Нефтехимия, 2020, T. 60, № 3, стр. 384-393
Термические превращения компонентов нефтяного остатка в присутствии ферросфер зол ТЭЦ и подсолнечного масла
М. А. Копытов 1, *, С. В. Бояр 1, М. В. Можайская 1
1 Институт химии нефти СО РАН
634055 Томск, Россия
* E-mail: kma@ipc.tsc.ru
Поступила в редакцию 14.10.2019
После доработки 14.11.2019
Принята к публикации 18.11.2019
Аннотация
Исследованы термические превращения компонентов нефтяного остатка (температура кипения выше 350°C) тяжелой высоко парафинистой нефти Зуунбаян (Монголия) в присутствии ферросфер зол ТЭЦ и подсолнечного масла. Использование добавок позволило получить дополнительное количества дистиллятных фракций (НК–360°C). Изучены физико-химические характеристики и состав получаемых продуктов. Проведено сравнение структурно-групповых характеристик смолисто-асфальтеновых компонентов исходного нефтяного остатка и продуктов его термической конверсии в присутствии подсолнечного масла и ферросфер зол ТЭЦ. Присутствие подсолнечного масла и ферросфер приводит к снижению молекулярной массы молекул смол и асфальтенов, выделенных из продуктов термолиза. В молекулах смолисто-асфальтеновых компонентов снижается число нафтеновых и парафиновых атомов углерода, при этом доля ароматических атомов заметно возрастает.
Постоянный рост потребления углеводородов (УВ), вынуждает к использованию альтернативных источников сырья и поиску способов увеличения глубины переработки нефтяного сырья. Одним из способов решения проблемы является вовлечение в переработку возобновляемого сырья, например растительного масла.
Интерес к использованию маслeл в качестве альтернативного источника углеводородного сырья неуклонно растет. Однако, большинство работ [1–13] рассматривают проблемы переэтерификации растительных масел в различных условиях для получения метиловых или этиловых эфиров жирных кислот – основного компонента биодизеля.
Актуальным является совместная переработка нефтяных остатков и растительных масел. Авторами [14–17] было показано, что совместная термическая переработка растительных масел и нефтяных остатков позволяет снизить выход коксоподобных продуктов и увеличить выход топливных фракций. В публикациях высказывается предположение, что растительные масла могут влиять на направленность превращения смолисто-асфальтеновых компонентов [14, 15]. Однако в данных работах не указывается направленность и особенности термических превращений смолисто-асфальтеновых компонентов, содержание которых может достигать от 20 до 50 мас. % в тяжелом нефтяном сырье. Данные компоненты во многом определяют реакционную способность и физико-химические свойства тяжелого сырья, а так же препятствуют использованию каталитических процессов.
В нашей работе [18] был изучен состав продуктов совместного термолиза нефтяного остатка и подсолнечного масла. Непредельные соединения подсолнечного масла, например триглицериды олеиновой и линолевой жирных кислот, могут препятствовать реакции рекомбинации высокомолекулярных радикалов, которые образуются при деструкции смолисто-асфальтеновых компонентов в процессе крекинга тяжелого нефтяного сырья, тем самым замедляя образование коксоподобных продуктов [14, 15, 18].
Ранее нами была показана возможность использования каталитических добавок на основе магнитных ферросфер зол ТЭЦ, которые более чем на 85 мас. % состоят из оксидов железа, для переработки нефтяных остатков [19–21]. В получаемых продуктах увеличивалось содержание светлых фракций и снижалось содержание смолисто-асфальтеновых компонентов.
Соединения железа могут проявлять активность не только в отношении нефтяного сырья [22–27], но и в отношении растительных масел [24, 28–30].
Цель работы – исследование совместного влияния добавок подсолнечного масла и ферросфер зол ТЭЦ на состав продуктов термолиза нефтяного остатка и на структурно-групповые характеристики смолисто-асфальтеновых компонентов.
В данной статье впервые представлено исследование совместного влияния добавок подсолнечного масла и ферросфер зол ТЭЦ на выход и структурно-групповые характеристики смолисто-асфальтеновых компонентов продуктов термолиза нефтяного остатка тяжелой нефти.
ЭКСПЕРИМЕНТАЛЬНАЯ ЧАСТЬ
В качестве объектов исследования были выбраны: остаток тяжелой нефти месторождения Зуунбаян (Монголия) и подсолнечное масло. Определение их физико-химических характеристик выполнено по стандартным и опубликованным в литературе методикам, данные представлены в табл. 1 и 2.
Таблица 1.
Физико-химические характеристики нефтяного остатка [18]
Показатели | Значения |
---|---|
Плотность, кг/м3 | 895.2 |
Кинематическая вязкость при 50°C, мм2/с | Нет свободного истечения |
Температура застывания, °C | 63.0 |
Коксуемость по Конрадсону, мас. % | 6.35 |
Средняя молекулярная масса, а. е. м. | 550 |
Элементный состав, мас. %: | |
С | 86.91 |
H | 11.12 |
S | 0.10 |
N | 0.72 |
O | 1.15 |
Н/С | 1.52 |
Содержание, мас. % | |
− н-алканов | 26.40 |
− твердых парафинов | 15.71 |
Компонентный состав, мас. %: | |
– масел | 74.1 |
– смол | 25.5 |
– асфальтенов | 0.4 |
Начало кипения, °C | >350 |
Таблица 2.
Характеристики подсолнечного масла [18]
Показатели | Значения |
---|---|
Плотность при 20°C, кг/м3 | 920.7 |
Кинематическая вязкость при 20°C, мм2/с | 63.68 |
Иодное число, г I2/100 г | 134.02 |
Кислотное число, мг KOH/г | 0.79 |
Коксуемость по Конрадсону, мас. % | 0.32 |
Зольность, мас. % | 0.014 |
Элементный состав, мас. %: | |
С | 77.56 |
H | 10.70 |
N | 0.49 |
О | 11.25 |
S | 0.01 |
Содержание жирных кислот, мас. %* | |
пальмитиновая (C16:0) | 6.0 |
стеариновая (C18:0) | 4.4 |
олеиновая (C18:1) | 12.3 |
линолевая (C18:2) | 61.5 |
Общее содержание жирных кислот, мас. % | 84.2 |
Нефтяной остаток (НО) был получен в процессе атмосферно-вакуумного фракционирования (отобраны фракции, выкипающие до 350°C), он характеризуется высоким содержание смол (25.5 мас. %), н-алканов (26.4 мас. %) и низким содержании асфальтенов и серы [18]. Данное сырье имеет высокий показатель коксуемости по Конрадсону – 6.35 мас. % (табл. 1), что осложняет его переработку с использованием традиционных каталитических систем. Возможным способом использования подобного сырья может являться его термическая переработка в присутствии “крекинг-добавок” [18].
В качестве “крекинг-добавки”, как и в предыдущей работе [18], использовали подсолнечное масло в количестве до 8.0 мас. % на реакционную смесь. Характеристики подсолнечного масла представлены в табл. 2 [18].
В качестве каталитической добавки использовались ферросферы (ФС), выделенные из летучей золы от пылевидного сжигания бурого угля марки Б2 Канско-Ачинского бассейна, описанные в работах [8–10]: фракция – 0.4 + 0.2 мм, насыпная плотность ρ = 1.87 г/см3, химический состав (мас. %) – 85.20 Fe2O3, 8.69 CaO, 4.00 SiO2, 1.90 Al2O3, остальное MgO, Na2O, K2O, TiO2, SO3. Удельная поверхность ФС составляет 0.22 м2/г [20].
По данным рентгенофазового анализа (РФА) ферросферы серии S1 в исходном состоянии представлены ферритовой шпинелью (64.7%) с параметром a = 8.3959(2) Å и гематитом (10.1%) с параметрами a = 5.0340(5) Å, c = 13.748(1) Å), остальное составляют рентгеноаморфный остаток (23.8%) и кварц [31]. Значения параметров решеток железооксидных фаз близки к таковым для стехиометрических магнетита (a = 8.3960 Å) [32] и гематита (a = 5.0356 Å, c = 13.7489 Å) [33]. Перед крекингом ФС прокаливали на воздухе 2 ч при 800°С, как и в наших предыдущих работах, для перевода магнетита в гематит [20, 21, 31, 34]. После прокаливания фаза феррошпинели на ~90% окисляется до гематита [20, 21].
Крекинг образцов проводили в автоклаве объемом 12 см3, оснащенным карманом для термопары, краном высокого давления и манометром. В реактор загружали 6.5 г сырья, герметично закрывали и продували аргоном, эксперимент проводили при температуре 435°С, в течении 1 ч. Описание эксперимента по крекингу и анализу продуктов подробно приведено в наших предыдущих работах [18, 21, 34].
В работе представлены данные исследования продуктов термолиза исходного нефтяного остатка [18], а также исходного подсолнечного масла [18]. Полученные данные сравнены c характеристиками продуктов термолиза смесей: нефтяного остатка и ФС в соотношении 90.0/10.0 мас. % [35]; нефтяного остатка и подсолнечного масла в соотношении 92.0/8.0 мас. % [18]; подсолнечного масла и ФС в соотношении 90.0/10.0 мас. %; нефтяного остатка, подсолнечного масла и ФС в соотношении 82.8/7.2/10.0 мас. %.
Определение выхода дистиллятных фракций в продуктах термолиза проводили методом термогравиметрического анализа, как в наших предыдущих работах [19, 21, 36, 37].
Для смол и асфальтенов, выделенных из исходного мазута и продуктов термолиза, был проведен структурно-групповой анализ (СГА), в основе которого лежит методика, разработанная в ИХН СО РАН и основанная на совместном использовании результатов определения элементного состава, средних молярных масс и данных ПМР-спектроскопии [38–40].
РЕЗУЛЬТАТЫ И ИХ ОБСУЖДЕНИЕ
Выход фракций НК–360°С в продуктах термолиза в расчете на исходное сырье представлен на рис. 1a. Сравниваются данные состава продуктов термолиза исходного нефтяного остатка [18, 35], подсолнечного масла [18], и смесь нефтяного остатка с подсолнечным маслом [18] без ФС и в присутствии ФС.
Рис. 1.
Состав продуктов термолиза в зависимости от состава сырьевой смеси: а – выход топливных фракций; б – выход твердых и газообразных продуктов; в – выход и состав жидких продуктов. НО – нефтяной остаток; ПМ – подсолнечное масло; ФС – ферросферы зол ТЭЦ; Состав смеси: НО/ФС = 90.0 : 10.0 мас. %; НО/ПМ = 92.0/8.0 мас. %; ПМ/ФС = 90.0/10.0 мас. %; НО/ПМ/ФС = 82.8/7.2/10.0 мас. %.
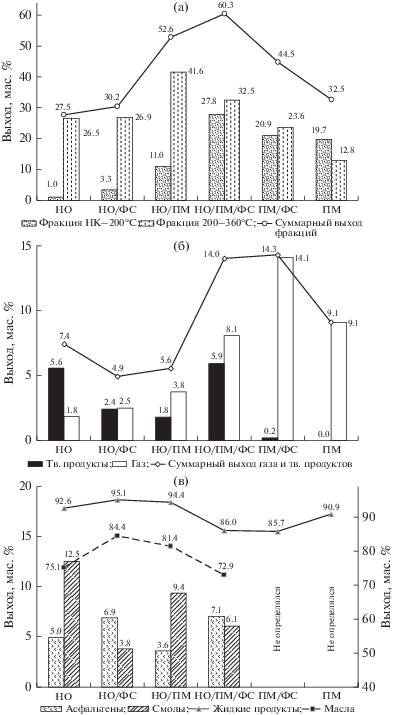
Использование ФС при термолизе исходного подсолнечного масла приводит к увеличению выхода дистиллятных фракций с 32.5 до 44.5 мас. %. Выход увеличивается за счет фракций с температурами кипения 200–360°С, их доля возрастает в 1.8 раза по сравнению с крекингом без добавок ФС. Возможно, состав дизельных фракций пополняется продуктами декарбоксилирования олеиновой и линоленовой кислоты с длиной цепи С17.
Добавка ФС при термолизе нефтяного остатка приводит к увеличению выхода бензиновых фракций с 1.0 до 3.3 мас. %, доля дизельных фракций остается фактически неизменной. Введение ФС при термолизе смеси ПМ и нефтяного остатка (рис. 1а), позволяет увеличить выход дистиллятных фракций с 52.6 до 60.3 мас. %, при этом более чем в 2.5 раза возрастает доля бензиновых фракций с 11.0 до 27.8 мас. %, но несколько снижается доля дизельных фракций с 41.6 до 32.5 мас. %. Увеличение выхода дистиллятных фракций указывает на то, что, присутствие ФС приводит к изменению направленности термических превращений, как компонентов ПМ, так и нефтяного остатка. Введение ФС сказывается на фракционном составе продуктов термолиза исходного ПМ и его смеси с нефтяным остатком.
Наиболее заметно выход дистиллятных фракций коррелирует с выходом газообразных продуктов. Выход газообразных и твердых продуктов термолиза в присутствии ФС представлен на рис. 1б. При термолизе подсолнечного масла с ФС увеличивается выход газообразных продуктов с 9.1 до 14.3 мас. %, выход твердых продуктов составляет менее 0.2 мас. %.
Выход газообразных продуктов при термолизе в присутствии ФС смеси нефтяного остатка и подсолнечного масла возрастает с 3.8 до 8.1 мас. % (рис. 1б). Это объясняется как активным разрушением компонентов подсолнечного масла в присутствии ФС (в том числе реакции декарбонилирования и декарбоксилирования кислот), так и деструкцией компонентов нефтяного остатка. Содержание твердых продуктов возрастает с 1.8 до 5.9 мас. %.
При термолизе исходного нефтяного остатка введение ФС, приводит к увеличению выхода газообразных продуктов в 1.4 раза, а выход твердых продуктов снижается в 2.3 раза. Снижение выхода твердых продуктов, объясняется сорбцией смолисто-асфальтеновых компонентов оксидами железами (основные компоненты ФС), что замедляет кокосообразование.
Анализ состава продуктов крекинга (рис. 1в) показывает, что при термолизе нефтяного остатка в присутствии ФС выход смол снижается почти в 3.3 раза (с 12.5 до 3.8 мас. %), а выход асфальтенов возрастает в 1.4 раза. Введение ФС в смесь нефтяного остатка и подсолнечного масла также влияет на выход смол, их содержание сокращается более чем в 1.5 раза (с 9.4 до 6.1 мас. %) и почти в 2 раза увеличивает выход асфальтенов (с 3.6 до 7.1 мас. %). Уменьшение выхода смол объясняется тем, что ФС инициируют их деструкцию, в том числе с образованием асфальтенов и затем твердых продуктов (“кокс”) [21].
Меньший эффект в снижении доли смол в продуктах каталитического крекинга смеси НО и подсолнечного масла может быть связан с адсорбцией компонентов масел, например, триглицеридов жирных кислот или самих жирных кислот, которые образуются при разрушении триглицеридов на ФС. Известно, что оксиды переходных металлов и в частности оксиды железа могут адсорбировать на себе смолы и асфальтены [41–44] и другие полярные соединения. Адсорбированные компоненты ПМ способны частично блокировать активные центры ФС, а затем сами могут подвергаться термокаталитическим превращениям.
Анализ газообразных продуктов крекинга представлен в табл. 3. В газообразных продуктах крекинга подсолнечного масла преобладает монооксид углерода и углекислый газ, что подтверждает протекание реакции декарбоксилирования и декарбонилирования. При этом отмечается более высокое содержание водорода (в сравнении с газообразными продуктами термолиза нефтяного остатка) и в 4 раз − более низкое содержание метана.
Таблица 3.
Состав бензиновой фракции НК–200°С и газообразных продуктов*
Компоненты | Состава исходной сырьевой смеси | |||||
---|---|---|---|---|---|---|
НО | НО/ФС | НО/ПМ | НО/ПМ/ФС | ПМ/ФС | ПМ | |
Состав бензиновой фракции НК–200°С, мас. % | ||||||
н-Алканы | 0.36 | 1.30 | 4.11 | 12.09 | 10.72 | 7.60 |
изо-Алканы | 0.20 | 0.49 | 1.54 | 5.00 | 1.59 | 4.00 |
Арены | 0.12 | 0.46 | 1.39 | 3.14 | 2.28 | 2.68 |
Нафтены | 0.16 | 0.49 | 1.99 | 3.00 | 2.68 | 1.26 |
Олефины | 0.10 | 0.42 | 1.11 | 2.53 | 2.76 | 2.66 |
Не определено | 0.07 | 0.14 | 0.85 | 2.03 | 0.88 | 1.50 |
Общий выход бензиновых фракций в расчете на исходное сырье, мас. % | 1.00 | 3.30 | 11.00 | 27.80 | 20.90 | 19.70 |
Содержание газообразных компонентов, мас. % | ||||||
H2 | 0.01 | 0.01 | 0.02 | 0.03 | 0.06 | 0.04 |
CO | 0.01 | 0.02 | 0.21 | 0.27 | 2.68 | 2.14 |
CO2 | 0.08 | 0.11 | 0.32 | 0.71 | 7.61 | 3.34 |
CH4 | 1.07 | 0.88 | 1.52 | 4.62 | 0.69 | 0.37 |
C2H4 | 0.01 | 0.02 | 0.03 | 0.05 | 0.06 | 0.01 |
C2H6 | 0.22 | 0.43 | 0.46 | 0.69 | 1.03 | 0.65 |
C3H8 | 0.19 | 0.57 | 0.65 | 0.84 | 0.82 | 0.77 |
C3H6 | 0.04 | 0.05 | 0.09 | 0.25 | 0.21 | 0.25 |
Алканы C4 | 0.10 | 0.28 | 0.25 | 0.08 | 0.53 | 0.65 |
Алкены C4 | 0.02 | 0.03 | 0.07 | 0.07 | 0.09 | 0.06 |
C5–C5+ | 0.05 | 0.10 | 0.17 | 0.49 | 0.33 | 0.82 |
Общий выход газообразных продуктов в расчете на исходное сырье, мас. % | 1.80 | 2.50 | 3.79 | 8.10 | 14.10 | 9.10 |
Крекинг подсолнечного масла в присутствии ФС приводит к заметному увеличению выхода метана, углекислого газа и этилена. Увеличение доли оксидов углерода объясняется как окислительной [25], так и их каталитической активностью оксидов железа [45].
При совместном крекинге нефтяного остатка и ПМ в газообразных продуктах увеличивается выход СО и СО2, алканов и алкенов С1–С4. На качественный и количественный состав газообразных продуктов при совместном термолизе нефтяного остатка и подсолнечного масла так же влияют добавки ФС, в присутствии которых существенно увеличивается выход метана.
Бензиновые фракции продуктов термолиза исходного ПМ главным образом представлены н-алканами и изо-алканами. Также стоит отметить высокое содержание ароматических УВ и олефинов. Из литературных данных [15, 46] известно, что растительные масла при высоких температурах способны образовывать ароматические соединения. При термолизе подсолнечного масла в присутствии ФС заметно увеличивается выход н-алканов и нафтенов (в пересчете на исходное сырье), но снижается выход изо-алканов.
При термолизе смеси подсолнечного масла и нефтяного остатка в присутствии ФС выход бензиновых фракций увеличивается главным образом за счет изо-алканов и н-алканов, содержание которых увеличивается почти в 3 раза. И более чем в 2 раза увеличивается выход олефинов. Высокое содержание олефинов в бензиновых фракциях будет требовать их дальнейшей каталитической переработки для получения конечных товарных продуктов.
Представляло интерес исследовать структурно-групповые характеристики смолисто-асфальтеновых компонентов продуктов термолиза нефтяного остатка в присутствии ФС и подсолнечного масла. Структурно-групповые характеристики асфальтенов и смол НО и продуктов крекинга представлены в табл. 4 и 5 соответственно.
Таблица 4.
Структурно-групповые характеристики асфальтенов
Асфальтены | |||||
исходный НО | продукты термолиза | ||||
НО | НО/ФС | НО/ПМ | НО/ПМ/ФС | ||
Средняя молекулярная масса, а. е. м. | |||||
MM | 1800 | 545 | 1400 | 502 | 339 |
Число атомов в средней молекуле | |||||
C | 129.45 | 39.40 | 100.68 | 35.90 | 24.50 |
H | 178.39 | 45.42 | 114.44 | 32.70 | 28.10 |
N | 2.46 | 0.43 | 0.83 | 0.70 | 0.30 |
S | 0.06 | 0.04 | 0.06 | 0.10 | 0.20 |
O | 1.91 | 1.20 | 3.93 | 1.50 | 0.40 |
H/C | 1.38 | 1.15 | 1.14 | 0.91 | 1.15 |
Кольцевой состав | |||||
Ko | 17.8 | 11.6 | 21.0 | 11.4 | 6.85 |
Ka | 11.4 | 2.5 | 10.4 | 4.0 | 1.87 |
Kн | 6.4 | 9.1 | 10.6 | 7.4 | 4.98 |
Распределение атомов С, % | |||||
fa | 36.1 | 29.2 | 44.4 | 48.9 | 36.9 |
fн | 20.7 | 65.2 | 43.6 | 48.6 | 58.1 |
fп | 43.2 | 5.6 | 12.0 | 2.6 | 5.0 |
Число углеродных атомов разного типа в средней молекуле | |||||
Ca | 46.8 | 11.5 | 44.7 | 17.5 | 9.0 |
Cн | 26.7 | 25.7 | 43.9 | 17.4 | 14.2 |
Cп | 55.9 | 2.2 | 12.1 | 0.9 | 1.2 |
Cα | 13.8 | 5.4 | 12.8 | 6.0 | 3.2 |
Cγ | 8.3 | 2.2 | 4.0 | 0.9 | 1.2 |
Среднее число блоков в молекуле | |||||
ma | 3.3 | 1.4 | 3.0 | 1.7 | 1.2 |
Параметры средних структурных блоков | |||||
${\text{K}}_{{\text{o}}}^{*}$ | 5.4 | 8.4 | 6.9 | 6.7 | 5.6 |
${\text{K}}_{{\text{а}}}^{*}$ | 3.5 | 1.8 | 3.4 | 2.4 | 1.5 |
${\text{K}}_{{\text{н}}}^{*}$ | 1.9 | 6.6 | 3.5 | 4.3 | 4.1 |
C* | 39.1 | 28.5 | 33.1 | 21.1 | 20.0 |
${\text{С}}_{{\text{а}}}^{*}$ | 14.1 | 8.3 | 14.7 | 10.3 | 7.4 |
${\text{С}}_{{\text{н}}}^{*}$ | 8.1 | 18.6 | 14.4 | 10.2 | 11.6 |
${\text{С}}_{{\text{п}}}^{*}$ | 16.9 | 1.6 | 4.0 | 0.5 | 1.0 |
${\text{С}}_{\alpha }^{*}$ | 4.2 | 3.9 | 4.2 | 3.5 | 2.6 |
${\text{С}}_{\gamma }^{*}$ | 2.5 | 1.6 | 1.3 | 0.5 | 1.0 |
Таблица 5.
Структурно-групповые характеристики смол
Смолы | |||||
---|---|---|---|---|---|
исходный НО | продукты термолиза | ||||
НО | НО/ФС | НО/ПМ | НО/ПМ/ФС | ||
Средняя молекулярная масса, а. е. м. | |||||
MM | 850 | 790 | 640 | 699 | 402 |
Число атомов в средней молекуле: | |||||
C | 55.67 | 55.20 | 44.20 | 46.70 | 28.10 |
H | 80.87 | 73.70 | 53.30 | 46.00 | 29.70 |
N | 0.82 | 0.60 | 0.50 | 0.80 | 0.60 |
S | 0.12 | 0.05 | 0.04 | 0.10 | 0.03 |
O | 5.33 | 2.60 | 3.00 | 5.00 | 1.60 |
H/C | 1.45 | 1.34 | 1.21 | 0.99 | 1.06 |
Кольцевой состав | |||||
Ko | 7.5 | 12.8 | 13.4 | 11.2 | 7.8 |
Ka | 3.6 | 2.8 | 2.0 | 5.8 | 2.8 |
Kн | 3.9 | 10.0 | 11.3 | 5.4 | 5.0 |
Распределение атомов С, % | |||||
fa | 25.6 | 21.4 | 19.6 | 51.5 | 43.3 |
fн | 29.1 | 72.7 | 75.1 | 43.1 | 52.7 |
fп | 45.3 | 6.0 | 5.4 | 5.4 | 4.0 |
Число углеродных атомов разного типа в средней молекуле | |||||
Ca | 14.2 | 11.8 | 8.6 | 24.1 | 12.2 |
Cн | 16.2 | 40.1 | 33.2 | 20.1 | 14.8 |
Cп | 25.2 | 3.3 | 2.4 | 2.5 | 1.1 |
Cα | 6.2 | 5.6 | 4.6 | 6.9 | 5.3 |
Cγ | 4.3 | 3.3 | 2.4 | 2.5 | 1.1 |
Среднее число блоков в молекуле | |||||
ma | 1.6 | 1.4 | 1.3 | 2.0 | 1.4 |
Параметры средних структурных блоков | |||||
${\text{K}}_{{\text{o}}}^{*}$ | 4.6 | 8.8 | 10.5 | 5.5 | 5.4 |
${\text{K}}_{{\text{а}}}^{*}$ | 2.2 | 1.9 | 1.6 | 2.9 | 1.9 |
${\text{K}}_{{\text{н}}}^{*}$ | 2.4 | 6.9 | 8.9 | 2.6 | 3.4 |
C* | 33.9 | 38.2 | 34.9 | 23.0 | 19.4 |
${\text{С}}_{{\text{а}}}^{*}$ | 8.7 | 8.2 | 6.8 | 11.8 | 8.4 |
${\text{С}}_{{\text{н}}}^{*}$ | 9.9 | 27.7 | 26.2 | 9.9 | 10.2 |
${\text{С}}_{{\text{п}}}^{*}$ | 15.4 | 2.3 | 1.9 | 1.2 | 0.8 |
${\text{С}}_{\alpha }^{*}$ | 3.8 | 3.9 | 3.6 | 3.4 | 3.7 |
${\text{С}}_{\gamma }^{*}$ | 2.6 | 2.3 | 1.9 | 1.2 | 0.8 |
Асфальтены исходного нефтяного остатка имеют молекулярную массу ММ = 1800 а. е. м., среднее число структурных блоков в молекуле ma = 3.3 (табл. 4) [47]. В усредненной молекуле содержится 129 атомов С, 47 из которых принадлежат ароматическим циклам (Ca), 26 – насыщенным циклам (Cн) и 56 – алифатическим фрагментам (Сп) [47]. Количество ароматических колец (Ка) в молекуле – 11, насыщенных (Кн) ~ 6. Большая часть атомов С представлена алифатическими фрагментами (fп = 43.2), нежели кольцевыми (fa = 36.1 и fн = 20.7). В среднем структурном блоке имеется пять колец (${\text{K}}_{{\text{o}}}^{*}$), два из которых являются насыщенными (Кн), а три ароматическими (${\text{K}}_{{\text{а}}}^{*}$), в алкильных фрагментах (${\text{С}}_{{\text{п}}}^{*}$) около 17 атомов углерода [47].
В результате термолиза НО значительно уменьшается молекулярная масса получаемых асфальтенов с 1800 до 545 а. е. м.; количества атомов углерода снижается с 129.45 до 39.40, атомов водорода – с 178.39 до 45.42. Общее число колец (Ко) сокращается с 17.8 до 11.6 в средней молекуле. Почти в 25 раз сокращается число атомов в алкильных фрагментах (Сп) с 55.9 до 2.2. Также уменьшилось число структурных блоков ma с 3.3 до 1.4, при этом несколько увеличивается содержание насыщенных колец (${\text{K}}_{{\text{н}}}^{*}$) с 1.9 до 6.6.
При совместном термолизе нефтяного остатка и ПМ молекулярная масса получаемых асфальтенов снижается с 545 (при термолизе без добавок ПМ) до 502 а. е. м., количество атомов углерода – с 39.40 до 35.9, атомов водорода – с 45.42 до 32.7, число насыщенных колец (Кн) – с 9.1 до 7.4. При этом возрастает доля ароматических атомов С (fa: с 29.19 до 48.87) и среднее число блоков (mа) с 1.38 до 1.70.
Добавление ФС в процессе термолиза смеси нефтяного остатка и ПМ приводит к образованию асфальтенов с молекулярной массой около 339 а. е. м. Число атомов углерода в средней молекуле асфальтенов сокращается с 35.9 до 24.5, атомов водорода – с 32.7 до 28.1, общего количества колец (Ко) – с 11.4 до 6.85, ароматических (Ка) – с 4.0 до 1.9, насыщенных (Кн) – с 7.4 до 5.0. Меняется и распределение атомов углерода: снижается доля ароматических (Са) с 17.5 до 9.0 и насыщенных (Сн) с 17.4 до 14.2, но повышается доля алифатических фрагментов (Сп) с 0.9 до 1.2.
Смолы исходного нефтяного остатка имеют молекулярную массу ММ = 850 а. е. м., среднее число структурных блоков в молекуле ma = 1.6 [47]. В усредненной молекуле содержится 56 атомов С, 14 из которых принадлежат ароматическим кольцам (Ca), 16 – насыщенным кольцам (Cн) и 25 – алифатическим фрагментам (Сп) [47]. Количество ароматических (Ка) и насыщенных (Кн) колец в молекуле по 4 [47]. Большая часть атомов углерода представлена алифатическими фрагментами (fп = 45.3). В среднем структурном блоке имеется большое количество алкильных фрагментов (${\text{С}}_{{\text{п}}}^{*}$) с общим числом атомов углерода около 15 [47].
В смолах, выделенных из продуктов термолиза (без добавок ФС и подсолнечного масла), уменьшается молекулярная масса (с 850 до 790 а. е. м.), число атомов в средней молекуле снижается с 55.6 до 55.2, водорода с 80.9 до 73.7, среднее число блоков в молекуле (mа) с 1.64 до 1.45. При этом образуется большое количество насыщенных колец (Кн), число которых повышается с 3.9 до 10.0 и немного снижается число ароматических (Ка) с 3.6 до 2.8.
Добавление ПМ в процессе термолиза способствует деструкции молекул смол, их молекулярная масса уменьшается с 790 до 699 а. е. м. Уменьшается число атомов углерода в средней молекуле с 55.2 до 46.7, водорода – с 73.7 до 46.0, количество колец (Ко) – с 12.8 до 11.2, (Кн) – с 10.0 до 5.4. Совместный термолиз нефтяного остатка, подсолнечного масла и ФС наиболее сильно влияет на структуру смол. Молекулярная масса снижается с 699 до 402 а. е. м., число атомов углерода в средней молекуле сокращается с 46.7 до 28.1, водорода – с 46.0 до 29.7, среднее число блоков в молекуле (ma) – с 2.03 до 1.44.
ВЫВОДЫ
Введение ФС зол ТЭЦ в смесь нефтяного остатка и подсолнечного масла позволяет более чем в 2.5 раза увеличить выход бензиновых фракций, но несколько сокращается выход фракций с Ткип > 200°С. При этом в продуктах термолиза снижается доля смол и возрастает содержание асфальтенов, твердых и газообразных продуктов (в сравнении с термолизом без феррофер). Это возможно объяснить тем, что гематит, содержащийся в ФС, может инициировать термическую деструкцию углеводородных компонентов и смол нефтяного остатка, а также компонентов растительного масла.
Присутствие подсолнечного масла и ФС в процессе термолиза нефтяного остатка приводит к снижению молекулярной массы молекул смол и асфальтенов, выделенных из продуктов термолиза. В молекулах смолисто-асфальтеновых компонентов снижается число нафтеновых и парафиновых атомов углерода, при этом доля ароматических атомов заметно возрастает. Это объясняется тем, что подсолнечное масло и его компоненты, образующиеся при термолизе, могут влиять на направленность превращений смолисто-асфальтеновых компонентов.
Список литературы
Tangy A., Pulidindi I.N., Perkas N., Gedanken A. // Bioresour. Technol. 2017. V. 224. P. 333.
Rahman M.T., Hainin M.R., Bakar W.A.W.A. // Constr. Build. Mater. 2017. V. 150. P. 95.
Muciño G.G., Romero R., Ramírez A., Martínez S.L., Baeza-Jiménez R., Natividad R. // Fuel. 2014. V. 138. P. 143.
Доронин В.П., Потапенко О.В., Липин П.В., Сорокина Т.П., Булучевская Л.А. // Нефтехимия. 2012. Т. 52. № 6. С. 422.
Доронин В.П., Потапенко О.В., Липин П.В., Сорокина Т.П. // Катализ в промышленности. 2013. № 6. С. 61.
Attia A.M.A., Hassaneen A.E. // Fuel. 2016. V. 167. P. 316.
Hong I.K., Jeon H., Kim H., Lee S.B. // J. Industrial and Engineering Chemistry. 2016. V. 42. P. 107.
Tran T.T.V., Kaiprommarat S., Kongparakul S., Reubroycharoen P., Guan G., Nguyen M.H., Samart C. // Waste Management. 2016. V. 52. P. 367.
Maneerung T., Kawi S., Dai Y., Wang C.H. // Energy Conversion and Management. 2016. V. 123. P. 487.
Tan Y.H., Abdullah M.O., Nolasco-Hipolito C., Taufiq-Yap Y.H. // Applied Energy. 2015. V. 160. P. 58.
Gupta A.R., Yadav S.V., Rathod V.K. // Fuel. 2015. V. 158. P. 800.
Mahesh S.E., Ramanathan A., Begum K.M.S., Narayanan A. // Energy Conversion and Management, 2015. V. 91. P. 442.
Pukale D.D., Maddikeri G.L., Gogate P.R., Pandit A.B., Pratap A.P. // Ultrasonics Sonochemistry. 2015. V. 22. P. 278.
Юсевич А.И., Тимошкина М.А., Грушова Е.И. // Нефтехимия. 2010. Т. 50. № 3. С. 241.
Тимошкина М.А., Юсевич А.И., Михаленок С.Г., Прокопчук Н.Р. // Нефтехимия. 2014. Т. 54. № 2. С. 113.
Тимошкина М.А., Юсевич А.И. // Труды БГТУ. Серия 2. Химические технологии, биотехнология, геоэкология. 2012. № 1. № 4. С. 234.
Юсевич А.И., Тимошкина М.А. // Химия и технология топлив и масел. 2013. № 3. С. 3.
Kopytov M.A., Boyar S.V., Golovko A.K. // AIP Conference Proceedings – AIP Publ. 2018. V. 2051. № 1. P. 020131.
Kopytov M.A., Dmitriev D.E., Golovko A.K. // ACS National Meeting Book of Abstracts. 2009. P. 1155.
Kopytov M.A., Golovko A.K., Kirik N.P., Anshits A.G. // Petroleum Chemistry. 2013. V. 53. № 1. P. 14.
Golovko A.K., Kopytov M.A., Sharonova O.M., Kirik N.P., Anshits A.G. // Catalysis in Industry. 2015. V. 7. № 4. P. 293.
Wang D., Jin L., Li Y., Yao D., Wang J., Hu H. // Energy. 2018. V. 162. P. 542.
Wang D., Jin L., Li Y., Wei B., Yao D., Hu H. // Fuel. 2019. V. 239. P. 764.
Ma Y., Wang Q., Sun X., Wu C., Gao Z. // Renewable Energy. 2017. V. 107. P. 522.
Hosseinpour M., Fatemi S., Ahmadi S.J. // Fuel. 2015. V. 159. P. 538.
Wang D., Jin L., Li Y., Hu H. // Fuel. 2017. V. 210. P. 803.
Теляшев Э.Г., Журкин О.П., Везиров Р.Р., Ларионов С.Л., Имашев У.Б. // Химия твердого топлива. 1991. Т. 33. № 5. С. 57.
Gan S., Ng H.K., Ooi C.W., Motala N.O., Ismail M.A.F. // Bioresource Technology. 2010. V. 101. № 19. P. 7338.
Mengyu G.A.N., Deng P.A.N., Li M.A., En Y.U.E., Jianbing H.O.N.G. // Chinese J. Chemical Engineering. 2009. V. 17. № 1. P. 83.
Patil P., Deng S., Rhodes J.I., Lammers P.J. // Fuel. 2010. V. 89. № 2. P. 360.
Sharonova O.M., Anshits N.N., Solovyov L.A., Salanov A.N., Anshits A.G. // Fuel. 2013. V. 111. p. 332.
International Center for Diffraction Data. ICDD PDF 19−629. www.icdd.com (accessed May 13, 2012).
International Center for Diffraction Data. ICDD PDF 33−664. www.icdd.com (accessed May 13, 2012).
Kopytov M.A., Golovko A.K., Kirik N.P., Anshits A.G. // Solid Fuel Chemistry. 2013. V. 47. № 2. P. 114.
Копытов М.А., Головко А.К. // Известия Томского политехнического университета. 2009. Т. 315. № 3. С. 83.
Kopytov M.A., Golovko A.K. // Russian J. Physical Chemistry B. 2010. V. 4. № 8. P. 1228.
Kopytov M.A., Golovko A.K. // Solid Fuel Chemistry. 2013. V. 47. № 6. P. 370.
Камьянов В.Ф., Большаков Г.Ф. // Нефтехимия. 1984. Т. 24. № 4. С. 450.
Камьянов В.Ф., Большаков Г.Ф. // Нефтехимия. 1984. Т. 24, № 4. С. 443.
Камьянов В.Ф., Большаков Г.Ф. // Нефтехимия. 1984. Т. 24. № 4. с. 460.
Ko S., Huh C. // J. Petroleum Science and Engineering. 2019. V. 172. P. 97.
Nassar N.N., Hassan A., Carbognani L., Lopez-Linares F., Pereira-Almao P. // Fuel. 2012. V. 95. P. 257.
Setoodeh N., Darvishi P., Lashanizadegan A. // J. Dispersion Science and Technology. 2018. V. 39. № 5. P. 711.
Abu Tarboush B.J., Husein M.M. // Fuel Process. Technol. 2015. V. 133. P. 120.
Kalishyn Y.Y., Bychko I.B., Trypolskyi A.I., Strizhak P.E. // Theoretical and Experimental Chemistry. 2017. V. 53. № 3. P. 199.
Dupain X., Costa D.J., Schaverien C.J., Makkee M., Moulijn J.A. // Applied Catalysis B: Environmental. 2007. V. 72. № 1–2. P. 44.
Kopytov M.A., Golovko A.K. // Petrol. Chemistry. 2017. V. 57. № 1. P. 39.
Дополнительные материалы отсутствуют.