Неорганические материалы, 2021, T. 57, № 12, стр. 1380-1389
Получение крупнокристаллических сплавов на основе вольфрама методом бестигельной электронно-лучевой плавки
Н. П. Бобырь 1, А. В. Голубева 1, *, Н. Н. Преснякова 1, В. А. Степанов 2, Д. И. Кочетов 2, Р. А. Федосеев 2, В. А. Барсук 3, А. А. Медников 1, А. В. Спицын 1
1 Национальный исследовательский центр “Курчатовский институт”
123182 Москва, пл. Академика Курчатова, 1, Россия
2 Научно-исследовательский институт научно-производственное объединение “ЛУЧ”
142100 Московская обл., Подольск, ул. Железнодорожная, 24, Россия
3 ГНЦ РФ Троицкий институт инновационных и термоядерных исследований
108840 Москва, Троицк, ул. Пушковых, вл. 12, Россия
* E-mail: Golubeva_AV@nrcki.ru
Поступила в редакцию 06.04.2021
После доработки 16.08.2021
Принята к публикации 18.08.2021
Аннотация
В работе методом бестигельной электронно-лучевой плавки создавались крупнокристаллические сплавы вольфрама с 1, 3, 5 ат. % легирующих добавок – Re, Mo, Та, Cr, Fe, V. Характеристики полученных слитков исследовались путем взвешивания, химического анализа, сканирующей электронной микроскопии, энергодисперсионного анализа. Установлено, что полученные сплавы вольфрама с тугоплавкими Re, Mo, Та состоят из крупнокристаллических зерен с размерами >1 см. Легирующая добавка равномерно распределена в объеме сплава. В объеме материалов практически отсутствуют полости. Напротив, сплавы вольфрама с легкоплавкими Cr, Fe, V содержат большое количество полостей размером 0.5 мкм–2 мм. Установлено, что легирующие легкоплавкие элементы находятся в вольфрамовой матрице в виде вкраплений. Показано, что выбранный метод подходит для получения крупнокристаллических сплавов вольфрама с тугоплавкими металлами (Re, Mo, Та) и неприменим для производства крупнокристаллических сплавов W c легкими компонентами (Cr, Fe, V).
ВВЕДЕНИЕ
Вольфрам – самый тугоплавкий материал в мире. Вольфрамовая облицовка будет использована в строящемся термоядерном реакторе ИТЭР для защиты стенок камеры реактора от разрушения при контакте с горячей плазмой. Существенными недостатками вольфрама являются его хрупкость при комнатной температуре, а также интенсивное окисление при температуре выше 573°С [1] в контакте с воздухом или водой, приводящее к быстрому разрушению материала. Эти проблемы предлагают решать легированием вольфрама различными элементами [2].
Ta и Re – два ближайших к вольфраму элемента Периодической системы Менделеева. Оба этих материала тугоплавки и обладают плотностью, близкой к плотности вольфрама (см. табл. 1). Именно их в первую очередь рассматривают в качестве легирующих элементов для вольфрама в термоядерных реакторах. Помимо того, что добавка рения или тантала приводит к улучшению обрабатываемости вольфрама, эти элементы, а также осмий, в любом случае будут образовываться в термоядерных установках в результате трансмутации вольфрама под действием нейтронного облучения [3].
Таблица 1.
Температуры плавления и кипения вольфрама и некоторых других металлов
Металл | V | Cr | Fe | Mo | Ta | W | Re |
---|---|---|---|---|---|---|---|
Атомный номер | 23 | 24 | 26 | 42 | 73 | 74 | 75 |
Температура плавления, °C | 1910 | 1907 | 1539 | 2623 | 3020 | 3422 | 3182 |
Температура кипения, °C | 3407 | 2671 | 3070 | 4639 | 6100 | 5555 | 5596 |
Плотность, г/см3 | 6.11 | 7.19 | 7.87 | 10.22 | 16.65 | 19.25 | 21.02 |
Для термоядерных приложений имеет смысл рассматривать те легирующие добавки, которые отвечают критерию сниженной активации под облучением термоядерными нейтронами. Этому требованию, помимо W, отвечают C, O, Si, Fe, Mn, Ta, V, Cr, Ti, Ga, Се. Прочие элементы, в частности Ni, Al, Nb, Mo, в термоядерных установках желательно не использовать или использовать ограниченно [4]. Тем не менее, некоторые авторы не исключают возможность использования молибдена в термоядерных реакторах [5], в том числе для легирования вольфрама [6].
Легирование вольфрама сопряжено со значительными техническими сложностями из-за его тугоплавкости. Свойства вольфрама и ряда возможных легирующих элементов приведены в табл. 1. Температура плавления вольфрама превышает не только температуру плавления всех других металлов, но также температуру кипения хрома, железа и ванадия. Поэтому получение бинарных сплавов W–Fe, W–Cr и W–V представляет собой весьма сложную задачу.
Свойства металла или сплава зависят не только от его состава. Микроструктура сплава, оказывающая критически важное влияние на механические свойства, весьма существенно зависит от типов и количества примесей, условий плавления и остывания сплава, термообработки после плавки и специфической истории каждого образца (механическая обработка, резка, прогрев).
Идеальным объектом для сравнительных исследований свойств вольфрама и легированного вольфрама является монокристалл – материал, в котором плотности точечных дефектов, дислокаций, граней кристаллитов на единицу объема на порядки меньше, чем в поликристаллическом образце. В этом случае различиями в микроструктуре можно пренебречь и сосредоточиться на том, как именно наличие конкретного легирующего компонента влияет на свойства вольфрама на макро- и микроуровнях.
Наиболее распространенные способы получения сплавов вольфрама – литье, порошковая металлургия, плавка в электронно-лучевых и дуговых плавильных печах [7, 8].
Недостатками литья являются неоднородность химического состава в пределах одного кристалла и в различных зонах слитка, вероятная гравитационная ликвация [9], а также неизбежное загрязнение сплава материалом контейнера (в случае вольфрама контейнером мог бы быть графит).
Применение порошковой металлургии практически неизбежно, если соединить металлы путем литья невозможно, например при производстве W–Cr-сплавов [10]. Весьма частым недостатком метода является снижение плотности сплава за счет полостей в объеме.
Продукты плавки в дуговой печи имеют крупнокристаллическую структуру, однако отличаются повышенной хрупкостью из-за выделения примесей по граням кристаллитов в виде относительно толстых пленок оксидов, карбидов, нитридов [7, 11].
Плавка в электронно-лучевой печи осуществляется в высоком вакууме. В этих условиях происходит очищение вольфрама от большинства примесей, в т. ч. О, N, C, H, Fe, Cu, Ni, Mn, Co, невозможное при плавке другими методами. Существенное достоинство этого метода – возможность создания очень узкой области нагрева путем фокусирования пучка электронов [8]. По причине высокой чистоты материала после электронно-лучевой плавки кристаллиты W весьма крупные, что существенно снижает его пластичность.
Бестигельная зонная плавка осуществляется путем локального нагрева перемещаемой относительно зоны плавки заготовки электронным пучком. Плавка в вакууме и отсутствие тигля позволяют достичь высокой чистоты переплавляемого тугоплавкого материала.
Цель данной работы – получение крупных кристаллов вольфрама и его сплавов для последующего исследования влияния легирования на свойства сплава как материала термоядерного реактора.
Требовалось создать славы W–Re, W–Ta, W–Mo, W–Fe, W–Cr, W–V, удовлетворяющие следующим условиям:
– фазовое состояние – раствор легирующего элемента в объеме материала;
– равномерное распределение легирующего элемента по объему материала;
– отсутствие или минимальное количество пор с размером ≥20 нм;
– суммарная концентрация примесей, помимо легирующей добавки, не выше 0.1 ат. %.
Для достижения заявленной цели в данной работе был выбран метод бестигельной зонной плавки.
ЭКСПЕРИМЕНТАЛЬНАЯ ЧАСТЬ
Изготовление сплавов вольфрама осуществлялось в ФГУП “НИИ НПО “ЛУЧ” (г. Подольск, Московская область). Технология получения слитков включала в себя три основных этапа:
1) изготовление спрессованных и спеченных штабиков из вольфрамового порошка;
2) переплав штабика, получение вольфрамового поликристаллического прутка;
3) выращивание крупнокристаллического слитка или вторичный (в ряде случаев третий) переплав легированного поликристаллического прутка для получения однородного слитка.
Изготовление штабиков. В качестве исходного материала использовался порошок вольфрама марки ПВВ ТУ 48-19-72-92. При изготовлении штабиков выполняли определенную последовательность технологических операций.
1. Исходный порошок вольфрама проходил операцию вакуумной сушки в вакуумных сушильных шкафах ШСВ-65В.
2. Формование штабиков проводилось методом гидростатического обжатия порошка, помещенного в эластичную оболочку, в установке гидростатического прессования длинномерных заготовок ХИП 150×800-150. Пластифицирующие добавки при операции формования не применялись. Порошок засыпался в эластичную оболочку и прессовался в гидростате при давлении 150 МПа в течение 3–5 мин. Спрессованные штабики представляли собой цилиндры с определенными геометрическими и массовыми характеристиками.
3. Далее штабики подвергались сушке с обезгаживанием в вакуумных сушильных шкафах типа ШСВ-65В при температуре 300°С и давлении от 20 до 27 Па.
4. Заключительным этапом производства штабиков являлось высокотемпературное спекание в вакуумной печи сопротивления СШВЭ-1.2,5/25. Штабики помещали в электропечь, объем откачивали, а затем заполняли смесью Ar и Н2 (содержание водорода от 5 до 7 об. %) до давления 27 Па. После этого температуру в печи поднимали до 900°С и выдерживали в течение 2 ч. Затем температуру увеличивали до максимальной и выдерживали 1–2 ч. Далее печь охлаждалась до комнатной температуры. Режим отжига подобран таким образом, чтобы избежать образования закрытой пористости в штабиках.
В результате проведенных ранее исследований для вольфрама были выбраны следующие параметры спекания: температура спекания в диапазоне 1700–2000°С, скорость подъема и снижения температуры 200–500°С/ч, время выдержки при максимальной температуре 1 ч. Такой режим спекания позволяет получать штабики с относительной плотностью 75–80%.
Исходный порошок вольфрама одной марки, но разных производителей может иметь различные свойства. В данной работе проводилось сравнение качества плавки штабиков, изготовленных из порошков марки ПВВ ТУ 48-19-72-92 двух производителей: ОАО “Победит” (г. Владикавказ) и ЗАО “Компания “ВОЛЬФРАМОФФ”. В табл. 2 представлен химический состав исходных порошков.
Таблица 2.
Химический состав исходных порошков вольфрама
Элемент | Химический состав, % (не более) | |
---|---|---|
ОАО “Победит” | АО “Компания “ВОЛЬФРАМОФФ” | |
Fe | 0.005 | 0.001 |
Al | 0.001 | 0.001 |
Si | 0.002 | 0.001 |
Ca | 0.002 | 0.002 |
Ni | 0.003 | 0.001 |
P | 0.001 | 0.001 |
S | 0.002 | 0.002 |
Mo | 0.02 | 0.005 |
C | 0.003 | 0.002 |
As | 0.002 | 0.001 |
K | 0.005 | 0.003 |
Na | 0.005 | 0.002 |
O2 | 0.02 | 0.3 |
На рис. 1 представлены результаты седиментационного анализа исходных порошков, полученные с применением фотоседиментометра ФСХ-6, позволившего определить распределение частиц порошка по размерам в процентном содержании, а также средний размер частиц и удельную поверхность порошковых материалов.
Рис. 1.
Распределение по размерам частиц вольфрамового порошка: а – ОАО “Победит”, б – ЗАО “Компания “ВОЛЬФРАМОФФ”.
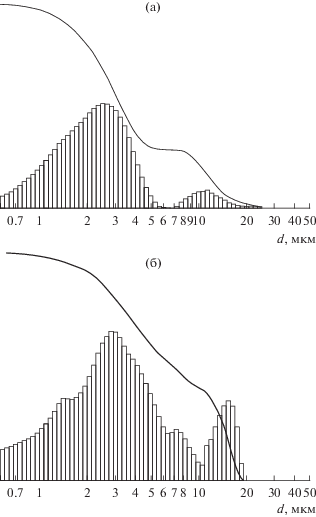
В порошке вольфрама производства ОАО “Победит” содержится 70% частиц менее 5 мкм, в порошке вольфрама производства ЗАО “Компания “ВОЛЬФРАМОФФ” таких частиц 60%, т.е. последний порошок в целом несколько крупнее.
Были проведены эксперименты по изменению режима спекания штабиков. В табл. 3 представлены параметры ранее применявшегося (режим 1) и разработанного в данной работе (режим 2) режимов спекания, в табл. 4 – свойства штабиков, полученных в этих двух режимах из порошков двух производителей.
Таблица 4.
Свойства спеченных штабиков W после спекания
Режим | 1 | 2 | ||
---|---|---|---|---|
Производитель | ОАО “Победит” | ЗАО “Компания “ВОЛЬФРА-МОФФ” | ОАО “Победит” | ЗАО “Компания “ВОЛЬФРА-МОФФ” |
Относительная плотность, % | 78.8 | 80.2 | 59.3 | 60.7 |
Закрытая пористость, % | 3.5 | 2.8 | 0 | 0 |
Результат первичной плавки | Малоинтенсивный вынос металла, слабое кипение зоны расплава | Среднеинтенсивный вынос металла, слабое кипение зоны | Малоинтенсивный вынос металла, кипение зоны расплава отсутствует | Вынос металла и кипение зоны расплава отсутствуют |
На рис. 2 показан штабик вольфрама, полученный при спекании в режиме 2.
Вольфрам при комнатной температуре хрупок. Если пористость спеченного штабика невысока, велика вероятность образования трещин и сколов при механической обработке. Если в объеме штабика присутствует достаточное количество микрополостей, развивающаяся трещина как правило прекращает свой рост, когда достигает полости. Было установлено, что штабики, спеченные в режиме 2, легче обрабатываются на токарном станке, сохраняя целостность, чем спеченные по первому режиму.
При изготовлении контрольных образцов штабиков выявлены некоторые особенности.
1. Снижение температуры спекания, а также скорости нагрева и охлаждения в процессе спекания приводит к уменьшению относительной плотности и практически нулевой закрытой пористости штабиков, что способствует возможности дегазации штабиков через открытую пористость в процессе плавки в условиях градиента температуры по оси штабика и практически исключает кипение зоны расплава и ее проливы. Это позволяет снизить потери материала в процессе плавки и исключить выход из строя плавильной установки вследствие интенсивных газовых выбросов из расплава.
2. Штабики вольфрама с низкой относительной плотностью легче подвергаются механической обработке без разрушения.
3. Понижение температуры выдержки в аргоно-водородной среде с последующим высокотемпературным спеканием в вакууме способствует увеличению времени эксплуатации тепловых зон вакуумных печей, снижению загрязненности атмосферы в печи и, как показали результаты плавки штабиков, не снижает эффекта восстановления вольфрама. Последующая выдержка в вакууме, видимо, способствует удалению остаточных газов из открытых пор, что также повышает качество плавки.
4. Незначительное различие в размерах частиц исходного порошка вольфрама не влияет на качество плавки при одинаковых технологических приемах производства штабиков.
Переплав и легирование. Для получения нелегированных поли- и крупнокристаллических слитков вольфрама использовали нелегированные штабики. Сплавы изготовляли из штабиков, легированных соответствующей проволокой. Для этого на боковой поверхности вольфрамового штабика по всей его длине фрезеровали рассчитанное количество пазов шириной 2 мм, в которые закладывали проволоку-лигатуру диаметром 2 мм заданной массы. Осуществлялось легирование 1, 3, 5 ат. % Cr, V, Fe, Ta, Mo, Re. Переплав штабика осуществляли на установке бестигельной зонной плавки с электронно-лучевым нагревом. Схема ростовой камеры этой установки представлена на рис. 3.
Рис. 3.
Ростовая камера с нагревательным узлом: 1 и 3 – нижний и верхний медные экраны, 2 и 11 – верхняя и нижняя водоохлаждаемые станины катодного узла, 4 – вольфрам-ториевый катод, 5 и 9 – верхний и нижний штоки, 6 – расплавленная зона, 7 – электронный пучок, 8 – корпус установки, 10 – водоохлаждаемая проставка, 12 – водохлаждаемые токовводы.
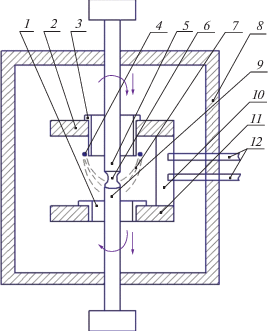
Нижний 1 и верхний 3 экраны, выполненные из бескислородной меди, служат для формирования тепловых условий и фокусировки электронного пучка в расплавленной зоне 6. Водоохлаждаемые по внутренним полостям верхняя 2 и нижняя 11 станины, выполненные из бескислородной меди, служат опорами экранам и формируют конструкцию нагревательного узла. Верхний 5 и нижний 9 штоки установлены соосно и являются основными элементами кинематической системы, приводящими во вращательное и поступательное движение закрепленные на них заготовку и затравочный монокристалл. Расплавленная зона формируется между расположенными друг относительно друга торцами заготовки и затравочного кристалла.
Переплавляемый штабик устанавливали в ростовую камеру на верхний шток. На нижнем штоке крепили в патроне поликристаллический стержень диаметром 16 мм, служащий приемником вольфрама, стекающего в процессе переплава с нижнего торца штабика на верхний торец стержня. Процесс переплава вели при остаточном давлении р ≤ 5 × 10–3 Па. Варьируя скорости перемещения верхнего и нижнего штоков, добивались того, чтобы остаточное давление в камере не превысило указанную величину вследствие высвобождения газа из полостей в процессе переплава.
В начале процесса переплава формировали единую расплавленную зону, близкую по форме к однополостному гиперболоиду. С учетом разности в значениях плотности штабика и прутка, скорость перемещения верхнего штока была выше, чем нижнего, на величину, пропорциональную разности плотностей, и составляла для верхнего штока 5–6, для нижнего – 3–4 мм/мин. Скорость вращения нижнего и верхнего штоков изменяли в диапазоне 8–12 об./мин. Мощность, выделяемая в расплавленной зоне, составляла от 10 до 14 кВ, анодный ток варьировался в пределах от 0.9 до 1.3 А, высокое напряжение – от 10 до 14 кВ. Диаметр полученного прутка составлял 16–18 мм, длина – 250–300 мм. Полученный пруток обтачивали на токарном станке по всей длине до диаметра 16 мм. Для облегчения процесса затравления на нижнем торце заготовки протачивали конус по образующей длиной 5–10 мм и конусностью от 10° до 15°. Диаметр заготовки был на 10–15% меньше или равен диаметру выращиваемого слитка. Это требование диктуется условием реализации механизма роста по методу “поджима зоны” как наиболее устойчивого процесса роста крупнокристаллических сплавов в методе бестигельной зонной плавки с электронно-лучевым нагревом.
Далее заготовка проходила операции обезжиривания, мойки в проточной и деионизованной воде, сушки в сушильном шкафу.
Переплавка и получение крупнокристаллических слитков. Переплавка с целью получения крупнокристаллических слитков осуществлялась в ростовой камере, схема которой приведена на рис. 3.
Заготовка устанавливается на цанговом концевике верхнего штока ростовой камеры, нижний торец заготовки центрировали относительно верхнего экрана и тестировали относительно вращения и перемещения.
Затравочный кристалл (рис. 4) с заданной ориентацией и углом отклонения оси роста от кристаллографической оси не более чем на 3°–4° устанавливали на молибденовом цилиндрическом основании нижнего штока с последующей проверкой приводов на вращение и перемещение. Торец затравочного кристалла подвергали травлению в течение 10 мин в смеси фтористоводородной, серной и азотной кислот в отношении 3 : 2 : 1.
Перед закрытием ростовой камеры на вакуумную откачку нижний торец заготовки и верхний торец затравочного кристалла взаимно центрировали для предотвращения асимметрии расплавленной зоны относительно общей вертикальной оси штоков и экранов катодного узла.
После завершения процедуры установки ростовая камера герметизировалась и откачивалась до давления 5 × 10–3 мм рт. ст. По достижении этого давления включали приводы вращения и перемещения верхнего и нижнего штоков, а заготовку и затравочный кристалл устанавливали в зоне между верхней и нижней станинами катодного узла на расстоянии 8–15 мм друг от друга.
Нагрев и расплавление заготовки и затравочного кристалла осуществляли их бомбардировкой сфокусированным ускоренным электронным пучком, испускаемым катодом, нагретым до температуры 1500–1700°С. Катод находился под отрицательным потенциалом 10–15 кВ, а заготовка и затравка – под потенциалом земли. Анодный ток составлял 0.8–1.5 А в зависимости от температуры плавления выращиваемого материала и диаметра растущего слитка. Регулируя ток накала катода, устанавливали последовательные значения высокого напряжения анодного тока, осуществляя процесс постепенного нагрева загрузки и затравочного кристалла при заданной мощности и постоянном контроле остаточного давления в ростовой камере. В процессе нагрева и плавления остаточное давление в камере не должно превышать 5 × 10–5 мм рт. ст.
Процесс получения поликристаллического слитка в результате переплава штабика отличался от процесса роста крупнокристаллического слитка значениями скоростей роста и вращения верхнего и нижнего штоков. В случае неоднородного распределения легирующей примеси по длине и диаметру необходим был еще один переплав поликристаллического слитка для достижения гомогенного состояния.
На рис. 5 представлен изготовленный крупнокристаллический слиток вольфрама с затравочным кристаллом с ориентацией 〈111〉.
Исследование свойств полученных слитков. Для проведения аттестации (выявления дефектов кристаллической структуры) полученных слитков сплавов вольфрама их подвергали электрохимическому травлению в 3%-ном водном растворе NаОН. Травление проводили на посту электрохимического травления в специальной ванне, установленной в вытяжном шкафу. Слиток являлся анодом, стенки ванны – катодом. Плотность тока при электрохимическом травлении вольфрама не должна превышать 0.5–0.7 А/см2, напряжение устанавливается ∼12 В. Температура электролита была не более 40 ± 5°С, длительность травления составляла 1–1.5 мин до появления матовых полос травления, характерных для ориентации выращенного слитка. После травления слиток извлекали из ванны и для удаления продуктов электролиза промывали в проточной воде, используя кальцинированную соду.
С целью контроля качества слитков проводили:
внешний осмотр на наличие объемных дефектов 3-го порядка (пор, трещин, сколов, раковин и т.д.); измерение геометрии слитка на предмет соответствия требованиям ТУ; контроль отклонения оси роста от кристаллографического направления методом рентгеноструктурного анализа; измерения химического состава слитков; исследование микроструктуры и нанопористости слитков.
РЕЗУЛЬТАТЫ И ОБСУЖДЕНИЕ
Химический состав. Для определения содержания примесей в образцах применяли следующие методы: высокотемпературной газовой экстракции (для определения углерода, водорода, азота и кислорода), атомно-эмиссионной спектрометрии с индуктивно-связанной плазмой (для определения рения), искровой масс-спектрометрии (для определения остальных примесей). Результаты химического анализа состава материала на примере сплава W–Re иллюстрирует табл. 5.
Таблица 5.
Химический состав сплава W, легированного 5 ат. % Re
Элемент | Содержание, частиц на миллион |
---|---|
H | 4 |
C | 17 |
O | 100 |
N | 6 |
Ta | 300 |
Re | 6.0% |
W | Oснова |
Na, Mg, Si, Pm S, K, V, Cr | <0.01 |
Al | 0.05 |
Zn, Zr, Cd, Sn | <0.05 |
Fe | 0.1 |
Ni, Cu, | <0.02 |
Pb, Bi | <0.2 |
Таким образом, требование высокой чистоты получаемых сплавов (суммарное содержание примесей <0.1 ат. %) выполнено. Данный результат является ожидаемым, т. к. для производства сплавов использовались материалы с малым содержанием примесей и в процессе бестигельной электронно-лучевой плавки происходило дополнительное очищение материала от примесей.
Пористость. Методом электроэрозионной резки из торцевых областей слитков были вырезаны образцы 10 × 10 × 1 мм. На поверхностях образцов из сплавов W–V, W–Cr, W–Fe с содержанием легирующих добавок 1, 3, 5 ат. % установили наличие каверн с размерами до 1.5 мм (рис. 6). Расчет плотности этих сплавов после взвешивания показал значение 60–80% от теоретической плотности вольфрама, что говорит о высокой пористости слитков.
Образцы W и сплавов W–Mo, W–Re, W–Ta при визуальном осмотре выглядели монолитными. Взвешивание с последующим расчетом показало, что плотности изготовленных сплавов вольфрама с молибденом, танталом и рением соответствуют ожидаемым, что говорит о низком содержании пор в материале. После протравливания образцов в смеси азотной и плавиковой кислот можно четко видеть границы зерен. На примере сплава W–Mo это демонстрирует рис. 7, на котором представлены фотографии сплавов вольфрама с 1, 3 и 5% Mo. С ростом содержания молибдена в сплаве хрупкость материала возрастает, и при содержании 5% Мо образцы легко разламываются по границе зерен. Как можно видеть из рис. 7, зерна кристаллитов весьма крупные, характерный размер зерна превышает размер образца (10 мм). Рентгенографический анализ поверхностей образцов сплавов W–Re, W–Mo, W–Ta подтвердил, что данные материалы являются крупнокристаллическими.
Для исследования нанопористости из слитков W и сплавов W–Mo, W–Re, W–Ta были приготовлены образцы в виде дисков толщиной ~1 мм и диаметром 15 мм. Поверхности образцов визуально не содержали пор. Диски были подвергнуты травлению в смеси азотной, серной и плавиковой кислот, промыты в проточной и деонизованной воде. Далее образцы подвергли излому. Исследование нанопористости на свежих изломах дисков проводили на сканирующем электронном микроскопе MIRA 3 LMU. Содержание легирующих элементов в сплавах определяли методом рентгенофлуоресцентного анализа на спектрометре СУР-02 РЕНОМ ФВ. Погрешность метода составляла ±10%. Для примера на рис. 8 представлено изображение излома сплава W–5Ta. Нанопоры размером ≥20 нм в этих слитках не обнаружены.
Исследование шлифов слитков W–5Cr, F–5Fe, W–5V на растровом электронном микроскопе (см. рис. 9) выявило наличие пор с размером от единиц до сотен мкм в количестве более 1000 на мм2. Худший результат демонстрирует микрофотография слитка W–V: фактура поверхности напоминает губку. Более ясное представление о пористости материала дает микрофотография сечения сплава W–5V, вырезанного при помощи сфокусированного ионного пучка (см. рис. 10).
Рис. 9.
Микроструктура поперечных шлифов сплавов, изображения получены на растровом электронном микроскопе: W–5Cr (а), W–5Fe (б), W–5V (в), W–5Ta (г).
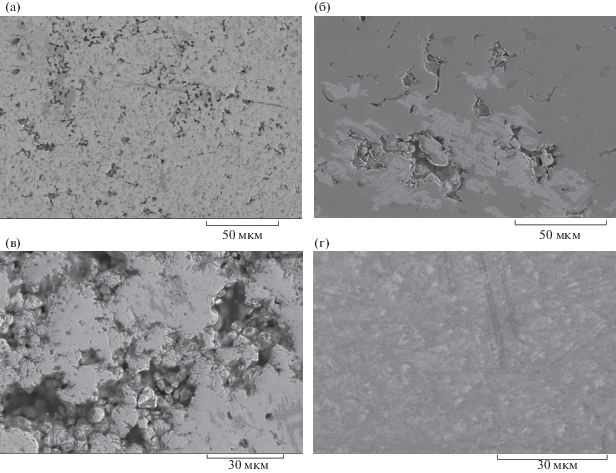
В отличие от сплавов W c Cr, Fe, V поверхность сплавов W–Ta не содержит полостей крупнее 1 мкм (рис. 9г).
Таким образом, с тяжелыми примесями – Mo, Ta, Re – получены хорошие крупнокристаллические сплавы с весьма низкой плотностью пор, тогда как материалы, полученные при легировании вольфрама легкими элементами – Fe, Cr, V, содержат большое количество полостей. Последнее объясняется тем, что температуры кипения железа, хрома и ванадия ниже температуры плавления вольфрама и при нагревании заготовки выше температуры плавления легирующих добавок происходит закипание и высвобождение этих добавок в газообразной форме.
Равномерность распределения легирующей добавки была исследована методом энергодисперсионной спектроскопии. Полученные карты распределения примесей приведены на рис. 11. Выявленная неоднородность распределения легирующей добавки в слитках W–5Cr, W–5Fe, W–5V свидетельствует о том, что эти материалы представляют собой матрицу вольфрама с вкраплениями введенных добавок. Таким образом, требование создать гомогенные крупнокристаллические сплавы не достигнуто для добавок Cr, Fe, V. Напротив, в материалах W–Mo, W–Ta, W–Re легирующая добавка равномерно распределена по объему. Типичное распределение тугоплавкой легирующей добавки в сплаве вольфрама иллюстрирует рис. 11г.
Рис. 11.
Распределение легирующей добавки по сечению материала: W–5% Cr (а), W–5% Fe (б), W–5% V (в), W–5Ta (г).
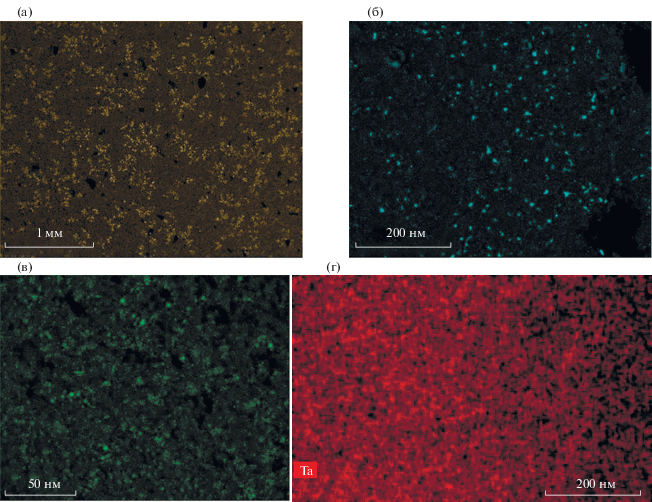
Таким образом, использованный метод подходит для создания крупнокристаллических сплавов вольфрама с тугоплавкими добавками Mo, Re, Ta, но непригоден в случае легкоплавких добавок Fe, Cr, V.
ЗАКЛЮЧЕНИЕ
Для производства крупнокристаллических сплавов вольфрама был применен метод беcтигельной электронно-лучевой плавки. Данным методом удалось получить крупнокристаллические слитки W и сплавов W–Re, W–Ta, W–Mo с содержанием легирующей добавки 1, 3, 5 ат. % и низким содержанием примесей. В полученных материалах легирующие добавки равномерно распределены по объему. Размер зерна в перечисленных сплавах превышает 1 см.
Метод бестигельной электронно-лучевой плавки оказался непригодным для производства крупнокристаллических сплавов вольфрама с легкоплавкими добавками Fe, Cr, V, поскольку полученные материалы содержат большое количество полостей от микро- до миллиметрового размера, а легирующие элементы присутствуют в виде вкраплений.
Список литературы
Иванов В.Е., Нечипоренко Е.П., Ефименко Л.Н., Юр-ченко М.И. Защита вольфрама от окисления при высоких температурах. М.: Атомиздат, 1968.
Голубева А.В., Черкез Д.И. Накопление водорода в разработанных для термоядерных установок сплавах вольфрама (обзор) // Вопросы атомной науки и техники. Серия термоядерный синтез. 2018. Т. 41. Вып. 4. С. 26–37.
Qiang Zhao, Zheng Zhang, Mei Huang, Xiaoping Ouyang. Effects of Transmutation Elements in Tungsten // Comput. Mater. Sci. 2019. V. 162. P. 133–139.
Колотов В.П. Теоретические и экспериментальные подходы к решению задач активационного анализа, гамма-спектрометрии и создания малоактивируемых материалов: Дис. … докт. хим. наук. 2007.
Kurishita H., Kitsunai Yu., Shibayama T., Kayano H. et al. Development of Mo Alloys with Improved Resistance to Embrittlement by Recrystallization and Irradiation // J. Nucl. Mater. 1996. V. 233–237. P. 557–564.
Diyou Jiang, Qing Zhou, Li Xue, Tao Wang et al. First-Principles Study the Phase Stability and Mechanical Properties of Binary W-Mo Alloys // Fusion Eng. Des. 2018. V. 130. P. 56–61.
Зеликман А.Н., Никитина Л.С. Вольфрам. М.: Металлургия, 1978.
Ратников Д.Г. Бестигельная зонная плавка. М.: Металлургия, 1986. 224 с.
Черепахин А.А., Колтунов И.И., Кузнецов В.А. Материаловедение. М.: КноРус, 2011.
Suresh Telu, Patra A., Sankaranarayana M., Mitra R. et al. Microstructure and Cyclic Oxidation Behavior of W–Cr Alloys Prepared by Sintering of Mechanically Alloyed Nanocrystalline Powders // Int. J. Refract. Met. Hard Mater. 2013. V. 36. P. 191–203.
Зеликман А.Н., Коршунов Б.Г. Металлургия редких металлов. М.: Металлургия, 1991.
Дополнительные материалы отсутствуют.
Инструменты
Неорганические материалы