Неорганические материалы, 2020, T. 56, № 3, стр. 343-347
Коррозионная стойкость и износостойкость покрытий, полученных методом вневакуумной электронно-лучевой наплавки тугоплавких карбидов на низкоуглеродистую сталь
Т. А. Крылова 1, *, К. В. Иванов 1, Ю. А. Чумаков 1, Р. В. Троценко 2
1 Институт физики прочности и материаловедения СО Российской академии наук
634055 Томск, пр. Академический, 2/4, Россия
2 Национальный исследовательский Томский политехнический университет
634050 Томск, пр. Ленина, 30, Россия
* E-mail: kta@ispms.tsc.ru
Поступила в редакцию 23.04.2019
После доработки 23.09.2019
Принята к публикации 26.09.2019
Аннотация
Методом вневакуумной электронно-лучевой наплавки порошковой смеси Cr3C2 + TiC сформированы покрытия в широком интервале режимов обработки на низкоуглеродистой стали. Проведены испытания на коррозионную стойкость и износостойкость полученных покрытий и образцов сравнения. Показано, что максимальной коррозионной стойкостью обладает покрытие при поверхностной плотности введенной энергии W = 8.8 кДж/см2, что связано с увеличением концентрации хрома в наплавленном слое до 16%. Установлено, что на износостойкость покрытий влияют количество и размер частиц титана. Наилучшей износостойкостью обладает покрытие при W = 10.0 кДж/см2.
ВВЕДЕНИЕ
Экономической тенденцией современного этапа развития технологий является вытеснение импортных дорогостоящих износостойких, кислотоупорных, нержавеющих сталей путем замены их на низкоуглеродистые стали, имеющие защитные покрытия. Как известно, коррозионное и механическое разрушение деталей оборудования, конструкций и инструментов начинается с поверхности, поэтому именно к поверхностному слою предъявляют повышенные эксплуатационные требования.
Одним из эффективных способов получения защитных покрытий на поверхности конструкционных материалов является метод электронно-лучевой наплавки при использовании пучка релятивистских электронов, выведенного в атмосферу [1–3]. Данная технология дает возможность в широких пределах изменять химический и фазовый состав покрытия за счет использования практически любых тугоплавких соединений.
Выполненные ранее работы по повышению коррозионной стойкости и износостойкости позволили значительно расширить технологические возможности получения наплавленных покрытий на низкоуглеродистых сталях. Так, в работе [4] показано, что при наплавке порошка Cr3C2 на низкоуглеродистую сталь формируются покрытия с повышенными значениями твердости и коррозионной стойкости по сравнению с материалом подложки Ст3. Покрытия при поверхностной плотности введенной энергии W = 8.5–9.5 кДж/см2 с содержанием хрома выше 12–14% обладают коррозионной стойкостью, близкой к стойкости нержавеющей стали 12Х18Н10Т. Как известно, на коррозионную стойкость главным образом оказывает влияние наличие хрома. Увеличение содержания хрома с 13 до 17% существенно усиливает коррозионную стойкость хромистых сталей. Однако износостойкость повышается незначительно.
Известно, что карбид титана обладает высокими твердостью и износостойкостью. Благодаря этому его часто используют в процессе литья стали в качестве модификатора или в роли упрочняющих частиц с целью повышения эксплуатационных свойств готового материала.
В работах [5, 6] показано, что после наплавки TiC твердость и износостойкость покрытий в несколько раз выше по сравнению с материалом подложки. Поэтому в данной работе для получения износостойких и коррозионно-стойких покрытий в качестве наплавочной смеси использовали смесь карбида хрома с карбидом титана.
Целью работы явилось исследование влияния режимов обработки на коррозионную стойкость и износостойкость покрытий, полученных методом вневакуумной электронно-лучевой наплавки порошковой смеси Cr3C2 + TiC на низкоуглеродистую сталь.
ЭКСПЕРИМЕНТАЛЬНАЯ ЧАСТЬ
На ускорителе электронов ЭЛВ-6, разработанном и установленном в Институте ядерной физики СО РАН (г. Новосибирск) [1] получены покрытия методом наплавки в пучке релятивистских электронов. Состав наплавляемой смеси состоял из порошков карбида хрома (Cr3C2, 54 мас. %), карбида титана (TiC, 6 мас. %) и фтористого магния (MgF2, 40 мас. %) дисперсностью 2–5 мкм. MgF2 использовали в качестве флюса. Наплавочную смесь равномерно распределяли по поверхности металлической подложки размером 100 × × 50 × 14 мм из стали Ст3 (ГОСТ 380–2005) и подпрессовывали с давлением 30–60 кПа. Плотность насыпки составляла 0.45 г/см2. Основные параметры наплавки: энергия электронов 1.4 МэВ, ток пучка 25 мA, диаметр пучка 12 мм, расстояние от выпускного отверстия до поверхности 90 мм, ширина развертки 50 мм. Получено пять покрытий, соответствующих различным скоростям перемещения (v) образцов под пучком и W (табл. 1).
Таблица 1.
Режимы обработки покрытий
Режим | 1 | 2 | 3 | 4 | 5 |
---|---|---|---|---|---|
v, см/с | 0.95 | 0.8 | 0.7 | 0.6 | 0.55 |
W, кДж/см2 | 7.4 | 8.8 | 10.0 | 11.7 | 12.7 |
Структуру наплавленных покрытий исследовали в поперечном сечении методами оптической и растровой электронной микроскопии на микроскопах Neophot-32 и Quanta 200 3D соответственно. Микротвердость покрытий измеряли по методу Виккерса на приборе Duramin-5 при нагрузке на индентор 0.98 Н в течение 15 с. Элементный состав покрытий изучали методами микрорентгеноспектрального анализа.
Для определения коррозионной стойкости наплавленных покрытий в агрессивной среде была проведена серия экспериментов при комнатных условиях в концентрированной азотной кислоте (99%). Для проведения эксперимента были подготовлены образцы из наплавленных покрытий с размером 10 × 15 мм, не содержащие материал подложки Ст3. Толщина образцов варьировалась в приделах 1.5−3.5 мм. В зависимости от режима электронно-лучевой обработки масса у всех образцов была разной. Поэтому коррозионную стойкость покрытий оценивали по относительному изменению массы пластин наплавленного слоя, а также образцов стали Ст3 и нержавеющей стали 12Х18Н10Т (для сравнения) согласно ГОСТ 9.905-82 и ГОСТ 9.908-85 [7, 8].
Ввиду того что образцы фактически имеют разные покрытия, а также различный материал (образцы с покрытием и образцы сравнения), испытания проводились в семи разных емкостях. Емкости представляли собой бюксы с утапливаемой крышкой со шлифом для герметичности. Образцы полностью погружались в концентрированную азотную кислоту. Испытания проводились с промежуточным весовым контролем, для чего осуществлялись выемки образцов из кислоты. Взвешивание проводилось по следующей схеме: 0.08, 0.17, 0.34, 0.5, 0.67, 0.84, 1.2, 5, 8, 17, 24 ч. Общее время эксперимента составило 59.6 ч. После каждой выемки проводилась замена кислоты, записывались результаты измерений. Взвешивание осуществляли на лабораторных электронных весах марки ВЛР-200Г-М с дискретностью отсчета 0.05 мг.
Для определения абразивной износостойкости наплавленных покрытий были проведены испытания на износостойкость при трении о нежестко закрепленные абразивные частицы согласно ГОСТу 23.208-79 [9]. В качестве эталонных образцов использовалась сталь 45 в отожженном состоянии. В качестве абразива использовался кварцевый песок. Средний размер абразивных частиц составлял 0.4–0.8 мм. Образец изнашивался с помощью абразива, увлекаемого резиновым роликом на поверхность трения. Суть методики состоит в измерении потери массы испытуемого образца после проведения восьми циклов испытаний (цикл испытаний включал в себя износ образца в течение 1 ч) и сравнения его с эталоном.
РЕЗУЛЬТАТЫ И ОБСУЖДЕНИЕ
После наплавки на поверхности стали формируются слои толщиной 2.2−3.7 мм, в зависимости от режима обработки, свободные от трещин, отслоений и пор (рис. 1). С ростом поверхностной плотности введенной энергии толщина покрытия увеличивается. Структура всех полученных покрытий является доэвтектической, т.е. представляет собой смесь фазы твердого раствора и эвтектики. По данным рентгенофазового анализа, зерна дендритов и основа эвтектики представляют собой аустенит (γ-железо), других фаз на дифрактограммах не выявлено, вероятно, вследствие их малого количества в покрытиях. Значение микротвердости в 2–4 раза выше микротвердости материала подложки Ст3.
В работе [10] более подробно исследовано влияние режимов электронно-лучевой обработки на структуру и микротвердость наплавленных покрытий. Данная работа является продолжением исследований с целью изучения способности наплавленных покрытий сопротивляться воздействию коррозионных сред и абразивному износу.
Результаты измерения коррозионной стойкости образцов сравнения (Ст3 и 12Х18Н10Т) и наплавленных покрытий в концентрированной азотной кислоте приведены на рис. 2. Из рис. 2а видно, что кривые потери массы образцов наплавленных покрытий с увеличением времени выдержки в концентрированной азотной кислоте выходят на плато. Это связано с образованием защитной оксидной пленки (Cr,Fe)2О3 на поверхности образцов.
Рис. 2.
Зависимости относительной потери массы покрытий и образцов сравнения от времени выдержки в концентрированной азотной кислоте (а) и режима обработки (время воздействия составляет 24 ч) (б): столбики 1–5 соответствуют режимам, обозначенным в табл. 1, 6 – низкоуглеродистая сталь, 7 – нержавеющая сталь.
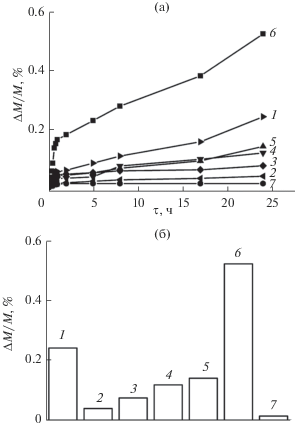
Зависимость коэффициента износостойкости от величины W приведена на рис. 3а. Из графика видно, что покрытия 2 и 3 имеют близкие коэффициенты износостойкости, превышающие значения для остальных образцов более чем в 2–4 раза. Из данных [11] известно, что для износостойкости важное значение имеет характер образующейся структуры: количественное соотношение структурных составляющих, их расположение, форма, размеры, состояние матрицы.
Рис. 3.
Зависимости коэффициента износостойкости Kи покрытий (а) и концентрации хрома и титана в покрытиях – в зернах аустенита (б) и в эвтектике (в) от режима обработки.
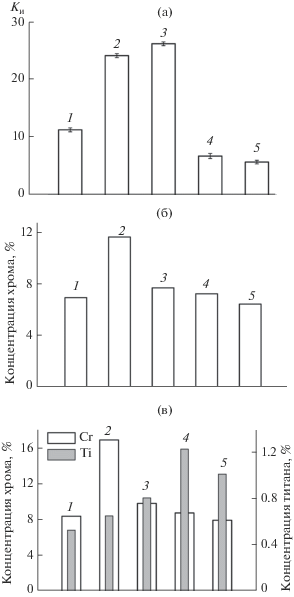
Для установления этих факторов были проведены исследования структуры и измерены концентрации легирующих элементов в различных фазах, присутствующих в составе покрытий.
Структурные исследования [12] показали, что во всех покрытиях присутствуют нерастворившиеся частицы карбида титана. Часть из них имеют размер, близкий к размеру исходного порошка TiC (~3 мкм), и кубическую огранку. Частицы меньшего размера могут располагаться как в теле зерен аустенита, так и на их границах. В покрытиях 1–5 наблюдаются существенные отличия в эвтектике. Так, в покрытиях 1 и 2 частиц карбида титана в эвтектиках не наблюдается. При увеличении W TiC в эвтектике хорошо просматривается в виде дисперсных частиц размером 0.15–0.20 мкм. Также встречаются частицы TiC более 0.5 мкм.
Методом микрорентгеноспектрального анализа измерены концентрации легирующих элементов в различных фазах, присутствующих в структуре покрытий. На рис. 3в приведены результаты микрорентгеноспектрального анализа, которые хорошо коррелируют со структурными исследованиями покрытий. В покрытиях 1 и 2 содержание титана в эвтектике низкое (отсутствуют следы карбида титана при структурных исследованиях). В покрытии 3 концентрация титана вырастает, коррелируя с наличием дисперсных частиц карбида титана в эвтектике. В покрытиях 4 и 5 концентрация титана еще увеличивается в связи с сохранением дисперсных частиц и возникновением более крупных частиц карбида титана в эвтектике.
Таким образом, покрытие 1 имеет более низкий коэффициент износостойкости в связи с малым количеством фазы TiC в эвтектике. В покрытиях 4 и 5 повышенное количество частиц TiC и более крупный их размер приводят к изменению механизма изнашивания – частицы TiC начинают выкрашиваться, а не истираться.
В покрытии 2 наблюдается пониженное содержание титана в эвтектике и повышенное содержание хрома по отношение к покрытию 3, что и является следствием повышенного значения износостойкости. Из рис. 3а, 3в следует, что покрытие 3 обладает оптимальным сочетанием концентрации хрома и титана в эвтектике с максимальным значением износостойкости.
При увеличении W толщина наплавленного слоя увеличивается, а концентрация легирующих веществ уменьшается на единицу объема. Из рис. 3б, 3в видно, что в покрытии 2 содержание хрома достигает 12–16%. Это и является причиной максимального значения коррозионной стойкости в покрытии 2.
В покрытиях 3, 4 и 5 (рис. 3), полученных при повышенных значениях W, наблюдается понижение содержания хрома и повышение содержания титана в эвтектике. Однако наличие титана в аустенитных сталях устраняет их восприимчивость к межкристаллитной коррозии, но несколько ухудшает их коррозионную стойкость в кипящей азотной кислоте и содержащих ее средах [13], что является дополнительной причиной более низкой коррозионной стойкости.
Результаты исследований показали, что коррозионная стойкость наплавленных покрытий порошковой смеси карбида хрома с карбидом титана в 16–22 раза выше по сравнению с наплавкой карбида хрома.
ЗАКЛЮЧЕНИЕ
Метод вневакуумной электронно-лучевой наплавки позволяет получать на низкоуглеродистой стали покрытия без дефектов в виде трещин и расслоений. При наплавке порошковой смеси Cr3C2 + TiC образуются покрытия с толщиной слоя 2.2−3.7 мм со структурой доэвтектического типа.
Выявлено, что на износостойкость и коррозионную стойкость покрытий влияют количество и размер частиц карбида титана. Оптимальными для получения износостойких и одновременно коррозионно-стойких покрытий при наплавке порошковой смеси Cr3C2 + TiC являются режимы при поверхностной плотности введенной энергии W = 8.8 и 10.0 кДж/см2.
Показано, что добавка карбида титана в наплавочную смесь при одном и том же режиме облучения позволяет повысить коррозионную стойкость в 16–22 раза по сравнению с наплавкой карбида хрома.
Список литературы
Фоминский Л.П., Казанский В.В. Наплавка порошковых покрытий пучком релятивистских электронов // Сварочное производство. 1985. № 5. С. 13–15.
Полетика И.М., Борисов М.Д., Краев Г.В., Вайсман А.Ф., Голковский М.Г., Дураков В.А. Основы легирования стали в пучке релятивистских электронов // Изв. ВУЗов. Физика. 1996. № 3. С. 115–125.
Bataev I.A., Bataev A.A., Golkovski M.G., Krivizhenko D.S., Losinskaya A.A., Lenivtseva O.G. Structure of Surface Layers Produced by Non-Vacuum Electron Beam Boriding // Appl. Surface Sci. 2013. V. 284. P. 472–481.
Полетика И.М., Иванов Ю.Ф., Голковский М.Г., Крылова Т.А., Перовская М.В. Структура и свойства коррозионно-стойких покрытий, полученных методом электронно-лучевой наплавки в атмосфере воздуха // МиТОМ. 2009. № 12. С. 33–39.
Муль Д.О., Дробяз Е.А., Чакин И.К., Самойленко В.В., Ложкин В.С., Доставалов Р.А. Структура и свойства стали после вневакуумной электронно-лучевой наплавки порошков титана, тантала, молибдена и графита // Обработка металлов (технология, оборудование, инструменты). 2013. № 3(60). С. 115–120.
Yun E., Kim Y.C., Lee S., Kim N.J. Correlation of Microstructure with Hardness and Wear Resistance in (TiC,SiC)/Stainless Steel Surface Composites Fabricated by High-Energy Electron-Beam Irradiation // Metall. Mater. Trans. A. 2004. V. 35. № 13. P. 1029–1038.
ГОСТ 9.905-82. Методы коррозионных испытаний. Общие требования.
ГОСТ 9.908-85. Методы определения показателей коррозии и коррозионной стойкости.
ГОСТ 23.208-79. Обеспечение износостойкости изделий. Метод испытания материалов на износостойкость при трении о нежестко закрепленные абразивные частицы.
Крылова Т.А., Иванов К.В., Овчаренко В.Е. Структурно-фазовое состояние и твердость покрытий, полученных при наплавке порошков Cr3C2 и TiC на низкоуглеродистую сталь высокоэнергетическим электронным пучком // ФиХОМ. 2018. № 3. С. 43–49.
Виноградов В.Н., Колокольников М.Г. Абразивное изнашивание. М.: Машиностроение, 1990. С. 224.
Krylova T.A., Ivanov K.V., Ovcharenko V.E. The Structure, Microhardness and Wear Resistance of Coatings Obtained through Non-Vacuum Electron Beam Cladding of Chromium and Titanium Carbides on Low Carbon Steel // Mater. Sci. Forum. 2018. V. 927. P. 13–19.
Кочергин В.П. Защита металлов от коррозии в ионных расплавах и растворах электролитов: Уч. пособие. Екатеринбург: Изд-во Урал. ун-та, 1991. 304 с.
Дополнительные материалы отсутствуют.
Инструменты
Неорганические материалы