Неорганические материалы, 2022, T. 58, № 1, стр. 37-43
Магниетермическое получение порошков сплавов молибдена с хромом
В. Н. Колосов 1, *, М. Н. Мирошниченко 1, Т. Ю. Прохорова 1
1 Институт химии и технологии редких элементов и минерального сырья им. И.В. Тананаева – обособленное подразделение ФИЦ “Кольский научный центр Российской академии наук”
184209 Мурманская обл., Апатиты, Академгородок, 26а, Россия
* E-mail: v.kolosov@ksc.ru
Поступила в редакцию 09.07.2021
После доработки 29.09.2021
Принята к публикации 30.09.2021
- EDN: TTXSUP
- DOI: 10.31857/S0002337X22010079
Аннотация
Исследован процесс получения порошков сплавов молибдена с хромом восстановлением молибдата хрома Cr2(MoО4)3 парами магния в температурном интервале 700–800°С при остаточном давлении в реакторе 5–15 кПа. Получены порошки сплава Mo0.3Cr0.7, смеси сплавов Mo0.3Cr0.7 и Mo0.7Cr0.3, а также сплавов непрерывного ряда твердых растворов MoхCr1– х (0 < х < 1). Удельная поверхность порошков находится в интервале 33–48 м2/г. Полученные порошки характеризуются мезопористой структурой.
ВВЕДЕНИЕ
Молибден обладает высокой прочностью, хорошей тепло- и электропроводностью, а также коррозионной стойкостью [1, 2]. Поэтому он и его сплавы широко используются во многих областях техники [3]. Тем не менее, использование молибдена в качестве высокотемпературного конструкционного материала во многом ограничивается окислением при умеренных температурах [4, 5]. Окалина, образующаяся на молибдене, в зависимости от температуры и времени окисления состоит из двух или трех оксидных слоев. Внешним слоем является летучий MoO3. Внутренние слои состоят из субоксидов, которые имеют состав, близкий к MoO2. Внешний слой триоксида молибдена не является защитным, поэтому скорость окисления MoO2 до MoO3 на их границе раздела равна скорости диффузии кислорода через пленку субоксида к металлу [4]. Одним из способов подавления окисления молибдена является сплавление его с хромом, который преимущественно окисляется в сплаве и образует непрерывные слои оксида Cr2O3, защищающие молибден от окисления [6, 7]. Использование хрома в качестве антикоррозионного элемента обусловлено тем, что система молибден–хром является изоморфной с разрывом смешиваемости ниже 880°C [8], а свободная энергия Гиббса образования Cr2O3 более отрицательна, чем энергия образования оксидов молибдена [9]. Поэтому в системе Mo–Cr предпочтительнее окисляется хром по сравнению с молибденом. Сплавы Mo–Cr в разрыве смешиваемости имеют тенденцию разлагаться на ОЦК-фазу α-Мо, обогащенную хромом, и ОЦК-фазу α-Cr, обогащенную молибденом. Это явление, известное как “475° охрупчивание” [10], приводит к повышенной твердости и снижению пластичности со старением.
В качестве метода получения порошков сплавов молибдена с хромом обычно используют высокоэнергетический механический размол смеси порошков Mo и Cr в шаровых мельницах [11–14]. В работе [11] проводили размол в течение 24 и 48 ч при температуре окружающей среды смеси порошков Mo (250 меш) и Cr (325 меш) составов Mo75Cr25, Mo50Cr50 и Mo25Cr75. При этом показано, что 24 ч размола достаточно для полного смешивания компонентов с образованием твердых растворов металлов с кристаллической структурой ОЦК. Средний размер частиц порошков составил 21 нм. Авторы [13] синтезировали нанокристаллический твердый раствор Cr〈Mo〉 размолом порошковой смеси состава Mo35Cr65 течение 18 и 22 ч при температуре 260 K. Было установлено, что в процессе размола происходят циклические переходы между твердым раствором Cr〈Mo〉 и аморфной фазой Mo–Cr [13, 14]. По мере увеличения времени размола первоначально образующийся нанокристаллический твердый раствор Cr〈Mo〉 трансформируется в аморфный сплав Cr–Mo, который снова превращается в нанокристаллический твердый раствор. Недостатком получения сплавов путем размола компонентов является долговременное потребление энергии и загрязнение полученного продукта материалами измельчающей среды, в частности карбидом вольфрама [11]. Сплавы Cr–Mo получали также совместным электрохимическим осаждением компонентов из водных электролитов [15, 16]. Однако они имели очень низкое содержание молибдена (не более 2–3 мас. %) и были загрязнены водородом [16].
Представляет интерес исследовать возможность получения порошков сплавов Mo–Cr альтернативными методами. Ранее была показана возможность получения порошков сплавов W–Mo восстановлением парами магния двойных оксидных соединений этих металлов [17, 18]. При их восстановлении происходит снижение температуры сплавообразования за счет более плотной упаковки компонентов получаемого сплава и, тем самым, уменьшается диффузионный путь атомов при образовании твердого раствора вольфрама с молибденом.
Цель настоящей работы – исследование возможности получения порошка сплава Mo–Cr восстановлением парами магния двойного оксидного соединения, содержащего молибден и хром.
ЭКСПЕРИМЕНТАЛЬНАЯ ЧАСТЬ
В качестве прекурсора для получения сплавов Mo–Cr был выбран молибдат хрома Cr2(MoO4)3. Его выбор обусловлен тем, что он относится к семейству материалов A2M3O12, где A – трехвалентный переходный металл или лантаноид, а M – шестивалентный молибден или вольфрам [19]. Эти материалы характеризуются фазовым переходом от низкотемпературной моноклинной (пр. гр. P21/a) к высокотемпературной орторомбической (пр. гр. Pbcn) структуре [20]. Обе структуры являются микропористыми, образуя открытые межузельные бескатионные каркасы, состоящие из связанных вершинами октаэдров AO6 и тетраэдров MO4, где каждый октаэдр AO6 соединяется с тетраэдрами MO4 общим атомом кислорода. В своей высокотемпературной орторомбической модификации соединения A2M3O12 проявляют отрицательное тепловое расширение (ОТР), причины возникновения которого точно не установлены [19]. Температура фазового перехода молибдата хрома Cr2(MoO4)3 в состояние с ОТР составляет 380°C, значение коэффициента ОТР в интервале 380–800°С составляет –9.39 × 10–6°C–1 [21]. Вследствие ОТР при нагревании Cr2(MoO4)3 будет происходить сокращение расстояния Mo–Cr и, тем самым, уменьшаться диффузионный путь атомов при образовании сплава.
Молибдат хрома Cr2(MoO4)3 является востребованным материалом, который проявляет хорошие магнитные, электрические и каталитические свойства [22, 23]. Его получают методом осаждения или термическим разложением растворов хроматов и молибдатов [21, 22, 24], а также твердофазной реакцией между оксидами [23, 25]
(1)
${\text{C}}{{{\text{r}}}_{{\text{2}}}}{{{\text{O}}}_{{\text{3}}}}\left( {{\text{тв}}{\text{.}}} \right) + 3{\text{Mo}}{{{\text{O}}}_{{\text{3}}}}\left( {{\text{тв}}{\text{.}}} \right) = {\text{C}}{{{\text{r}}}_{{\text{2}}}}{{{\text{(Mo}}{{{\text{O}}}_{{\text{4}}}}{\text{)}}}_{{\text{3}}}}\left( {{\text{тв}}{\text{.}}} \right)$В настоящей работе для синтеза Cr2(MoO4)3 оксиды Cr2O3 и MoO3 с соотношением 1 : 3 перемешивали с помощью верхнеприводной мешалки в воде (Т : Ж = 1 : 5) в течение 3 ч. Скорость вращения мешалки 320 мин–1. После сушки на воздухе при температуре 80–85°С шихту спекали сначала при температуре 600°С, а затем 800°С в течение 5 ч при каждой температуре. В результате был получен чистый по данным рентгенофазового анализа (РФА) Cr2(MoO4)3 (рис. 1).
Аппаратура, методика получения и исследования порошков аналогичны использованным ранее [18]. Процесс вели в атмосфере паров магния и аргона (ВЧ). Емкость с магнием (М95) устанавливали на дно реакционного стакана. Навеску Cr2(MoO4)3 массой 5 г загружали в металлические тигли, которые устанавливали над емкостью с магнием. Над тиглями помещали экран, расстояние от которого до поверхности прекурсора составляло 27–30 мм. Реакционный стакан закрывали крышкой, в центре которой имелось отверстие для чехла термопары. Сборку помещали в реторту из нержавеющей стали, которую герметизировали, вакуумировали, заполняли аргоном и нагревали до требуемой температуры при закрытой крышке реакционного стакана. Процесс восстановления вели в температурном интервале 700–800°C и при остаточном давлении аргона в реакторе 5–15 кПа в течение 4 ч. Продукты реакции обрабатывали 15%-ным раствором азотной кислоты (“х. ч.”), а затем отмывали дистиллированной водой до нейтральной реакции раствора и сушили на воздухе при температуре 80°C. РФА проводили на дифрактометрах ДРОН-2 и SHIMADZU XRD-6000 (CuKα-излучение) с использованием базы PDF-4 (2021). Удельную поверхность и пористость порошков измеряли методами БЭТ и BJH на приборе TriStarII 3020 V1.03. Средний размер кристаллитов сплавов оценивали рентгеновским методом по формуле Шерера [26]
где форм-фактор K = 0.94, длина волны рентгеновского излучения λ = 0.15406 нм, β – ширина на половине высоты дифракционного пика в радианах, θ – угол Брэгга. Морфологический анализ порошков проводили с помощью сканирующего электронного микроскопа SEM LEO-420.РЕЗУЛЬТАТЫ И ОБСУЖДЕНИЕ
Реакция магниетермического восстановления молибдата хрома Cr2(MoO4)3 является экзотермической и протекает с выделением большого количества тепла. Использование в качестве восстановителя паров магния позволяет регулировать скорость их поступления в реакционную зону и, тем самым, ограничить температуру реакции, поддерживая ее постоянной в течение всего процесса восстановления значительно выше температуры фазового перехода молибдата хрома в состояние с ОТР.
Вид тиглей после восстановления Cr2(MoO4)3 представлен на рис. 2. Видно, что на поверхности реакционной массы, на внутренней боковой поверхности тиглей выше уровня загрузки прекурсора и на поверхности экрана, обращенной к прекурсору, имеются отложения вещества белого цвета. Согласно данным РФА, они представляют собой чистый оксид магния (рис. 3). Ранее было показано, что пространственное разделение металлической и оксидной фаз при восстановлении парами Mg или Ca ряда оксидных соединений металлов подгруппы хрома обусловлено протеканием электронно-опосредованных реакций без непосредственного физического контакта реагирующих веществ [27, 28]. При повышении остаточного давления аргона в реакторе доля соединения, восстанавливаемого в режиме электронно-опосредованных реакций, увеличивается и, тем самым, растет количество MgO на поверхности реакционной массы и на поверхности экрана, обращенной к прекурсору (рис. 2).
Рис. 2.
Тигли с реакционной массой (а–в) и соответствующие им экраны (г–е) после восстановления Cr2(MoO4)3: температура 750°C, остаточное давление аргона в реакторе: 5 (а, г), 10 (б, д), 15 кПа (в, е).
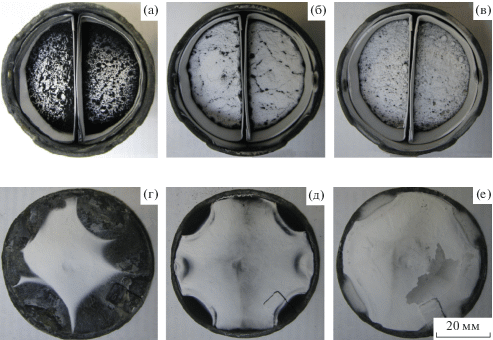
Рис. 3.
Дифрактограмма белого вещества с поверхности экрана после восстановления Cr2(MoO4)3: остаточное давление аргона в реакторе 15 кПа, температура 750°С.
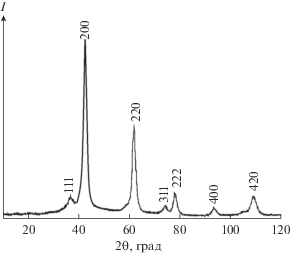
Мольное отношение молибдена к хрому в прекурсоре составляет 2 : 3. Следовательно, при восстановлении Cr2(MoO4)3 можно ожидать образования сплава с составом Mo0.6Cr0.4. Однако такой сплав получить не удалось. При полном восстановлении Cr2(MoO4)3 в большинстве случаев (при 700°С и давлении 5 кПа, 750°С и давлении 5 и 10 кПа, 800°С и давлении 15 кПа) продуктами реакции кроме MgO были сплав Mo0.3Cr0.7 и молибден (дифрактограммы 1 на рис. 4а, 4б). При этом после отмывки реакционной массы получали порошки сплава Mo0.3Cr0.7 (дифрактограмма 2 на рис. 4а, рис. 5а) или смесь этого сплава с молибденом (дифрактограмма 2 на рис. 4б). Восстановление Cr2(MoO4)3 при температуре 800°С и остаточном давлении 10 кПа приводит к образованию сплавов, соответствующих составам Mo0.3Cr0.7 и Mo0.7Cr0.3 (рис. 4в). Проведение процесса при такой же температуре, но более низком остаточном давлении приводит к образованию порошка непрерывного ряда твердых растворов MoхCr1 – х (0 < х < 1) (рис. 4г).
Рис. 4.
Дифрактограммы продуктов восстановления Cr2(MoO4)3 (1) и отмытого порошка (2): температура – 700 (а), 750 (б, д), 800°С (в, г); остаточное давление аргона в реакторе – 5 (а, г), 10 (б, в), 15 кПа (д).
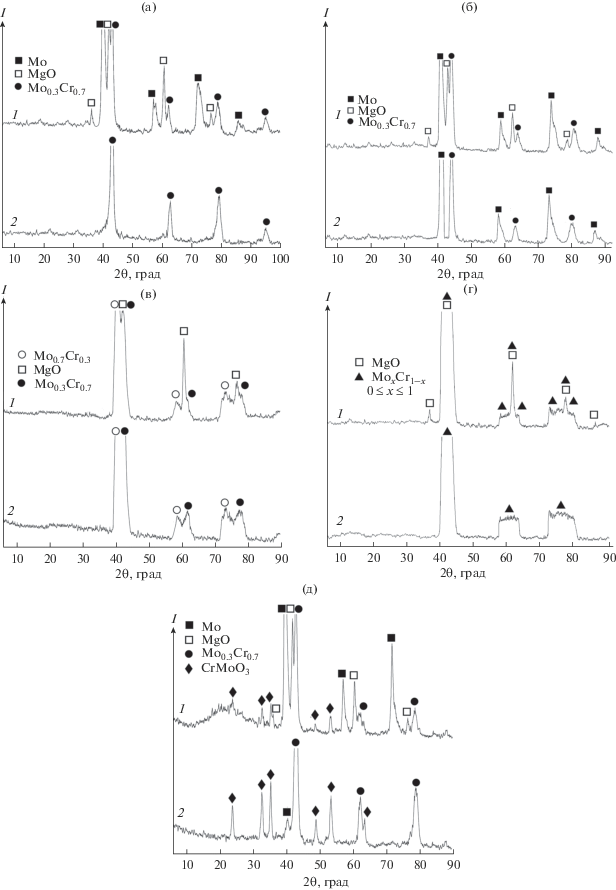
Рис. 5.
Продукты восстановления Cr2(MoO4)3 после отмывки и сушки: а – чистый сплав Mo0.3Cr0.7, б – смесь сплава Mo0.3Cr0.7, Mo и CrMoO3.
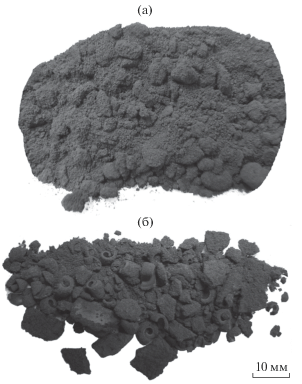
При неполном восстановлении прекурсора в продуктах реакции кроме MgO, Mo0.3Cr0.7 и Mo было обнаружено соединение CrMoO3 (рис. 4д). Оно не отмывалось из реакционной массы раствором азотной кислоты, а при высушивании отмытый продукт формировал твердую корку, при самопроизвольном разрушении которой ее отдельные фрагменты скручивались в спирали диаметром 4–5 мм (рис. 5б).
Удельная поверхность порошков сплавов, полученных восстановлением молибдата хрома, составила 33–48 м2/г. Высокоразвитая поверхность порошков обусловлена тем, что образующийся в процессе восстановления тугоплавкий оксид MgO, создавая прослойки между частицами образующегося сплава, затрудняет их коагуляцию. Остается значительным и количество нанопор после выщелачивания MgO, которые вносят основной вклад в удельную поверхность порошка сплава (рис. 6).
Рис. 6.
Зависимости поверхности пор от их среднего диаметра: удельная поверхность порошков сплава Mo0.3Cr0.7 – 33 (1), 39 (2), 48 м2/г (3).
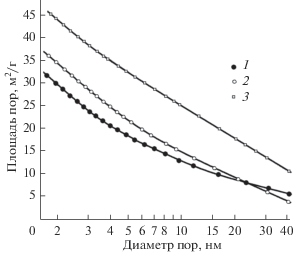
Согласно расчетам, выполненным по формуле (2), для полученных порошков сплавов молибдена с хромом средний размер кристаллитов находится на уровне 12–21 нм. При этом порошки представлены достаточно крупными агрегированными частицами размером 1–10 мкм (рис. 7).
Кривые адсорбции порошков сплавов, полученных при всех режимах восстановления молибдата хрома Cr2(MoO4)3, соответствуют IV типу по IUPAC. Они отличаются наличием петли гистерезиса и характерны для материалов с мезопористой структурой. Количество вещества, адсорбируемого порошками сплавов, полученных при одинаковых остаточных давлениях, больше для порошков, полученных при более низких температурах (рис. 8). Это обусловлено большей коагуляцией частиц порошка сплава при более высоких температурах.
Рис. 8.
Кривые адсорбции–десорбции азота порошков сплава Mo0.3Cr0.7 с удельной поверхностью 33 (а), 39 (б), 48 м2/г (в).
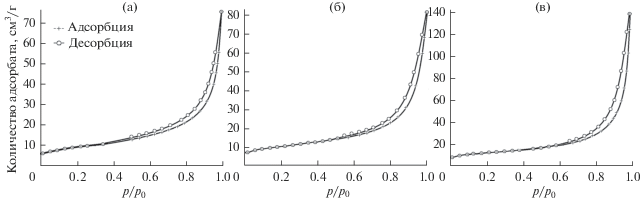
Таким образом, результаты исследований показали возможность получения порошков сплава молибдена с хромом с развитой поверхностью магниетермическим восстановлением Cr2(MoO4)3.
ЗАКЛЮЧЕНИЕ
Изучены закономерности восстановления молибдата хрома Cr2(MoO4)3 парами магния в температурном интервале 700–800°C при остаточном давлении аргона в реакторе 5–15 кПа. Исследованы характеристики полученных порошков сплавов молибдена с хромом.
Восстановление Cr2(MoO4)3 в приведенных выше условиях приводило к пространственному разделению металлической и оксидной фаз продуктов реакции, обусловленному протеканием электронно-опосредованной реакции без непосредственного физического контакта между Cr2(MoO4)3 и Mg.
Получены порошки сплава Mo0.3Cr0.7, смеси сплавов Mo0.3Cr0.7 и Mo0.7Cr0.3, а также непрерывного ряда твердых растворов MoхCr1– х (0 < х < 1) с удельной поверхностью 33–48 м2/г. Форма кривых адсорбции порошков сплавов соответствует IV типу по IUPAC, что подтверждает их мезопористую структуру.
Список литературы
Таблицы физических величин / Под ред. Кикоина И.К. М.: Атомиздат, 1976. 1008 с.
Xiao M., Li F., Xie H., Wang Y. Characterization of Strengthening Mechanism and Hot Deformation Behavior of Powder Metallurgy Molybdenum // Mater. Des. 2012. V. 34. № 2. P. 112–119.
Shields J.A. Applications of Molybdenum Metal and Its Alloys. London: IMOA, 2013. 42 p.
Jones E.S., Mosher J.F., Speiser R, Spretnak J.W. The Oxidation of Molybdenum // Corrosion. 1958. V. 14. № 1. P. 20–26. https://doi.org/10.5006/0010-9312-14.1.20
Зайцев А.А., Коротков Н.А., Лазарев Э.М. Окисление молибдена и молибден-вольфрамовых сплавов // Металловедение и термическая обработка металлов. 1976. № 10. С. 34–38. https://doi.org/10.1007/bf00705195
Дубинин Г.Н., Мулякаев Л.М. Термическая стабильность хромированного молибдена // Металловедение и термическая обработка металлов. 1969. № 11. С. 35–39. https://doi.org/10.1007/BF00655521
Lee D.-B., Simkovich G. Oxidation of Molybdenum-Chromium-Palladium Alloys // Oxidation Met. 1990. V. 34. № 12. P. 13–22.
Phase Equilibria, Crystallographic and Thermodynamic Data of Binary Alloys, Landolt-Börnstein, New Series IV, V. 5d / Ed. Madelung O. Berlin: Springer-Verlag, 1994.
Barin I., Platzki G. Thermochemical Data of Pure Substances. N.Y.: VCH. Weinheim, 1995.
Odusote Y.A., Popoola A.I. Thermodynamic and Surface Properties of Cr-X, (X = Mo, Fe) Liquid Alloys // Am. J. Condens. Matter Phys. 2017. V. 7. № 10. P. 57–66. https://doi.org/10.5923/j.ajcmp.20170703.01
Hahn J.D., Wu F., Bellon P. Cr–Mo Solid Solutions Forced by High-Energy Ball Milling // Metall. Mater. Trans. A. 2004. V. 35. № 10. P. 1105–1111. https://doi.org/10.1007/s11661-004-1013-8
Sun C.-F., Xi S.-Q., Zhang Y. et al. Thermodynamic Characteristic and Phase Evolution in Immiscible Cr–Mo Binary Alloys // Acta Metall. Sin. 2015. V. 28. № 8. P. 1074–1081. https://doi.org/10.1007/s40195-015-0297-6
Sun C.F., Xi S.Q., Zhang Y. et al. Synthesising Amorphous Cr–Mo Alloy via Mechanical Alloying of Immiscible Cr and Mo Elements // Mater. Res. Innov. 2015. V. 19. P. S1-308–S1-311. https://doi.org/10.1179/1432891715Z.0000000001493
Sun C., Hai X., Xi S. et al. New Insights of Solid-State Alloying and Amorphous-Nanocrystalline Cyclic Phase Transitions During Cr-40 wt. % Mo Powder Milling // J. Alloys Compd. 2018. V. 731. № 1. P. 667–677. https://doi.org/10.1016/j.jallcom.2017.10.083
Едигарян А.А., Полукаров Ю.М. Электроосаждение хрома и его сплавов из сульфатных растворов Cr(III) // Гальванотехника и обработка поверхности. 2001. Т. 9. № 3. С. 17–24.
Кузнецов В.В., Матвеев Д.В. Электроосаждение сплава хром-молибден из электролита на основе сульфата хрома // Электрохимия. 2008. Т. 44. № 6. С. 796–801. https://doi.org/10.1134/S1023193508060153
Колосов В.Н., Мирошниченко М.Н., Прохорова Т.Ю. Исследование получения порошков сплава Mо–W при восстановлении сложных оксидных соединений парами магния // Тр. Кольского науч. центра РАН. 2018. Вып. 9. Ч. 1. № 1. С. 285–289.
Kolosov V.N., Miroshnichenko M.N., Prokhorova T.Yu. Magnesiothermic Reduction of Molybdenum with Tungsten Double Oxides. IOP Science: Conf. Ser. 2019. V. 1347. P. 012128(1–5). https://doi.org/10.1088/1742-6596/1347/1/012128
Wu M.-Y., Wang L., Jia Y. et al. Theoretical Study of Hydration in Y2Mo3O12: Effects on Structure and Negative Thermal Expansion // AIP Advanc. 2015. V. 5. P. 027126(1–9). https://doi.org/10.1063/1.4913361
Marinkovic B.A., Jardim P.M., de Avillez R.R., Rizzo F. Negative Thermal Expansion in Y2Mo3O12 // Solid State Sci. 2015. V. 7. № 11. P. 1377–1383. https://doi.org/10.1016/j.solidstatesciences.2005.08.012
Tyagi A.K., Achary S.N., Mathews M.D. Phase Transition and Negative Thermal Expansion in A2(MoO4)3 System (A = Fe3+, Cr3+ and Al3+) // J. Alloys Compd. 2002. V. 339. № 1–2. P. 1377–1383.
Yadagiri M., Ramakrishna S., Ravi G. et al. Preparation, Characterization and Photocatalytic Studies of Cr2(MoO4)3 and Nitrogen-Doped Cr2(MoO4)3 // Chem. Chem. Technol. 2015. V. 9. № 4. P. 391–399. https://doi.org/10.23939/chcht09.04.391
Oudghiri-Hassani H. Synthesis, Characterization and Application of Chromium Molybdate for Oxidation of Methylene Blue Dye // J. Mater. Environ. Sci. 2018. V. 9. № 3. P. 1051–1057.
Forzatti P., Mari C.M., Villa P. Defect Structure and Transport Properties of Cr2(MoO4)3 and Al2(MoO4)3 // Mater. Res. Bull. 1987. V. 22. № 12. P. 1051–1057, 1593–1602. https://doi.org/10.1016/0025-5408(87)90001-8
Tabero P. Synthesis of Cr2(MoO4)3 // React. Kinet. Catal. Lett. 1999. V. 67. № 1. P. 137–141. https://doi.org/10.1007/bf02475839
Cullity B.D., Stock S.R. Elements of X-Ray Diffraction, 3rd ed. Prentice-Hall Inc., 2001.
Колосов В.Н., Орлов В.М. Электронно-опосредованные реакции при металлотермическом восстановлении оксидных соединений молибдена и вольфрама // Докл. РАН. 2019. Т. 484. № 4. С. 447–450. https://doi.org/10.31857/S0869-56524844447-450
Колосов В.Н., Орлов В.М., Мирошниченко М.Н. Восстановление кислородных соединений металлов V и VI групп парами кальция // Неорган. материалы. 2020. Т. 56. № 1. С. 37–43. https://doi.org/10.1134/S0002337X20010066
Дополнительные материалы отсутствуют.
Инструменты
Неорганические материалы