Нефтехимия, 2019, T. 59, № 6-1, стр. 659-665
Влияние морфологии цеолитных катализаторов на основные показатели реакции алкилирования изобутана бутиленами
И. М. Герзелиев 1, *, В. А. Темникова 1, М. Н. Басханова 1, А. Л. Максимов 1
1 Институт нефтехимического синтеза им. А.В. Топчиева РАН
Москва, 119991 Россия
* E-mail: gerzeliev@ips.ac.ru
Поступила в редакцию 21.05.2019
После доработки 02.07.2019
Принята к публикации 02.07.2019
Аннотация
Проведены исследования по влиянию морфологии цеолитных катализаторов в катионообменной форме, синтезированных на основе отечественных цеолитов типа NaХ, на основные показатели реакции алкилирования изобутана бутиленами. Установлено, что условия приготовления катализаторов не оказывают существенного влияния на структуру их поверхности. Оптимальные показатели реакции алкилирования (конверсия бутиленов 98–100 мас. %, выход алкилата близок к теоретическому 99–100 мас. %, селективность по ТМП держится на уровне 72 мас. %, С8-прочие не превышают 1.5 мас. %) достигаются при размере частиц катализаторов в двух диапазонах до 0.8 и/или выше 3.5 мкм.
Алкилбензин (алкилат) является важнейшей составной частью товарного бензина, так как представляет собой высокооктановые егo компоненты, не содержащие серы, олефинов и ароматических углеводородов (УВ), количество которых в автомобильных топливах регламентировано [1, 2]. В промышленности алкилат получают в процессе алкилирования изобутана олефинами с использованием серной и плавиковой кислот в качестве катализаторов. Понятно, что использование таких катализаторов связано с коррозией оборудования, опасностью транспортировки и необходимостью утилизации отработанных кислот, а также наличием дополнительных систем отчистки готового продукта, что приводит к экологическим и экономическим проблемам. Поэтому проводится поиск альтернативных безопасных катализаторов, в частности катализаторов на основе цеолитов [3–5].
Катализаторы на основе цеолитов типа Х проявляют высокие каталитические показатели в реакции алкилирования изобутана бутиленами [6–10], однако, влияние морфологии на эти свойства в литературе практически не описано.
Цель работы: определение влияния морфологии катализаторов алкилирования изобутана бутиленами на основные показатели процесса алкилирования изобутана бутиленами.
ЭКСПЕРИМЕНТАЛЬНАЯ ЧАСТЬ
Методика проведения ионного обмена
Ниже (рис. 1) представлен порядок проведения экспериментов в виде блок-схемы.
Исходные цеолиты: четыре отечественных коммерческих цеолита типа NaX, отличающиеся методом формовки со связующим и без связующего, и прессованный порошок.
Гидротермальный синтез. Для проведения ионного обмена использовали одинаковую по массе навеску цеолитов NaX российского производства в расчете на абсолютно сухое вещество (образцы 1–4, см. ниже в табл. 1). В качестве солей металлов использовали нитраты кальция, лантана и аммония. Массовое соотношение раствор/гранулы = 8 : 1. Концентрация растворов Ca(NO3)2, La(NO3)3 и NH4NO3 составляла 37.5, 135.0 и 26.5 г/л соответственно.
Таблица 1.
Свойства исходных цеолитов и образцов катализаторов
№ п/п | Свойства | Обозначение исходных цеолитов и образцов катализатора | |||||||||
---|---|---|---|---|---|---|---|---|---|---|---|
1 | 2 | 3 | 4 | 1.1 | 2.1 | 2.2 | 2.3 | 3.1 | 4.1 | ||
1 | Химический состав, мас. % | ||||||||||
SiO2 | 49.2 | 50.9 | 52.2 | 52.5 | 46.4 | 47.9 | 50.3 | 49.7 | 49.4 | 51.0 | |
Al2O3 | 32.7 | 31.2 | 32.4 | 32.3 | 30.7 | 29.4 | 30.4 | 30.0 | 30.6 | 30.9 | |
La2O3 | 0.0 | 0.0 | 0.0 | 0.0 | 20.7 | 20.2 | 16.9 | 18.3 | 16.0 | 15.6 | |
CaO | 0.0 | 0.2 | 0.2 | 0.1 | 0.5 | 0.7 | 1.0 | 0.6 | 0.4 | 0.5 | |
Na2O | 17.0 | 16.5 | 12.6 | 13.9 | 0.8 | 0.7 | 0.3 | 0.4 | 0.9 | 1.0 | |
прочие оксиды* | 1.1 | 1.2 | 2.6 | 1.2 | 0.9 | 1.1 | 1.1 | 1.0 | 2.7 | 1.0 | |
2 | Мольное соотношение Si/Al | 1.27 | 1.39 | 1.37 | 1.38 | 1.28 | 1.38 | 1.41 | 1.41 | 1.37 | 1.40 |
3 | Степень кристалличности, % | 80.6 | 93.0 | 82.0 | 82.2 | 77.5 | 83.2 | 80.0 | 83.3 | 72.6 | 82.1 |
4 | Механическая прочность на раскол, кг/гранулу | – | 4 | 10 | 9 | – | 2 | 2 | 2 | 3 | 3 |
5 | Размеры частиц (по данным СЭМ), мкм | ||||||||||
минимальный | 1.3 | 1.0 | 1.3 | 2.3 | 1.0 | 0.2 | 1.1 | 0.2 | 0.7 | 0.6 | |
максимальный | 2.0 | 3.3 | 2.6 | 8.5 | 2.5 | 3.9 | 3.4 | 4.0 | 3.3 | 7.7 |
Ионный обмен проводили в среде водных растворов солей во вращающемся автоклаве (1 об./с) при температуре 155°С в течениe 6 ч, т.е. методом гидротермального синтеза. Прокаливание образцов катализатора осуществляли после последнего ионного обмена (1.5 ч при 300°C и 2.5 ч при 450°C в атмосфере воздуха).
Образцы катализаторов. На основе четырех исходных отечественных цеолитов после ионных обменов в растворах солей нитратов кальция, лантана и аммония было приготовлено 6 образцов катализаторов (табл. 1):
– 1.1 – образец катализатора, полученный на основе цеолита 1 без связующего методом прессования;
– 2.1, 2.2 и 2.3 – образцы катализаторов, полученные на основе цеолита 2, гранулированного без связующего вещества;
– 3.1 – образец катализатора, полученный на основе цеолита 3, формованного со связующим (глина, 30%),
– 4.1 – образец катализатора, полученный на основе цеолита 4, формованного со связующим (гидроксид алюминия, 30%).
Физико-химические методы исследования образцов катализаторов
Анализ химического состава катализаторов проводили с использованием волнового рентгенофлуоресцентного спектрометра ARL PERFORM’X 2500 (ThermoFisherScientific). Для анализа образцы катализаторов (навеска 200 мг) прессовали (в виде таблеток) с борной кислотой.
Механическую прочность на раскол определяли путем их раскалывания на ноже или раздавливания на пластине в соответствии с СТО 04610600-008-2007 на приборе HOUNSFIELD марки H5KS. Механическую прочность катализатора измеряли силой, под действием которой гранула катализатора разрушается клиновидным ножом либо путем ее сжатия в условиях нагружения с постоянной скоростью.
Фазовый состав определяли на рентгеновской установке Rigaku Rotaflex RU-200 с вращающимся медным анодом в режиме 50 кВ–160 мА (CuKα-излучение, Ni-фильтр). С помощью горизонтального гониометра по схеме Брэгга–Брентано в режиме θ–2θ-сканирования проводили рентгеновскую съемку. В качестве детектора использовали сцинтилляционный счетчик.
Определение морфологии проводили методом сканирующей электронной микроскопии (СЭМ) на настольном электронном микроскопе Hitachi TM3030.
Каталитические исследования образцов катализаторов
Исследование каталитических свойств катализаторов осуществляли на лабораторной проточной установке алкилирования изобутана бутиленами со стационарным слоем катализатора в режиме “АСР” (алкилирование в “структурированном” режиме) по методу, описанному в [1, 6, 11], в условиях: температура 80°С, давление 1.23 МПа, объемная скорость подачи сырья по олефинам 0.6 ч–1, продолжительность подачи сырья 4 ч.
Критерием для сравнительной оценки каталитических свойств катализаторов служило достижение следующих показателей: активность – конверсия бутиленов – максимум 100% и выход алкилата от бутиленов в сырье от теоретического максимума 100 мас. %; селективность – содержание в алкилате – триметилпентаны (ТМП) – максимум 100 мас. %; диметилгексаны – минимум 0 мас. %; суммарное содержание УВ, выкипающих выше изооктановой фракции, – минимум 0 мас. %.
Конверсия бутиленов (Х(Б)) – отношение количества превращенных бутиленов к взятым, характеризует полноту использования бутиленов в сырье:
Выход алкилата (η(АБ)) от бутиленов в сырье – выход продукта реакции (алкилата) при расчете на бутилены, содержащиеся в сырье:
Селективность реакции δ(ИЗО) – относительная концентрация изооктановой фракции в расчете на продукты реакции, %:
где C(ИЗО) – концентрация изооктановой фракции в продукте, мас. %, C(прод.) – общая концентрация продуктов реакции, мас. %.РЕЗУЛЬТАТЫ И ИХ ОБСУЖДЕНИЕ
Известно [7, 12–15], что в реакции алкилирования изобутана бутиленами катализаторы на основе цеолитов обладают высокой каталитической активностью при максимально возможном замещении катионов натрия на катионы кальция, аммония и редкоземельных элементов при сохранении исходной кристаллической структуры. Это достигается с помощью высокоэффективного ионного обмена, в частности, гидротермальным синтезом, полноту которого контролируют по элементному составу катализаторов (табл. 1).
После ионного обмена внешняя форма образцов катализаторов не отличалась от исходных цеолитов. Однако у цеолитов со связующим компонентом наблюдаются потери массы: при использовании цеолита 3 она составляла 25 мас. %, для цеолита 4–10 мас. %. Потери также отражаются на размере экструдата (длина и диаметр уменьшились). Например, у исходного цеолита 3 диаметр составлял 3 мм, а длина – от 4 до 10 мм; после ионного обмена размеры образца катализатора 3.1 изменились (диаметр 2 мм, длина – от 3 до 9 мм).
Маточный раствор (табл. 2) образцов 3.1 и 4.1 содержит в своем составе оксиды кремния (16.7–44.7 мас. %) и алюминия (10.0–28.0 мас. %), что подтверждает унос цеолита в образцах со связующим веществом в ходе гидротермального синтеза.
Таблица 2.
Химический состав маточных растворов образцов катализаторов
п/п | Состав маточных р-ров, мас. % | Обозначение образцов | |||||
---|---|---|---|---|---|---|---|
1.1 | 2.1 | 2.2 | 2.3 | 3.1 | 4.1 | ||
1 | SiO2 | 1.7 | 0.5 | 18.6 | 3.2 | 44.7 | 16.7 |
2 | Al2O3 | 0.6 | 0.4 | 13.0 | 2.0 | 28.0 | 10.0 |
3 | La2O3 | 66.9 | 94.5 | 38.9 | 71.6 | 20.5 | 48.4 |
4 | CaO | 12.3 | 1.2 | 13.3 | 9.8 | 2.0 | 10.8 |
5 | Na2O | 13.8 | 1.2 | 11.0 | 10.9 | 1.3 | 11.1 |
6 | Прочие оксиды* | 4.7 | 2.2 | 5.2 | 2.5 | 3.5 | 3.0 |
Выпаренный осадок в маточном растворе, мас. доля | 0.04 | 0.03 | 0.03 | 0.04 | 0.25 | 0.10 |
Для образца катализатора 2.2 наблюдается значительное содержание SiO2 и Al2O3 18.6 и 13.0 мас. %, соответственно, что подтверждает некоторое разрушение структуры цеолита и снижение степени кристалличности до 80% (степень кристалличности в исходном цеолите составляет 93%).
Мольное соотношение Si/Al в цеолитах типа фожазит – однa из основных контролируемых характеристик цеолитов в производстве [16]. Мольные соотношения исходных цеолитов и образцов катализаторов, полученных на их основе, различаются незначительно (табл. 1).
Степень кристалличности является еще одной характеристикой катализаторов на основе цеолитов, которую необходимо контролировать в ходе их формовки, синтеза и т.д. Анализ дифрактограмм (рис. 2) показал частичное разрушение кристаллической структуры цеолитов, что соотносится со снижением степени кристалличности для каждой группы “исходный цеолит – образец катализатора” (табл. 1) и интенсивности рефлексов при 6°, 16° и 27° [7, 18], наиболее характерных для цеолита NaX для всех образцов катализаторов. Соответственно наблюдается изменение кристаллической структуры. Это происходит в равной степени в ходе ионного обмена для всех образцов. Искажение цеолитного каркаса происходит, видимо, из-за введения в структуру катионов La3+ и [La(OH)]2+ [19].
Период решетки полученных образцов составляет 24.91–25.04 Å, что превышает полученный в работе [20] размер решетки 24.3 Å.
Механическая прочность – эксплуатационная характеристика катализаторов. У гранулированных и формованных цеолитов она различна (табл. 2). У формованных со связующим цеолитов 3 и 4 она выше (10 и 9 кг/гранула соответственно), чем у гранулированного без связующего 2 (4 кг/гранула). Это связано со свойствами, которые вносит связующее вещество. Аналогичная ситуация наблюдается у синтезированных образцов катализаторов со связующим (для образцов 3.1 и 4.1 – 3 кг/гранула) и без связующего (образцы 2.1, 2.2 и 2.3 – 2 кг/гранула).
Структуру поверхности изучали с помощью электронного микроскопа [21]. На рис. 3 представлены микрофотографии СЭМ исходных цеолитов и образцов катализаторов.
На микрофотографиях у цеолита 1 (рис. 3а) наблюдается однородное распределение частиц кубической формы. Цеолит 3 имеет частички кубической формы с чешуйчатыми и листовыми образованиями (рис. 3ж). Вероятно, последние принадлежат связующему компоненту. Аналогичное распределение частиц на микрофотографиях наблюдается у образцов катализаторов 1.1 и 3.1, приготовленных на основе указанных выше цеолитов 1 и 3 (рис. 3б и 3з соответственно). Распределение частиц на микрофотографиях цеолитов 2 и 4, образцов катализаторов 2.1, 2.2, 2.3 и 4.1 имеет более широкий диапазон значений (0.2–7.7 мкм).
Рис. 3.
Микрофотографии СЭМ исходных цеолитов и образцов катализаторов: (а) 1; (б) 1.1; (в) 2; (г) 2.1; (д) 2.2; (е) 2.3; (ж) 3; (з) 3.1; (и) 4; (к) 4.1.
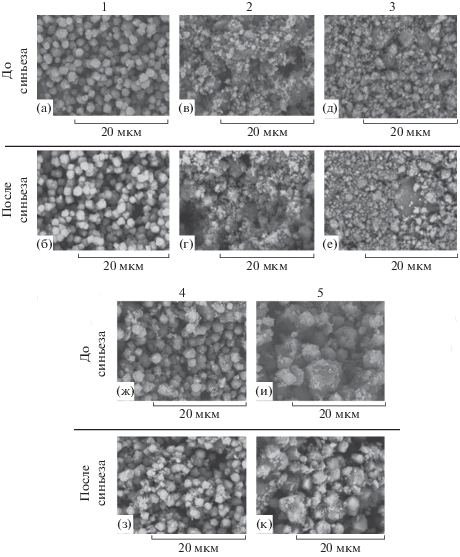
Из микрофотографий видно, что для катализаторов на основе цеолитов без связующего вещества морфология после гидротермального синтеза практически не меняется, в то время как в образцах со связующим веществом размер частиц становится меньше (табл. 1).
На рис. 4 представлены каталитические показатели в зависимости от размера частиц по данным СЭМ.
Рис. 4.
Показатели образцов (1.1, 2.1, 2.2, 2.3, 3.1, 4.1) катализаторов в реакции алкилирования изобутана бутиленами в зависимости от размера частиц, где: конверсия (◼), выход алкилата (▲), селективности по ТМП (⚫), С8-прочие (–) и ΣС9+ (◆).
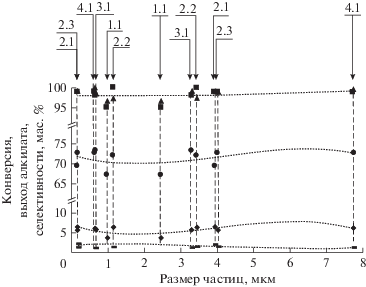
По указанным критериям наблюдаются две области с наилучшими показателями (рис. 4): до 0.8 мкм и свыше 3.5 мкм, при довольно жестких условиях эксперимента (объемная скорость подачи сырья по бутиленам 0.6 ч–1) конверсия находилась в пределах 99–100 мас. %, выход алкилата 99–100 мас. %, селективность по ТМП 70–75 мас. %, фракция С9+ не превышала 7 мас. %. При рассмотрении результатов с размером частиц от 0.8 до 3.5 мкм наблюдается ухудшение качества продуктов процесса и снижение выхода алкилата. Например, катализатор на основе прессованного цеолита, обладающий однородным распределением частиц кубической формы размером 1.0–2.5 мкм, имел сравнительно низкие показатели: конверсию 96 мас. %, выход алкилата на бутилены 97 мас. % и селективность по ТМП 69 мас. %. Полученные результаты не показали однозначного влияния связующего вещества на каталитическую активность образцов в зависимости от размера частиц катализатора. Тем не менее, можно отметить, что частицы размером выше 4.5 мкм свойственны только катализатору на основе цеолита с 30% гидроксида алюминия в качестве связующего вещества.
В целом оптимальный катализатор алкилирования должен иметь распределение частиц, размер которых не выше 0.8 мкм и/или больше 3.5 мкм, что способствует получению качественного алкилата с высокими значениями по выходу алкилата и конверсии бутиленов.
ЗАКЛЮЧЕНИЕ
Исследовано влияние морфологии цеолитных катализаторов в CaLaHХ форме на основе отечественных цеолитов. Методом сканирующей электронной микроскопии установлено, что условия приготовления катализаторов не изменяют структуру их поверхности. Показано, что в ходе гидротермального синтеза цеолитов со связующим компонентом происходит потеря их массы до 25 мас. %. Анализы маточного раствора показали, что происходит вымывание связующего вещества и цеолита. Показано, что происходит частичное разрушение кристаллической решетки, которое приводит к некоторому снижению механических свойств образцов. Оптимальные показатели реакции алкилирования (конверсия бутиленов 98–100 мас. %, выход алкилата близок к теоретическому 99–100 мас.%, селективность по ТМП около 72 мас. %, С8-прочие не превышают 1.5 мас. %) достигаются при размере частиц катализаторов в двух диапазонах до 0.8 и/или выше 3.5 мкм. Лучшие показатели у катализатора, синтезированного на основе цеолита, гранулированного без связующего.
Список литературы
Герзелиев И.М., Цодиков М.В., Хаджиев С.Н. // Нефтехимия. 2009. Т. 49. № 1. С. 3 [Petrol. Chemistry. 2009. V. 49. № 1. P. 59].
Aschauer S., Schilder L., Korth W., Fritchi S., Jess A. // Catal. Letters. 2011. V. 141. № 10. P. 1405.
Brelsford R. // Oil Gas J. 2019. V. 117. № 1. P. 98.
Hsu C.S., Robinson P.R. Handbook of Petroleum Technology. Springer, 2017. P. 551.
Feller A., Lercher J.A. // Adv. Catal. 2004. V. 48. P. 229.
Герзелиев И.М., Остроумова В.А., Басханова М.Н., Саитов З.А., Темникова В.А., Хусаимова Д.О. // Нефтехимия. 2017. Т. 57. № 6. С. 205 [Petrol. Chemistry. 2017. V. 57. № 12. P. 1182].
Герзелиев И.М., Остроумова В.А., Басханова М.Н. // Нефтехимия. 2018. Т. 58. № 4. С. 469 [Petrol. Chemistry. 2018. V. 58. № 8. P. 676].
Хаджиев С.Н., Герзелиев И.М., Ведерников О.С., Клейменов А.В., Кондрашев Д.О., Окнина Н.В., Кузнецов С.Е., Саитов З.А., Басханова М.Н // Катализ в промышленности. 2016. Т. 6. С. 42.
Трапезникова Е.Ф., Смольникова Т.В., Хафизова С.Р., Николаева Т.В., Нурисламова Р.Р. // Сетевое издание “Нефтегазовое дело”. 2018. № 4. С. 117.
Li Y., Liu R., Zhao G., Zhou Zh., Zhang J., Shi Ch., Liu X., Zhang X., Zhang S. // Fuel. Elsevier. 2018. V. 216. P. 686.
Хаджиев С.Н., Герзелиев И.М., Окнина Н.В., Кузьмин А.Е., Саитов З.А. // Патент РФ № 2637922. 2017.
Хаджиев С.Н., Герзелиев И.М. // Патент РФ № 2445165. 2012.
Несмеянова Т.С., Мирский Я.В., Калико М.А., Чередниченко В.Т. // Труды ГрозНИИ. Технология нефти. Катализ и адсорбция на цеолитах. 1975. Т. XXIX. С. 77.
Размахнин К.К., Хатькова А.Н. // Горный информационно-аналитический бюллетень (научно-технический журнал). 2011. Т. 4. С. 246.
Ковальская Л.В., Александрова И.Л., Байбурский В.Л. // Сб. научных трудов ГрозНИИ. Алкилирование изопарафиновых и ароматических углеводородов. 1980. С. 103.
Мегедь Н.Ф., Сидерман В.И., Мирский Я.В. // Труды ГрозНИИ. Технология нефти. Катализ и адсорбция на цеолитах. 1974. Т. XXVII. С. 87.
Кипнис М.А., Сухореброва О.А., Герзелиев И.М., Родионова, Л.И., Белова, М.В., Коротков А.С. // Нефтехимия. 2015. Т. 55. № 2. С. 134 [Petrol. Chemistry. 2015. Т. 55. № 2. С. 127].
Olson D.H. // J. Phys. Chem. 1970. V. 74. № 14. P. 2758.
Sievers C., Liebert J.S., Stratmann M.M., Olindo R., Lercher J.A. // Appl. Catal. A Gen. 2008. V. 336. № 1–2. P. 89.
Corma A., Martínez A., Martínez C. // J. Catal. 1994. V. 146. № 1. P. 185.
Крылов О.В. Гетерогенный катализ. М.: ИКЦ “Академкнига”, 2004. 679 с.
Дополнительные материалы отсутствуют.