Неорганические материалы, 2022, T. 58, № 6, стр. 658-665
Поверхностное внутреннее трение в высокодобротных резонаторах из кварцевого стекла
Б. С. Лунин 1, *, В. М. Лопатин 2
1 Московский государственный университет им. М.В. Ломоносова
119991 Москва, Ленинские горы, 1, Россия
2 Филиал Южно-Уральского государственного университета
456318 Челябинская обл., Миасс, пр. Октября, 16, Россия
* E-mail: luninboris@yandex.ru
Поступила в редакцию 13.11.2021
После доработки 13.02.2022
Принята к публикации 14.02.2022
- EDN: GFEQDB
- DOI: 10.31857/S0002337X22050074
Аннотация
Рассмотрены причины появления внутреннего трения в поверхностном слое кварцевого стекла, ухудшающего характеристики высокодобротных механических резонаторов. Предложена комплексная технология обработки поверхности таких резонаторов, включающая асимптотическую механическую обработку, химическое удаление поверхностной зоны стекла и вторичный отжиг для устранения напряжений в материале. Приведены результаты экспериментов, подтверждающие корректность этого подхода. Предложенная технология позволяет изготавливать механические резонаторы из кварцевого стекла с добротностью 107 и выше.
ВВЕДЕНИЕ
Кварцевое стекло является конструкционным материалом для производства высокодобротных механических резонаторов, используемых в современном приборостроении. Из него изготавливают высокодобротные пробные массы-зеркала лазерных детекторов гравитационных волн [1], а также чувствительные элементы волновых твердотельных гироскопов, применяемых в современных навигационных системах различного назначения [2]. Для изготовления таких резонаторов используют особо чистые кварцевые стекла с низким уровнем внутреннего трения. Между тем наряду с качеством стекла большое значение имеет состояние поверхности резонатора, поскольку поверхностные потери вносят значительный вклад в общий диссипативный процесс. Состояние поверхности в свою очередь определяется способами и режимами обработки кварцевого стекла, которое относится к категории хрупких материалов, имеющих высокий показатель твердости.
Механическая обработка и формообразование изделий из таких материалов выполняются преимущественно шлифованием с помощью абразивных или алмазных материалов высокой твердости. Способы шлифовальной обработки стекол хорошо известны (см., например, [3]) и широко используются в оптическом производстве, но их прямое копирование не позволяет получать высокие значения добротности механических резонаторов. Уменьшение добротности кварцевых резонаторов связано с появлением поверхностного нарушенного слоя в процессе механической обработки стекла. При мехобработке абразивными и алмазными зернами стекло испытывает локальное ударное воздействие, приводящее к хрупкому разрушению материала и возникновению микротрещин, развивающихся затем за счет расклинивающего воздействия смачивающе-охлаждающих жидкостей (СОЖ). Кроме того, механическая обработка приводит к возникновению пластических деформаций и сдвиговых напряжений в удаленных от поверхности слоях материала. Возникающий при этом поверхностный нарушенный слой имеет сложную структуру, в которой выделяют три основных зоны: рельефную, трещиноватую и область деформаций.
Рельефная зона представляет собой развитую поверхность, состоящую из микротрещин и выступов. Толщина зоны не превышает размер абразивного зерна, поскольку в процессе обработки зерно лишь частично погружается в стекло. Под рельефной зоной находится трещиноватая зона, толщина которой может быть в несколько раз больше [3]. Ниже трещиноватой зоны лежит область деформаций, характеризующаяся наличием сдвиговых деформаций и сильных механических напряжений. Общая толщина нарушенного слоя зависит от размера зерен абразива, режимов обработки, СОЖ и может достигать сотен мкм [4–9].
Внутреннее трение в поверхностном слое велико и обусловлено разными механизмами. В рельефной зоне внутреннее трение связывают с изменением температуры слабосвязанных микрочастиц кварца, что приводит к возникновению локальных тепловых потоков [10]. В трещиноватой зоне диссипация вызвана диффузионным движением кончиков микротрещин [11]. Механические напряжения в кварцевом стекле (третья зона) деформируют его кремнекислородную сетку и увеличивают внутреннее трение [12].
В оптической промышленности для уменьшения толщины нарушенного слоя шлифованную поверхность полируют, уменьшая размер зерна при переходе от шлифования к полированию на порядок и более. Однако использование полировки при изготовлении механических кварцевых резонаторов имеет два негативных следствия. Во-первых, полировка приводит к некоторому геометрическому искажению формы, которое в отдельных случаях не допускается. Во-вторых, при полировке механическое разрушение поверхностного слоя сочетается с химическим действием суспензии полирующего абразива на стекло и инструмент. Зерна полирующего абразива срезают микроскопические частицы с выступов на шероховатой поверхности стекла и постепенно уменьшают глубину рельефной и трещиноватой зон. В присутствии полирующей суспензии происходит гидролиз срезанных частиц стекла, продукты гидролиза втираются и заполняют микротрещины поверхности. Остаточные углубления трещиноватой зоны, заполненные микроскопическими частицами стекла и продуктами его взаимодействия с жидкой субстанцией, образуют зону упрочненного материала. Дефекты упрочненной зоны не нарушают прозрачности поверхности, но создают сильное внутреннее трение. Кроме того, в процессе полировки возникают дополнительные механические напряжения, отрицательно влияющие на добротность резонатора. В результате даже тщательно отполированный резонатор часто имеет невысокие диссипативные характеристики.
Более полное удаление нарушенного слоя обеспечивает химическое травление поверхности. Технология этого процесса отработана в [13, 14], но в силу неравномерности скорости удаления материала с различных участков поверхности химическое удаление нарушенного слоя может привести к значительным искажениям геометрии резонатора.
Вторичный отжиг позволяет снять механические напряжения в кварцевом стекле и значительно снизить уровень внутреннего трения как в поверхностной зоне, так и в объеме кварцевого стекла. Вместе с тем вторичный отжиг может стимулировать и процессы образования поверхностных трещин [15]. Перечисленные методы обработки поверхности могут вносить дополнительные потери и, использованные по отдельности, не обеспечивают полное удаление нарушенного слоя и устранение связанных с ним диссипативных потерь. Возможное решение проблемы состоит в комплексном применении этих трех методов.
Основные подходы к созданию комплексной технологии следующие.
Механическая обработка поверхности резонатора из кварцевого стекла может ограничиваться тонкой шлифовкой, если резонатор не является частью оптической системы, при этом исключаются геометрические погрешности, вносимые полировальным процессом. Толщина рельефной и трещиноватой зон поверхности не должна при этом превышать 4–5 мкм.
Химическая обработка поверхности, применяемая для удаления нарушенного слоя, должна обеспечивать равномерное удаление материала, чтобы вносимые геометрические погрешности резонатора не превышали нескольких десятых долей мкм.
Вторичный отжиг резонатора должен обеспечить снятие внутренних напряжений без создания поверхностных дефектов, что обеспечивается корректным выбором режима отжига.
Цель настоящей работы заключается в анализе структуры нарушенного поверхностного слоя кварцевого стекла и диссипативных процессов в нем, а также в выборе основных принципов технологического процесса изготовления механических резонаторов, обеспечивающих достижение их высокой добротности.
ЭКСПЕРИМЕНТАЛЬНАЯ ЧАСТЬ
Влияние различных видов обработки поверхности механических резонаторов из кварцевого стекла на внутреннее трение исследовалось экспериментально. В опытах использованы цилиндрические (длина 80–150, диаметр 15–25 мм) и полусферические (диаметр 30, толщина стенки 1 мм) резонаторы, изготовленные из кварцевого стекла КУ-1, которое характеризуется малым уровнем примесей (∼1 ррм) за исключением гидроксильных групп (∼1300 ррм).
Добротность резонаторов измерялась по времени затухания свободных колебаний, функциональная схема установки приведена на рис. 1. Резонаторы размещались в вакуумной термокамере (давление ∼10–5 мм рт. ст., температура –100…+300°С), возбуждение колебаний и измерение их амплитуды осуществлялось с помощью емкостных датчиков. Собственная частота колебаний цилиндрических резонаторов составляла 20–30 кГц, полусферических – около 5 кГц. Для возбуждения колебаний с амплитудой 0.02–0.1 мкм к емкостным электродам прикладывалось постоянное (500–1000 В) и переменное (амплитуда 300–500 В на резонансной частоте) напряжения от источников 1 и 2 (рис. 1). Для детектирования колебаний резонатора использовался высокочастотный преобразователь с независимым возбуждением от внешнего высокочастотного генератора 3 на частоте 20–25 МГц. Частота ВЧ-генератора соответствовала квазилинейному участку резонансной кривой колебательного контура, образованного емкостью датчиков и индуктивностью L. Настройка ВЧ-генератора на эту частоту осуществлялась с помощью вольтметра V по напряжению на колебательном контуре. Колебания резонатора приводят к изменению емкости датчиков и к амплитудной модуляции напряжения на этом ВЧ-контуре, низкочастотная огибающая при этом выделяется диодом Д, усиливается и измеряется селективным микровольтметром 4. Замыкание ключа S приводит к возникновению положительной обратной связи и появлению автоколебаний в резонаторе, после достижения заданной амплитуды колебаний цепь размыкают и измеряют время затухания свободных колебаний τ. Добротность резонатора определяют по формуле $Q = \pi f\tau $, где f – частота собственных колебаний, а внутреннее трение – $\xi = {{Q}^{{ - 1}}}$. Погрешность измерения добротности резонаторов этим способом не превышает 2–3%. Подробная методика измерения приведена в [15].
МИНИМИЗАЦИЯ ГЛУБИНЫ НАРУШЕННОГО ПОВЕРХНОСТНОГО СЛОЯ ПРИ МЕХАНИЧЕСКОЙ ОБРАБОТКЕ
Как правило, при обработке стекла используется т. н. “асимптотическая обработка”, основанная на последовательных инструментальных переходах с постепенным уменьшением размеров зерна в обрабатывающем инструменте. На каждом переходе удаляется нарушенный слой от предыдущего инструмента и образуется новый с глубиной меньше предыдущего. Последовательное уменьшение размеров зерна в инструменте позволяет свести нарушенный слой к минимально возможному значению, хотя и не устраняет его полностью. Существует корреляция между размером зерен шлифовального инструмента и глубиной нарушенного поверхностного слоя. В табл. 1 приведены рассчитанные по данным [8] максимально возможные значения глубины нарушенного слоя в зависимости от размера зерен основной фракции абразивного материала. В последнем столбце таблицы в качестве примера приведен вариант поэтапной обработки, основанный на данных о глубине нарушенного слоя и включающий последовательное использование инструментов с зернистостью М63, М40, М20, М10, М5. Глубина удаляемого слоя для каждого инструмента в этом ряду выбрана таким образом, чтобы полностью удалить нарушенный слой от предыдущего инструмента.
Таблица 1.
Глубина нарушенного слоя при шлифовании поверхности кварцевого стекла и рекомендуемая глубина обработки
Образец | Обозначение зернистости | Размер зерен основной фракции, мкм | Глубина нарушенного слоя, мкм | Глубина удаляемого слоя, мкм | |
---|---|---|---|---|---|
min | max | ||||
Микрошлифпорошки | М63 | 50 | 63 | 67.7 | |
М50 | 40 | 50 | 55.6 | ||
М40 | 28 | 40 | 46.0 | 68 | |
М28 | 20 | 28 | 34.0 | ||
М20 | 14 | 20 | 25.5 | 47 | |
М14 | 10 | 14 | 18.8 | ||
Тонкие микрошлифпорошки | М10 | 7 | 10 | 14.2 | 26 |
М7 | 5 | 7 | 10.5 | ||
М5 | 3 | 5 | 7.9 | 15 | |
М3 | 2 | 3 | 5.1 |
Табличные данные выбранного варианта дополняются схемой обработки поверхности (рис. 2), на которой для каждого инструмента выделен слой удаляемого материала, нарушенный слой и монолитная зона. Из схемы видно, что на каждом этапе обработки происходит образование нарушенного слоя, глубина которого меньше, чем на предыдущем этапе. В частности, после обработки инструментом с зернистостью М40 полностью удаляется нарушенный слой, созданный предшествующим инструментом с зернистостью М63, а образованный при этом нарушенный слой меньше предыдущего. Остаточная глубина нарушенного слоя после нескольких этапов механической обработки может доходить до 5–8 мкм, а ее финишное значение может быть еще меньше за счет использования специальных технологических приемов обработки. Следует отметить, что, согласно данным [7], глубина поверхностных трещин увеличивается с ростом давления (Р), создаваемого инструментом, пропорционально. Поэтому асимптотическая обработка поверхности будет эффективно уменьшать толщину нарушенного слоя, если давление инструмента на поверхность регулируется и не увеличивается при смене инструмента. Кроме того, давление, создаваемое инструментом, и глубина нарушенного слоя уменьшаются при переходе от свободных зерен к связанным. В работе [6], в частности, отмечено, что при M63/50 переход от свободного абразива к связанному позволяет уменьшить толщину нарушенного слоя почти вдвое.
Рис. 2.
Схема механической обработки поверхности кварцевого резонатора; для каждого инструмента выделены толщины удаляемого слоя (1), нарушенного слоя (2) и монолита стекла (3).
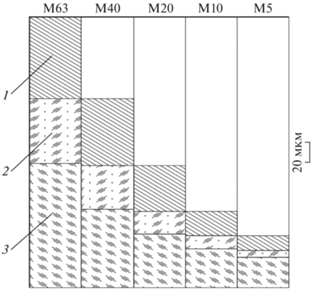
Определенное значение имеет и выбор связки шлифовального инструмента. Шлифовальные круги на твердых связках с высокой стойкостью к ударным и температурным воздействиям используют преимущественно на предварительных этапах обработки. Круги на мягких связках позволяют уменьшить давление алмазного зерна на обрабатываемую поверхность и повысить качество обработки поверхности. В шлифовальных кругах с эластичными связками зерна закреплены слабее и с повышением нагрузки могут выкрашиваться из инструмента, такие круги быстрее изнашиваются, но сохраняют режущую способность за счет подключения к шлифованию более глубоких зерен с острыми кромками. Такие инструменты предпочтительно использовать на финишных этапах обработки.
ХИМИЧЕСКОЕ УДАЛЕНИЕ НАРУШЕННОГО ПОВЕРХНОСТНОГО СЛОЯ
Химическое растворение поверхностного слоя кварцевого стекла можно осуществить растворами плавиковой кислоты по реакции
(1)
${\text{Si}}{{{\text{O}}}_{{\text{2}}}} + 6{\text{HF}} = {{{\text{H}}}_{{\text{2}}}}{\text{Si}}{{{\text{F}}}_{6}} + 2{{{\text{H}}}_{{\text{2}}}}{\text{O}}{\text{.}}$Следует учитывать, что продукты травления (поликремниевые кислоты различной степени полимеризации) адсорбируются на шлифованной поверхности по-разному, препятствуя доступу травильного раствора к поверхности. Диффузия раствора сквозь этот гелеобразный адсорбированный слой лимитирует скорость реакции (1), и в результате травление в водных растворах чистой плавиковой кислоты идет неравномерно с увеличением шероховатости поверхности. Для удаления нерастворимых в воде фторидов и фторсиликатов в раствор добавляют сильную минеральную кислоту, обычно серную. Химическое травление можно осуществлять и солями плавиковой кислоты, наиболее эффективен при этом фторид-бифторид аммония NH4F∙NH4HF2, при взаимодействии которого с серной кислотой в растворе образуется плавиковая кислота:
(2)
$\begin{gathered} {\text{N}}{{{\text{H}}}_{{\text{4}}}}{\text{F}} + {{{\text{H}}}_{{\text{2}}}}{\text{S}}{{{\text{O}}}_{4}} = {\text{N}}{{{\text{H}}}_{{\text{4}}}}{\text{HS}}{{{\text{O}}}_{{\text{4}}}} + {\text{HF,}} \\ {\text{N}}{{{\text{H}}}_{{\text{4}}}}{\text{H}}{{{\text{F}}}_{{\text{2}}}} + {{{\text{H}}}_{{\text{2}}}}{\text{S}}{{{\text{O}}}_{{\text{4}}}} = {\text{N}}{{{\text{H}}}_{{\text{4}}}}{\text{HS}}{{{\text{O}}}_{4}} + 2{\text{HF}}{\text{.}} \\ \end{gathered} $Для увеличения степени очистки поверхности применяют циклическую химическую обработку, которая наряду с травлением включает в себя промывку изделия в серной кислоте и воде. Число таких циклов может достигать нескольких десятков. С этой же целью в травильные растворы добавляют поверхностно-активные вещества (ПАВ). Использование ПАВ при травлении и промывке резонатора позволяет лучше очистить поверхность от продуктов гидролиза поликремниевых кислот, для этой цели подходит, например, перфторпеларгоновая кислота или ее соли. Толщину (h) удаленного слоя определяют по убыли массы (Δm):
где ρ – плотность кварцевого стекла, S – площадь поверхности резонатора.На рис. 3 приведены результаты эксперимента, демонстрирующие эффективность циклической химической обработки для достижения высокой добротности резонатора из кварцевого стекла. Травильный раствор содержал фторид-ионы (3.6%) и перфторпеларгоновую кислоту (0.002%); промывка проводилась в серной кислоте (40%) и воде. График показывает зависимости добротности цилиндрического резонатора и скорости растворения материала от глубины удаляемого слоя. Видно, что скорость растворения дефектного слоя $v$ уменьшается по мере его удаления, одновременно возрастает и добротность резонатора. Постоянство скорости растворения на конечной стадии эксперимента говорит о полном удалении дефектного слоя и растворении монолита стекла.
Рис. 3.
Зависимости добротности резонатора и скорости растворения кварцевого стекла от толщины удаленного слоя.
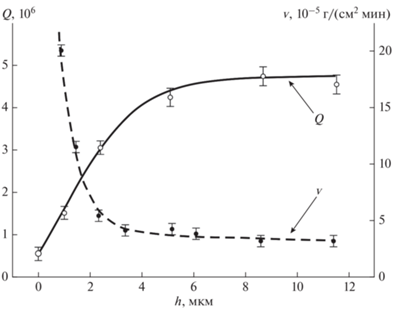
На рис. 4 приведена температурная зависимость внутреннего трения в поверхностном слое резонаторов из кварцевого стекла КУ-1, прошедших шлифовку абразивными инструментами различной зернистости и последующую химическую обработку. Резонатор I имел поверхность с финишной обработкой алмазным порошком М14, резонатор II – с финишной обработкой алмазным порошком М5, а резонатор III был отполирован. Температурная зависимость потерь в поверхностном слое Δξ(t) определялась как разность температурных зависимостей потерь в резонаторе, измеренных до ($Q_{{in}}^{{ - 1}}$) и после ($Q_{f}^{{ - 1}}$) химической обработки:
Рис. 4.
Температурные зависимости внутреннего трения в нарушенном слое кварцевого стекла для резонаторов, обработанных алмазными порошками М14 (1), М5 (2) и полировальным инструментом (3).
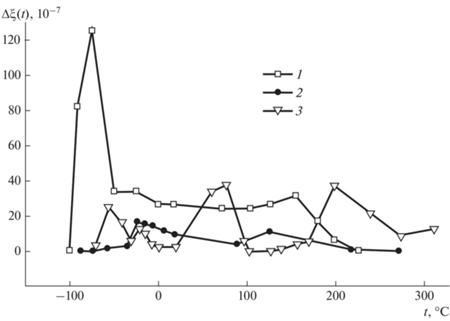
Видно, что поглощение энергии в поверхностном слое в целом увеличивается по мере роста размера зерен абразива. Локальные пики внутреннего трения, наблюдаемые при определенных температурах, связаны с протеканием различных диссипативных процессов в соответствии с зинеровской теорией неупругости [16]. Полученные результаты указывают на то, что и в тщательно отполированном резонаторе есть значительные поверхностные потери. В отдельных температурных областях появляются пики внутреннего трения, связанные с взаимодействием наночастиц поверхностного слоя как с монолитом стекла, так и между собой. Наличие таких локальных пиков потерь, по-видимому, осталось незамеченным другими авторами, сделавшими вывод о возможности полного удаления нарушенного слоя кварцевого стекла механической полировкой [17]. В действительности полного устранения поверхностной диссипации можно достичь только химическим способом.
УСТРАНЕНИЕ ВНУТРЕННИХ НАПРЯЖЕНИЙ ПРИ ОТЖИГЕ
Как известно, стекло представляет собой переохлажденную жидкость с очень высокой вязкостью; при повышении температуры вязкость уменьшается и за счет течения стекла напряжения исчезают. Поэтому выбор условий отжига следует делать на основе данных о скорости течения кварцевого стекла. В [15] была определена температурная зависимость постоянной времени релаксации структуры кварцевого стекла КУ-1 в диапазоне температур 825–980°С в виде: τr = = $2 \times {{10}^{{ - 15}}}{\text{exp}}\left( {85800{\text{/}}RT} \right)$ (R = 2 кал/(моль град), а время отжига, необходимое для достижения квазиравновесного состояния структуры, предложено брать равным ∼ 3τr. Вместе с тем полученные в [15] данные характеризуют процесс структурной перестройки кремнекислородной сетки стекла, и можно ожидать, что при релаксации только механических напряжений постоянная времени процесса будет меньше. При выборе режима отжига надо учитывать величину термонапряжений при охлаждении стекла и вероятность возникновения напряжений в дегидроксилированном поверхностном слое. В выполненных экспериментах температура отжига составляла 920°С. При этом, согласно [15], полное равновесие структуры стекла КУ-1 наступает через ∼20–25 ч и дегидроксилирование поверхностного слоя не приводит к появлению напряжений и трещин. Охлаждение до температуры 750°С проводили со скоростью 35°C/ч для обеспечения уровня термонапряжений менее 0.1 кг/см2. Ниже 750°С охлаждение шло естественным путем. Кроме добротности, определялось и начальное механическое напряжение в материале резонаторов. Устранение напряжений при отжиге сопровождается изменением скорости звука в кварцевом стекле [18] и собственной частоты резонатора. Этот эффект был использован для определения начального (до отжига) уровня механических напряжений σ0, который рассчитывался по формуле [18]
(5)
${{\sigma }_{0}} = 14{\kern 1pt} 700\left( {1 - \frac{{{{f}_{{in}}}}}{{{{f}_{f}}}}} \right)\,\,\left( {{\text{МПа}}} \right),$На рис. 5 показаны экспериментальные результаты по изменению добротности трех полусферических резонаторов, прошедших шлифовку алмазным порошком М50, химическое травление и отжиг, которые до отжига имели различный уровень механических напряжений. Из рис. 5 видно, что начальная добротность монотонно зависит от уровня внутренних напряжений, которые после механической шлифовки оказались достаточно большими. При этом резонаторы I и II после отжига показали одинаковую добротность, хотя время отжига отличалось более чем в 5 раз. Это указывает на то, что релаксация механических напряжений в кварцевом стекле действительно идет быстрее, чем формирование квазиравновесной кремнекислородной структуры. На практике для полного устранения напряжений при данной температуре достаточен отжиг в течение ∼5 ч. Добротность резонатора III также существенно увеличилась, однако оказалась ниже в ∼1.5 раза по сравнению с другими. Наиболее вероятная причина этого различия состоит не только в более высоком начальном уровне механических напряжений в резонаторе III, но и в значительно большей глубине нарушенного слоя, что в итоге и ограничило его добротность.
ЗАКЛЮЧЕНИЕ
Нарушенный поверхностный слой в механических резонаторах из кварцевого стекла имеет сложную структуру, и внутреннее трение в нем гораздо выше, чем в объеме стекла. В результате проведенного исследования установлено, что для устранения поверхностного внутреннего трения обработка должна включать в себя следующие операции.
1. Асимптотическую механическую обработку с последовательным уменьшением размеров зерна в обрабатывающем инструменте, причем давление инструмента на поверхность стекла не должно увеличиваться при смене размера абразивного зерна. Механическая обработка поверхности может ограничиваться тонкой шлифовкой, если резонатор не является частью оптической системы, при этом остаточная толщина рельефной и трещиноватой зон поверхности не должна превышать 4–5 мкм.
2. Химическое травление поверхности растворами, содержащими фторид-ионы и добавки ПАВ. Обработка должна вестись циклами, включающими собственно травление, промывку в серной кислоте и воде. Число таких циклов может достигать нескольких десятков.
3. Вторичный отжиг, обеспечивающий снятие внутренних напряжений. Отжиг резонаторов из кварцевого стекла КУ-1 можно проводить при температуре 920°С в течение ∼5 ч. Скорость последующего охлаждения до температуры ∼750°С рассчитывают исходя из размеров отжигаемого изделия и допустимой величины термонапряжений – 0.1 кг/см2. Ниже 750°С охлаждение происходит естественным путем.
Предлагаемая комплексная технология позволяет изготавливать механические резонаторы из кварцевого стекла с добротностью выше 107.
Список литературы
Брагинский В.Г., Биленко И.А., Вятчанин М.Л., Городецкий М.Л., Митрофанов В.П., Прохоров Л.Г., Стрыгин С.Е., Халили Ф.Я. Дорога к открытию гравитационных волн // Успехи физ. наук. 2016. Т. 186. № 9. С. 968–974. https://doi.org/10.3367/UFNr.2016.03.037811
Климов Д.М., Журавлев В.Ф., Жбанов Ю.К. Кварцевый полусферический резонатор (волновой твердотельный гироскоп). М.: Ким Л.А, 2017. 193 с.
Гетц И. Шлифовка и полировка стекла: пер. с чеш. / под ред. Смысловой М.А. Л.: Стройиздат, 1967. 280 с.
Обейд А. Динамика формирования поверхностной шероховатости при обработке свободным абразивом: дис. ... канд. техн. наук: 05.11.07. С-П.: Университет ИТМО, 2005. 131 с.
Пискарев П.В. Повышение качества алмазно-абразивной обработки стекла путем применения эффективных синтетических смазочно-охлаждающих технологических сред: дис. ... канд. техн. наук: 05.03.01. Иваново: ИвГУ, 2004. 149 с.
Липатова А.Б. Повышение производительности и качества обработки кристаллографически ориентированных пластин алмазными кругами: дис. ... канд. техн. наук: 05.03.01. М.: МГТУ “Станкин”, 2008. 193 с.
Miller P.E., Suratwala T.I., Wong L.L., Feit M.D., Menapace J.A., Davis P.J., Steele R.A. The Distribution of Subsurface Damage in Fused Silica // Laser-Induced Damage in Optical Materials. 2005. V. 5991. P. 599101-1. https://doi.org/10.1117/12.638821
Lambropoulos J.C. From Abrasive Size to Subsurface Damage in Grinding // OSA Technical Digest. 2000. P. 17–18. https://doi.org/10.1364/OFT.2000.OMA6
Панасюк Г.П., Козерожец И.В., Ворошилов И.Л., Ивакин Ю.Д., Привалов В.И., Данчевская М.Н. Формы воды на поверхности и в объеме диоксида кремния // Журн. неорган. химии. 2021. Т. 66. № 5. С. 623–630. https://doi.org/10.31857/S0044457X21050123
Смагин А.Г. Явление поглощения звука в поверхностном слое кристалла // Вопросы радиоэлектроники. Детали и компоненты аппаратуры. 1964. № 11. С. 65–69.
Даринский Б.М., Измайлов Н.В., Логинов В.А., Митрохин В.И., Ярославцев Н.П. Неупругая релаксация в твердых телах, связанная с нарушениями их поверхности // ФТТ. 1987. Т. 29. № 12. С. 3529–3533.
Лунин Б.С., Торбин С.Н. Влияние напряжений в кварцевом стекле на внутреннее трение // Вестн. МГУ. Сер.2. Химия. 2003. Т. 44. № 2. С. 108–114.
Spierings G.A. Review: Wet Etching of Silicate Glasses in Hydrofluoric Acid Based Solutions // J. Mater. Sci. 1993. V. 28. P. 6261–6273. https://doi.org/10.1007/BF01352182
Cook L.M. Chemical Processes in Glass Polishing // J. Non-Cryst. Solids. 1990. V. 120. № 1–3. P. 152–171. https://doi.org/10.1016/0022-3093(90)90200-6
Lunin B.S., Tokmakov K.V. Reduction in Internal Friction in Silica Glass with High OH Content // J. Am. Ceram. Soc. 2019. V. 102. № 6. P. 3329–3340. https://doi.org/10.1111/jace.16187
Zener C. Internal Friction in Solids. I. Theory of Internal Friction in Reeds //Phys. Rev. 1937. V. 52. № 3. P. 230–235.
Startin W.J., Beilby M.A., Saulson P.R. Mechanical Quality Factors of Fused Silica Resonators // Rev. Sci. Instrum. 1998. V. 69. № 10. P. 3681–3689. https://doi.org/10.1063/1.1149159
Strakna R.E., Clark A.E., Bradley D.L., Slie W.M. Effect of Fast-Neutron Irradiation on the Pressure and Temperature Dependence of the Elastic Moduli of SiO2 Glass // J. Appl.Phys. 1963. V. 34. № 5. P. 1439–1443.
Дополнительные материалы отсутствуют.
Инструменты
Неорганические материалы