Нефтехимия, 2020, T. 60, № 1, стр. 51-56
Актуальные проблемы аминовой очистки природных газов, анализ и пути решения
И. А. Голубева 1, *, А. В. Дашкина 1, И. В. Шульга 1
1 Российский государственный университет нефти и газа (НИУ) имени И.М. Губкина
119991 Москва, Россия
* E-mail: golubevaia@gmail.com
Поступила в редакцию 01.03.2019
После доработки 04.09.2019
Принята к публикации 09.09.2019
Аннотация
Проведен анализ процесса аминовой очистки природных газов от кислых примесей, рассмотрены проблемы, сопровождающие его, пути их решения. Проанализированы такие задачи, как оптимизация составов аминового раствора и выделяемых кислых газов, проблемы загрязнения аминовых растворов различными примесями, деструкция аминов, высокие энергозатраты при их регенерации. Рассмотрены вопросы пенообразования в абсорбере и пути его снижения, основные направления утилизации отработанных аминов.
Важнейшим этапом подготовки природных газов к переработке является очистка от кислых примесей, в первую очередь, от сероводорода и диоксида углерода, в результате чего образуются товарный газ и кислые газы – сырье для производства газовой серы [1].
Для очистки газов от кислых примесей широко применяют алканоламины, так как они обладают низкой вязкостью, эффективно очищают газ в широком диапазоне парциальных давлений H2S и CO2, почти не абсорбируют углеводороды (УВ) [1].
Однако, технология абсорбции алканоламинами имеет серьезные недостатки: высокие энергетические затраты на регенерацию аминов, деструкция аминов, загрязнение их различными примесями, вспенивание при абсорбции и др. При использовании аминовой очистки возникают задачи, требующие серьезных исследований и нахождения путей их решения, например: выбор параметров абсорбции, обеспечивающих получение товарных газов, отвечающих необходимым требованиям, которые постоянно ужесточаются; обеспечение (при очистке высокосернистых газов) оптимального состава кислых газов, направляемых на производство газовой серы. Важными задачами являются также: утилизация отработанных аминовых растворов, разработка процесса регенерации аминов, не требующего высоких энергетических затрат и предотвращающего деструкцию аминов, применение эффективных пеногасителей и антивспенивателей для решения проблем вспенивания при абсорбции алканоламинами и многие другие [2].
Предмет обсуждения данной статьи – проблемы при эксплуатации установок аминовой очистки газа, их анализ и пути решения.
РЕЗУЛЬТАТЫ И ИХ ОБСУЖДНЕИЕ
Ниже приведены обобщающие моменты по аминовой очистке кислых газов, основанные, в частности, на работах, проведенных нами ранее.
Оптимизация состава кислых газов. При использовании кислых газов в качестве сырья для производства серы важным фактором является концентрация в них сероводорода. При увеличении же содержания диоксида углерода ухудшается горение кислых газов в печах термической ступени, снижение концентрации реагирующих компонентов уменьшает их конверсию [1]. Для того, чтобы увеличить концентрацию сероводорода в кислых газах, необходимо при очистке природных газов подобрать соответствующий абсорбент, селективный к H2S.
Однако, сегодня на Астраханском ГПЗ – основном производителе серы в России – применяют в качестве абсорбента диэтаноламин (ДЭА), не селективный по отношению к H2S. Можно заменить абсорбент третичным амином, например, метилдиэтаноламином (МДЭА), который селективен к сероводороду и практически не извлекает CO2, но в этом случае в товарном газе может остаться большее количество CO2, чем предусмотрено требованиями к нему. Для увеличения избирательности к H2S можно использовать смесь ДЭА с МДЭА, которая селективна к сероводороду, но, чтобы не превысить допустимое содержание диоксида углерода в товарном газе, необходимо подобрать оптимальное содержание МДЭА в этой смеси.
Предполагаемые улучшения в работе установки при замене амина следующие: увеличение выхода серы; улучшение экономических показателей процессов аминовой очистки производства серы; увеличение срока службы оборудования; сокращение рециркуляции абсорбента и подачи водяного пара на регенерацию; снижение образования COS и CS2 при производстве серы [2].
Нами было проведено моделирование аминовой очистки с использованием смеси ДЭА–МДЭА при различном соотношении аминов с помощью универсальной системы моделирования AspenHYSIS [3]. Целесообразность предлагаемых технических решений иллюстрируют результаты проведенных расчетов (табл. 1).
Таблица 1.
Состав кислого газа при различном соотношении аминов [3]
Абсорбент | МДЭА 70% : ДЭА 30% (35%-ный раствор) | ДЭА (40%-ный раствор) | ||
---|---|---|---|---|
состава I | состава II | |||
Кислый газ | кг/ч | мас. % | кг/ч | мас. % |
Сероводород | 81 743.94 | 69.15 | 61 293.18 | 51.85 |
Углекислый газ | 32 035.59 | 27.10 | 52 486.35 | 44.4 |
Вода | 3877.37 | 3.28 | 3877.37 | 3.28 |
Метан | 520.14 | 0.44 | 520.14 | 0.44 |
Метилмеркаптан | 35.46 | 0.03 | 35.46 | 0.03 |
ИТОГО | 118 212.50 | 100 | 118 212.50 | 100.00 |
Таким образом, предлагаемое усовершенствование – заменить ДЭА, применяемый на АГПЗ, композицией его с МДЭА, позволит значительно повысить содержание сероводорода в кислых газах, извлечь требуемое количество CO2, исходя из нормирования его содержания в товарном газе.
С помощью моделирования нами было также установлено, что на АГПЗ целесообразно применить процесс “ADIP-X” с использованием водного раствора МДЭА с активатором пиперазин (диэтилендиамин – алифатический циклический амин с общей формулой C4H10N2), который повышает активность МДЭА к CO2 и позволяет получить кислые газы оптимального состава для производства газовой серы.
Деструкция аминовых растворов. Серьезной проблемой при использовании алканоламинов является термохимическое разложение абсорбента под влиянием диоксида углерода, содержащегося в кислом газе. В результате такого взаимодействия образуются азотсодержащие органические вещества, которые негативно воздействуют на абсорбент – увеличивают его вязкость, снижают абсорбционные свойства, повышают пенообразование.
Данную проблему можно решить за счет фильтрации и сорбционной очистки, либо воздействуя на факторы, влияющие на разложение аминов: состав газа, режим работы абсорбера и десорбера, наличие примесей в самом растворе амина.
В растворе абсорбента образуется, как правило, не один продукт его разложения, а несколько, причем основное влияние на их образование, как уже было отмечено, оказывает диоксид углерода. В случае применения в качестве абсорбента ДЭА основной продукт разложения – N,N-ди(2-оксиэтил)-пиперазин (ОЭП), его производные некоррозионноактивны и не влияют на поглотительную способность амина [3].
Необходимо учитывать, что разложение аминов с увеличением температуры усиливается: при 100°С и 1.2 МПа разложение ДЭА под действием СО2 несущественно, при температуре 175°С и давлении 4.1 МПа – разлагается 90% аминов. Важно отметить, что скорости реакций невысокие, но при этом трудно регенерируемые соединения со временем накапливаются в аппаратах, в результате чего снижается активность амина, увеличиваются вязкость и вспениваемость раствора, усиливается коррозионная активность; весь процесс очистки становится менее эффективным.
На рис. 1 показана зависимость константы скорости деструкции аминов под действием СО2 от температуры. Из графика видно, что МДЭА стабильнее ДЭА, а с увеличением температуры эта разница становится еще значительнее.
Рис. 1.
Зависимость константы скорости процесса термохимической деструкции аканоламинов от температуры при давлении СО2 > 0.1 МПА [3].
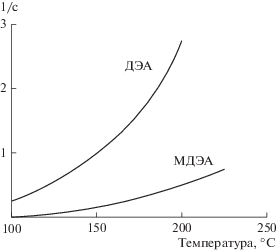
Как уже упоминалось, деструкция аминов максимальна при высоких температурах (80–110°С) и высоких концентрациях диоксида углерода. Но процессы десорбции проводят и при более высоких температурах (до 120–130°С), в таких условиях при регенерации неизбежно разложение даже химически стабильных алканоламинов, особенно под воздействием кислорода, который, в свою очередь, поступает из воды, присутствующей в газе и в растворе амина.
Пенообразование в абсорбере. Серьезной проблемой в процессе очистки от кислых примесей является пенообразование. Причин для пенообразования достаточно много, а именно: ускорение коррозии в аппаратах; попадание в газ различных веществ в процессе добычи; попадание в абсорбер капель тяжелых УВ; разложение аминов при высоких температурах; накопление продуктов побочных реакций и распада амина; попадание капель воды в газ; присутствие минеральных солей в технической воде, которая используется для получения раствора абсорбента [4]. Пенообразование приводит к ухудшению качества газа, потерям абсорбента, нарушению режима работы установки и снижению ее производительности, перепаду давления в аппарате (что, кстати, является основным признаком пенообразования).
Известно несколько методов борьбы с пенообразованием: физические, механические, технологические и химические. Следует предотвращать накопление примесей в растворе, для чего проводят очистку абсорбента.
К физическим методам борьбы с пенообразованием относят: термическое воздействие (замораживание, нагревание, обработка острым паром), действие электрического тока, акустических волн (чаще всего это ультразвук), вибрации, создание высокого капиллярного давления в пене и др. Наиболее эффективное средство – вывод примесей из системы путем непрерывной фильтрации раствора амина [5].
Химическое пеногашение – самый распространенный способ борьбы с пенообразованием при котором применяют специальные реагенты – антивспениватели и пеногасители. Пеногасители должны быть высокоэффективными, иметь высокую скорость пеногашения, работать при малых концентрациях и обладать пролонгирующим действием; они не должны изменять свойства полупродукта и затруднять последующую переработку, не должны оказывать токсического действия, должны быть стабильными при воздействии высоких температур и хранении [5].
Пеногасители делятся на группы по способу введения в раствор. Одни пеногасители вводят заранее для предотвращения пенообразования (антивспениватели), другие – подают, когда пена уже образовалась (собственно пеногасители). При этом пеногасители не стоит вводить до образования пены, а антивспениватели не эффективны, когда пена уже образовалась. Однако для упрощения в дальнейшем мы будем называть все эти вещества пеногасителями.
Итак, для определения эффективности пеногасителя учитывают три характеристики: способность предупреждать пенообразование, длительность (стабильность) предупреждающего пенообразование действия, эффективность пеногашения при введении пеногасителя в среду.
Нами проведено моделирование технологической схемы установки сероочистки природного газа с помощью универсальной системы моделирования AspenHYSYS. В результате анализа эффективности действия применяемых и предлагаемых пеногасителей в процессе аминовой сероочистки природных газов предложено усовершенствование технологии пеногашения путем замены применяемого зарубежного пеногасителя на эффективную композицию пеногасителя и антивспенивателя [6].
C помощью моделирования был рассчитан КПД тарелки в абсорбере, получены материальный и тепловой балансы абсорбера (табл. 2 и 3).
Таблица 2.
Материальный баланс абсорбера [6]
Материальный баланс | |||
---|---|---|---|
входящий материальный поток | массовый расход | выходящий материальный поток | массовый расход |
Газ | 270 564.1 кг/ч | Конденсат | 4123.8 кг/ч |
Доб. Вода 1 | 6510.2 кг/ч | Чистый газ | 155 220.8 кг/ч |
Доб. Вода 2 | 19.7 кг/ч | Горючий газ | 1432.1 кг/ч |
Кислый газ | 116 511.0 кг/ч | ||
Суммарный входящий поток: 277 094.0 кг/ч | Суммарный выходящий поток: 277 287.6 кг/ч |
Таблица 3.
Тепловой баланс абсорбера [6]
Энергетический баланс | |||
---|---|---|---|
входящий энергетический поток | количество теплоты | выходящий энергетический поток | количество теплоты |
Газ | 3 530 2652.8 ккал/ч | Конденсат | 171 523.5 ккал/ч |
Q102 | 72 479 461.9 ккал/ч | Конденсат | 285 27506.0 ккал/ч |
Доб. Вода 1 | –2 945 753.5 ккал/ч | Горючий газ | 168 824.7 ккал/ч |
Q-101 | 895 552.4 ккал/ч | Q101 | 367 1251.1 ккал/ч |
Доб. Вода 2 | –8911.9 ккал/ч | Кислый газ | 8 476 185.9 ккал/ч |
Q-103 | 2 312 807.2 ккал/ч | Q-100 | 21 638 480.7 ккал/ч |
Q-102 | 45 214 096.5 ккал/ч | ||
Суммарный входящий поток: 108 035 808.9 ккал/ч | Суммарный выходящий поток: 107 867 868.4 ккал/ч |
В результате анализа выявлены недостатки применяемого пеногасителя: большие энергозатраты; химическая и термическая деструкция аминов, их потери; высокая загрязненность аминового раствора механическими примесями различного происхождения, а также термостабильными солями. Причины загрязненности абсорбента – его частое и сильное вспенивание, использование большого количества импортного пеногасителя, что, в свою очередь, является дополнительным загрязнением абсорбента.
На основании этого анализа на рис. 2 и 3 показана эффективность действия наиболее широко применяемых в России зарубежных пеногасителей и наиболее перспективных, с нашей точки зрения, отечественных аналогов [6].
Рис. 2.
Зависимость высоты пены от времени для различных пеногасителей: I – КПГ-200АВ (ПАВ 1 мл); II – Родорсил 411; III – DB -31; IV – КПГ-200АВ (ПАВ 3 мл) [6].

Рис. 3.
Пеногасящие характеристики КПГ-200: 1, 3, 5 – подача пеногасителя; 2, 4 – минимальное значение высоты пены [6].
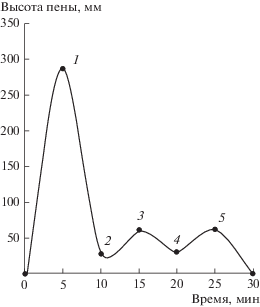
На рис. 2 показано, что пеногаситель КПГ-200АВ проявляет наиболее высокую эффективность при снижении высоты пены. Пеногаситель КПГ-200 также обладает высокой пеногасящей способностью и эффективен в момент вспенивания при подаче его на столб пены абсорбента.
На основании проведенного нами анализа различных предложений по уменьшению вспенивания и сравнения их с данными для применяемых в промышленности пеногасителей, установлено, что наилучшим вариантом технологии пеногашения является применение пеногасителя КПГ-200АВ в комплексе с пеногасителем КПГ-200. Первый следует применять практически постоянно, добавляя небольшие порции для предотвращения образования пены, второй – в моменты образования пены для ее гашения.
Очистка раствора абсорбента фильтрацией. Для снижения пенообразования необходимо также воздействовать на его причины: при пенообразовании несмачиваемые вещества (примеси, продукты коррозии) прилипают к пузырькам газа, тем самым увеличивая скорость пенообразования; вместе с ними, переходя в пену, к повышению скорости пенообразования предрасположены высококипящие парафиновые УВ.
Снижение энергозатрат при регенерации аминовых растворов. Очистка газа с помощью алканоламинов позволяет достичь высокой степени очистки при сравнительно невысоком расходе самого алканоламина. Однако необходимость регенерации абсорбента требует большего расхода тепловой энергии.
Традиционно схема очистки состоит из абсорбера и десорбера, в первый подают два потока: частично регенерируемый амин из середины десорбера поступает в середину абсорбера, полностью регенерируемый амин – в верхнюю часть абсорбера. Данная технология позволяет значительно снизить энергозатраты в процессе регенерации [7].
Эффективными являются схемы очистки с использованием паровой рекомпрессии. Данный способ заключается в подаче регенерированного амина из десорбера с предварительно пониженным давлением в сепаратор. Жидкая фаза сепаратора – тонко реrенерированный амин –направляется в абсорбер. Паровая фаза подвергается компрессии и возвращается обратно в десорбер в качестве дополнительного потока питания. Схема очистки газа с помощью паровой рекомпрессии позволяет получить регенерированный амин с меньшим содержанием кислых газов, благодаря чему степень очистки в абсорбере возрастает.
Возможна комбинация двух последних схем. В этом случае тонко регенерированный амин делится на два потока, один из которых направляется в середину абсорбера, а второй – в сепаратор, откуда жидкая фаза поступает наверх абсорбера. Применение данной схемы позволяет снизить расход пара на ~11%.
Удаление загрязняющих веществ из аминовых растворов. В составе газов, подвергающихся очистке растворами алканоламинов, могут содержаться различные примеси, которые необратимо с ними реагируют. К таковым относятся, например, сернистые соединения, карбоновые кислоты и другие. При взаимодействии амина и данных примесей образуются так называемые термостойкие соли (ТСС). Термостойкими солями принято считать любые ионные соединения, которые не могут быть выведены из аминового раствора при нагревании (например, в регенераторе или десорбционном устройстве). Кроме того, ТСС образуются при введении “нейтрализаторов”, других специальных добавок, а также солей, которые поступают в амин в результате утечки охлаждающей воды и т.д. [8].
ТСС можно удалить из аминового раствора тремя способами: вакуумная дистилляция, электродиализ на ионообменных мембранах, ионный обмен на ионитах. Каждый из них имеет свои преимущества и недостатки, но наиболее технологичным, экономичным и экологичным способом очистки аминов от ТСС считается ионный обмен на ионитах [9].
Вакуумная дистилляция представляет собой перегонку отработанного амина под вакуумом, который необходим из-за достаточно высокой температуры кипения МДЭА и ДЭА; при этом потери аминов с парами воды сведены к минимуму. С помощью вакуумной дистилляции можно полностью удалить ТСС и ВМС, а также летучие примеси с температурой кипения, сильно отличающейся от температуры кипения используемого амина. Соответственно, чем меньше отличается температура кипения примеси от температуры кипения применяемого амина, тем менее эффективно идет процесс удаления примеси.
Дoвольно эффективно сочетание ионного обмена или электродиализа с интенсивной фильтрацией раствора через активированный уголь. Ионный обмен (электродиализ) позволяет избавиться от ТСС, а интенсивная фильтрация – от высокомолекулярных продуктов термической и химической деструкции и осмоления. Такое сочетание позволяет почти полностью удалить бицин – наиболее коррозионно-активную примесь, характерную для деградации МДЭА. Регенерация амина может происходить непосредственно в его водном растворе, что позволяет пропустить стадию удаления воды.
Недостатки процесса: не удаляются промежуточные и конечные продукты деградации амина разной степени летучести, при наличии в растворе некоторых ПАВ даже усиленная фильтрация бесполезна, восстановленный раствор склонен к повышенной вспениваемости.
Применение ионитов для удаления ТСС из аминов дополняет используемую в контурах штатную систему фильтрации. Штатная система фильтрации принципиально не может извлечь растворимые ТСС, а ионный обмен не может остановить нарастание в абсорбенте примесей, не связанных с ТСС (продукты деградации, тяжелые углеводороды, продукты осмоления, поверхностно-активные вещества).
Утилизация отработанного аминового раствора. Известно несколько способов утилизации отработанного аминового раствора. Один из способов – утилизация в печах термического обезвреживания или утилизация в качестве жидких отходов [10].
Существует также такой способ утилизации: из отработанного раствора амина отгоняется вода при атмосферном давлении и температуре в кубе до 160°С. Водный отгон с содержанием амина до 1% нейтрализуется эфирами сульфоянтарной кислоты или алкилбензолсульфокислотой, в результате чего получают раствор ПАВ. Кубовый остаток перегоняется в вакууме (10–20 мм рт. ст.) с выделением трех фракций. Первая (10–15%-ный раствор моноэтаноламина) возвращается на первую стадию отгонки, вторая (98–99.6% моноэтаноламина) – товарный продукт. Третья фракция (кубовый остаток в количестве 1.5–5% от массы раствора моноэтаноламина) нейтра лизуется кислотой, а полученный раствор применяют в качестве восстановителя при производстве кожи и меха. Таким образом, происходит полная переработка отработанного раствора амина [10].
Таким образом, в данной работе проведен анализ проблем аминовой очистки и предложены возможные пути их решения: подбор оптимального состава смеси алканоламинов, поддержание условий технологического режима, предотвращение попадания нежелательных веществ в раствор абсорбента, а также применение специальных реагентов-пеногасителей для снижения пенообразования в растворе абсорбента.
Список литературы
Голубева И.А. Газовая сера. М.: Издательский центр РГУ нефти и газа им. И.М. Губкина, 2015. 243 с.
Голубева И.А., Хайруллина Г.Р., Старынин А.Ю., Каратун О.Н. // НефтеГазоХимия. 2017. № 3. С. 5.
Голубева И.А., Морозкин Ф.С. // НефтеГазоХимия. 2015. № 3. С. 77.
Прайс Дж. // Нефтегазовые технологии. 2006. № 1–2. С. 589.
Алигириева Р.Р. // Дис. ... канд. тех. наук, М., РГУ нефти и газа им. И.М. Губкина. 2017. 123 с.
Голубева И.А., Маренкова О.С. Клюев В.М. // НефтеГазоХимия. 2014. № 12. С.18.
Лапидус А.Л., Голубева И.А., Жагфаров Ф.Г. Газохимия: Учебник для вузов. М.: Издательский центр РГУ нефти и газа им. И.М. Губкина, 2013. 405 с.
Хасанов А.С., Сатторов М.О., Ямалетдинова А.А. // Молодой ученый. 2015. № 2. С. 223. https://moluch.ru/archive/82/14945/
Пангаева Н.А., Ильчибаева А.К., Руднев Н.А., Абызгильдин А.Ю. // Нефтегазовое дело, 2016. № 3. С. 157.
Остапенко С.В., Пономаренко В.В., Степанов В.А., Туголуков А.В., Федосеенко Д.В., Шуплик О.Ю. // Патент РФ № 2223943. 2004.
Дополнительные материалы отсутствуют.