Неорганические материалы, 2021, T. 57, № 10, стр. 1056-1062
Влияние температуры горения смесей Al + AlN в азоте на содержание кислорода, растворенного в структуре нитрида алюминия
В. В. Закоржевский 1, *, И. Д. Ковалев 1, Н. И. Мухина 1
1 Институт структурной макрокинетики и проблем материаловедения им. А.Г. Мержанова
Российской академии наук
142432 Московская обл., Черноголовка, ул. Академика Осипьяна, 8, Россия
* E-mail: zakvl@ism.ac.ru
Поступила в редакцию 29.03.2021
После доработки 16.06.2021
Принята к публикации 18.06.2021
Аннотация
Исследовано влияние температуры горения смесей Al + AlN в азоте и длительности остывания продуктов синтеза на содержание примеси кислорода, растворенной в решетке нитрида алюминия. Показано, что в интервале температур 1460–2000°С происходит внедрение поверхностного кислорода в структуру AlN. Установлено, что с ростом температуры синтеза содержание растворенного в нитриде алюминия кислорода возрастает. Концентрация растворенного кислорода увеличивается при использовании разбавителя (AlN) с более мелкими частицами. Показано, что с увеличением температуры синтеза происходят укрупнение зерен нитрида алюминия и их срастание, что характерно для собирательной рекристаллизации. Определено, что для снижения концентрации примеси кислорода, растворенной в нитриде алюминия, в шихту необходимо вводить добавки, которые способствуют восстановлению оксида алюминия или переводу поверхностного кислорода в газовую фазу.
ВВЕДЕНИЕ
В настоящее время нитрид алюминия является наиболее привлекательным материалом для электроники и электротехники. Сочетание таких качеств, как высокая теплопроводность, высокое электрическое сопротивление и низкий коэффициент теплового расширения, позволили использовать его для получения теплопроводящей диэлектрической керамики широкого спектра применения. Керамика из нитрида алюминия для производства подложек микросхем – более дешевая и безопасная альтернатива токсичного оксида бериллия [1, 2].
Электрофизические свойства керамики из нитрида алюминия во многом зависят от характеристик исходного порошка нитрида алюминия и режима спекания. Основными факторами являются чистота исходного порошка нитрида алюминия по кислороду [3–5], примесям катионов металлов [6–8], гранулометрический состав, а также наличие спекающих добавок [7]. Кислород – наиболее определяющая примесь, особенно та его часть, которая растворена в решетке нитрида алюминия. Исследования показали, что для обеспечения теплопроводности керамики более 170 Вт/(м К) общее содержание примеси кислорода в порошке AlN не должно превышать 0.9 мас. %, а растворенного в решетке – 0.4 мас. % [9, 10].
Установлено, что при внедрении атомов кислорода в структуру AlN уменьшается параметр решетки с. Таким образом, значение параметра кристаллической решетки с коррелирует с концентрацией примеси кислорода, растворенного в нитриде алюминия, и, соответственно, с теплопроводностью керамики из AlN [11, 12]. Экспериментально определенная зависимость между теплопроводностью и содержанием кислорода в спеченном AlN показана в [10, 13–15].
Поскольку присутствие растворенного в решетке AlN кислорода влияет на параметр с, он может являться количественным индикатором содержания кислорода в структуре AlN, что позволит прогнозировать величину теплопроводности керамики. Так, порошок нитрида алюминия производства Tokuyama Soda, AlN Grade F при общей концентрации кислорода 0.8–0.9 мас. % содержит 0.4 мас. % растворенного кислорода. При спекании такого порошка в течение 5 ч по рекомендованному режиму при температуре 1850°С получается керамика с теплопроводностью 160–170 Вт/(м К). При этом в процессе спекания содержание примеси кислорода в спеченном AlN снижается до 0.2 мас. %. Таким образом, для повышения теплопроводности керамики из нитрида алюминия важно использовать порошок нитрида алюминия с низким содержанием растворенного кислорода.
Наличие примеси кислорода в AlN определяется чистотой сырья и условиями синтеза. Поскольку очистка кристаллической структуры AlN от растворенного кислорода – процесс диффузионный и протекает очень медленно, то основными влияющими на него параметрами являются восстановительная среда, температура и длительность синтеза. При печном синтезе методом прямого азотирования или карботермическом восстановлении оксида алюминия в азоте процесс идет в течение нескольких часов при температуре 1400–1600°С. Этого времени достаточно, чтобы получить AlN с содержанием растворенного кислорода 0.4–0.5 мас. % [16, 17]. Синтез нитрида алюминия в режиме горения – процесс быстротекущий, характеризуется быстрым достижением максимальной температуры и быстрым охлаждением продуктов. Время нахождения синтезированного нитрида алюминия при температурах более 1400°С составляет от 1 до 5 мин, в зависимости от начальных условий синтеза. Однако максимальная температура горения может достигать 2200°С, что значительно выше температуры печного синтеза. Таким образом, представляет интерес влияние температуры синтеза и длительности охлаждения на содержание примеси растворенного кислорода в нитриде алюминия, полученном методом самораспространяющегося высокотемпературного синтеза (СВС).
Целью данной работы является изучение влияния температуры синтеза и времени остывания продуктов на концентрацию растворенного в структуре нитрида алюминия кислорода при горении смесей Al + AlN в азоте.
ЭКСПЕРИМЕНТАЛЬНАЯ ЧАСТЬ
Эксперименты проводили в промышленном реакторе с рабочим объемом 30 л. Навеска шихты – 3.0 кг, начальное давление азота – 2.0 МПа. Реакционная шихта состояла из смеси порошков алюминия и разбавителя, нитрида алюминия, который вводили в состав шихты для обеспечения необходимого температурного режима синтеза. Содержание порошка алюминия в шихте составляло 18 и 24 мас. %.
Для приготовления реакционной шихты использовали порошок алюминия марки АСД-1 и два вида СВС-порошков нитрида алюминия: крупнодисперсный (1) и мелкодисперсный (2). Поскольку процесс удаления примеси кислорода, растворенного в решетке AlN, диффузионный, размер частиц нитрида алюминия является важным параметром. Крупнодисперсный порошок AlN был представлен частицами размером 2–5 мкм, объединенными в кагломераты размером 10–20 мкм (рис. 1а). Мелкодисперсный порошок AlN состоял из отдельных частиц размером 0.5–3 мкм (рис. 1б).
Для определения количества кислорода, растворенного в решетке AlN, был построен график (рис. 2) на основе зависимостей теплопроводности от параметра с и от содержания кислорода в решетке AlN [3, 10–15, 18, 19].
Характеристики исходных компонентов представлены в табл. 1. Видно, что, помимо растворенного в решетке кислорода, в разбавителе присутствует примесь кислорода, находящаяся на поверхности частиц разбавителя в виде оксигидроксида алюминия (AlOOH), который образуется в процессе гидролиза при контакте нитрида алюминия с атмосферной влагой. Содержание поверхностного кислорода выше у более мелкого порошка нитрида алюминия.
Таблица 1.
Характеристика компонентов шихты
Компонент | Кислород, мас. % | Удельная поверхность, м2/г | Средний диаметр частиц d50, мкм | Параметры элементарной ячейки, Å | |
---|---|---|---|---|---|
общий | растворенный в решетке AlN | ||||
Al (АСД-1) | 0.2 | 0.1 | 22.0 | ||
AlN (СВС-1) | 0.9 | 0.4 | 1.2 | 8.8 | а = 3.1114(1) с = 4.97995(20) |
AlN (СВС-2) | 1.1 | 0.4 | 3.5 | 2.2 | а = 3.1113(1) с = 4.9800(1) |
Азот “ос. ч.” | 0.0001 об. % |
Порошки исходных компонентов смешивали в шаровой мельнице в течение 1 ч. Полученную шихту загружали в реакционную лодочку и помещали в реактор. Реактор продували азотом квалификации “ос. ч.” для удаления кислорода воздуха, затем заполняли азотом до необходимого давления и осуществляли воспламенение шихты. После охлаждения спек извлекали из реактора и направляли на исследование и переработку.
Для определения параметра с AlN снимали рентгенограммы (дифрактометр ДРОН-3М, излучение CuKα, шаг по углу 0.02°, время экспозиции 1 с). Рентгенофазовый анализ (РФА) проводился в программе Crystallographica Search-Match. В качестве эталона в образцы добавляли 15 мас. % кремния. Параметры ячейки рассчитывались в программном комплексе “Буревестник”. Для расчета параметров ячейки AlN (гексагональная сингония, пр. гр. P63mc) использовались следующие отражения: 103, 200, 112, 201, 202, 210, 211, 114, 212, 105, 300, 213, 302.
Морфологию продуктов синтеза исследовали с помощью сканирующего электронного микроскопа LEO 1450 фирмы Carl Zeiss SMT AG Company. Гранулометрический состав порошков определяли с помощью лазерного анализатора MicroSizer 201. Удельную поверхность определяли методом БЭТ по адсорбции азота с помощью прибора “Сорби-М”. Для измерения температур горения использовали термопары ВР5/ВР20. Запись температурных кривых осуществляли с помощью блока АЦП с соответствующим компьютерным и программным обеспечением.
РЕЗУЛЬТАТЫ И ОБСУЖДЕНИЕ
В процессе исследований установлено, что при горении реакционной смеси Al+AlN в азоте по сечению спека формируется градиент температур, величина которого зависит от состава шихты. Возникновение градиента температур связано с низкой скоростью горения (0.2–0.4 мм/с) и интенсивным теплоотводом с поверхности спека в газовую среду. В связи с этим измеренная температура горения зависила от глубины погружения термопары. Поэтому для получения объективных результатов пробы образцов AlN отбирали из области спая термопары. На рис. 3 показаны температурные профили горения шихт с минимальным содержанием алюминия. Видно, что при низком (18 мас. %) содержании алюминия в шихте максимальная температура синтеза равна 1460–1500°С и сохраняется на одном уровне около 30 с, а затем плавно снижается для обоих составов. Охлаждение спеков AlN, полученных из шихты, содержащей 24 мас. % алюминия, более медленное, а время пребывания при максимальной температуре составляет около 50 с (рис. 4). Таким образом, нитрид алюминия, синтезированный из шихты с 24 мас. % порошка алюминия, подвергается более длительному тепловому воздействию. Время пребывания при температуре выше 1500°С составляет около 300 с для состава с мелкодисперсным разбавителем и 200 с для состава с крупнодисперсным разбавителем.
Рис. 3.
Температурные профили горения шихт с содержанием 18 мас. % алюминия: разбавитель – 1 (а), 2 (б).
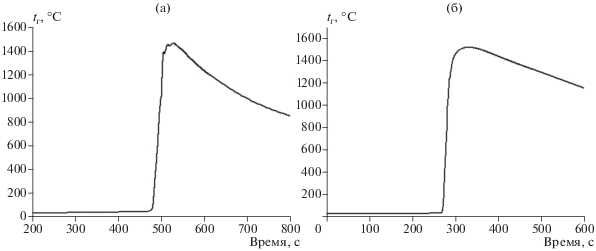
Рис. 4.
Температурные профили горения шихт с содержанием 24 мас. % алюминия: разбавитель – 1 (а), 2 (б).
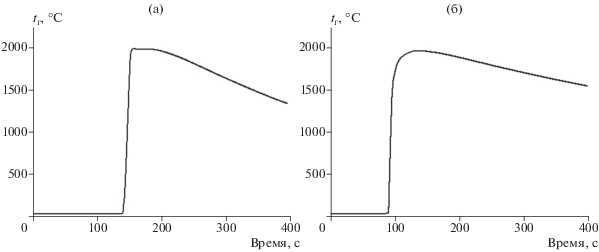
Значительная разница между минимальными и максимальными температурами синтеза и временами воздействия температуры существенно повлияла на концентрацию примеси кислорода в структуре AlN. При синтезе AlN в режиме горения без восстановительной атмосферы с ростом температуры параметр с снижается, а следовательно, содержание кислорода, растворенного в структуре AlN, возрастает (рис. 5). Это значит, что без восстановительной атмосферы или иной среды, которая бы создавала отрицательный градиент концентрации кислорода между поверхностью частицы AlN и ее в объемом, происходит диффузия поверхностной примеси кислорода в объем частицы нитрида алюминия. Ранее было установлено, что при синтезе композита AlN–Y2O3 с возрастанием температуры параметр с увеличивается. Происходит очистка поверхности зерен AlN от примеси кислорода с образованием алюминатов иттрия. Это создает дефицит атомов кислорода на поверхности зерен AlN и является движущей силой для диффузии кислорода к поверхности зерна [20].
Рис. 5.
Зависимости параметра с AlN от температуры синтеза: кривые 1, 2 соответствуют номерами разбавителя.
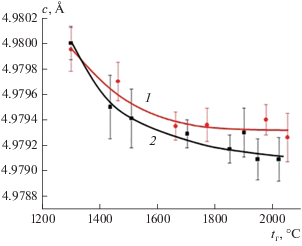
Из рис. 5 видно, что при использовании более мелкого разбавителя снижение параметра с значительнее по сравнению с более крупным, что можно объяснить большей площадью при диффузии кислорода. Сопоставление рассчитанных параметров с (рис. 5) с графиком на рис. 2 показало, что при максимальных температурах синтеза содержание кислорода в решетке AlN возросло с 0.4 до 0.6 и 0.7 мас. % при использовании крупного и мелкого разбавителя соответственно. Химический анализ образцов нитрида алюминия, полученных при максимальной температуре синтеза, показал снижение содержания общего кислорода до 0.7 и 0.9 мас. % соответственно. Таким образом, общее содержание кислорода в AlN снизилось, а растворенного в решетке возросло.
Из рис. 5 видно, что при температуре выше 1900°С кривая 1 вышла на горизонталь, т.е. вся поверхностная примесь кислорода перешла в объем синтезированных частиц нитрида алюминия. Это также подтверждается совпадением результатов химического анализа и оценки по калибровочному графику. Снижение общего содержания кислорода произошло за счет образования нового, более чистого по кислороду нитрида алюминия.
Нитрид алюминия, полученный из шихты с 18 мас. % порошка алюминия, представляет собой мягкие, легко разрушаемые спеки. Микроструктура спеков в основном состоит из слабоспеченных частиц нитрида алюминия равноосной формы размером 1–4 мкм, а также субмикронных частиц иглоподобной и равноосной форм (рис. 6). Условия синтеза не повлияли на характер микроструктуры разбавителя. Исходя из снижения параметра с AlN можно предположить, что в процессе горения частиц алюминия в азоте возрастание содержания примеси кислорода в решетке AlN произошло за счет диффузии поверхностного кислорода разбавителя в объем частицы нитрида алюминия. При горении шихты с 24 мас. % Al температура синтеза приблизилась к температуре плавления оксида алюминия и составила 1950–2000°С. Произошла усадка продукта синтеза на 10%. Спеки представляют собой достаточно прочный материал. Нитрид алюминия, синтезированный при максимальной температуре, состоит из спеченных, хорошо сформированных, ограненных частиц (рис. 7). Форма и размер частиц образцов, полученных с мелким и крупным разбавителем, похожи. Обращает на себя внимание отсутствие субмикронных частиц. Для образцов, синтезированных при температуре 2000°C, характерно укрупнение зерен и изменение морфологии с образованием однотипных частиц AlN независимо от гранулометрического состава исходного разбавителя. Это свидетельствует о начальной стадии собирательной рекристаллизации нитрида алюминия, что подтверждается наличием хорошо сформированных тонких границ между сросшимися зернами (рис. 8). Параметр с для данных образцов имеет самые низкие значения. Таким образом, при температуре синтеза около 2000°С в процессе рекристаллизации AlN происходит активное внедрение примеси кислорода в структуру нитрида алюминия. Более высокое содержание примеси кислорода, растворенной в AlN, при использовании разбавителя с удельной поверхностью 3.5 м2/г обусловлено бóльшим содержанием поверхностного кислорода в исходном разбавителе. Таким образом, можно предположить, что при температурах синтеза 1460–1700°С внедрение атомов кислорода в решетку AlN происходит путем диффузии, а при температурах 1900–2100°С оксид алюминия растворяется в нитриде алюминия в процессе синтеза и рекристаллизации.
Рис. 6.
Морфология частиц нитрида алюминия, полученного из шихты, содержащей 18 мас. % алюминия: разбавитель – 1 (а), 2 (б).
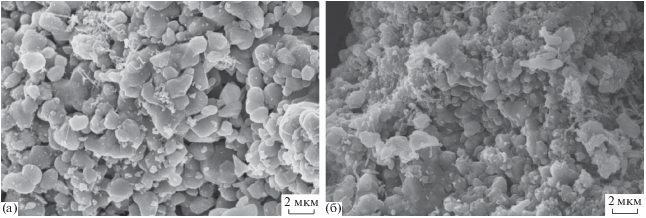
ЗАКЛЮЧЕНИЕ
Изучено влияние температуры синтеза на параметр с AlN. Установлено, что с ростом температуры синтеза параметр с уменьшается, а следовательно, содержание растворенного в решетке AlN кислорода возрастает. Таким образом, при СВС AlN в интервале температур 1460–2000°С происходит внедрение поверхностного кислорода в кристаллическую структуру AlN. Установлено, что в исследованном диапазоне температур снижение параметра с больше у нитрида алюминия, синтезированного при использовании разбавителя с более мелкими частицами. Это объясняется большей поверхностью взаимодействия Al2O3 с AlN и бóльшим содержанием поверхностной примеси кислорода в разбавителе. Для получения чистого по кислороду нитрида алюминия необходимо использовать компоненты шихты с низким содержанием примеси кислорода. Для снижения концентрации кислорода, растворенного в синтезированном нитриде алюминия, в шихту необходимо вводить добавки, которые способствуют восстановлению оксида алюминия или переводу поверхностного кислорода в газовую фазу.
Список литературы
Sheppard L.M. Aluminum Nitride: A Versatile but Challenging Material // Ceram. Bull. 1990. V. 69. № 11. P. 1801–1812.
Knudsen K. Aluminum Nitride // Am. Ceram. Soc. Bull.1995. V. 74. № 6. P. 97–101.
Slack G.A., Tanzilli R.A., Pohl R.O., Vandersande J.W. The Intrinsic Thermal Conductivity of AlN // J. Phys. Chem. Solids. 1987. V. 48. № 7. P. 641–647.
Sakai T. et al. Effects of the Oxygen Impurity on the Sintering on the Thermal Conductivity of AlN Polycrystal // Yogyo-Kyokai-Shi. 1978. V. 86. № 4. P. 174–1179.
Buhr H., Muller G., Wiggers H., Aldinger F., Roosen A. Phase Composition, Oxygen Content, and Thermal Conductivity of AlN(Y2O3) Ceramics // J. Am. Ceram. Soc. 1991. V. 74. № 4. P. 718–723.
Baranda P.S., Knudsen A.K., Rah E. Effect of Silica on the Thermal Conductivity of Aluminum Nitride // J. Am. Ceram. Soc. 1993. V. 76. № 7. P. 1761–1771.
Kuramoto N., Taniguchi H., Numata Y., Aso I. Sintering Process of Translucent AlN and Effect of Impurities on Thermal Conductivity of AlN Ceramics // Yogyo-Kyokai-Shi. 1985. V.93. № 9. P. 41–46.
Sakuma K., Okada A., Kawamoto H. Effect of Cation Impurities on Thermal Conductivity of Yttria-Dopped Aluminum Nitride // J. Mater. Synth. Process. 1998. V. 6. № 5. P. 315–321.
Watari Koji et al. Influence of Powder characteristics on Sintering Process and Thermal Conductivity of Aluminum Nitride Ceramics // J. Ceram. Soc. Jpn. 1995. V. 103. № 9. P. 891–900.
Watari Koji, Kawamoto Mitsuru, Ishizaki Kozo. Sintering Chemical Reactions to Increase Thermal Conductivity of Aluminum Nitride // J. Mater. Sci. 1991. V. 26. № 17. P. 4727–4732.
Kobayashi R., Moriya Y., Imamura M., Oosawa K., Oh-Ishi M. Relation between Oxygen Concentration in AlN Lattice and Thermal Conductivity of AlN Ceramics Sintered with Various Sintering Additives // J. Ceram. Soc. Jpn. 2011. V. 119. № 4. P. 291–294.
Goto Y., Ueno F., Kasori M., Horiguchi A. The Relation between Oxygen Content of Aluminum Nitride and Its Thermal Conductivity // Proc. An. Meet. Ceram. Soc. Jpn. 1990. P. 10.
Potter G.E., Knudsen A.K., Tou J.C., Choudhury A. Measurement of the Oxygen and Impurity Distribution in Polycrystalline Aluminum Nitride with Secondary Ion Mass Spectrometry // J. Am. Ceram. Soc. 1992. V. 75. № 12. P. 3215–3224.
Kumashiro Yukinobu. Electric Refractory Materials. ISBN 9780824700492 CRC Press. Published August 24. 2000. 776 p.
Carbide, Nitride and Boride Materials Synthesis and Processing / Ed. Weimer A.W. Chapman & Hall, 1997. 671 p.
Pathak Lokesh Chandra, Ray Ajoy Kumar, Das Samar, Sivaramakrishnan C.S., Ramachandrarao P. Carbothermal Synthesis of Aluminum Nitride Powders // J. Am. Ceram. Soc. 1999. V. 82. № 1. P. 257–260.
Takayuki Ide, Katsutoshi Komeya, Takeshi Meguro, Junichi Tatami. Synthesis of AlN Powder by Carbothermal Reduction-Nitridation of Various Al2O3 Powders with CaF2 // J. Am. Ceram. Soc. 1999. V. 82. № 11. P. 2993–2998.
Kasori Mitsuo, Ueno Fumio. Thermal Conductivity Improvement of YAG Added AlN Ceramics in the Grain boundary Elimination Process // J. Eur. Ceram. Soc. 1995. V. 15. P. 435–443.
Slack G.A. Nonmetallic Crystals with High Thermal Conductivity // J. Phys. Chem. Solids. 1973. V. 34. P. 321–335.
Закоржевский B.B., Ковалев И.Д., Мухина Н.И. Закономерности структуро- и фазообразования при синтезе композиций AlN–Al2O3–Y2O3 в режиме горения // Новые огнеупоры. 2020. № 9. С. 32–36. https://doi.org/10.17073/1683-4518-2020-9-32-36
Дополнительные материалы отсутствуют.
Инструменты
Неорганические материалы