Неорганические материалы, 2021, T. 57, № 2, стр. 137-143
Магниетермическое получение порошков хрома
В. Н. Колосов 1, *, М. Н. Мирошниченко 1, В. М. Орлов 1
1 Институт химии и технологии редких элементов и минерального сырья им. И.В. Тананаева – обособленное подразделение ФИЦ “Кольский научный центр Российской академии наук”
184209 Мурманская обл., Апатиты, Академгородок, 26а, Россия
* E-mail: v.kolosov@ksc.ru
Поступила в редакцию 04.08.2020
После доработки 31.08.2020
Принята к публикации 02.09.2020
Аннотация
Исследован процесс получения порошков хрома восстановлением оксидных соединений Cr2O3 и MgCr2O4 парами магния в интервале температур 700–800°С при остаточном давлении в реакторе 5–20 кПа. При восстановлении хромита MgCr2O4 получены порошки хрома с удельной поверхностью на уровне 34 м2/г. Порошки характеризуются мезопористой структурой.
ВВЕДЕНИЕ
Порошки хрома используются для получения металлокерамик, представляющих собой композиты с высокой электропроводностью, термической стабильностью и коррозионной стойкостью при высоких температурах [1], изготовления высокочистых мишеней для нанесения покрытий различного функционального назначения [2–5] и производства проводящих паст для электроники [6]. В промышленном масштабе порошки хрома получают металлотермическим (Al, Ca) или электролитическим восстановлением оксидных соединений (Cr2O3, K2CrO4) [7–11]. Полученный после восстановления продукт является хрупким (в частности, электролитический хром загрязнен водородом [11]) и может быть легко размолот. В результате измельчения обычно получают порошок с частицами микронных размеров [9].
Наряду с производством микрокристаллического хрома существует ряд методов получения наноразмерного материала. Среди них можно выделить длительный (40–70 ч) высокоэнергетический размол промышленного микрокристаллического порошка хрома [12], магнетронное распыление металла [13], восстановление нитрата хрома в жидких средах [14, 15], дуговой разряд в смеси водорода и аргона с использованием в качестве анода чистого металлического хрома [16], термическое испарение металла [17], термолиз карбенового комплекса Фишера [18] и другие методы [19–21]. Образующийся на поверхности металла очень тонкий (приблизительно 1 нм) пассивирующий оксид [13] позволяет работать с порошком на воздухе. Наноразмерные структуры на основе хрома используют при производстве оптоэлектронных и химических датчиков и в качестве катализаторов [13–15, 22]. Кроме того, они являются перспективными материалами спинтроники [16, 17, 22]. Для катализаторов и ряда других применений представляют интерес порошки хрома с высокой удельной поверхностью. Ранее было показано, что перспективным способом получения порошков других металлов подгруппы хрома (W, Mo) с удельной поверхностью до 20 м2/г является восстановление парами магния их оксидных соединений [23, 24].
Цель настоящей работы – исследование возможности получения порошков хрома с развитой поверхностью восстановлением парами магния его оксидных соединений и изучение характеристик порошков в зависимости от состава прекурсора и условий восстановления.
ЭКСПЕРИМЕНТАЛЬНАЯ ЧАСТЬ
В качестве прекурсоров использовали Cr2O3 (“ч.”) и хромит MgCr2O4, который синтезировали в виде порошка методом спекания Cr2O3 (“ч.”) с MgCO3 (“х. ч.”). Аппаратура, методика получения и исследования порошков аналогичны использованным ранее [23]. Тигель с магнием (М95) устанавливали на дно реакционного стакана. Навеску прекурсора массой 5 г загружали в металлические тигли, которые устанавливали над емкостью с магнием. Реакционный стакан закрывали крышкой, в центре которой имелось отверстие для чехла термопары. Сборку помещали в реторту из нержавеющей стали, которую герметизировали, вакуумировали, заполняли инертным газом и нагревали до требуемой температуры при закрытой крышке реакционного стакана. Процесс вели в температурном интервале 700–800°C и при остаточном давлении аргона в реторте 5–20 кПа. Продукты восстановления обрабатывали 30%-ным раствором азотной кислоты (“х. ч.”) для удаления оксида магния. Порошок хрома отмывали дистиллированной водой до нейтральной реакции раствора и сушили на воздухе при температуре 80°C. Рентгенофазовый анализ (РФА) продуктов проводили на дифрактометре SHIMADZU XRD-6000. Удельную поверхность и пористость порошков измеряли методами БЭТ и BJH на приборе TriStarII 3020 V1.03. Средний размер частиц порошка оценивали в предположении, что они имеют сферическую форму, по формуле
где SБЭТ – удельная поверхность порошка, ρ – плотность хрома. Морфологический анализ порошков проводили с помощью сканирующего электронного микроскопа SEM LEO-420.РЕЗУЛЬТАТЫ И ОБСУЖДЕНИЕ
Реакции восстановления Cr2O3 и MgCr2O4 магнием являются экзотермическими, сопровождаются значительной убылью энергии Гиббса и протекают с выделением большого количества тепла (табл. 1). Так, например, адиабатическая температура реакции восстановления Cr2O3 магнием составляет 2708°C, что превышает температуру кипения хрома 2672°C [25]. Восстановление парами магния позволяет регулировать скорость поступления восстановителя в реакционную зону и тем самым ограничить температуру реакции, а также контролировать ее в течение всего процесса восстановления.
Таблица 1.
Термодинамические характеристики реакций восстановления магнием оксидных соединений хрома
Реакция | –ΔH, кДж/моль | –ΔS, Дж/(моль К) | ΔQ, кДж/кг | –ΔG973, кДж/моль | –ΔG1073, кДж/моль |
---|---|---|---|---|---|
Cr2O3 + 3Mg = 2Cr + 3MgO (I) | 1049 | 445 | 4664 | 615 | 571 |
MgCr2O4 + 3Mg = 2Cr + 4MgO (II) | 1004 | 443 | 3785 | 573 | 528 |
Исходные вещества, за исключением магния, и продукты реакций (I) и (II) (табл. 1) в исследуемом интервале температур 700–800°C характеризуются низкой упругостью паров, не превышающей 10–18–10–14 Па [26–28]. Отсюда должно следовать, что полученная реакционная масса будет однородна и располагаться на месте загрузки прекурсора. Однако на практике в ряде экспериментов это было не так.
Вид тиглей после восстановления Cr2O3 и MgCr2O4 представлен на рис. 1. Видно, что после восстановления Cr2O3 на внутренней боковой поверхности всех контейнеров выше уровня их загрузки и на поверхности реакционной массы имеются отложения вещества белого цвета (рис. 1а–1в). По данным РФА, белое вещество на поверхности реакционной массы и боковых поверхностях тиглей идентично и представляет собой чистый оксид магния (рис. 2, дифрактограмма 1). Под белой коркой находилась однородная смесь порошка хрома с примесью оксида магния (рис. 2, дифрактограмма 2). Количество оксида магния в смеси под коркой снижается, а толщина корки на поверхности увеличивается при повышении остаточного давления аргона в реакторе (рис. 1б, 1в).
Ранее было показано, что пространственное разделение металлической и оксидной фаз при восстановлении парами Mg или Ca ряда оксидных соединений вольфрама и молибдена обусловлено протеканием электронно-опосредованных реакций (ЭОР) без непосредственного физического контакта реагирующих веществ [29, 30]. Оксид хрома при высоких температурах представляет собой электропроводящую среду, способную обеспечить перенос электронов. Переносчиком ионов кислорода при определенных условиях, которые обеспечиваются высоким тепловым эффектом реакции восстановления (4664 кДж/кг), становится среда инертного газа аргона. При повышении остаточного давления аргона в реакторе доля металла, восстанавливаемого в режиме ЭОР, увеличивается. Для хромита MgCr2O4 при исследованных условиях восстановления расслоения продуктов реакции не происходило (рис. 1г). Они представляли собой однородную смесь темного цвета, по составу соответствующую стехиометрическому соотношению реакции (рис. 2, дифрактограмма 3). Тепловой эффект реакции MgCr2O4 с магнием значительно меньше, чем с Cr2O3, и не обеспечивает условий для протекания реакции (2) в режиме ЭОР. Дифрактограмма 4 на рис. 2 относится к порошку хрома, полученному восстановлением MgCr2O4.
Рис. 1.
Тигли с реакционной массой после восстановления Cr2O3 (а–в) и MgCr2O4 (г) (остаточное давление аргона в реакторе 10 кПа, температура 750°С).
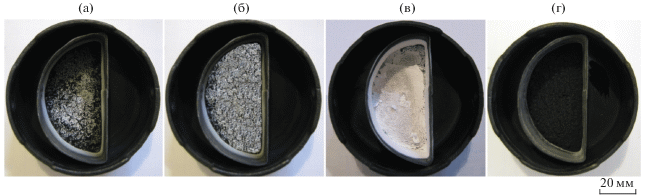
Рис. 2.
Дифрактограммы продуктов восстановления: белой корки на поверхности реакционной массы (1) и реакционной массы под коркой (2) после восстановления Cr2O3, реакционной массы после восстановления MgCr2O4 (3) и отмытого порошка хрома (4) (остаточное давление аргона в реакторе, кПа: 1 – 5, 2 – 10, 3, 4 – 15; температура 750°С).
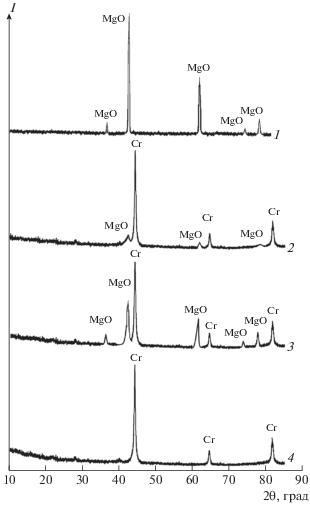
Результаты исследования влияния температуры и остаточного давления аргона в реакторе на удельную поверхность порошков хрома приведены на рис. 3. Там же приведены значения удельной поверхности порошков вольфрама и молибдена, полученных восстановлением вольфрамата и молибдата кальция при аналогичных условиях. Данные подтверждают установленную ранее для W [23] и Mo [24] возможность увеличения удельной поверхности порошков при магниетермическом восстановлении сложного оксидного соединения, имеющего в своем составе тугоплавкий оксид. Удельная поверхность порошков хрома, полученных восстановлением хромита магния, в 4–8 раз больше, чем у порошков, полученных восстановлением в аналогичных условиях оксида хрома (III). Это обусловлено тем, что присутствующий в хромате тугоплавкий оксид MgO, создавая дополнительные прослойки между частицами образующегося хрома, затрудняет их коагуляцию. Увеличивается и количество пор, остающихся после выщелачивания оксидов, результатом является рост удельной поверхности порошка. При использовании в качестве прекурсора MgCr2O4 получены порошки хрома с удельной поверхностью 28–34 м2/г, что в 1.4–1.7 раз выше поверхности порошков вольфрама и молибдена, полученных при восстановлении MgWO4, CaWO4 [23] и MgMO4, CaMoO4 [24] в тех же условиях. По-видимому, это обусловлено меньшей плотностью хрома при приблизительно равном количестве пор, образующихся на единицу объема металла.
Согласно соотношению (1), величине удельной поверхности порошков хрома 28–34 м2/г соответствует размер частиц металла 25–30 нм. Однако, как можно оценить из СЭМ-изображений (рис. 4), порошки представлены достаточно крупными агрегированными частицами со средним размером более 200 нм. Высокая удельная поверхность порошка является следствием его нанопористой структуры. Причем рост удельной поверхности происходит в основном за счет увеличения количества нанопор меньшего диаметра (рис. 5).
Рис. 5.
Зависимости суммарной поверхности пор от их среднего диаметра; прекурсоры: 1 – Cr2O3, 2 и 3 – MgCr2O4; удельная поверхность порошков хрома: 5 (1), 28 (2), 34 м2/г (3).
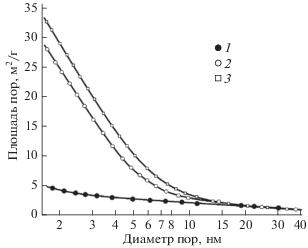
Кривые адсорбции порошков хрома, полученных восстановлением как MgCr2O4, так и Cr2O3, соответствуют IV типу по IUPAC. Они отличаются наличием петли гистерезиса и характерны для материалов с мезопористой структурой. Количество вещества, адсорбируемого при одних и тех же относительных давлениях порошком хрома, полученным восстановлением MgCr2O4, в 4–8 раз больше, чем порошком, полученным с использованием в качестве прекурсора Cr2O3 (рис. 6).
Рис. 6.
Кривые адсорбции–десорбции азота порошками хрома с удельной поверхностью 5 м2/г (прекурсор Cr2O3) (а), 34 м2/г (прекурсор MgCr2O4) (б).
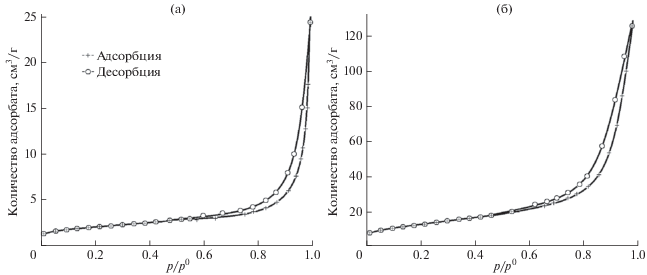
Таким образом, результаты проведенных исследований показали возможность использования хромита MgCr2O4 для получения магниетермическим восстановлением наноструктурных порошков хрома с развитой поверхностью.
ЗАКЛЮЧЕНИЕ
Исследованы закономерности восстановления оксидных соединений хрома Cr2O3 и MgCr2O4 парами магния в интервале температур 700–800°C при остаточном давлении аргона в реакторе 5–20 кПа и характеристики полученных порошков хрома.
На примере восстановления хромита MgCr2O4 подтверждена возможность повышения удельной поверхности магниетермического порошка при использовании в качестве прекурсора соединения, содержащего в своем составе тугоплавкий оксид. При получении хрома восстановлением этого соединения удельная поверхность порошка достигала 28–34 м2/г, что в 4–8 раз превышает таковую у порошков, полученных восстановлением Cr2O3 в аналогичных условиях.
Форма кривых адсорбции порошков хрома, полученных магниетермическим восстановлением Cr2O3 и MgCr2O4, соответствует IV типу по IUPAC, что подтверждает их мезопористую структуру.
Список литературы
Schatt W., Wieters K.-P. Powder Metallurgy-Processing and Materials. Shrewsbury: European Powder Metallurgy Association, 1997. 492 p.
Rudoy A.P., Milman Yu.V., Korzhova N.P. High-Purity Chromium Targets // J. Phys. C IV. 1995. V. 5. № 7. P. 149–153. https://doi.org/10.1051/jp4:1995714
Müller M., Heimann R.B., Gitzhofer F. et al. Radio Frequency Plasma Processing to Produce Chromium Sputter Targets // J. Therm. Spray. Tech. 2000. V. 9. № 4. P. 488–493. https://doi.org/10.1007/BF02608551
El Sayed R., Massicano A.V.F., Queern S.L. et al. Manganese-52 Production Cross-Section Measurements via Irradiation of Natural Chromium Targets up to 20 MeV // Appl. Radiat. Isot. 2019. V. 147. № 5. P. 165–170.
Хрущов М.М., Марченко Е.А., Левин И.С. и др. Структура и функциональные свойства покрытий, полученных с помощью мишеней на основе хрома и наноалмазов детонационного синтеза // Металлы. 2020. № 7. С. 85–95.
Loubiere S., Laurent Ch., Bonino J.P., Rousset A. Powders of Chromium and Chromium Carbides of Different Morphology and Narrow Size Distribution // Mater. Res. Bull. 1998. V. 33. № 6. P. 935–944.
Лякишев, Н.П., Гасик М.И. Металлургия хрома. М.: Элиз, 1999. 581 с.
Eggert H. Process for the Preparation of Finely Particulate Chromium Metal Powder Having a Low Oxygen Content: Пат. США № 4767454. Опубл. 30.08.1988.
Chen G.Z., Gordo E., Fray D.J. Direct Electrolytic Preparation of Chromium Powder // Metall. Materi. Trans. B. 2004. V. 35. № 4. P. 223–233.
Gordo E., Chen G.Z., Fray D.J. Toward Optimization of Electrolytic Reduction of Solid Chromium Oxide to Chromium Powder in Molten Chloride Salts // Electrochim. Acta. 2004. V. 49. № 13. P. 2195–2208.
Weng W., Wang M., Gong X. Direct Electro-deposition of Metallic Chromium from K2CrO4 in the Equimolar CaCl2–KCl Molten Salt and Its Reduction Mechanism // Electrochim. Acta. 2016. V. 212. № 9. P. 162–170.
Abdul-Razzaq W., Seehra M.S. Observation of Oxidation and Mechanical Strain in Cr Nanoparticles Produced by Ball-Milling // Phys. Status Solidi A. 2002. V. 193. № 1. P. 94–102. https://doi.org/10.1002/1521-396x(200209)193:1 <94::aid-pssa94>3.0.co;2-s
Shaban M., Hamdy H., Shahin F., Ryu S.-W. Fabrication of Ordered Cr Nanostructures by Self Agglomeration on Porous Anodic Alumina Membranes // J. Nanosci. Nanotechnol. 2011. V. 11. № 8. P. 7145–7150. https://doi.org/10.1166/jnn.2011.4831
Tilley R.D., Jefferson D.A. The Preparation of Chromium, Nickel and Chromium-Nickel Alloy Nanoparticles on Supports // J. Mater. Chem. 2002. V. 12. № 12. P. 3809–3813. https://doi.org/10.1039/b204774h
Chandra S., Kumar A. Spectral, Thermal and Morphological Studies of Chromium Nanoparticles // Spectrochim. Acta, Part A. 2013. V. 102. № 2. P. 250–255. https://doi.org/10.1016/j.saa.2012.10.003
Zhang W.S., Brück E., Zhang Z. D. et al. Structure and Magnetic Properties of Cr Nanoparticles and Cr2O3 Nanoparticles // Phys. B. 2005. V. 538. № 1–4. P. 332–338. https://doi.org/10.1016/j.physb.2005.01.469
Zhang K., Tenailleau C., Alphonse P., Chane-Ching, J.-Y. Realization of Aligned Three-Dimensional Single-Crystal Chromium Nanostructures by Thermal Evaporation // Spectrochim. Appl. Phys. A. 2010. V. 100. № 4. P. 1049–1055. https://doi.org/10.1007/s00339-010-5905-8
Son S.U., Jang Y., Yoon K.Y. et al. Synthesis of Monodisperse Chromium Nanoparticles from the Thermolysis of a Fischer Carbene Complex // Chem. Commun. 2005. V. 1. P. 86–88. https://doi.org/10.1039/b411656a
Ishibashi H., Nakahigashi K., Tsunoda Y. Neutron Diffraction Studies on Cr Fine Particles // J. Phys.: Condens. Matter. 1993. V. 5. № 33. P. L415–L418.
Tsunoda Y., Nakano H., Matsuo S. Antiferromagnetism of Cr Fine Particles // J. Phys.: Condens. Matter. 1993. V. 5. № 3. P. L29–L34.
Trenczek-Zajac A., Radecka M., Jasinski M. et al. Influence of Cr on Structural and Optical Properties of TiO2:Cr Nanopowders Prepared by Flame Spray Synthesis // J. Power Sources. 2009. V. 194. № 1. P. 104–111.
Koda T., Mitani S., Mizuguchi M., Takanashi K. Spin Accumulation in Cr Nanoparticles in Single Electron Tunneling Regime // IEEE Trans. Magn. 2010. V. 46. № 6. P. 2060–2062. https://doi.org/10.1109/TMAG.2010.2044870
Колосов В.Н., Мирошниченко М.Н., Орлов В.М. Влияние химического состава прекурсора и условий восстановления на фазовый состав и свойства магниетермических порошков вольфрама // Неорган. материалы. 2016. Т. 52. № 8. С. 945–852. https://doi.org/10.7868/S0002337X16080108
Колосов В.Н., Мирошниченко М.Н., Орлов В.М. Влияние состава прекурсора и условий восстановления на свойства магниетермических порошков молибдена // Неорган. материалы. 2017. Т. 53. № 10. С. 1081–1086. https://doi.org/10.7868/S0002337X17100098
Shekhter L.N., Tripp T.B., Lanin L.L. et al. Metalothermic Reduction of Refractory Metal Oxides: Патент США № 7678175. Опубл. 16.03.2010.
Таблицы физических величин / Под ред. Кикоина И.К. М.: Атомиздат, 1976. 1008 с.
Казенас Е.К. Термодинамика испарения двойных оксидов. М.: Наука, 2004. 551 с.
Казенас Е.К., Цветков Ю.В. Термодинамика испарения оксидов. М.: Изд-во ЛКИ, 2008. 480 с.
Колосов В.Н., Орлов В.М. Электронно-опосредованные реакции при металлотермическом восстановлении оксидных соединений молибдена и вольфрама // Докл. РАН. 2019. Т. 484. № 4. С. 447–450. https://doi.org/10.31857/S0869-56524844447-450
Колосов В.Н., Орлов В.М., Мирошниченко М.Н. Восстановление кислородных соединений металлов V и VI групп парами кальция // Неорган. материалы. 2020. Т. 56. № 1. С. 37–43. https://doi.org/10.1134/S0002337X20010066
Дополнительные материалы отсутствуют.
Инструменты
Неорганические материалы