Неорганические материалы, 2022, T. 58, № 5, стр. 513-520
Силицирование карбидных фаз в системах Ti–Ta–C и Ti–Zr–C в газовой атмосфере SiO
И. М. Беляев 1, *, П. В. Истомин 1, Е. И. Истомина 1
1 Институт химии ФИЦ Коми НЦ УрО Российской академии наук
167000 Сыктывкар, ул. Первомайская, 48, Россия
* E-mail: 987ilya@gmail.com
Поступила в редакцию 03.12.2021
После доработки 11.01.2022
Принята к публикации 12.01.2022
- EDN: XMLDEY
- DOI: 10.31857/S0002337X22040017
Аннотация
Исследованы процессы силицирования порошков карбидных фаз в системах Ti–Ta–C и Ti–Zr–C в газовой атмосфере монооксида кремния при 1400°C. Установлено, что силицирование карбидных фаз в тройных системах Ti–Ta–C и Ti–Zr–C имеет селективный характер. Селективность силицирования проявляется в том, что при содержании TiC до 50 мол. % в карбидной смеси продуктами силицирующей обработки являются только силицидные фазы циркония и тантала: ZrSi, Ta5Si3 и TaSi2. При содержании TiC 80 мол. % и выше в системе Ti–Ta–C происходит образование МАХ-фазы Ti3SiC2.
ВВЕДЕНИЕ
Карбиды переходных металлов групп IVB-VB, в частности TiC, ZrC, TaC, известны как тугоплавкие материалы, характеризующиеся превосходными физико-химическими свойствами. Они обладают высокой твердостью (до 25 ГПа), высокой износостойкостью, чрезвычайно высокой температурой плавления (более 3200°C). Помимо этого, для этих карбидов характерны высокие электро- и теплопроводность. Такая комбинация свойств тугоплавких карбидов привлекает внимание как с научной, так и с технической точек зрения. Тугоплавкие карбиды считаются одними из наиболее перспективных кандидатов при создании высокотемпературных конструкционных материалов, устойчивых к тепловым ударам, износу и коррозии. Высокие твердость и износостойкость этих материалов особо ценятся в производстве режущих инструментов и при создании защитных покрытий на оптических и механических компонентах различных технических систем. Эти тугоплавкие карбиды также используются в микроэлектронике для хранения информации [1–5].
Низкая спекаемость монокарбидов TiC, ZrC, TaC и их твердых растворов затрудняет производство монолитных объемных изделий на их основе. Улучшению спекания способствует добавление небольшого количества металлов (Mo, Co, Ni), кремния или кремнийсодержащих соединений, таких как MoSi2, TaSi2. Известно, однако, что кремнийсодержащие спекающие добавки, как правило, снижают твердость и термохимическую стойкость тугоплавких карбидов при высоких температурах [6–9]. Данную проблему мы предлагаем решать альтернативным путем – химическим модифицированием поверхности карбидных порошков, которое заключается в предварительной стадии силицирования порошков карбидов в газовой атмосфере монооксида кремния (SiO). Такая обработка газом SiO позволит создать субмикронный карбид-кремниевый слой на карбидных зернах, который будет способствовать уплотнению порошков с применением методов спекания под давлением. Ранее этот подход был успешно реализован нами в работе [10] при силицировании порошков карбида титана TiC газом SiO, что приводило к образованию Ti3SiC2 и позволяло спекать порошки до состояния высокоплотной керамики при существенно более низких параметрах термобарического воздействия. К тому же рост фазы Ti3SiC2 на зернах TiC способствовал улучшению механических характеристик, таких как трещиностойкость и прочность. В работе [11] нами показано, что химическая модификация газом SiO поверхности порошков ZrC и TaC приводит к образованию силицидов соответствующих металлов. Спекание модифицированных порошков карбида тантала, выполненное в работе [12], также подтвердило перспективность развиваемого нами подхода, основанного на использовании предварительной стадии силицирования порошков тугоплавких карбидов.
Однако на сегодняшний день невыясненным остается вопрос о селективности силицирования карбидов переходных металлов групп IVB–VB газом SiO. В частности, не ясно, какие именно кремнийсодержащие фазы будут формироваться в случае силицирования карбидов, в металлической подрешетке которых содержится одновременно несколько различных элементов. Такая информация особенно важна при создании карбидной керамики из смесей тугоплавких карбидов или твердых растворов на их основе.
Цель данной работы заключалась в исследовании высокотемпературного силицирования порошков твердых растворов в системах Ti–Ta–C и Ti–Zr–C в газовой атмосфере SiO и изучении фазового состава полученных продуктов.
ЭКСПЕРИМЕНТАЛЬНАЯ ЧАСТЬ
В качестве исходных материалов были использованы: коммерческие порошки карбидов TaC (“ч.”, ТУ 6-09-03-33-75), ZrC (“ч.”, ТУ 6-09-03-408-75), TiC (“х. ч.”, ТУ-6-09-5050-82); порошок кремния Si (“х. ч.”); порошок диоксида кремния SiO2 (“ч. д. а.”, ГОСТ 9428-73). Карбидные смеси, содержащие твердые растворы (Ti,Ta)C, (Ta,Ti)C, (Ti,Zr)C и (Zr,Ti)C, были приготовлены путем многократного спекания порошковых смесей состава xTiC + (1 – x)TaC (x = 0.2, 0.5, 0.8); xTiC + + (1 – x)ZrC (x = 0.2, 0.5) в условиях вакуума при температуре 1700°C. Смешивание исходных компонентов проводили в лабораторной шаровой мельнице КМ-1 в течение 7 ч. Из приготовленной шихты компактировали таблетки, которые затем обжигали в вакуумной электропечи при температуре 1700°C в условиях вакуума в течение 6 ч. После этого спеченные образцы дезинтегрировали, перетирали, снова компактировали и обжигали при тех же условиях. Указанную процедуру повторяли несколько раз, чтобы общая продолжительность обжига при 1700°C составила не менее 24 ч для каждого образца.
Силицирование приготовленных карбидных смесей проводили в высокотемпературном лабораторном реакторе, обеспечивающем равномерное распределение потока газа SiO над зоной реакции и защиту печного оборудования от нежелательного воздействия паров SiO. Схема реактора представлена на рис. 1. Реактор состоял из пяти последовательно поставленных друг на друга корундовых тиглей тарельчатой формы марки КВПТ, в каждый из которых помещали исследуемый образец. В этих же тиглях размещали корундовые тигли меньшего размера с порошковой смесью Si + + SiO2, используемой в качестве реакционного источника SiO. Тигельную сборку накрывали корундовым колпаком для удерживания над исследуемыми порошками газовой атмосферы с высоким содержанием SiO. Газовые продукты силицирования и непрореагировавший SiO через технологические зазоры поступали в секцию с химическим поглотителем SiO – активированным углем марки БАУ-А. Собранный реактор помещали в вакуумную шахтную электропечь и проводили термическую обработку при непрерывной откачке газообразных продуктов. Режим термообработки включал в себя нагрев со скоростью 500°C/ч, изотермическую выдержку в течение 1 ч при 1400°C, охлаждение со скоростью 500°C/ч до 700°C и далее самопроизвольное охлаждение до комнатной температуры. До и после термической обработки проводили измерение массы образцов.
Фазовый состав образцов исследовали методом рентгенофазового анализа (РФА) с использованием дифрактометра Shimadzu XRD 6000 (CuKα-излучение, Ni-фильтр). Оценку количественного содержания кристаллических фаз проводили по рентген-дифракционным данным методом Ритвельда с помощью программы Powder Cell 2.4 [13]. Микроструктуру образцов изучали методом сканирующей электронной микроскопии (СЭМ) на микроскопе Tescan Vega 3 SBU. Локальный элементный состав образцов исследовали методом рентгеноспектрального микроанализа (РСМА) с помощью энергодисперсионного микроанализатора X-act, совмещенного с электронным микроскопом.
РЕЗУЛЬТАТЫ И ОБСУЖДЕНИЕ
Рентгенограммы образцов карбидных смесей TiC + TaC и TiC + ZrC, прошедших термообработку при 1700°C, представлены на рис. 2. Составы порошковых карбидных смесей TiC + TaC и TiC + ZrC до и после термообработки представлены в табл. 1. Установлено, что в результате многократной термической обработки при 1700°C в порошковых смесях, содержащих пáры индивидуальных карбидов, происходит образование следующих твердых растворов: 1) карбида тантала, допированного титаном (Ta,Ti)C; 2) карбида титана, допированного танталом (Ti,Ta)C; 3) карбида циркония, допированного титаном (Zr,Ti)C; 4) карбида титана, допированного цирконием (Ti,Zr)C. На рентгенограммах всех образцов наблюдается смещение и уширение рентгеновских пиков твердых растворов по сравнению с пиками соответствующих индивидуальных карбидов. Уширение пиков, особенно в дальней области углов 2θ, указывает на то, что в ходе продолжительного спекания смесей карбидов происходит внедрение атомов титана в кристаллическую решетку карбидов тантала и циркония с образованием твердых растворов. Смещение рентгеновских пиков это подтверждает. Так, рентгеновские пики твердых растворов на основе карбида титана (Ti,Ta)C и (Ti,Zr)C смещены в сторону меньших углов 2θ, пики твердых растворов на основе карбидов тантала и циркония (Ta,Ti)C и (Zr,Ti)C смещены в сторону больших углов 2θ. Количественное содержание твердых растворов в образцах, рассчитанное по рентгеновским данным, зависит от исходного состава карбидных порошковых смесей и от взаимной растворимости титана в кристаллических решетках карбидов тантала и циркония.
Рис. 2.
Рентгенограммы образцов I–V карбидных смесей TiC + TaC и TiC + ZrC, прошедших термообработку при 1700°C (см. табл. 1).
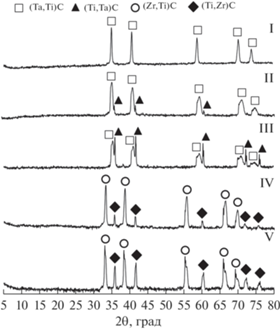
Таблица 1.
Составы карбидных смесей до и после термообработки
Исходный состав карбидных смесей | Фазовый состав образцов после термообработки (по данным РФА), об. % | Обозначение образца | |||
---|---|---|---|---|---|
смесь TiC + TaC | смесь TiC + ZrC | ||||
(Ti,Ta)C | (Ta,Ti)C | (Ti,Zr)C | (Zr,Ti)C | ||
0.2TiC + 0.8TaC | – | 100 | I | ||
0.5TiC + 0.5TaC | 6 | 94 | II | ||
0.8TiC + 0.2TaC | 80 | 20 | III | ||
0.2TiC + 0.8ZrC | 15 | 85 | IV | ||
0.5TiC + 0.5ZrC | 50 | 50 | V |
Микроструктуры образцов карбидных смесей, прошедших термообработку при 1700°C, показаны на рис. 3. Во всех образцах выявлен контраст фаз, связанный с тем, что полученные карбидные порошки представляют собой смеси твердых растворов. Методом РСМА установлено, что фаза, имеющая темный оттенок, это преимущественно твердые растворы на основе карбида титана – (Ti,Ta)C и (Ti,Zr)C. Фаза, имеющая светлый оттенок, – это твердые растворы на основе карбида тантала (Ta,Ti)C либо карбида циркония (Zr,Ti)C. Количественное содержание элементов в образцах, исследованное методом РСМА, представлено в табл. 2. В целом эти результаты согласуются с рентгеновскими данными.
Рис. 3.
Микроструктуры образцов карбидных смесей TiC + TaC и TiC + ZrC, прошедших термообработку при 1700°C: II (а), III (б), V (в) (см. табл. 1).
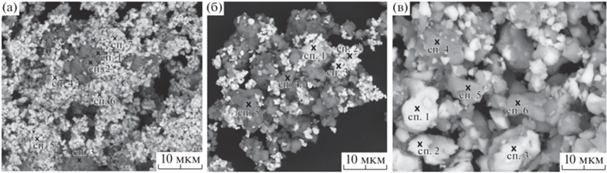
Таблица 2.
Локальный элементный состав карбидных смесей TiC + TaC и TiC + ZrC, прошедших термообработку при 1700°C (см. рис. 3)
Образец | № спектра | Элементный состав, ат. % | |||
---|---|---|---|---|---|
Ti | Ta | Zr | C | ||
II | 1 | 41 | 1 | − | 58 |
2 | 44 | 1 | − | 55 | |
3 | 47 | 1 | − | 52 | |
4 | 16 | 17 | − | 67 | |
5 | 15 | 14 | − | 71 | |
6 | 17 | 19 | − | 64 | |
7 | 15 | 17 | − | 68 | |
III | 1 | 39 | 9 | − | 52 |
2 | 10 | 22 | − | 68 | |
3 | 11 | 12 | − | 77 | |
4 | 35 | 1 | − | 64 | |
5 | 61 | 1 | − | 38 | |
V | 1 | 3 | − | 43 | 54 |
2 | 7 | − | 26 | 67 | |
3 | 6 | − | 23 | 71 | |
4 | 34 | − | 2 | 64 | |
5 | 30 | − | 4 | 66 | |
6 | 29 | − | 2 | 69 |
На полученных образцах (I–V), содержащих смеси твердых растворов (Ta,Ti)C и (Ti,Ta)C, (Zr,Ti)C и (Ti,Zr)C, исследовали процессы высокотемпературного силицирования газом SiO. Исходные массы образцов и порошковой смеси Si + SiO2, используемой в качестве источника SiO, представлены в табл. 3.
Таблица 3.
Исходные массы компонентов для силицирования карбидных смесей и их фазовый состав после силицирования
Обра-зец | Масса, г | ∆m, % | Фазовый состав образцов после силицирования (по данным РФА), об. % | Обозначение после силициро-вания | ||||||||
---|---|---|---|---|---|---|---|---|---|---|---|---|
образ-ца | смеси Si + SiO2 | смесь TiC + TaC | смесь TiC + ZrC | |||||||||
(Ta,Ti)C | (Ti,Ta)C | TaSi2 | Ta5Si3 | Ti3SiC2 | (Zr,Ti)C | (Ti,Zr)C | ZrSi | |||||
I | 15 | 3.5 | 0.5 | 82 | – | 7 | 11 | – | I-1 | |||
25 | 7.0 | 1.3 | 70 | – | 10 | 20 | – | I-2 | ||||
II | 25 | 3.5 | 0.7 | 90 | 6 | 2 | 2 | – | II-1 | |||
25 | 7.0 | 1.2 | 83 | 6 | 6 | 5 | – | II-2 | ||||
III | 10 | 2.5 | 2.6 | 20 | 60 | – | – | 20 | III-1 | |||
10 | 5.0 | 3.4 | 18 | 57 | – | – | 25 | III-2 | ||||
10 | 7.0 | 3.9 | 17 | 55 | – | – | 28 | III-3 | ||||
IV | 15 | 3.5 | 3.0 | 75 | 13 | 12 | IV-1 | |||||
25 | 7.0 | 4.3 | 67 | 13 | 20 | IV-2 | ||||||
V | 20 | 3.5 | 3.8 | 47 | 48 | 5 | V-1 |
В ходе проведения высокотемпературного силицирования наблюдалось изменение масс всех участвующих компонентов. Было установлено, что в результате термической обработки при 1400°C происходит уменьшение массы реакционной смеси Si + SiO2 и в зависимости от ее исходной загрузки потери массы достигали 95%. Это хорошо согласуется с нашими предыдущими опубликованными результатами, например в работах [10–12]. В них показано, что эквимолярная порошковая смесь Si + SiO2 является эффективным источником газа SiO. Помимо этого, в работах [14, 15] установлено, что при температуре 1400°C парциальное давление газа SiO над смесью Si + SiO2 достигает 800–900 Па, а его концентрация в газовой фазе близка к 100%.
Весовой анализ карбидных смесей, содержащих твердые растворы, показал, что в результате силицирующей обработки газом SiO происходит увеличение массы образцов. По результатам весового анализа было рассчитано относительное увеличение массы образцов (∆m). Эта величина связана с протеканием процессов силицирования и может быть использована в качестве характеристики степени силицирования. Установлено, что прибавка массы образцов зависит от исходной загрузки порошков и от исходной массы реакционной смеси Si + SiO2. С увеличением исходной массы источника газа SiO прибавка массы карбидных смесей линейно возрастала. Это свидетельствует о том, что в ходе силицирующей термообработки образующийся газ SiO взаимодействовал с твердыми растворами.
Анализ фазового состава образцов после силицирования газом SiO показал, что в продуктах присутствовали только бескислородные кремнийсодержащие кристаллические фазы (рис. 4, 5, табл. 3). В случае силицирования образцов I и II происходит образование силицидов тантала Ta5Si3 и TaSi2, суммарное содержание которых достигает 30 об. % в зависимости от исходного состава карбидной смеси и от степени силицирования. В случае силицирования образца III, в котором содержание твердого раствора (Ti,Ta)C составляло 80 об. %, происходит образование карбидосилицида титана Ti3SiC2 без присутствия других силицидных фаз. Содержание Ti3SiC2 может достигать 28 об. % в зависимости от степени силицирования. Силицирование образцов IV и V в газовой атмосфере SiO приводит к образованию силицида циркония ZrSi независимо от состава твердых растворов. Количественное содержание фазы ZrSi в образцах IV и V после силицирования может достигать 20 об. % в зависимости от степени силицирования.
Рис. 4.
Рентгенограммы образцов I-1, II-1, III-1 твердых растворов (Ta,Ti)C и (Ti,Ta)C после силицирования газом SiO (см. табл. 3).
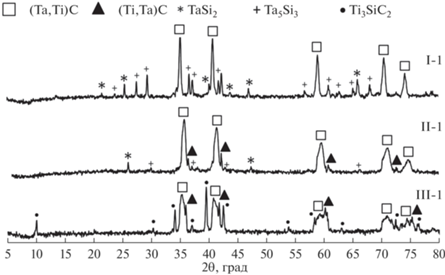
Рис. 5.
Рентгенограммы образцов IV-1, V-1 твердых растворов (Zr,Ti)C и (Ti,Zr)C после силицирования газом SiO (см. табл. 3).
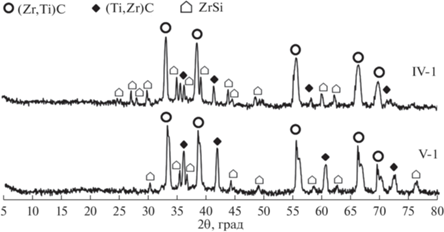
Полученные результаты согласуются с нашими предыдущими работами, в которых показано, что высокотемпературное силицирование стехиометрических монокарбидов титана, тантала и циркония газом SiO сопровождается образованием MAX-фазы Ti3SiC2, силицидов тантала и циркония соответственно. В связи с этим ожидалось, что в ходе процессов силицирования карбидных фаз будут образовываться смеси указанных продуктов. Однако, как мы видим, это совсем не так. В случае силицирования карбидных фаз в системе TiC–TaC происходит образование либо силицидов тантала, либо MAX-фазы Ti3SiC2 в зависимости от исходного состава и содержания твердых растворов (Ta,Ti)C и (Ti,Ta)C. Смесь карбидосилицида титана и силицидов тантала не образуется. В случае силицирования карбидных фаз в системе TiC–ZrC происходит образование только силицида циркония ZrSi, а MAX-фаза Ti3SiC2 вообще не образуется независимо от исходного состава и содержания твердых растворов (Zr,Ti)C и (Ti,Zr)C. Все это позволяет судить о селективном характере протекания процессов силицирования с участием газа SiO. На состав продуктов силицирования порошков твердых растворов в системах Ti–Ta–C и Ti–Zr–C оказывает влияние природа самого карбида и его содержание в карбидной смеси.
На рис. 6 представлены микроструктуры образцов твердых растворов после силицирования в газовой атмосфере SiO. В табл. 4 представлены данные по локальному элементному составу в силицированных образцах. При исследовании образцов методом СЭМ в режиме отраженных электронов, дающим информацию о локальном составе по композиционному контрасту, кристаллические фазы, идентифицированные методом РФА, хорошо различимы. Установлено, что в карбидных смесях, содержащих твердые растворы и прошедших силицирующую обработку газом SiO, присутствуют области с высоким содержанием кремния (табл. 4). Кремнийсодержащие фазы достаточно равномерно распределены по всему исследуемому материалу. При этом рост частиц, содержащих кремний, в ходе силицирования происходил непосредственно на поверхности карбидных частиц. После силицирования газом SiO микроструктура порошков карбидных фаз, содержащих твердые растворы, претерпевает заметные изменения. Силицирование оказывает влияние на морфологию зерен порошков, вследствие чего карбидные зерна становятся более округлыми и спекшимися. Более глубокое высокотемпературное силицирование карбидных фаз приводит к тому, что зерна образцов твердых растворов полностью покрываются силицидной фазой. Следует отметить, что морфология образца III, прошедшего силицирующую обработку газом SiO (образцы III-1–III-3), существенно отличается от таковой для других образцов. Например, на рис. 7 представлена микроструктура образца III-2. По всем морфологическим и микроструктурным признакам кремнийсодержащая фаза имеет явную слоисто-пластинчатую форму и образуется в виде маленьких ступенек преимущественно на зернах фазы, содержащей карбид титана, – (Ti,Ta)C. Известно, что такую микроструктуру имеют MAX-фазы, к которым в т. ч. относится карбидосилицид титана Ti3SiC2, его наличие было выявлено методом РФА.
Рис. 6.
Микроструктуры образцов твердых растворов после силицирования газом SiO: II-1 (а), III-2 (б), V-1 (в) (см. табл. 3).
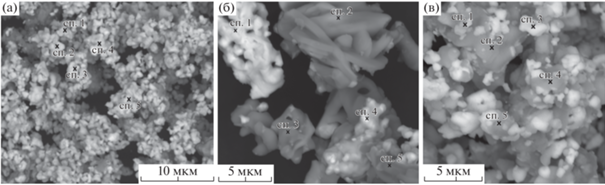
Таблица 4.
Локальный элементный состав образцов твердых растворов после силицирования газом SiO (см. рис. 6)
Образец | Спектр | Элементный состав, ат. % | ||||
---|---|---|---|---|---|---|
Ti | Ta | Zr | C | Si | ||
II-1 | 1 | 17 | 14 | − | 65 | 4 |
2 | 29 | 21 | − | 48 | 2 | |
3 | 14 | 20 | − | 60 | 6 | |
4 | 13 | 17 | − | 64 | 6 | |
5 | 12 | 14 | − | 68 | 6 | |
III-2 | 1 | 31 | 14 | − | 52 | 3 |
2 | 43 | 1 | − | 49 | 7 | |
3 | 22 | 1 | − | 76 | 1 | |
4 | 27 | 4 | − | 68 | 1 | |
5 | 20 | 1 | − | 78 | 1 | |
V-1 | 1 | 20 | − | 9 | 70 | 1 |
2 | 24 | − | 3 | 72 | 1 | |
3 | 6 | − | 20 | 73 | 1 | |
4 | 37 | − | 7 | 55 | 1 | |
5 | 22 | − | 5 | 72 | 1 |
ЗАКЛЮЧЕНИЕ
Спеканием порошковых карбидных смесей TiC + TaC и TiC + ZrC в условиях вакуума при 1700°C были получены твердые растворы (Ti,Ta)C, (Ta,Ti)C, (Ti,Zr)C, (Zr,Ti)C. Проведены исследования по высокотемпературному силицированию этих твердых растворов в газовой атмосфере SiO. Установлено, что фазовый состав твердых растворов после силицирования газом SiO зависит от исходного состава карбидных смесей. Так, для образцов, содержащих до 50 мол. % TiC и TaC, характерно образование силицидов тантала Ta5Si3 и TaSi2, а для образца, содержащего 80 мол. % TiC и 20 мол. % TaC, характерно образование карбидосилицида титана Ti3SiC2. В случае силицирования смеси твердых растворов (Ti,Zr)C и (Zr,Ti)C основным продуктом является силицид циркония ZrSi.
Таким образом, процесс силицирования имеет селективный характер, проявляющийся в том, что при содержании TiC до 50 мол. % продуктами силицирующей обработки являются только силицидные фазы циркония и тантала: ZrSi, Ta5Si3 и TaSi2; образования кремнийсодержащей МАХ-фазы Ti3SiC2 либо твердых растворов на ее основе в указанных условиях не происходит.
Кроме этого, силицирование газом SiO оказывает положительное влияние на микроструктуру порошков твердых растворов, вследствие чего карбидные зерна приобретают более округлый вид по сравнению с исходными карбидными порошками. Такой эффект очень важен при дальнейшем использовании этих образцов для получения высокоплотной керамики с применением методов спекания под давлением.
Список литературы
Pierson H.O. Handbook of Refractory Carbides and Nitrides: Properties, Characteristics, Processing and Applications. N.Y.: Noyes, 1996. 362 p. https://www.elsevier.com/books/handbook-of-refractory-carbides-and-nitrides/pierson/978-0-8155-1392-6
Wang C.R., Yang J.-M., Hoffman W. Thermal Stability of Refractory Carbide/Boride Composites // Mater. Chem. Phys. 2002. V. 74. № 3. P. 272–281. https://doi.org/10.1016/S0254-0584(01)00486-2
Bansal N.P. Handbook of Ceramic Composites. Boston: Springer, 2005. 554 p. https://doi.org/10.1007/b104068
Wuchina E., Opila E., Opeka M., Fahrenholtz W., Talmy I. UHTCs: Ultra-High Temperature Ceramic Materials for Extreme Environment Applications // Electrochem. Soc. Interface. 2007. V. 16. № 4. P. 30–36. https://www.electrochem.org/dl/interface/wtr/wtr07/ wtr07_p30-36.pdf
Shabalin I.L. Ultra-High Temperature Materials II. N.Y.: Springer, 2019. 755 p. https://doi.org/10.1007/978-94-024-1302-1
Sciti D., Silvestroni L., Guicciardi S., Fabbriche D.D., Bellosi A. Processing, Mechanical Properties and Oxidation Behavior of TaC and HfC Composites Containing 15 vol. % TaSi2 or MoSi2 // J. Mater. Res. 2009. V. 24. № 6. P. 2056–2065. https://doi.org/10.1557/jmr.2009.0232
Silvestroni L., Sciti D., Balat-Pichelin M., Charpentier L. Zirconium Carbide Doped with Tantalum Silicide: Microstructure, Mechanical Properties and High Temperature Oxidation // Mater. Chem. Phys. 2013. V. 143. № 1. P. 407–415. https://doi.org/10.1016/j.matchemphys.2013.09.020
Pirso J., Viljus M., Letunovits S. Sliding Wear of TiC–NiMo Cermets // Tribology Int. 2004. V. 37. № 10. P. 817–824. https://doi.org/10.1016/j.triboint.2004.04.009
Geng G., Liu L., Wang Y., Hai W., Sun W., Chen Y., Wu L. Microstructure and Mechanical Properties of TaC Ceramics with 1–7.5 mol. % Si as Sintering Aid // J. Am. Ceram. Soc. 2017. V. 100. № 6. P. 2461–2470. https://doi.org/10.1111/jace.14806
Istomin P., Istomina E., Nadutkin A., Grass V. Effect of Silicidation Pretreatment with Gaseous SiO on Sinterability of TiC Powders // Int. J. Refract. Met. Hard Mater. 2016. V. 57. P. 12–18. https://doi.org/10.1016/j.ijrmhm.2016.02.004
Беляев И.М., Истомин П.В., Истомина Е.И. Силицирование порошков карбидов тантала и циркония в газовой атмосфере SiO // Неорган. материалы. 2018. Т. 54. № 8. С. 823–830. https://doi.org/10.1134/S0002337X1808002X
Беляев И.М., Истомин П.В., Истомина Е.И., Лысенков А.С., Ким К.А. Получение и свойства керамики на основе карбида тантала, модифицированного газом SiO // Новые огнеупоры. 2020. № 11. С. 27–33. https://doi.org/10.17073/1683-4518-2020-11-27-33
Kraus W., Nolze G. Powder cell – a Program for the Representation and Manipulation of Crystal Structures and Calculation of the Resulting X-ray Powder Patterns // J. Appl. Crystallogr. 1996. V. 29. P. 301–303. https://doi.org/10.1107/S0021889895014920
Казенас Е.К., Цветков Ю.В. Испарение оксидов. М.: Наука, 1997. 543 с.
Ferguson F.T., Nuth J.A. Vapor Pressure of Silicon Monoxide // J. Chem. Eng. Data. 2008. V. 53. P. 2824–2832. https://doi.org/10.1021/je800560b
Дополнительные материалы отсутствуют.
Инструменты
Неорганические материалы