Нефтехимия, 2020, T. 60, № 3, стр. 422-430
Закономерности каталитического облагораживания тяжелой кармальской нефти в присутствии аморфных алюмосиликатов
Н. Н. Свириденко 1, *, А. В. Восмериков 1, М. Р. Аглиуллин 2, Б. И. Кутепов 2
1 Институт химии нефти СО РАН
634055 Томск, Россия
2 Институт нефтехимии и катализа РАН
450075 Уфа, Россия
* E-mail: dark_elf26@mail.ru
Поступила в редакцию 14.10.2019
После доработки 23.10.2019
Принята к публикации 18.11.2019
Аннотация
Изучено влияние различных аморфных алюмосиликатов на состав продуктов крекинга тяжелой кармальской нефти (республика Татарстан) в реакторе-автоклаве. Показано, что добавки 0.5% алюмосиликатов с размером пор 70 Å и 1.0 мас. % Al–Si с размером пор 50 Å увеличивают деструкцию высокомолекулярных компонентов на 13–14% и выход фракций, выкипающих до 360°C, более чем на 20 мас. %. Выявлено, что масла обогащаются насыщенными и моноароматическими углеводородами (УВ). Установлено, что добавка аморфного алюмосиликата с размером пор 50 Å приводит к образованию асфальтенов коксоподобной структуры с низким атомным отношением Н/С = 0.75, а катализатор полностью закоксовывается. Выявлено, что использование аморфного алюмосиликата с размером пор 70 Å, приводит к образованию асфальтенов с меньшей молекулярной массой и атомным отношением Н/С = 0.96, а катализатор в меньшей степени подвергается отложению продуктов уплотнения.
По мере истощения запасов легких и средних нефтей важным сырьевым источником становятся тяжелые высоковязкие нефти и природные битумы. По разным оценкам запасы тяжелых нефтей и природных битумов на территории Российской Федерации составляют от 30 до 75 млрд тонн [1]. Переработка такого углеводородного сырья по классическим схемам является нерентабельной [2–4].
Одной из важнейших проблем, связанной с переработкой тяжелого углеводородного сырья (тяжелых нефтей, природных битумов, вакуумных дистиллятов и остаточных фракций), является высокое содержание в них смолисто-асфальтеновых веществ, гетероатомных соединений и металлсодержащих компонентов [5, 6]. Разработка методов термокаталитической деструкции смолисто-асфальтеновых компонентов с получением дополнительных количеств светлых фракций без использования водорода позволит существенно повысить эффективность процессов переработки тяжелого углеводородного сырья и, как следствие, получать нефтепродукты с более низким содержанием высокомолекулярных и гетероатомных соединений и высоким содержанием дистиллятных фракций [7–11].
Для разработки эффективных термокаталитических способов и дальнейшего использования продуктов конверсии тяжелых видов нефтяного сырья необходимы знания о влиянии температуры, давления и катализаторов на деструкцию молекул смол и асфальтенов. Известно, что существенное влияние на активность и селективность катализаторов оказывают концентрация кислотных центров и текстурные характеристики. Наиболее часто используемыми катализаторами при переработке тяжелого углеводородного сырья являются аморфные алюмосиликаты [12, 13], цеолиты Y [14, 15] и их комбинации [13, 16]. Высокая кислотность цеолитов в процессе крекинга может способствовать увеличению выхода побочных продуктов, в частности “кокса”. Они находят наибольшее применение в промышленности вследствие сочетания их разумной цены и каталитических свойств [17]. Знания о влиянии температуры, давления и катализаторов на деструкцию молекул смол и асфальтенов важны для более глубокого понимания изменений, которые происходят в компонентах тяжелого углеводородного сырья в процессах термического и каталитического крекинга, и выбора оптимальных схем модернизации установок и определения режимов нефтеперерабатывающими предприятиями [18–21].
Цель данной работы – изучение влияния текстурных характеристик аморфных алюмосиликатов на состав продуктов крекинга тяжелой нефти.
ЭКСПЕРИМЕНТАЛЬНАЯ ЧАСТЬ
Объектом исследования служила тяжелая кармальская нефть (республика Татарстан), основные физико-химические характеристики которой представлена в табл. 1. Сырье характеризуется высоким содержанием серы (S0 = 3.7 мас. %), низким содержанием дистиллятных фракций, выкипающих до 360°С (41.3 мас. %) и высоким содержанием смолисто-асфальтеновых веществ (более 30 мас. %).
Таблица 1.
Физико-химические характеристики тяжелой нефти
Показатели | Значения |
---|---|
Плотность, $\rho _{4}^{{20}},$ кг/м3 | 956 |
Вязкость, ν20, мм2/с | 1609 |
Массовая доля S, % | 3.7 |
Отношение Н/С | 1.71 |
Содержание, мас. % | |
Масла | 70.3 |
Смолы | 24.5 |
Асфальтены | 5.2 |
Фракционный состав, мас. % | |
До 200°C | 6.7 |
200–360°C | 34.6 |
>360°C | 58.7 |
Катализаторы. В качестве катализаторов использовались аморфные алюмосиликаты Al–Si-1 и -2, полученные в Институте нефтехимии и катализа РАН (г. Уфа) методом золь-гель синтеза [22]; текстурные характеристики представлены в табл. 2. Выбор данных алюмосиликатов обусловлен предположением, что именно большой размер пор (50 и 70 Å) позволит увеличить глубину деструкции высокомолекулярных компонентов масел, смол и асфальтенов (размер молекул от 14 до 45 Å).
Таблица 2.
Характеристики исходных аморфных алюмосиликатов
Параметры | Al–Si-1 | Al–Si-2 |
---|---|---|
Dср, Å | 50 | 70 |
Sуд, м2/г | 500 | 600 |
Vмикро, см3/г | 0.05 | 0.05 |
Vмезо, см3/г | 0.62 | 0.74 |
Мольное отношение SiO2/Al2O3 | 20 | 40 |
Слабые кислотные центры, мкмоль/г | 110 | 387 |
Сильные кислотные центры, мкмоль/г | 60 | 190 |
Суммарная концетрация кислотных центров, мкмоль/г | 170 | 577 |
Характеристики пористой структуры катализатора были определены методом низкотемпературной адсорбции-десорбции азота на автоматизированном газо-адсорбционном анализаторе ASAP 2020M Micromeretics. Количество рабочих адсорберов – 3, рабочий объем ампулы адсорбера – 3.5 см3, предел допускаемой погрешности температур ~10°С. Навеска образца для анализа составляла 0.2–0.3 г. Дегазацию образцов осуществляли в условиях вакуума при температуре 350°С в течение 2–4 ч. Расчет удельной поверхности (Sуд) исследуемого образца проводили с использованием одно- и многоточечного метода БЭТ в диапазоне относительных давлений 0.05 до 0.22 МПа. Объем пор (Vмикро и Vмезо) и их размер были определены из изотермы адсорбции-десорбции с использованием модели BJH (Barett–Joyner–Halenda) при относительном давлении P/P0 = 0.99. Объем микропор в присутствии мезопор определяли методом t-plot Хэлси.
Кислотные свойства исходных алюмосиликатов определяли методом температурно-программированной десорбции аммиака (ТПД-NH3) на приборе Autosorb-1-C/TCD (Quantachrome Instruments, США), оборудованного детектором по теплопроводности. Навеску образца алюмосиликата (0.5 г) прокаливали в потоке кислорода при температуре 550°С в течение 3 ч, затем образец охлаждали в потоке инертного газа до 100°С, после чего проводили адсорбцию аммиака в проточном режиме в течение 10 мин. Физически адсорбированный аммиак удаляли вакуумированием при той же температуре в течение 2 ч. Сигналы ТПД записывали в температурном интервале от 100 до 550°C при скорости нагрева 10°С/мин в потоке гелия (36 мл/мин).
Крекинг. Крекинг тяжелой нефти проводили в стационарном режиме в автоклавах объемом 12 см3. Масса нефти, загружаемой в реактор, составляла 7 г. В ранее проделанных работах мы определили оптимальные условия крекинга – 450°C в течение 100 мин [23]. Нефть с катализатором предварительно смешивали и помещали в реактор, количество Al–Si-1 и-2 варьировали от 0.5 до 5.0% от массы нефти. Оптимальное количество катализатора определяли по выходу светлых фракций и степени деструкции смол и асфальтенов.
При проведении экспериментов фиксировали массу реактора без образца и массу подготовленного к крекингу реактора с образцом. После проведения термической обработки тяжелой нефти выход газообразных продуктов определяли по потере массы реактора с образцом после удаления из реактора газовых продуктов. После удаления жидких продуктов реактор промывали хлороформом и взвешивали. Полученная разница между массой реактора до эксперимента и после рассматривалась как масса твердых продуктов (“кокс”) на поверхности реактора. Количество кокса на катализаторе определяли методом термогравиметрии. Содержание кокса в жидких продуктах определяли при анализе вещественного состава как продукт, который не смывается хлороформом с фильтра.
Определение компонентного состава жидких продуктов. Содержание асфальтенов определяли, разбавляя пробу образца н-гексаном в объемном соотношении 1 : 40, выдерживая раствор в течение суток, отфильтровывая выпавший осадок. Полученный осадок помещали в бумажный патрон и в аппарате Сокслета отмывали н-гексаном от масел и смол, затем асфальтены из патрона вымывали хлороформом, далее отгоняли растворитель и сушили асфальтены до постоянной массы.
Гексановый раствор присоединяли к деасфальтенизированному образцу, отгоняли растворитель и выделенные мальтены наносили на слой активированного силикагеля АСК (соотношение 1 : 15), загружали полученную смесь силикагеля с адсорбированным материалом в экстрактор Сокслета и последовательно вымывали нефтяные масла н-гексаном и смолы – смесью этанола и бензола (1 : 1) при температурах кипения данных растворителей. После удаления растворителей из гексанового и спирто-бензольного элюатов, высушивания и доведения до постоянной массы определяли соответственно содержание масел и смол.
Определение фракционного состава жидких продуктов. Фракционный состав жидких продуктов крекинга определяли методом газо-жидкостной хроматографии на хроматографе “Кристалл-2000М” с пламенно-ионизационным детектором, используя кварцевую капиллярную колонку 25 м × 0.22 мм со стационарной фазой SE-54, газ-носитель – гелий. Условия хроматографирования: линейное повышение температуры от 40 до 290°С, скорость нагрева термостата колонки – 15°С/мин. Идентификацию УВ для разделения отрезков хроматограмм на бензиновую (НК–200) и дизельную (200–360°С) фракции проводили по временам удерживания н-алканов с использованием калибровочной смеси С8–С40 SIGMA Aldrich.
Определение группового состава масел. Групповой углеводородный состав масел исходного сырья и продуктов его крекинга устанавливали методом жидкостно-адсорбционной хроматографии на активированном Al2O3 II степени активности по Брокману [24]. Хроматографическую колонку размером 75 × 1.8 см заполняли сорбентом “мокрым” способом в соотношении образец : сорбент = 1 : 80 по массе. Навеску образца смешивали с н-гексаном и равномерно распределяли по всей поверхности сорбента. Фракции насыщенных, моно- и биароматических УВ выделяли н-гексаном, триароматические УВ элюировали смесью гексан : бензол (3 : 1 по объему), а полиароматические УВ – смесью спирт : бензол (1 : 1 по объему). Контроль за разделением УВ различных групп осуществляли по электронным спектрам поглощения элюатов, снятым на спектрометре UNICO UV-2804.
Структурно-групповой анализ молекул смол и асфальтенов. Смолы и асфальтены, выделенные из тяжелой нефти и продуктов крекинга, исследовали методом структурно-группового анализа (СГА) по методике, основанной на совместном использовании результатов определения элементного состава, молекулярных масс и данных ПМР-спектроскопии (протонный магнитный резонанс) [25].
Элементный анализ смол и асфальтенов определяли на CHNS-анализаторе Vario EL Cube. Молекулярные массы измеряли криоскопией в нафталине на созданном в ИХН СО РАН приборе “Крион”. Спектры ПМР снимали на Фурье-спектрометре AVANCE-AV-300 при 1%-ной концентрации смол и асфальтенов с использованием в качестве растворителя дейтерохлороформа, внутренний стандарт – гексаметилдисилоксан.
РЕЗУЛЬТАТЫ И ИХ ОБСУЖДЕНИЕ
Состав продуктов крекинга тяжелой нефти представлен в табл. 3. Показано, что крекинг нефти без каталитических добавок способствует образованию газа (1.8%) и продуктов уплотнения – “кокса” (2.0%). Жидкие продукты крекинга содержат на 10.8 мас. % больше фракций, выкипающих до 360°C, по сравнению с исходным сырьем. Содержание серы снижается на 0.31 мас. % за счет образования побочных продуктов.
Таблица 3.
Состав продуктов крекинга тяжелой нефти*
Образцы | Содержание, мас. % | ||||||||
---|---|---|---|---|---|---|---|---|---|
НК–200°C | 200–360°C | 360–500°C | S | М | С | А | Г | ПУ | |
Исходная нефть | 6.7 | 34.6 | 34.6 | 3.7 | 70.3 | 24.5 | 5.2 | 0.0 | 0.0 |
Крекинг без катализатора | 12.7 | 39.4 | 19.1 | 3.3 | 72.9 | 17.9 | 5.4 | 1.8 | 2.0 |
Количество добавки катализатора мас. % | Al–Si-1 | ||||||||
0.1 | 14.2 | 35.9 | 28.7 | 2.6 | 79.0 | 9.5 | 3.8 | 5.5 | 2.2 |
0.5 | 19.8 | 36.9 | 24.1 | 2.9 | 80.1 | 9.6 | 4.4 | 4.9 | 1.0 |
1.0 | 12.4 | 48.9 | 20.2 | 3.1 | 80.5 | 12.2 | 3.5 | 2.6 | 1.2 |
3.0 | 14.7 | 45.5 | 22.7 | 2.8 | 77.2 | 12.8 | 4.3 | 4.5 | 4.2 |
5.0 | 19.2 | 36.4 | 29.9 | 2.6 | 74.1 | 14.1 | 4.2 | 4.8 | 4.5 |
Al–Si-2 | |||||||||
0.1 | 10.2 | 35.3 | 32.2 | 2.7 | 73.7 | 16.0 | 4.7 | 5.0 | 0.6 |
0.5 | 15.5 | 49.6 | 19.4 | 2.6 | 78.2 | 12.8 | 4.0 | 4.1 | 0.9 |
1.0 | 15.2 | 38.1 | 27.2 | 2.6 | 80.3 | 11.4 | 3.6 | 3.6 | 1.1 |
3.0 | 15.3 | 37.3 | 26.5 | 2.5 | 81.1 | 10.1 | 3.5 | 4.1 | 1.2 |
5.0 | 19.8 | 46.0 | 17.8 | 2.5 | 81.6 | 7.1 | 3.2 | 5.7 | 1.3 |
Установлено, что зависимость состава продуктов крекинга нефти от варьирования количества аморфных алюмосиликатов в интервале от 0.1 до 5.0 мас. % носит нелинейный характер. Оптимальное количество катализатора оценивали по выходу светлых фракций и деструкции смол и асфальтенов.
Так при 0.1 мас. % Al–Si-1 наблюдается увеличение суммарного выхода побочных продуктов (газа и кокса) на 3.9 мас. % и деструкции смол и асфальтенов на 8.4 и 1.6 мас. % соответственно по сравнению с крекингом без катализатора. Однако при этом выход целевых продуктов – фракций выкипающих до 360°C – меньше на 2 мас. %, чем при крекинге без катализатора.
При увеличении количества Al–Si-1 от 0.1 до 1.0 мас. % наблюдается снижение выхода газообразных и твердых продуктов и их суммарное содержание не превышает 4 мас. %. Выход светлых фракций (НК–360°C) составил 61.3 мас. %, что на 20.0% больше, чем в исходной нефти. Суммарное количество смол и асфальтенов составило 15.7 мас. %, что на 7.6 мас. % меньше, чем при крекинге без катализатора, но на 2.4 мас. % больше, чем при крекинге нефти с использованием 0.1 мас. % Al–Si-1. Исходя из сравнительных данных по крекингу нефти с 1.0 мас. % Al–Si-1 и исходной нефтью, видно, что суммарное содержание смол и асфальтенов уменьшилось на 14.0 мас. %, а выход светлых фракций увеличился на 20.0 мас. %, можно сделать заключение, что высокомолекулярные компоненты масел, тоже деструктируют с образованием фракций НК–360°C.
Дальнейшее увеличение количества катализатора до 3.0 и 5.0 мас. % приводит к:
• повышению выхода газообразных и твердых продуктов;
• увеличению деструкции фракций, выкипающих в интервале 200–360°C, с образованием фракций НК–200°C;
• конденсации масел по пути реакции: масла > > смолы > асфальтены > продукты уплотнения.
Содержание серы снижается в серии экспериментов с использованием Al–Si-1 по сравнению с крекингом без катализатора. В процессе крекинга сера из жидких продуктов переходит в газ и в продукты уплотнения. Минимальное содержание серы в жидких продуктах крекинга наблюдается при использовании катализатора в количествах 0.1 и 5.0 мас. %. При использовании оптимального количества Al–Si-1 1.0 мас. % удаление серы происходит всего на 0.6 мас. %, что обусловлено снижением выхода побочных продуктов в этом эксперименте.
Таким образом, исходя из полученных данных, оптимальным количеством катализатора Al–Si-1 является 1.0 мас. %.
Использование катализатора Al–Si-2, обладающего большим размером и объемом пор, приводит к другому составу продуктов крекинга по сравнению с Al–Si-1. Это обусловлено большей поверхностью катализатора и доступностью для крупных молекул смол и асфальтенов, которые не могли попасть в объем катализатора Al–Si-1. При сравнительном анализе состава продуктов крекинга с катализаторами 1 и 2 с одинаковыми количествами (0.1 мас. %) установлено, что крекинг с Al–Si-2 приводит к снижению выхода масел, бензиновых фракций, замедлению деструкции смол и асфальтенов, образованию продуктов уплотнения.
При крекинге нефти с 0.5 мас. % Al–Si-2 снижается суммарный выход побочных продуктов на 0.6 мас. % за счет газообразования. Деструкция смолисто-асфальтеновых компонентов на 3.9 мас. % выше, чем при крекинге с 0.1 мас. %-ным катализатором. Содержание светлых фракций (НК–360°C) в жидких продуктах крекинга увеличивается на 23.8 мас. % по сравнению с исходным сырьем и на 13.0 мас. % по сравнению с крекингом нефти без катализатора.
Если сравнить деструкцию смол и асфальтенов (12.9 мас. %) и дополнительный выход светлых фракций (23.8 мас. %) при крекинге с 0.5 мас. % Al–Si-2 с исходной нефтью, то видно, что прирост фракций, выкипающих до 360°C, обеспечивается не только деструкцией смолисто-асфальтеновых компонентов, но и высокомолекулярными компонентами масел.
Увеличение количества добавки катализатора Al–Si-2 от 1.0 до 5.0 мас. % приводит к увеличению выхода газообразных и твердых продуктов крекинга, повышению деструкции смолисто-асфальтеновых компонентов и увеличению выхода фракций, выкипающих до 360°C.
Следует отметить, что выход светлых фракций при крекинге нефти с 5.0% Al–Si-2 составил 65.8 мас. %, что больше, чем при 0.5 мас. %-ном Al–Si-2. При этом содержание смол и асфальтенов ниже на 6.5 мас. %, чем при использовании 0.5 мас.%-ного Al–Si-2. Поскольку различия в выходах светлых фракций незначительны, оптимальным количеством катализатора Al–Si-2 было принято считать 0.5 мас. %.
Данные по составу газообразных продуктов крекинга представлены на рис. 1. Видно, что катализатор Al–Si-2, у которого концентрация кислотных центров выше, чем у Al–Si-1, приводит к увеличению выхода серосодержащих газов и олефинов С2-С5. Кроме того, в составе газообразных продуктов идентифицированы н-С5Н12, изо-С5Н12 и изо-С5Н10. Следует отметить, что при использовании Al–Si-1 отношение суммарного содержания газообразных н-алканов С1–С2 к сумме С3–С5 равно 2, тогда как при использовании Al–Si-2 оно равно 1.3.
В табл. 4 представлены характеристики аморфных алюмосиликатов до и после процесса крекинга с тяжелой нефтью, из которой видно, что воздействие компонентов нефти на пористую структуру Al–Si протекало интенсивно. При крекинге с Al–Si-1 поверхность катализатора практически полностью покрывается продуктами уплотнения, снижается удельная поверхность (Sуд) катализатора в 15.5 раз, размер (Dср) и объем пор (Vмезо) в 25 и 21 раз соответственно. При использовании Al–Si-2 также происходит деградация катализатора, но в меньшей степени, о чем свидетельствуют снижения Sуд (в 3.5 раза), Dср (в 2.7 раза) и Vмезо (в 3.9 раза).
Таблица 4.
Характеристики Al–Si до и после крекинга тяжелой нефти
Катализатор | Dср, Å | Sуд, м2/г | Vмикро, см3/г | Vмезо, см3/г | |
---|---|---|---|---|---|
Al–Si-1 | До крекинга | 50 | 500 | 0.05 | 0.62 |
После крекинга | 2 | 32 | 0.01 | 0.03 | |
Al–Si-2 | До крекинга | 70 | 600 | 0.05 | 0.74 |
После крекинга | 26 | 175 | 0.04 | 0.19 |
Отличия в характеристиках (Sуд, Dср и Vмезо) аморфных алюмосиликатов после процесса, вероятно, обусловлены тем, что активные центры катализатора, которые сосредоточены в объеме, становятся более доступными для крупных молекул смол и асфальтенов с увеличением размера пор исходного катализатора от 50 до 70 Å.
Для оценки влияния аморфных алюмосиликатов на процесс крекинга тяжелой нефти проанализирован групповой состав масел (рис. 2). При крекинге нефти Al–Si-1 и 2 наблюдаются схожие закономерности:
Рис. 2.
Углеводородный состав масел исходной нефти и продуктов крекинга с оптимальными количествами Al–Si-1 и Al–Si-2: Н– насыщенные УВ; М –моноароматические УВ; Б – биароматические УВ; Т– триароматические УВ; П – полиароматические УВ.
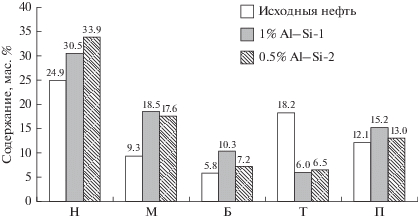
– увеличивается содержание насыщенных, моно-, би- и полиаренов по сравнению с исходной нефтью;
– уменьшается количество триароматических углеводородов.
Для установления основных направлений деструкции высокомолекулярных компонентов был проведен структурно-групповой анализ смол и асфальтенов, выделенных из исходной нефти и продуктов ее крекинга (табл. 5 ). Согласно данным структурно-группового анализа усредненная молекула асфальтенов исходной нефти имеет молекулярную массу 1921 а. е. м. и состоит из четырех блоков; содержит 24 кольца – 15 ароматических и 9 нафтеновых. Атомное отношение Н/C составляет всего 1.22. В составе средней молекулы асфальтенов содержится 2 атома кислорода, 4 серы и 3 азота.
При крекинге нефти без катализатора молекулярная масса асфальтенов снижается с 1921 до 1668 а. е .м. Увеличивается число блоков с 4.0 до 6.6. Размеры блоков уменьшаются по сравнению с исходными асфальтенами. В средней молекуле асфальтенов снижается общее количество колец на 3.1 за счет снижения количества ароматических циклов. Количество атомов углерода в алифатических фрагментах снижается с 35 до 23 атомов.
При крекинге нефти в присутствии 1.0 мас. %-ного Al–Si-1 снижается молекулярная масса асфальтенов с 1921 до 1220 а. е. м. и количество блоков с 4.0 до 3.0. Общее количество колец увеличивается на 6.3 (нафтеновые циклы увеличиваются на 10.6, а ароматические снижаются на 4.3). В средних молекулах асфальтенов снижается атомное отношение Н/C с 1.22 до 0.75 и количество атомов углерода в алифатических фрагментах с 35.0 до 1.8. Эти данные указывают, что при крекинге нефти с 1.0 мас. %-ного Al–Si-1 средние структуры молекул асфальтенов подвергаются деструкции за счет реакций деалкилирования и циклизации.
Таблица 5.
Структурно-групповые параметры молекул асфальтенов и смол тяжелой нефти и продуктов ее термо- и каталитического крекинга
Параметры | Асфальтены | Смолы | ||||||
---|---|---|---|---|---|---|---|---|
1 | 2 | 3 | 4 | 1 | 2 | 3 | 4 | |
Средняя ММ, а. е. м. | 1921 | 1668 | 1220 | 1039 | 743 | 768 | 557 | 622 |
Атомное отношение Н/C | 1.22 | 1.29 | 0.75 | 0.96 | 1.28 | 1.19 | 1.09 | 1.07 |
Число атомов в средней молекуле | ||||||||
C | 130.1 | 111.7 | 81.9 | 68.9 | 49.7 | 51.7 | 36.9 | 41.0 |
H | 157.4 | 143.6 | 60.9 | 65.6 | 63.1 | 60.8 | 39.8 | 43.6 |
N | 3.1 | 2.5 | 1.6 | 1.5 | 0.6 | 0.9 | 0.6 | 0.7 |
S | 3.9 | 2.5 | 1.9 | 1.4 | 1.2 | 1.1 | 0.6 | 0.8 |
O | 2.2 | 4.2 | 5.8 | 4.9 | 2.2 | 2.4 | 2.8 | 3.1 |
Число колец | ||||||||
Ko | 24.3 | 21.2 | 30.6 | 16.6 | 10.8 | 11.6 | 9.8 | 10.7 |
Ka | 14.7 | 10.8 | 10.4 | 9.7 | 3.8 | 5.0 | 3.6 | 4.2 |
Kнас | 9.6 | 10.4 | 20.2 | 6.9 | 7.0 | 6.6 | 6.2 | 6.5 |
ma | 4.0 | 6.6 | 3.0 | 2.8 | 1.7 | 1.9 | 1.6 | 1.8 |
σа | 0.54 | 0.36 | 0.56 | 0.47 | 0.63 | 0.57 | 0.59 | 0.57 |
Распределение атомов углерода, % | ||||||||
ƒа | 43.1 | 54.0 | 49.7 | 55.7 | 31.1 | 39.3 | 40.3 | 42.1 |
ƒн | 29.9 | 25.5 | 48.1 | 40.8 | 58.1 | 51.9 | 54.5 | 52.7 |
ƒп | 27.0 | 20.5 | 2.2 | 3.5 | 10.8 | 8.8 | 5.2 | 5.3 |
Число атомов углерода разного типа в средней молекуле | ||||||||
Са | 56.1 | 60.3 | 40.7 | 38.4 | 15.4 | 20.3 | 14.9 | 17.3 |
Сн | 39.0 | 28.4 | 39.5 | 28.1 | 28.9 | 26.8 | 20.1 | 21.6 |
Сп | 35.0 | 23.0 | 1.8 | 2.4 | 5.4 | 4.6 | 1.9 | 2.2 |
Сα | 19.4 | 16.8 | 14.9 | 11.9 | 7.3 | 8.3 | 6.6 | 7.2 |
Сγ | 7.8 | 5.3 | 1.8 | 1.9 | 3.8 | 3.3 | 1.9 | 2.2 |
Примечания. (а) 1 – исходная нефть; 2 – продукты крекинга нефти без катализатора; 3 – продукты крекинга нефти в присутствии 1.0 мас. %-ного Al–Si-1; 4 – продукты крекинга нефти в присутствии 0.5 мас. %-ного Al–Si-2;. (б) число атомов углерода в средней молекуле: ММ – молекулярная масса, Са – в ароматических и Сн – в нафтеновых кольцах, Сп – в алифатических фрагментах, Сα – в α-положении к ароматическому кольцу, Сγ – в положениях β- и далее от ароматического кольца; (в) число колец: Ко –общее, Ка –ароматических, Кнас –насыщенных; (г) доля атомов углерода в: ƒа –ароматических, ƒн – нафтеновых и ƒп – парафиновых фрагментах. (д) σа – cтепень замещенности ароматических ядер, ma – число блоков в молекуле.
Крекинг нефти с 0.5 мас. %-ным Al–Si-2 приводит к снижению молекулярной массы асфальтенов с 1921 до 1039 а. е. м. и количества блоков с 4.0 до 2.8. В средних молекулах асфальтенов снижается атомное отношение Н/C с 1.22 до 0.96, общее количество колец на 7.7, количество атомов углерода в алифатических фрагментах с 35.0 до 2.4. Из этих данных можно сделать вывод, что средняя молекула асфальтенов состоит из ароматических колец в центре и нафтеновых по периферии.
Средняя молекула смол исходной нефти имеет молекулярную массу 743 и состоит преимущественно из нафтеновых и ароматических колец. Содержание ароматических атомов углерода Са составляет всего 1/3 от общего числа атомов углерода. Средняя молекула смол преимущественно двухблочная, общее число колец 10.8, из которых 3.8 – ароматических и 7.0 – нафтеновых. Низкое отношение Н/С (1.28) является следствием сконденсированности ароматических колец и значительной их замещенности σа. В средней молекуле смол содержится 2 атома кислорода, по одному атому серы и азота.
Крекинг нефти без катализатора приводит к увеличению молекулярной массы смол с 743 до 768 а. е. м.; содержание атомов С увеличивается на 2.0, а Н уменьшается на 2.3. Количество колец в средней молекуле смол увеличивается до 11.6, а доля атомов углерода в ароматических циклах (ƒа) возрастает на 8.2%. Число атомов углерода в алифатических фрагментах (Cп) снижается, отношение Н/С также снижается с 1.28 до 1.19. Все это свидетельствует о протекании реакций деалкилирования и ароматизации. Количество кислорода и азота в составе средней молекулы незначительно увеличивается.
Смолы, выделенные из продуктов крекинга нефти в присутствии 1.0 мас. %-ного Al–Si-1 и 0.5 мас.%-ного Al–Si-2 претерпевают одинаковые изменения по сравнению с исходными смолами: снижается молекулярная масса, число атомов углерода в алифатических фрагментах (Сп) и их длина (Сγ), увеличивается доля атомов углерода в ароматических фрагментах (ƒа). Исходя из данных структурно-групповго анализа асфальтенов, выделенных из продуктов крекинга нефти с катализаторами, можно сделать вывод, что Al–Si-1 способствует образованию более конденсированных молекул асфальтенов, приводящих к образованию продуктов уплотнения, тогда, как Al–Si-2 способствует образованию ароматического ядра в асфальтенах, которые сопряжены с нафтеновыми кольцами по периферии молекулы.
ЗАКЛЮЧЕНИЕ
Изучен крекинг тяжелой нефти в присутствии различного количества аморфных алюмосиликатов с размером пор 50 и 70 Å. Установлены оптимальные количества Al–Si-1 (1.0 мас. %) и Al–Si-2 (0.5 мас. %), которые позволяют увеличить выход светлых фракций на 22–24% и деструкцию смол, асфальтенов и высокомолекулярных компонентов масел. Исходя из данных группового состава масел показано, что аморфные алюмосиликаты способствуют значительной деструкции триароматических углеводородов, а основный прирост количества масел происходит за счет увеличения содержания насыщенных и моноароматических УВ.
Установлено, что использование аморфного алюмосиликата с размером пор 50 Å приводит к практически полному покрытию Al–Si-1 продуктами уплотнения. Выявлено, что средняя молекула асфальтенов при крекинге тяжелой нефти в присутствии Al–Si-1 становится более сконденсированной (коксоподобной).
Изучено, что Al–Si-2 (с размером пор 70 Å) при крекинге тяжелой нефти, в меньшей степени подвергается отложению продуктов уплотнения. Показано, что средние молекулы асфальтенов становятся меньше, состоят из ароматического ядра окруженного нафтеновыми кольцами. Установлено, что различные текстурные характеристики Al–Si-1 и Al–Si-2 не оказывают изменения в структуре средних молекул смол.
Список литературы
Okunev A.G., Parkhomchuk E.V., Lysikov A.I., Parunin P.D., Semeikina V.S., Parmon V.N. // Russ. Chem. Rev. 2015. № 9. P. 987.
Angeles M.J., Leyva C., Ancheyta J., Ramírez S. // Catal. Today. 2014. V. 220−222. P. 274.
Shahandeh H., Li Z. // Energy & Fuels. 2016. V. 30. P. 5202.
Nassar N.N., Hassan A., Pereira-Almao P. // Energy & Fuels. 2011. V. 25. P. 1566.
Yakubov M.R., Milordov D.V., Yakubova S.G., Borisov D.N., Ivanov V.T. Sinyashin K.O. // Petrol. Chemistry. 2016. V. 56. № 1. P. 16.
Yakubov M.R., Milordov D.V., Yakubova S.G., Borisov D.N., Gryaznov P.I., Mironov N.A., Abilova G.R., Borisova Y.Y., Tazeeva E.G. // Petroleum Science and Technology. 2016. V. 34. № 2. P. 177.
Sodero A.C.R., Silva H.S., Level P.G., Bouyssiere B., Korb J.-P., Carrie H., Alfarra A., Bégué D., Baraille I. // Energy & Fuels. 2016. V. 30. P. 4758.
Ortega García F.J., Juárez E.J. // Energy & Fuels. 2017. V. 31. P. 7995.
Hauser A., Humaidan F., Al-Rabiah H., Halabi M.A. // Energy & Fuels. 2014. V. 28. P. 4321.
Zhang J.X., Zhou Y., Xu Y., Tian H.P. // China Petroleum Processing & Petrochemical Technology. 2014. V. 6. P. 7.
Sviridenko N.N., Krivtsov E.B., Golovko A.K. // Chemistry for sustainable development. 2017. V. 25. № 1. P. 79.
Leyva C., Ancheyta J., Travert A., Maugé F., Mariey L., Ramírez J., Rana M.S. // Applied Catalysis A: General. 2012. V. 425–426. P. 1.
Ahmed S., Ali S.A., Hamid H., Honna K. // Science and Technology in Catalysis. 2002. V. 145. P. 295.
Hassan A., Ahmed S., Ali M.A., Hamid H., Inui T. // Applied Catalysis A: General. 2001. V. 220. P. 59.
Ishihara A., Itoh T., Nasu H., Hashimoto T., Doi T. // Fuel Processing Technology. 2013. V. 116. P. 222.
Ali M.A., Tatsumi T., Masuda T. // Applied Catalysis A: General. 2002. V. 233. P. 77.
Minderhoud J.K., Veen J.A.R., Hagan A.P. // Studies in Surface Science and Catalysis. 1999. V.127. P. 3.
Bagheri S.R., Gray M.R., Shaw J.M., McCaffrey W.C. // Energy & Fuels. 2012. V. 26. № 6. P. 3167.
Palermo A., Solovyov A., Ertler D., Okrut A., Gates B.C., Katz A. // Chem. Sci. 2017. V. 8. № 7. P. 4951.
Martinez-Grimaldo H., Ortiz-Moreno H., Sanchez-Minero F., Ramírez J., Cuevas-Garcia R., Ancheyta-Juarez J. // Catal. Today 2014. V. 220−222. P. 295.
Luo H., Deng W., Gao J., Fan W., Que G. // Energy & Fuels. 2011. V. 25. P. 1161.
Agliullin M.R., Grigor’eva N.G., Danilova I.G., Magaev O.V., Vodyankina O.V. // Kinetics and Catalysis. 2015. V. 56. № 4. P. 501.
Свириденко Н.Н., Кривцов Е.Б., Головко А.К. // Химия в интересах устойчивого развития. 2018. № 2. С. 193.
Певнева Г.С., Воронецкая Н.Г., Корнеев Д.С., Головко А.К. // Нефтехимия. 2017. Т. 57. № 4. С. 479.
Головко А.К., Горбунова Л.В., Камьянов В.Ф. // Геология и геофизика. 2010. Т. 51. № 3. С. 364.
Дополнительные материалы отсутствуют.
Инструменты
Нефтехимия