Неорганические материалы, 2021, T. 57, № 5, стр. 506-511
Оценка температурного диапазона процессов синтеза порошковых композиционных материалов B4C–TiB2 и B4C–ZrB2
В. А. Шестаков 1, Т. С. Гудыма 2, Ю. Л. Крутский 2, *, Н. Ф. Уваров 2, 3, А. Е. Брестер 2, И. Н. Сковородин 4
1 Институт неорганической химии им. А.В. Николаева СО Российской академии наук
630090 Новосибирск, просп. Академика Лаврентьева, 3, Россия
2 Новосибирский государственный технический университет
630073 Новосибирск, просп. К. Маркса, 20, Россия
3 Институт химии твердого тела и механохимии СО Российской академии наук
630090 Новосибирск, ул. Кутателадзе, 18, Россия
4 Институт автоматики и электрометрии СО Российской академии наук
630090 Новосибирск, просп. Академика Коптюга, 1, Россия
* E-mail: j_krutskii@rambler.ru
Поступила в редакцию 09.07.2020
После доработки 08.12.2020
Принята к публикации 12.12.2020
Аннотация
На основе анализа диаграмм состояния и термодинамического моделирования определены оптимальные температурные диапазоны процессов получения композиционных порошков B4C–TiB2 и B4C–ZrB2 по карбидоборным реакциям с избытком карбида бора: 2MO2 + (n + 1)B4C + 3C = 2MB2 + + 4CO + nB4C (M = Ti, Zr). Величины n были выбраны для получения композиционных порошков составов (мол. %): 90B4C–10MB2 (n = 19), 80B4C–20MB2 (n = 9), 75B4C–25MB2 (n = 7), 70B4C–30MB2 (n = 5.67). Были найдены значения температуры, обеспечивающие при разных давлениях СО получение композиционных порошков заданного состава. При давлении СО 0.0773 МПа эти температуры для обеих реакций 1816 К ≈ 1540°С независимо от состава получаемых порошков. Температура плавления эвтектики в системе B4C–TiB2 равна ~2200°С, а в системе B4C–ZrB2 ~ 2280°С. Таким образом, при давлении СО в реакторе, близком к атмосферному, оптимальная температура синтеза композиционного порошка B4C–TiB2 находится в диапазоне 1540–2200°С, а композиционного порошка B4C–ZrB2 – в диапазоне 1540–2280°С. Такие порошки перспективны для получения керамики с повышенными эксплуатациоными характеристиками.
ВВЕДЕНИЕ
Карбид бора характеризуется уникальной комбинацией низкой плотности (2.52 г/см3), высокой твердости (до 40 ГПа для горячепрессованных изделий) и химической инертности в сочетании с высокой температурой плавления (2450°С), вследствие чего керамика из этого соединения нашла применение в ряде областей современной техники [1–3]. Однако получение плотной керамики из этого соединения является трудной задачей из-за низкого значения коэффициента самодиффузии (вследствие сильной ковалентной связи между атомами бора и углерода), низкой пластической деформации этого соединения и высокого сопротивления скольжения между его зернами [4].
Перспективным направлением улучшения эксплуатационных характеристик керамики на основе карбида бора является использование модифицирующих добавок. Их присутствие активирует процесс спекания за счет снижения энергии активации, что приводит к уменьшению размеров зерен, увеличению плотности, прочности и трещиностойкости спеченных смесей [5]. Для этой цели часто используются дибориды титана и циркония. Возможны следующие способы изготовления композиционных порошков, используемых для приготовления керамики B4C–TiB2 и B4C–ZrB2: смешивание карбида бора и диборида титана [6–8] или карбида бора и диборида циркония [9–11] (1); смешивание бора, углерода и титана [12–14] или бора, углерода и циркония [15, 16] (2); карбидоборное восстановление оксида титана при избытке карбида бора [17–19] (3). Сведения о карбидоборном восстановлении оксида циркония при избытке карбида бора отсутствуют. Только в публикации [16] сообщается об использовании шихты из бора, углерода и оксида циркония для получения керамики B4C–ZrB2. Особенностью процессов 1 и 2 является необходимость тщательного смешения шихтовых материалов перед осуществлением операции спекания. При карбидоборном восстановлении оксидов необходимость трудоемкого смешения отпадает, поскольку образовавшиеся частицы диборидов несомненно должны быть равномерно распределены в матрице карбида бора. При получении композиционных порошков карбидоборным методом в цитируемых публикациях обоснование выбора температуры синтеза не проводилось.
Целью данной работы является оценка температурного диапазона процессов получения карбидоборным методом порошковых композиционных материалов B4C–TiB2 и B4C–ZrB2, а также индивидуальных соединений (TiB2 и ZrB2) с использованием анализа диаграмм состояния и термодинамического моделирования.
ОПРЕДЕЛЕНИЕ ВЕРХНЕГО ТЕМПЕРАТУРНОГО ПРЕДЕЛА РЕАКЦИЙ СИНТЕЗА ПОРОШКОВЫХ КОМПОЗИЦИОННЫХ МАТЕРИАЛОВ B4C–TiB2 И B4C–ZrB2
Диаграммы состояния систем B4C–TiB2 и B4C–ZrB2 приведены на рис. 1. Обе диаграммы состояния [6, 9] относятся к бинарным с эвтектикой без образования твердых растворов и химических соединений. Поэтому при синтезе диборидов титана или циркония по карбидоборным реакциям с избытком карбида бора продукты реакций при температурах процессов ниже эвтектических (~2200°С для системы B4C–TiB2 и ~2280°С для системы B4C–ZrB2) будут состоять из смеси порошков индивидуальных соединений независимо от составов.
Для анализа были выбраны следующие реакции:
(1)
$2{\text{М}}{{{\text{O}}}_{2}} + 19{{{\text{B}}}_{{\text{4}}}}{\text{C}} + 3{\text{C}} = 2{\text{М}}{{{\text{B}}}_{2}} + 18{{{\text{B}}}_{{\text{4}}}}{\text{C}} + 4{\text{CO}},$(2)
$2{\text{М}}{{{\text{O}}}_{2}} + 9{{{\text{B}}}_{{\text{4}}}}{\text{C}} + 3{\text{C}} = 2{\text{М}}{{{\text{B}}}_{2}} + 8{{{\text{B}}}_{{\text{4}}}}{\text{C}} + 4{\text{CO}},$(3)
$2{\text{М}}{{{\text{O}}}_{2}} + 7{{{\text{B}}}_{{\text{4}}}}{\text{C}} + 3{\text{C}} = 2{\text{М}}{{{\text{B}}}_{2}} + 6{{{\text{B}}}_{{\text{4}}}}{\text{C}} + 4{\text{CO}},$(4)
$\begin{gathered} 2{\text{М}}{{{\text{O}}}_{2}} + {\text{ }}5.67{{{\text{B}}}_{{\text{4}}}}{\text{C}} + 3{\text{C}} = \\ = \,\,2{\text{М}}{{{\text{B}}}_{2}} + 4.67{{{\text{B}}}_{{\text{4}}}}{\text{C}} + 4{\text{CO}}. \\ \end{gathered} $Таким образом, в ходе реакций содержание компонентов в конденсированной фазе становилось равным (мол. %): для реакции (1) 90В4С и 10МВ2; для реакции (2) 80В4С и 20МВ2; для реакции (3) 75В4С и 25МВ2; для реакции (4) 70В4С и 30МВ2. Такие составы были выбраны из следующих соображений. В источниках [7, 10–13, 15–18] сообщается, что наиболее качественная керамика на основе карбида бора с модифицирующими добавками диборидов титана и циркония получается при содержании их на уровне 25 мол. % или немного ниже. Первые два состава применительно к содержанию МВ2 являлись доэвтектическими, третий был фактически эвтектическим, а четвертый – заэвтектическим.
ВОЗМОЖНЫЙ МЕХАНИЗМ КАРБИДОБОРНЫХ ПРОЦЕССОВ ОБРАЗОВАНИЯ ДИБОРИДОВ ТИТАНА И ЦИРКОНИЯ
На основании имеющейся в литературе информации можно предложить возможный механизм образования тугоплавких соединений TiB2 и ZrB2. При анализе процессов следует исходить из того, что при температурах синтеза давление паров углерода существенно ниже давления паров бора и оксидов металлов. Так, давление паров углерода при температурах 1700, 1800, 1900, 2000, 2200 и 2400 К составляет ~9 × 10–9, ~2 × 10–7, ~3 × × 10–6, ~4 × 10–5, ~2.6 × 10–3 и ~8.5 × 10–2 Па соответственно [20]. Известно [21], что давление пара бора над системой карбид бора–углерод при температуре 2000 К (примерно соответствует оптимальным температурам синтеза диборидов рассматриваемых переходных металлов) равно ~0.1 Па, а давление других газообразных компонентов на два (ВС2) и на три (В2С) порядка ниже. Давление пара над используемыми при синтезе оксидами следующее [22]: для оксида TiO2 при температуре 2000 К (примерно соответствует оптимальной температуре синтеза диборида титана) ~0.01 Па; для оксида ZrO2 при температуре 2000 К (примерно соответствует оптимальной температуре синтеза диборида циркония) ~0.0001 Па.
Таким образом, давление паров бора и оксидов при оптимальных температурах синтеза рассматриваемых тугоплавких соединений значительно (иногда на несколько порядков) превышает давление паров углерода.
Следовательно, с большой долей вероятности можно утверждать, что эти процессы осуществляются путем переноса паров высших и низших оксидов наряду с парами бора на поверхность твердого углерода. Далее следуют диффузионные процессы (хотя они реальны и при контакте реагентов). Считается [23], что реакции происходят на границе раздела фаз с последующей диффузией реагентов в объем частиц через слой продуктов реакции. Следует отметить, что процессы карбидоборного синтеза очень сложны и механизм их до сих пор детально не исследован.
ТЕРМОДИНАМИЧЕСКИЙ РАСЧЕТ
Целью термодинамического моделирования было определение оптимальных температурных режимов процессов, обеспечивающих полное превращение оксидов металлов в дибориды при отсутствии в продуктах реакции посторонних фаз.
Основную реакцию, происходящую в исследуемых системах, можно выразить уравнением
(5)
$2{\text{M}}{{{\text{O}}}_{2}} + {{{\text{B}}}_{{\text{4}}}}{\text{C}} + 3{\text{C}} = 2{\text{M}}{{{\text{B}}}_{2}} + 4{\text{CO}}.$Поскольку синтез планируется осуществлять в проточном реакторе при давлении, близком к атмосферному, в токе аргона, который удаляет СО из газовой фазы, равновесие в системе, в соответствии с законом Ле-Шателье, смещается в сторону прямой реакции. При этом происходит изменение состава системы и, соответственно, парциального давления СО в ней, соответствующего реакции моновариантного равновесия. Хотя, строго говоря, такая система не является равновесной, можно ожидать, что состав газовой фазы в тонком слое вблизи поверхности раздела фаз мало отличается от равновесного и процесс проходит в квазиравновесном режиме. Это обстоятельство позволяет использовать термодинамическое моделирование на основе расчета равновесий для описания процессов, происходящих в проточных реакторах [24]. Подобное моделирование успешно использовалось, например, в работах [25, 26]. В данной работе моделирование использовано для определения минимальной температуры в реакторе, обеспечивающей достижение сформулированной выше цели. Эта температура определяется моновариантным равновесием в системе и зависит от парциального давления в ней СО. Поэтому для решения поставленной задачи необходимо рассчитать такую зависимость.
Расчет условий фазовых равновесий проводили с использованием стандартного программного обеспечения банка данных “Свойства материалов электронной техники” ИНХ СО РАН [27], основу которого составляют величины термодинамических характеристик индивидуальных веществ, рекомендованных справочным изданием [28]. Предполагалось, что в системе присутствуют конденсированные фазы постоянного состава и равновесный идеальный газ, образованный из молекулярных форм. При расчетах минимизировалась энергия Гиббса системы, образованной из заданного количества элементов, при заданных Т и р. Были рассчитаны количество молей каждой из конденсированных фаз, а также содержание и парциальное давление молекулярных форм в газовой фазе. Для учета изменения состава системы в процессе удаления из нее током аргона СО была использована итерационная процедура, позволяющая проводить расчеты при переменном составе системы. При расчетах для системы с цирконием учитывалась возможность образования конденсированных фаз: Zr(3), ZrO2(2), ZrC, ZrB2, B2O3(2), B4C, B(3), C, а также 27 молекулярных форм газовой фазы; для системы с титаном – Ti(3), Ti4O7(2), Ti3O5(3), Ti2O3(2), TiO2(3), TiO(4), TiC, C, TiB2, B2O3(2), B4C, B(3) и 27 молекулярных форм газовой фазы. В скобках указано общее число твердых и жидких фаз, способных образоваться в исследуемом температурном интервале 298.15–2500 К.
РЕЗУЛЬТАТЫ И ОБСУЖДЕНИЕ
Получение композиционных порошков B4C–TiB2 и B4C–ZrB2 карбидоборным методом. При избытке карбида бора по сравнению со стехиометрическим для осуществления реакции (5) расчеты показали, что оксиды металлов уже при сравнительно низких температурах полностью переходят в дибориды с одновременным образованием оксида бора по реакции
(6)
$6{\text{M}}{{{\text{O}}}_{2}} + 5{{{\text{B}}}_{{\text{4}}}}{\text{C}} = 4{{{\text{B}}}_{{\text{2}}}}{{{\text{O}}}_{3}} + 6{\text{M}}{{{\text{B}}}_{2}} + 5{\text{C}}.$Поэтому целью моделирования для таких систем было определение минимальной температуры, при которой из композиционного порошка полностью удаляется оксид бора, в зависимости от парциального давления СО. Соответствующая реакция моновариантного равновесия имеет вид
(7)
$2{{{\text{B}}}_{{\text{2}}}}{{{\text{O}}}_{3}} + 7{\text{C}} = 6{\text{CO}} + {{{\text{B}}}_{{\text{4}}}}{\text{C}}.$Это одна и та же реакция для обеих систем. Поэтому результаты расчетов отвечают как системе с титаном, так и системе с цирконием. На рис. 2 показана полученная по результатам расчета зависимость температуры, при превышении которой оксид бора полностью удаляется из композиционного порошка, от парциального давления СО. Поскольку оксид бора расходуется на образование карбида бора, при достижении температур, указанных на графике, содержание этого соединения в композиционных порошках будет соответствовать заданному. На основе расчетов установлено, что при давлении СО 0.0773 МПа значение этой температуры составляет 1816 К ≈ 1540°С. При понижении давления она уменьшается, достигая при 0.0001 МПа 1338 К ≈ 1070°С.
Рис. 2.
Зависимость температуры, при превышении которой оксид бора полностью удаляется из композиционного порошка, от парциального давления СО.
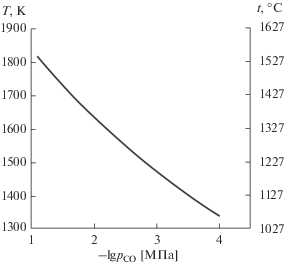
Получение диборидов циркония и титана карбидоборным методом. В данном случае при различном составе системы рассчитывалась температура моновариантного равновесия, при превышении которой оксид металла полностью переходит в диборид. Расчеты показали, что в системе с цирконием моновариантное равновесие, определяющее температуру полного перехода оксида в диборид, имеет вид
(8)
${\text{2Zr}}{{{\text{O}}}_{2}} + {{{\text{B}}}_{{\text{4}}}}{\text{C}} + 3{\text{C}} = 2{\text{Zr}}{{{\text{B}}}_{2}} + 4{\text{CO}}.$Между тем, оксид TiO2 не имеет достаточной термодинамической устойчивости, позволяющей ему принять участие в реакции моновариантного равновесия, отвечающей полному переходу оксида в диборид в исследованной области температур. В разных температурных интервалах такими реакциями являются
(9)
${\text{T}}{{{\text{i}}}_{{\text{2}}}}{{{\text{O}}}_{3}} + {{{\text{B}}}_{{\text{4}}}}{\text{C}} + 2{\text{C}} = 2{\text{Ti}}{{{\text{B}}}_{2}} + 3{\text{CO}},$(10)
$2{\text{TiO}} + {{{\text{B}}}_{{\text{4}}}}{\text{C}} + {\text{C}} = 2{\text{Ti}}{{{\text{B}}}_{2}} + 2{\text{CO}}.$Реакция (10) реализуется только в области высоких температур.
На рис. 3 показана расчетная зависимость температуры, при превышении которой оксид металла полностью переходит в диборид, от парциального давления СО для систем с цирконием (1) и титаном (2). По результатам расчетов установлено, что при парциальном давлении СО 0.08 МПа полное превращение оксидов титана в TiB2 происходит при температуре 1958 К ≈ 1680°С, а ZrO2 в ZrB2 – при 1900 К ≈ 1630°С. При снижении парциального давления СО температуры полного превращения уменьшаются. Так, при давлении СО 0.0001 МПа полное превращение оксидов титана в TiB2 происходит при 1178 К ≈ 910°С, а ZnO2 в ZrB2 – при 1306 К ≈ 1030°С.
ЗАКЛЮЧЕНИЕ
На основе анализа диаграмм состояния систем B4C–TiB2 и B4C–ZrB2 и термодинамического анализа определены температурные диапазоны процессов получения композиционных порошков карбида бора с диборидами титана и циркония по карбидоборным реакциям. Данные порошки перспективны для получения композиционной керамики B4C–TiB2 и B4C–ZrB2. При давлении СО в реакторе, близком к атмосферному (0.0773 МПа), независимо от задаваемых составов оптимальная температура синтеза композиционного порошка B4C–TiB2 находится в диапазоне 1540–2200°С, а композиционного порошка B4C–ZrB2 – в диапазоне 1540–2280°С. Дополнительно установлено, что при карбидоборном синтезе диборида титана при давлении СО 0.08 МПа температура полного превращения реагентов в это соединение должна быть выше 1680°С, при карбидоборном синтезе диборида циркония при таком же давлении СО – выше 1630°С.
Список литературы
Spohn M.T. Annual Minerals Review. Boron Carbide // Am. Ceram. Soc. Bull. 1995. V. 74. № 6. P. 113–115.
Кислый П.С., Кузенкова М.А., Боднарук Н.И., Грабчук Б.Л. Карбид бора. Киев: Наук. думка, 1988. 216 с.
Серебрякова Т.И., Неронов В.А., Пешев П.Д. Высокотемпературные бориды. М.: Металлургия, 1991. 368 с.
Zhang W., Yamashita S., Kita H. Progress in Pressureless Sintering of Boron Carbide Ceramics – a Review // Adv. Appl. Ceram. 2019. V. 118. № 4. P. 222–239. https://doi.org/10.1080/17436753.2019.1574285
Heydari M.S., Baharvandi H.R. Effect of Different Additives on the Sintering Ability and the Properties of B4C–TiB2 Composites // Int. J. Refract. Met. Hard Mater. 2015. V. 51. P. 61–69. https://doi.org/10.1016/j.ijrmhm.2015.02.014
Орданьян С.С., Степаненко К.К., Дмитриев А.И., Щемелева М.В. Взаимодействие в системе B4C–TiB2 // Сверхтвердые материалы. 1986. № 5. С. 27–29.
Huang S., Vanmeensel K., Malek O., van der Biest O., Vleugels J. Microstructure and Mechanical Properties of Pulsed Electric Current Sintered B4C–TiB2 Composites // Mater. Sci. Eng., A. 2011. V. 528. № 3. P. 1302–1309. https://doi.org/10.1016/j.msea.2010.10.022
Xu C., Cai Y., Flodström K., Li Z., Esmaeilzadeh S., Zhang G.-J. Spark Plasma Sintering of B4C Ceramics: the Effects of Milling Medium and TiB2 Addition // Int. J. Refract. Met. Hard Mater. 2012. V. 30. № 1. P. 139–144. https://doi.org/10.1016/j.ijrmhm.2011.07.016
Орданьян С.С., Дмитриев А.И., Бижев К.Т., Степаненко Е.К. Взаимодействие в системе B4C–ZrB2 // Порошковая металлургия. 1988. № 1. С. 41–43.
Mestvirishvili Z., Bairamashvili I., Kvatchadze V., Rekhviashvili N. Thermal and Mechanical Properties of B4C–ZrB2 Ceramic Composite // J. Mater. Sci. Eng., B. 2015. V. 9–10. P. 385–393 https://doi.org/10.17265/2161-6221/2015.9-10.007
Chakraborty S., Debnath D., Mallick A.R., Das P.K. Mechanical, Tribological, and Thermal Properties of Hot-pressed ZrB2-B4C Composite // Int. J. Appl. Ceram. Technol. 2014. V. 9. P. 1–9. https://doi.org/10.1111/ijac.12290
Dudina D.V., Hulbert D.M., Jiang D., Unuvar C., Cytron S.J., Mukherjee A.K. In Situ Boron Carbide–Titanium Diboride Composites Prepared by Mechanical Milling and Subsequent Spark Plasma Sintering // J. Mater. Sci. 2008. V. 43. № 10. P. 3569–3576. https://doi.org/10.1007/s10853-008-2563-8
Nikzad L., Licheri R., Ebadzadeh T., Orrù R., Cao G. Effect of Ball Milling on Reactive Spark Plasma Sintering of B4C–TiB2 Composites // Ceram. Int. 2012. V. 38. № 8. P. 6469–6480. https://doi.org/10.1016/j.ceramint.2012.05.024
Hulbert D., Jiang M.D., Dudina D.V., Mukherjee A.K. The Synthesis and Consolidation of Hard Materials by Spark Plasma Sintering // Int. J. Refract. Met. Hard Mater. 2009. V. 27. № 2. P. 367–375. https://doi.org/10.1016/j.ijrmhm.2008.09.011
Shcherbakov V.A., Gryadunov A.N., Alymov A.I. Synthesis and Characteristics of the B4C–ZrB2 Composites // Lett. Mater. 2017. V. 7. № 4. P. 398–401. https://doi.org/10.22226/2410-3535-2017-4-398-401
Guo W.-M., Wu L.-X., You Y., Lin H.-T., Zhang G.-J. Three-Step Reactive Hot Pressing of B4C–ZrB2 Ceramics // J. Eur. Ceram. Soc. 2016. V. 36. № 4. P. 951–957. https://doi.org/10.1016/j.jeurceramsoc.2015.11.022
Huang S., Vanmeensel K, van der Biest O., Vleugels J. In Situ Synthesis and Densification of Submicrometer-Grained B4C–TiB2 Composites by Pulsed Electric Current Sintering // J. Eur. Ceram. Soc. 2011. V. 31. № 4. P. 637–644. https://doi.org/10.1016/j.jeurceramsoc.2010.10.028
Skorokhod V., Krstic V. High Strength-High Toughness B4C–TiB2 Composites // J. Mater. Sci. Lett. 2000. V. 19. P. 237–239. https://doi.org/10.1023/A:1006766910536
Wang Y.-J., Peng H.-X., Ye F., Zhou Y. Effect of TiB2 Content on Microstructure and Mechanical Properties of in-situ Fabricated TiB2/B4C composites // Trans. Nonferrous Met. Soc. China. 2011. V. 21. № 2. P. 369–373. https://doi.org/10.1016/S1003-6326(11)61608-7
Свойства элементов. Ч. 1. Справ. изд. / Под ред. Самсонова Г.В. М.: Металлургия, 1976. 600 с.
Болгар А.С., Турчанин А.Г., Фесенко В.В. Термодинамические свойства карбидов. Киев: Наук. думка, 1973. 272 с.
Физико-химические свойства окислов. Справ. изд. / Под общ. ред. Самсонова Г.В. М.: Металлургия, 1978. 472 с.
Вест А. Химия твердого тела. Теория и приложения. Ч. 1. Пер. с англ. М.: Мир, 1988. 558 с.
Кузнецов Ф.А., Смирнова Т.П. Фундаментальные основы процессов химического осаждения пленок и структур для наноэлектроники. Новосибирск: СО РАН, 2013. 176 с.
Суляева В.С., Шестаков В.А., Румянцев Ю.М., Косинова М.Л. Синтез пленок диборида циркония и гетероструктур ZrB2/BCxNy // Неорган. материалы. 2018. Т. 54. № 2. С. 146–152. https://doi.org/10.7868/S0002337X18020057
Шестаков В.А., Косяков В.И., Косинова М.Л. Термодинамическое моделирование осаждения борсодержащих пленок из газовой фазы с использованием B(OAlk)3 // Изв. АН. Сер. хим. 2019. № 11. С. 1983–1990.
Киселева Н.Н. Компьютерное конструирование неорганических соединений. Использование баз данных и методов искусственного интеллекта. М.: Наука, 2005. 289 с.
Гурвич Л.В., Вейц И.В., Медведев В.А., Хачкурузов Г.А., Юнгман В.С., Бергман Г.А., Байбуз В.Ф., Иориш В.С., Юрков Г.Н., Горбов С.И., Назаренко И.И., Дорофеева О.В., Куратова Л.Ф., Осина Е.Л., Гусаров А.В., Леонидов В.Я., Пржевальский И.Н., Рогацкий А.Л., Ефремов Ю.М., Рябова В.Г., Зицерман В.Ю., Хайт Ю.Г., Шенявская Е.А., Ефимов М.Е., Кулемза В.А., Ходеев Ю.С., Томберг С.Э., Вдовин В.Н., Якобсон А.Я., Демидова М.С. Термодинамические свойства индивидуальных веществ: Справочное издание. Т. IV. Кн. I. М.: Наука, 1982. 623 с.
Дополнительные материалы отсутствуют.
Инструменты
Неорганические материалы