Неорганические материалы, 2019, T. 55, № 12, стр. 1305-1312
Влияние структуры и состава носителя на активность Cu–Ni-катализаторов процесса парового риформинга метанола
А. А. Лыткина 1, *, Н. А. Бакулева 1, Н. В. Орехова 1, М. М. Ермилова 1, А. Б. Ярославцев 1, 2, 3
1 Институт нефтехимического синтеза им. А.В. Топчиева Российской академии наук
119991 Москва, Ленинский пр., 29, Россия
2 Институт общей и неорганической химии им. Н.С. Курнакова Российской академии наук
119071 Москва, Ленинский пр., 31, Россия
3 Национальный исследовательский университет “Высшая школа экономики“
101000 Москва, ул. Мясницкая, 20, Россия
* E-mail: lytkina@ips.ac.ru
Поступила в редакцию 10.05.2019
После доработки 06.06.2019
Принята к публикации 21.06.2019
Аннотация
Исследована каталитическая активность биметаллических Cu–Ni-катализаторов, полученных на основе оксидов циркония и церия, допированнных иттрием, оловом, цинком и ниобием, в процессе парового риформинга метанола (ПРМ) для получения водорода. Изучено влияние природы допанта и температуры отжига на структуру и дисперсность оксидного носителя, а также каталитическую активность металл-оксидного композита. Введение гетеровалентных ионов во всех случаях приводило к повышению каталитической активности образцов в процессе ПРМ по сравнению с недопированным оксидом циркония, максимальный выход водорода достигался при использовании катализаторов, допированных оксидами ниобия и иттрия.
ВВЕДЕНИЕ
В связи с проблемой загрязнения окружающей среды продуктами сгорания топлива поиск новых экологически чистых источников энергии с каждым годом становится все более актуальным. Одной из перспективных технологий является производство электроэнергии с использованием топливных элементов. В связи с этим водород становится одним из наиболее востребованных продуктов для альтернативной энергетики [1–6]. Однако его транспортировка и хранение представляются достаточно сложными задачами. Одним из решений упомянутых проблем является производство водорода из жидкого сырья, такого как низшие спирты [7–11].
Паровой риформинг метанола (ПРМ) протекает при относительно низких температурах (200–350°С) с высокой селективностью по водороду. В процессе ПРМ помимо целевой реакции (1) протекают также реакции разложения метанола (2) и взаимодействия образующегося СО с водой (3), в результате чего образуется смесь водорода, диоксида углерода и небольшой примеси монооксида углерода:
(1)
$\begin{gathered} {\text{C}}{{{\text{H}}}_{{\text{3}}}}{\text{OH}} + {{{\text{H}}}_{{\text{2}}}}{\text{O}} \leftrightarrow {\text{C}}{{{\text{O}}}_{2}} + 3{{{\text{H}}}_{2}},~ \\ \Delta H_{{298{\text{ K}}}}^{0} = 49.7\,\,{{{\text{кДж}}} \mathord{\left/ {\vphantom {{{\text{кДж}}} {{\text{моль}};}}} \right. \kern-0em} {{\text{моль}};}} \\ \end{gathered} $(2)
$\begin{gathered} {\text{C}}{{{\text{H}}}_{{\text{3}}}}{\text{OH}} \leftrightarrow {\text{CO}} + 2{{{\text{H}}}_{2}},~ \\ \Delta H_{{298{\text{ K}}}}^{0} = 90.2\,\,{{{\text{кДж}}} \mathord{\left/ {\vphantom {{{\text{кДж}}} {{\text{моль}};}}} \right. \kern-0em} {{\text{моль}};}} \\ \end{gathered} $(3)
$\begin{gathered} {\text{CO}} + {{{\text{H}}}_{{\text{2}}}}{\text{O}} \leftrightarrow {\text{C}}{{{\text{O}}}_{2}} + {{{\text{H}}}_{2}}, \\ \Delta H_{{298{\text{ K}}}}^{0} = - 41.2\,\,{{{\text{кДж}}} \mathord{\left/ {\vphantom {{{\text{кДж}}} {{\text{моль}}}}} \right. \kern-0em} {{\text{моль}}}}. \\ \end{gathered} $Наиболее часто в качестве катализаторов используются медь и металлы VIIIB-группы, отличающиеся высокой активностью и селективностью по водороду. Одним из способов повышения стабильности и снижения стоимости таких катализаторов является добавление второго металла [12–16]. Используемые каталитические системы в основном представлены нанодисперсными частицами металлов, нанесенными на носитель, роль которого зачастую играют оксидные системы [17–22]. При этом, согласно бифункциональному механизму, стадии превращения спирта протекают на атомах металла, а носитель обеспечивает центры для активации воды, что подчеркивает важность его выбора. Дизайн структуры и химический состав носителя позволяют влиять на активность и селективность каталитического композита в целом.
Таблица 1.
Удельная площадь поверхности и характерные размеры частиц исследуемых катализаторов, рассчитанные методами БЭТ и РФА
Материал | S, м2/г | Средний размер частиц по БЭТ, нм | ОКР, нм | |
---|---|---|---|---|
ZrO2 | MxOy | |||
ZrO2 | 155 ± 8 | 40 | 10 ± 1 | – |
CeO2–SnO2 (10%) | 75 ± 3 | 80 | 11 ± 1 | – |
ZrO2–Y2O3 (10%) | 52 ± 2 | 70 | 13 ± 1 | |
ZrO2–SnO2 (10%) | 49 ± 2 | 120 | 8 ± 1 | 4 ± 2 |
ZrO2–ZnO (10%) (400°С) | 59 ± 2 | 100 | 5 ± 2 | – |
ZrO2–ZnO (10%) (800°С) | 14 ± 1 | 33 ± 1 | 24 ± 1 | |
ZrO2–Nb2O5 (10%) (400°С) | 134 ± 4 | 45 | 8 ± 2 | – |
ZrO2–Nb2O5 (10%) (800°С) | 47 ± 2 | 12 ± 1 | 17 ± 1 |
Значительный интерес в качестве носителя металлических катализаторов процесса ПРМ представляет оксид циркония [23–26], являющийся, как показано рядом исследований, промотором медьсодержащих катализаторов [27]. Оксид циркония может существовать в нескольких кристаллических модификациях, при этом формирования той или иной структуры можно добиться, регулируя температуру обработки, природу и концентрацию допанта [28]. Кроме того, использование допантов приводит к большей разупорядоченности и подвижности кислородной подрешетки оксида циркония и к увеличению числа активных центров на поверхности катализатора, в роли которых, возможно, выступают структурные дефекты [29, 30]. В качестве допантов представляется перспективным использование гетеровалентных ионов (Y3+, Sc3+, Ca2+, Mg2+), введение которых приводит к появлению вакансий в подрешетке, обеспечивающих высокую подвижность кислорода, а также элементов, обладающих способностью к окислительно-восстановительным превращениям, таких, например, как церий и олово [31, 32]. Интерес к SnO2 в гетерогенном катализе главным образом обусловлен его способностью выступать в качестве эффективного катализатора окисления, особенно в реакциях с участием СО [33], что, по нашему предположению, могло бы повысить селективность катализаторов ПРМ. Оксид ниобия выполняет двоякую функцию: повышает дефектность кристаллической решетки и, несмотря на низкую окислительно-восстановительную активность, способен обеспечить повышение активности катализатора в реакциях окисления и дегидрирования [34–37].
Ранее нами были исследованы Ni–Сu-катализаторы на основе оксида циркония с тетрагональной и моноклинной структурами [24]. Целью данной работы явилось создание биметаллических Ni–Cu-катализаторов на основе оксидов циркония и церия, допированнных иттрием, оловом, цинком и ниобием, а также исследование полученных катализаторов в реакции паровой конверсии метанола в диапазоне температур 200–350°С.
ЭКСПЕРИМЕНТАЛЬНАЯ ЧАСТЬ
Синтез и физико-химические исследования катализаторов и методика каталитических опытов. Недопированный оксид циркония был приготовлен методом осаждения концентрированным раствором гидроксида аммония из оксинитрата циркония ZrO(NO3)2 (99% ALDRICH) при pH 9 по методике, подробно описанной в работе [38]. Образцы ZrO2–0.1Y2O3, ZrO2–0.1SnO2, ZrO2–0.1ZnO, ZrO2–0.1Nb2O5, CeO2–0.1SnO2 были приготовлены методом соосаждения из оксинитрата циркония ZrO(NO3)2 (99% ALDRICH), нитратов церия Ce(NO3)3 ∙ 6H2O (99.995%), иттрия Y(NO3)3 ∙ 6H2O (“х. ч.”), хлоридов олова(IV) SnCl4 ⋅ 5H2O (98%, ALDRICH) и ниобия NbCl5 (99.8%, Acros) и ацетата цинка Zn(CH3COO)2 ⋅ 2H2O (“ч. д. а.”, ALDRICH) по аналогичной методике. Полученные на первой стадии гидратированные оксиды отжигали на воздухе в течение 5 ч при температуре 400°С в муфельной печи для формирования кристаллической структуры. Для установления влияния температуры отжига на физико-химические характеристики некоторые материалы повторно отжигали при 800°С.
Полученные образцы поочередно пропитывали водными растворами Сu(NO3)2 · 3H2O (>98%) и Ni(NO3)2 · 6H2O (≥98.5% ALDRICH) в количествах, рассчитанных так, чтобы суммарное содержание металлов составило 20% от массы носителя. Соотношение никеля и меди в образцах составило 1 : 4, что, согласно данным [24], является оптимальным для системы Cu–Ni. Приготовленную суспензию диспергировали в ультразвуковой ванне в течение 1 ч, затем избыток воды выпаривали при 100°С в сушильном шкафу. Полученные катализаторы отжигали на воздухе при 400°С в течение 3 ч и в потоке Н2 (5%)/Ar (20 мл/мин) в течение 3 ч при 350°С для восстановления металлов. По данным микрозондового анализа, соотношение никеля и меди для всех образцов приблизительно соответствует исходной загрузке.
Площадь поверхности и размер пор полученных носителей и катализаторов были исследованы методом БЭT на приборе ASAP-2020N (Micromeritics Co, USA). Рентгенофазовый анализ (РФА) образцов осуществляли с помощью рентгеновского дифрактометра Rigaku D/Max-2200 (${\text{Cu}}{{K}_{{{{\alpha }_{1}}}}}$-излучение). Для обработки спектров и качественного анализа использовался пакет программ Rigaku Application Data Processing. Размер частиц (область когерентного рассеяния (ОКР)) был оценен по ширине рентгеновских пиков с помощью формулы Шеррера:
где k = 0.89 – постоянная Шеррера, λ = 1.5406 Å – длина волны используемого излучения, B – полуширина пика на полувысоте (2θ), b – инструментальное уширение (2θ), θ – угол положения пика.ПРМ проводили при атмосферном давлении в традиционном трубчатом реакторе (длина трубки 21.5 см, внутренний диаметр 0.9 см) в диапазоне температур 200–400°С. Образец катализатора (загрузка 0.3 г) смешивался с гранулированным кварцем (фракция 1–3 мм) и помещался в середину реактора. Нагревание реактора до температуры опытов осуществлялось электропечью при омывании катализатора потоком аргона (20 мл/мин), температуру реактора измеряли хромель-алюмелевой термопарой. Перед каждой серией опытов катализатор восстанавливали током Н2 (5%)/Ar (20 мл/мин) при температуре 350°С в течение 3 ч. Жидкая смесь метилового спирта с водой со стехиометрическим молярным соотношением 1 : 1 подавалась в испаритель с помощью инфузионного насоса Instilar 1488 Dixion. Непрореагировавшие воду и спирт конденсировали в стеклянном приемнике, охлажденном до +1°С. Анализ состава несконденсировавшихся продуктов реакции проводили на газовом хроматографе ЛХМ 8МД с детектором по теплопроводности, газом-носителем – He и колонками со стационарной фазой Porapak T (для воды, метанола и других оксигенатов) – и активированным углем (для СO и СO2). Концентрации водорода и метана в продуктах определяли на хроматографе Chrom-4 с детектором по теплопроводности и цеолитной колонкой (фаза CaA Zeosorb, газ-носитель Ar). Хроматограммы обрабатывались с помощью программы Ecochrom.
Величины степени конверсии метанола Х (мол. %) и селективности процесса риформинга (S, %) рассчитывались по результатам анализа с использованием следующих уравнений:
(5)
$X{}_{{{\text{C}}{{{\text{H}}}_{{\text{3}}}}{\text{OH}}}} = \frac{{{{n}_{{{\text{C}}{{{\text{H}}}_{{\text{3}}}}{\text{OH}},in}}} - {{n}_{{{\text{C}}{{{\text{H}}}_{{\text{3}}}}{\text{OH}},out}}}}}{{{{n}_{{{\text{C}}{{{\text{H}}}_{{\text{3}}}}{\text{OH}},in}}}}} \times 100\% ,$(6)
$S = \frac{{{{n}_{{{\text{C}}{{{\text{O}}}_{2}},out}}}}}{{{{n}_{{{\text{C}}{{{\text{O}}}_{{\text{2}}}},out}}} + {{n}_{{{\text{CO,}}out}}}}} \times 100\% ,$РЕЗУЛЬТАТЫ И ОБСУЖДЕНИЕ
Структурные и морфологические характеристики катализаторов и носителя. На рис. 1 приведены рентгенограммы полученных образцов, отожженных при температуре 400°С. Рефлексы образцов ZrO2–Y2O3 и CeO2–SnO2 индицируются в кубической сингонии; при этом линий, соответствующих оксидам олова и иттрия, не обнаружено, что свидетельствует о формировании твердых растворов (рис. 1, дифрактограммы 5, 6). Следует отметить небольшое смещение положений полос CeO2 в сторону больших углов, что связано с частичным замещением ионов Ce4+ (0.97 Å) на катионы Sn4+ с меньшим ионным радиусом (0.69 Å) при формировании твердого раствора. Параметр кубической элементарной ячейки твердого раствора CeO2–SnO2 составляет 5.4018 ± 0.0009, что несколько меньше величины, характерной для элементарной ячейки недопированного диоксида церия (5.4111 Å). В системе ZrO2–Y2O3 допирование иттрием, напротив, приводит к увеличению параметра решетки ZrO2 (${{a}_{{{\text{Zr}}{{{\text{O}}}_{2}} - {{{\text{Y}}}_{{\text{2}}}}{{{\text{O}}}_{3}}}}}$ = 5.1233 Å) за счет замещения Zr4+ (0.84 Å) на катионы Y3+ с бóльшим ионным радиусом (0.93 Å) с формированием твердых растворов.
Рис. 1.
Фрагменты рентгенограмм материалов, отожженных при 400°С: 1 – ZrO2, 2 – ZrO2–SnO2, 3 – ZrO2–Nb2O5, 4 – ZrO2–ZnO, 5 – ZrO2–Y2O3, 6 – CeO2–SnO2.
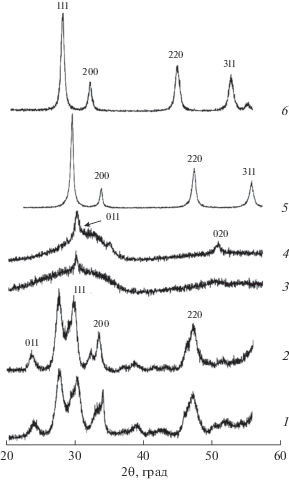
В случае допирования оксида циркония оловом эффект выражен намного слабее. Этот материал, как и недопированный образец, отожженный при 400°С, кристаллизуется в моноклинной модификации (рис. 1, кривые 1, 2). При этом на его рентгенограмме присутствуют рефлексы как оксида циркония, так и оксида олова, что указывает на меньшую растворимость олова в кристаллической решетке оксида циркония.
Что касается образцов ZrO2–ZnO и ZrO2–Nb2O5, после отжига при температуре 400°С они дают слабо закристаллизованную массу, в которой присутствуют наночастицы тетрагонального оксида циркония и рентгеноаморфная фаза, проявляющаяся на рентгенограмме в виде широкого галло (рис. 1, кривые 3 и 4).
При увеличении температуры отжига образца, допированного оксидом цинка, до 800°С формируется моноклинная модификация ZrO2, (рис. 2, кривая 1), однако также присутствует слабый рефлекс, отвечающий тетрагональной структуре. Кроме того, оксид цинка формирует самостоятельную фазу, рефлексы которой четко индицируются на полученной рентгенограмме.
В системе, допированной ниобием, после отжига при 800°С оксид циркония формирует тетрагональную фазу (рис. 2, кривая 2). При этом наблюдаются и слабые рефлексы оксида ниобия. Таким образом, в данном случае ниобий частично растворяется в оксиде циркония, формируя дефектную тетрагональную структуру.
В табл. 1 представлены некоторые характеристики синтезированных носителей, полученные методами БЭТ и РФА. Прослеживается тенденция к понижению удельной площади поверхности полученных материалов при введении допанта. При этом размеры ОКР основной оксидной фазы меняются слабо. Рассчитанный на основании данных БЭТ размер частиц на один–два порядка превышают величину ОКР, что обусловлено агломерацией наночастиц. Повышение температуры отжига приводит к формированию материала с менее развитой поверхностью и существенно более крупными частицами (табл. 1). В связи с этим для получения каталитических систем далее использовались носители, отожженные при 400°С.
Рефлексы на рентгенограммах Cu–Ni-катализаторов, нанесенных на оксидные системы, соответствуют доминирующей в составе катализатора меди (рис. 3). В то же время наблюдается отчетливо выраженное смещение ее пиков, что свидетельствует об образовании твердых растворов. Параметр кубической элементарной ячейки для полученного сплава Cu0.8–Ni0.2 составляет 3.6162 ± ± 0.0007 Å. Следует также отметить, что рефлексы металлов несколько уже, чем для оксидных носителей, что свидетельствует о большем размере частиц металлов по сравнению с частицами носителя. Величина ОКР для них составляет около 20 нм, что примерно в 2 раза превосходит размер ОКР для частиц носителя.
Активность катализаторов в реакции ПРМ. Согласно полученным данным, все исследованные материалы характеризуются высокой селективностью в целевой реакции получения водорода, которая для всех катализаторов даже при высоких температурах оказалась не менее 99.5%.
На рис. 4 приведены температурные зависимости выхода водорода и конверсии метилового спирта для полученных катализаторов. Минимальную каталитическую активность проявляли образцы, полученные на основе недопированного оксида циркония, и катализатор Cu–Ni/CeO2–SnO2. В работе [31] показано, что концентрация катионов Ce4+ и Ce3+ на поверхности катализатора во многом определяет степень каталитической активности композитов. При этом уменьшение количества катионов Ce3+ по сравнению с Ce4+ приводило к понижению конверсии спирта и выхода водорода. Вероятно, допирование оксида церия четырехвалентным оловом происходит в значительной степени на поверхности частиц и приводит к уменьшению концентрации ионов трехвалентного церия на поверхности, что и обусловливает низкую каталитическую активность полученного материала. Активность образца Cu–Ni/ZrO2–SnO2 также была невысока, что может указывать на низкую адсорбционную способностью оксида олова по отношению к воде. Однако, как и предполагалось, при тестировании образцов, допированных оловом, даже при высоких температурах диоксид углерода в продуктах реакции не был обнаружен в пределах погрешности хроматографического метода.
Рис. 4.
Температурные зависимости выхода H2 (а) и конверсии метилового спирта (б) для полученных катализаторов.
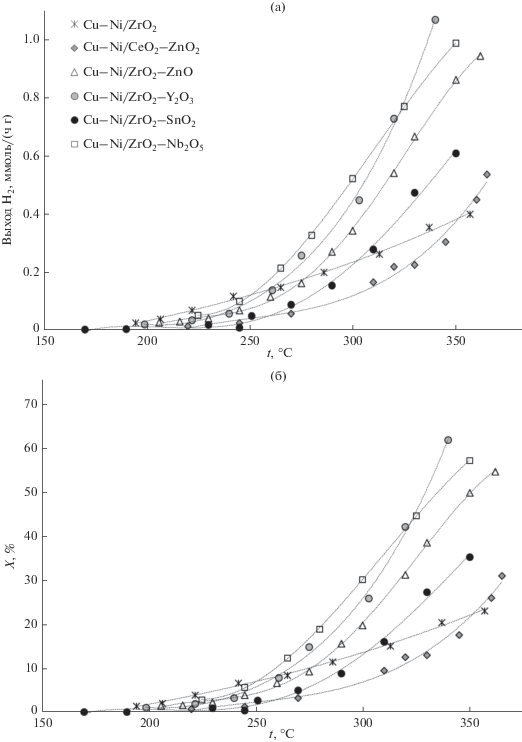
Максимальный выход водорода достигался при использовании образцов, допированных оксидом ниобия и иттрия. Как показано выше, материалы ZrO2–Y2O3 и ZrO2–Nb2O5 имеют кубическую и тетрагональную модификации соответственно. Это свидетельствует о более высокой активности катализатора, нанесенного на высокотемпературные модификации ZrO2. Введение ионов трехвалентного либо пятивалентного металла приводит к большей разупорядоченности и подвижности кислородной подрешетки в оксиде и к увеличению числа активных центров на поверхности катализатора, в роли которых, возможно, выступают структурные дефекты. Кроме того, как показано в табл. 1, удельная площадь поверхности носителя, содержащего оксид ниобия, значительно выше, что можно считать свидетельством более высокой активности катализатора, нанесенного на мелкодисперсный оксид.
ЗАКЛЮЧЕНИЕ
Сопоставляя полученные данные, можно отметить, что изменение состава и структуры оксидного носителя может влиять на активность сорбционных центров, склонность носителя к протеканию процессов переноса кислорода и/или протона, а также на возможность его участия в окислительно-восстановительных процессах. Введение гетеровалентных ионов во всех случаях приводило к повышению каталитической активности образцов по сравнению с недопированным оксидом циркония, вероятно, вследствие большей разупорядоченности и подвижности кислородной подрешетки в оксиде и к увеличению числа активных центров на поверхности катализатора, в роли которых, возможно, выступают структурные дефекты.
Повышение выхода водорода в процессе ПРМ для Cu–Ni-катализаторов наблюдается при повышении симметрии кристаллической решетки оксидного носителя. Показан рост каталитической активности в ряду: Cu–Ni/ZrO2 (монокл.) < < Cu–Ni/ZrO2–SnO2 (монокл.) < Cu–Ni/ZrO2–ZnO (монокл.) < Cu–Ni/ZrO2–Nb2O5 (тетр.) ≈ ≈ Cu–Ni/ZrO2–Y2O3 (куб.).
Список литературы
Yaroslavtsev A.B., Stenina I.A., Kulova T.L., Skundin A.M., Desyatov A.V. Nanomaterials for Electrical Energy Storage // Comprehensive Nanoscience and Nanotechnology. Second edition / Eds. Andrews D.L. et al. Amsterdam: Elsevier. Academic Press, 2019. P. 165–206.
Shafiei E., Davidsdottir B., Leaver J., Stefansson H., Asgeirsson E.I. Energy, Economic, and Mitigation Cost Implications of Transition Toward a Carbon-Neutral Transport Sector: A Simulation-Based Comparison between Hydrogen and Electricity // J. Clean Prod. 2017. V. 141. P. 237–247.
Moliner R., Lazaro M.J., Suelves I. Analysis of the Strategies for Bridging the Gap towards the Hydrogen Economy // Int. J. Hydrogen Energy. 2016. V. 41. P. 19500–19508.
Abe J.O., Popoola A.P.I., Ajenifuja E., Popoola O.M. Hydrogen Energy, Economy and Storage: Review and Recommendation // Int. J. Hydrogen Energy. 2019. V. 44. P. 15072–15086.
Naruki E., Shimoda E., Goshome K., Yamane T., Nozu T., Maeda T. Construction and Operation of Hydrogen Energy Utilization System for a Zero Emission Building // Int. J. Hydrogen Energy. 2019. V. 44. P. 14596–14604.
Miranda P.E. Hydrogen Energy // Sustainable and Perennial Science and Engineering of Hydrogen-Based Energy Technologies / Ed. Miranda P.E. Amsterdam: Academ. Press, 2019. Chap. 1. P. 1–38.
Frusteri F., Bonura G. Hydrogen production by reforming of bio-alcohols // Compendium of Hydrogen Energy. Hydrogen Production and Purification / Eds. Subramani V. et al. Woodhead Publishing Series in Energy, 2015. 550 p.
Ghasemzadeh K., Jalilnejad E., Mohamad S., Tilebon S. Hydrogen Production Technologies From Ethanol // Ethanol / Eds. Basile A. et al. Amsterdam: Elsevier, 2019. Chap. 12. P. 307–340.
López-Tenllado F.J., Hidalgo-Carrillo J., Montes-Jiménez V., Sánchez-López E., Urbano F.J., Marinas A. Photocatalytic Production of Hydrogen from Binary Mixtures of C-3 Alcohols on Pt/TiO2: Influence of Alcohol Structure // Catal. Today. 2019. V. 328. P. 2–7.
Li Sh., Zheng H., Zheng Y., Tian J., Jing T., Chang Jo-Sh., Ho Sh.H. Recent Advances in Hydrogen Production by Thermo-Catalytic Conversion of Biomass // Int. J. Hydrogen Energy. 2019. V. 44. P. 14266–14278.
Chiu Y.J., Chiu H.C., Hsieh R.H., Jang J.H., Jiang B.Y. Simulations of Hydrogen Production by Methanol Steam Reforming // Energy Procedia. 2019. V. 156. P. 38–42.
Lytkina A.A., Orekhova N.V., Yaroslavtsev A.B. Catalysts for the Steam Reforming and Electrochemical Oxidation of Methanol. A Review // Inorg. Mater. 2018. V. 54. P. 1301–1315.
Kim D.H., Kim J.H., Jang Y.S., Kim J.C. Hydrogen Production by Oxidative Steam Reforming of Methanol over Anodic Aluminum Oxide-Supported Cu–Zn Catalyst // Int. J. Hydrogen Energy. 2019. V. 44. P. 9873–9882.
Tahay P., Khani Y., Jabari M., Bahadoran F., Safari N. Highly Porous Monolith/TiO2 Supported Cu, Cu–Ni, Ru, and Pt Catalysts in Methanol Steam Reforming Process for H2 Generation // Appl. Catal. A: General. 2018. V. 554. P. 44–53.
Khzouz M., Gkanas E.I., Du S., Wood J. Catalytic Performance of Ni–Cu/Al2O3 for Effective Syngas Production by Methanol Steam Reforming // Fuel. 2018. V. 232. P. 672–683.
Kuo M.T., Chen Y.Y., Hung W.Y., Lin S.F., Lin H.P., Hsu C.H., Shih H.Y., Xie W.A., Li S.N. Synthesis of Mesoporous CuFe/Silicates Catalyst for Methanol Steam Reforming // Int. J. Hydrogen Energy. 2019. V. 44. P. 14416–14423.
Sa S., Silva H., Brandao L., Sousa J.M., Mendes A. Catalysts for Methanol Steam Reforming–a Review // Appl. Catal.: B. 2010. V. 99. P. 43–57.
Azenha C.S.R., Mateos-Pedrero C., Queirós S., Concepción P., Mendes A. Innovative ZrO2-Supported CuPd Catalysts for the Selective Production of Hydrogen from Methanol Steam Reforming // Appl. Catal.: B. 2017. V. 203. P. 400–404.
Sarafraz M.M., Safaei M.R., Goodarzi M., Ajomandi M. Reforming of Methanol with Steam in a Micro-Reactor with Cu–SiO2 Porous Catalyst // Int. J. Hydrogen Energy. 2019. In press. https://doi.org/10.1016/j.ijhydene.2019.05.215
Hwang B.Y., Sakthinathan S., Chiu T.W. Production of Hydrogen from Steam Reforming of Methanol Carried out by Self-Combusted CuCr1 – xFexO2 (x = 0–1) Nanopowders Catalyst // Int. J. Hydrogen Energy. 2019. V. 44. P. 2848–2856.
Thyssen V.V., Sartore D.M., Assaf E.M. Effect of Preparation Method on the Performance of Ni/MgOSiO2 Catalysts for Glycerol Steam Reforming // J. Energy Institute. 2019. V. 92. P. 947–958.
Liu X., Men Y., Wang J., He R., Wang Y. Remarkable Support Effect on the Reactivity of Pt/In2O3/MOx Catalysts for Methanol Steam Reforming // J. Power Sources. 2017. V. 364. P. 341–350.
Wang S., Niu H., Guo M., Wang J., Chen T., Wang G. Effect of Zirconia Polymorph on the Synthesis of Diphenyl Carbonate over Supported Lead Catalysts // Mol. Catal. 2019. V. 468. P. 117–124.
Lytkina A.A., Zhilyaeva N.A., Ermilova M.M., Orekhova N.V., Yaroslavtsev A.B. Influence of the Support Structure and Composition of Ni–Cu-Based Catalysts on Hydrogen Production by Methanol Steam Reforming // Int. J. Hydrogen Energy. 2015. V. 40. P. 9677–9684.
Liu X., Toyir J., Piscina P.R., Homs N. Hydrogen Production from Methanol Steam Reforming over Al2O3- and ZrO2-Modified CuOZnOGa2O3 Catalysts // Int. J. Hydrogen Energy. 2017. V. 42. P. 13704–13711.
Guangwei X., Laitao L., Changquan L., Xiaomao Y. Synthesis of Mesoporous ZnO (m-ZnO) and Catalytic Performance of the Pd/m-ZnO Catalyst for Methanol Steam Reforming // Energy Fuels. 2009. V. 23. P. 1342–1346.
Sanches S.G., Huertas Flores J., Pais da Silva M.I. Cu/ZnO and Cu/ZnO/ZrO2 Catalysts Used for Methanol Steam Reforming // Mol. Catal. 2018. V. 454. P. 55–62.
Стенина И.А., Воропаева Е.Ю., Бруева Т.Р., Синельников А.А., Дроздова Н.А., Иевлев В.М., Ярославцев А.Б. Эволюция морфологии и микроструктуры в ходе термообработки гидратированного оксида циркония, полученного из хлоридных растворов // Журн. неорган. химии. 2008. Т. 53. № 6. С. 912–918.
Borik M.A., Volkova T.V., Kuritsyna I.E., Lomonova E.E., Myzina V.A., Ryabochkina P.A., Tabachkova N.Yu. Features of the Local Structure and Transport Properties of ZrO2–Y2O3–Eu2O3 Solid Solutions // J. Alloys Comp. 2019. V. 770. P. 320–326.
Shukla V., Balani K., Subramaniam A., Omar S. Phase Stability and Conductivity in the Pseudo Ternary System of xYb2O3 – (12 – x)Sc2O3–88ZrO2 (0 ≤ x ≤ 5) // Solid State Ionics. 2019. V. 332. P. 93–101.
Lytkina A.A., Orekhova N.V., Ermilova M.M., Yaroslavtsev A.B. The Influence of the Support Composition and Structure (MxZr1 – xO2 –d) of Bimetallic Catalysts on the Activity in Methanol Steam Reforming // Int. J. Hydrogen Energy. 2018. V. 43. P. 198–207.
Trovarelli A. Catalysis by Ceria and Related Materials. London: Imperial College Press, 2002. P. 508.
Zhao Q., Lorenz H., Turner S., Lebedev O.I., Tendeloo G.V., Rameshan C., Klotzer B., Konzett J., Penner S. Catalytic Characterization of Pure SnO2 and GeO2 in Methanol Steam Reforming // Appl. Catal. A: General. 2010. V. 375. P. 188–195.
Guarido C.E.M., Cesar D.V., Souza M.M.V.M., Schmal M. Ethanol Reforming and Partial Oxidation with Cu/Nb2O5 Catalyst // Catalysis Today. 2009. V. 142. P. 252–257.
Dancini-Pontes I., De Souza M., Silva F.A., Scalia-nte M.H.N.O., Alonso C.G., Bianchi G.S., Neto A.M., Pereira G.M., Fernandes-Machado N.R.C. Influence of the CeO2 and Nb2O5 Supports and the Inert Gas in Ethanol Steam Reforming for H2 Production // Chem. Eng. J. 2015. V. 273. P. 66–74.
Bejugama S., Pandey A.K. Effect of Nb2O5 on Sintering and Mechanical Properties of Ceria Stabilized Zirconia // J. Alloys Compd. 2018. V. 765. P. 1049–1054.
Cai F., Lu P., Ibrahim J.J., Fu Y., Zhang J., Sun Y. Investigation of the role of Nb on Pd–Zr–Zn Catalyst in Methanol Steam Reforming for Hydrogen Production // Int. Hydrogen Energy. 2019. V. 44. P. 11717–11733.
Стенина И.А., Воропаева Е.Ю., Вересов А.Г., Капустин Г.И., Ярославцев А.Б. Влияние величины pH осаждения и термообработки на свойства гидратированного оксида циркония // Журн. неорган. химии. 2008. Т. 53. № 3. С. 397–403.
Дополнительные материалы отсутствуют.
Инструменты
Неорганические материалы