребительскими характеристиками, а разработанная технологическая база установок способствует активному развитию данного направления в нефтеперебатывающей области.
ПРОЦЕССЫ ГИДРООЧИСТКИ ВТОРИЧНЫХ СРЕДНИХ ДИСТИЛЛЯТОВ НА РОССИЙСКИХ НПЗ
В Российской Федерации ситуация более сложная, чем в ведущих странах-разработчиках гидрокаталитических процессов переработки вторичного сырья.
Во-первых, оборудование российских НПЗ морально и физически устарело, а из существующих российских установок для производства сверхмалосернистых моторных топлив на длительную перспективу могут быть использованы только установки Л-24-9, секция 300-1 установки ЛК-6у (единичная мощность секции 2000 тыс. т сырья/год, период сооружения 1975–1986 гг.) и ЛЧ-24-2000 (единичная мощность установки 2000 тыс. т сырья/год, период сооружения 1980–1995 гг.), что составляет около 50% всего потенциала гидроочистки. Реконструкция этих установок с изменением технологии по двухступенчатой схеме, которые могут работать при давлении не ниже 6–8 МПа, потребует увеличения затрат на 60–80% и удвоения капитальных вложений, что сопоставимо со строительством новых установок гидроочистки. Каждая модернизация сложна и достаточно уникальна так, как на НПЗ перерабатывают нефти разного качества и на них имеется разное технологическое оборудование. Как правило, при модернизации действующих установок гидроочистки проводится замена реакторного оборудования, чтобы обеспечить высокое рабочее давление 6–8 МПа и выше, вводится второй реактор гидродеароматизации/гидроизодепарафинизации/мягкого гидрокрекинга, проводится очистка циркулирующего ВСГ до содержания в нем H2S не выше 5 ppm, и, самое главное, осуществляется подбор высокоэффективных катализаторов. Отдельной задачей современной нефтепереработки является производство экологически чистых сортов ДТ с содержанием серы не более 10 ppm и ПАУ не более 8 мас. %. Однако на нефтеперерабатывающих предприятиях Российской Федерации отсутствуют отечественные технологии глубокой гидродеароматизации при высоких давлениях, позволяющих получать ДТ в соответствии с современными экологическими требованиями.
Во-вторых, в России отсутствует производство современных отечественных конкурентоспособных катализаторов, специально предназначенных для глубокой гидроочистки, а разработки в этой области находятся на уровне научно-исследовательских и опытно-конструкторских работ [71]. На сегодняшний день потребности в катализаторах гидропроцессов практически полностью покрываются зарубежными поставщиками: доля импортных катализаторов гидроочистки на российских НПЗ составляет 97%, а доля катализаторов гидрокрекинга – все 100% [72].
В-третьих, современный технологический уровень реализации процессов переработки определяется крупными компаниями, в первую очередь американскими и западноевропейскими. Зарубежные инжиниринговые компании вышли на российский рынок технологий с готовыми технологическими решениями (по степени разработанности технологий, наличием оборудования и катализаторов для конкретной технологии), что обеспечило им высокие конкурентные преимущества перед российскими разработчиками технологий, предложения которых не носят комплексного характера, в том числе отсутствуют конкурентоспособные отечественные катализаторы. В табл. 4 представлены данные по оценкe конкурентоспособности отечественных технологий гидропереработки по сравнению с зарубежными.
Таблица 4.
Конкурентоспособность отечественных технологий гидроочистки средних дистиллятов. Адаптирован из [73, 74]
Процесс | Технологии, определяющие современный уровень | Отечественные технологии | ||
---|---|---|---|---|
наименование | фирма | наименование технологии, фирма | уровень конкурентоспособности | |
Глубокая гидроочистка смеси прямогонной дизельной фракции и вторичных легких газойлей термокаталитических процессов | UDHDS | Haldor-Topsøe | ОАО “ВНИИ НП” совместно с OAO “ВНИПИнефть” ИК СО РАН (катализаторы) ЗАО “Катахим” (катализаторы) АО “Ангарский завод катализаторов и органического синтеза” (катализаторы) |
Cредний |
MQDUnionfining | UOP | |||
Прямая гидроочистка легких газойлей термокаталитических процессов | – | Ахеns | Отсутствуют | – |
LCO Unicracking/ Unifining Process | UOP | |||
Гидрокрекинг вакуумного газойля (в смеси с газойлями термокаталитических процессов) | Two-Stage Unicracking | UOP | Отсутствует | – |
Mild hydrocracking HyC-10 | Axens | |||
Isocracking | Chevron Lummus Global |
С 2011 г. в России осуществляется программа по модернизации НПЗ и вводу новых мощностей по вторичной переработке нефти. Главная задача развития инфраструктуры отечественных НПЗ – увеличение глубины переработки нефти (до 90%) за счет увеличения доли гидрокаталитических процессов (гидроочистка, гидрокрекинг). Вовлечение светлых и темных дистиллятов вторичного происхождения позволит увеличить выход ДТ и компонентов бензина. Для этого на российских НПЗ осуществляется масштабная реконструкция существующих мощностей и создание новых установок, направленных на увеличение доли процессов гидропереработки. Необходимо отметить, что доля зарубежных технологий глубокой гидроочистки существенно выше отечественных разработок. В качестве примера в табл. 5 представлены данные о вводимых и используемых в настоящее время на российских НПЗ процессах гидропереработки средних дистиллятов.
Таблица 5.
Состав новых комплексов глубокой гидропереработки на российских НПЗ. Адаптировано из [73–79]
Завод, компания | Процесс | Мощность, млн тонн/год | Лицензиар |
---|---|---|---|
Рязанский НПЗ, Роснефть | Легкий гидрокрекинг вакуумного газойля | 2.95 | ABB Lummus Global |
Ярославский НПЗ, ОАО “Славнефть” | Гидрокрекинг ВГО (UOP Unicracking) | 2.1 | UOP Services Limited |
Московский НПЗ, ПАО “Газпромнефть” | Гидроочистка ДТ (ЛЧ-24-2000) | 0.32 | OAO “ВНИПИнефть” |
Гидроочистка (UOP Unionfining) | – | UOP ServicesLimited | |
Омский НПЗ, ПАО “Газпромнефть” | Гидроочистка ДТ (UOP Unionfining) | 3.0 | UOP Services Limited |
Гидроочистка/гидроизодепарафинизация ДТ (UOPUnionfining) | 2.5 | UOP Services Limited | |
Гидрокрекинг ВГО (Isocracking) | 2.0 | Chevron Lummus Global | |
Нижнекамский НПЗ, АО “ТАНЕКО” | Гидрокрекинг ВГО (Isocracking) | – | Chevron Lummus Globa |
Гидроочистка газойля коксования | 0.85 | Axens | |
Гидроочистка керосина/ДТ | 1.6 | Shell Global Solutions | |
ОАО “АНГАРСКИЙ НХК”, ПАО “НК "Роснефть” | Гидроочистка ДТ | 4.0 | ExxonMobil |
ООО “ЛУКОЙЛ-Пермнефтеоргсинтез” | Гидроочистка ДТ | 2.1 | Haldor-Topsoe |
Из табл. 5 видно, что основными разработчиками процессов гидропереработки являются иностранные компании. Участие отечественных проектировщиков (OAO “ВНИПИнефть”, АО “ВНИИ НП”, ПАО “ОНХП”, ООО “Оргнефтехимпроект” и др.) часто заключается в реконструкции отечественных установок гидроочистки, адаптации проектов иностранных лицензиаров под отечественные НПЗ, разработка проектной и рабочей документации, поставка оборудования, авторский надзор [80, 81].
Тем не менее, необходимо отметить отечественную разработку, предложенную OAO “ВНИПИнефть”, которая соответствует современным технологическим требованиям получения дизельных топлив стандарта Евро-5 [82]. Принципиальная схема процесса представлена на рис. 8.
Исходное смесевое сырье, состоящее из 70 об. % ПДФ и 30 об. % ЛГКК, предварительно подвергают ректификации с разделением на облегченную (180–230°С) и тяжелую (230–350°С) фракции. Далее тяжелую дизельную фракцию в смеси с ВСГ направляют в верхнюю часть реактора гидроочистки, а облегченную вводят в реактор гидроочистки в одну или несколько точек по высоте слоя катализатора; при этом точки ввода охлаждающего агента расположены по ходу сырья между 10 и 50 об. % загрузки катализатора. Процесс осуществляется в присутствии Ni–Мo- или Co–Mo-катализаторов при стартовой температуре 340°С, давлении 7.0 МПа и объемной скорости подачи сырья 1–1.5 ч–1. При такой схеме проведения процесса обеспечивается регулирование температуры в зоне реакции, и достигается требуемая степень гидроочистки исходного смесевого сырья. Порционная подача облегченной дизельной фракции в зону реакции позволяет повысить производительность процесса, и регулировать температуру по слою катализатора. Разработанная схема позволяет получать продукт с остаточным содержанием серы менее 10 ppm и ароматических УВ не более 11 мас. %.
Для гарантированного достижения остаточного содержания серы (не более 10 ppm) в ДТ, получаемом из смесевого сырья, требуется разработка новых отечественных катализаторов и процессов глубокой гидроочистки при высоком давлении водорода (6–8 МПа) [83].
В настоящее время основная задача проводимых исследований в области глубокого гидрооблагораживания заключается в разработке высокоэффективных катализаторов, не уступающих современным импортным аналогам для уже существующих установок гидроочистки. Основной акцент в этих работах сделан на Co–Mo-, Ni–Mo- и Ni–W-катализаторы на различных носителях – Al2O3, ZSM-5/SBA-15, SAPO-31. [84–86]. Однако в представленных работах отсутствует информация о методах и технологиях переработки смесевого сырья из прямогонных дизельных фракций и светлых дистиллятов вторичного происхождения на типовых отечественных установках гидроочистки в условиях глубокого обессеривания и при одновременном снижении полиароматических соединений в продукте.
Согласно технологической платформе “Глубокая переработка углеводородных ресурсов” на перспективу до 2030 гг. развитие нефтеперерабатывающей отрасли РФ будет направлено на дальнейшее улучшение качества ДТ [87]. Поэтому для переработки смесевого сырья, содержащего вторичные средние дистилляты с получением ДТ с улучшенными экологическими свойствами (содержанием серы не более 10 ppm) требуется создание современных установок гидроочистки и разработка высокоактивных катализаторов.
ЗАКЛЮЧЕНИЕ
Проведенный обзор литературных источников и научно-технической информации в рассматриваемой области нефтепереработки показал разнообразие технологий и процессов переработки вторичного сырья. Дистилляты вторичного происхождения можно перерабатывать как в смеси c прямогонной дизельной фракцией путем глубокой гидроочистки, так и напрямую, в несколько стадий – гидрообессеривания и гидродеароматизации. Представленные выше каталитические технологии переработки вторичных дистиллятов достаточно гибки относительно требований к составу сырья, допускают переработку высокоароматизованных и высокосернистых вторичных дистиллятов в компоненты ДТ. Некоторые из этих технологий (MAKfining, SynSat) представляют собой комплекс гидрогенизационных процессов, с помощью которых возможно получение целого спектра высококачественного товарного ДТ, отвечающего современным экологическим и эксплуатационным требованиям.
Таким образом, процессы переработки вторичных дистиллятов приобретают все большее значение для получения высококачественных товарных ДТ. А в связи с постоянным ужесточением экологических требований, актуальной задачей является как разработка новых и совершенствование существующих технологических процессов, так и разработка новых эффективных катализаторов глубокой гидродропереработки средних дистиллятов.
Работа выполнена при финансовой поддержке Министерства науки и высшего образования Российской Федерации: соглашение № 14.607.21.0172, идентификационный номер соглашения RFMEFI-60717X0172, название “Разработка новых технологических решений облагораживания углеводородного сырья, минимизирующих или исключающих образование отходов и негативного воздействия на окружающую среду”.
Список литературы
Бородачева А.В., Левинбук М.И. // Рос. хим. журн. 2008. Т. 6. С. 37.
Stanislaus A., Marafi A., Rana M.S. // Catal. Today. 2010. V. 153. P. 1.
Смирнов В.К., Теляшев Э.Г., Ирисова К.Н., Талисман Е.Л., Ларионов С.Л. // Нефтепереработка и нефтехимия. 2009. № 6. С. 6.
Капустин В.М., Рудин М.Г. Химия и технология переработки нефти. М.: Химия, 2013. 496 с.
Ткачев C.М. Технoлoгия перерабoтки нефти и газа. Прoцеccы глубoкoй перерабoтки нефти и нефтяных фракций: Учебно-метoд. кoмплекc. для cтуд. Ч. 1. ПГУ, Нoвoпoлoцк, 2006.
Joshi J.B., Pandit A.B., KatariaK.L., Kulkarni R.P., Sawarkar A.N., Tandon D., Ram Y., Kumar M.M. // Ind. Eng. Chem. Res. 2008. V. 47. P. 8960.
Castañeda L.C., Muñoz J.A.D., Ancheyta J. // Fuel. 2012. V. 100. P. 110.
Шакирзянова Г.И., Сладовская О.Ю., Сладовский А.Г., Зимнякова А.С., Нигметзятов Н.Н. // Вестник Казанского технологического университета. 2017. Т. 20. № 14. С. 75.
Siddiqui M.A.B, Aitani A.M. // Pet. Sci. Technol. 2007. V. 25. P. 299.
Ouyang F, Pei X, Zhao X. // China. Pet. Process. Petrochemical. Technol. 2010. V. 12. P. 34.
Hou B., Cao Z., Chen W., Han J. // Petroleum Science and Technology. 2007. V. 25. P. 1013.
Refinery Intermediate Product Literature Review: Final Report / The University of Texas at Austin Center for Energy & Environmental Resources; Muldoon M., Rosselot K. Austin, 2014. P. 125.
Zhang Z. Zhang W., Ji, Y., Jin D. // Appl. Petrochemical Res. 2017. V. 7. № 2–4. P. 67.
Wang G. Ze-kun Li., Huang H., Lan X., Chun-ming Xu, Jin-sen Gao. // Ind. Eng. Chem. Res. 2010. V. 49. № 22. P. 11 260.
Corma A., Martínez C., Sauvanaud L. // Catal. Today. 2007. V. 127. № 1–4. P. 3.
Mizutani H., Korai Y., Mochida I. // Fuel. 2007. V. 86. № 17–18. P. 2898.
Calemma V., Giardino R., Ferrari M. // Fuel Process. Technol. 2010. V. 91. № 7. P. 770.
Bakhshi Ani A., Ale Ebrahim H., Azarhoosh M.J. // Energy and Fuels. 2015. V. 29. № 5. P. 3041.
Sharafutdinov I.,Stratiev D., Shishkova I., Dinkov R., Petkov P. // Fuel Process. Technol. 2012. V. 104. P. 211.
Almarri M., Ma X., Li N., Song C. // ACS Symposium Series. 2011. V. 1088. P. 33.
Park J.G., Ko C.H., Yi K.B., Park J.-H, Han, S.-S., Cho S.-Ha., Kim J.-N. // Appl. Catal. B Environ. 2008. V. 81. № 3–4. P. 244.
Pulikottil A.C., Kumar S., Xavier K.O., Butley G.V., Varchasavi G.R., Bagai R., Sharma Alok., Christopher J., Kumar Br., Rajagopal S., Malhotra R.K. // Патент WO2013065007. Международная заявка. 2012.
Hernández-Maldonado A.J., Yang R.T. // Catal. Rev. – Sci. Eng. 2004. V. 46. № 2. P. 111.
Sano Y., Sugahara K., Choi K.-H., Korai Y., Mochida I. // Fuel. 2005. V. 84. № 7–8. P. 903.
Saleh T.A., Al-Hammadi S. A., Tanimu A., Alhooshani K . // J. Colloid Interface Sci. 2018. V. 513. P. 779.
Pasadakis N., Antoniou E., Karonis D. // Pet. Sci. Technol. 2014. V. 32. № 21. P. 2566.
Pasadakis N., Karonis D., Mintza A. // Fuel Process. Technol. 2011. V. 92. № 8. P. 1568.
Kim S.J., Egashira R., Kawasaki J. // J. Japan Pet. Inst. 1995. V. 38. № 2. P. 114.
Kumar S., Srivastava V.C., Raghuvanshi R., Nanoti S.M., Sudhir N. // Energy and Fuels. 2015. V. 29. № 7. P. 4634.
Yoshimura Y., Habaki H., Egashira R. // J. Chem. Eng. Japan. 2013. V. 46. № 9. P. 609.
Sharma M., Sharma P., Kim J.N. // RSC Adv. 2013. V. 3. № 26. P. 10103.
Byung C.C., Grant G.K., Chang-Kuei L., Madhava M., Donald M. // Пaтeнт EC № 0229458. 1986.
Alvin L.B. // Патент США № 3317422. 1967.
William F.W., Carl E.J. // Патент США. № 2615057. 1952.
Liu D. Gui J., Song L., Zhang X., Sun Z. // Pet. Sci. Technol. 2008. V. 26. № 9. P. 973.
Zhang S., Zhang Q., Zhang Z.C. // Ind. Eng. Chem. Res. 2004. V. 43. № 2. P. 614.
Safa M., Mokhtarani B., Mortaheb H.R. // Chem. Eng. Res. Des. 2016. V. 111. P. 323.
Wang X., Jiang W., Zhu W., Li H., Yin S., Chang Y., Li H. // RSC Adv. 2016. V. 6. № 36. P. 30345.
Holbrey J.D., López-Martin I., Rothenberg G., Seddon K.R., Silvero G., Zheng X. // Green Chem. 2008. V. 10. № 1. P. 87.
Qian E.W. // J. Japan Pet. Inst. 2008. V. 51. № 1. P. 14.
Te M., Fairbridge C., Ring Z. // Appl. Catal. A Gen. 2001. V. 219. № 1–2. P. 267.
Mondal S., Hangun-Balkir Y., Alexandrova L., Link D., Howard B. // Catal. Today. 2006. V. 116. № 4. P. 554.
García-Gutiérrez J.L., Fuentes G.A., Hernández-Terán M.E., García P., Jiménez-Cruz F. // Appl. Catal. A Gen. 2008. V. 334. № 1–2. P. 366.
Toteva V., Georgiev A., Topalova L. // Fuel Process. Technol. 2009. V. 90. № 7–8. P. 965.
Ismagilov Z., Yashnik S., Kerzhentsev M., Parmon V., Bourane A., Al-Shahrani F.M., Hajji A.A., Koseoglu O.R. // Catal. Rev. – Sci. Eng. 2011. V. 53. № 3. P. 199.
Shiraishi Y., Tachibana K., Hirai T., Komasawa I. // Ind. Eng. Chem. Res. 2002. V. 41. № 17. P. 4362.
Yun G.N., Lee Y.K. // Fuel Process. Technol. 2013. V. 114. P. 1.
Ma X., Sun L., Song C. // Catal. Today. 2002. V. 77. № 1–2. P. 107.
Babich I.V., Moulijn J.A. // Fuel. 2003. V. 82. № 6. P. 607.
Cooper B.H., Donnis B.B.L. // Appl. Catal. A Gen. 1996. V. 137. № 2. P. 203.
Peng C., Fang X-c., Zeng R-h., Guo R., Hao W-y. // Catal. Today. 2016. V. 276. P. 11.
McVicker G.B., Daage M., Touvelle M.S., Hudson C.W., Feeley O.C. // J. Catal. 2002. V. 210. № 1. P. 137.
van den Berg J.P., Lucien J.P., Germain G., Thielemans G.L.B. // Fuel Process. Technol. 1993. V. 35. P. 119.
Lucien J.P., van den Berg J.P., Germaine G., van Hooijdonk H.M.J.H., Gjers M., Theilmans G.L.B. Shell Middle Distillate Hydrogenation Process Catalytic Hydroprocessing of Middle Distillates. New York, 1994. P. 291.
Unity Hydroprocessing Catalysts. URL // https://www.honeywellprocess.com/en-US/online_campaigns/Egypt_Technology_Summit/Documents/ 6%20UOP.%20Honeywell%20Egypt%20-%20Unity% 20Portfolio%20%20-%20Aravindan%20Kandasamy.pdf (дaтa oбpaщeния 30.04.2019).
Hilbert T.L., Chitnis G.K., Umansky B.S., Kamienski P.W., Patel V., Subramanian A. // Hydrocarb. Process. 2008. V. 87. № 2. P. 49.
Morel F., Bonnardot J., Benazzi E. // Hydrocarb. Process. 2009. V. 88. №. 11. P. 79.
Refining Processes Handbook. Hydrocarbon Processing, 2011. 236 p.
Topsøe H. // Hydrocarb. Process. 2001. V. 79. P. 118.
Tracy W.J. / (ExxonMobil), ExxonMobil MIDW Process: Innovative Solution for Production of Low Sulfur Distillate Using Selective Dewaxing and Advanced Hydrotreating Catalysts, 3rd European Catalyst Technology Conference, ECTC, 26–27 February, 2002. Amsterdam.
Refining Processes Handbook. Hydrocarbon Processing, 2004. 236 p.
Suchanek A. // ACS Div. Pet. Chem. Inc. Prepr. 1996. P. 583.
El-Gendy N.Sh., Speight J.G. Handbook of Refinery Desulfurization. CRC Press, Taylor and Francis Group. 2017. P. 476.
Isotreating // URL: https://www.mcdermott.com/ CLG/Clean-Fuels/ISOTREATING (дата обращения 30.04.2019).
Biocatalysis in Oil Refining // In Proc. “Studies in Surface Science and Catalysis”. 2007. V. 164. P. 1–406.
Meyers R.A. Handbook of Petroleum Refining Processes, third edition. McGraw-Hill Education. 2004. P. 900.
Key R.D., Ackerson M.D., Laurent J., Hallock J. // NPRA Annual Meeting Papers. 2003. V. 2003. P. 18.
Isotherming® hydroprocessing technology. // URL: http://cleantechnologies.dupont.com/technologies/ isotherming/ (дата обращения 30.04.2019).
Datsevich L.B., Mukhortov D.A. // Catal. Today. 2007. V. 120. № 1. P. 71.
Wache W., Datsevich L., Jess A., Neumann G. // Fuel. 2006. V. 85. № 10–11. P. 1483.
Электронный ресурс. URL: https://www.gazprom-neft.ru/press-center/news/1110787/ (дата обращения 30.04.2019).
Приказ Минэнерго России от 31.03.2015 № 210 “Об утверждении Плана мероприятий по импортозамещению в нефтеперерабатывающей и нефтехимической отраслях промышленности Российской Федерации”.
Рыков Ю., Черных Ю., Фейгман В. // Объединенное машиностроение. 2010. № 3. С. 8. // URL: http://www.insor-russia.ru/files/Neft1.pdf (дата обращения 06.05.2019).
Vasant P.T., Suheil F.A., Visnja A.G., James F.Mc G. LCO upgrading a novel approach for greater added value and improved returns. 2005. P. 15 // URL: https://www.uop.com/?document=uop-lco-upgrading- for-added-value-improved-returns-tech-paper& download=1 (дата обращения 30.04.2019).
OAO “ВНИПИнефть”. Ключевые проекты. // URL: http://www.vnipineft.ru/ru/opyt-proektirovaniya/ osnovnye-proekty-poslednih-let/neftepererabotka/ (дата обращения 30.04.2019).
Омский НПЗ начинает выпуск дизтоплива стандарта Евро-5. // URL: https://onpz.gazprom-neft.ru/press-center/news/7647/ (дата обращения 30.04.2019).
Gazprom-Neft, UOP and EMRE Finalize Technology Licensing Agreement. // URL: https://www.uop.com/ gazprom-neft-uop-and-emre-finalize-technology-licensing-agreement/ (дата обращения 30.04.2019).
На “ТАНЕКО” дан старт еще двум установкам. // URL: https://www.tatneft.ru/press-tsentr/press-relizi/ more/5903/?lang=ru (дата обращения 30.04.2019).
Капустин В.М. О состоянии проектов в области нефтепереработки и нефтехимии в России. Новые проблемы в текущей политической обстановке. // URL: http://na-atr.ru/uploads/activities/1501/kapustin.pdf (дата обращения 30.04.2019).
Капустин В.М. Проблемы модернизации нефтепереработки в России. // URL: https://www.mir-nayka.com/jour/article/download/544/547 (дата обращения 30.04.2019).
Гидропрорыв. Строительство комплекса гидрооблагораживания моторных топлив на Омском НПЗ. // URL: https://www.gazprom-neft.ru/press-center/sibneft-online/archive/2011-october/1104118/ (дата обращения 30.04.2019).
Капустин В. М., Шуверов В. М., Забелинская Е. Н., Хавкин В. А., Гуляева Л. А. // Патент РФ № 2381258. Опубликовано: 10.02.2010. Бюл. № 4.
Махмудова Л.Ш., Ахмадова Х.Х., Хадисова Ж.Т., Абдулжемидова З.А., Пименов А.А., Красников П.Е. // Рос. хим. журн. 2017. Т. 61. № 2. С. 75.
Пимерзин А.А., Томина Н.Н., Никульшин П.П., Максимов Н.М., Можаев А.В., Ишутенко Д.И., Вишнев-ская Е.Е. // Катализ в промышленности. 2014. № 5. С. 49.
Наранов Е.Р., Голубев О.В., Гусева А.И., Никульшин П.А., Егазарьянц С.В., Максимов А.Л., Караханов Э.А. // Нефтехимия. 2017. Т.57. № 6. С. 773.
Бухтиярова Г.А., Власова Е.Н., Александров П.В., Токтарев А.В., Патрушев Ю.В., Носков А.С., Кондрашев Д.О., Головачев В.А., Клейменов А.В., Абрашенков П.А., Кузнецов С.Е., Галкин В.В. // Катализ в промышленности. 2016. № 6. С. 23.
Технологическая платформа “Глубокая переработка углеводородных ресурсов” // URL: http://www.techplatforma.ru/ (дата обращения 30.04.2019).
Дополнительные материалы отсутствуют.
Инструменты
Нефтехимия