Неорганические материалы, 2021, T. 57, № 9, стр. 925-932
Влияние механической активации иридия на его реакцию с тугоплавкими карбидами
Д. А. Банных 1, *, М. А. Голосов 1, В. В. Лозанов 1, Н. И. Бакланова 1
1 Институт химии твердого тела и механохимии СО Российской академии наук
630128 Новосибирск, ул. Кутателадзе, 18, Россия
* E-mail: denbannykh@gmail.com
Поступила в редакцию 10.03.2021
После доработки 21.04.2021
Принята к публикации 30.04.2021
Аннотация
Изучено твердофазное взаимодействие порошка иридия, в том числе подвергнутого механической обработке в мельнице, с порошками SiC и WC в интервале температур 800–1400°С. Взаимодействие иридия с SiC приводит к образованию различных силицидов иридия, состав и содержание которых зависят от температуры обработки реакционных смесей и размера частиц иридия. Взаимодействие иридия с WC приводит к образованию интерметаллической фазы WxIr1– x с широкой областью гомогенности. Установлено, что механическая обработка порошка иридия заметно ускоряет реакции твердофазного взаимодействия иридия и карбидов тугоплавких металлов, прежде всего за счет увеличения удельной поверхности иридия и накопления дефектов.
ВВЕДЕНИЕ
Иридий относится к группе благородных металлов и обладает исключительной химической инертностью по отношению к большинству реагентов даже при высоких температурах. Он является компонентом сверхвысокотемпературных сплавов для газотурбинных двигателей и ядерных реакторов, керамических покрытий и композиционных материалов для термостойких изделий [1–3]. Известно, что иридий используется также как компонент сверхвысокотемпературного “припоя” для интеграции отдельных керамических деталей в изделия сложной геометрической формы [4]. Подобные изделия могут работать в агрессивной среде при высоких тепловых нагрузках и находят применение в качестве термостойкой системы теплозащиты поверхности летательных аппаратов, компонентов силовых установок. Другая область применения иридия связана с разработкой ювелирных сплавов, электрокатализом, тонким химическим синтезом, медициной (например, контактная лучевая терапия) [5, 6]. Для использования иридия в качестве реагента требуется повысить его реакционную способность по отношению к другим компонентам, например тугоплавким соединениям и металлам, увеличив, таким образом, степень превращения иридия в целевой продукт. Реакционная способность иридия определяется рядом параметров, среди которых размер частиц и дефектность кристаллической решетки являются наиболее существенными.
Одним из способов получения иридия с повышенной реакционной способностью является термическое разложение его летучих металлорганических предшественников [7]. Разложение предшественника, например 1,5-циклооктадиен(ацетилацетонат) иридия (I) [Ir(acac)(cod)], в потоке водорода или кислорода при температуре 500–600°С приводит к образованию иридия с размером частиц 200–300 нм. В описываемом методе активность иридия повышается в первую очередь за счет образования частиц субмикронного размера. Методом электрохимического осаждения порошка иридия из солевых расплавов NaCl–KCl также можно получать частицы субмикронного размера (до 25 нм) с удельной поверхностью 6–16 м2/г [8, 9].
В работах [10, 11] предложен подход к получению металлических порошков, в том числе иридия, с повышенной реакционной способностью посредством механического воздействия в высокоэнергетической мельнице. Было установлено, что смеси порошков, основу которых составляют железо, кобальт, никель, а вторым компонентом является благородный металл, после обработки в высокоэнергетической мельнице лучше спекаются. Так, начало усадки обработанного порошка наблюдается при 992 К, при этом максимальная скорость усадки отмечена при 1288 К. Для необработанного иридиевого порошка усадка начинается только при 1144 К и максимальной скорости достигает при температуре 1376 К [10].
Целью настоящей работы является исследование взаимодействия порошка металлического иридия, подвергнутого механической обработке, с тугоплавкими карбидами – кремния и вольфрама. Системы на основе карбидов кремния и вольфрама в сочетании с иридием представляют большой интерес с точки зрения разработки высокотемпературных материалов, обладающих повышенной окислительной устойчивостью.
ЭКСПЕРИМЕНТАЛЬНАЯ ЧАСТЬ
В качестве исходных веществ были использованы порошки WC (ООО ИПК “Юмэкс”, Россия, содержит 5 мас. % примеси W2C) и α-SiC (Pacific Rundum Co., Ltd., Япония, чистота 98.6%). Гранулометрический состав исходных порошков был охарактеризован с помощью анализатора частиц Microsizer (ГОСТ Р 57923-2017). В качестве исходного использовали порошок иридия (ГОСТ 12338-81, Россия) с размером частиц D50 ~ 22 мкм. Размер частиц α-SiC составил D50 ∼ 1 мкм. Для изучения реакции иридия с карбидом вольфрама использовали порошки WC двух типов: крупный – с размером частиц D50 ∼ 3.7 мкм и мелкий – с размером частиц D50 ∼ 1.68 мкм, что сопоставимо с размерами частиц порошка SiC.
Механическую обработку порошков иридия осуществляли в планетарной мельнице Retsch PM 200 с использованием барабанов, футерованных WC, объемом 50 мл и мелющих тел из WC (диаметр 3 мм, масса 200 г) в воздушной атмосфере. Ускорение мелющих тел составляло 40 g, а время обработки 4–6 ч. Для механической обработки иридия в барабан загружали смесь, содержащую металлический иридий, хлорид натрия (интенсификатор размола) и этанол [12]. Массовое соотношение мелющих тел к загружаемой смеси составляло 5 : 1.
Для исследования взаимодействия иридия с карбидами вольфрама и кремния готовили смеси порошков Ir : WC и Ir : SiC в мольном соотношении 1 : 1. Смеси помещали в высоковакуумную печь СНВЭ-1,7.3.1,7/20 (ООО “Призма”, Россия), вакуумировали до остаточного давления 10–3 Па, затем нагревали до заданной температуры 1000–1400°С (область твердофазного взаимодействия для обеих систем) с шагом в 100°С. Время выдержки при заданной температуре составляло 1 ч, скорость нагрева 640°С/ч. Охлаждение образцов проводили при непрерывном вакуумировании.
Морфологию частиц исходных порошков и смесей после термообработки исследовали с помощью электронных микроскопов ТМ-1000, S-3400N (Hitachi Ltd., Япония) и MIRA 3 LMU (Tescan, Чехия). Элементный микроанализ был проведен с использованием приставок для элементного анализа SwiftedΤΜ, ThermoScientific® EDS detector и INCA Energy XMax (Oxford Instruments, GB) соответственно. Порошковые рентгенограммы исходных порошков и смесей были записаны в геометрии Брэгга–Брентано (θ–θ) на порошковом дифрактометре D8 Advance (Bruker, Германия) с характеристичным излучением Kα медного анода. Запись рентгенограмм проводилась в диапазоне углов 15° < 2θ < 120°. Качественный и количественный рентгенофазовый анализ (РФА) проводили с помощью программных пакетов Search-Match (Oxford Cryosystems, Великобритания) и TOPAS (Bruker, Германия) с использованием баз данных PDF-4 и ICSD.
РЕЗУЛЬТАТЫ И ОБСУЖДЕНИЕ
На рис. 1 представлены результаты сканирующей электронной микроскопии (СЭМ) исходного порошка иридия (а) и обработанного в мельнице (б). Из анализа снимков следует, что механическая обработка приводит не только к дезинтеграции агрегатов частиц, но и к изменению их формы – они становятся плоскими. Их толщина составляет менее 1 мкм. Образование плоских частиц может быть связано с пластической деформацией металла под воздействием мелющих тел. По данным анализа гранулометрического состава, значение D50 и D90 для иридия, обработанного в мельнице, составило 7.37 и 15 мкм, что значительно меньше значений для исходного порошка (D50 = = 22.03 мкм, D90 = 40 мкм). Отметим, что порошок иридия является полидисперсным как по данным СЭМ, так и по результатам гранулометрического анализа (рис. 1б, 1в). Согласно результатам РФА (рис. 2), пики, принадлежащие иридию, значительно уширились, размер областей когерентного рассеяния (ОКР) уменьшился до ∼40 нм (∼100 нм для исходного порошка), а микронапряжения кристаллической решетки возросли до ε = 0.784 ± 0.006. Плотность дислокаций для механически обработанного иридия, оцененная по формуле ρ = $\frac{{2\sqrt 3 \varepsilon }}{{Db}},$ связывающей плотность дислокаций с размером кристаллитов, вектором Бюргерса (для механически обработанного иридия b = $\frac{{\sqrt 2 a}}{2}$ ≈ 0.271 нм) и микроискажениями кристаллической решетки [13], составила величину 2.33 × 1013 см–2. Относительная погрешность составляет 2%. Значение плотности дислокаций гораздо выше значения, определенного для исходного иридия.
Рис. 1.
СЭМ-снимки исходного (а) и механически обработанного в мельнице (б) порошка иридия; гранулометрический состав порошка до и после механической обработки в мельнице (в).
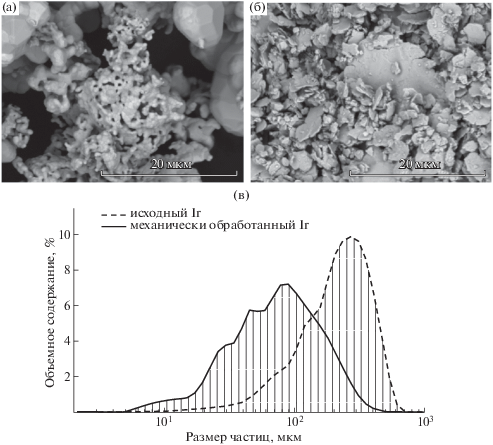
Рис. 2.
Дифрактограммы порошка иридия: исходного (1), механически обработанного в мельнице без (2) и c последующим термическим отжигом при 800°С (3).

Таким образом, в процессе измельчения и деформации в частицах иридия накапливаются внутренние и внешние дефекты, приводящие к микроискажениям кристаллической решетки, увеличивается плотность дислокаций, уменьшается значение ОКР, увеличивается удельная поверхность. Так, удельная поверхность иридия, оцененная по данным СЭМ, после механической обработки в мельнице существенно увеличилась (~0.47 м2/г против ~0.01 м2/г). Перечисленные факторы могут приводить к увеличению реакционной способности иридия при взаимодействии с карбидами. Следует подчеркнуть, что после отжига при температуре 800°С (~0.3tпл) микроискажения решетки иридия исчезают, а размер ОКР увеличивается до 95 ± 2 нм, что близко к значению, определенному для исходного иридия (рис. 2).
Качественный и количественный РФА позволил установить состав продуктов взаимодействия иридия с карбидом кремния, а также температуры появления отдельных фаз для обеих порошковых смесей – с исходным и механически обработанным иридием (рис. 3а, 3б). Для обоих типов смесей взаимодействие начинается при температуре 1000°С с образования фазы Ir3Si. Дальнейший нагрев до 1200°С приводит к увеличению содержания этой фазы в образцах с крупным иридием, а в образцах с механически обработанным иридием еще и к образованию фазы Ir3Si2. В продуктах, полученных при 1300°С с крупным иридием, появляются фазы Ir3Si2 и Ir2Si, а в образцах с механически обработанным иридием – фаза IrSi наряду с вышеупомянутыми фазами. Отметим, что в крупнодисперсных образцах фаза IrSi появляется только при 1400°С. Обобщая результаты РФА, можно заключить, что образование всех силицидных фаз в образцах с механически обработанным иридием происходит при более низких температурах, чем для смесей с крупным иридием, за исключением фазы Ir2Si, которая для мелкодисперсных смесей наблюдается только при 1400°С.
Рис. 3.
Дифрактограммы продуктов взаимодействия карбида кремния и иридия – исходного (а), механически обработанного (б).
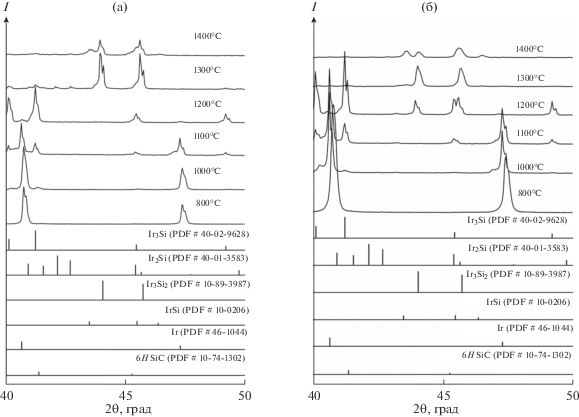
Для одних и тех же температур суммарное содержание (мол. %) силицидных фаз больше для смесей с механически обработанным иридием (рис. 4). Из рис. 4 следует, что реакция иридия с карбидом кремния ускоряется при температурах выше 1100°С (температура Таммана для иридия 1110°С [14]). Содержание продуктов реакции в мелкодисперсной порошковой смеси (с механически активированным порошком иридия и мелким порошком карбида кремния) при самой высокой исследованной нами температуре (1400°С) превышает содержание продуктов в смеси крупный порошок иридия + мелкий порошок SiC примерно в 2 раза. Эти результаты дают основание заключить, что увеличение удельной поверхности иридия после его механической обработки вносит, по-видимому, наиболее значимый вклад в ускорение этой реакции.
Рис. 4.
Зависимости суммарного содержания силицидов иридия от размера частиц в порошковых смесях Ir + SiC: 1 – исходный, 2 – механический обработанный порошок иридия.
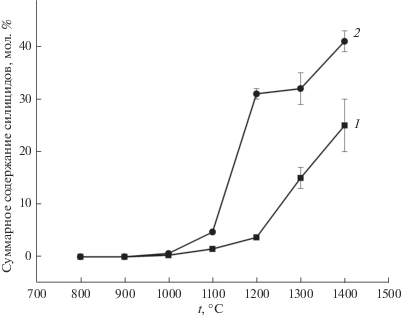
Из данных количественного РФА следует, что в реакции с механически активированным иридием образовалось продукта больше, однако сравнительный анализ морфологии продуктов реакции карбида кремния с исходным и механически активированным порошком иридия не позволяет подтвердить этот результат, так как во всех исследованных случаях зерна продуктов имеют неправильную форму и не обладают каким-либо отличительным габитусом (рис. 5а, 5б). Больше информации можно получить из анализа СЭМ-снимков сечений зерен. На СЭМ-снимках (режим обратнорассеянных электронов) сечений зерен порошков продуктов, полученных при 1400°С в реакции с исходным и обработанным в мельнице иридием, наблюдается характерная эвтектоидная микроструктура (рис. 5в, 5г). Элементный состав этой области близок к Ir2Si. Наблюдаемая микроструктура характерна для большого количества зерен. Можно предположить, что наблюдаемый эвтектоид образовался в результате распада фазы Ir2Si на Ir3Si и Ir3Si2, что находится в согласии с данными [14]. Как было отмечено выше, методом РФА была обнаружена фаза Ir2Si в продуктах реакции, однако ее содержание незначительно и составляет примерно 2 мол. % при температуре 1400°С. Причины стабилизации фазы Ir2Si пока не вполне понятны и требуют дальнейшего изучения.
Рис. 5.
СЭМ-снимки продуктов, образовавшихся при 1400°С в реакции с исходным (а) и механически активированным иридием (б); СЭМ/ЭДС-анализ сечений зерен продукта реакции SiC с исходным (в) и механически активированным иридием (г).
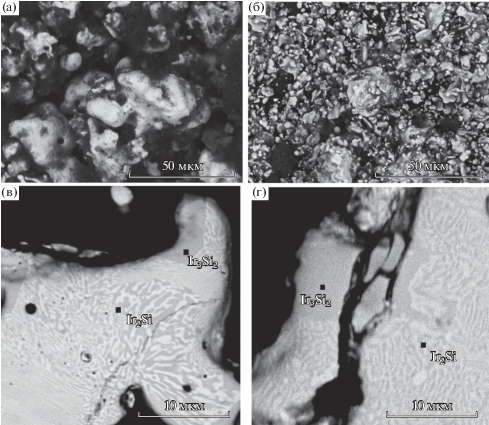
На рис. 6а, 6б представлены рентгенограммы продуктов реакции карбида вольфрама с исходным порошком иридия и механически обработанным в мельнице. Согласно данным качественного и количественного РФА (рис. 6а), после термообработки при 800°С смесей исходного порошка иридия с карбидом вольфрама (крупным и мелким) на рентгенограмме присутствуют рефлексы только фаз иридия, WC и W2C (примесь в исходном WC). Предварительная механическая обработка иридия приводит к увеличению скорости его взаимодействия с карбидом вольфрама и появлению малоинтенсивных рефлексов продукта реакции, интерметаллида WxIr1 – x, содержание которого, по данным РФА, составляет 5 мас. % при 800°С. Отметим, что смесь предварительно обработанного в мельнице порошка Ir и мелкого WC реагирует при 800°С еще быстрее, о чем свидетельствует повышение содержания WxIr1 – x до 10 мас. %. С использованием зависимости объема элементарной ячейки от состава (правила Вегарда) определили значение x для интерметаллида WxIr1 – x, которое оказалось равным ∼0.33. Таким образом, состав образующегося интерметаллида близок к WIr2.
Рис. 6.
Рентгенограммы продуктов взаимодействия иридия и карбида вольфрама при 800 (а) и 1000°С (б): 1 – исходный Ir + крупный WC; 2 – исходный Ir + мелкий WC, 3 – механически обработанный Ir + крупный WC, 4 – механически обработанный Ir + мелкий WC.
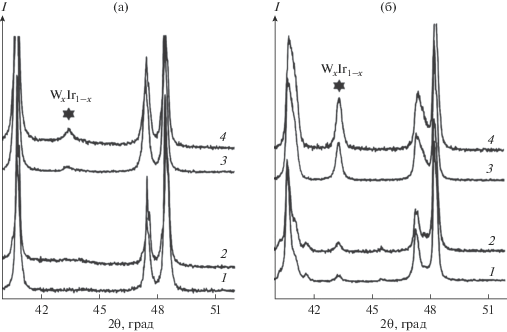
Как и для системы Ir–SiC, нагрев смесей порошков иридия и карбида вольфрама выше 1000°С приводит к увеличению скорости взаимодействия как между исходным порошком иридия и крупным порошком карбида вольфрама, так и между мелкими порошками (рис. 6б). Как следует из рис. 7, использование мелкого порошка WC не приводит к какому-либо значительному увеличению скорости реакции с иридием. Например, содержание интерметаллида составляет 3 и 4 мас. % для смесей с крупным и мелким WC соответственно. Содержание WxIr1– x в продуктах, полученных при 1000°С с использованием предварительно активированного иридия, в 4 раза выше и составляет 14 и 16 мас. % соответственно для смеси с крупным и мелким WC (рис. 7). Отметим, что для продукта с содержанием WxIr1 – x менее 15 мас. % относительная ошибка составляла ≤5%, более 15 мас. % – ≤1%. Таким образом, наиболее заметное влияние на скорость взаимодействия WC с Ir оказывает предварительная механическая обработка иридия.
Рис. 7.
Зависимости содержания иридида вольфрама после термообработки смесей иридия и карбида вольфрама в интервале температур 800–1400°С: 1 – исходный Ir + исходный WC, 2 – исходный Ir + механически обработанный WC, 3 – механически обработанный Ir + исходный WC, 4 – механически обработанный Ir + механически обработанный WC.
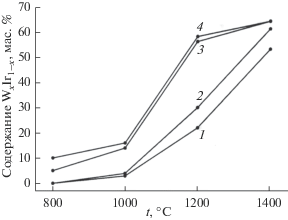
Согласно данным [15], при температурах 1000–1200°С взаимодействие WC и Ir (и для смеси 1 : 1, и для смеси 1 : 3) приводит к образованию фазы W0.245Ir0.755, состав которой близок к верхней границе области гомогенности твердого раствора WxIr1– x [16]. При температурах 1300–1400°С границы состава этой фазы расширяются и достигают значений W0.25Ir0.75 и W0.32Ir0.68 (WIr2). Можно отметить, что состав полученной в настоящей работе интерметаллической фазы также близок к WIr2. По данным количественного РФА, массовое содержание WxIr1– x при t = 1300–1400°С выходит на плато (для реакционной смеси с участием иридия, прошедшего механическую обработку). Полученный результат можно объяснить тем, что интерметаллид состава W0.33Ir0.67 является наиболее стабильной фазой по сравнению с другими составами разупорядоченного иридида вольфрама, что недавно было подтверждено термодинамическими расчетами энтальпий образования этих фаз [17].
Сравнительный анализ СЭМ-снимков продуктов, полученных при взаимодействии карбида вольфрама с исходным и механически обработанным порошком иридия, показывает, что существуют некоторые морфологические отличия. Так, морфология продукта взаимодействия исходного Ir с WC представлена крупными зернами непрореагировавшего иридия (подтверждено данными энергодисперсионной спектроскопии (ЭДС) анализа) и более мелкими зернами продукта (рис. 8а). С увеличением температуры доля мелких зерен продукта возрастает, особенно для пары механически обработанный Ir + WC (рис. 8б). Это наблюдение хорошо согласуется и с данными РФА: содержание интерметаллической фазы WxIr1 – x существенно увеличивается при температуре 1200°С.
ЗАКЛЮЧЕНИЕ
Изучено твердофазное взаимодействие крупнозернистого порошка иридия и порошка иридия, подвергшегося механической обработке, с порошками карбида кремния и карбида вольфрама в интервале температур 800–1400°С. Установлено, что взаимодействие иридия с SiC приводит к образованию различных силицидов иридия, состав и содержание которых зависят от температуры обработки реакционных смесей и размера частиц иридия. Взаимодействие иридия с WC приводит к образованию интерметаллической фазы WxIr1– x с широкой областью гомогенности. Полученные результаты сопоставлены с результатами для реакционных смесей, содержащих иридий, не подвергавшийся механической обработке. Сравнительный анализ показал, что механическая обработка порошка иридия заметно ускоряет реакции твердофазного взаимодействия иридия и карбидов тугоплавких металлов, прежде всего за счет увеличения удельной поверхности, а также накопления дефектов в структуре иридия.
Список литературы
Yamabe-Mitarai Y., Murakami H. Mechanical Properties at 2223 K and Oxidation Behavior of Ir Alloys // Intermetallics. 2014. V. 48. P. 86–92. https://doi.org/10.1016/j.intermet.2013.09.014
Ohriner E., Yang Y. Thermodynamic Analysis on Interactions of Silicon Dioxide with Iridium During Module Reduction and Monitoring Treatment // J. Phase Equilib. Diffus. 2018. V. 39. P. 532–537. https://doi.org/10.1007/s11669-018-0637-0
Lozanov V.V., Baklanova N.I., Bulina N.V., Titov A.T. New Ablation-Resistant Material Candidate for Hypersonic Applications: Synthesis, Composition, and Oxidation Resistance of HfIr3-Based Solid Solution // ACS Appl. Mater. Interfaces. 2018. V. 10. № 15. P. 13062–13072. https://doi.org/10.1021/acsami.8b01418
Cockeram B.V. Diffusion Bonded Silicon Carbide Having Iridium and Hermetic Silicon Carbide-Iridium Bonds: Pat. US, No. US 2019/0329519 A1, 2019.
Wang Y., Zhang L., Yin K., Zhang J., Gao H., Liu N., Peng Z., Zhang Z. Nanoporous Iridium-Based Alloy Nanowires as Highly Efficient Electrocatalysts toward Acidic Oxygen Evolution Reaction // ACS Appl. Mater. Interfaces. 2019. V. 11. № 43. P. 39728–39736. https://doi.org/10.1021/acsami.9b09412
Production Techniques and Quality Control of Sealed Radioactive Sources of Palladium-103, Iodine-125, Iridium-192 and Ytterbium-169 // Final Report No. IAEA-TECDOC-1512, IAEA, 2006. 148 p. https:// www-pub.iaea.org/MTCD/publications/PDF/ te_1512_ web.pdf
Лозанов В.В., Ильин И.Ю., Морозова Н.Б., Трубин С.В., Бакланова Н.И. Химическое осаждение из газовой фазы иридия на карбиды гафния и тантала. // Журн. неорган. химии. 2020. Т. 65. № 11. С. 1570–1578. https://doi.org/10.31857/S0044457X20110100
Зайков Ю.П., Исаков А.В., Аписаров А.П., Никитина А.О. Электрохимический синтез порошка иридия с высокой удельной поверхностью // Расплавы. 2016. Т. 6. С. 1–10.
Александров Е.П., Александров Д.Е., Казаков А.С. Свойства металлического нанопорошка иридия и его применение. Физико-химические аспекты предельных состояний и структурных превращений в сплошных средах, материалах и технических системах: Вып. 3 / Под общ. ред. Петрова Ю.В. СПб.: Политехника, 2019. С. 138–145. https://doi.org/10.25960/7325-1150-5-138
Шолль Р., Фистер Д., Шпикер К., Динх Л.Н. Способ получения тонкодисперсных металлических, легированных и композиционных порошков: Пат. РФ, № RU 2367542 C2, 2009.
Павлов Е.А., Мальцев Э.В., Гущинский А.А. Интенсификация процесса вскрытия упорных промпродуктов аффинажного производства. Часть 1. Влияние механоактивации на структуру и реакционную способность металлов спутников платины и материалов их содержащих // Изв. Самарского научного центра РАН. 2013. Т. 15. № 6-2. С. 432–437.
McCormick P.J, Tzuzuki T. Process for the Production of Ultrafine Powders of Metal Oxides: Pat. US, No. US 6503475 B1, 2003.
Ichiyanagi K., Takagi S., Kawai N., Fukaya R., Nozawa S., Nakamura K.G., Liss K.-D., Kimura M., Adachi S. Microstructural Deformation Process of Shock-Compressed Polycrystalline Aluminum // Sci. Rep. 2019. V. 9. P. 7604. https://doi.org/10.1038/s41598-019-43876-2
Sha J.B., Yamabe-Mitarai Y. Phase and Microstructural Evolution of Ir–Si Binary Alloys with fcc/Silicide Structure // Intermetallics. 2006. V. 14. P. 672–684. https://doi.org/10.1016/j.intermet.2005.11.005
Rybin V., Lozanov V., Utkin A., Matvienko A., Baklanova N. The Formation of Disordered Intermetallic Phase during the Solid-State Interaction of WC with Ir // J. Alloys Compd. 2019. V. 775. P. 503–510. https://doi.org/10.1016/j.jallcom.2018.10.118
Rapperport E.J., Smith M.F. Refractory Metal Constitution Diagrams // Technical Report No. WADD TR 60-132, Part II, Wright-Patterson Air Force Base, 1962. https://archive.org/stream/DTIC_AD0287548
Huang Y.-Y., Wu B., Li F., Chen L.-L., Deng Z.-X., Chang K. First-Principles and CALPHAD-Type Study of the Ir–Mo and Ir–W Systems // J. Min. Metall., Sect. B. 2020. V. 56. № 1. P. 109–118. https://doi.org/10.2298/JMMB190211001H
Дополнительные материалы отсутствуют.
Инструменты
Неорганические материалы