Неорганические материалы, 2022, T. 58, № 9, стр. 945-955
Синтез композиционных порошков B4C/ZrB2 методом карбидоборного восстановления для изготовления керамики
Т. С. Гудыма 1, *, Ю. Л. Крутский 1, Е. А. Максимовский 2, А. В. Ухина 3, А. И. Апарнев 1, А. И. Смирнов 1, Н. Ф. Уваров 3
1 Новосибирский государственный технический университет
630073 Новосибирск,
пр. К. Маркса, 20, Россия
2 Институт неорганической химии им. А.В. Николаева СО Российской
академии наук
630090 Новосибирск, пр. Академика Лаврентьева, 3, Россия
3 Институт химии твердого тела и механохимии СО Российской
академии наук
630090 Новосибирск, ул. Кутателадзе, 18, Россия
* E-mail: gudymatan@mail.ru
Поступила в редакцию 08.03.2022
После доработки 23.06.2022
Принята к публикации 30.06.2022
- EDN: TJSJFT
- DOI: 10.31857/S0002337X22090056
Аннотация
Исследован процесс получения композиционного порошкового материала B4C/ZrB2 методом карбидоборного восстановления оксида циркония в присутствии углеродного восстановителя – нановолокнистого углерода. Синтез материала проводили в диапазоне температур 1200–1900°С в течение 20 мин. Оптимальная температура синтеза независимо от состава шихты составила 1650°С. Изучены характеристики композиционных порошков, содержащих 10–30 мол. % ZrB2. Средний размер 50% частиц композиционного порошка данного состава не превышает 9.5 мкм. Полученные порошки представляют собой агрегированные частицы фаз B4C и ZrB2 размером до 10 и 40 мкм соответственно. Визуальный анализ микрофотографий порошков показал, что смеси, содержащие 20–30 мол. % ZrB2, демонстрируют равномерное распределение модифицирующей добавки в объеме частиц B4C, при этом содержание средних и крупных включений не превышает 15 об. %. Значение удельной поверхности образцов находится в диапазоне 1.3–2.1 м2/г. Частицы диборида циркония равномерно распределены в матрице карбида бора. Увеличение содержания ZrB2 в композиционном порошковом материале с 10 до 30 мол. % приводит к повышению его термической стойкости в окислительной среде. Полученный композиционный материал перспективен для изготовления керамики.
ВВЕДЕНИЕ
Керамика на основе B4C является весьма перспективным материалом в различных областях науки и техники. Благодаря уникальному сочетанию низкой плотности и высокой твердости данный материал применяется в производстве легкой брони [1, 2] и режущих инструментов [3]. Из-за большого сечения поглощения нейтронов карбид бора перспективен для области атомной энергетики [4]. Однако производство и применение керамики на основе карбида бора ограничено его плохой спекаемостью, низкими значениями пластичности и коэффициента самодиффузии, а также невысокой трещиностойкостью (2.0–4.0 МПа м1/2) [5, 6]. Для улучшения способности к спеканию и увеличения трещиностойкости в материал вводят модифицирующие добавки. В качестве такой добавки может быть использован диборид циркония ZrB2 [7, 8].
Диборид циркония в термодинамическом отношении является весьма стабильным соединением. Температура его плавления составляет ~3200°С. ZrB2 относится к металлоподобным тугоплавким соединениям, поскольку обладает высокими значениями коэффициента теплопроводности и удельной электропроводности. Микротвердость керамики из диборида циркония довольно высока и находится в диапазоне 22.3–22.7 ГПа при температуре 25°С [9, 10]. Керамика состава B4C–ZrB2 демонстрирует более высокие прочность на сжатие и трещиностойкость, чем монолитный B4C [11, 12], а также обладает большей стойкостью к окислению [13]. Это позволяет расширить область применения композиционной керамики на основе карбида бора в промышленности.
Стоит отметить, что на данный момент наиболее распространено получение композиционного керамического материала с использованием готовых порошков В4С и ZrB2 в качестве компонентов шихты [12, 14, 15]. Однако такая шихта требует длительного (8–24 ч) перемешивания путем высокоэнергетического размола, поскольку фазы В4С и ZrB2 имеют разную плотность и склонны к расслаиванию. Имеются немногочисленные данные о получении материалов B4C/ZrB2 методами in situ в соответствии с реакциями (1) [16], (2) [17] и (3) [18]:
(1)
${\text{Zr}}{{{\text{B}}}_{{\text{2}}}}{\text{ + 4B + C = Zr}}{{{\text{B}}}_{{\text{2}}}}{\text{ + }}{{{\text{B}}}_{{\text{4}}}}{\text{C,}}$(2)
$\begin{gathered} (1--x)({\text{Zr + 2B)}} + x({\text{4B + C}}) = \\ = \,\,(1--x){\text{Zr}}{{{\text{B}}}_{2}} + x{{{\text{B}}}_{{\text{4}}}}{\text{C,}} \\ \end{gathered} $(3)
$\begin{gathered} (1 + x){{{\text{B}}}_{{\text{4}}}}{\text{C}} + 2x{\text{Zr}}{{{\text{O}}}_{2}} + 3x{\text{C}} = \\ = \,\,{{{\text{B}}}_{{\text{4}}}}{\text{C}} + 2x{\text{Zr}}{{{\text{B}}}_{{\text{2}}}} + 4x{\text{CO}}{\text{.}} \\ \end{gathered} $При этом реакции (1) и (2) перспективны для совмещения процесса получения шихты и ее компактирования, поскольку отсутствуют газообразные продукты. Однако использование дорогостоящего бора и необходимость длительного перемешивания шихты ограничивают возможность проведения процессов в соответствии с данными реакциями для получения компактных композиционных материалов. Предварительное получение шихты по реакци (3) позволяет получить хорошо перемешанную смесь, не требующую дальнейшей длительной гомогенизации.
В качестве источника углерода при проведении синтеза чаще всего используют ламповую сажу [8, 17]. Перспективным направлением является исследование процессов синтеза композиционных порошковых материалов с использованием нановолокнистого углерода (НВУ) [19]. Данный материал обладает развитой удельной поверхностью, что позволит получить высокодисперсную шихту для изготовления керамики при удовлетворительных параметрах синтеза.
Целью настоящей работы было исследование процесса синтеза и свойств композиционных порошков B4C/ZrB2, полученных методом карбидоборного восстановления (реакция (3)) с использованием НВУ.
ЭКСПЕРИМЕНТАЛЬНАЯ ЧАСТЬ
Для получения композиционного порошкового материала B4C/ZrB2 в качестве реагентов использовали высокодисперсный карбид бора В4С (содержание основного вещества 98.5 мас. %, средний размер частиц 2.1 мкм), синтезированный из простых веществ [20]; оксид циркония ZrO2 (ТУ 6-09-2486-77, содержание основного вещества 98.8 мас. %, средний размер частиц 10.4 мкм); нановолокнистый углерод (содержание углерода 99 мас. %, удельная поверхность около 150 м2/г) [21, 22]. Порошок ZrO2 предварительно измельчали в планетарной шаровой мельнице АГО–2С (материал мелющих тел – ZrO2) при соотношении массы порошка к массе шаров 1 : 30 в течение 5 мин с ускорением 20 g. Средний размер частиц ZrO2 после измельчения составил 3.3 мкм. На рис. 1 представлены микрофотографии реагентов.
Состав шихты подбирали таким образом, чтобы в соответствии с реакцией (3) были получены порошковые материалы, содержащие 10, 20, 25 и 30 мол. % ZrB2. В соответствии с диаграммой состояния системы B4C–ZrB2 в точке эвтектики содержание ZrB2 составляет ~25 мол. % [23]. Таким образом, для исследований были выбраны доэвтектические, эвтектический и заэвтектический составы.
Образцы были обозначены как Z10, Z20, Z25 и Z30 соответственно. Исходные порошки смешивали в планетарной шаровой мельнице в течение 5 мин с ускорением 20 g, после чего просеивали через сито с размером ячейки 100 мкм.
Синтез проводили в индукционной печи тигельного типа ВЧ–25АВ в среде аргона для предотвращения нежелательного азотирования карбида бора и образующегося диборида циркония. Калибровка была проведена по температурам плавления меди квалификации “х. ч.” (1083°С), никеля квалификации “х. ч.” (1455°С), сульфида марганца с содержанием основного вещества не менее 99.9% (1615°С) и платины квалификации “х. ч.” (1769°С). Контроль температуры осуществляли с использованием оптического пирометра Кельвин Компакт 2300. Давление в реакторе было близким к атмосферному. Поскольку определение парциального давления оксида углерода в газовой смеси Ar + CO затруднительно, температуры начала восстановления диоксида циркония в соответствии с реакцией (3) определяли для разных давлений СО. Результаты термодинамических расчетов, выполненных по методике, изложенной в монографии [24], приведены на рис. 2.
Рис. 2.
Температурные зависимости изобарно-изотермического потенциала (энергии Гиббса) реакции синтеза B4C/ZrB2 для разных давлений СО.
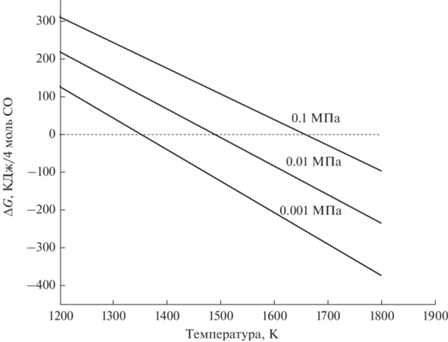
Величина изобарно-изотермического потенциала реакции карбидоборного восстановления диоксида циркония становится отрицательной при температурах 1353, 1491 и 1660 К для давлений СО 0.001, 0.01 и 0.1 МПа соответственно. Для обеспечения полноты протекания реакции может потребоваться термообработка при более высоких температурах. Это подтверждено данными термодинамического моделирования, приведенными в публикациях [25, 26]. В данных работах показано, что оптимальная температура синтеза находится в диапазоне 1540–2280°С.
В настоящем исследовании термообработку шихты для изготовления порошкового материала B4C–25 мол. % ZrB2 (Z25) проводили при 1200, 1400, 1650 и 1900°С в течение 20 мин в соответствии с реакцией (3). Полноту протекания реакции определяли путем взвешивания шихты и продуктов реакции и сопоставления экспериментальных данных с теоретическими. Расчетная убыль массы при полном протекании реакции в данном случае составляет 16.6 мас. %. С учетом незначительного содержания примесей в реагентах она может быть немного ниже. Поскольку результаты проведенных исследований показали, что оптимальная температура синтеза составила 1650°С, то дальнейшие эксперименты проводили при этой температуре. Для исследования влияния состава шихты на свойства получаемого материала была проведена термообработка образцов Z10, Z20 и Z30 при температуре 1650°С в течение 20 мин.
Полученные композиционные порошки исследовали с помощью рентгенофазового и химического анализов. Рентгенофазовый анализ проводили на дифрактометре ДРОН-3 с использованием CuKα-излучения. При расшифровке дифрактограмм применяли банк данных Power Diffraction File (PDF–2). Соотношение фаз B4C и ZrB2 определялось методом корундовых чисел. Содержание общего углерода определяли методом инфракрасной абсорбционной спектрометрии на анализаторе серы и углерода LECO CS 844 в соответствии с ГОСТ 12344-2003. Микроструктуру материала и морфологию частиц изучали с применением растрового электронного микроскопа S–3400N (Hitachi), оборудованного приставкой для энергодисперсионного анализа производства (Oxford Instruments). Анализ микрофотографий проводили с использованием программы ImageJ. Распределение частиц по размерам устанавливали на лазерном анализаторе частиц MicroSizer 201 ВА “Инструментс”. Удельную поверхность определяли по методике низкотемпературной адсорбции азота с использованием прибора Quantachrom NOVA 2200e. Тугоплавкие соединения и изделия из них обычно эксплуатируются в экстремальных условиях, в т.ч. и в окислительных средах. Поэтому их стойкость к действию кислорода при повышенных температурах является важным свойством. Термоокислительную стабильность образцов определяли с использованием прибора синхронного термического анализа Netzsch STA 449 C Jupiter. В ходе анализа проводили окисление образца в атмосфере синтетического воздуха при нагревании до температуры 1000°С со скоростью 15°С/мин.
РЕЗУЛЬТАТЫ И ОБСУЖДЕНИЕ
В табл. 1 приведены данные по убыли массы образцов, полученных при различных температурах синтеза из шихты, состав которой соответствует содержанию 25 мол. % ZrB2. Из полученных результатов следует, что реакция боридообразования полностью завершается только при температуре 1650°С.
Таблица 1.
Значения убыли массы шихты состава B4C–25 мол. % ZrB2 в зависимости от температуры синтеза
Температура синтеза, °С | Убыль массы, мас. % |
---|---|
1200 | 1.3 |
1400 | 2.3 |
1650 | 16.0 |
1900 | 15.8 |
Дифрактограммы образцов представлены на рис. 3. Анализ дифрактограмм показывает, что при температуре синтеза 1200°С отчетливо видны пики непрореагировавших фаз ZrO2 и С, а также имеются небольшие пики, соответствующие фазе ZrB2. При температуре синтеза 1400°C пики фазы ZrO2 еще присутствуют, при этом наблюдается явное наличие целевых фаз ZrB2 и B4C. При температуре 1650°С и выше процесс протекает полностью и на дифрактограмме присутствуют только пики целевых фаз.
На рис. 4 приведены электронные микрофотографии порошковых материалов, синтезированных при температурах 1200–1900°С. На снимках образцов, полученных при 1200 и 1400°С, можно наблюдать наличие разнородных частиц, часть из которых по размеру и форме сходна с частицами используемого НВУ (рис. 1в). Это может свидетельствовать о неполном протекании реакции синтеза. Образцы, полученные при температурах 1650 и 1900°С, имеют однородные агрегированные частицы, размер которых не превышает нескольких микрон. Частицы имеют ровные края. Результаты энергодисперсионного анализа показали наличие циркония, бора и незначительного количества кислорода.
Рис. 4.
Снимки РЭМ порошков B4C–25 мол. % ZrB2, синтезированных при 1200 (а), 1400 (б), 1650 (в) и 1900°С (г).
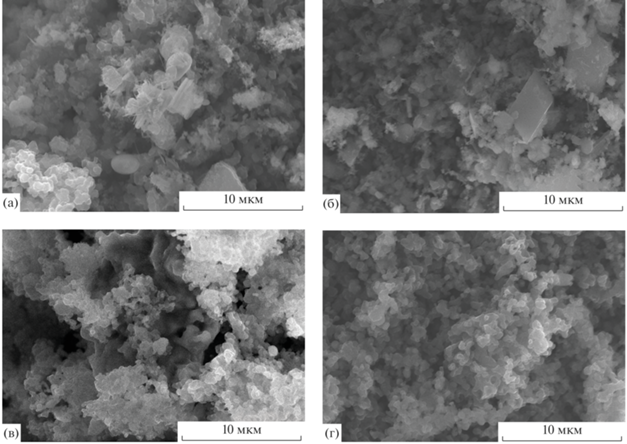
Для определения оптимальной температуры синтеза было исследовано влияние повышения температуры синтеза на некоторые свойства порошкового материала B4C–25 мол. % ZrB2. Установлено, что с увеличением температуры термообработки с 1650 до 1900°С средний размер частиц возрастает с 8.5 до 8.7 мкм, а удельная поверхность уменьшается с 1.4 до 1.3 м2/г. Данные характеристики меняются незначительно. Это позволяет сделать вывод, что проведение синтеза при более высокой температуре (1900°С) нецелесообразно, поскольку ведет к повышению энергозатрат и усиленному износу печного оборудования.
Таким образом, можно сделать вывод, что оптимальная температура синтеза композиционных материалов составляет ~1650°С. По этой причине было изучено влияние состава шихты на свойства порошковых материалов, синтезированных при данной температуре.
Экспериментальная убыль массы образцов, полученных при термообработке шихты, содержащей 10, 20, 25 и 30 мол. % ZrB2, практически полностью совпадала с расчетной (отклонение не более 0.6 мас. %) (табл. 2). Это свидетельствует о полном протекании реакции при температуре 1650°С, что также подтверждается данными рентгенофазового анализа. Фазы ZrB2 и B4C присутствуют во всех термообработанных образцах (рис. 5). Содержание фазы ZrB2, рассчитанное методом корундовых чисел, составило 11, 20, 24 и 29 мол. % для образцов Z10, Z20, Z25 и Z30 соответственно. Полученные значения близки к расчетным.
Таблица 2.
Результаты определения содержания общего углерода
Образец | СС, мас. % | |
---|---|---|
эксперимент | расчет | |
Z10 | 17.9 | 17.7 |
Z20 | 14.1 | 14.4 |
Z25 | 12.5 | 12.9 |
Z30 | 11.9 | 11.6 |
Результаты определения содержания общего углерода в образцах представлены в табл. 2, они близки к расчетным значениям. Это позволяет сделать вывод о полном протекании реакций синтеза.
На рис. 6 и 7 приведены микрофотографии образцов с различным содержанием ZrB2. Анализ микрофотографий позволяет сделать вывод, что полученные порошки представляют собой агрегированные частицы фаз B4C и ZrB2 размером до 10 и 40 мкм соответственно. Изображения, представленные на рис. 7, характеризуют распределение частиц фазы ZrB2 (светлая область) в матрице B4C (темная область). На рис. 7а наблюдается неравномерный характер распределения фазы ZrB2 для образца Z10. При этом для образцов с бóльшим содержанием модифицирующей добавки наблюдается равномерное распределение частиц (рис. 7б–7г), а также наличие средних и крупных включений. Для образца Z20 (рис. 7б) характерно наличие единичных крупных включений фазы ZrB2 размером 10–40 мкм в количестве не более 2.5 об. %. В образце Z25 зафиксировано до 5 об. % включений ZrB2 размером менее 10 мкм (рис. 7в). Для образца Z30 (рис. 7г) наблюдалось содержание до 5 об. % крупных включений размером 10–40 мкм и до 15 об. % средних включений размером менее 10 мкм.
Рис. 6.
Снимки РЭМ композиционных порошков B4C/ZrB2, содержащих 10 (а), 20 (б), 25 (в), 30 мол. % ZrB2 (г).
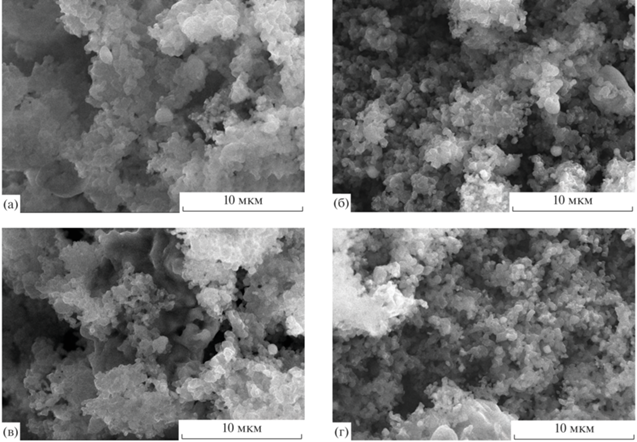
Рис. 7.
Снимки РЭМ композиционных порошков B4C/ZrB2, содержащих 10 (а), 20 (б), 25 (в), 30 мол. % ZrB2 (г), при бóльшем увеличении.
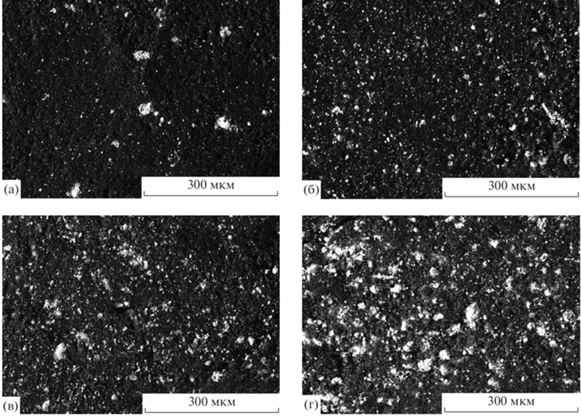
В процессе проведения седиментационного анализа композиционные порошки B4C/ZrB2 подвергались ультразвуковому диспергированию при мощности 200 Вт в течение 30 с. Гистограммы образцов Z10 и Z30 представлены на рис. 8 . На гистограммах присутствуют два пика. Примечателен тот факт, что высота второго пика с увеличением содержания ZrB2 возрастает. Можно предположить, что часть гистограммы с меньшим размером частиц в основном характеризует фазу B4C. Следовательно, часть гистограммы с большим размером частиц характеризует фазу ZrB2. Этот предположение согласуется с исследованиями процессов синтеза индивидуальных порошков карбида бора [27] и диборида циркония [28]. Гистограммы распределения частиц по размерам, представленные в работе [27], показали, что для карбида бора характерно образование более мелких частиц со средним размером около 2 мкм. При этом ZrB2, синтезированный методом карбидоборного восстановления [28], имел средний размер частиц около 11 мкм. Исходя из этого в настоящей работе был рассчитан средний размер частиц и агрегатов для каждой фазы по соответствующим участкам гистограммы, а также определены стандартные отклонения и показатели асимметричности по методике [29] (табл. 3).
Таблица 3.
Результаты гранулометрических исследований композиционных порошков B4C/ZrB2
Образец | D50, мкм | Фаза | Средний размер частиц фазы, мкм | Стандартное отклонение, мкм | Степень асимметричности |
---|---|---|---|---|---|
Z10 | 7.26 | B4C | 4.71 | 1.89 | –0.04 |
ZrB2 | 39.88 | 1.57 | 0.01 | ||
Z20 | 8.58 | B4C | 5.13 | 1.91 | –0.04 |
ZrB2 | 39.35 | 1.57 | 0.01 | ||
Z25 | 8.49 | B4C | 5.30 | 1.85 | –0.04 |
ZrB2 | 41.01 | 1.58 | 0.01 | ||
Z30 | 9.44 | B4C | 5.17 | 1.94 | –0.06 |
ZrB2 | 36.79 | 1.57 | 0.02 |
Все образцы характеризуются значительным разбросом частиц по размерам. Наблюдается закономерное увеличение размера частиц фазы B4C в результате термообработки в сравнении с исходным порошком B4C (2.1 мкм). Величины стандартного отклонения свидетельствуют о широком диапазоне распределения частиц по размерам (частицы полидисперсны). Невысокое значение степени асимметричности является доказательством симметричности кривых распределения. Наибольшее значение среднего размера частиц фаз B4C и ZrB2 характерно для образца, состав которого близок к эвтектическому (25 мол. % ZrB2).
Значения удельной поверхности для образцов Z10, Z20, Z25 и Z30 составили 1.8, 2.1, 1.3 и 1.7 м2/г соответственно. Таким образом, наименьшая удельная поверхность характерна для образца, содержащего 25 мол. % ZrB2.
При нагревании композиционных порошков B4C/ZrB2 в токе синтетического воздуха процесс окисления предположительно протекает в соответствии с реакцией (4). При этом наблюдается прирост массы образцов
(4)
$\begin{gathered} х{\text{Zr}}{{{\text{B}}}_{2}} + y{{{\text{B}}}_{{\text{4}}}}{\text{C}} + (2.5x + 4y){{{\text{O}}}_{2}} = \\ = \,\,x{\text{Zr}}{{{\text{O}}}_{2}} + (x + 2y){{{\text{B}}}_{{\text{2}}}}{{{\text{O}}}_{3}} + y{\text{C}}{{{\text{O}}}_{2}}. \\ \end{gathered} $Для определения термоокислительной стабильности полученных порошков проводили их окисление в атмосфере кислорода. Термогравиметрические кривые порошков B4C/ZrB2 различного состава практически идентичны. На рис. 9 представлены результаты термического анализа образца Z10.
Результаты термогравиметрического анализа показывают, что прирост массы, вызванный процессом окисления, начинается при температуре ~550°С. При достижении 1000°С окисляется не более 50% порошкового материала (табл. 4).
Таблица 4.
Результаты термогравиметрического анализа образцов B4C/ZrB2
Образец | Расчетная прибыль массы, % | Фактическая прибыль массы, % | Массовая доля окисленных веществ, % |
---|---|---|---|
Z10 | 237 | 106 | 45 |
Z20 | 225 | 95 | 42 |
Z25 | 219 | 83 | 38 |
Z30 | 214 | 78 | 36 |
Неполное окисление образцов можно объяснить образованием жидкой защитной пленки оксида бора В2О3 (температура плавления ~450°С) [30] на поверхности частиц B4C и ZrB2. Следует отметить, что доля окисленных веществ в композиционном материале уменьшается с увеличением содержания ZrB2. Это позволяет сделать вывод, что внесение модифицирующей добавки ZrB2 повышает стойкость материала к окислению при повышенных температурах.
Проведенные исследования показали, что получение композиционных порошков B4C/ZrB2 методом карбидоборного восстановления позволяет получить материал с относительно равномерным распределением частиц ZrB2 в матрице В4С. При этом наличие модифицирующей добавки повышает термоокислительную стабильность композиционного порошка и делает его перспективным для изготовления керамики. Однако полученная таким образом шихта должна подвергаться предварительному измельчению, поскольку в синтезированном материале обнаружено наличие относительно крупных включений фазы ZrB2. Кроме того, компактирование порошков B4C/ZrB2 следует проводить в инертной среде или в вакууме, поскольку материал склонен к окислению кислородом воздуха при температурах выше 550°С.
ЗАКЛЮЧЕНИЕ
Композиционные порошки B4C/ZrB2 получены методом карбидоборного восстановления оксида циркония в присутствии избытка карбида бора и нановолокнистого углерода. Установлено, что процесс образования фазы ZrB2 начинается при 1200°С, но полностью завершается при 1650°С. Дальнейшее повышение температуры приводит к увеличению размера частиц. Увеличение содержания ZrB2 с 10 до 30 мол. % приводит к повышению термической стойкости материала в окислительной среде. Средний размер 50% частиц композиционного порошка для данных составов не превышает 10 мкм, значение удельной поверхности находится в диапазоне 1.3–2.1 м2/г. Полученный композиционный материал перспективен для изготовления керамики.
Список литературы
Yuan Y., Ye T., Wu Y., Xu Y. Mechanical and Ballistic Properties of Graphene Platelets Reinforced B4C Ceramics: Effect of TiB2 Addition // Mater. Sci. Eng. A. 2021. V. 45. № 17 P.141294. https://doi.org/10.1016/j.ceramint.2019.08.095
Wu C., Li Y.K., Wan C.L. Reactive-Sintering B4C Matrix Composite for Armor Applications // Rare Met. 2020. V. 39. P. 529–544. https://doi.org/10.1016/j.ceramint.2019.08.095 10.1007/s12598-020-01404-6
Zhang X., Zhang Z., Sun Y., Xiang M., Wang G., Bai Y., Mu J., Che H., Wang W. Preparation, Microstructure and Toughening Mechanism of Superhard Ultrafine-Grained Boron Carbide Ceramics with Outstanding Fracture Toughness // J. Alloys Compd. 2018. V. 762. P. 125–132. https://doi.org/10.1016/j.jallcom.2018.05.228
Shon I.J. High-Frequency Induction Sintering of B4C Ceramics and Its Mechanical Properties // Ceram. Int. 2016. V. 42. № 16 P. 19406–19412. https://doi.org/10.1016/j.ceramint.2016.08.132
Liu Y., Ge S., Huang Y., Huang Z., Zhang D. Influence of Sintering Process Conditions on Microstructural and Mechanical Properties of Boron Carbide Ceramics Synthesized by Spark Plasma Sintering // Materials (Basel). 2021. V. 14. P. 1–14. https://doi.org/10.3390/ma14051100
Swab J.J., Pittari J.J., Gamble W.R. Uniaxial Tensile Strength and Fracture Analysis of a Hot-Pressed Boron Carbide // J. Eur. Ceram. Soc. 2019. V. 39. № 6. P. 1965–1973. https://doi.org/10.1016/j.jeurceramsoc.2019.01.031
Parlakyigit A.S., Ergun C. In situ Synthesis of B4C–SiC, B4C–TiB2, and B4C–ZrB2 Composites from Organic–Inorganic Hybrid Precursor via a Simple Bottom-Up Approach // J. Sol-Gel Sci. Technol. 2019. V. 92. P. 745–759. https://doi.org/10.1007/s10971-019-05143-8
Щербаков В.А., Грядунов А.Н., Алымов М.И. Самораспространяющийся высокотемпературный синтез композитов ZrB2–B4C с дисперсной фазой в виде пустотелых оболочек // Докл. Академии наук. 2019. Т. 485. № 2. С. 190–193. https://doi.org/10.31857/S0869-56524852190-193
Крутский Ю.Л., Гудыма Т.С., Дюкова К.Д., Кузьмин Р.И., Крутская Т. М. Дибориды некоторых переходных металлов: свойства, области применения и методы получения. Часть 2. Дибориды хрома и циркония // Изв. вузов. Черная металлургия. 2021. Т. 64. № 6. С. 395–412. https://doi.org/10.17073/0368-0797-2021-6-395-412
Neuman E.W., Thompson M., Fahrenholtz W.G., Hilmas G.E. Thermal Properties of ZrB2-TiB2 Solid Solutions // J. Eur. Ceram. Soc. 2021 V. 41. № 15. P. 7434–7441. https://doi.org/10.1016/j.jeurceramsoc.2021.08.004
Zhang S.C., Hilmas G.E., Fahrenholtz W.G. Pressureless Densification of Zirconium Diboride with Boron Carbide Additions // J. Am. Ceram. Soc. 2006. V. 89. № 2. P. 1544–1550. https://doi.org/10.1111/j.1551-2916.2006.00949.x
He R., Jing L., Qu Z., Zhou Z., Ai S., Kai W. Effects of ZrB2 Contents on the Mechanical Properties and Thermal Shock Resistance of B4C-ZrB2 Ceramics // Mater. Des. 2015. V. 71. P. 56–61. https://doi.org/10.1016/j.matdes.2015.01.002
Radev D., Zahariev Z. Oxidation Stability of B4C–MexBy, Composite Materials // J. Alloys Compd. 1993. V. 197. P. 87–90. https://doi.org/10.1002/CHIN.199335028
Wenbo H., Jiaxing G., Jihong Z., Jiliang Y. Microstructure and Properties of B4C-ZrB2 Ceramic Composites // Int. J. Eng. Innov. Technol. 2013. V. 3. P. 163–166.
Cheng Y.H., Han W.B., Liu D.Z., An J.D., Wang P., Zhao G.D. Spark Plasma Sintering of B4C–ZrB2 and B4C–ZrB2–SiC Ceramics // Mater. Res. Innov. 2015. V. 19. P. 1343–1346. https://doi.org/10.1179/1432891715Z.0000000001501
Le T.D., Hirota K., Kato M., Miyamoto H., Yuasa M., Nishimura T. Fabrication of Dense ZrB2/B4C Composites Using Pulsed Electric Current Pressure Sintering and Evaluation of Their High-Temperature Bending Strength // Ceram. Int. 2020. V. 46. № 11. P. 18478–18486. https://doi.org/10.1016/j.ceramint.2020.04.153
Щербаков В.А., Грядунов А.Н., Алымов М.И. Синтез и характеристики композитов B4C–ZrB2// Письма о материалах. 2017. Т. 7. № 4. С. 398–401. https://doi.org/10.22226/2410-3535-2017-4-398-401
Huang S.G., Vanmeensel K., Vleugels J. Powder Synthesis and Densification of Ultrafine B4C-ZrB2 Composite by Pulsed Electrical Current Sintering // J. Eur. Ceram. Soc. 2014. V. 34. № 4. P. 1923–1933. https://doi.org/10.1016/j.jeurceramsoc.2014.01.022
Gudyma T.S., Krutskii Yu.L., Uvarov N.F., Aparnev A.I. Optimization of the Obtaining Temperature of Powder Composite Material B4C–ZrB2 by the Boron Carbide Method // Matec Web Conf. 2021. V. 340. P. 5. https://doi.org/10.1051/matecconf/202134001028
Крутский Ю.Л., Баннов А.Г., Соколов В.В., Дюкова К.Д., Шинкарев В.В., Ухина А.В., Максимовский Е.А., Пичугин А.Ю., Соловьев Е.А., Крутская Т.М., Кувшинов Г.Г. Синтез высокодисперсного карбида бора из нановолокнистого углерода // Российские нанотехнологии. 2013. Т. 8. № 3–4. С. 43–48. https://doi.org/10.1134/S1995078013020109
Курмашов П.Б., Максименко В.В., Баннов А.Г., Кувшинов Г.Г. Горизонтальный пилотный реактор с виброожиженным слоем для процесса синтеза нановолокнистого углерода // Хим. технология. 2013. № 10. С. 635–640.
Попов М.В. Повышение эффективности процесса получения метано-водородной смеси каталитическим разложением легких углеводородов: Автореф. дис. … канд. тех наук: 05.17.08. Новосибирск. 2019. с. 20.
Ordan’yan S.S. Rules for the Reactions in B4C–MeIV–VIB2 Systems // Refractories. 1993. V. 34. P. 268–271. https://doi.org/10.1007/bf01293229
Взаимодействие окислов металлов с углеродом / Под ред. Елютина В.П. и др. М.: Металлургия, 1976. 360 с.
Шестаков В.А., Гудыма Т.С., Крутский Ю.Л., Уваров Н.Ф., Брестер А.Е., Сковородин И.Н. Оценка температурного диапазона процессов синтеза порошковых композиционных материалов B4C–TIB2 и B4C–ZRB2 // Неорган. материалы. 2021. Т. 57. № 5. С. 506–511. https://doi.org/10.31857/S0002337X21050080
Shestakov V.A., Gudyma T.S., Krutskii Y.L., Uvarov N.F. Determination of the Optimal Temperature Range for Synthesis of B4C-TiB2 and B4C–ZrB2 Powder Composite Materials // Mater. Today Proc. 2020 V. 31. P. 506–508. https://doi.org/10.1016/j.matpr.2020.05.822
Крутский Ю.Л., Непочатов Ю.К., Пель А.Н., Сковородин И.Н., Дюкова К.Д., Крутская Т.М., Кучумова И.Д., Матц О.Э., Тюрин А.Г., Эмурлаева Ю.Ю., Подрябинкин С.И. Синтез полидисперсного карбида бора и получение керамики на его основе // Журн. прикл. химии. 2019. Т. 92. № 6. С. 719–727. https://doi.org/10.1134/S0044461819060045
Крутский Ю.Л., Максимовский Е.А., Попов М.В., Нецкина О.В., Крутская Т.М., Черкасова Н.Ю., Квашина Т.С., Дробяз Е.А. Синтез высокодисперсного диборида циркония для изготовления керамики специального назначения // Журн. прикл. химии. 2017. Т. 90. № 10. С. 1295–1302.
Blott S.J., Pye K. Technical Communication Gradistat : a Grain Size Distribution and Statistics Package for the Analysis of Unconsolidated Sediments // Earth Surf. Process. Landforms. 2001 V. 1248. P. 1237–1248. https://doi.org/10.1002/esp.261
Физико-химические свойства окислов: Cправ. изд. / Под общ. ред. Самсонова Г.В. М.: Металлургия, 1978. 472 с.
Дополнительные материалы отсутствуют.
Инструменты
Неорганические материалы