Неорганические материалы, 2019, T. 55, № 3, стр. 304-310
Структурообразование в системе SiO2–Na2O–H2O при синтезе пеностеклокерамики экструзионным методом
К. С. Иванов *
Институт криосферы Земли Тюменского научного центра СО Российской академии наук
625000 Тюмень, ул. Малыгина, 86, а/я 1230, Россия
* E-mail: sillicium@bk.ru
Поступила в редакцию 04.04.2018
После доработки 15.10.2018
Принята к публикации 24.09.2018
Аннотация
Рассмотрен метод синтеза неорганического теплоизоляционного материала – пеностеклокерамики – путем экструзии смеси опал-кристобалитовой породы и раствора гидроксида натрия через калиброванные отверстия. Метод позволяет достичь высокой гомогенизации смеси, а также совместить операции смешивания компонентов и грануляции смеси. Происходит интенсификация взаимодействия аморфных фаз опал-кристобалитовой породы с гидроксидом натрия в системе SiO2–Na2O–H2O, в связи с чем средняя плотность материала снижается в 1.5 раза. В результате достигается экономический эффект за счет пропорционального снижения содержания в материале дорогостоящего гидроксида натрия. С помощью электронной микроскопии установлено влияние температуры на структурообразование материала. Процесс поризации смеси начинается с 200 и до 500°С сопровождается образованием разрыхленной структуры в виде неоднородной сетки. Диапазон 400–500°С является переходным, после 600°С начинает формироваться ячеистая структура, в результате чего при 850°С синтезируется материал со средней плотностью 0.38–0.57 г/см3 и прочностью при сжатии 3.1–5.9 МПа.
ВВЕДЕНИЕ
Жидкие стекла широко применяются при получении неорганических теплоизоляционных материалов, являясь их основным структурообразующим компонентом [1]. В этой связи важную роль играют вопросы удешевления жидкого стекла как сырьевого компонента материалов. Существенно упростить процесс получения жидких стекол позволяет их гидротермальный синтез на основе опал-кристобалитовых пород (ОКП), к которым относятся диатомиты, трепелы и опоки. Высокое содержание аморфных фаз кремнезема способствует растворению ОКП в щелочах [2], однако сопутствующие примеси в виде глинистых минералов, кварца и органики приводят к образованию темно-бурых суспензий – жидких стекол с нерастворимым остатком. Несмотря на это, существуют направления прямого применения жидких стекол с нерастворимым остатком (в виде суспензий), например, при получении материалов щелочной активации [3], силикат-натриевых связующих [4] и т.п.
Процесс растворения ОКП в щелочах лежит в основе синтеза неорганического теплоизоляционного материала – пеностеклокерамики (ПСК). Порода и раствор щелочи смешиваются с образованием гидратированных щелочных силикатов, после чего смесь нагревается и вспенивается при температуре 700–900°С [5–8]. Вспенивание смеси происходит при физико-химическом взаимодействии в системе SiO2–Na2O–H2O за счет перехода гидратированных щелочных силикатов в пиропластическое состояние, их дегидратации и последующей поликонденсации кремнекислородных анионов. В результате формируется силикатная “пена”, которая содержит как стекловидную фазу, так и вносимую с нерастворимым остатком ОКП кристаллическую фазу. Таким образом, возникает возможность прямого синтеза неорганического теплоизоляционного материала без применения коммерческого жидкого стекла, что экономически более оправдано.
ПСК является аналогом классического пеностекла, которое получают из стеклобоя. Пеностекло сочетает в себе легкость, высокую прочность и изолирующую способность (теплопроводность 0.045–0.07 Вт/(м К)). Негорючесть, высокая химическая стойкость, низкое водопоглощение благодаря закрытопористой структуре и неограниченный срок службы пеностекла (в отличие от органических и волокнистых утеплителей) делают его одним из самых прогрессивных теплоизоляционных материалов [9].
К преимуществам ПСК можно отнести наличие широко распространенной сырьевой базы ОКП, а также возможность получения гранул размером 0.1–0.5 мм. Насыпная плотность порошков из таких гранул может составлять 0.2–0.4 г/см3, что делает их особо востребованными в создании облегченных композиционных материалов, высокопрочных бетонов и т.п.
К недостаткам ПСК можно отнести необходимость применения дорогостоящего гидроксида натрия, поэтому снижение его содержания при сохранении функциональных свойств ПСК является актуальной научно-технической проблемой. Отсутствие единой технологии ПСК является сдерживающим фактором в реализации промышленного производства. Например, в аналогичных исследованиях по получению композиций из ОКП и гидроксида натрия [5, 6] авторы не приводят методологию смешивания ОКП со щелочью, хотя эта процедура является сложным физико-химическим процессом, требующим определенного описания.
С одной стороны, смешивание ОКП с раствором NaOH должно сопровождаться химическим взаимодействием этих компонентов с образованием гидратированных силикатов натрия, с другой – процесс смешивания существенно затруднен тем, что ОКП обладают высокой адсорбционной способностью. Следовательно, полнота протекания реакции образования гидратированных силикатов натрия, которая будет влиять на свойства ПСК, может существенно зависеть от параметров смешивания компонентов, т.е. способа смешивания, интенсивности механического воздействия и т.п. В литературе также недостаточно исследованы и освещены вопросы структурообразования материала, что необходимо для понимания особенностей технологии [7, 8].
Цель работы заключалась в исследовании влияния интенсивности механического воздействия при смешивании компонентов на образование гидратированных силикатов натрия, структуру и основные свойства ПСК.
ЭКСПЕРИМЕНТАЛЬНАЯ ЧАСТЬ
Применялась ОКП в виде диатомита Ирбитского месторождения Свердловской области следующего химического состава (мас. %): SiO2 – 76.7, CaO – 0.4, MgO – 0.9, Al2O3 – 7.3, Fe2O3 – 2.4, TiO2 – 0.6, Na2O – 0.4, K2O – 0.8, SO3 – 0.7; потери при прокаливании 9.8. Диатомит высушивался до постоянной массы при 100°C и измельчался в порошок до полного прохода через сито с размером ячейки 0.16 мм. Строение материалов исследовали с применением сканирующего электронного микроскопа Jeol JSM-6510A (Япония). Фазовый состав изучали с помощью дифрактометра ДРОН-6 (Россия): длина волны 0.179 нм, CoKα-излучение, Fe-фильтр.
Результаты сканирующей электронной микроскопии (СЭМ) свидетельствуют о том, что диатомит сложен в основном из обломков панцирей диатомей – ископаемых водорослей, состоящих из аморфного кремнезема (рис. 1). О высоком содержании в диатомите аморфной фазы в виде опала свидетельствует рефлекс на дифрактограмме в диапазоне углов 18°–26° (рис. 2, дифрактограмма 1). Идентификация кристаллических фаз диатомита проводилась с применением базы данных American Mineralogist Crystal Structure Database. На дифрактограмме 1 (рис. 2) отмечаются пики, характерные для таких минералов, как: кварц (при углах 20.87°, 26.65°, 36.56°, 39.49°, 40.41°, 50.17°), монтмориллонит (19.60°, 34.67°), иллит (имеет пики, схожие с монтмориллонитом), полевошпатный минерал альбит (21.69° и 27.84°).
Рис. 2.
Дифрактограммы: 1 – исходный диатомит; 2 и 3 – экструдированная смесь после выдержки при 100 и 800°С соответственно.
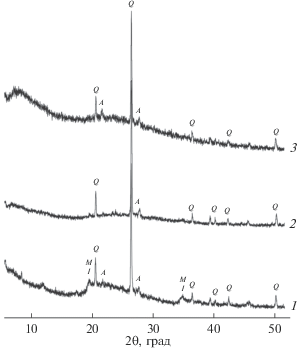
На рис. 3а представлены кривые термического анализа диатомита. Эндотермические эффекты на ДСК-кривой в диапазоне 70–200°С и при 490°С соответствуют удалению воды из глинистой составляющей диатомита, что подтверждается соответствующими максимумами изменения скорости потери массы образца на ДТГ-кривой. Экзотермический эффект при 350°С может объясняться выгоранием органических примесей. Эндотермический эффект на ДСК-кривой при 870°С, не связанный с изменением массы образца, характеризует разрушение кристаллических решеток монтмориллонита и иллита в результате их дегидратации, что подтверждается данными Грима и Роуланда, проводившими термический анализ этих минералов [10]. Таким образом, основными фазами диатомита являются: опал в виде растворимых в щелочи панцирей диатомовых водорослей, кварц и глинистые минералы. Идентифицированные фазы находятся в соответствии с химическим составом диатомита.
Получение образцов ПСК состояло в первичном смешивании диатомита с раствором NaOH, имеющим концентрацию 40 мас. %, в стальной сферической чаше до образования пресс-порошка. Массовое соотношение между диатомитом и сухим NaOH было принято равным 9.1. Теоретически это дает молярное соотношение между растворимым кремнеземом диатомита и щелочью (в пересчете на Na2O), равное 5. У традиционных жидких стекол данное соотношение, называемое силикатным модулем, составляет 3–4. Более низкое соотношение (при выбранном методе получения материала) не оправдано экономически, а более высокое соотношение приводит к низкой кратности вспенивания смеси, в результате чего ухудшаются теплоизоляционные свойства ПСК. Для сравнения, в исследованиях [6, 7] массовое соотношение между диатомитом и сухим NaOH принималось равным 5 и 4 соответственно, т.е. смесь содержала почти вдвое большее количество NaOH.
Для последующего смешивания компонентов и оценки влияния механических воздействий на свойства ПСК использовался экструзионный метод, суть которого в одновременном перемешивании компонентов и продавливании смеси через калиброванные отверстия с помощью шнека. К основным преимуществом метода относятся:
возможность оказания многократного механического воздействия на смесь путем ее возврата и повторной экструзии;
процессы смешивания компонентов и грануляции смеси объединяются в одной операции;
грануляция происходит при сравнительно низком содержании воды в смеси компонентов, что существенно упрощает дальнейшую сушку.
Лабораторный экструдер имел следующие параметры: диаметр шнека 80 мм, число витков шнека 5, шаг витка 80 мм, число оборотов шнека 45 мин–1, номинальный крутящий момент привода 490 Н м, диаметр отверстий в гранулирующей решетке – 5 мм. Последний параметр задает диаметр гранул на выходе из экструдера и является наиболее оптимальным при заданных параметрах экструдера. Под воздействием шнека пресс-порошок получает дополнительное перемешивание и, уплотняясь, превращается в туго пластичную смесь, которая продавливается сквозь отверстия гранулирующей решетки и принимает вид отдельных гранул диаметром и длиной 5 мм. Средняя плотность гранулы составляла 1.65 г/см3, весовая влажность 17% (при температуре сушки 100°С).
Пресс-порошок заданного состава подвергался 1-, 2-, либо 3-кратной экструзии (т.е. в двух последних случаях смесь повторно возвращалась в экструдер после прохождения через гранулирующую решетку). В зависимости от кратности экструзии образцы имели маркировку соответственно E1, E2 и E3. Повышение кратности экструзии свыше трех нецелесообразно по причине резкого снижения пластичности смеси из-за высоких адсорбционных свойств диатомита, что вызывает перегрев и аварийную остановку оборудования. Гранулированная смесь высушивалась при 80°С, измельчалась до фракции 1–2.5 мм, после чего засыпалась в формы из жаростойкой стали и подвергалась обжигу в муфельной печи при 850°С в течение 20 мин. При обжиге отдельные зерна смеси размягчались и спекались между собой, образуя единую структуру. Охлаждение форм происходило вместе с печью, после чего из полученного материала выпиливались образцы в виде кубов с длиной ребра 30 мм.
Влияние кратности экструзии смеси оценивалось по следующим параметрам: силикатный модуль экструдированной смеси, средняя плотность образцов, пористость структуры и прочность образцов при сжатии. От средней плотности образцов напрямую зависит расход NaOH на единицу объема материала. Кроме того, средняя плотность в основном определяет значение теплопроводности как основной характеристики теплоизоляционного материала.
При одинаковом начальном содержании Na2O в смесях силикатный модуль характеризует степень извлечения SiO2 при механической обработке смеси в экструдере, т.е. количество SiO2 в растворенном состоянии. Значение силикатного модуля определялось с помощью методики [11]. Навеска смеси, высушенная до постоянной массы, измельчалась в порошок до полного прохода через сито с размером ячейки 0.1 мм. Затем навеска подвергалась кипячению в воде (в пикнометре на водяной бане) при температуре 98°С в течение часа. Полученный раствор анализировался на содержание Na2O и SiO2 аналогично традиционным жидким стеклам.
РЕЗУЛЬТАТЫ И ОБСУЖДЕНИЕ
Исследование физико-химических процессов, происходящих при обжиге ПСК, проводилось с помощью термического анализа (рис. 3б). Для ДТГ- и ДСК-кривых нагревания смеси диатомита и раствора NaOH характерно наличие эндотермических эффектов в виде острого пика при 100°С и более растянутого эффекта (в отличие от ДТГ- и ДСК-кривых для образца диатомита на рис. 3а) в интервале 350–600°С. В соответствии с кривой ТГ, второй эффект сопровождается почти половиной от суммарных потерь массы образцом, что, наиболее вероятно, связано с дегидратацией силикатов натрия. Интересно отметить, что последний незначительный эндотермический эффект на ДСК-кривой при 760°С на рис. 3б, возможно, связан с плавлением кристаллической фазы Na6Si8O19. Возникновение данной фазы диагностировано Рагваном и соавтором с помощью рентгенофазового и термического анализов коммерческого жидкого стекла при нагревании до 750°С с последующим разложением Na6Si8O19 при 800°С и образованием расплава [12].
Рентгенофазовый анализ смеси проводился с интервалом 100°С. В сравнении с дифракционной картиной диатомита (рис. 2, дифрактограмма 1) нагрев смеси не приводит к существенным изменениям ее кристаллической составляющей. После сушки смеси при 100°С (рис. 2, дифрактограмма 2) отмечается исчезновение аморфного гало в диапазоне углов 18°–26°, что характерно для растворения аморфной составляющей диатомита в растворе NaOH. Для дифрактограммы 2 характерно исчезновение пиков монтмориллонита и иллита, которые под воздействием NaOH могут превращаться в искусственные цеолиты [13]. Нагревание смеси до 800°С сопровождается образованием аморфного гало (рис. 2, дифрактограмма 3, 2θ = 8°–13°), характеризующего наличие стеклофазы, что согласуется с данными термического анализа (рис. 3б) и других авторов, проводивших рентгенофазовый анализ жидкого стекла после нагрева до 800°С [12].
Структурные изменения в гранулированной смеси исследовались с помощью СЭМ по мере нагревания через каждые 100°С. На рис. 4а и 4б представлена структура смеси после нагревания до 200°С. На изображениях отсутствуют следы обломков панцирей диатомей, наблюдавшиеся на рис. 1. При более сильном увеличении (рис. 4б) на поверхности диагностируются новообразования округлой формы размером примерно 1 мкм. Увеличение температуры до 400°С приводит к образованию пор, на рис. 4в и 4г (в центре изображений) отмечаются включения непрореагировавших с NaOH обломков панцирей диатомей. Кристаллы игольчатой формы на рис. 4г относятся к карбонизированным производным NaOH, часть которого не вступила во взаимодействие с SiO2. Аналогичные образования наблюдались в работе [5].
Рис. 4.
СЭМ-фотографии образцов ПСК: а и б – 200°С (а ×1000, б ×5000); в и г – 400°С (в ×1000, г ×2000); д и е – 600°С (д ×1000, е ×3000); ж – 800°С (×1000).
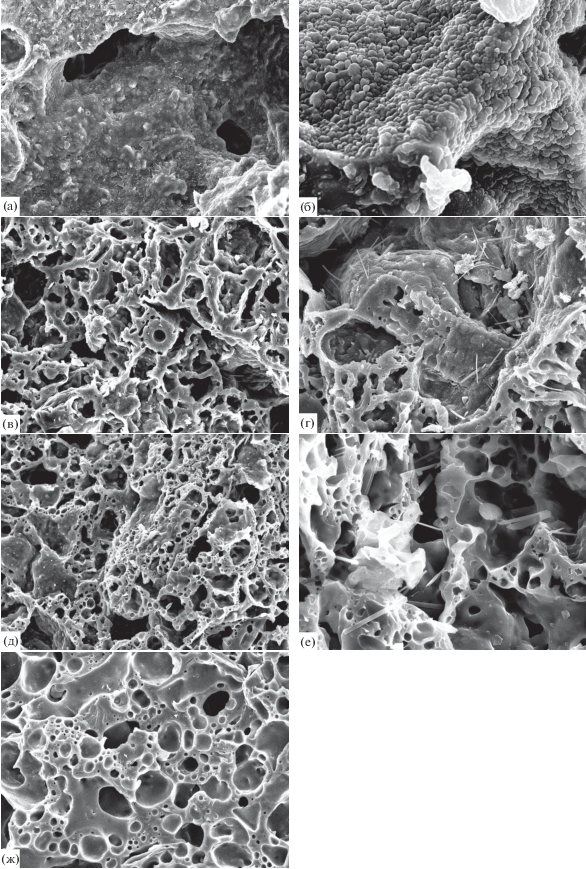
Дальнейшие изменения структуры отмечаются при 600°С. На рис. 4д и 4е видна неупорядоченная ячеистая структура в виде как отдельно взятых, так и сообщающихся пор диаметром примерно 1 мкм. По-видимому, при температуре, близкой к 600°С, смесь переходит в пиропластическое состояние. Образование стеклофазы при 800°С сопровождается формированием более упорядоченной структуры, на рис. 4ж диаметр пор колеблется от 1 до 15 мкм. Обжиг при 850°С приводит к увеличению размера пор от 0.1 до 1 мм. Излом пеностеклокерамики обладает характерным стеклянным блеском. При температурах 800 и 850°С на снимках СЭМ не диагностируются следы панцирей диатомей и кристаллических производных NaOH в связи с их растворением в силикатном расплаве. Увеличение температуры обжига до 900°С приводит к увеличению средней плотности образцов за счет усадки и уплотнения пены, в связи с чем температуру обжига 850°С следует считать оптимальной.
Результаты влияния кратности экструзии смеси на среднюю плотность образцов представлены на рис. 5 в виде диаграммы. В ряду E1–E2–E3 происходит увеличение интенсивности воздействия на смесь. В результате наблюдается снижение средней плотности образцов, которая составляет соответственно 0.57, 0.42 и 0.38 г/см3 (рис. 5, кривая 1). Таким образом, в сравнении с E1 у образцов E2 и E3 средняя плотность снижается соответственно в 1.36 и 1.5 раза. Следовательно, наибольший эффект в плане снижения содержания NaOH в материале дает 3-кратная экструзия смеси (E3). В случае E1, при принятом массовом соотношении между диатомитом и сухим NaOH, его расход на 1 л материала составит 64 г, а в случаях E2 и E3 – 47 и 44 г соответственно, таким образом; расход NaOH снижается пропорционально средней плотности образцов.
Рис. 5.
Диаграмма, иллюстрирующая влияние кратности экструзии на среднюю плотность и силикатный модуль: 1 – кривая изменения средней плотности, 2 – кривая изменения прочности при сжатии.
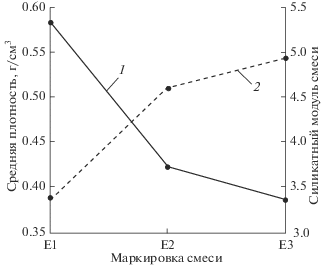
Кривая 2 на рис. 5 характеризует увеличение силикатного модуля смеси с 3.3 до 4.1 и 4.9 в результате возрастания кратности экструзии в ряду E1–E2–E3, что является основной причиной снижения средней плотности образцов. В случае E3 значение силикатного модуля (4.9) близко к 5, что говорит о практически полном извлечении из диатомита растворимого SiO2 за счет механического воздействия на смесь в виде 3-кратной экструзии. На СЭМ-снимках наблюдается значительно меньшее количество непрореагировавших останков панцирей диатомей. Возрастание силикатного модуля говорит о формировании в смеси большего количества гидратированных щелочных силикатов, которые, с одной стороны, являются источником образования расплава, а с другой – порообразователями за счет их дегидратации при обжиге. Кроме того, ввиду существования известных способов гидротермального синтеза искусственных цеолитов из глин и щелочей [12], вполне вероятно их образование также и в рассматриваемой системе. Искусственные цеолиты могут являться источником порообразования, т.к. способны постепенно дегидратироваться при нагревании и снижать среднюю плотность материала. Однако это лишь теоретическое предположение, т.к. на дифрактограмме 2 (рис. 2) отсутствуют следы новообразований в виде цеолитов.
Возрастание кратности экструзии в ряду E1–E2–E3 приводит к закономерному снижению прочности образцов при сжатии в связи со снижением их средней плотности (рис. 5, кривая 1). Прочность при сжатии образцов E1, E2 и E3 (рис. 5, кривая 2) составляет 5.9, 3.8 и 3.1 МПа соответственно. Значения средней плотности и прочности образцов можно сравнить с результатами других авторов, синтезировавших ПСК со средней плотностью 0.20–0.22 г/см3, прочностью при сжатии 2.0–2.3 МПа и массовым соотношением между диатомитом и сухим NaOH, равным 4 [7]. Наиболее близкие значения средней плотности и прочности при сжатии имеют образцы E3 (соответственно 0.38 г/см3 и 3.1 МПа), однако расход NaOH на 1 л ПСК в этом случае составляет 44 против 55 г, т.е. ниже на 20%.
ЗАКЛЮЧЕНИЕ
Формирование пористой структуры ПСК происходит в 2 этапа: в интервале 400–500°С наблюдается неупорядоченная поризованная масса с рыхлой поверхностью, которая при дальнейшем нагревании от 600 до 850°С непрерывно видоизменяется и упорядочивается, превращаясь в ячеистую структуру с преобладанием замкнутых пор.
Кратность экструзии смеси из диатомита и раствора NaOH оказывает существенное влияние на среднюю плотность образцов ПСК, которая снижается в 1.5 раза при увеличении кратности с 1 до 3. Благодаря этому достигается экономический эффект, выраженный в пропорциональном снижении расхода NaOH на единицу объема ПСК.
Увеличение кратности экструзии приводит к росту силикатного модуля в системе SiO2–Na2O–H2O вследствие дополнительного растворения кремнезема диатомита, что способствует росту кратности вспенивания образцов и снижению средней плотности материала.
Список литературы
Нажарова Л.Н., Гнусина Т.С., Губайдуллина А.М., Филиппович Е.Н. Ирбитские диатомиты как потенциальное сырье для синтеза растворимых силикатов // Вестн. Казанского технологического ун-та. 2013. № 21. С. 49–51.
Малявский Н.И. Щелочносиликатные утеплители. Свойства и химические основы производства // Рос. хим. журн. 2003. Т. XLVIV. № 4. С. 39–45.
Иванов К.С., Коротков Е.А. Исследование влияния силикат-натриевых суспензий на свойства материалов щелочной активации // Неорган. материалы. 2017. Т. 53. № 9. С. 993–1000.
Иващенко Ю.Г., Страхов А.В. Свойства силикатнатриевого связующего, полученного на основе силицитовых пород методом гидротермального синтеза // Вестн. Саратовского ГТУ. 2010. Т. 4. № 1(49). С. 193–200.
Казанцева Л.К., Железнов Д.В., Сереткин Ю.В., Ращенко С.В. Формирование источника порообразующего газа при увлажнении природных алюмосиликатов раствором NaOH // Стекло и керамика. 2012. № 10. С. 37–42.
Сеник Н.А., Мешков А.В., Виницкий А.Л., Вакалова Т.В., Верещагин В.И. Получение высокоэффективного теплоизоляционного материала на основе диатомита путем низкотемпературного вспенивания // Техника и технология силикатов. 2012. Т. 19. № 4. С. 6–12.
Kazantseva L.K., Rashchenko S.V. Chemical Processes during Energy-Saving Preparation of Lightweight Ceramics // J. Am. Ceram. Soc. 2014. V. 97. P. 1743–1749. doi 10.1111/jace.12980
Иванов К.С., Радаев С.С., Селезнева О.И. Диатомиты в технологии гранулированного пеностекла // Стекло и керамика. 2014. № 5. С. 15–19.
Минько Н.И., Пучка О.В., Евтушенко Е.И., Нарцев В.М., Сергеев С.В. Пеностекло – современный эффективный неорганический теплоизоляционный материал // Фундаментальные исследования. 2013. № 6. С. 849–854.
Grim R.E., Rowland R.A. Differential Thermal Analysis of Clay Minerals and Other Hydrous Materials. Part 1 // Am. Mineral. 1942. V. 27. №. 11. P. 746–761.
Соколович В.Е. К экспресс-методу определения модуля раствора силиката натрия // Стекло и керамика. 1975. № 10. С. 36.
Raghvan S., Helfried N. Phase Evolution on Heat Treatment of Sodium Silicate Water Glass // J. Non-Cryst. Solids. 2008. V. 354. P. 896–900. doi 10.1016/j.jnoncrysol.2007.08.037
Breck D.W. Zeolite Molecular Sieves: Structure, Chemistry and Use. N.Y.: Wiley, 1973. 771 p.
Дополнительные материалы отсутствуют.
Инструменты
Неорганические материалы