Журнал неорганической химии, 2021, T. 66, № 5, стр. 648-657
Зависимость реакционной способности высокодисперсной системы Ta2O5–HfO2–C от температуры карбонизации ксерогеля
Е. П. Симоненко a, *, Н. П. Симоненко a, И. А. Нагорнов a, b, А. С. Мокрушин a, М. В. Мальцева a, b, В. Г. Севастьянов a, Н. Т. Кузнецов a
a Институт общей и неорганической химии им. Н.С. Курнакова РАН
119991 Москва, Ленинский пр-т, 31, Россия
b Российский химико-технологический университет им. Д.И. Менделеева
125047 Москва, Миусская пл., 9, Россия
* E-mail: ep_simonenko@mail.ru
Поступила в редакцию 14.12.2020
После доработки 22.12.2020
Принята к публикации 23.12.2020
Аннотация
Для создания энергоэффективного метода изготовления керамических материалов на основе системы TaC–HfC с применением реакционного горячего прессования или искрового плазменного спекания изучено влияние температуры карбонизации ксерогелей на химическую активность образующихся составов Ta2O5–HfO2–C. Разработан новый метод формирования тантал-гафний-полимерсодержащего геля путем создания взаимопроникающих органо-неорганических сеток при одновременной инициации гидролиза металлсодержащих прекурсоров и полимеризации фурфурилового спирта (кислотный катализ муравьиной кислотой). На основе полученного после сушки ксерогеля путем карбонизации в условиях динамического вакуума при различных температурах (400, 700 и 1000°С) получены образцы системы Ta2O5–HfO2–C с различной реакционной способностью в процессе карботермического синтеза сложных карбидов. Изучен их элементный и фазовой состав, микроструктура и термическое поведение в токе воздуха. Отмечена максимальная реакционная способность порошка, синтезированного при минимальной температуре 400°С, однако для него характерно также и присутствие достаточно высокого количества непиролизованных органических фрагментов (3–4 мас. %), что должно быть учтено при планировании высокотемпературной консолидации карбидной керамики.
ВВЕДЕНИЕ
Начиная с ~30–60-х годов XX в. [1–8] сверхтугоплавкие карбиды элементов IVБ и VБ групп привлекают пристальное внимание исследователей благодаря своим уникальным свойствам. Это связано не только с температурой плавления, находящейся в интервале 2800–4000°С, но и с высокой твердостью и прочностью, низким давлением пара при очень высоких температурах [5, 9], интересными магнитными свойствами, а также с относительно высокой электро- и теплопроводностью. Кроме того, известно, что кубические монокарбиды указанных элементов за счет своей изоструктурности образуют непрерывный ряд твердых растворов [10–14], что позволяет осуществлять тонкую подстройку необходимых характеристик.
Наибольший интерес приковывает к себе система TaC–HfC, поскольку в ней установлен состав 4TaC–1HfC (Ta4HfC5), обладающий максимальной температурой плавления (~4000°С) из полученных на настоящий момент [4, 6]. В последние годы с появлением новых конструкторских решений в авиакосмической отрасли резко выросла востребованность подобных сверхтугоплавких соединений, в связи с этим появились новые исследования, направленные на прецизионное определение точки плавления данного состава. Так, в [15] методом лазерного нагрева установлено, что температура плавления указанного состава несколько ниже таковой для индивидуального карбида гафния. Этот вывод опровергается в исследовании [16], где при быстром нагреве микросекундным импульсом электрического тока подтверждается температура плавления состава Ta4HfC5 на уровне 4300 ± 80 K, которая заметно превышает температуры плавления HfC и TaC.
Возобновившиеся исследования фундаментальных свойств сверхтугоплавких карбидов связаны с перспективой их применения для изготовления карбидных ультравысокотемпературных керамических материалов [17–20], а также использования для допирования керамических материалов на основе систем MB2–SiC (M = Zr, Hf) [21–27]. Так, ранее нами показано, что введение 10 об. % высокодисперсного сложного карбида Ta4HfC5 позволяет повысить стойкость к окислению керамики HfB2–30 об. % SiC при долговременном воздействии сверхзвукового потока диссоциированного воздуха [23].
Реакционное горячее прессование или искровое плазменное спекание (ИПС) бескислородной керамики имеет значительные преимущества перед консолидацией смесей порошков тугоплавких фаз [28–31], в частности, позволяет применять относительно невысокие температуры спекания и приводит к формированию керамики с минимальным размером зерна, что положительно сказывается на ее механических и термических свойствах. Кроме того, образующиеся фазы карбидов зачастую являются нанокристаллическими [24]. Для эффективного использования данного метода необходимо применение исходных систем с наибольшей реакционной способностью и максимально равномерным взаимным распределением оксидных и углеродных компонентов.
Наши предыдущие работы [29, 32–35] основывались на контролируемом гидролизе металлсодержащих прекурсоров (алкоксидов и алкоксоацетилацетонатов металлов) в растворе фенолформальдегидной смолы, которая в результате пиролиза в ходе карбонизации ксерогеля в среде инертного газа или в динамическом вакууме являлась источником аморфного углерода, необходимого для относительно низкотемпературного синтеза тугоплавких карбидов. Данная методика имеет некоторые преимущества, но в зависимости от типа прекурсора в некоторых случаях возможно высаливание компонентами друг друга, что приводит к расслоению системы и менее равномерному распределению составляющих в образующемся после карбонизации составе MOx–C.
В последние годы разрабатываются подходы по получению высокодисперсных тугоплавких карбидов (преимущественно в виде аэрогелей) в результате формирования так называемых взаимопроникающих органо-неорганических сеток (interpenetrating organic–inorganic network) [36–43]. Для образования связнодисперсной системы, которая дает возможность наследования от растворной стадии практически гомогенного распределения оксидных компонентов и полимера, одновременно запускаются процессы гидролиза прекурсоров c последующей поликонденсацией (первая трехмерная сетка) и полимеризации мономера, в результате чего формируется вторая трехмерная сетка. В основном подобные исследования касаются синтеза нанокристаллического карбида кремния с высокой удельной площадью поверхности путем гидролиза тетраэтоксисилана и полимеризации резорцина с формальдегидом [40–43] либо фурфурилового спирта [44–46]. Известны работы по синтезу нанопорошков или пористой керамики на основе карбидов титана [47–50] и циркония [51, 52]. Oднако исследований, направленных на изучение возможности синтеза карбидов элементов VБ группы или смешанных карбидов описанным методом, нами в литературе не найдено.
Целью настоящей работы является выявление закономерностей между реакционной способностью высокодисперсной системы Ta2O5–HfO2–C в процессе карботермического синтеза карбида тантала-гафния состава 9TaC–1HfC и температурой карбонизации тантал-гафний-полимерсодержащего ксерогеля, полученного в результате одновременной полимеризации продуктов гидролиза металлсодержащих прекурсоров и фурфурилового спирта.
ЭКСПЕРИМЕНТАЛЬНАЯ ЧАСТЬ
Для синтеза алкоксоацетилацетоната гафния осуществляли термическую обработку раствора ацетилацетоната гафния (>99%) в изоамиловом спирте (>98%, ЭКОС-1) при температуре масляной бани 150–160°С в течение 6 ч [33, 53]. Раствор пентабутоксида тантала получали путем взаимодействия пентахлорида тантала (99.995%, Lanhit) с н-бутанолом (>98%, Химмед) при барботировании осушенным аммиаком с последующим отделением осадка на центрифуге (3500 об/мин, 30 мин).
С целью получения тантал-гафний-полимерсодержащего геля в раствор пентабутоксида тантала Ta(OBu)5 добавляли аликвоту раствора алкоксоацетилацетоната гафния, чтобы соотношение n(Ta) : n(Hf) составляло 9 : 1. Далее при перемешивании в раствор вводили фурфуриловый спирт C5H6O2 (98%, Acros Organics) в количестве, удовлетворяющем отношению n(C5H6O2) : n(Ta + + Hf) = 1.5, муравьиную кислоту CH2O2 (>98%, Спектр-Хим) как катализатор полимеризации фурфурилового спирта (n(CH2O2) : n(Ta + Hf) = 4.5) и гидролизующую смесь, представляющую собой раствор дистиллированной воды в этаноле (10 об. %). Количество воды в растворе соответствовало отношению n(H2O) : n(Ta + Hf) = 10. После смешения всех компонентов получали прозрачный раствор (рис. 1а), однако при помещении его на водяную баню с температурой 90–95°С через ~2 мин после начала нагрева образовался плотный гель. При этом, как видно из рис. 1а, одновременно происходило и потемнение системы, что свидетельствует о протекающей полимеризации фурфурилового спирта. Через 20–25 мин после начала нагрева образовывался плотный темно-коричневый гель, который далее сушили при температуре 110–120°С до прекращения изменения массы.
Рис. 1.
Внешний вид тантал-гафний-полимерсодержащей системы в различные моменты получения геля (а) и кривые ДСК (красная) и ТГА (зеленая), полученные в результате термического анализа соответствующего ксерогеля в токе аргона (б).
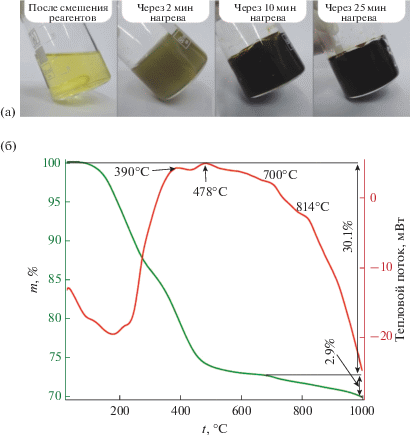
Изучение термического поведения полученных высокодисперсных порошков системы Ta2O5–HfO2–C выполняли на совмещенном ТГА/ДСК/ДТА-анализаторе SDT Q-600 в интервале температур 20–1400°С (скорость нагрева 20 град/мин) в токе как аргона, так и воздуха (скорость потока 250 мл/мин).
Рентгенограммы полученных порошков исходной системы Ta2O5–HfO2–C и продуктов их восстановления записывали на рентгеновском дифрактометре Bruker D8 Advance (излучение CuKα, разрешение 0.02° при накоплении сигнала в точке в течение 0.3 с). Рентгенофазовый анализ (РФА) выполняли с применением программы MATCH! – Phase Identification from Powder Diffraction, Version 3.8.0.137 (Crystal Impact, Germany), в которую интегрирована база данных Crystallography Open Database (COD).
Растровую электронную микроскопию (РЭМ) промежуточных нанокомпозитов и продуктов выполняли на трехлучевой рабочей станции NVision 40, Carl Zeiss; элементный состав оценивали в областях размером 2 × 3 мм с помощью приставки для энергодисперсионного анализа EDX Oxford Instrumets.
РЕЗУЛЬТАТЫ И ОБСУЖДЕНИЕ
Выполненный термический анализ полученного ксерогеля в токе аргона (рис. 1б) позволил сделать вывод о том, что процесс пиролиза его органических фрагментов протекает в несколько стадий. Так, ориентировочно до температуры 250–270°С падение массы происходит за счет испарения летучих компонентов, с чем связан интенсивный эндотермический эффект с минимумом при ~175°С и плечами при 90 и 250°С. Дальнейшее повышение температуры приводит к началу процесса термической деструкции органических фрагментов, которому соответствуют уширенные малоинтенсивные экзотермические эффекты с максимумами при температурах 390, 478, 700 и 814°С.
Наибольшая потеря массы образца происходит, как видно из рис. 1б, при температуре <400–500°С и составляет 21–26%. Суммарная потеря массы в результате карбонизации ксерогеля в токе аргона при нагреве до 700°С составляет 30%, а дальнейший нагрев до 1000°С приводит к увеличению Δm до 33%. Изменение наклона кривой ТГА при температуре ~700°C может быть вызвано как превалирующей ролью процесса дегидрирования ароматических фрагментов, так и началом карботермического синтеза сложных карбидов тантала-гафния.
Опираясь на полученные данные ДСК/ТГА, для оценки реакционной способности составов Ta2O5–HfO2–C выбраны температуры карбонизации 400, 700 и 1000°С. Процесс пиролиза органических фрагментов ксерогелей осуществляли в графитовых лодочках в условиях динамического вакуума (остаточное давление 30–100 Па). Скорость нагрева составляла 400 град/ч в интервале температур 20–700°С и 200 град/ч при температурах 700–1000°С; время выдержки при заданной температуре составляло 2 ч.
Данные РЭМ показали (рис. 2), что микроструктура полученных составов Ta2O5–HfO2–C независимо от температуры карбонизации ксерогеля несколько отличается от таковой, наблюдаемой для данных систем, полученных с применением фенолформальдегидной смолы [33, 35, 54]. Порошки являются, очевидно, менее пористыми, причем ориентировочный размер частиц при повышении температуры термообработки от 400 до 1000°С уменьшается с 50–60 до 20–30 нм соответственно. Такая плотная морфология может быть связана с тем, что на этапе гелеобразования формировались одновременно две полимерные сетки, которые при усадке более жестко фиксировали образующиеся аморфные частицы, вероятно, формируя мезопористые композиты. Элементный EDX-анализ как с площади 2 × 3 мм, так и с площади 2 × 3 мкм показал, что соотношение n(Ta) : n(Hf) составляет 89 : 11 с погрешностью ±1.2 для всех образцов, что соответствует целевому составу. Для температуры карбонизации 400°С в образце присутствует примесь хлора, вероятно, из исходного TaCl5, которая исчезает при более высоких температурах пиролиза.
Рис. 2.
Микроструктура составов Ta2O5–HfO2–C, полученных в результате карбонизации ксерогелей при температурах 400 (а, б) и 1000°С (в, г).
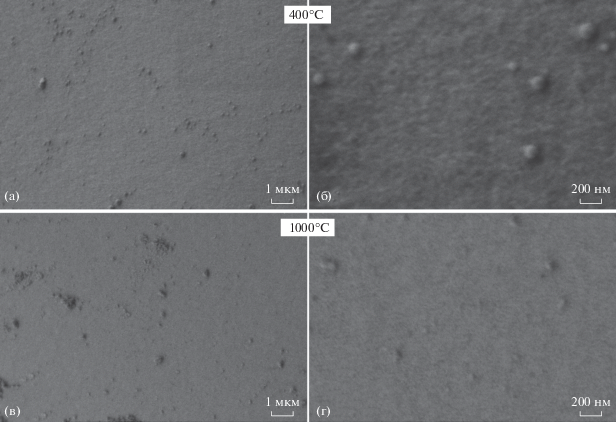
Рентгенограммы образцов приведены на рис. 3. На первой рентгенограмме видно, что динамический нагрев ксерогеля до температуры 1000°С со скоростью 20 град/мин в токе аргона приводит к кристаллизации лишь орторомбического Ta2O5 [55]. Более продолжительный процесс карбонизации ксерогеля (с выдержкой в течение 2 ч) при температуре 400°С приводит к формированию рентгеноаморфного вещества (рентгенограмма 2), в котором присутствуют признаки локального структурирования, выражающиеся в диффузных гало. Повышение температуры пиролиза до 700°С приводит к тому, что на фоне гало начинают появляться наиболее интенсивные рефлексы фазы оксида тантала также в орторомбической модификации (рентгенограмма 3). Для образца, подвергнутого наиболее высокотемпературному нагреву – карбонизации при температуре 1000°С (рентгенограмма 4), помимо фазы o-Ta2O5 [55] наблюдается образование и достаточно большого количества карбидной фазы на основе TaC. Очевидно, термическая обработка в условиях динамического вакуума при температуре 1000°С приводит к началу осуществления карботермического синтеза (Ta,Hf)C, что в случае карбида тантала термодинамически не запрещено [33].
Рис. 3.
Рентгенограммы образцов, полученных при термическом анализе ксерогеля в токе аргона (1), а также в результате карбонизации при температурах 400 (2), 700 (3) и 1000°С (4).
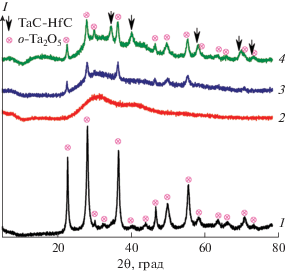
Изучение термического поведения в токе воздуха систем Ta2O5–HfO2–C, полученных при различных температурах, проводили с использованием совмещенного ДСК/ТГА (рис. 4). Установлено, что для образцов, синтезированных при температурах 400 и 700°С, наблюдается исключительно потеря массы за счет выгорания углерода и, возможно, недопиролизованных органических фрагментов, прежде всего ароматических. Этому процессу соответствует широкий и интенсивный экзотермический эффект с максимумом при 560–580°С. Причем для образца, полученного при температуре 400°С, значимая потеря массы начинается при существенно меньших температурах (430–440°C), а суммарная величина Δm является наибольшей (–21.2%). Сравнение с потерей массы (–17.8%) для образца, полученного при 700°С, позволяет предположить, что в составе наиболее низкотемпературного образца присутствуют органические фрагменты, превратившиеся в аморфный углерод не в полной мере. Помимо этого, на кривой ДСК для образцов, полученных при 400 и 700°С, присутствует экзотермический эффект, не связанный с изменением массы, вероятно, соответствующий кристаллизации Ta2O5.
Рис. 4.
Кривые ДСК (а) и ТГА (б) в токе воздуха образцов, полученных в результате карбонизации тантал-гафний-полимерсодержащих ксерогелей при температурах 400, 700 и 1000°С.
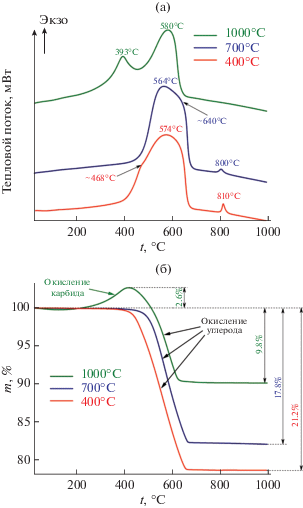
Термическое же поведение образца, полученного при температуре карбонизации 1000°С, значительно отличается: при относительно невысоких температурах (>220–250°C) происходит прирост массы на 2.6%, который сопровождается экзоэффектом с максимумом при 393°С, вероятно, обусловленный окислением образовавшейся в ходе карбонизации карбидной фазы 9TaC–1HfC. Данный тепловой эффект перекрывается с последующим экзотермическим эффектом (с максимумом при температуре 580°С), связанным с окислением углерода в стартовой системе. Причем наблюдаемая потеря массы составляет всего 9.8%, что также подтверждает сделанный вывод о частично произошедшем карботермическом синтезе непосредственно в процессе пиролиза органических компонентов при температуре 1000°С. Чтобы оценить содержание карбидной фазы в составе стартового порошка, приняли предположение, что процессы окисления синтезированного карбида и пиролитического углерода не перекрываются и прирост массы 2.6% связан с полным окислением TaC–HfC. Полученные расчеты свидетельствуют о том, что в системе, образовавшейся в ходе наиболее высокотемпературной карбонизации ксерогеля, содержится не менее 19–20 мол. % карбидной фазы.
Оценку реакционной способности полученных образцов в процессе карботермического синтеза карбида тантала-гафния выполняли путем исследования их термического поведения при нагреве в токе аргона до температуры 1400°С (рис. 5). Для сравнительных экспериментов использовали навески порошков в количестве 73 ± 5 мг.
Рис. 5.
Кривые ДСК (а) и ТГА (б) в токе аргона образцов, полученных в результате карбонизации тантал-гафний-полимерсодержащих ксерогелей при температурах 400, 700 и 1000°С.
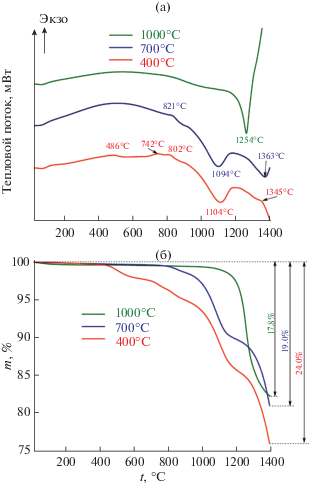
Показано, что минимальная потеря массы (17.8%) характерна для образца исходной системы Ta2O5–HfO2–C–(Ta,Hf)C, полученной в результате карбонизации ксерогеля при наивысшей температуре 1000°С. Этому процессу соответствует выраженный эндотермический эффект с минимумом при 1254°С.
Рис. 6.
Рентгенограммы продуктов нагрева до температуры 1400°С в токе аргона образцов, полученных в результате карбонизации тантал-гафний-полимерсодержащих ксерогелей при температурах 400 (1), 700 (2) и 1000°С (3).
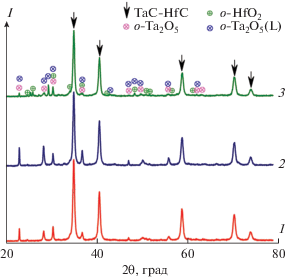
Лишь немногим бóльшая потеря массы за счет карботермии наблюдается для образца, полученного при температуре 700°С (19.0%), причем кривая ДСК свидетельствует о том, что реакционный процесс имеет ступенчатый характер: на термограмме присутствует уширенный слабый экзотермический эффект с максимумом при ~820°С, который, вероятно, связан с термической деструкцией остаточных органических фрагментов (потеря массы ~1.3%). При бóльших температурах наблюдаются два эндотермических эффекта с минимумами при 1094 и 1363°С, что приводит к мысли о возможности раздельного синтеза карбидов на основе TaC и HfC. Гипотеза о присутствии в системах существенно различающихся по дисперсности фракций, для которых различна и реакционная способность, маловероятна, так как не подтверждается данными РЭМ на различных ускоряющих напряжениях.
Максимальная потеря массы (24%) в результате нагрева системы Ta2O5–HfO2–C до 1400°С в токе аргона свойственна образцу, полученному при минимальной температуре карбонизации 400°С. Однако следует учитывать, что зафиксированное изменение массы является результатом протекания следующих процессов:
– окончательного пиролиза органических фрагментов (чему соответствуют уширенные и слабые экзотермические эффекты с максимумами при температурах 486, 742 и 802°С, положение которых близко к таковым для случая пиролиза ксерогеля (рис. 1б);
– карботермического синтеза сложного карбида (Ta,Hf)C, сопровождающегося эндотермическими эффектами с максимумами при температурах 1104 и >1345°C.
Смещение положения первого эндоэффекта в область больших температур может быть объяснено частичным перекрыванием температурных интервалов первого и второго процессов. В рассматриваемом случае также возможно формирование двухфазной системы (Ta,Hf)C + (Hf,Ta)C с явным превалированием первого продукта, что, в принципе, свойственно для низкотемпературного синтеза карбидов тантала-гафния [35, 56, 57].
На рентгенограммах продуктов, полученных в результате нагрева образцов в процессе карбонизации тантал-гафний-полимерсодержащих ксерогелей при различных температурах (400–1000°С), присутствуют интенсивные рефлексы, соответствующие фазе сложного карбида (Ta,Hf)C на основе карбида тантала [58] с параметром решетки 4.451–4.453 Å, а также рефлексы фазы орторомбического оксида тантала [55]. Для образца, полученного при наивысшей температуре 1000°С, помимо названных фаз присутствуют также орторомбический оксид гафния [59] и низкотемпературная модификация o-Ta2O5 [60].
Оценка содержания фазы (Ta,Hf)C в полученных продуктах с применением метода Ритвельда показала, что максимальное ее количество (88.7%) образовалось при нагреве образца, синтезированного при минимальной температуре карбонизации 400°С, что свидетельствует о его высокой реакционной способности. Содержание карбидной фазы в образце, полученном при температуре 700°С, существенно ниже – 69.1%. Наиболее интересная ситуация просматривается для образца, полученного в результате карбонизации при температуре 1000°С: содержание фазы (Ta,Hf)C в нем приближается к таковому для первого образца и составляет 85.4%. Однако с учетом того, что в исходном порошке уже после карбонизации количество карбида тантала-гафния составляет не менее 19–20%, увеличение его количества в ходе динамического нагрева до 1400°С составляет лишь ~65–66%.
ЗАКЛЮЧЕНИЕ
В рамках исследований разработан новый метод получения высокодисперсного и химически активного состава Ta2O5–HfO2–C, перспективного для реакционного горячего прессования или искрового плазменного спекания керамических материалов на основе сложного карбида тантала-гафния.
Метод включает в себя одновременную инициацию процессов гидролиза тантал-гафнийсодержащих прекурсоров класса алкоксидов и алкоксоацетилацетонатов металлов и кислотно-катализируемой полимеризации фурфурилового спирта с образованием плотного геля (методика создания взаимопроникающих органо-неорганических сеток). Определены концентрационные интервалы, позволяющие избежать неконтролируемого гидролиза или полимеризации, препятствующих формированию связнодисперсных систем.
На основе полученного после сушки ксерогеля путем карбонизации в условиях динамического вакуума при различных температурах (400, 700 и 1000°С) получены образцы системы Ta2O5–HfO2–C с различной реакционной способностью с точки зрения карботермического синтеза сложных карбидов. Изучен их элементный и фазовый состав, микроструктура и термическое поведение в токе воздуха. Отмечено, что благодаря высокой температуре карбонизации (1000°С) уже на данной стадии возможно образование ≥19–20% нанокристаллической карбидной фазы, окисление которой на воздухе начинается уже при температуре ~220°C. Для образца же, синтезированного при минимальной температуре 400°С, отмечается присутствие достаточно высокого количества непиролизованных органических фрагментов (до 3–4 мас. %).
Анализ термического поведения полученных систем Ta2O5–HfO2–C при нагреве до температуры 1400°С в токе инертного газа показал, что, как и ожидалось, наибольшей реакционной способностью (максимальное количество синтезированного в данном процессе карбида тантала-гафния) обладает образец, температура карбонизации которого минимальна. Однако в случае его применения для реакционной высокотемпературной консолидации карбидной керамики необходимо иметь в виду вероятное активное газовыделение на начальной стадии прессования, которое может срывать вакуум в камере.
Минимальную реакционную способность именно при карботермическом синтезе в токе аргона продемонстрировала система Ta2O5–HfO2–C–(Ta,Hf)C, полученная в результате карбонизации ксерогеля при наивысшей температуре 1000°С. Несмотря на высокое финальное содержание карбидной фазы (~85%) и отсутствие остаточных органических фрагментов, ее вряд ли стоит использовать для реакционного горячего прессования или ИПС, поскольку при нагреве кристаллизуется не только оксид тантала, но и существенно менее реакционноспособный оксид гафния.
Полученные данные позволяют осознанно выбирать температуру карбонизации тантал-гафний-полимерсодержащих ксерогелей с формированием максимально реакционноспособных составов Ta2O5–HfO2–C для последующего изготовления карбидной керамики в системе TaC–HfC.
Список литературы
Samsonov G.V. // Refractory transition metal compounds. N.Y.: Academic Press,1964.
Rudy E., Benesovsky F., Toth L.E. // Z. Metallkd. 1963. V. 54. P. 345.
Nowotny H., Kieffer R., Benesovsky F. et al. // Monatsh. Chem. 1959. V. 90. № 5. P. 669.
Agte C., Alterthum H. // Z. Techn. Phys. 1930. V. 6. P. 182.
Deadmore D.L. // J. Am. Ceram. Soc. 1965. V. 48. № 7. P. 357. https://doi.org/10.1111/j.1151-2916.1965.tb14760.x
Andrievskii R.A., Strel’nikova N.S., Poltoratskii N.I. et al. // Powder Metall. Met. Ceram. 1967. V. 6. № 1. P. 65. https://doi.org/10.1007/BF00773385
Barantseva I.G., Paderno V.N., Paderno Y.B. // Powder Metall. Met. Ceram. 1967. V. 6. № 2. P. 139.
Rudy E., Nowotny H. // Monatsh. Chem. 1963. V. 94. № 3. P. 507. https://doi.org/10.1007/BF00903490
Фесенко В.В., Болгар А.С. Испарение тугоплавких соединений. M.: Металлургия, 1966.
Киффер Р., Бенезовский Ф. Твердые материалы. M.: Металлургия, 1968.
Холлек Х. Двойные и тройные карбидные и нитридные системы переходных металлов. M.: Металлургия, 1988.
Rudy E., Nowotny H., Benesovsky F. et al. // Monatshefte für Chemie und verwandte Teile anderer Wissenschaften. 1960. V. 91. № 1. P. 176. https://doi.org/10.1007/BF00903181
Nowotny H., Kieffer R., Benesovsky F. et al. // Monatshefte für Chemie und verwandte Teile anderer Wissenschaften. 1959. V. 90. № 5. P. 669. https://doi.org/10.1007/BF00902392
Bittner H., Goretzki H. // Monatsh. Chem. 1960. V. 91. № 4. P. 616. https://doi.org/10.1007/BF00899797
Cedillos-Barraza O., Manara D., Boboridis K. et al. // Sci. Rep. 2016. V. 6. № 1. P. 37962. https://doi.org/10.1038/srep37962
Savvatimskiy A.I., Onufriev S.V., Muboyadzhyan S.A. // J. Eur. Ceram. Soc. 2019. V. 39. № 4. P. 907. https://doi.org/10.1016/j.jeurceramsoc.2018.11.030
Zhang C., Gupta A., Seal S. et al. // J. Am. Ceram. Soc. 2017. V. 100. № 5. P. 1853. https://doi.org/10.1111/jace.14778
Zhang C., Boesl B., Agarwal A. // Ceram. Int. 2017. V. 43. № 17. P. 14798. https://doi.org/10.1016/j.ceramint.2017.07.227
Feng L., Kim J.-M., Lee S.-H. et al. // J. Am. Ceram. Soc. 2016. V. 99. № 4. P. 1129. https://doi.org/10.1111/jace.14144
Shahedifar V., Kakroudi M.G. // Int. J. Refract. Met. Hard Mater. 2018. V. 71. P. 15. https://doi.org/10.1016/j.ijrmhm.2017.10.025
Simonenko E.P., Simonenko N.P., Sevastyanov V.G. et al. // Russ. J. Inorg. Chem. 2019. V. 64. № 14. P. 1697. https://doi.org/10.1134/S0036023619140079
Симоненко Е.П., Симоненко Н.П., Севастьянов В.Г. и др. Ультравысокотемпературные керамические материалы: современные проблемы и тенденции. М., 2020.
Simonenko E.P., Simonenko N.P., Gordeev A.N. et al. // J. Eur. Ceram. Soc. 2021. V. 41. № 2. P. 1088. https://doi.org/10.1016/j.jeurceramsoc.2020.10.001
Simonenko E.P., Simonenko N.P., Lysenkov A.S. et al. // Russ. J. Inorg. Chem. 2020. V. 65. № 3. P. 446. https://doi.org/10.1134/S0036023620030146
Liu H.-L., Liu J.-X., Liu H.-T. et al. // Scripta Mater. 2015. V. 107. P. 140. https://doi.org/10.1016/j.scriptamat.2015.06.005
Xiang M., Gu J., Ji W. et al. // Ceram. Int. 2018. V. 44. № 7. P. 8417. https://doi.org/10.1016/j.ceramint.2018.02.035
Ghassemi Kakroudi M., Dehghanzadeh Alvari M., Shahedi Asl M. et al. // Ceram. Int. 2020. V. 46. № 3. P. 3725. https://doi.org/10.1016/j.ceramint.2019.10.093
Simonenko E.P., Simonenko N.P., Papynov E.K. et al. // J. Sol-Gel Sci. Technol. 2017. V. 82. № 3. P. 748. https://doi.org/10.1007/s10971-017-4367-2
Simonenko E.P., Simonenko N.P., Papynov E.K. et al. // Russ. J. Inorg. Chem. 2018. V. 63. № 1. P. 1. https://doi.org/10.1134/S0036023618010187
Simonenko E.P., Simonenko N.P., Gordeev A.N. et al. // J. Sol-Gel Sci. Technol. 2019. V. 92. № 2. P. 386. https://doi.org/10.1007/s10971-019-05029-9
Simonenko E.P., Simonenko N.P., Mokrushin A.S. et al. // Russ. J. Inorg. Chem. 2019. V. 64. № 14. P. 1849. https://doi.org/10.1134/S0036023619140109
Sevastyanov V.G., Simonenko E.P., Ignatov N.A. et al. // Russ. J. Inorg. Chem. 2011. V. 56. № 5. P. 661. https://doi.org/10.1134/S0036023611050214
Simonenko E.P., Ignatov N.A., Simonenko N.P. et al. // Russ. J. Inorg. Chem. 2011. V. 56. № 11. P. 1681. https://doi.org/10.1134/S0036023611110258
Simonenko E.P., Simonenko N.P., Derbenev A.V. et al. // Russ. J. Inorg. Chem. 2013. V. 58. № 10. P. 1143. https://doi.org/10.1134/S0036023613100215
Simonenko E.P., Simonenko N.P., Petrichko M.I. et al. // Russ. J. Inorg. Chem. 2019. V. 64. № 11. P. 1317. https://doi.org/10.1134/S0036023619110196
Li F., Liu J., Huang X. et al. // J. Am. Ceram. Soc. 2019. V. 102. № 10. P. 5746. https://doi.org/10.1111/jace.16488
Zhang X.-F., Chen Z., Feng Y. et al. // ACS Sustain. Chem. Eng. 2018. V. 6. № 1. P. 1068. https://doi.org/10.1021/acssuschemeng.7b03375
Miao Y., Yang Z., Rao J. et al. // Ceram. Int. 2017. V. 43. № 5. P. 4372. https://doi.org/10.1016/j.ceramint.2016.12.083
Chandrasekar M.S., Srinivasan N.R. // Ceram. Int. 2016. V. 42. № 7. P. 8900. https://doi.org/10.1016/j.ceramint.2016.02.145
Kong Y., Zhong Y., Shen X. et al. // Mater. Lett. 2013. V. 99. P. 108. https://doi.org/10.1016/j.matlet.2013.02.047
Kong Y., Zhong Y., Shen X. et al. // J. Porous Mater. 2013. V. 20. № 4. P. 845.
Badhe Y., Balasubramanian K. // RSC Adv. 2014. V. 4. № 55. P. 28956. https://doi.org/10.1039/C4RA03316G
Liu B., Ju W., Zhang J. et al. // J. Sol-Gel Sci. Technol. 2017. V. 83. № 1. P. 100.
Wang D.H., Fu X. // Adv. Mater. Res. 2011. V. 194–196. P. 562. https://doi.org/10.4028/www.scientific.net/AMR.194-196.562
Mojarad B.S., Nourbakhsh A., Kahrizsangi R.E. et al. // Ceram. Int. 2015. V. 41. № 4. P. 5287. https://doi.org/10.1016/j.ceramint.2014.12.007
Zhang Y., Yuan Z., Zhou Y. // Ceram. Int. 2014. V. 40. № 6. P. 7873. https://doi.org/10.1016/j.ceramint.2013.12.134
Zhou M., Rodrigo P.D.D., Wang X. et al. // J. Eur. Ceram. Soc. 2014. V. 34. № 8. P. 1949. https://doi.org/10.1016/j.jeurceramsoc.2014.01.028
Wang X., Lu M., Qiu L. et al. // Ceram. Int. 2016. V. 42. № 1. P. 122. https://doi.org/10.1016/j.ceramint.2015.08.017
Zhong J., Peng Y., Zhou M. et al. // Microporous Mesoporous Mater. 2014. V. 190. P. 309. https://doi.org/10.1016/j.micromeso.2014.02.029
Zhong J., Liang S., Zhao J. et al. // J. Eur. Ceram. Soc. 2012. V. 32. № 12. P. 3407. https://doi.org/10.1016/j.jeurceramsoc.2012.04.047
Ang C., Seeber A., Williams T. et al. // J. Eur. Ceram. Soc. 2014. V. 34. № 12. P. 2875. https://doi.org/10.1016/j.jeurceramsoc.2014.04.015
Li F., Huang X. // J. Eur. Ceram. Soc. 2018. V. 38. № 4. P. 1103. https://doi.org/10.1016/j.jeurceramsoc.2017.11.031
Sevast’yanov V.G., Simonenko E.P., Simonenko N.P. et al. // Russ. J. Inorg. Chem. 2012. V. 57. № 3. P. 307. https://doi.org/10.1134/S0036023612030278
Simonenko E.P., Simonenko N.P., Ezhov Y.S. et al. // Phys. At. Nucl. 2015. V. 78. № 12. P. 1357. https://doi.org/10.1134/S106377881512011X
Aleshina L.A., Loginova S.V. // Crystallogr. Reports. 2002. V. 47. № 3. P. 415. https://doi.org/10.1134/1.1481927
Fedorov T.F. Carbon–Hafnium-Tantalum Ternary Alloy Phase Diagram 1000C. ASM Alloy Phase Diagrams Cent., 2007.
Гусев А.И. // Журн. физ. химии. 1985. T. 59. № 3. C. 579.
von Schwarz M., Summa O. // Met. Met. Met. 1933. V. 12. P. 298.
Ohtaka O., Yamanaka T., Kume S. // J. Ceram. Soc. Jpn. 1991. V. 99. № 1153. P. 826. https://doi.org/10.2109/jcersj.99.826
Stephenson N.C., Roth R.S. // Acta Crystallogr., Sect. B: Struct. Crystallogr. Cryst. Chem. 1971. V. 27. № 5. P. 1037. https://doi.org/10.1107/S056774087100342X
Дополнительные материалы отсутствуют.
Инструменты
Журнал неорганической химии