Неорганические материалы, 2022, T. 58, № 9, стр. 1024-1032
Аналитическое сопровождение процесса получения теллура Т 000
О. В. Лундовская 1, А. Р. Цыганкова 1, 2, *, Н. А. Орлов 2, Ф. В. Яцунов 3
1 Институт неорганической химии им. А.В. Николаева СО Российской
академии наук
630090 Новосибирск, пр. Академика Лаврентьева, 3, Россия
2 Новосибирский национальный исследовательский государственный
университет
630090 Новосибирск, ул. Пирогова, 2, Россия
3 ООО “СибХимТехнологии”
633004 Бердск, ул. Химзаводская, 11/26, Россия
* E-mail: alphiya@yandex.ru
Поступила в редакцию 14.12.2021
После доработки 24.06.2022
Принята к публикации 27.06.2022
- EDN: YPCVKZ
- DOI: 10.31857/S0002337X2209010X
Аннотация
Исследование посвящено разработке унифицированной методики АЭС-ИСП, позволяющей оценить чистоту металлического теллура и примесный состав полупродуктов технологии получения теллура марки Т 000. Процесс получения состоит из двух последовательных стадий: гидрометаллургической переработки концентрата пылей электрофильтров, основанной на классической гидрометаллургической схеме переработки анодных шламов медного производства, и электролитического выделения теллура с последующей восстановительно-рафинирующей плавкой для получения металлического теллура. Для оперативного аналитического контроля технологии получения теллура марки Т 000 разработана атомно-эмиссионная спектральная методика. Выбраны аналитические линии, мощность индуктивно-связанной плазмы, оптимально-компромиссная концентрация матричного компонента и оценена правильность разработанной методики. В литературе отсутствуют экспрессные универсальные методики химического анализа металлического теллура, промежуточных продуктов разной степени чистоты и исходного сырья. Предложенная методика позволяет определять до 61 примеси с пределами обнаружения в интервале от n × 10–7 до n × 10–4 мас. % и внутрилабораторной прецизионностью не более 25%. Информация о содержании аналитов, полученная согласно предложенной методике, позволяет оптимизировать параметры технологического процесса, делать заключения о качестве исходного сырья и соответствии конечной продукции – металлического теллура – указанной марке Т 000. Полученные данные о химическом составе конечного продукта, промежуточных продуктов и сырья наглядно демонстрируют эффективность каждого этапа в предложенной схеме получения чистого теллура.
ВВЕДЕНИЕ
Теллур – это редкий металлоид с относительно низким содержанием в земной коре: 0.001–0.005 г/т (для сравнения: содержание золота в земной коре 0.0031 г/т, платины 0.0037 г/т) [1]. Металлический теллур и его соединения востребованы во многих сферах современного наукоемкого производства. В частности, стекла тройной системы Ge–Sb–Te прозрачны в дальнем ИК-диапазоне, а также испытывают быстрые и обратимые фазовые превращения при облучении лазерным лучом, что используется в технологии изготовления DVD-дисков [2]. Он широко используется в производстве полупроводников CdTe [3, 4], CdZnTe [5–7], BiTe [8, 9]. Значительная часть производимого в настоящее время теллура идет на изготовление высокоэффективных фотогальванических элементов для солнечных электростанций.
Диоксид теллура является ключевым компонентом при изготовлении стекол, обладающих уникальными свойствами: низкой температурой плавления, высоким показателем преломления и диэлектрической постоянной, прозрачностью в инфракрасной области [10, 11].
Основные промышленные источники для производства теллура – анодные шламы электролитического рафинирования меди, в значительно меньших масштабах щелочные съемы рафинирования чернового свинца и иные полупродукты металлургических производств [12, 13].
Данное исследование посвящено аналитическому сопровождению процесса получения теллура Т 000 путем обогащения продуктов аффинажного производства – гидроксидных осадков (ГО) с относительно высоким содержанием теллура. К образованию ГО неблагородных металлов от концентратов пылей электрофильтров (КПЭФ) приводит переработка полупродуктов аффинажного производства от концентратов драгоценных металлов (ДМ) ПАО “ГМК “Норильский никель” с последующей гидрометаллургической переработкой КПЭФ по извлечению ДМ.
С 2011 года на предприятии ООО “СибХимТехнологии” после ряда укрупненных испытаний была разработана и внедрена опытно-промышленная переработка ГО неблагородных металлов от КПЭФ, поступающих с ОАО “Красцветмет”. ГО от КПЭФ содержат в себе цветные металлы, основными из которых являются Te, Pb и Sn. ДМ представлены в полном составе – Au, Ag и металлы платиновой группы. За основу оригинальной схемы технологического производства была взята типовая схема гидрометаллургической переработки анодных шламов медного производства, в которую были внесены изменения. В настоящее время сырьe, поступающее с ОАО “Красцветмет”, характеризуется высоким содержанием свинца, что приводит к увеличению содержания данного примесного элемента в оксиде теллура – продукте для электроэкстракции теллура. Этим обусловлена необходимость оптимизации процесса очистки с целью получения теллура марки Т 000 (ГОСТ 17614-2018 [14]). Описанные в литературе методики анализа теллурсодержащих соединений трудоeмки и/или не приспособлены к столь разнообразным объектам (не только форма присутствия теллура, но и содержание примесей и сопутствующих компонентов, обусловленных технологией очистки). Для достижения цели рационально применить постадийный аналитический контроль современным многоэлементным методом, например атомно-эмиссионной спектрометрией с индуктивно связанной плазмой (АЭС-ИСП).
ТЕОРЕТИЧЕСКИЙ АНАЛИЗ
Общий технологический процесс получения теллура, внедрeнный на предприятии ООО “СибХимТехнологии”, можно разделить на две последовательных стадии: гидрометаллургическая переработка КПЭФ и электроэкстракция теллура из щелочного электролита с последующей восстановительно-рафинирующей плавкой.
На первом этапе гидрометаллургической переработки КПЭФ проводят выщелачивание (70°С) в растворе NaOH (80–100 г/л) при соотношении ТВ : Ж = 1 : 3. При этом в раствор переходят Se, Sn, Te, частично Pb (до 10 мас. %) и ряд примесных элементов, таких как Bi, Cu, Fe, Ni, Sb, Zn. На втором этапе проводят очистку теллуритных растворов введением сульфид-ионов S2–, которые приводят к осаждению некоторых элементов, например Pb, Se, Sn и ДМ. На последнем этапе переработки ГО проводят осаждение оксида теллура раствором серной кислоты из очищенного раствора теллурита натрия.
Электроэкстракция теллура из щелочного электролита проводится по следующей схеме: промытый от избытка натрия и отжатый оксид теллур растворяют в растворе KOH, после чего проводят процесс электролиза при концентрациях теллура 100–120 г/л. В результате электролиза образуется плотный катодный осадок – губчатый теллур с содержанием основного компонента 99.5–99.9%. После нейтрализации и подсушивания теллуровую губку направляют на восстановительно-рафинирующую плавку. На рис. 1 представлена общая схема получения теллура марки Т 000, разработанная и внедренная на ООО “СибХимТехнологии”.
Для характеризации исходного сырья, промежуточных и конечных продуктов, а также для выбора или оперативного изменения технологического процесса требуется аналитический контроль на всех стадиях процесса. Наибольшее внимание следует уделять примесям As, Fe, K, Na, Pb, Se, Sn, присутствие которых связано как с исходным материалом (КПЭФ), так и с технологией получения. Следует отметить, что кроме перечисленных элементов ГОСТ 17614-2018 на теллур Т 000 регламентирует содержание Al, Cu, Ni и Si.
Для решения поставленной задачи целесообразно применять многоэлементные спектральные методы. При аналитическом контроле теллура высокой чистоты используют методику ГОСТ 24977.2-81 [15], основанную на методе атомно-эмиссионной спектрометрии с возбуждением в дуге постоянного тока. Образцы сравнения и исследуемый образец готовят растворением в кислотах, далее полученные растворы упаривают на графитовом коллекторе. Данные методики позволяют определять 15 аналитов (Ag, Al, Au, Bi, Co, Cr, Cu, Fe, Ga, In, Mg, Mn, Ni, Pb, Sn) с пределами обнаружения (ПО) на уровне 10–6–10–3 мас. %.
Авторы методики количественного химического анализа (КХА) диоксида теллура [16] растертую до мелкодисперсного состояния пробу TeO2 смешивали с графитовым порошком, содержащим 30% NaCl, в соотношении 1 : 1 по массе. Далее определение примесей проводили методом атомно-эмиссионной спектрометрии с двухструйным дуговым плазмотроном (АЭС-ДДП). Методика позволяет определить 36 аналитов (Ag, Al, As, Au, Ba, Be, Bi, Ca, Cd, Co, Cr, Cu, Fe, Ga, Ge, Hf, Hg, In, La, Mg, Mn, Mo, Ni, Nb, Pb, Pd, Pt, Sb, Sc, Sn, Ta, Ti, Tl, V, W, Zn) с ПО на уровне 10–6–10–4 мас. %.
Анализ металлов и их оксидов при помощи приведенных методик – трудоемкий процесс. Пробоподготовка включает в себя растворение пробы, упаривание раствора на графитовом порошке и последующее последовательное разбавление графитовым порошком или спектральным буфером. В ходе подобной пробоподготовки трудно избежать загрязнения пробы и обеспечить экспрессность процедуры анализа.
Использование АЭС ИСП для анализа теллура, его оксида и других теллурсодержащих полупродуктов предпочтительней, так как процесс пробоподготовки сводится к растворению навески образца и приготовлению линейки растворов. Преимуществом является построение градуировочных зависимостей с использованием коммерчески доступных многоэлементных растворов.
ЭКСПЕРИМЕНТАЛЬНАЯ ЧАСТЬ
Анализ выполняли методом АЭС-ИСП с использованием спектрометра высокого разрешения iCAP-6500 (Thermo, Великобритания). Для растворения проб (сырье, промежуточный оксид теллура, теллур разной чистоты) использовали минимальные объемы концентрированных минеральных кислот: HNO3 ОСЧ 27–5 и HCl ОСЧ 20–4 дополнительно очищенных перегонкой без кипения; соотношение кислот HCl : HNO3 = 3 : 1. Растворение проводили при нагревании (95–100°С) в открытых сосудах при 1 атм. Масса навески 100 мг для КПЭФ, 300–500 мг для оксида теллура и теллура металлического. Для разбавления головных растворов проб использовали 1 М раствор HCl или 1 М смесь HCl : HNO3 = 3 : 1. Регистрацию первичных данных – спектров эмиссии – проводили в стандартных условиях, описанных в статье [17].
Для выбора аналитических линий (АЛ), свободных или подверженных минимальному влиянию со стороны матричного компонента, регистрировали полный спектр раствора, содержащего 70 мг/мл теллура, и раствор с тем же количеством матричного компонента и добавкой многоэлементных стандартных (МЭС) растворов 1, 2, 3, 4 и 5 (“Скат”, Новосибирск) и одноэлементных лабораторных стандартов МПГ (кроме Os).
Для изучения влияния концентрации матричного компонента на аналитические сигналы (АС) аналитов были приготовлены растворы, содержащие теллур в концентрации от 0 до 70 г/л с добавкой растворов МЭС 1, 2, 3, 4, 5 и одноэлементных лабораторных стандартов МПГ (кроме Os). Для коррекции возможных матричных помех использовали внутренний стандарт – иттрий с концентрацией металла 50 мкг/мл.
Влияние мощности на интенсивность АЛ изучали в интервале 750–1350 Вт с шагом в 200 Вт при стандартном потоке аргона через распылитель 0.7 л/мин. В ходе эксперимента регистрировали спектры растворов, содержащих 40 г/л теллура и добавку аналитов.
Чтобы оценить достоверность определения аналитов, ПО которых находятся в диапазоне от 1 × 10–7 до 4 × 10–4 мас. %, вводили примеси с концентраций в 2–10 раза выше ПО. Для приготовления образцов с введенными примесями к пробам добавляли известное количество примесей из растворов МЭС.
Концентрация аналитов во всех экспериментах составила 0.2 мкг/мл. Растворы МЭС содержали следующие аналиты:
• 1: Al, Ca, Cd, Fe, K, P, Mg, Mn, Na, Cr, Zn – 50 мкг/мл; Li – 10 мкг/мл;
• 2: B, V, Bi, Ga, In, Со, Cu, Ni, Si, Ti – 50 мкг/мл;
• 3: Вa, Sr – 20 мкг/мл; Be, Ag, Au – 10 мкг/мл; As, Sn, Pb, Rb, Se, Sb – 50 мкг/мл; Hg – 5 мкг/мл;
• 4: W, Hf, Mo, Nb, Re, Ta, Zr – 50 мкг/мл;
• 5: Се, Dy, Er, Eu, Gd, Но, Lа, Lu, Nd, Pr, Sc, Sm, Tb, Tm – 50 мкг/мл; Yb – 25 мкг/мл.
РЕЗУЛЬТАТЫ И ОБСУЖДЕНИЕ
При АЭС-ИСП чистого теллура важно обеспечить минимальные ПО примесных элементов. Достигнуть низких ПО, не прибегая к отделению матричного компонента и концентрированию примесей, можно при анализе растворов с высоким содержанием матричного компонента. При этом необходимо добиться высокого АС аналита при минимальном уровне флуктуации фона. В ходе разработки методик КХА указанных объектов был проведен выбор спектральных линий, концентрации матричного компонента, мощности ИСП, выполнена оценка ПО аналитов и правильности их определения.
Выбор АЛ. Принимая во внимание все особенности профиля спектра теллура, было изучено более 100 спектральных линий, в качестве АЛ выбраны линии для 61 аналита и элемента внутреннего стандарта. Список АЛ с достаточной относительной интенсивностью и минимальным уровнем спектральных интерференций приведен в табл. 1 (I – атомные линии, II – ионные линии).
Таблица 1.
АЛ для АЭС-ИСП теллура и его соединений
Элемент | λ, нм | Тип | Элемент | λ, нм | Тип | Элемент | λ, нм | Тип |
---|---|---|---|---|---|---|---|---|
Ag | 328.068 | I | Gd | 335.047 | II | Rb | 780.023 | I |
338.289 | I | Hf | 232.247 | II | Re | 227.525 | II | |
Al | 394.401 | I | 339.980 | II | Ru | 240.272 | II | |
396.152 | I | Hg | 194.227 | II | 349.894 | I | ||
As | 189.042 | I | Ho | 345.600 | II | Pb | 216.999 | I |
197.262 | I | 339.898 | II | 220.353 | II | |||
Au | 242.795 | I | In | 325.609 | I | 261.418 | II | |
267.595 | I | 230.606 | II | Sb | 217.581 | I | ||
B | 249.773 | I | Ir | 212.861 | II | Sc | 361.384 | II |
249.678 | I | 205.222 | I | 363.075 | II | |||
Ba | 455.403 | II | K | 766.490 | I | Se | 196.090 | I |
493.409 | II | Li | 670.784 | I | 241.350 | I | ||
Be | 234.861 | I | La | 333.749 | II | Si | 251.611 | I |
313.107 | II | 412.323 | II | 288.158 | I | |||
Bi | 223.061 | I | Lu | 261.542 | II | Sm | 330.639 | II |
Ca | 393.366 | II | 291.139 | II | Sn | 189.989 | II | |
396.847 | II | Mg | 279.553 | II | 283.999 | I | ||
Cd | 226.502 | II | 280.270 | II | 242.949 | I | ||
228.802 | I | Mn | 259.373 | II | Sr | 407.771 | II | |
Ce | 404.4076 | II | 260.569 | II | 421.552 | II | ||
Co | 228.616 | II | Mo | 202.030 | II | Ta | 263.558 | II |
238.892 | II | 284.823 | II | Tb | 332.440 | II | ||
Cr | 205.562 | II | Na | 589.592 | I | 350.917 | II | |
267.716 | II | Nb | 313.079 | II | Ti | 323.452 | II | |
Cu | 324.754 | I | Nd | 406.109 | II | 334.941 | II | |
327.396 | I | 401.225 | II | Tm | 346.220 | II | ||
Dy | 353.170 | II | Ni | 231.604 | II | V | 309.311 | II |
364.540 | II | P | 177.495 | I | 292.402 | II | ||
Er | 323.058 | II | 178.284 | I | Y | 224.306 | II | |
337.271 | II | Pd | 340.458 | I | 371.030 | II | ||
Eu | 381.967 | II | 342.124 | I | Yb | 328.937 | II | |
412.970 | II | Pt | 214.423 | II | 369.419 | II | ||
Fe | 259.837 | II | 265.945 | I | W | 207.911 | II | |
239.562 | II | Pr | 414.311 | II | 224.875 | II | ||
259.940 | II | 422.535 | II | Zn | 213.856 | II | ||
Ga | 294.364 | I | Rh | 343.489 | I | Zr | 339.198 | II |
403.298 | I | 369.236 | I | 343.823 | II |
Выбор концентрации матричного компонента. Для унификации методик анализа теллура и его соединений целесообразно использовать единый набор образцов сравнения, например на основе водных или слабокислых растворов. По этой причине необходимо изучить влияние концентрации матричного компонента на АС аналитов. Для оценки уровня влияния концентрации матричного компонента на АС аналитов пользовали следующую относительную величину: Iотн = (ITe+добавка – ITe)/Sф, где (ITe+добавка – ITe) – чистый сигнал аналита для раствора, содержащего теллур (от 0 до 70 г/л); SФ – среднеквадратичное отклонение (СКО) сигнала фона при регистрации спектров раствора, содержащего теллур (от 0 до 70 г/л). На рис. 2 для удобства сопоставления изменения Iотн для АЛ, обладающих различной интенсивностью, значения Iотн нормировали на отношение $I_{{{\text{отн}}}}^{0}$ для раствора с концентрацией теллура 0 г/л. В качестве примера приведены некоторые АЛ: Bi 223.061, Cr 283.562, Cu 327.396, Ga 294.364, Mg 280.270, Pb 220.353, Sb 217.581 нм. Видно, что максимум отношения Iотн/$I_{{{\text{отн}}}}^{0}$ наблюдается при концентрации теллура 40 г/л, в дальнейшем все эксперименты проводили при указанной концентрации матричного компонента. Для выбранной концентрации матрицы экспериментально показано наличие депрессирующего влияния на АС некоторых аналитов. При этом применение внутреннего стандарта Y полностью компенсирует эффекты и позволяет исключить систематические погрешности при определении аналитов.
Рис. 2.
Зависимости Iотн/$I_{{{\text{отн}}}}^{0}$ примесных элементов от концентрации теллура в растворе.
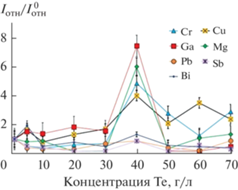
Выбор мощности ИСП. При выборе оптимальной мощности плазмы принимали во внимание тип АЛ (атомные и ионные). Как и при выборе оптимальной концентрации теллура, оценивали относительную интенсивность АС при разной мощности IW. Значения IW для текущей мощности нормировали на значение IWдля начальной мощности ИСП – 750 Вт ($I_{W}^{{750}}$). На рис. 3 представлены зависимости IW/$I_{W}^{{750}}$ от мощности плазмы для атомных и ионных АЛ.
Рис. 3.
Зависимости IW/$I_{W}^{{750}}$ примесных элементов от мощности плазмы для атомных и ионных АЛ.
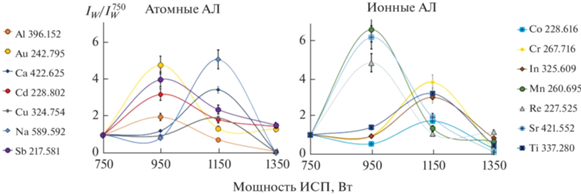
Зависимости, представленные на рис. 3, демонстрируют наличие двух экстремумов при мощности 950 и 1150 Вт, видно, что наличие экстремумов не зависит от типа АЛ. Повтор эксперимента в интервале 950–1150 Вт с шагом 100 Вт показал, что наибольшее количество АЛ достигает максимума IW при мощности ИСП 1150 Вт (см. рис. 4), по этой причине указанная мощность была выбрана в качестве оптимально-компромиссной и использована для всех дальнейших экспериментов.
Оценка ПО методики. Для оценки ПО аналитов использовали 3s-критерий: ПО = ЗSф, где Sф – СКО концентрации аналита в растворе, содержащем 40 г/л теллура. Величину Sф рассчитывали из 10–12 значений с использованием самого чистого образца теллура, имеющегося в нашем распоряжении (6N). Результаты оценки ПО и сравнение их с опубликованной ранее инструментальной методикой анализа диоксида теллура методом АЭС-ДДП [16] представлены в табл. 2.
Таблица 2.
Сравнение ПО для опубликованной методики [16] и разработанной АЭС-ИСП
Аналит | ПО, мас. % | Аналит | ПО, мас. % | ||
---|---|---|---|---|---|
[16] | АЭС ИСП | [16] | АЭС ИСП | ||
Ag | 3 × 10–6 | 3 × 10–6 | Mo | 2 × 10–5 | 3 × 10–6 |
Al | 5 × 10–5 | 8 × 10–6 | Na | – | 2 × 10–6 |
As | 8 × 10–4 | 1 × 10–5 | Nb | 9 × 10–5 | 2 × 10–6 |
Au | 5 × 10–5 | 2 × 10–6 | Nd | – | 3 × 10–6 |
B | – | 3 × 10–6 | Ni | 2 × 10–5 | 1 × 10–5 |
Ba | 5 × 10–5 | 3 × 10–7 | P | – | 5 × 10–5 |
Be | 3 × 10–6 | 3 × 10–7 | Pb | 5 × 10–5 | 9 × 10–5 |
Bi | 2 × 10–5 | 1 × 10–5 | Pd | 3 × 10–5 | 3 × 10–6 |
Ca | 1 × 10–4 | 3 × 10–6 | Pr | – | 7 × 10–6 |
Cd | 1 × 10–5 | 1 × 10–6 | Pt | 5 × 10–5 | 2 × 10–5 |
Ce | – | 7 × 10–6 | Rb | – | 2 × 10–5 |
Co | 1 × 10–5 | 1 × 10–6 | Re | – | 4 × 10–6 |
Cr | 2 × 10–5 | 1 × 10–5 | Rh | – | 7 × 10–5 |
Cu | 6 × 10–6 | 1 × 10–5 | Ru | – | 3 × 10–5 |
Dy | – | 1 × 10–6 | Sb | 8 × 10–5 | 6 × 10–5 |
Er | – | 3 × 10–6 | Sc | 4 × 10–5 | 2 × 10–7 |
Eu | – | 4 × 10–7 | Se | – | 6 × 10–5 |
Fe | 3 × 10–5 | 5 × 10–5 | Si | – | 2 × 10–5 |
Ga | 8 × 10–6 | 2 × 10–5 | Sm | – | 1 × 10–5 |
Ge | 2 × 10–4 | – | Sn | 3 × 10–5 | 4 × 10–4 |
Gd | – | 4 × 10–6 | Sr | – | 1 × 10–7 |
Hf | 5 × 10–5 | 2 × 10–6 | Ta | 3 × 10–4 | 1 × 10–5 |
Hg | 1 × 10–4 | 5 × 10–6 | Tb | – | 3 × 10–6 |
Ho | – | 2 × 10–6 | Ti | 2 × 10–5 | 3 × 10–6 |
In | 5 × 10–5 | 1 × 10–5 | Tl | 4 × 10–5 | – |
Ir | – | 1 × 10–4 | Tm | – | 1 × 10–6 |
K | – | 1 × 10–4 | V | 2 × 10–5 | 1 × 10–6 |
La | 4 × 10–5 | 1 × 10–6 | W | 2 × 10–4 | 4 × 10–5 |
Li | – | 1 × 10–5 | Yb | – | 1 × 10–7 |
Lu | – | 2 × 10–7 | Zn | 3 × 10–5 | 3 × 10–6 |
Mg | 4 × 10–6 | 1 × 10–6 | Zr | – | 3 × 10–7 |
Mn | 3 × 10–6 | 1 × 10–6 |
Методика [16] позволяет определять 36 аналитов, в том числе Ge и Tl, которые не определяли методом АЭС-ИСП. Разработанная методика АЭС-ИСП позволяет определять 61 аналит, в том числе 17 важных технологических примесей – Ag, Al, As, Au, Cd, Co, Cr, Cu, Fe, Hg, Ga, In, Mg, Mn, Ni, Pb и Sb [14]; 5 МПГ – Ir, Pd, Pt, Rh и Ru; 15 РЗЭ – Се, Dy, Er, Eu, Gd, Но, Lа, Lu, Nd, Pr, Sc, Sm, Tb, Tm, Yb. ПО для большинства аналитов (за исключением Cu, Fe, Ga, Pb и Sn) по разработанной методике АЭС-ИСП ниже в среднем на 1 порядок величины, что объясняется более широким диапазоном доступных длин волн и приборными возможностями при детектировании сигнала.
Оценка правильности методики. Для проверки правильности разработанной методики проводили эксперимент “введено–найдено”. В качестве примера в табл. 3 представлены результаты эксперимента “введено–найдено” для некоторых примесей. Результаты “найдено” в пределах доверительного интервала совпадают с результатами “введено” для изученных аналитов, внутрилабораторная прецизионность при этом не превышает 25%, что удовлетворяет критериям количественного определения.
Таблица 3.
Результаты эксперимента “введено–найдено” (P = 0.95 для n = 3–5)
Элемент | ПО, мас. % | Введено, мас. % | Найдено, мас. % | Sr, % |
---|---|---|---|---|
Ba | 3 × 10–7 | (4.0 ± 0.4) × 10–6 | (3.7 ± 0.3) × 10–6 | 9 |
Cd | 1 × 10–6 | (1.0 ± 0.1) × 10–5 | (9.5 ± 1.2) × 10–6 | 13 |
Co | 1 × 10–6 | (1.0 ± 0.1) × 10–5 | (8.2 ± 1.2) × 10–6 | 15 |
Cu | 1 × 10–5 | (1.0 ± 0.1) × 10–5 | (8.8 ± 1.9) × 10–6 | 22 |
Mg | 1 × 10–6 | (1.0 ± 0.1) × 10–5 | (9.5 ± 0.2) × 10–6 | 2 |
Mn | 1 × 10–6 | (1.0 ± 0.1) × 10–5 | (8.7 ± 0.6) × 10–6 | 7 |
Ru | 3 × 10–5 | (8.0 ± 0.8) × 10–5 | (8.0 ± 1.0) × 10–5 | 13 |
Sc | 2 × 10–7 | (1.0 ± 0.1) × 10–5 | (8.8 ± 0.8) × 10–6 | 9 |
Sr | 1 × 10–7 | (4.0 ± 0.4) × 10–6 | (3.7 ± 0.3) × 10–6 | 9 |
V | 1 × 10–6 | (1.0 ± 0.1) × 10–5 | (8.9 ± 1.0) × 10–6 | 11 |
Zr | 3 × 10–7 | (1.0 ± 0.1) × 10–5 | (8.6 ± 0.9) × 10–6 | 11 |
Анализ реальных объектов. Разработанная АЭС-ИСП-методика была применена для оперативного аналитического контроля. В табл. 4 представлены результаты анализа актуального исходного сырья: КПЭФ, оксида теллура после выщелачивания и обезблагораживания (1), катодного губчатого теллура (2), теллура металлического (3). На рис. 1 знаком “*” отмечены этапы, на которых были получены перечисленные объекты: осаждение и фильтрация ТеО2 (1), электролизный процесс получения губчатого теллура (2), восстановительно-рафинирующая плавка (3). В первом столбце представлен усредненный примесный состав КПЭФ, определенный в аналитическом центре ОАО “Красцветмет”.
Таблица 4.
Результаты АЭС-ИСП аналитов в различных объектах
Элемент | Содержание, мас. % | |||
---|---|---|---|---|
КПЭФ | 1 | 2 | 3 | |
Ag | (8.4 ± 0.6) × 10–2 | н/о(3 × 10–6) | н/о(3 × 10–6) | н/о(3 × 10–6) |
Al | Нет данных | 1.40 ± 0.11 | 0.16 ± 0.06 | н/о(8 × 10–6) |
As | 0.15 ± 0.03 | 0.8 ± 0.2 | 0.10 ± 0.05 | н/о(1 × 10–5) |
Au | (5.2 ± 0.5) × 10–4 | н/о(2 × 10–6) | н/о(2 × 10–6) | н/о(2 × 10–6) |
Cu | (3.2 ± 0.3) × 10–2 | (1.7 ± 0.2) × 10–2 | (4.7 ± 1.4) × 10–4 | (5 ± 3) × 10–4 |
Fe | (4.3 ± 0.4) × 10–1 | (1.3 ± 0.2) × 10–2 | н/о(5 × 10–5) | н/о(5 × 10–5) |
Ga | Нет данных | (7.1 ± 0.5) × 10–2 | н/о(2 × 10–5) | н/о(2 × 10–5) |
Ir | (2.0 ± 0.3) × 10–3 | н/о(1 × 10–4) | н/о(1 × 10–4) | н/о(1 × 10–4) |
K | Нет данных | (1.03 ± 0.14) × 10–2 | 1.8 ± 0.6 | (9 ± 6) × 10–3 |
Mo | Нет данных | 1.0 ± 0.2 | (4.0 ± 1.9) × 10–2 | н/о(3 × 10–6) |
Na | Нет данных | 0.157 ± 0.014 | (9 ± 3) × 10–2 | н/о(2 × 10–6) |
P | Нет данных | 0.243 ± 0.014 | (3.4 ± 1.3) × 10–2 | н/о(5 × 10–5) |
Pb | 8–25 | 0.34 ± 0.02 | (4.9 ± 1.9) × 10–2 | (6 ± 2) × 10–3 |
Pd | (4.5 ± 0.7) × 10–3 | н/о(3 × 10–6) | н/о(3 × 10–6) | н/о(3 × 10–6) |
Pt | (2.5 ± 0.4) × 10–3 | н/о(2 × 10–5) | н/о(7 × 10–5) | н/о(2 × 10–5) |
Rh | (1.3 ± 0.3) × 10–3 | н/о(7 × 10–5) | н/о(7 × 10–5) | н/о(7 × 10–5) |
Sb | 0.13 ± 0.03 | (7.5 ± 0.5) 10–2 | (2.1 ± 1.1) × 10–2 | н/о(6 × 10–5) |
Se | 5–11 | 2.02 ± 0.08 | 0.20 ± 0.11 | 0.403 ± 0.014 |
Sn | 8–16 | 2.9 ± 0.9 | 0.74 ± 0.06 | н/о(4 × 10–4) |
V | Нет данных | (4.5 ± 0.6) 10–3 | (1.2 ± 0.4) × 10–4 | н/о(1 × 10–6) |
W | Нет данных | 0.39 ± 0.15 | н/о(4 × 10–5) | н/о(4 × 10–5) |
Zn | (5.2 ± 0.6) × 10–2 | (4.0 ± 0.2) 10–2 | (2.6 ± 0.6) × 10–3 | н/о(3 × 10–6) |
При разработке методики использовали единый набор образцов сравнения на основе слабокислых растворов с добавлением внутреннего стандарта, что позволило достоверно определять примесный состав не только конечного продукта, но и полупродуктов ключевых этапов технологического процесса получения теллура.
Результаты АЭС-ИСП наглядно демонстрируют эффективность каждого этапа процесса. Прослеживается соответствие состава продукта и этапа технологической схемы. После гидрометаллургического этапа в исследуемых продуктах полностью отсутствуют Ag, Au, Ir, Pd, Pt и Rh на уровне концентраций 2 × 10—6–1 × 10–4 мас. %. Губчатый теллур после электролизного процесса содержит существенные количества калия – 1.8 мас. %. Видно, что применение предложенной схемы позволяет эффективно отделить все основные компоненты ГО из КПЭФ – Pb, Se и Sn – с уровнем концентраций от n ×10–1 мас. % и ниже.
ЗАКЛЮЧЕНИЕ
Разработанная методика КХА контроля продуктов и полупродуктов приведенного технологического процесса получения теллура марки T 000 на ООО “СибХимТехнологии” с высокой эффективностью реализует аналитические возможности метода АЭС-ИСП, при этом решает все производственные задачи. Явными достоинствами методики АЭС-ИСП является возможность использования высокой концентрации матричного компонента (до 40 г/л) и внутреннего стандарта, что при анализе конечного продукта обеспечивает достоверное определение как редких, так и распространенных примесей. При аналитическом контроле полупродуктов, характеризующихся значительным содержанием примесных элементов, легко прибегнуть к разбавлению. Оптимизация операционного параметра метода АЭС-ИСП – мощности индукционного разряда – позволяет достичь максимального отношения интенсивности сигналов аналитов к флуктуациям фона и в результате снизить ПО аналитов. Тщательный выбор АЛ для определяемых примесей, оптимальной концентрации основного компонента в растворе обеспечивают минимальные матричные влияния при концентрации теллура в растворе до 40 г/л.
Представленная методика позволяет определять 61 аналит с пределами обнаружения 1 × 10–7–4 × × 10–4 мас. % и внутрилабораторной прецизионностью, не превышающей 25%. Методика позволяет охарактеризовать теллур чистотой 4N8, что удовлетворяет всем требованиям нормативного документа [14].
Список литературы
Makuei F.M., Senanayake G. Extraction of Tellurium from Lead and Copper Bearing Feed Materials and Interim Metallurgical Products – A short review // Miner. Eng. 2018. V. 115. P. 79–87. https://doi.org/10.1016/j.mineng.2017.10.013
Bureau B. et al. Tellurium Based Glasses: a Ruthless Glass to Crystal Competition // Solid State Sci. 2008. V. 10. № 4. P. 427–433. https://doi.org/10.1016/j.solidstatesciences.2007.12.017
Zaiour A. et al. Electrical Properties Study of Three Highly Purified CdTe Ingots // Phys. Procedia. 2014. V. 55. P. 470–475. https://doi.org/10.1016/j.phpro.2014.07.068
Zaiour A., Hamié A., Hage-Ali M. Segregation Study of Some Impurities in Three Purification Process of CdTe Ingots // Phys. Procedia. 2014. V. 55. P. 464–469. https://doi.org/10.1016/j.phpro.2014.07.067
Del Sordo S. et al. Progress in the Development of CdTe and CdZnTe Semiconductor Radiation Detectors for Astrophysical and Medical Applications // Sens. Mol. Diversity Preservation Int. 2009. V. 9. № 5. P. 3491–3526. https://doi.org/10.3390/s90503491
Liu H. et al. Purification of Cd0.9Zn0.1Te by Physical Vapor Transport Method // Mater. Lett. 2005. V. 59. № 29–30. P. 3837–3840. https://doi.org/10.1016/j.matlet.2005.06.059
Wang T. et al. Study on the Behaviors of Impurities in Cadmium Zinc Telluride // J. Cryst. Growth. 2007. V. 304. № 2. P. 313–316. https://doi.org/10.1016/j.jcrysgro.2007.03.013
Horn W., Földvari I., Denz C. Holographic Data Storage in Photorefractive Bismuth Tellurite // J. Phys. D: Appl. Phys. 2008. V. 41. № 22. P. 1–9. https://doi.org/10.1088/0022-3727/41/22/224006
Földvári I. et al. Bismuth Tellurite – a New Material for Holographic Memory // Opt. Commun. 2000. V. 177. № 1. P. 105–109. https://doi.org/10.1016/S0030-4018(00)00560-5
Koudelka L. et al. The Structural Role of Tellurium Dioxide in Lead Borophosphate Glasses // J. Non.-Cryst. Solids. 2014. V. 401. P. 124–128. https://doi.org/10.1016/j.jnoncrysol.2014.01.044
Pujari N. et al. Effect of Li2O Content on Structural and Optical Properties of Li2O–TeO2–As2O3–B2O3 Glasses // J. Phys. Chem. Solids. 2021. V. 148. P. 124–128. https://doi.org/10.1016/j.jpcs.2020.109627
Кудрявцев А.А. Химия и технология селена и теллура. М.: Высш. шк., 1961. 286 c.
Чижиков Д.М., Счастливый В.П. Теллур и теллуриды. М.: Наука, 1966. 286 c.
ГОСТ 17614-2018. Теллур технический. Технические условия (с Поправкой). М.: Изд. стандартов, 2018. 12 с.
ГОСТ 24977.2-81. Теллур высокой чистоты. Спектральный метод определения примесей. М.: Изд. стандартов, 1981. С. 18–27.
Заксас Н.П., Комиссарова Л.Н., Шелпакова И.Р. Атомно-эмиссионный спектральный анализ высокочистого диоксида теллура с возбуждением спектров в двухструйном дуговом плазмотроне // Аналитика и контроль. 2005. Т. 9. № 3. С. 240–244.
Shaverina A.V., Tsygankova A.R., Saprykin A.I. A Procedure of ICP-AES Analysis of Silicon Using Microwave Digestion and Preconcentration // J. Anal. Chem. 2015. V. 7. № 1. P. 28–31. https://doi.org/10.1134/S1061934815010153
Дополнительные материалы отсутствуют.
Инструменты
Неорганические материалы