Неорганические материалы, 2021, T. 57, № 6, стр. 615-620
Диспергирование литых материалов, полученных методом СВС в системе Mn–Cr–Al–C
В. А. Горшков 1, *, Н. Ю. Хоменко 1, Н. В. Сачкова 1
1 Институт структурной макрокинетики и проблем материаловедения им. А.Г. Мержанова
Российской академии наук
142432 Московская обл., Черноголовка, ул. Академика Осипьяна, 8, Россия
* E-mail: gorsh@ism.ac.ru
Поступила в редакцию 30.11.2020
После доработки 18.12.2020
Принята к публикации 21.12.2020
Аннотация
Исследован процесс самопроизвольного диспергирования литых материалов, состоящих из MAX-фазы Cr2AlC, допированной Mn, а также карбидов и алюминидов хрома, марганца и алюминия. Образцы получены в виде слитков методом СВС в реакторе объемом 3 л под давлением аргона р = 5 МПа. В качестве шихт использовали смеси порошков оксидов марганца(IV) и хрома(III) с алюминием (АСД-I) и углеродом. Обнаружено, что присутствие в литом материале карбида алюминия (Al4C3) приводит к самопроизвольному диспергированию (без механического или химического воздействия) литого материала в порошки с размером кристаллических частиц менее 100 мкм. Показано, что диспергирование происходит в результате взаимодействия карбида алюминия с влагой воздуха. Полученные продукты охарактеризованы методами рентгенографического и локального рентгеноспектрального анализов. Изучены структурно-фазовые состояния частиц целевых продуктов, полученных в результате самодиспергирования литого СВС-материала.
ВВЕДЕНИЕ
Бинарные и тройные соединения марганца, хрома, алюминия и углерода относятся к тугоплавким материалам, которые обладают полезными практическими свойствами. Сплавы с большим содержанием Mn и Al имеют высокую удельную прочность и могут быть использованы в литейном и деформационном производстве как жаропрочные и износостойкие, а также в других отраслях промышленности. Они давно известны и хорошо изучены [1–3]. В последнее время возник большой интерес к композиционным материалам, состоящим из MAX-фаз, карбидов и интерметаллидов переходных металлов, поскольку MAX-фазы имеют уникальное сочетание особенностей как металлов, так и керамики и обладают отличными механическими, химическими, тепловыми и электрическими свойствами [4].
В настоящее время MAX-фаза Cr2AlC является третьим широко изученным соединением после Ti3SiC2 и Ti3AlC2 среди семейства MAX-фаз. Имеется предположение, что при комнатной температуре Cr2AlC может вести себя как парамагнетик [5–7]. Для повышения магнитосопротивления в Cr2AlC вводят марганец, получая твердый раствор (Cr1 – xMnx)2AlC. Для этого смеси необходимых элементов в стехиометрических отношениях сплавлялись методом дуговой плавки в атмосфере Ar с температурой дуги более 1000оС [8, 9].
Для получения материалов на основе MAX-фазы Cr2AlC наиболее часто используют методы горячего прессования; плазменно-искрового спекания; двухстадийного спекания, включающего реакцию жидкого алюминия с карбидами хрома [10, 11]. Перспективным способом получения таких материалов является одностадийный метод – самораспространяющийся высокотемпературный синтез (СВС). Он практически не требует затрат электроэнергии, обладает высокой производительностью и экологической чистотой [12]. Одним из технологических направлений этого метода является СВС-металлургия, позволяющая получать литые материалы за счет полного плавления компонентов в волне горения. В результате продукт в волне горения формируется в жидкофазном состоянии. Из-за различного удельного веса под действием гравитации происходит сепарация тяжелой металлоподобной и легкой оксидной фаз в образовавшихся продуктах [13, 14]. Большинство из вышеперечисленных процессов проводят при повышенных температурах (>1200°С), в результате чего конечные продукты представляют собой спеченные блоки (“спеки”) или слитки. Для дальнейшего использования проводят их передел (измельчение) в порошки определенных фракций.
Наиболее распространенными способами диспергирования являются механические и химические методы. При механическом измельчении твердых материалов частицы размером менее 60 мкм образуют конгломераты, а на поверхности зерен образуются микротрещины, что обуславливает загрязнение продукта материалом истирающих частей мельниц [15]. При химическом диспергировании [16–18] процессы проводят в агрессивных (кислотных или щелочных) средах, часто при повышенной температуре, что крайне нежелательно с экологической точки зрения. Под воздействием агрессивной среды происходит также частичное растворение целевого продукта. В работах [19–21] отмечено, что присутствие в составе композитов фазы Al4C3 приводит к разрушению материала под действием влаги воздуха вследствие гидролиза. В работе [21] обнаружено, что карбид алюминия гидролизуется со скоростью 1%/ч. Было установлено, что Al4C3 нестабилен на воздухе, поглощает воду из окружающей среды с образованием Al(OH)3.
Целью данной работы является исследование процесса “самопроизвольного” диспергирования литого материала Cr–Mn–Al–C и получение мелкодисперсных порошков.
ЭКСПЕРИМЕНТАЛЬНАЯ ЧАСТЬ
В экспериментах использовали порошки оксидов марганца(IV) квалификации “ч.” и хрома(III) “ч.”, алюминия (АСД-I) и углерода (графит марки ПГ). Составы исходных смесей выбирали из условий их термической стабильности и возможности реализовать высокую температуру горения (синтеза). Соотношения компонентов рассчитывали из следующих реакций и их сочетаний:
(I)
$6{\text{Mn}}{{{\text{O}}}_{2}} + 11{\text{Al}} + 3{\text{C}} = 3{\text{M}}{{{\text{n}}}_{{\text{2}}}}{\text{AlC}} + 4{\text{A}}{{{\text{l}}}_{{\text{2}}}}{{{\text{O}}}_{3}},$(II)
${\text{C}}{{{\text{r}}}_{{\text{2}}}}{{{\text{O}}}_{3}} + 3{\text{Al}} + {\text{C}} = {\text{C}}{{{\text{r}}}_{{\text{2}}}}{\text{AlC}} + {\text{A}}{{{\text{l}}}_{{\text{2}}}}{{{\text{O}}}_{3}}.$Исходные смеси готовили вручную в фарфоровой ступке. Готовые шихты помещали в прозрачные кварцевые тигли диаметром 20, высотой 50 мм. Масса смеси во всех экспериментах составляла 20 г (рис. 1а). Синтез проводили в СВС-реакторе объемом 3 л при начальном избыточном давлении аргона 5 МПа. Воспламенение смеси инициировали спиралью из молибденовой проволоки диаметром 0.5 мм.
Рис. 1.
Кварцевый тигель с шихтой (а), внешний вид конечных продуктов (б): 1 – оксид (Al2O3), 2 – целевой продукт (Cr–Mn–Al–C).
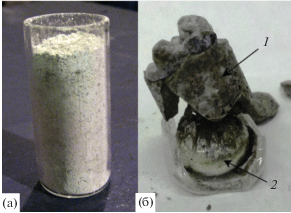
Эксперименты со стехиометрической смесью II показали, что эта реакция слабоэкзотермическая. После воспламенения образцов фронт горения распространяется на 5–10 мм, после чего происходит его остановка. Поэтому в дальнейших экспериментах опыты проводили на составах I и I/II = = 0.5/0.5. Температуры горения (синтеза) таких смесей превышают температуры плавления исходных реагентов и конечных продуктов, получаемых в волне горения в жидкофазном состоянии. Конечные продукты состоят из двух фаз: целевой металлоподобной (Cr–Mn–Al–C) и оксидной (Al2O3). Из-за различных удельных весов происходит их сепарация – более тяжелая фаза оседает и формирует нижний слиток, а, более легкая формируется сверху (рис. 1б).
В экспериментах для оценки параметров синтеза использовали следующие величины: uг = = Нсм/τг – средняя линейная скорость горения, η1 = Мсл/Мсм × 100% – выход продукта в слиток, η2 = (Мсм – Мк)/Мсм × 100% – потеря массы за счет разлета компонентов при горении, где Нсм – высота образца, τг – время сгорания всей шихты, Мсл – масса слитка, Мсм – масса исходной смеси, Мк – общая масса продукта после горения.
Рентгенофазовый анализ проводили на дифрактометре ДРОН-3 с графитовым монохроматором на вторичном пучке (излучение CuKα). Регистрация дифрактограмм велась в режиме пошагового сканирования в интервале углов 2θ = 12°–100° с шагом 0.02° и экспозицией 4 с. Микроструктуру и элементный состав образцов исследовали на автоэмиссионном сканирующем электронном микроскопе сверхвысокого разрешения Zeiss Ultra plus на базе Ultra 55, Германия (Zeiss Ultra plus Field Emission Scanning Electron Microscope).
РЕЗУЛЬТАТЫ ЭКСПЕРИМЕНТА
Визуальные наблюдения за процессом горения показали, что образцы 1 и 2 (табл. 1), составы которых рассчитывали из реакций (I) и (II), горят в нестационарных режимах с небольшим дымовыделением и потерей массы. Конечные продукты формируются в волне горения в жидкофазном состоянии и после сепарации и охлаждения получаются в виде двух слитков: вверху (более легкий) – Al2O3, внизу (более тяжелый) – целевой продукт Mn/Cr/Al/C. Составы исходных смесей и параметры синтеза приведены в табл. 1.
Таблица 1.
Составы исходных смесей и параметры синтеза
Образец | Смесь | Расчетный состав слитка | uг, см/с | η1, мас. % | η2, мас. % |
---|---|---|---|---|---|
1 | I | Mn2AlC | 0.85 | 42 | 8.3 |
2 | 0.5I + 0.5II | (Cr0.5Mn0.5)2AlC | 0.76 | 38 | 8.0 |
Из табл. 1 видно, что значения параметров синтеза (uг, η1 и η2) для образца 2, рассчитанного на конечный продукт (Cr0.5Mn0.5)2AlC, несколько ниже, чем для образца 1, рассчитанного на конечный продукт Mn2AlC. Это связано, по-видимому, с тем, что при добавлении в высокоэкзотермическую смесь I, низкоэкзотермической II снижается температура горения шихты, что приводит к уменьшению этих параметров. По данным РФА, конечные продукты в обоих случаях являются многофазными и состоят из карбидов и алюминидов хрома и марганца. Отмечено, что после хранения слитков на открытом воздухе они самодиспергировались в порошки с размером частиц менее 100 мкм (рис. 2).
Рис. 2.
Внешний вид порошков конечных продуктов после самодиспергирования: а – образец 1 (Mn–Al–C), б – образец 2 (Cr–Mn–Al–C).
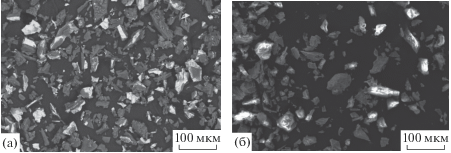
Для образца 1 первоначально (до диспергирования слитка в порошок) РФА показал присутствие следующих основных фаз: Mn3AlC, MnAl, Al0.42Mn0.545C0.035, AlCr2, Al4C3 и углерод (рис. 3).
Рис. 3.
Дифрактограмма материала (слиток), полученного при горении смеси I (MnO2/Al/C → Mn2AlC + Al2O3).
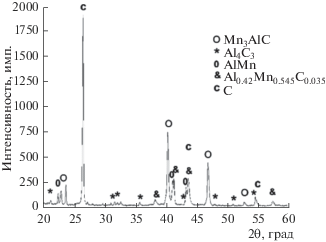
После нахождения на открытом воздухе в течение 100 ч на дифрактограмме образованного порошка исчезли рефлексы Al4C3 и появились рефлексы Al2O3 (рис. 4). По-видимому, в данном случае фаза Al4C3 разлагается на воздухе за счет поглощения и реакции с влагой или кислородом воздуха.
Для образца 2 (табл 1), конечный продукт, полученный в виде слитка, также является многофазным. Основные фазы – Mn3AlC, (CrxMn1 –x)2AlC и интерметаллид AlCr2 (рис. 5). Рефлексы МАХ-фазы смещены относительно положения рефлексов Cr2AlC (ICDD PDF2 # 65-3492), что, вероятно, связано с замещением части атомов хрома атомами марганца. В результате формулу МАХ-фазы можно представить как (CrxMn1 – x)2AlC. На дифрактограмме также наблюдаются слабые рефлексы Al4C3, Cr5Al8, C, Mn0.545Al0.42C0.035. Локальный рентгеноспектральный анализ (рис. 6, табл. 2) показал наличие зерен тройного карбида Mn3AlC (1–4), MAX-фазы (CrxMn1 – x)2AlC (5, 6) и алюминида хрома AlCr2 (7, 8).
Рис. 5.
Дифрактограмма материала (слиток), полученного при горении смеси I + II (MnO2/Cr2O3/Al/C → → Mn2AlC/Cr2AlC + Al2O3).
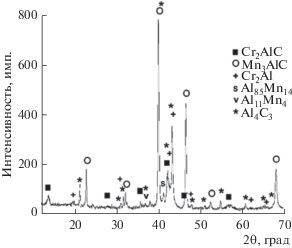
Рис. 6.
Микроструктура поверхности излома литого (слитка) композиционного материала, полученного при горении смеси I + II (MnO2/Cr2O3/Al/C → → Mn2AlC/Cr2AlC + Al2O3).
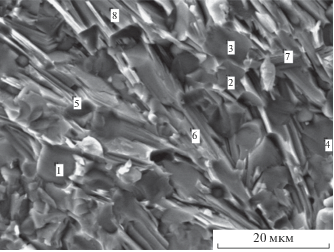
Таблица 2.
Элементный состав поверхности излома литого (слитка) композиционного материала, полученного при горении смеси I + II (MnO2/Cr2O3/Al/C → → Mn2AlC/Cr2AlC + Al2O3)
№ | C | Al | Mn | Cr | Фаза* |
---|---|---|---|---|---|
1 | 5.9 | 13.3 | 80.7 | 0.1 | Mn3AlC |
2 | 5.7 | 13.6 | 80.3 | 0.4 | Mn3AlC |
3 | 5.5 | 13.2 | 80.5 | 0.8 | Mn3AlC |
4 | 5.3 | 13.5 | 80.8 | 0.4 | Mn3AlC |
5 | 8.4 | 18.80 | 15.3 | 57.5 | (CrxMn1 – x)2AlC |
6 | 8.2 | 18.5 | 15.4 | 57.9 | (CrxMn1 – x)2AlC |
7 | 0.5 | 20.4 | 0.2 | 78.9 | AlCr2 |
8 | 0.6 | 20.7 | 0.1 | 78.6 | AlCr2 |
После хранения на воздухе синтезированный продукт также “деградировал” из слитка в порошок. РФА показал присутствие в материале тех же основных фаз: Mn3AlC, (CrxMn1 –x)2AlC, AlCr2. При этом на дифрактограмме исчезли рефлексы Al4C3 и появились рефлексы фазы AlO(OH) и С (рис. 7). По-видимому, фаза Al4C3 также разлагается (гидролиз) на воздухе за счет поглощения влаги. В пользу такого механизма диспергирования слитка в порошок свидетельствуют характерный вид (рис. 8) и состав (табл. 3) частиц материала и оксигидроксида алюминия (рис. 9, табл. 4).
ОБСУЖДЕНИЕ РЕЗУЛЬТАТОВ
В работах [19–21] отмечено, что присутствие в составе композитов фазы Al4C3 приводит к разрушению материала под действием влаги воздуха вследствие гидролиза, т.к. Al4C3, поглощая воду из окружающей среды, реагирует с ней с образованием CH4 и Al(OH)3. При этом обнаружено [21] , что карбид алюминия гидролизуется со скоростью ∼1%/ч. Было высказано предположение, что взаимодействие карбида алюминия с влагой воздуха происходит по следующим реакциям:
(1)
${\text{A}}{{{\text{l}}}_{{\text{4}}}}{{{\text{C}}}_{3}} + 18{{{\text{Н}}}_{{\text{2}}}}{\text{О}} \to 4{\text{Al}}{{\left( {{\text{ОН}}} \right)}_{3}} + 3{\text{С}}{{{\text{О}}}_{2}} + 12{{{\text{Н}}}_{{2,}}}$(2)
${\text{A}}{{{\text{l}}}_{{\text{4}}}}{{{\text{C}}}_{3}} + 12{{{\text{Н}}}_{{\text{2}}}}{\text{О}} \to 4{\text{Al}}{{\left( {{\text{ОН}}} \right)}_{3}} + 3{\text{С}}{{{\text{Н}}}_{4}}.$При СВС литых материалов конечные продукты (слитки) состоят, как правило, из зерен основных фаз: алюминидов и карбидов марганца и хрома, а фаза карбида алюминия располагается по границам этих зерен. Из анализа литературных данных [20, 21] и результатов проведенных экспериментов можно предположить следующие химические стадии механизма диспергирования литых материалов в системе Cr–Mn–Al–C:
(3)
${\text{A}}{{{\text{l}}}_{{\text{4}}}}{{{\text{C}}}_{3}} + {{\text{O}} \mathord{\left/ {\vphantom {{\text{O}} {{{{\text{Н}}}_{{\text{2}}}}{\text{О}}}}} \right. \kern-0em} {{{{\text{Н}}}_{{\text{2}}}}{\text{О}}}} \to {\text{A}}{{{\text{l}}}_{{\text{2}}}}{{{\text{О}}}_{3}} + {{{\text{C}}{{{\text{O}}}_{2}}} \mathord{\left/ {\vphantom {{{\text{C}}{{{\text{O}}}_{2}}} {{{{\text{С}}}_{{\text{2}}}}{{{\text{Н}}}_{2}}}}} \right. \kern-0em} {{{{\text{С}}}_{{\text{2}}}}{{{\text{Н}}}_{2}}}} \uparrow ,$(4)
${\text{A}}{{{\text{l}}}_{{\text{4}}}}{{{\text{C}}}_{3}} + {{{\text{Н}}}_{{\text{2}}}}{\text{О}} \to {\text{AlO}}\left( {{\text{ОН}}} \right) + {{{\text{С}}}_{{\text{2}}}}{{{\text{Н}}}_{2}}{\kern 1pt} \uparrow .$В результате этих реакций происходит выделение ацетилена, о чем свидетельствует характерный запах, а зерна Al4C3, расположенные между зернами основных фаз (карбидов и алюминидов марганца и хрома), превращаются в частицы Al2О3 или AlO(ОН), что приводит к разрушению компактности литых материалов и диспергированию в порошки. Реакция (3) соответствует механизму диспергирования литых материалов в системе Mn–Al–C, а реакция (4) – механизму диспергирования литых материалов в системе Cr–Mn–Al–C. Следует отметить относительную корреляцию полученных результатов с литературными данными. Некоторые отличия (наличие в продуктах диспергирования Al2О3, AlO(ОН) и С2Н2) можно объяснить различными объектами исследования.
ЗАКЛЮЧЕНИЕ
Показана возможность получения мелкодисперсных порошков при самопроизвольном диспергировании (без механического или химического воздействия агрессивных сред) литых материалов в системе Mn–Cr–Al–C.
Изучено влияние содержания карбида алюминия в слитках на их деградацию в порошкообразное состояние.
На основании результатов проведенных исследований и анализа литературных данных предложены химические стадии механизма диспергирования.
Изучены структурно-фазовые состояния целевых продуктов, полученных в системах Mn–Al–C и Cr–Mn–Al–C.
Список литературы
Guilemagy J.M., Espallargas N., Suegama P.H., Benedetti A.V. Comparative Study of Cr3C2–NiCr Coating // Corros. Sci. 2006. V. 48. № 10. P. 2998–3013. https://doi.org/10.1016/j.corsci.2005.10.016
Бурханов Г.С., Миляев И.М., Юсупов В.С. Современное состояние и тенденции развития магнитотвердых материалов // Перспективные материалы. 2011. № 11. С. 208–215.
Алымов М.И., Миляев И.М., Нурисламов А.Х., Юсупов В.С. Магнитотвердые сплавы на основе системы Mn–Al // Цв. металлы. 2015. № 1. С. 91–96.
Barsoum M.W. The MAX Phases: A New Class of Solids: Thermodynamically Stable Nanolaminates // Prog. Solid State Chem. 2000. V. 28. P. 201–281. https://doi.org/10.1016/S0079-6786(00)00006-6
Tian W.B., Wang P.L., Zhang G., Kan Y., Li Y., Yan D. Synthesis and Thermal and Electrical Properties of Bulk Cr2AlC // Scr. Mater. 2006. V. 54. P. 841–846. https://doi.org/10.1016/j.scriptamat.2005.11.009
Lin Z., Zhou Y., Li M. Synthesis, Microstructure, and Property of Cr2AlC // J. Mater. Sci. Technol. 2007. V. 23. № 6. P. 721–746.
Schneider J.M., Sun Z., Mertens R., Uestel F., Ahuja R. Ab-Initio Calculations and Experimental Determination of the Structure of Cr2AlC // Solid State Commun. 2004. V. 130. № 7. P. 445–449. https://doi.org/10.1016/j.ssc.2004.02.047
Lin S., Huang Y., Zu L., Kan X., Lin J., Song W., Tong P., Zhu X., Sun Y. Alloying Effects on Structural, Magnetic and Electric/Thermal Transport Properties in MAX phase Cr2 –xMxGeC (M = Ti, V, Mn, Fe and Mo) // J. Alloys Compd. 2016. V. 680. P. 452–461. https://doi.org/10.1016/j.jallcom.2016.04.197
Hamm C.M., Bocarsly J.D., Seward G., Kramm U.I., Birke C.S. Non-Conventional Synthesis and Magnetic Properties of MAX Phases (Cr/Mn)2AlC and (Cr/Fe)2AlC // J. Mater. Chem. C. 2017. V. 5. № 23. P. 5700–5708. https://doi.org/10.1039/C7TC00112F
Tian W., Vanmeensel K., Wang P., Zhang G., Li Y., Vleugels J., Biest O. Synthesis and characterization of Cr2AlC ceramics prepared by spark plasma sintering // Mater. Lett. 2007. V. 61. P. 4442–4445.
Xiao Li.O., Li S.B., Song G., Sloof W.G. Synthesis and Thermal Stability of Cr2AlC // J. Eur. Ceram. Soc. 2011. V. 31. P. 1497–1502.
Levashov E.A., Mukasyan A.S., Rogachev A.S., Shtansky D.V. Self-Propagating High-Temperature Synthesis of Advanced Materials and Coatings // Int. Mater. Rev. 2017. V. 62. № 4. P. 203–239. https://doi.org/10.1080/09506608.2016.1243291
Горшков В.А., Милосердов П.А., Лугинина М.А., Сачкова Н.В., Беликова А.Ф. Высокотемпературный синтез литого материала с максимальным содержанием МАХ-фазы Cr2AlC // Неорган. материалы. 2017. Т. 53. № 3. С. 260–266. https://doi.org/10.7868/S0002337X1703006X
Горшков В.А., Милосердов П.А., Сачкова Н.В., Лугинина М.А., Юхвид В.И. СВС-металлургия литых материалов на основе MAX-фазы Cr2AlC // Изв. вузов. Порошковая металлургия и функциональные покрытия. 2017. № 2. С. 47–54. https://doi.org/10.17073/1997-308X-2017-2-47-54
Ребиндер П.А., Щукин Е.Д. Поверхностные явления в твердых телах в процессах их деформации и разрушения // Успехи физ. наук. 1972. Т. 108. № 1. С. 26–36.
Gorshkov V.A., Miloserdov P.A., Ignat’eva T.I., Semenova V.N., Kovalev I D. AlON Powders by Aluminothermic SHS under Pressure: Synthesis and Characterization // Int. J. Self-Propag. High-Temp. Synth. 2017. V. 26. № 4. P. 240–243.
Игнатьева Т.И., Милосердова О.М., Семенова В.Н., Боровинская И.П. Химическое диспергирование как способ выделения ультра- и нанодисперсных порошков карбида титана // Перспективные материалы. 2009. № 3. С. 82–87.
Игнатьева Т.И., Баринова Т.В., Семенова В.Н., Баринов В.Ю. Выщелачивание порошков Si3N4 из продуктов СВС. Влияние процесса на морфологию и размер частиц // Междунар. журн. прикл. и фундаментальных исследований. 2017. № 11-1. С. 135–139.
Орданьян С.С., Несмелов Д.Д., Овсиенко А.И. Фазообразование в процессе реакционного спекания композитов B4C–SiC‒Si(Al) // Новые огнеупоры. 2017. № 12. С. 42–48. https://doi.org/10.17073/1683-4518-2017-12-42-48
Laipeng Yan, Zhanqiu Tan, Gang Ji, Zhiqiang Li, Genlian Fan, D. Schryvers, Aidang Shan, Di Zhang. A Quantitative Method to Characterize the Al4C3-Formed Interfacial Reaction: The Case Study of MWCNT/Al Composites // Mater. Character. V. 112 (2016). P. 213–216. https://doi.org/10.1016/j.matchar.2015.12.031
Hihara L.H. Corrosion of Aluminum-Matrix Composites // Corros. Rev. 1997. V. 15. P. 361–386.
Дополнительные материалы отсутствуют.
Инструменты
Неорганические материалы