Журнал неорганической химии, 2020, T. 65, № 10, стр. 1317-1324
Синтез и свойства оксидов марганца, полученных в реакциях горения с глицином и лимонной кислотой
В. Д. Журавлев a, *, **, Ш. М. Халиуллин a, Л. В. Ермакова a, В. Г. Бамбуров a
a Институт химии твердого тела УрО РАН
620990 Екатеринбург, ул. Первомайская, 91, Россия
* E-mail: zhvd@ihim.uran.ru
** E-mail: zhuravlev47@bk.ru
Поступила в редакцию 04.04.2020
После доработки 28.05.2020
Принята к публикации 30.05.2020
Аннотация
Выполнен синтез оксидов марганца в реакциях горения с глицином и лимонной кислотой. Показано, что при синтезе из реакционных растворов, в которых доминирует лимонная кислота Σ(φcit + φgl) = 1.8–2.1 при φgl = 0.5, реакции протекают с умеренной интенсивностью при максимальной температуре не выше 315°C. В полученных нанопорошках (16–33 нм) преобладает тетрагональный Mn3O4. Первичные кристаллиты собраны в ажурные агрегаты типа “мятой бумаги” с многочисленными отверстиями и сквозными порами с удельной площадью поверхности 22–27 м2/г. Проведены расчеты изменения максимальных температур горения от площади реактора, массы получаемого оксида, содержания воды в ксерогеле.
ВВЕДЕНИЕ
Оксиды марганца наряду с оксидами ванадия, церия, хрома, меди и кобальта рассматриваются как перспективные катализаторы общего окисления летучих органических соединений (VOC) и являются более стабильными, чем катализаторы на основе благородных металлов [1–5]. Наиболее эффективный среди них – Mn3O4 [6]. Высокая активность катализаторов на основе оксидов марганца обнаружена при нейтрализации NOx в диапазоне 120–350°C как в присутствии, так и в отсутствие SO2 [7]. Их регенерация после дезактивации серой полностью восстанавливает первоначальную каталитическую активность. Смешанные оксиды CeO2/MnOx используются в процессах селективного каталитического восстановления оксидов азота с применением аммиака [8]. Присутствие Mn3O4 с низкой степенью кристалличности в полученном материале, по-видимому, является ключевым фактором высокой активности подобных катализаторов.
Оксид марганца Mn3O4 рассматривается как эффективный анодный материал для литий-ионных аккумуляторов [9–11] и электродов суперконденсаторов [12–15]. Он исследуется в рамках поиска методов лечения рака [16].
Во всех упомянутых областях применения главными требованиями к оксидам марганца, в частности к Mn3O4, являются высокая удельная площадь поверхности и дисперсность. Поэтому их чаще всего получают гидротермальными методами [9, 10, 12, 14] или в реакциях горения из растворов (Solution Combustion Synthesis (SCS)) [1, 5, 7, 8]. Так, авторы [5] использовали раствор марганца (кобальта) азотнокислого с глиоксиловой (C2H2O3) или кетоглутаровой (C5H6O5) кислотой. Представленные в [5] данные указывают на использование избытка восстановителя при синтезе и благоприятное для комплексообразования соотношение кислота : нитрат марганца. В первом случае оно равно 2 : 1, во втором – примерно 3 : 1. В целях полного удаления углерода из геля (ксерогеля) при синтезе и отжиге процесс проводили с подачей воздуха в зону нагревания при температурах до 350°C. Активность марганецсодержащего катализатора, полученного из кислотных комплексов, была выше по сравнению с катализаторами, полученными простым термолизом нитрата марганца. Их удельная площадь поверхности превышала значение для контрольного образца в 3–6 раз [5]. Удельная площадь поверхности порошка, полученного с глиоксиловой кислотой, достигала 43 м2/г, а с глутаровой – 23 м2/г. Сами материалы представляли смесь оксидов Mn3O4 и Mn2O3.
В работе [7] синтез вели из раствора, содержащего марганец азотнокислый (N) и глицин (G) в соотношении G : N = 1 : 2 и 2 : 1, т.е. в первом случае в реакционной смеси доминировал окислитель, во втором – восстановитель. В соответствии с этим реакции проводили в режиме окислительного или восстановительного горения [17]. Выбранная методика термообработки позволила авторам получить материал, состоящий в основном из Mn2O3, из раствора с минимумом глицина, а Mn3O4 – из растворов, обогащенных глицином. Удельная площадь поверхности материалов составила 31–80 м2/г. В работе [8] при синтезе композитов CeO2/MnOx применяли глицин или лимонную кислоту для получения именно Mn3O4. Как и в предыдущей работе, топливо вводили в количестве, меньшем и большем стехиометрического значения. Согласно [8], образцы, содержащие Mn3O4, имели более высокие каталитические характеристики.
В настоящей работе исследованы условия получения Mn3O4 методом SCS c применением одновременно двух видов топлива – глицина и лимонной кислоты.
ЭКСПЕРИМЕНТАЛЬНАЯ ЧАСТЬ
В качестве исходных реактивов использовали марганец углекислый основной водный (MnCO3 ∙ mMn(OH)2 ∙ nH2O) “ч.”, азотную кислоту “х. ч.”, аминоуксусную кислоту (глицин) “ч. д. а.” и лимонную кислоту 1-водную “ч. д. а.”. Для проведения экспериментов марганец(II) углекислый основной водный растворяли в небольшом избытке азотной кислоты и получали раствор марганца азотнокислого, содержащий 149.7 г/дм3 Mn2+. Эксперименты по синтезу оксидов марганца проводили в алюминиевом цилиндрическом реакторе объемом 1 дм3 и площадью открытой поверхности 0.010 м2. Раствор марганца азотнокислого (65 см3) помещали в реактор, а затем вносили навески глицина и лимонной кислоты в соответствии с табл. 1.
Таблица 1.
Фазовый состав, области когерентного рассеяния (ОКР) и удельная площадь поверхности (S) образцов после SCS
№ опыта | φcitr/Σ(φcitr + φgl) | Фазы, мас. % | ОКР, нм | S, м2/г | ||||
---|---|---|---|---|---|---|---|---|
Mn3O4 | Mn2O3 | Mn5O8 | Mn3O4 | Mn2O3 | Mn5O8 | |||
1 | 0/1 | 89.2 | 4.4 | 6.4 | 33.1 | 36.2 | 46.8 | 23 ± 0.4 |
2 | 0/0.9 | 96.9 | 2.4 | 0.7 | 14.0 | 28.7 | 22.1 | 17 ± 0.9 |
3 | 1.3/1.8 | 92.4 | 4.5 | 3.1 | 16.8 | 29.3 | 24.5 | 34.6 ± 2.0 |
4 | 1.4/1.9 | 94.6 | 3.7 | 1.7 | 19.9 | 16.9 | 33.7 | 31.4 ± 2.9 |
5 | 1.5/2.0 | 94.5 | 3.5 | 2.1 | 22.7 | 34.0 | 17.3 | 32.8 ± 2.7 |
6 | 1.6/2.1 | 96.5 | 2.3 | 1.2 | 24.0 | 35.4 | 30.1 | 28.9 ± 2.2 |
Реактор с реакционным раствором нагревали с помощью электрического нагревателя при температуре его поверхности ~500°С. После окончания реакции горения полученный прекурсор перемешивали и проводили отжиг при температуре 500°С в течение 5 ч.
Для сравнения характера фазового состава и физико-химических характеристик получаемых оксидов марганца с одним и двумя видами топлива были проведены два эксперимента (опыты 1 и 2) по синтезу оксида марганца(III) с глицином при φ = 1.0 и 0.9, а также синтезированы четыре образца в условиях восстановительного горения, т.е. с Σφ > 1. Доля глицина была постоянной и соответствовала φ = 0.5, а доля лимонной кислоты возрастала от φ = 1.3 до 1.6 (опыты 3–6). Все эксперименты были рассчитаны на получение 5 г оксида марганца(III) в соответствии с реакциями (1, 2):
(1)
$\begin{gathered} {\text{3Mn}}{{\left( {{\text{N}}{{{\text{O}}}_{{\text{3}}}}} \right)}_{2}} + 3.333{{{\text{H}}}_{{\text{2}}}}{\text{N}}\left( {{\text{C}}{{{\text{H}}}_{{\text{2}}}}} \right){\text{COOH}} \to \\ \to 3{\text{MnO}} + 4.67{{{\text{N}}}_{2}} + 6.67{\text{C}}{{{\text{O}}}_{2}} + 8.33{{{\text{H}}}_{{\text{2}}}}{\text{O}}. \\ \end{gathered} $При расчетах сделано допущение, что после или в ходе реакции горения происходит параллельная реакция (2):
РФА образцов после сжигания и отжига выполняли с помощью дифрактометра Shimadzu XRD-7000 (CuKα-излучение, 2θ = 10°–80°). Обработку данных и анализ фазового состава образцов проводили с применением программного обеспечения POWDER CELL 2.4 и использованием картотеки PDF4 (ICDD, USA, Release 2009). Кристаллохимические сведения для интерпретации фазовых составляющих, в частности координаты атомов, были найдены в базе данных Springer Materials. Размеры ОКР вычисляли по методу Вильямсона-Холла в программе POWDER CELL 2.4.
Исследование структурно-морфологических характеристик проводили на сканирующем электронном микроскопе JEOL JSM 6390 LA. Удельную площадь поверхности порошков оксида марганца определяли методом БЭТ (Tri Star 3000V6.03A) по тепловой десорбции азота.
Температуры горения фиксировали видеографическим регистратором Ш932.9А 29.015/1 с периодом измерений 0.3 с, датчиками температуры служили термопары ТПП. Термодинамический анализ процессов синтеза оксидов марганца выполняли с помощью разработанной программы расчета температур горения (SCSTempCal) для моделирования и вычисления максимальных температур, развиваемых в реакциях SCS [18].
РЕЗУЛЬТАТЫ И ОБСУЖДЕНИЕ
Синтез оксидов в реакциях горения из растворов – достаточно распространенный метод [17, 19–21]. От соотношения нитратных групп к органической составляющей и типа катиона, участвующего в синтезе, протекание реакции существенно изменяется. Одной из возможных пограничных ситуаций может быть высокая скорость реакции, которая сопровождается захватом получаемого продукта потоком отходящих газов [19]. Например, взаимодействие азотнокислых солей d-элементов с глицином протекает весьма активно в широком диапазоне соотношений восстановитель/окислитель (0.6 < φ < 1.8) [20].
Эксперимент показал, что реакция с глицином при φ = 0.9–1.0 протекает очень бурно: из реактора идет вынос плотного коричневого дыма, в котором присутствуют “тонкие” частицы оксидов марганца. Через 10–12 с вынос заканчивается, в реакторе остается немного порошка. Материал представляет собой “тонкий” пушистый порошок коричневого цвета, в котором доминирует (89–97%) Mn3O4 (табл. 1). Вследствие удаления основной массы прекурсора из реактора максимальная температура в опыте 1 была занижена до 315°С (рис. 1). Поэтому важной задачей при использовании метода SCS становятся приемы снижения скорости реакции до оптимальных значений. В ряде случаев она может быть решена путем использования двух видов топлива, одно из которых является ингибитором реакции. В этом качестве успешно применяются карбоновые кислоты, в частности лимонная кислота [21]. На рис. 1 (вставка) представлен температурный профиль взаимодействия в системе H3C6H5O7 ∙ H2O/Mn(NO3)2 · nH2O при φ = 1. Видно, что температура реакционной массы лимонной кислоты и марганца азотнокислого монотонно возрастает. В соответствии с принципом минимизации свободной энергии Гиббса процесс окисления лимонной кислоты нитратом марганца сопровождается выделением продуктов разложения: CO2, N2, H2O [20] и начинается при ∼132°С.
Рис. 1.
Температурный профиль процесса горения в системе H2N(CH2)COOH/Mn(NO3)2 · nH2O при φgl = 1. Вставка – профиль горения в системе H3C6H5O7 ∙ H2O/Mn(NO3)2 · nH2O при φcit = 1.
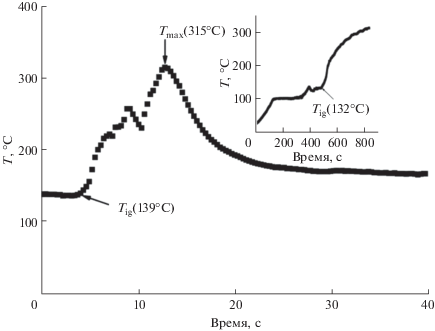
Объем формирующегося прекурсора растет, но скорость возрастания температуры невысокая, хотя и приводит к появлению каления прекурсора. Процесс, в отличие от SCS, существенно затянут во времени – 6–7 мин от начала реакции до окончания процесса (снижения температуры прекурсора). Однако по окончании реакции получена смесь оксидов марганца, содержащая преимущественно Mn3O4 в виде пушистого тонкодисперсного коричневого порошка.
Использование лимонной кислоты совместно с глицином при синтезе оксида марганца(III) позволяет существенно снизить интенсивность реакции SCS и переводит процесс в более спокойный режим. Например, реакция горения нитрата марганца из реакционного раствора протекает с умеренной интенсивностью (рис. 2) при максимальной температуре 185°С, если количество лимонной кислоты эквивалентно количеству глицина, т.е. φcitr = φgl = 0.5 или φcitr + φgl = 1. Синтез протекает в несколько этапов: нагревание реакционного раствора, испарение воды с образованием геля, нагревание геля (ксерогеля), начало разложения ксерогеля с выделением гипергольных газов, возгорание, горение, догорание и охлаждение. При охлаждении в реактор попадает воздух из атмосферы, в результате чего кислород воздуха вступает в реакцию окисления с не полностью сгоревшими органическими фрагментами. Этот процесс происходит в виде каления образовавшегося в реакторе продукта.
Рис. 2.
Температурный профиль процесса горения в системе (H2N(CH2)COOH + H3C6H5O7 ∙ ∙ H2O)/Mn(NO3)2 · nH2O при φgl = 0.5 и φcit = 0.5. 1 – нагрев раствора, 2 – испарение воды, 3 – нагрев геля (ксерогеля), 4 – начало разложения ксерогеля, 5 – горение, 6 – догорание и охлаждение, 7 – каление.
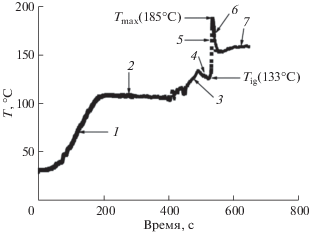
Наличие в реакционном растворе глицина обеспечивает достаточно короткое время реакции горения и формирования смеси оксидов марганца, которые завершаются за 5 с без выбросов материала из реактора.
В опытах 3–6 синтез за счет доминирования в реакционной смеси лимонной кислоты протекает при резком снижении интенсивности реакции. Согласно данным РФА (табл. 1, рис. 3а), преобладающей фазой в продукте является Mn3O4 (ICDD, card 24-734), после отжига при 500°C его содержание несколько снижается (табл. 2, рис. 3б), а доля фаз Mn2O3 (ICDD, card 41-1442) и Mn5O8 (ICDD, card 39-1218) возрастает примерно в 2–3 раза.
Таблица 2.
Фазовый состав, области когерентного рассеяния (ОКР) и удельная площадь поверхности (S) образцов после отжига при 500°C
№ опыта | φcitr/Σ(φcitr + φgl) | Фазы, мас. % | ОКР, нм | S, м2/г | ||||
---|---|---|---|---|---|---|---|---|
Mn3O4 | Mn2O3 | Mn5O8 | Mn3O4 | Mn2O3 | Mn5O8 | |||
3 | 1.3/1.8 | 77.6 | 7.4 | 15 | 23.5 | 34.4 | 16.8 | 27.4 ± 0.4 |
4 | 1.4/1.9 | 87.5 | 5.6 | 6.9 | 19.6 | 21.0 | 36.0 | 27.7 ± 1.0 |
5 | 1.5/2.0 | 79.8 | 5.9 | 14.3 | 21.00 | 30.8 | 17.3 | 23.4 ± 0.3 |
6 | 1.6/2.1 | 80.1 | 8.8 | 11.1 | 16.6 | 34.2 | 16.6 | 22.1 ± 0.3 |
Средние значения ОКР для образцов после синтеза приведены в табл. 1. Морфология материалов на примере опыта 4 (рис. 4а) представлена в виде первичных кристаллитов размером 14–33 нм, собранных в ажурные агломераты со сквозными порами и отверстиями. В процессе термической обработки начинается разрушение агломератов (рис. 4б), что приводит к уменьшению размеров ОКР основной фазы (табл. 2), возможно, связанному с начальными процессами фрагментации кристаллитов фаз, образованием в них новых внутренних границ в результате роста термических напряжений. Надо отметить, что введение в реакционный раствор лимонной кислоты повышает удельную площадь поверхности порошков по сравнению с материалом, полученным с глицином. Удельная площадь поверхности порошков после синтеза и смешения в опытах 3–6 составила ∼32 м2/г, тогда как в опыте 1 она равна ~23 м2/г. Термообработка материалов при 500°С способствует снижению удельной площади поверхности до 22–27.4 м2/г, но также проявляется тенденция к линейному уменьшению удельной площади поверхности с ростом содержания лимонной кислоты.
Процессы SCS весьма чувствительны не только к типу и соотношению топлива, но и к типу реактора и массе получаемого продукта [21]. С увеличением площади открытой поверхности (для цилиндрического реактора это эквивалентно площади нагрева) температура и интенсивность горения (максимальная температура) снижаются. А увеличение количества получаемого оксида при постоянном объеме реактора сопровождается увеличением максимальной температуры горения, переходом от тления к открытому пламени и т.п.
В связи с бурным и непредсказуемым характером реакций SCS достаточно сложно и нецелесообразно вести многочисленные эксперименты, меняя факторы влияния, чтобы оптимизировать процесс получения той или иной кристаллической формы оксида в доминирующем количестве или увеличить производительность процесса синтеза для его масштабирования вплоть до организации производства. Поэтому для моделирования протекания процессов с различными исходными факторами была создана программа расчета [18], которая позволяет рассчитывать максимальные температуры, развиваемые в процессах горения при получении нано- и ультрадисперсных оксидов в реакциях SCS, в четырех приближениях: 1) адиабатическом при стандартных значениях теплоемкости и энтальпии; 2) адиабатическом с учетом температурной зависимости теплоемкости и энтальпии; 3) с учетом температурной зависимости энтальпии и теплоемкости и работы по расширению исходящих газов; 4) с учетом температурной зависимости теплоемкости и энтальпии, работы по расширению газов и потерь теплоты на излучение.
Ниже мы приведем примеры термодинамического анализа условий получения оксидов марганца, рассчитанных по уравнению, являющемуся базовым для программы расчета температур SCSTempCal:
(3)
$\begin{gathered} \frac{m}{M}\Delta {{H}_{{{\text{reag}}}}}({{T}_{{{\text{ig}}}}}) - \frac{m}{M}\Delta {{H}_{{{\text{prod}}}}}({{T}_{{\max }}}) - \frac{m}{M}\mu R\Delta {{T}_{{\max }}} - \\ - \,\,\frac{m}{M}n\lambda - \sigma T_{{\max }}^{4}S{{t}_{{{\text{com}}}}} = \frac{m}{M}{{{\bar {C}}}_{p}}(T)\Delta {{T}_{{\max }}}, \\ \end{gathered} $Выполнены расчеты по программе SCSTempCal на получение 5 г Mn3O4 с глицином в реакторе с площадью открытой поверхности 0.010 м2 при φ = 0.9–1.4 и n = 0 с использованием экспериментальных данных по температуре возгорания 139°C. Использовано измеренное время горения (от момента возгорания до достижения Tmax), равное ~9 с. Ожидаемые значения Tmax составляют 938–1108°C.
Однако в процессе моделирования необходимо учитывать возможность неполного связывания нитрата марганца в хелатный комплекс и возможность его сохранения в ксерогеле к моменту возгорания в виде кристаллогидратов Mn(NO3)2 · · nH2O. Хотя кристаллогидрат Mn(NO3)2 · 6H2O при нагреве до 110°C обезвоживается до дигидрата (n = 2), расчеты Tmax при моделировании проводили для n = 0, 1, 2, 3, 4 и 6. На рис. 5а показано, какое влияние это оказывает на Tmax при φ = 1.0. Пунктиром обозначена часть графика при n > 2. Масса синтезируемого оксида составляет 10 г. Время горения равно 12 с. Видно, что чем суше ксерогель, тем выше Tmax реакции. Чем меньше воды остается в ксерогеле к моменту возгорания, тем больше различия в максимальной температуре горения от площади открытой поверхности реактора. Гипотетически, если температура возгорания будет ниже 110°C, то при максимальном содержании воды, 6 молей, максимальные температуры горения почти не зависят от S.
Рис. 5.
Изменение Tmax в зависимости от содержания воды в ксерогеле (n) при массе синтезируемого Mn3O4 10 г и площади открытой поверхности реактора: 1 – 0.01, 2 – 0.02, 3 – 0.04 м2 (а). Изменение Tmax от изменения площади излучающей поверхности: n = 0 (1), n = 1 (2), n = 2 (3) (б).
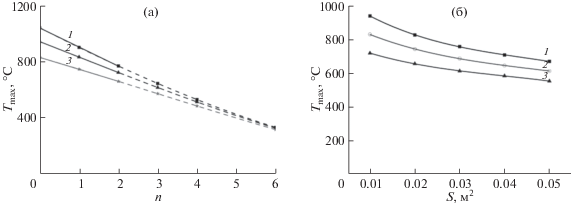
Для планирования эксперимента и масштабирования процесса всегда нужно иметь оценочные данные по влиянию площади излучающей поверхности реактора и массы получаемого оксида на максимальную температуру реакции. На рис. 5б представлена зависимость изменения Tmax при синтезе 5 г Mn3O4 с глицином при φ = 1 и n = 0, 1, 2 от площади открытой поверхности реактора. Сделано допущение, что время горения не зависит от количества получаемого оксида и равно 12 с.
Согласно уравнению (3), увеличение площади открытой поверхности реактора при постоянной массе получаемого материала способствует понижению температуры реакции синтеза.
Видно, что это один из возможных путей снижения температуры горения, который позволяет увеличить загрузку реактора. Так, увеличение площади поверхности реактора в 5 раз приводит к уменьшению максимальной температуры горения на ~23–29%. Зависимость максимальной температуры горения от массы синтезируемого продукта выражена немного слабее (рис. 6). Увеличение массы синтезируемого оксида в 5 раз в том же самом реакторе приводит к увеличению максимальной температуры горения на 16–21%. Комбинируя оба этих фактора, можно в определенной степени регулировать как максимальные температуры горения, так и производительность метода SCS.
ЗАКЛЮЧЕНИЕ
Исследование формирования оксидов марганца в реакциях горения с глицином и лимонной кислотой показало, что процесс протекает с умеренной скоростью и формированием нанодисперсного порошка, в котором преобладает оксид Mn3O4 в форме гаусманита, кроме него присутствуют примеси Mn2O3 и Mn5O8. После отжига при 500°C содержание Mn3O4 несколько снижается, а общая доля фаз Mn2O3 и Mn5O8 возрастает до 19.9–24.4 мас. %.
Введение в реакционный раствор лимонной кислоты повышает удельную площадь поверхности порошков по сравнению с материалом, полученным с глицином, от ~23 до 32 м2/г. Термообработка материалов при 500°C способствует снижению удельной площади поверхности до 22–27.4 м2/г, но также проявляется тенденция к линейному уменьшению удельной площади поверхности с ростом содержания лимонной кислоты. Морфология материала представлена в виде первичных кристаллитов размером 14–33 нм, собранных в ажурные агломераты со сквозными порами и отверстиями.
Образование в реакции горения тетрагонального Mn3O4 обусловлено проведением синтеза в условиях восстановительного горения и присутствием в зоне реакции CO, пергидрольных газов и т.п., а также частиц углерода и фрагментов лимонной кислоты при отжиге прекурсора.
Рассмотрены некоторые аспекты моделирования реакций горения с помощью программы SCSTempCal.
Список литературы
Piumetti M., Fino D., Russo N. // Appl. Catal., B: Environ. 2015. V. 163. P. 277. https://doi.org/10.1016/j.apcatb.2014.08.012
Baldi M., Finocchio E., Milella F. et al. // Appl. Catal., B: Environ. 1998. V. 16 P. 43. https://doi.org/10.1016/S0926-3373(97)00061-1
Baldi M., Escribano V.S., Amores et al. // Appl. Catal., B: Environ. 1998. V. 17. P. 175.
Lahousse C., Bernier A., Grange P. et al. // J. Catal. 1998. V. 178. P. 214. https://doi.org/10.1006/jcat.1998.2148
Puértolas B., Smith A., Vázquez I. et al. // Chem. Eng. J. 2013. V. 229. P. 547.https://doi.org/10.1016/j.cej.2013.06.041
Kim S.C., Shim W.G. // Appl. Catal., B. 2010. V. 98. P. 180. https://doi.org/10.1016/j.apcatb.2010.05.027
Andreoli S., Deorsola F.A., Galletti C. et al. // Chem. Eng. J. 2015. V. 278. P. 174. https://doi.org/10.1016/j.cej.2014.11.023
Andreoli S., Deorsola F.A., Pirone R. // Catal. Today. 2015. V. 253. P. 199. https://doi.org/10.1016/j.cattod.2015.03.036
Xiaoyan Han, Yiping Cui, Haowen Liu // J. Alloys Compd. 2020. V. 814. P. 152348. https://doi.org/10.1016/j.jallcom.2019.152348
Varghese S.P., Babu B., Prasannachandran R. et al. // J. Alloys Compd. 2019. V. 780. P. 588. https://doi.org/10.1016/j.jallcom.2018.11.394
Ding P., Li W., Zheng X. et al. // Key Eng. Mater. 2019. V. 15. P. 3. https://doi.org/10.4028/www.scientific.net/KEM.815.3
Dadamiah P.M.D. Shaik, Rosaiah Pitcheri, Yejun Qiuc, Hussain O.M. // Ceram. Int. 2019. V. 45. P. 2226. https://doi.org/10.1016/j.ceramint.2018.10.135
Ranjithkumar R., Ezhil Arasi S., Nallamuthu N. et al. // Superlattices Microstruct. 2020. V. 138. P. 106380. https://doi.org/10.1016/j.spmi.2019.106380
Bin Li, Xihua Zhang, Jinhe Dou, Cheng Hu // Ceram. Int. 2019. V. 45. P. 16297. https://doi.org/10.1016/j.ceramint.2019.05.155
Jifeng Shi, Mingxuan Sun, Heming Hu // Mater. Res. Express. 2018. V. 6. P. 035511. https://doi.org/10.1088/2053-1591/aaf58a
Gotić M., Ivanković S., Musi S. et al. // Collect. Czech. Chem. Commun. 2009. V. 74. P. 135. https://doi.org/10.1135/cccc2009047
Varma A., Mukasyan A.S., Rogachev A.S. et al. // Chem. Rev. 2016. V. 116. P. 14493. https://doi.org/10.1021/acs.chemrev.6b00279
Khaliullin Sh.M., Popov I.S., Zhuravlev V.D. // Int. J. Self-Propag. High-Temp. Synth. 2020. V. 29. P. 87. https://doi.org/10.3103/S1061386220020077
Khaliullin Sh.M., Zhuravlev V.D., Bamburov V.G. et al. // J. Sol-Gel Sci. Technol. 2020. V. 93. P. 251. https://doi.org/10.1007/s10971-019-05189-8
Khaliullin Sh.M., Zhuravlev V.D., Ermakova L.V. et al. // Int. J. Self-Propag. High-Temp. Synth. 2019. V. 28. № 4. P. 226. https://doi.org/10.3103/S1061386219040058
Khaliullin Sh.M., Zhuravlev V.D., Bamburov V.G. // Int. J. Self-Propag. High-Temp. Synth. 2017. V. 26. P. 93. https://doi.org/10.3103/S1061386217020078
Дополнительные материалы отсутствуют.
Инструменты
Журнал неорганической химии