Неорганические материалы, 2022, T. 58, № 9, стр. 973-981
Высокотемпературный синтез материалов на основе Mo3Al2C при горении порошковых смесей MoO3 + Al + C + Al2O3
Д. Ю. Ковалев 1, *, В. А. Горшков 1, О. Д. Боярченко 1
1 Институт структурной макрокинетики и проблем материаловедения им. А.Г. Мержанова
Российской академии наук
142432 Московская обл., Черноголовка, ул. Академика Осипьяна, 8, Россия
* E-mail: kovalev@ism.ac.ru
Поступила в редакцию 24.03.2022
После доработки 06.05.2022
Принята к публикации 12.05.2022
- EDN: LJRWUI
- DOI: 10.31857/S0002337X22090081
Аннотация
Представлены результаты по исследованию самораспространяющегося высокотемпературного синтеза литых материалов в системе Mo–Al–C. Эксперименты проводили в реакторе объемом 3 л при давлении аргона р = 5 МПа. В качестве шихты использовали смеси порошков оксида молибдена(VI) с алюминием (АСД-I), углеродом (графитом) и оксидом алюминия (электрокорундом). Показано, что, варьируя содержание исходных реагентов в шихте, можно влиять на параметры синтеза, фазовый состав и микроструктуру конечных продуктов. Обнаружено, что при стехиометрическом содержании исходных компонентов, рассчитанном на фазу Mo3Al2C, в эксперименте, кроме целевой фазы, образуются алюминиды и карбиды молибдена. Смесь горит с разбросом реагентов и конечных продуктов. Увеличение содержания целевой фазы Mo3Al2C в продуктах синтеза происходит при разбавлении исходной смеси инертной добавкой Al2O3. Максимальное содержание Mo3Al2C в слитке достигается при 20% Al2O3.
ВВЕДЕНИЕ
В системе Mo–Al–C бинарные соединения (карбиды и алюминиды) молибдена известны и хорошо изучены. Среди них наиболее широко используется на практике карбид молибдена Mo2C [1]. Карбид молибдена применяется в качестве катализатора, заменяющего благородные металлы (Pt, Pd и Ir) в реакциях гидрообессеривания, гидрообескислороживания, в сухом риформинге метана, в качестве анодного катализатора для микробных топливных элементов, катализатора для разложения гидразина, в регуляторах малых двигателей космических ракет [2–4]. Для синтеза карбида молибдена применяются разные методы: карботермическое восстановление MoO3 графитом в инертной среде, электрохимический синтез, плавка с графитом, восстановление оксида с помощью метан-водородной смеси или других источников углерода [5, 6]. Из тройных соединений молибдена с алюминием и углеродом наибольший интерес представляет соединение Mo3Al2C – сверхпроводник с температурой перехода Tc ~ 9 K. В работах [7–9] это соединение получали методами дугового и высокочастотного плавления при давлении до 10 ГПа. Известные способы получения Mo3Al2C малопроизводительны и энергозатратны.
Перспективным способом получения таких соединений является одностадийный метод – самораспространяющийся высокотемпературный синтез (СВС). Он практически не требует затрат электроэнергии, обладает высокой производительностью и экологической чистотой [10, 11]. Одним из технологических направлений этого процесса является СВС-металлургия, позволяющая получать “литые” материалы за счет полного плавления компонентов в волне горения. Особенность процесса состоит в использовании смесей, состоящих из оксидов металлов, металла-восстановителя (Al) и углерода. При определенном соотношении реагентов температура горения превышает температуру плавления исходных реагентов и конечных продуктов. В результате продукт во время синтеза формируется в жидком состоянии. Из-за различного удельного веса под действием гравитации происходит сепарация тяжелой металлоподобной и легкой оксидной фаз образовавшихся продуктов. Из тройных соединений, полученных этим методом, наиболее интересными являются MAX-фазы: Cr2AlC [12–14], Nb2AlC [15, 16], V2AlC [17].
Целью работы является получение методом СВС литого материала на основе фазы Mo3Al2C из порошковой смеси MoO3 + Al + C и исследование влияния инертной добавки Al2O3 на его фазовый состав и микроструктуру.
ЭКСПЕРИМЕНТАЛЬНАЯ ЧАСТЬ
В качестве исходных реагентов использовали порошки MoO3 (“ч.”, чистота 99.9%), Al (АСД-1, чистота 99.2%, размер частиц менее 30 мкм), графита (ПГ, чистота 99.2%, размер частиц менее 400 мкм) и Al2O3 (электрокорунд белый, чистота 99.6%, размер частиц 315–250 мкм). Состав базовой смеси рассчитывали исходя из реакции
(1)
$3{\text{Mo}}{{{\text{O}}}_{{\text{3}}}} + 8{\text{Al}} + {\text{C = M}}{{{\text{o}}}_{{\text{3}}}}{\text{A}}{{{\text{l}}}_{{\text{2}}}}{\text{C}} + 3{\text{A}}{{{\text{l}}}_{{\text{2}}}}{{{\text{O}}}_{{\text{3}}}}.$Эксперименты показали, что горение такой смеси протекает с выбросом реагентов из тигля. Поэтому в стехиометрическую смесь (3MoO3 + 8Al + C) в качестве инертного компонента добавляли Al2O3 в количестве 10, 20, 30% от массы базовой смеси. При этом соотношение между реагентами MoO3, Al и C во всех опытах было постоянным, рассчитанным из реакции (1). В работе концентрации фаз приведены в мас. %. Перед смешиванием порошки выдерживали в сушильном шкафу СНОЛ в течение 3 ч при температуре 60°С. Шихту готовили перемешиванием вручную в фарфоровой ступке. Реакционную смесь насыпной плотности помещали в кварцевый тигель диаметром 20 и высотой 50 мм (рис. 1б). Синтез проводили в реакторе (рис. 1а) объемом 3 л в среде Ar при начальном давлении 5 МПа по методике [12]. Реакцию инициировали спиралью из молибденовой проволоки. Скорость горения определяли по видеозаписи процесса, измеряя время прохождения волны горения по высоте образца. Для оценки параметров синтеза использовали следующие величины: ηс – выход продукта в слиток и ηр – потеря массы за счет разлета компонентов при горении:
Рис. 1.
Схема реактора: 1 – корпус, 2 – подложка, 3 – смотровое окно, 4 – шихта, 5 – инициирующая спираль (а); кварцевый тигель с шихтой (б); конечные продукты: оксидный слой (1) “металлический” слиток (2) (в).
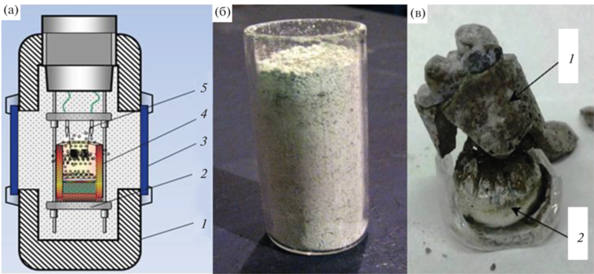
Рентгенофазовый анализ (РФА) продуктов синтеза проводили на дифрактометре ДРОН-3 (излучение CuKα). Для анализа использовался порошок дисперсностью менее 63 мкм, полученный путем размола слитка. Регистрация дифрактограмм велась в режиме пошагового сканирования в интервале углов 2θ = 20°–80° с шагом 0.02° и экспозицией 4 с. Количественный РФА проводился методом Ритвельда в пакете Jana2006 [18]. В качестве исходной модели для уточнения использовались структурные данные идентифицированных фаз, приведенные в Crystallography Open Database [19] и Materials Project [20]. Уточнялись профильные параметры рефлексов, фон, параметры элементарной ячейки, текстура и содержание фаз. Для прецизионного определения параметров элементарной ячейки применялся метод внутреннего эталона, в качестве которого использовался Si (NIST SRM 640b). Исследование микроструктуры и элементного состава образцов проводили на автоэмиссионном сканирующем электронном микроскопе сверхвысокого разрешения ULTRA Plus Zeiss с системой микроанализа INCA 350 Oxford Instruments.
РЕЗУЛЬТАТЫ И ОБСУЖДЕНИЕ
Образцы после синтеза состоят из двух легко разделяющихся слитков, различающихся по форме и плотности. Материал в верхней части образца имеет низкую плотность и, по результатам РФА, представляет собой преимущественно фазу α-Al2O3. В нижней части образуется каплевидный слиток с характерным металлическим блеском (рис. 1в). Формирование слитка свидетельствует об образовании жидкой фазы при протекании экзотермической реакции (1), т.е. температура горения смеси превышает температуру плавления образующихся соединений. Вследствие различия плотности и достаточно продолжительного времени нахождения материала в жидком состоянии под действием гравитации происходит фазоразделение – более тяжелая “металлическая” фаза оседает вниз тигля, а более легкая оксидная фаза формируется сверху.
Горение смеси без добавки инертного компонента протекает со скоростью 3.5 см/c и сопровождается выбросом из тигля ~16% от массы реагентов (табл. 1). При разбавлении смеси Al2O3 часть тепла, выделяемого в результате реакции (1), уходит на его плавление, что приводит к уменьшению скорости горения до 1.5 см/с при 30% добавки. Уменьшение скорости горения свидетельствует о снижении температуры горения, т.к., согласно [21], зависимость скорости горения (Uг) от температуры (Tг) имеет аррениусовский вид $U_{{\text{г}}}^{2}$ ~ ${{{\text{e}}}^{{E/R{{T}_{{\text{г}}}}}}}$. Максимальный выход продукта в слиток ηс ~ 44–45% наблюдается при 10–20% добавки (табл. 1). На выход влияют два конкурирующих фактора: разброс реагентов и температура горения. Увеличение количества добавки, с одной стороны, уменьшает разброс реагентов и, соответственно, повышает ηс. А с другой стороны, уменьшает температуру горения, что приводит к понижению ηс за счет уменьшения времени нахождения продукта в жидком состоянии, когда происходит пространственная сепарация оксидной и “металлической” фаз. В результате при максимальном содержании добавки преобладает температурный фактор, а при отсутствии добавки – фактор разброса.
Таблица 1.
Параметры синтеза в зависимости от содержания Al2O3
Смесь | Содержание Al2O3, мас. % | Uг, см/с | ηс, % | ηp, % |
---|---|---|---|---|
1 | 0 | 3.5 | 36 | 16 |
2 | 10 | 3.2 | 45 | 14 |
3 | 20 | 1.7 | 44 | 12 |
4 | 30 | 1.5 | 37.5 | 10 |
РФА слитков, полученных при горении смесей с различным содержанием добавки, показал, что в результате синтеза образуется материал, в состав которого входят фазы Mo3Al2C, Mo2C, Mo3Al и Mo3Al8. Количественное соотношение фаз зависит от содержания добавки Al2O3 в шихте (табл. 2).
Таблица 2.
Фазовый состав продукта в зависимости от содержания Al2O3
Смесь | С, мас. % | ||||
---|---|---|---|---|---|
Al2O3 | Mo3Al2C (P4132) | Mo3Al (Pm3n) |
Mo3Al8 (C2/m) |
Mo2C (Pbnc) |
|
1 | 0 | 24.3 | 57.3 | 9.3 | 9.1 |
2 | 10 | 65.5 | 9.0 | 6.0 | 19.5 |
3 | 20 | 73.7 | 7.5 | 1.6 | 17.2 |
4 | 30 | 60.3 | 0.6 | 3.7 | 35.4 |
Горение смеси 1 протекает в нестационарном режиме с нелинейным фронтом и частичным выбросом материала из тигля. Реакция (1) является высокоэкзотермичной с адиабатической температурой ~3000°С, что превышает температуру плавления Mo и соединений этой системы. РФА слитка (рис. 2б), образовавшегося при горении смеси 1, показал, что в результате синтеза формируется продукт с содержанием Mo3Al более 55%, в то время как содержание целевой фазы Mo3Al2С не превышает 25%. Суммарное содержание карбидных фаз Mo3Al2C и Mo2C в этом случае существенно ниже, чем в продуктах, полученных из смесей 2–4 с добавкой Al2O3. Можно предположить, что недостаток углерода связан с его выбросом из реакционной смеси в виде частиц или газообразных оксидов.
Рис. 2.
Микроструктура (СЭМ) (а) и дифрактограмма (эксперимент и расчет) (б) продукта горения смеси 1 (без добавки Al2O3).
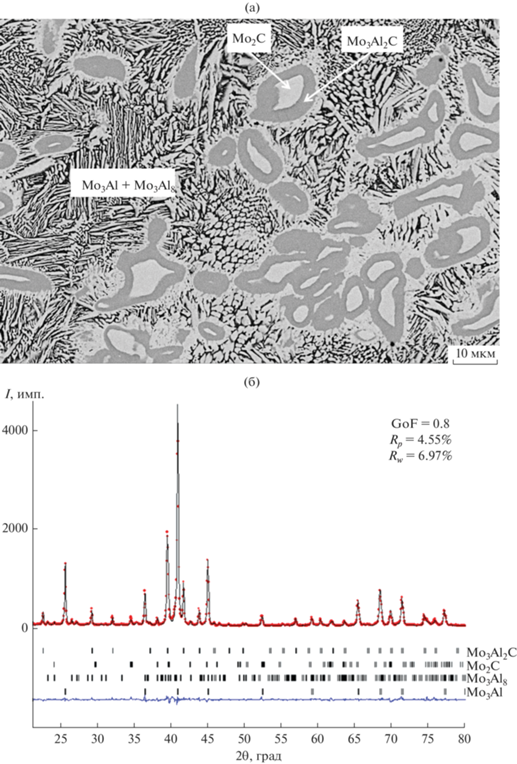
В волне горения смесь исходных реагентов претерпевает ряд физических и химических превращений. В зоне прогрева происходит плавление Al (tпл = 668°C) и МoО3 (tпл = 800°C), образующих жидкофазную среду, в которой распределены частицы графита. В зоне химического превращения происходит взаимодействие алюминия и углерода с оксидом молибдена:
(2)
${\text{Мo}}{{{\text{О}}}_{3}} + 2{\text{Al}} \to {\text{Mо}} + {\text{A}}{{{\text{l}}}_{{\text{2}}}}{{{\text{O}}}_{{\text{3}}}},$(3)
${\text{Мo}}{{{\text{О}}}_{3}} + х{\text{C}} \to {\text{Mо}}{{{\text{C}}}_{х}} + {\text{CO}}\left( {{\text{С}}{{{\text{О}}}_{{\text{2}}}}} \right) \uparrow .$В результате часть углерода в виде газа улетучивается из реакционной зоны и создается его недостаток для реакции (1). Чем выше температура горения смеси, тем больше вероятность участия углерода в окислительно-восстановительной реакции (3).
Микроструктура сплава (рис. 2a) отражает процесс кристаллизации и характеризуется наличием трех структурных составляющих: светлые зерна Mo2C; серые области Mo3Al2C, окружающие карбидную фазу, и эвтектоид Mo3Al + Mo3Al8. При охлаждении расплава Mo–Al–С происходит первичная кристаллизация с образованием зерен фазы Mo2C как наиболее тугоплавкой в рассматриваемой системе (tпл = 2486°C). В результате образуется расплав Mo–Al, окружающий зерна Mo2C, на границе которых протекает реакционная диффузия Al с формированием вокруг карбидного зерна тройного соединения Mo3Al2C (tпл ~ 1700°C). Наличие светлых областей Mo3Al на внешней границе фазы Mo3Al2C свидетельствует об обеднении расплава алюминием. Температура эвтектики Mo3Al + MoAl(h) (высокотемпературная фаза), составляющая 1720°C, близка к температуре плавления Mo3Al2C. Характерная эвтектоидная структура формируется при распаде MoAl(h) → Mo3Al + + Mo3Al8, и, согласно фазовой диаграмме Mo–Al [22], превращение происходит при 1470°С. В результате карбидные фазы находятся в эвтектоидной матрице Mo3Al + Mo3Al8, где более светлые ламели соответствуют фазе Mo3Al, а темные – фазе Mo3Al8. Полученный в результате горения смеси 1 фазовый состав не является равновесным, т.к. в системе Mo–Al–C отсутствуют области с одновременным существованием четырех фаз. В термодинамическом равновесии могут находиться только три фазы: Mo3Al2C–Mo2C–Mo3Al или Mo3Al2C–Mo3Al–Mo3Al8 (рис. 3). По-видимому, формирование неравновесного продукта обусловлено кинетическими затруднениями при диффузии атомов алюминия через слой фазы Mo3Al2C, окружающий частицы Mo2C. Кроме того, заложенный в соответствии с реакцией (1) стехиометрический состав на получение Mo3Al2C изменяется вследствие частичного выброса компонентов из тигля и протекания реакции (3).
Рис. 3.
Изотермическое сечение при 1000°С диаграммы состояния Mo–Al–C [23]; точками 3 и 4 обозначен состав продукта, полученный на основе результатов РФА для смесей с 20 и 30% Al2O3 соответственно.
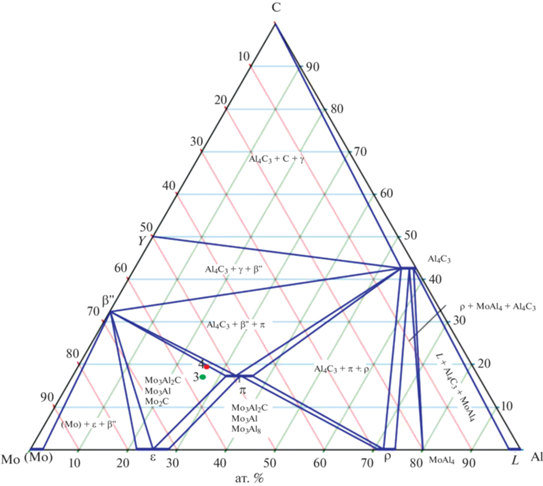
Введение в смесь 10–30% Al2O3 приводит к увеличению содержания карбидных фаз в продукте (табл. 2). Содержание интерметаллидов Mo3Al, Mo3Al8, образующих эвтектоид, последовательно снижается, а максимальный выход Mo3Al2C, составляющий ~74%, получен при разбавлении смеси 20% Al2O3. Фазовый состав слитков для смесей с 20 и 30% Al2O3 является практически равновесным и находится в трехфазной области Mo3Al2C–Mo2C–Mo3Al (точки 3 и 4 на диаграмме состояния (рис. 3)). Параметр элементарной ячейки Mo3Al2C составил 6.8666(2) Å и близок к параметру ячейки 6.866 Å, приведенному в базе PDF-2, Сard 000-65-3346. Однофазный продукт, содержащий только Mo3Al2C, не удалось получить, что обусловлено несколькими причинами. Во-первых, изменением стехиометрического состава в реакции (1) вследствие выброса компонентов при горении и протеканием реакции (3). Действительно, несмотря на введение инертной добавки, разброс ηp для смесей 3 и 4 составлял 10–12% (табл. 2). Возможно, помимо углерода, материал слитка обеднялся Al. Косвенным доказательством этого служит фазовый состав смеси 4, находящийся практически в двухфазной области Mo3Al2C–Mo2C. Во-вторых, высокой скоростью кристаллизации, определяемой условиями теплоотвода и теплофизическими свойствами системы. Микроструктура образцов (рис. 2, 4) указывает на то, что формирование слоя Mo3Al2C происходит на поверхности частиц Mo2C. Рост слоя происходит за счет диффузии Al через слой Mo3Al2C в зерно Mo2C. В результате быстрого охлаждения диффузия Al затруднена, что приводит к образованию многофазного материала.
ЗАКЛЮЧЕНИЕ
Методом СВС из порошковых смесей MoO3 + + Al + C + xAl2O3 получен литой материал, содержащий фазы Mo3Al2C, Mo2C, Mo3Al и Mo3Al8. Установлено существенное влияние инертной добавки Al2O3 на параметры синтеза, микроструктуру и фазовый состав слитка. Введение в реакционную смесь MoO3 + Al + C 10–30% Al2O3 приводит к увеличению содержания карбидных фаз в продукте. Максимальное содержание (~73%) целевой фазы Mo3Al2C получено при 20% Al2O3. Наличие вторичных фаз связано с изменением стехиометрического состава смеси вследствие выброса компонентов при горении и с реакцией между MoO3 и C с выделением газообразных оксидов углерода. Показано, что формирование слоев Mo3Al2C происходит на поверхности частиц Mo2C вследствие диффузии Al через слой тройной фазы в первичные кристаллы карбида молибдена.
Список литературы
Wang X.H., Hao H.L., Zhang M.H., Li W., Tao K.Y. Synthesis and Characterization of Molybdenum Carbides Using Propane as Carbon Source // J. Solid. State Chem. 2006. V. 179. P. 538–543.
Manoli J.M., Da Costa P., Brun M., Vrinat M., Mauge F., Potvin C. Hydrodesulfurization of 4,6-Dimethyldibenzothiophene over Promoted (Ni, P) Alumina-supported Molybdenum Carbide Catalysts: Activity and Characterization of Active Sites // J. Catal. 2004. V. 221. P. 365–377. https://doi.org/10.1016/j.jcat.2003.08.011
Zeng L., Zhang L., Li W., Zhao S., Lei J., Zhou Z. Molybdenum Carbide as Anodic Catalyst for Microbial Fuel Cell Based on Klebsiella Pneumoniae // Biosens. Bioelectron. 2010. V. 25. P. 2696–2700. https://doi.org/10.1016/j.bios.2010.05.002
Cho S.J., Lee J., Lee Y.S., Kim D.P. Characterization of Iridium Catalyst for Decomposition of Hydrazine Hydrate for Hydrogen Generation // Catal. Lett. 2006. V. 109. P. 181–186. https://doi.org/10.1007/s10562-006-0081-3
Nguyen T.H., Nguyen T.V., Lee Y.J., Safinski T., Adesina A.A. Structural Evolution of Alumina Supported Mo–W Carbide Nanoparticles Synthesized by Precipitation from Homogeneous Solution // Mater. Res. Bull. 2005. V. 40. P. 149–157. https://doi.org/10.1016/j.materresbull.2004.09.007
Zhu Q., Chen Q., Yang X., Ke D. A New Method for the Synthesis of Molybdenum Carbide // Mater. Lett. 2007. V. 61. P. 5173–5174. https://doi.org/10.1016/j.matlet.2007.04.056
Karki A.B., Xiong Y.M., Vekhter I., Browne D., Adams P.W., Thomas K.R., Chan J.Y., Prozorov R., Kim H., Young D.P. Structure and Physical Properties of the Noncentrosymmetric Superconductor Mo3Al2C // Phys. Rev. B. 2010. V. 82. P. 064512(1)–064512(7). https://doi.org/10.1103/PhysRevB.82.064512
Bonalde I., Kim H., Prozorov R., Rojas C., Rogl P., Bauer E. Evidence for Conventional Superconducting Behavior in Noncentrosymmetric Mo3Al2C // Phys. Rev. B. 2011. V. 84. P. 134506(1)–134506(4). https://doi.org/10.1103/PhysRevB.84.134506
Sekine1 C., Sai1 U., Hayashi1 J., Kawamura1 Y., Bauer E. High-Pressure Synthesis and Bulk Modulus of Non-centrosymmetric Superconductor Mo3Al2C // Ser. J. Phys. Conf. Ser. 2017. V. 950. P. 042028. https://doi.org/10.1088/1742-6596/950/4/042028
Merzhanov A.G. The Chemistry of Self-Propagating High-Temperature Synthesis // J. Mater. Chem. 2004. V. 14. № 12. P. 1779–1786. https://doi.org/10.1039/B401358C
Levashov E.A., Mukasyan A.S., Rogachev A.S., Shtansky D.V. Self-Propagating High-Temperature Synthesis of Advanced Materials and Coatings // Int. Mater. Rev. 2016. V. 62. № 4. P. 203–239. https://doi.org/10.1080/09506608.2016.1243291
Горшков В.А., Милосердов П.А., Лугинина М.А., Сачкова Н.В., Беликова А.Ф. Высокотемпературный синтез литого материала с максимальным содержанием МАХ-фазы Cr2AlC // Неорган. материалы. 2017. Т. 53. № 3. С. 260–266. https://doi.org/10.7868/S0002337X1703006X
Горшков В.А., Милосердов П.А., Сачкова Н.В., Лугинина М.А., Юхвид В.И. СВС-металлургия литых материалов на основе МАХ-фазы Cr2AlC // Изв. вузов. Порошк. металлургия и функц. покрытия. 2017. № 2. С. 47–54. https://doi.org/10.17073/1997-308X-2017-2-47-54
Горшков В.А., Милосердов П.А., Хоменко Н.Ю., Сачкова Н.В. Получение литых материалов на основе MAX-фазы Cr2AlC методом СВС-металлургии с использованием химически сопряженных реакций // Изв. вузов. Порошк. металлургия и функц. покрытия. 2019. № 4. С. 14–20. https://doi.org/10.17073/1997-308X-2019-4-14-20
Miloserdov P.A., Gorshkov V.A., Kovalev I.D., Kovalev D.Yu. High-Temperature Synthesis of Cast Materials Based on Nb2AlC MAX Phase // Ceram. Int. 2019. V. 45. № 2. P. 2689–2691. https://doi.org/10.1016/j.ceramint.2018.10.198
Ковалев И.Д., Милосердов П.А., Горшков В.А., Ковалев Д.Ю. Синтез МАХ-фазы Nb2AlC методом СВС-металлургии // Изв. вузов. Порошк. металлургия и функц. покрытия. 2019. № 2. С. 42–48. https://doi.org/10.17073/1997-308X-2019-2-42-48
Горшков В.А., Карпов А.В., Ковалев Д.Ю., Сычев А.Е. Синтез, структура и свойства материала на основе МАХ-фазы V2AlC // Физика металлов и металловедение. 2020. Т. 121. № 8. С. 842–848. https://doi.org/10.31857/S0015323020080033
Petricek V., Dusek M., Palatinus L. Crystallographic Computing System JANA2006: General Features // Z. Kristallogr. 2014. V. 229(5). P. 345–352. https://doi.org/10.1515/zkri-2014-1737
Crystallography Open Database. http://www.crystallography.net/cod
Jain A., Ong S.P., Hautier G. et al. The Materials Project: A Materials Genome Approach to Accelerating Materials Innovation // APL Materials. 2013. V. 1. P.011002(1)–011002(5). https://materialsproject.org.
Юхвид В.И., Боровинская И.П., Мержанов А.Г. Влияние давления на закономерности горения плавящихся гетерогенных систем // Физика горения и взрыва. 1983. № 3. С.30–32.
Schuster J.C. and MSIT. Springer Materials / Ed. Effenberg G. Heidelberg: Springer, 2005. 20.12123.1.3. https://materials.springer.com/msi/docs/sm_msi_r_ 20_012123_01
Velikanova T.Ya. and MSIT. Springer Materials / Ed. Effenberg G. Heidelberg: Springer, 1990. https://doi.org/10.22242.1.6. https://materials.springer.com/msi/docs/sm_msi_r_10_022242_01
Дополнительные материалы отсутствуют.
Инструменты
Неорганические материалы