Неорганические материалы, 2020, T. 56, № 3, стр. 336-342
Высокотемпературный синтез литых материалов на основе MAX-фазы Cr2AlC из смесей CaCrO4 + Al + C
В. А. Горшков 1, *, П. А. Милосердов 1, Н. В. Сачкова 1
1 Институт структурной макрокинетики и проблем материаловедения им. А.Г. Мержанова
Российской академии наук
142432 Московская обл., Черноголовка, ул. Академика Осипьяна, 8, Россия
* E-mail: gorsh@ism.ac.ru
Поступила в редакцию 31.01.2019
После доработки 24.09.2019
Принята к публикации 26.09.2019
Аннотация
Представлены экспериментальные результаты высокотемпературного синтеза литых композиционных материалов системы Cr–Al–C с различным соотношением между MAX-фазой Cr2AlC, карбидами и алюминидами хрома. Опыты проводили в универсальных СВС-реакторах под давлением аргона p = 5 МПа. В качестве шихт использовали смеси порошков хромата кальция (CaCrO4) с алюминием (АСД-I) и углеродом. Показано, что, варьируя содержание углерода в шихте, можно существенным образом влиять на закономерности синтеза, фазовый состав и микроструктуру целевых продуктов. Обнаружено, что при стехиометрическом содержании углерода в исходной смеси синтезируются литые композиционные материалы, состоящие в основном из MAX-фазы Cr2AlC, а также низшего карбида хрома Cr7C3 и алюминида хрома Cr5Al8. Введение дополнительного (сверхстехиометрического) количества углерода в исходную смесь приводит к увеличению содержания MAX-фазы Cr2AlC в целевом продукте, исчезновению алюминида хрома Cr5Al8, и образованию высшего карбида Cr3C2 вместо низшего. Полученные конечные продукты охарактеризованы методами рентгенографического и локального микроструктурного анализов. Изучены структура и состав целевых продуктов, полученных в различных условиях.
ВВЕДЕНИЕ
В системе Cr–Al–C известны следующие соединения хрома: карбиды Cr23C6, Cr7C3, Cr3C2, алюминиды Cr2Al, CrAl, Cr5Al8 и MAX-фаза Cr2AlC. Все они относятся к тугоплавким соединениям, обладающим полезными практическими свойствами. Карбиды и алюминиды хрома давно известны и хорошо изучены [1–4]. В последнее время большой интерес возник к MAX-фазам карбидных тройных соединений из-за необычной комбинации свойств металлов и керамики, делающих их перспективными для использования в аэрокосмической, автомобильной и индустриальной сферах [5, 6]. В настоящее время Cr2AlC является третьим наиболее широко изученным соединением после Ti3SiC2 и Ti3AlC2 среди семейства MAX-фаз.
В жидком состоянии хром и углерод неограниченно растворимы друг в друге. Кристаллическая структура Cr2AlC представляет собой 6 плотноупакованных слоев, 4 из которых состоят из атомов Cr и 2 из атомов Al. Имеется предположение, что при комнатной температуре Cr2AlC может вести себя как парамагнетик [7–9].
Из способов получения MAX-фазы Cr2AlC в литературе наиболее часто представлены методы горячего прессования и плазменно-искрового спекания [10, 11]. В работе [12] материал на основе Cr2AlC был получен методом двухстадийного спекания, включающего прямую реакцию жидкого алюминия с карбидами хрома с образованием интерметаллидов Cr–Al и карбида Al4C3, которые далее реагировали с формированием Cr2AlC. Порошок Cr2AlC также был успешно синтезирован из смеси гидрата сульфата алюминия (Al2(SO4)3 ⋅ 18H2O), аморфного диоксида кремния (SiO2) в расплавленной солевой среде сульфата натрия (Na2SO4) [13]. Синтез высокочистой металлокерамики Cr2AlC, включающий спекание (PLS) элементарных порошков с последующим плазменно-искровым спеканием (SPS) измельченного реакционного продукта, описан в работе [14].
Синтез тройного соединения Cr2AlC из порошковой смеси Cr, Al4C3 и графита в соотношении Cr : Al : C = 2 : 1.1 : 1 методом спекания импульсным разрядом в вакууме в диапазоне температур от 850 до 1350°C был исследован в работе [15]. Было обнаружено, что количество фазы Cr2AlC значительно увеличилось при проведении синтеза в температурном диапазоне от 950 до 1250°C в расчете на избыток Cr и Al4C3. Преимущественно однофазный Cr2AlC с небольшим количеством Cr7C3 образуется при температуре спекания 1250°C. Предполагается, что фаза Cr2AlC образуется вблизи частицы Al4C3 путем диффузии Cr и взаимного растворения Cr и Al4C3.
В работе [16] керамический материал на основе MAX-фазы Cr2AlC был получен методом горячего прессования в аргоне в диапазоне температур 850–1450°С. Исходные образцы в этом способе прессовали из порошков Cr, Al и углерода в соотношении Cr : Al : C = 1 : 1.2 : 1. Было обнаружено, что Cr5Al8, Cr2Al и Cr7C3 представляют собой промежуточные фазы, концентрация которых уменьшалась в процессе нагрева. Количество фазы Cr2AlC постепенно увеличивалось с повышением температуры за счет реакции между интерметаллидом Cr–Al, хромом и графитом. Промежуточные фазы полностью исчезают при температуре выше 1250°C. Методом совмещения самораспространющегося высокотемпературного синтеза (СВС) и процесса изостатического прессования (HIP) синтезирован объемный нанослоистый композит, содержащий Cr2AlC [17].
Большинство перечисленных процессов проводят при повышенных температурах (>1200°С), высоких давлениях прессования (до 20 МПа) с использованием сложного оборудования. Они малопроизводительны и энергозатратны. Наиболее перспективным способом получения таких материалов является одностадийный СВС [18]. Одним из направлений этого метода является СВС-металлургия, использующая исходные смеси, состоящие из оксидов металлов, металла-восстановителя (алюминия) и неметалла (углерод, бор, кремний). Температуры горения таких смесей превышают, как правило, температуры плавления исходных реагентов и конечных продуктов, получаемых в волне горения в жидкофазном (литом) состоянии [19]. Этим методом были получены литые материалы с различным содержанием фазы Cr2AlC [20, 21], при этом авторы для получения целевых конечных продуктов использовали исходные смеси, содержащие хромовый ангидрид (CrO3), который является гигроскопичным и термически нестабильным, что ограничивает практическую реализацию метода.
Целью данной работы является разработка синтеза методом СВС-металлургии литых материалов на основе MAX-фазы Cr2AlC с использованием в исходной смеси вместо хромового ангидрида (CrO3) хромата кальция (CaCrO4), имеющего более высокую термическую стабильность и малую гигроскопичность.
ЭКСПЕРИМЕНТАЛЬНАЯ ЧАСТЬ
В экспериментах использовали смеси порошков хромата кальция квалификации “ч. д. а.”, алюминия марки АСД–1 и графита марки ГМЗ с размером частиц 40–160 мкм. Исходные смеси готовили в планетарном смесителе или в шаровой мельнице. В качестве базовой использовали стехиометрическую смесь, состав которой рассчитывали из следующей реакции:
(I)
$2{\text{CaCr}}{{{\text{O}}}_{{\text{4}}}} + 5{\text{Al}} + {\text{C}} = {\text{C}}{{{\text{r}}}_{{\text{2}}}}{\text{AlC}} + 2{\text{A}}{{{\text{l}}}_{{\text{2}}}}{{{\text{O}}}_{3}} + 2{\text{CaO}}.$Смеси помещали в прозрачные кварцевые стаканчики диаметром 15–25 мм, высотой 50–60 мм. Масса смеси во всех экспериментах составляла 20 г. Синтезы проводили в СВС-реакторе объемом 3 л при начальном избыточном давлении аргона 5 МПа.
В экспериментах изучали влияние содержания избытка углерода в исходной смеси (ΔC) на скорость горения (u), относительный выход металлической фазы в слиток (ηв) и относительную потерю массы смеси при горении (ηд). Содержание избытка углерода в исходной смеси (ΔC) рассчитывали по формуле ΔC = ($М_{{\text{С}}}^{{{\text{эксп}}}}$ – $М_{{\text{С}}}^{{{\text{стех}}}}$)/$М_{{\text{С}}}^{{{\text{стех}}}},$ где $М_{{\text{С}}}^{{{\text{эксп}}}}$ – количество углерода в смеси в эксперименте, $М_{{\text{С}}}^{{{\text{стех}}}}$ – количество углерода, рассчитанное из формулы (I). Скорость горения рассчитывали по формуле u = h/τ, где h – высота слоя смеси в кварцевом стаканчике, τ – время горения. Выход металлической фазы в слиток (ηв) и относительную потерю массы смеси (диспергирования) при горении (ηд) рассчитывали по формулам: ηв = = mсл/Mсм × 100%, ηд = (Mсм – Mк)/Mсм × 100%, где Mсм – масса исходной смеси, Mк – масса конечных продуктов горения, mсл – масса металлического слитка. Время горения смеси замеряли с помощью секундомера и видеозаписи.
Фазовый состав продуктов горения определяли методами рентгенофазового анализа и электронной микроскопии. Рентгенофазовый анализ проводился на дифрактометре ДРОН-3М с использованием излучения Cu с монохроматором на вторичном пучке. Исследование микроструктуры и элементного анализа образцов проводили на автоэмиссионном сканирующем электронном микроскопе сверхвысокого разрешения ULTRA plus Zeiss с системой микроанализа INCA 350 Oxford Instruments.
РЕЗУЛЬТАТЫ ЭКСПЕРИМЕНТА
При сжигании исходных смесей со стехиометрическим соотношением реагентов, рассчитанным из формулы (I), было обнаружено, что смеси горят в стационарном режиме с ровным фронтом. Скорость горения равна 11 мм/с. Конечные продукты в волне горения получаются в жидкофазном состоянии и из-за различных удельных весов под действием гравитации разделяются на два слоя: нижний – металлоподобный, верхний – оксидный. На рис. 1 представлены кварцевая форма (стаканчик) с исходной смесью (а), внешний вид конечных продуктов (б): верхний слиток (1) – оксидный Al2O3/СаО, нижний слиток (2) – целевой продукт Cr–Al–C. В дальнейших экспериментах было изучено влияние содержания избытка углерода в исходной смеси ΔC на закономерности синтеза: (u, ηв, ηд), а также на фазовый состав и микроструктуру конечных целевых продуктов. Из рис. 2 видно, что при добавлении избытка углерода в исходную смесь (ΔC = 0–3.75) происходит увеличение выхода целевого продукта (ηв) от 15 до 27% при одновременном снижении относительной потери массы смеси (ηд) от 13 до 7.5% и скорости горения (u) от 11 до 7.5 мм/с.
Рис. 1.
Кварцевая форма с исходной смесью (а), внешний вид конечных продуктов (б): верхний слиток (1) – оксидный Al2O3/СаО, нижний слиток (2) – целевой продукт Cr–Al–C.
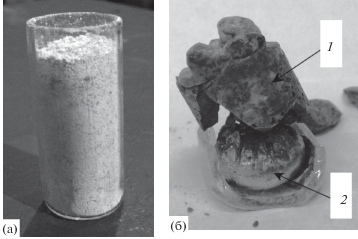
Рис. 2.
Влияние избытка углерода в исходной смеси (ΔC) на скорость горения u, выход металлической фазы (ηв) и разброс продуктов горения (диспергирование) (ηд).
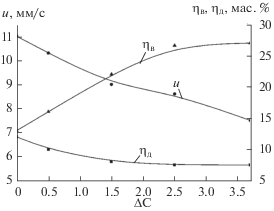
Рентгенофазовый анализ (рис. 3) показал, что при сжигании смеси (I) со стехиометрическим соотношением реагентов целевой продукт состоит из MAX-фазы Cr2AlC, низшего карбида хрома Cr7C3 и алюминида хрома Cr5Al8. Дифракционные линии MAX-фазы Cr2AlC узкие, что свидетельствует о высокой степени совершенства ее кристаллической структуры. Параметры элементарной ячейки синтезированной МАХ-фазы Cr2AlC (a = 0.286 нм, c = 1.283 нм) практически совпадают с данными базы PDF2 (№ 89–2275: a = 0.286 нм, c = 1.282 нм). Количественный анализ, проведенный методом Ритвельда, показал, что содержание фазы Cr2AlC составляет 67 об. %.
На рис. 4 представлены микроструктура, элементный и расчетный фазовый состав образца, полученного при горении стехиометрической смеси: CaCrO4 + Al + С (ΔC = 0). Видно, что материал состоит в основном из фазы Cr2AlC, а также небольшого количества алюминида хрома Cr5Al8 и карбида хрома Cr7C3. Результаты электронной микроскопии хорошо соответствуют данным рентгенофазового анализа, представленным на рис. 3. По данным локального микроструктурного анализа (рис. 4), кроме указанных выше фаз в целевом продукте присутствует в небольшом количестве тройная карбидная фаза CrхAlyCz, состав которой из-за ее малого содержания определить не удалось.
Рис. 4.
Микроструктура, элементный состав (мас. %) и расчетный фазовый состав целевого продукта при горении стехиометрической (ΔC = 0) смеси (I) (Мсм = 20 г, фазовый состав рассчитывали из данных рентгенофазового и локального микроструктурного анализов).
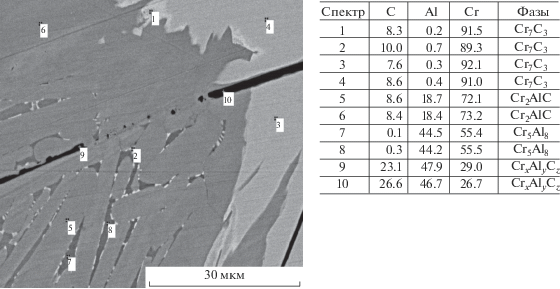
С введением в исходную смесь дополнительного (сверхстехиометрического) количества углерода в целевом продукте исчезает (за счет образования MAX-фазы Cr2AlC) алюминид хрома Cr5Al8, а вместо низшего карбида Cr7C3 образуется высший карбид Cr3C2. На рис. 5 представлена дифрактограмма образца, полученного при горении исходной смеси с избытком углерода ΔС = 2.5. Видно, что целевой продукт состоит из фазы Cr2AlC и небольшого количества высшего карбида хрома Cr3C2. Дифракционные линии MAX-фазы Cr2AlC узкие. Наличие карбидов и алюминидов хрома в конечном целевом продукте объясняется тем, что во время горения исходной смеси, состав которой рассчитан в соответствии с (I), углерод и алюминий в волне горения образуют газообразные продукты (СО, СО2, Alg, AlO, Al2O) и удаляются из расплава. Вследствие этого в системе образуется их “дефицит” по сравнению со стехиометрическим содержанием, что приводит к образованию фаз Cr5Al8 и Cr7C3 [20, 21].
Рис. 5.
Дифрактограмма образца, полученного при горении исходной смеси с избытком углерода ΔС = = 2.5 (Мсм = 20 г).
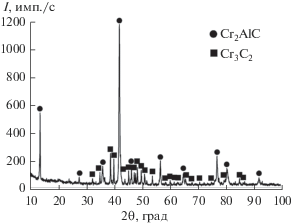
На рис. 6 представлены микроструктура, элементный и фазовый состав целевого продукта, полученного при горении исходной смеси с избытком углерода ΔС = 2.5. Видно, что материал состоит из MAX-фазы Cr2AlC и зерен высшего карбида Cr3C2.
Рис. 6.
Микроструктура, элементный состав (мас. %) и расчетный фазовый состав целевого продукта, полученного при горении исходной смеси с избытком углерода ΔС = 2.5 (Мсм = 20 г, фазовый состав рассчитывали из данных рентгенофазового и локального микроструктурного анализов).
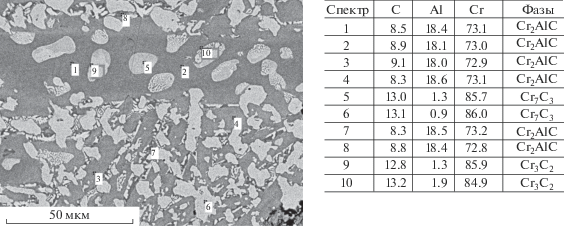
На рис. 7 представлены микроструктура, элементный и фазовый состав поверхности излома целевого продукта, полученного при горении смеси с избытком углерода ΔС = 2.5. Видно, что зерна MAX-фазы Cr2AlC имеют слоистую структуру, внутри них находятся зерна Cr3C2.
Рис. 7.
Микроструктура, элементный состав (мас. %) и расчетный фазовый состав поверхности излома целевого продукта, полученного при горении смеси с избытком углерода ΔС = 2.5 (фазовый состав рассчитывали из данных рентгенофазового и локального микроструктурного анализов).
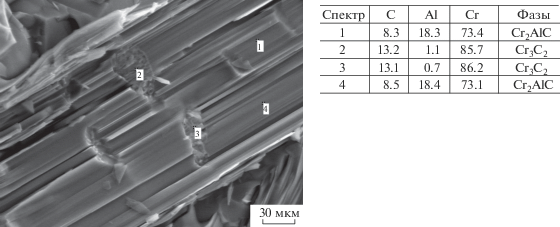
На рис. 8 представлен характерный вид слоистой структуры MAX-фазы Cr2AlC. При этом наблюдается наноламинатная структура с толщиной слоев 3.06 и 12.9 нм. Данные локального микроструктурного анализа (рис. 6, 7 и 8) хорошо коррелируют с результатами рентгенофазового анализа (рис. 5).
ОБСУЖДЕНИЕ РЕЗУЛЬТАТОВ
Наличие фаз карбидов и алюминидов хрома в конечном целевом продукте объясняется тем, что СВС-металлургия – сложный и многостадийный процесс [19–21]. Во время горения исходной смеси (I) часть углерода участвует в окислительно-восстановительной реакции с образованием газообразных продуктов (СО, СО2) и удаляется из расплава. В результате этого в системе образуется “дефицит” углерода по сравнению со стехиометрическим значением и, наоборот, “избыток” алюминия по сравнению с его расчетным стехиометрическим содержанием. Для устранения “дефицита” углерода в исходную стехиометрическую смесь в различном количестве вводили его избыток (∆C).
(II)
$\begin{gathered} 2{\text{CaCr}}{{{\text{O}}}_{4}} + 5{\text{Al}} + ({\text{C}} + \Delta {\text{С}}) = \\ = \,\,{\text{C}}{{{\text{r}}}_{{\text{2}}}}{\text{AlC}} + 2{\text{A}}{{{\text{l}}}_{{\text{2}}}}{{{\text{O}}}_{3}} + 2{\text{CaO}}\, + \uparrow \left( {{\text{СО}},{\text{ С}}{{{\text{О}}}_{2}}} \right). \\ \end{gathered} $Из анализа проведенных экспериментов можно предположить следующие химические стадии синтеза:
(1)
${\text{CaCr}}{{{\text{O}}}_{4}} + {\text{Al}} + {\text{C}} \to {\text{C}}{{{\text{r}}}_{{\text{2}}}}{\text{AlC}} + {\text{A}}{{{\text{l}}}_{{\text{2}}}}{{{\text{O}}}_{3}} + {\text{CaO}},$(2)
${\text{CaCr}}{{{\text{O}}}_{{\text{4}}}} + {\text{С}} \to {\text{C}}{{{\text{r}}}_{{\text{7}}}}{{{\text{C}}}_{3}} + ({\text{СО}},\,\,{\text{C}}{{{\text{O}}}_{2}}){\kern 1pt} \uparrow + {\text{ CaO}},$(3)
${\text{CaCr}}{{{\text{O}}}_{4}} + \Delta {\text{Al}} \to {\text{C}}{{{\text{r}}}_{{\text{5}}}}{\text{A}}{{{\text{l}}}_{8}} + {\text{A}}{{{\text{l}}}_{{\text{2}}}}{{{\text{O}}}_{3}} + {\text{СаО}},$(4)
${\text{C}}{{{\text{r}}}_{{\text{7}}}}{{{\text{C}}}_{3}} + \Delta {\text{С}} \to {\text{C}}{{{\text{r}}}_{{\text{3}}}}{{{\text{C}}}_{2}},$(5)
${\text{C}}{{{\text{r}}}_{{\text{5}}}}{\text{A}}{{{\text{l}}}_{8}} + \Delta {\text{С}} \to {\text{C}}{{{\text{r}}}_{{\text{2}}}}{\text{AlС}},$(6)
${\text{C}}{{{\text{r}}}_{{\text{7}}}}{{{\text{C}}}_{3}} + \Delta {\text{Al}} \to {\text{C}}{{{\text{r}}}_{{\text{2}}}}{\text{AlC}}.$При прохождении базовой реакции (1) из-за участия углерода в окислительно-восстановительной реакции (2) образуется низший карбид хрома Cr7C3. При этом в системе остается избыток алюминия (∆Al), который реагирует с CaCrO4 (3) с образованием алюминида хрома Cr5Al8 (в литературе [16] известны также случаи формирования Cr2Al). Введение в исходную базовую смесь избытка углерода (ΔС) привело к увеличению полноты реагирования и выхода целевого продукта (ηв) в отдельный слиток (рис. 2). При этом ΔС реагирует с Cr7C3 (4) и с Cr5Al8 (5), образуя Cr3C2 и Cr2AlС. Избыток алюминия вступает в реакцию с Cr7C3 и образует Cr2AlC (6). В результате введение в исходную смесь избытка углерода приводит к увеличению содержания MAX-фазы Cr2AlC в целевом продукте, исчезновению алюминида хрома Cr5Al8, а вместо низшего карбида хрома Cr7C3 образуется высший карбид Cr3C2.
ЗАКЛЮЧЕНИЕ
Методом СВС-металлургии получены литые материалы на основе MAX-фазы Cr2AlC с использованием в исходной смеси вместо хромового ангидрида (CrO3) хромата кальция (CaCrO4), имеющего более высокую термическую стабильность и малую гигроскопичность.
Изучено влияние содержания избытка углерода в шихте на закономерности синтеза (u, ηв, ηд), фазовый состав и микроструктуру конечных продуктов.
Изучены структурно-фазовые состояния целевых продуктов, полученных в различных условиях.
Обнаружено, что при стехиометрическом содержании углерода в исходной смеси синтезируются литые композиционные материалы, состоящие в основном из MAX-фазы Cr2AlC, а также низшего карбида хрома Cr7C3 и алюминида хрома Cr5Al8.
Введение дополнительного (сверхстехиометрического) количества углерода в исходную смесь приводит к увеличению содержания MAX-фазы Cr2AlC в целевом продукте, исчезновению алюминида хрома Cr5Al8, а вместо низшего карбида хрома Cr7C3 образуется высший карбид Cr3C2.
Список литературы
Кифер Р., Бенезовский Ф. Твердые материалы. М.: Металлургия, 1968. С. 384.
Руднева В.В., Галевский Г.В. Исследование коррозионной стойкости нанопорошков тугоплавких боридов и карбидов в растворах электролитов // Изв. вузов. Цв. металлургия. 2007. № 2. С. 67–70.
Ноздрин И.В., Галевский Г.В., Ширяева Л.С., Руднева В.В. Структура и свойства композиционных покрытий никель–нанопорошок карбонитрида хрома // Наноинженерия. 2013. № 7(25). С. 36–42.
Guilemagy J.M., Espallargas N., Suegama P.H., Benedetti A.V. Comparative Study of Cr3C2–NiCr Coating // Corrosion Sci. 2006. V. 48. P. 2998–3013.
Barsoum M.W. The MAX Phases: A New Class of Solids: Thermodynamically Stable Nanolaminates // Prog. Solid State Chem. 2000. V. 28. P. 201–281.
Hettinger J.D., Lofland S.E., Finkel P., Meehan T., Palma J., Harrell K., Gupta S., Ganguly A., El-Raghy T., Barsoum M.W. Electrical Transport, Thermal Transport, and Elastic Properties of M2AlC (M = Ti, Cr, Nb, and V) // Phys. Rev. B. 2005. V. 72. № 11. P. 115120.
Tian W.B., Wang P.L., Zhang G., Kan Y., Li Y., Yan D. Synthesis and Thermal and Electrical Properties of Bulk Cr2AlC // Scr. Mater. 2006. V. 54. P. 841–846.
Lin Z., Zhou Y., Li M. Synthesis, Microstructure, and Property of Cr2AlC // J. Mater. Sci. Technol. 2007. V. 23. № 6. P. 721–746.
Schneider J.M., Sun Z., Mertens R., Uestel F., Ahuja R. Ab-Initio Calculations and Experimental Determination of the Structure of Cr2AlC // Solid State Commun. 2004. V. 130. P. 445–449.
Tian W., Vanmeensel K., Wang P., Zhang G., Li Y., Vleugels J., Van der Biest O. Synthesis and Characterization of Cr2AlC Ceramics Prepared by Spark Plasma Sintering // Mater. Lett. 2007. V. 61. P. 4442–4445.
Xiao L.O., Li S.B., Song G., Sloof W.G. Synthesis and Thermal Stability of Cr2AlC // J. Eur. Ceram. Soc. 2011. V. 31. P. 1497–1502.
Panigrahi B.B., Chu M.C., Kim Y-II, Cho S.J, Gracio J.J. Reaction Synthesis and Pressureless Sintering of Cr2AlC // Powder. Am. Ceram. Soc. 2010. V. 93. № 6. P. 1530–1533.
Xiao D., Zhu J., Wang F., Tang Y. Synthesis of Nano Sized Cr2AlC Powders by Molten Salt Method // J. Nanosci. Nanotechnol. 2015. V. 15. P. 7341–7345.
Duan X., Shen L., Jia D., Zhou Y., Zwaag S., Sloof W.G. Synthesis of High-Purity, Isotropic or Textured Cr2AlC Bulk Ceramics by Spark Plasma Sintering of Pressure-Less Sintered Powders // J. Eur. Ceram. Soc. 2015. V. 35. P. 1393–1400.
Tian W.B., Sun Z.M., Du Y., Hashimoto H. Synthesis Reactions of Cr2AlC from Cr–Al4C3–C by Pulse Discharge Sintering // Mater. Lett. 2008. V. 62. P. 3852–3855.
Tian W.B., Wang P.L., Kana Y.M., Zhang G.J., Li Y.X., Yan D.S. Phase Formation Sequence of Cr2AlC Ceramics Starting from Cr–Al–C Powders // Mater. Sci. Eng. A. 2007 V. 443. P. 229–234.
Ying G., He X., Li M., Li Y., Du S. Synthesis and Mechanical Properties of Nano-Layered Composite // J. Alloys Compd. 2010. V. 506. P. 734–738.
Levashov E.A., Mukasyan A.S., Rogachev A.S., Shtansky D.V. Self-Propagating High-Temperature Synthesis of Advanced Materials and Coatings // Int. Mater. Rev. 2017. V. 62. № 4. P. 203–239.
Левашов Е.А., Рогачев А.С., Курбаткина В.В., Максимов Ю.М., Юхвид В.И. Перспективные материалы и технологии самораспространяющегося высокотемпературного синтеза М.: Издат. Дом МИСиС, 2011. С. 378.
Горшков В.А., Милосердов П.А., Лугинина М.А., Сачкова Н.В., Беликова А.Ф. Высокотемпературный синтез литого материала с максимальным содержанием МАХ-фазы Cr2AlC // Неорган. материалы. 2017. Т. 53. № 3. С. 260–266.
Горшков В.А., Милосердов П.А., Сачкова Н.В., Лугинина М.А., Юхвид В.И. СВС-металлургия литых материалов на основе MAX-фазы Cr2AlC // Изв. вузов. Порошковая металлургия и функциональные покрытия. 2017. № 2. С. 47–54.
Дополнительные материалы отсутствуют.
Инструменты
Неорганические материалы