Нефтехимия, 2020, T. 60, № 1, стр. 34-43
Влияние размерного фактора на активность цеолитов в реакции жидкофазного крекинга углеводородов
К. И. Дементьев 1, *, Т. А. Паланкоев 1, П. С. Кузнецов 1, Д. С. Абрамова 1, 2, Д. А. Ромазанова 1, 2, Д. Ю. Махин 1, 2, А. Л. Максимов 1, 2
1 Институт нефтехимического синтеза им. А.В. Топчиева РАН
119991 Москва, Россия
2 Московский государственный университет имени М.В. Ломоносова
119991 Москва, Россия
* E-mail: kdementev@ips.ac.ru
Поступила в редакцию 17.08.2019
После доработки 05.09.2019
Принята к публикации 09.09.2019
Аннотация
Проведено исследование каталитической активности диспергированных в реакционной среде цеолитов типа FAU, MFI и BEA с различным соотношением SiO2/Al2O63 в реакции жидкофазного крекинга н-алканов при температуре 300–350°С и давлении водорода 7 атм. Наивысшую активность проявил катализатор на основе цеолита типа BEA с соотношением SiO2/Al2O3, равным 75. Показано, что основным фактором, определяющим активность цеолитов в этих условиях, является удельная площадь поверхности частиц катализатора размером менее 200 нм.
ВВЕДЕНИЕ
Цеолиты являются важнейшим классом материалов для осуществления реакций, катализируемых кислотами. Основная особенность цеолитов – наличие упорядоченной структуры с развитой системой пор и, как следствие, большой удельной поверхности. Размер пор большинства цеолитов лежит в диапазоне 3–8 Å, что обеспечивает возможность превращения органических соединений различных классов с высокой селективностью [1].
С другой стороны, при использовании цеолитов для превращения крупных молекул (например, асфальтенов) или не углеводородных молекул с карбонильными группами, возникает проблема быстрой дезактивации катализатора. Снижение активности происходит из-за закупорки пор молекулами субстрата или продуктами его превращения, что приводит к резкому снижению доступной для реакции поверхности катализатора. Для решения этой проблемы существует ряд подходов.
Первый подход состоит в управлении пористой структурой катализатора. В рамках этого подхода разработаны способы модифицирования цеолита для увеличения в нем доли мезопор (термопаровая обработка [2], десиликатизация/ деалюминирование [3, 4] или перекристаллизация цеолита [5]), либо формирование композитных структур типа “ядро−оболочка”, состоящих одновременно из микро- и мезопористых материалов [6].
В рамках второго подхода развивается синтез цеолитов с кристаллами размером 20–100 нм. Применение нанокристаллических цеолитов в катализе позволяет повысить их удельную активность за счет увеличения внешней поверхности и облегчения транспорта молекул реагентов и продуктов реакции как в порах цеолитов, так и между кристаллами.
Альтернативным подходом к решению проблемы дезактивации цеолитных катализаторов в процессе катализа может быть снижение размера зерна катализатора до размера кристалла. Такой метод позволит существенно увеличить внешнюю поверхность катализаторов и потому снизить скорость дезактивации [7]. Основная проблема подхода – сложность обеспечения агрегативной устойчивости цеолитов – может быть решена путем проведения реакции в жидкой среде, в которой возможно использование нанокатализатора в виде суспензии. В качестве подобной среды может выступать инертная жидкость или непосредственно реакционный субстрат. Возможность эффективной стабилизации дисперсий наночастиц показана для процессов гидроконверсии [8], синтеза Фишера–Тропша [9], реакций превращения диметилового эфира [10], гидрирования [11], крекинга углеводородов [12, 13].
Протекание кислотнокатализируемых реакций в жидкой фазе имеет свои особенности по сравнению с катализом в газовой фазе. Так, на примере альдольной конденсации бензальдегида с гептаналем показано [14–16],что определяющим фактором является морфология катализатора, а не его кислотные свойства. Подобный вывод был получен и в работе [17], где повышение соотношения SiO2/Al2O3 для цеолита HY приводило к увеличению каталитической активности цеолита в реакции этерификации уксусной кислоты различными спиртами вследствие возрастания доли мезопор в структуре катализатора.
В научной литературе сведения о факторах, обуславливающих активность цеолитов в катализе превращений углеводородов (УВ) в жидкой фазе, практически отсутствуют. Известен цикл работ об использовании нанодисперсий цеолитов в УВ в контексте разработки подходов к получению эндотермического топлива [18–21]. С использованием ряда техник, в том числе, силанизации, был приготовлен цеолит HZSM-5 с размером частиц порядка 300 нм с размером кристалла порядка 20–40 нм. При использовании в качестве нанодисперсного катализатора такой цеолит проявил на 30% большую крекирующую активность в реакции крекинга н-додекана в сверхкритических условиях, чем немодифицированный HZSM-5.
Ранее нами было показано [22], что цеолит типа BEA обладает высокой активностью в реакции жидкофазного крекинга н-алканов, причем корреляция каталитической активности цеолитов с их кислотными и текстурными характеристиками не наблюдалась. Настоящая работа направлена на изучение основных особенностей жидкофазного крекинга н-алканов как модельных субстратов, катализируемого дисперсиями цеолитов типа FAU, MFI, BEA с различным соотношением SiO2/Al2O3, и выявление основных факторов, определяющих каталитическую активность таких систем.
ЭКСПЕРИМЕНТАЛЬНАЯ ЧАСТЬ
Приготовление катализаторов. В качестве основы для катализаторов крекинга использовались стандартные порошки цеолитов со структурой FAU, MFI, BEA и различным соотношением SiO2/Al2O3 производства компании Zeolyst (табл. 1). Также применялся цеолит ИК-17-1 производства ПАО “НЗХК”. Так как ряд цеолитов изначально находится в аммонийной форме, перед дальнейшим использованием все образцы подвергались прокалке при 550°С в токе воздуха в течение 5 ч. После прокалки проводилось измельчение цеолитов на шаровой мельнице MLWKM1 в одинаковых условиях: загрузка цеолита 200 мг, время размола 40 мин при максимальной мощности.
Таблица 1.
Перечень и некоторые свойства используемых в работе цеолитов (по данным производителей)
Маркировка | Марка | Тип | Катион | Мольное соотношение SiO2/Al2O3 | Содержание Na, % | Sуд*, см2/г |
---|---|---|---|---|---|---|
FAU5 | CBV500 | Y | ${\text{NH}}_{4}^{ + }$ | 5.2 | 0.15 | 750 |
FAU12 | CBV712 | ${\text{NH}}_{4}^{ + }$ | 12.0 | 0.04 | 730 | |
FAU80 | CBV780 | H+ | 80.0 | 0.02 | 700 | |
BEA75 | CP-811E-75 | Beta | H+ | 75.0 | 0.04 | 620 |
BEA150 | CP-811E-150 | H+ | 150.0 | 0.04 | 620 | |
BEA300 | CP811C-300 | H+ | 300.0 | 0.04 | 620 | |
MFI30 | ИК-17-1 | ZSM-5 | H+ | 28.0–37.8 | <0.12 | >300 |
MFI80 | CBV8014 | ${\text{NH}}_{4}^{ + }$ | 80.0 | 0.004 | 425 |
Исследование катализаторов. Определение размера частиц цеолитов и их распределения проводилось двумя способами. По первому способу проводилась микросъемка порошков цеолитов с помощью просвечивающей электронной микроскопии (ПЭМ) на электронном микроскопе LEO 912 AB Omega (CarlZeiss, Германия) с ускоряющим напряжением 100 кВ. Полученные микрофотографии использовались для подсчета частиц и построения распределения их по размерам.
По второму способу распределение по размерам частиц определялось методом динамического светорассеяния (DLS). Для измерений 15 мг порошка цеолита взвешивали в 1.5–2.0 мл н-гексадекана в присутствии 1% SPAN-80, после чего дисперсию подвергали обработке в ультразвуковой ванне Elmasonic P30H в течение 20 мин при частоте 80 кГц и мощности 100 Вт. Полученную дисперсию далее исследовали на приборе ZetasizerNanoZS (компании Malvern). Источником света служил гелий-неоновый лазер с длиной волны с длиной волны 633 нм.
Фазовый состав образцов цеолитов определяли с помощью рентгеновского спектрометра RigakuRotaflex RU-200 с вращающимся медным анодом (излучение CuKα с Ni-фильтром) в режиме 50 kВ/160 мА. Спектры записывали с помощью горизонтального широкоуглового гониометра по геометрии Брегга–Бретано в режиме сканирования θ–2θ.
Элементный состав определяли с помощью рентгенофлуоресцентного спектрометра ARLPERFORM’X 2500 (ThermoFischerScientific), оборудованноо рентгеновской трубкой 2500 В.
Текстурные характеристики цеолитов исследовали методом низкотемпературной адсорбции азота с помощью прибора Micromeritics ASAP 2020. Свойства образцов рассчитывались с помощью стандартного программного обеспечения. Удельную площадь поверхности рассчитывали по модели Брунауэра–Эмметта–Теллера (БЭТ) при относительном парциальном давлении азота P/P0 = 0.17. Объем пор рассчитывался по модели Barrett–Joyner–Halenda (BJH) при относительном парциальном давлении азота P/P0 = 0.95. Объем микропор определялся по методу t-plot.
Характеристика кислотности образцов проводилась методом термопрограммированной десорбции аммиака (ТПД NH3) с использованием анализатора хемосорбции УСГА-101 (“УНИСИТ”, Россия). Спектры десорбции аммиака снимали в диапазоне температур 60–750°С при нагреве со скоростью 8°С/мин до 750°С в потоке гелия (30 мл/мин). Выделяющийся аммиак регистрировался детектором по теплопроводности. Расчет количества десорбированного аммиака производился с учетом предварительной калибровки прибора УСГА-101.
Каталитические эксперименты. Для исследования активности катализаторов использовали установку с реактором автоклавного типа, проточную по газу и снабженную механической мешалкой (рис. 1), подробное описание которой приведено в [22]. В реактор загружали 0.7–0.8 г катализатора, после чего заливали 100 мл парафина П-2 (ГОСТ 23683-89) при температуре 110°С; таким образом, содержание катализатора в дисперсионной среде для всех экспериментов составляет 1%. Парафин содержал свыше 98% алканов С20–С35 нормального строения; его молекулярно-массовое распределение приведено на рис. 2.
Для оценки протекающего при температуре реакции термического крекинга парафина проводили серию экспериментов в отсутствие катализатора. Активность цеолитов при заданной температуре Т в крекинге рассчитывали с учетом образования продуктов в термическом крекинге по формуле:
Анализ газового продукта осуществляли на хроматографе “Кристаллюкс-4000М” с детектором ПИД/ДТП по двухколоночной схеме. Неуглеводородные газы, водород и метан разделяли на насадочной колонке с молекулярным ситом типа CaX (3 м × 3 мм), УВ С1–С6 определяли на капиллярной колонке HP-PlotAl2O3/Na2SO4 (Agilent, 50 м, 0.32 мм). Анализ жидкого продукта проводили на хроматографе “Кристаллюкс-4000М”, оснащенном капиллярной колонкой длиной 25 м с фазой типа OV-101.
РЕЗУЛЬТАТЫ И ИХ ОБСУЖДЕНИЕ
Изучение катализаторов. По данным рентгенофазового анализа все используемые в работе цеолиты соответствует своим структурным типам (спектры приведены в разделе Дополнительная информация http://neftekhimiya.ips.ac.ru/***, рис. Д1–Д3). Текстурные характеристики и данные по элементному составу приведены в табл. 2. Содержание натрия во всех образцах в целом соответствует заявленному производителем и находится в допустимом для декатионированных цеолитов диапазоне (менее 0.2%).
Таблица 2.
Текстурные характеристики катализаторов
Образец | SiO2/Al2O3 (мольн.) | Na, % | Удельная площадь поверхности, м2/г | Удельный объем пор, м3/г | ||||
---|---|---|---|---|---|---|---|---|
Sмикро | Sмезо | Σ | Vмикро | Vмезо | Σ | |||
FAU5 | 5.7 | 0.17 | 445.5 | 58.2 | 503.7 | 0.189 | 0.071 | 0.260 |
FAU12 | 12.3 | 0.07 | 544.1 | 140.9 | 685.0 | 0.238 | 0.164 | 0.402 |
FAU80 | 91.4 | 0.07 | 411.2 | 219.4 | 630.6 | 0.180 | 0.196 | 0.376 |
BEA75 | 70.5 | 0.07 | 365.2 | 213.5 | 578.7 | 0.159 | 0.461 | 0.620 |
BEA150 | 140.6 | 0.13 | 349.4 | 196.5 | 545.9 | 0.152 | 0.416 | 0.568 |
BEA300 | 230.1 | 0.06 | 401.8 | 178.3 | 580.1 | 0.176 | 0.151 | 0.327 |
MFI30 | 35.1 | 0.09 | 261.6 | 70.3 | 331.9 | 0.113 | 0.051 | 0.164 |
MFI80 | 73.7 | 0.03 | 238.3 | 167.5 | 405.8 | 0.100 | 0.132 | 0.232 |
Текстурные характеристики цеолитов также соответствуют паспортным характеристикам; удельная площадь поверхности на 5–15% ниже заявленных, что может быть связано с частичной аморфизацией цеолитов при прокалке. Наиболее развитой поверхностью обладают цеолиты типа Y (630–685 м2/г), наименьшей – цеолиты типа ZSM-5 (менее 450 м2/г). Увеличение соотношения SiO2/Al2O3 в рамках каждого структурного типа приводит к некоторому повышению доли мезопор, что коррелирует с литературными данными [23].
Кислотные свойства образцов катализаторов существенно различаются в зависимости от типа цеолита и соотношения SiO2/Al2O3 (табл. 3, http://neftekhimiya.ips.ac.ru/***, рис. Д4–Д6). К слабым относили кислотные центры с температурой десорбции аммиака менее 300°С, к сильным – с температурой десорбции аммиака более 300°С. Наибольшей кислотностью обладает образец MFI30 (1323 мкмоль NH3/г), причем положение максимумов пиков на спектрах десорбции аммиака для данного образца сдвинуто в область более сильных кислотных центров. Цеолиты других типов имеют несколько меньшую кислотность, причем увеличение соотношения SiO2/Al2O3 способствует снижению кислотности за счет уменьшения числа атомов алюминия врешетке цеолита.
Таблица 3.
Кислотные свойства катализаторов
Кислотность, мкмоль NH3/г | |||
---|---|---|---|
слабые центры | сильные центры | Σ | |
FAU5 | 325 | 219 | 544 |
FAU12 | 397 | 425 | 822 |
FAU80 | 57 | 97 | 154 |
BEA75 | 230 | 246 | 476 |
BEA150 | 85 | 73 | 158 |
BEA300 | 69 | 58 | 127 |
MFI30 | 575 | 748 | 1323 |
MFI80 | 245 | 290 | 535 |
Рис. 6.
Зависимость каталитической активности образцов катализаторов от кислотности (а) и удельной площади поверхности (б).
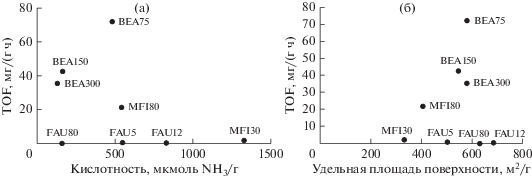
Микрофотографии ряда образцов приведены на рис. 3, а результаты измерения размера частиц катализаторов двумя методами представлены в табл. 4. Можно отметить, что размер частиц, определенный по микрофотографиям ПЭМ и по данным DLS несколько различается. Первый метод показывает наличие бимодального распределения частиц по размерам для всех катализаторов; для цеолитов с наибольшим соотношением SiO2/Al2O3 в каждой линейке структурных типов также наблюдается наличие крупных частиц с размером более 300–400 нм. Распределение, рассчитанное по данным DLS, мономодальное, причем значение максимума распределения несколько выше, чем получаемое подсчетом частиц по микрофотографиям. Такое расхождение двух методов объясняется одновременно двумя причинами: во-первых, частицы цеолитов в среде углеводорода образуют агломераты, во-вторых, в рамках метода DLS фиксируется зависимость интенсивности светорассеяния от размера частиц. Как известно, крупные частицы рассеивают свет значительно лучше мелких, что и приводит к сдвигу положения максимума светорассеяния в область бόльших размеров частиц. Хотя существуют методы пересчета данных по распределению размера частиц по интенсивности и распределение по объему или числу частиц, их применение приводит к потере значительной части количественной информации, поэтому в данной работе используется распределение размеров частиц по интенсивности светорассеяния. Тем не менее, наличие корреляции между данными, полученными по двум методам, очевидно. Наименьшим размером частиц обладают цеолиты BEA75 и BEA150, наибольшим – цеолиты типа FAU, размер частиц которых составляет свыше 500 нм. Цеолиты типа MFI занимают в этом ряду промежуточное положение.
Таблица 4.
Размер частиц образцов катализаторов
Образец | Средний размер частиц, нм | |
---|---|---|
по данным ПЭМ | по данным DLS | |
FAU5 | 200/400 | 500.0 |
FAU12 | 100/260/440 | 527.5 |
FAU80 | 160/300/450 | 842.2 |
BEA75 | 70/130 | 232.0 |
BEA150 | 90/175 | 229.3 |
BEA300 | 80/140/400 | 470.9 |
MFI30 | 120/170 | 259 |
MFI80 | 110/430 | 361.5 |
Фракционный состав катализаторов (рис. 4) существенно различается для всех образцов. Катализаторы типа FAU более, чем на 70%, состоят из частиц размером более 200 нм, доля частиц менее 100 нм не превышает 6%. Образцы цеолитов типа BEA, напротив, содержат в основном частицы размером менее 200 нм, причем во всех образцах обнаруживаются частицы размером менее 50 нм. Цеолиты типа MFI по фракционному составу находятся ближе к цеолитам типа BEA; образец MFI80 практически соответствует образцу BEA150. Необходимо отметить, что корреляция между фракционным составом и соотношением SiO2/Al2O3 образцов отсутствует даже в рамках одного структурного типа.
Изучение каталитической активности цеолитов. По удельной каталитической активности все образцы существенно отличаются друг от друга (рис. 5). Наименее активными являются катализаторы типа FAU, показатель TOF при 350°С для них находится в диапазоне от 93.5 мг/(г ч) (FAU80) до 1000 мг/(г ч) (FAU5). Катализатор MFI30 обладает средней активностью, которая составляет 2108 мг/(г ч). Наконец, все образцы структурного типа BEA и образец MFI80 являются высокоактивными – показатель TOF для них лежит в диапазоне 20 000–80 000 мг/(г ч).
Как правило, для газофазных реакций активность прежде всего зависит от кислотности и текстурных характеристик катализатора, в жидкофазных условиях на первый план выходит удельная поверхность мезопор [16]. Полученные нами данные свидетельствуют о низкой степени корреляции между каталитической активностью и кислотными свойствами (рис. 6а) и удельной площадью поверхности (рис. 6б), что подтверждает выводы более ранней работы [22]. Вместе с тем, была найдена взаимосвязь между фракционным составом катализаторов и каталитической активностью: последняя существенно увеличивается вместе с удельной поверхностью частиц катализаторов размером менее 200 нм, рассчитываемой как произведение доли частиц на общую удельную площадь поверхности (рис. 7). Повышение удельной поверхности образцов и увеличение доли мелких частиц приводит к резкому увеличению каталитической активности в реакции жидкофазного крекинга алканов нормального строения. По всей видимости, данный результат объясняется существенным снижением диффузионных ограничений и большей доступностью внутренней поверхности частиц размером менее 200 нм для молекул субстрата.
Рис. 7.
Зависимость каталитической активности образцов катализаторов при 300°С (а) и при 350°С (б) от удельной площади поверхности частиц размером менее 200 нм.
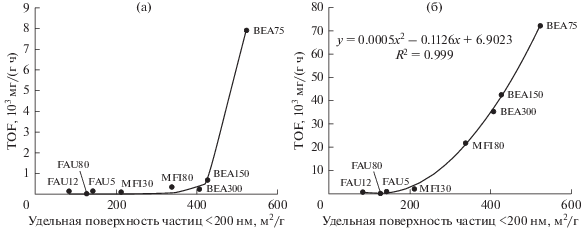
Повышение температуры реакции с 300 до 350°С приводит к резкому росту активности катализаторов в крекинге. Активность цеолитов типа FAU и BEA75 повышается на порядок, цеолита BEA300 – на два порядка; все остальные цеолиты занимают промежуточное положение в этом ряду. По всей видимости, при 300°С большое значение играет роль диффузионное торможение, ослабляющееся при повышении температуры. Следует отдельно отметить, что зависимость активности при 300°С (рис. 7а) от удельной поверхности имеет характер экспоненты, в то время как при температуре 350°С (рис. 7б) зависимость между активностью и удельной поверхностью лучше аппрокисимируется параболой. Это также может быть обусловлено различием в области протекания реакций.
Групповой состав жидких продуктов крекинга также, как и активность, слабо зависит от кислотных свойств катализаторов (рис. 8). Основным фактором, определяющим состав продуктов, является, по всей видимости, пористая структура катализаторов. В присутствии широкопористых цеолитов типа FAU и BEA с входным размером пор свыше 6 Å доля разветвленных и циклических углеводородов в продуктах крекинга составляет свыше 70%. В случае узкопористого цеолита MFI доля разветвленных снижается до 50–60%.
С повышением активности цеолита соотношение газ/жидкость, и, соответственно, относительный выход газа, существенно снижается (рис. 9). Низкоактивные катализаторы (цеолиты FAU, MFI30) способствуют образованию газообразных УВ, в то время как активные (BEA, MFI80) сдвигают селективность реакций крекинга в сторону жидких УВ. Основные свойства газа крекинга приведены в табл. 5. Для всех цеолитов наблюдается существенное отличие от термического крекинга – повышается доля олефинов, в разы увеличивается доля изомерных структур. Во всех случаях соотношение бутилены/бутаны составляет 0.86–0.90, что является показателем активности цеолитов в жидкофазном крекинге [22]. Для каждого типа цеолита характерен специфичный состав газовой фракции: цеолиты типа FAU более селективны в отношении пропилена, MFI – этилена, BEA – изобутана и изобутилена. Увеличение соотношения SiO2/Al2O3 в рамках каждого структурного типа приводит к изменению углеводородного состава газа: для цеолитов MFI соотношение этилен/этан увеличивается с 2.79 до 8.54, для цеолитов FAU соотношение пропилен/пропан повышается с 1.61 до 5.17, для цеолитов BEA соотношение бутилены/бутаны увеличивается с 0.86 до 0.90. Увеличение соотношения олефин/парафин во всех случаях коррелирует со снижением кислотности цеолита и, соответственно, уменьшением интенсивности протекания реакций переноса водорода. Интересно отметить, что состав газа крекинга в жидкой фазе заметно отличается от состава газофазного крекинга на коммерческом катализаторе. Для жидкофазного крекинга характерно повышенное соотношение пропилен/пропан, изо-C4/н-C4 и пониженное соотношение бутилены/бутаны.
Таблица 5.
Свойства газа крекинга (350°С)
Терм. | Кат. [24] | FAU5 | FAU12 | FAU80 | BEA75 | BEA150 | BEA300 | MFI30 | MFI80 | |
---|---|---|---|---|---|---|---|---|---|---|
С2=/С2 | 0.18 | 1.50 | 1.21 | 1.43 | 0.56 | 2.31 | 2.17 | 2.32 | 2.79 | 8.54 |
С3=/С3 | 0.93 | 0.84 | 1.61 | 2.07 | 5.17 | 1.52 | 1.86 | 1.60 | 1.14 | 0.97 |
С4=/С4 | 0.54 | 1.16 | 0.87 | 0.86 | 0.89 | 0.86 | 0.88 | 0.89 | 0.87 | 0.90 |
изо-C4/н-С4 | 0.21 | 1.10 | 2.27 | 2.13 | 1.62 | 3.38 | 4.13 | 4.83 | 0.69 | 0.58 |
ЗАКЛЮЧЕНИЕ
В работе исследованы закономерности реакции жидкофазного крекинга алканов в присутствии цеолитов типов FAU, MFI и BEA с различным соотношением SiO2/Al2O3. Показано, что наблюдается существенная дисперсия активности различных образцов; цеолиты типа FAU относятся к малоактивным (менее 1000 мг/(г ч)), цеолит типа MFIс соотношением SiO2/Al2O330 проявляет среднюю активность, равную около 2000 мг/(г ч), а все цеолиты типа BEA и цеолит MFI с соотношением SiO2/Al2O3, равным 80, имеют высокую активность – свыше 20 000 мг/(г ч). Статистический анализ показывает, что увеличение активности коррелирует с возрастанием удельной площади поверхности частиц катализатора размером менее 200 нм. По всей видимости, данный результат объясняется резким снижением диффузионных ограничений и высокой доступностью внутренней поверхности мелких частиц для молекул субстрата. Полученные данные открывают путь к направленному синтезу высокоактивных катализаторов превращения углеводородов в жидкой фазе.
Список литературы
Corma A. // J. Catal. 2003. V. 216. № 1–2. P. 298–312.
Guo D., Shen B., Qin Y., Sun J., Guo Q., Ren Sh., Gao X., Pang X., Wang B., Zhao H., Liu H. // Microporous Mesoporous Mater. 2015. V. 211. P. 192.
Qin Z., Shen B., Gao X., Lin F., Wang B., Xu C. // J. Catal. 2011. V. 278. № 2. P. 266.
Yu Q., Sun H., Li L., Zhu X., Ren Sh., Guo Q., Shen B. // Microporous Mesoporous Mater. 2019. V. 273. P. 297.
Kazakov M.O., Nadeina K.A., Danilova I.G., Dik P.P., Klimov O.V., Pereyma V.Yu., Gerasimov E.Yu., Dobryakova I.V., Knyazeva E.E., Ivanova I.I., Noskov A.S. // Catal. Today. 2018. V. 305. P. 117.
Jia L., Sun X., Ye X, Zou Ch., Gu H., Huang Y., Niu G., Zhao D. // Microporous Mesoporous Mater. 2013. V. 176. P. 16.
Khadzhiev S.N. // Petrol. Chemisrty. 2011. V. 51. № 1. P. 3.
Khadzhiev S.N., Kadiev K.M., Kadieva M.K. // Petrol. Chemistry. 2014. V. 54. № 5. P. 323.
Kulikova M.V., Khadzhiev S.N. // Petrol. Chemistry. 2017. V. 57. № 12. P. 1173.
Kolesnichenko N.V., Konnov S.V., Pavlov V.S., Yashina O.V., Ezhova N.N., Khadzhiev S.N. // Petrol. Chemistry. 2017. V. 57. № 7. P. 576.
Kniazeva M., Maximov A. // Catalysts. 2018. V. 8. № 12. P. 644.
Onishchenko M.I., Maksimov A.L. // Petrol. Chemistry. 2018. V. 58. № 8. P. 2018.
Onishchenko M.I., Kulikov A.B., Maksimov A.L. // Petrol. Chemistry. 2017. V. 57. № 14. P. 1287.
Climent M.J., Corma A., Guil-López R., Iborra S., Primo J. // J. Catal. 1998. V. 175. № 1. P. 70
Climent M.J., Corma A., Garcia H., Guil-Lopez R., Iborra S., Fornés V. // J. Catal. 2001. V. 197. № 2. P. 385.
Zhang R., Xu Sh., Raja D., Khusni N.B., Liu J., Zhang J., Abdulridha S., Xiang H., Jiang S., Guan Y., Jiao Y., Fan X. // Microporous Mesoporous Mater. 2019. V. 278. P. 297.
Osatiashtiani A., Puértolas B., Oliveira C.C.S., Manayil J.C., Barbero B., Isaacs M., Michailof Ch., Heracleous E., Pérez-Ramírez J., Lee A.F., Wilson K. // Biomass Convers. Biorefinery. 2017. V. 7. № 3. P. 331.
Sun W., Liu G., Wang L., Zhang X. // Fuel. 2015. V. 144. P. 96.
Bao S., Liu G., Wang L., Zhang X. // Appl. Catal. A Gen. 2011. V. 405. № 1–2. P. 61.
Bao S., Liu G., Wang L., Zhang X., Mi Z. // Microporous Mesoporous Mater. 2011. V. 143. № 2–3. P. 458.
Wan L., Bao S., Liu G., Wang L., Zhang X. // Catal. Commun. 2013. V. 32. P. 71.
Dement’ev K.I., Palankoev T.A., Abramova D.S., Kuznetsov P.S., Zolotukhina A.V., Maksimov A.L., Khadzhiev S.N. // Petrol. Chemistry. 2019. V. 59. № 6. P. 596.
Hudec P., Nociar A., Smiešková A., Jakubík T. // Studies in Surface Science and Catalysis. 2005. V. 158. Part B. P. 1795.
Pakhmanova O.A., Antonov S.V., Dement’ev K.I., Gerzeliev I.M., Khadzhiev S.N. // Petrol. Chem. 2012. V. 52. № 6. P. 401.
Дополнительные материалы
- скачать Dementev_1.tiff
- Рис. Д1 – Рентгенограммы образцов цеолитов со структурным типом FAU
- скачать Dementev_2.tiff
- Рис. Д2 – Рентгенограммы образцов цеолитов со структурным типом BEA
- скачать Dementev_3.tiff
- Рис. Д3 – Рентгенограммы образцов цеолитов со структурным типом MFI
- скачать Dementev_4.tiff
- Рис. Д4 – Спектры ТПД аммиака для образцов цеолитов со структурным типом FAU
- скачать Dementev_5.tiff
- Рис. Д5 – Спектры ТПД аммиака для образцов цеолитов со структурным типом BEA
- скачать Dementev_6.tiff
- Рис. Д6 – Спектры ТПД аммиака для образцов цеолитов со структурным типом MFI