Журнал неорганической химии, 2023, T. 68, № 8, стр. 1111-1118
Взаимодействие SiC с оксидной композицией Al2O3−(t + m)ZrO2(Y2O3)
М. Г. Фролова a, *, А. С. Лысенков a, С. Н. Перевислов b, Н. В. Петракова a, К. А. Ким a, М. А. Севостьянов a, А. Ю. Иванников a, М. Д. Мельников a, c, Ю. Ф. Каргин a
a Институт металлургии и материаловедения им. А.А. Байкова РАН
119334 Москва, Ленинский пр-т., 49, Россия
b Институт химии силикатов им. И.В. Гребенщикова РАН
199034 Санкт-Петербург, наб. Макарова, 2, Россия
c Российский химико-технологический университет им. Д.И. Менделеева
125048 Москва, Миусская пл., 9, Россия
* E-mail: frolovamarianna@bk.ru
Поступила в редакцию 09.02.2023
После доработки 27.03.2023
Принята к публикации 15.04.2023
- EDN: MLBTKF
- DOI: 10.31857/S0044457X23600172
Аннотация
Методом контактного взаимодействия в интервале температур 1000–1860°С изучена специфика взаимодействия SiC с оксидной композицией Al2O3−(t + m)ZrO2(Y2O3). В ходе эксперимента по данным фоторегистрации в режиме реального времени изменения размеров и формы образца Al2O3−(t + m)ZrO2(Y2O3) на керамической подложке SiC установлено, что в интервале температур 1720–1860°С происходит взаимодействие композиции Al2O3−(t + m)ZrO2(Y2O3) с подложкой из карбида кремния, которое сопровождается ее расплавлением и проникновением (пропиткой) в подложку. Выполнен рентгенофазовый анализ области взаимодействия оксидной композиции с SiC непосредственно на подложке и поверхностного слоя глубиной <1 мм (отделенного скалыванием). Установлено, что в области контакта помимо фаз 6H-SiC, Si и Al2O3, t-ZrO2, являющихся соответственно исходными компонентами подложки и оксидной композиции, образуются ZrС, Al2Y4O9, Al3.21Si0.47 вследствие окислительно-восстановительных реакций с участием оксидного расплава.
ВВЕДЕНИЕ
Керамика на основе карбида кремния является распространенным материалом для применения в различных отраслях промышленности благодаря ее стабильности при высоких температурах, стойкости к разрушению под действием агрессивных химикатов и истирающим воздействиям [1, 2]. Эти важные свойства позволяют рекомендовать данный вид материалов для применения в авиакосмической, автомобильной, химической и многих других областях для изготовления разнообразных видов изделий и конструкций [3–9].
Ввиду преимущественно ковалентного типа связи Si−C спекание карбидокремниевой керамики, как правило, проводят при высоких температурах (до 2200°C) методом твердофазного спекания (sintered silicon carbide, S-SiC) либо с участием спекающих добавок – жидкофазное спекание (liquid phase – sintered silicon carbide, LPS-SiC). При LPS-SiC происходит образование жидкой фазы, что способствует интенсификации спекания по сравнению с S-SiC. Как следствие, температура спекания может быть снижена до 1800°С и ниже, если состав добавок близок к эвтектическому [10–15]. Спекание керамики с образованием жидкой фазы оказывает существенное влияние на структуру, фазовый состав и, следовательно, на свойства материала. Свойства керамики LPS-SiC были изучены многими авторами. В качестве добавок, интенсифицирующих спекание предпочтительны соединения Al2O3, Y2O3, MgO, ZrO2, CaO, Er2O3, AlN и их различные сочетания [16–26]. В результате жидкофазного спекания происходит совокупность различных физико-химических процессов, обусловливающих специфическую структуру материалов, которая представляет собой зерна SiC и межзеренную фазу, кристаллизующуюся при охлаждении [27–31].
Достаточно широко изучено взаимодействие карбида кремния со спекающими добавками оксидов, такими как Al2O3, Y2O3 или их комбинациями – Al2O3−Y2O3 [32–41]. Сведения об использовании ряда многокомпонентных спекающих добавок (как правило, трехкомпонентных, в частности Al2O3−CaO−Y2O3, Al2O3−CaO−C, Al2O3−TiO2−MnO, Al2O3−MnO−SiO2, MgO−SiO2, Al2O3(MgO)−SiO2−MgO, MnO–TiO2, CaO–B2O3–SiO2, CaO– Al2O3–Y2O3, Al2O3–ZrO2 < MgO–Al2O3–Y2O3) приведены в работах [29–42], однако их взаимодействие с карбидом кремния изучено недостаточно. Одной из таких является добавка в системе Al2O3−Y2O3−ZrO2.
Цель настоящей работы – изучение специфики взаимодействия SiC с оксидной композицией Al2O3−(t + m)ZrO2(Y2O3) в режиме реального времени методом непосредственного контактного взаимодействия в интервале температур от 1000 до 1860°С, а также исследование фазового состава продуктов взаимодействия.
ЭКСПЕРИМЕНТАЛЬНАЯ ЧАСТЬ
В работе использовали порошки в виде заранее синтезированной добавки в системе Al2O3−Y2O3−ZrO2. Оксидную композицию расчетного состава 60.6Al2O3−3.6Y2O3−35.8ZrO2 получали плазмохимическим методом из водных растворов нитратных солей – термическим разложением в плазме высокочастотного разряда капель раствора. Предполагаемая температура плавления этой композиции, согласно диаграмме состояния системы Al2O3−Y2O3−ZrO2, составляет 1860°С (рис. 1). Ранее указанную смесь в виде спекающей добавки не использовали, однако, по литературным данным, композит на основе глинозема с добавкой фаз моноклинного и тетрагонального циркония обладает высокими прочностными и высокотемпературными характеристиками [42–47 ].
Рентгенофазовый анализ образцов синтезированной композиции в системе Al2O3−Y2O3−ZrO2 выявил присутствие фаз ZrO2 (смесь тетрагональной и моноклинной модификаций) и Al2O3. Присутствие оксида иттрия идентифицировать не удалось (рис. 2). Это свидетельствует о том, что в результате плазмохимического синтеза произошла частичная стабилизация диоксида циркония оксидом иттрия. Таким образом, в данной работе изучена специфика взаимодействия SiC и оксидной композиции Al2O3−(t + m)ZrO2(Y2O3).
Рис. 2.
Дифрактограмма порошка композиции Al2O3−(t + m)ZrO2(Y2O3), полученного плазмохимическим синтезом.
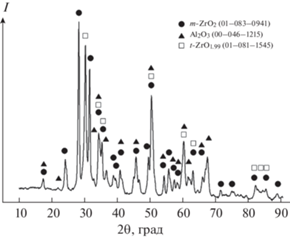
СЭМ-изображение морфологии частиц порошков композиции в системе Al2O3−Y2O3−ZrO2 представлено на рис. 3. Видно, что синтезированный порошок представлен наночастицами с отдельными агломератами округлой формы, характерными для плазмохимического метода.
Специфику взаимодействия SiC и оксидной композиции Al2O3−(t + m)ZrO2(Y2O3) изучали в интервале температур 1000–1860°С методом непосредственного контактного взаимодействия. Для проведения экспериментов использовали плоские полированные пластины керамики карбида кремния, полученные методом реакционного спекания. Образец карбида кремния состоит из смеси модификаций β- и α-SiC, выявлено также присутствие фазы кремния, поскольку керамика получена методом реакционного спекания. Пористость реакционно-спеченной карбидокремниевой пластины 5%, плотность 3.08 г/см3. Образец оксидной композиции Al2O3−(t + m)ZrO2(Y2O3) формировали сухим прессованием в форме таблетки с диаметром 5 мм и высотой 3 мм, который помещали на поверхность керамического образца реакционноспеченного SiC (10 × 10 × 3 мм) (рис. 4). Подложку SiC с размещенным образцом оксидной композиции Al2O3−(t + m)ZrO2(Y2O3) помещали в графитовую печь Thermal Technology Inc. high temperature experts (модель HP20-3560-20). Камеру печи вакуумировали и заполняли аргоном до атмосферного давления 1 атм. Печь нагревали со скоростью 10 град/мин до температуры полного расплавления образца оксидной композиции Al2O3−(t + m)ZrO2(Y2O3) при постоянной продувке камеры печи аргоном. Изменение геометрической формы и размеров регистрировали с помощью фотокамеры и компьютера, изменение температуры – пирометром Raytek.
Рис. 4.
Оксидная композиция Al2O3−(t + m)ZrO2(Y2O3) на подложке из SiC: а – до эксперимента, б – после эксперимента.
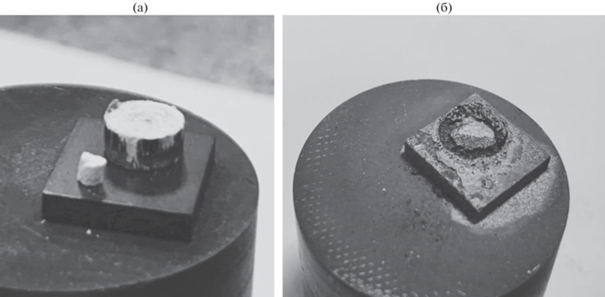
Фазовый состав образцов определяли при помощи дифрактометра XRD ДРОН-3 в CoKα-излучении (λ = 1.79020 Å, скорость сканирования 2θ = = 2 град/мин). Идентификацию фаз осуществляли с помощью базы данных ICDD-2013. Морфологию частиц исходных порошков и микроструктурные особенности керамических образцов исследовали методом растровой электронной микроскопии (электронный микроскоп Tescan Vega II SBU) с системой INCA VEGA для микрорентгеноспектрального анализа.
РЕЗУЛЬТАТЫ И ОБСУЖДЕНИЕ
На рис. 5 представлены фотографии образца оксидной композиции Al2O3−(t + m)ZrO2(Y2O3) на подложке SiC при нагревании до температуры 1860°С.
В ходе визуальных наблюдений за протеканием эксперимента, а также по изображениям на фотографиях установлено, что размягчение оксидной композиции Al2O3−(t + m)ZrO2(Y2O3), сопровождаемое изменением геометрической формы, происходит при температуре ⁓1720°С. При увеличении температуры выше 1750°С образуется жидкая фаза, происходит ее растекание по поверхности карбида кремния и частичная пропитка области вокруг контакта оксидной композиции с подложкой (рис. 4б).
После проведения эксперимента по изучению взаимодействия реакционноспеченного SiC с оксидной композицией Al2O3−(t + m)ZrO2(Y2O3) поверхность керамических подложек исследовали с помощью СЭМ. На рис. 6 представлены микрофотографии участков поверхности образцов керамики в области контакта оксидной композиции с подложкой, на которых видно, что после взаимодействия поверхность является неоднородной – зерна (частицы) SiC (темные участки) окружены продуктами кристаллизации жидкой фазы (светлые области).
Рис. 6.
СЭМ-изображение поверхности образца SiC (1) после взаимодействия со смесью оксидов Al2O3 и YSZ (2).

Фазовый состав области контакта карбида кремния с оксидной композицией Al2O3−(t + + m)ZrO2(Y2O3) после плавления оксидной композиции изучали с помощью рентгенофазового анализа. По данным РФА керамических подложек SiC, в поверхностном слое регистрируются следующие основные фазы: ZrC, 6H-SiC, Si, Al2O3 (рис. 7).
Рис. 7.
Дифрактограмма поверхности подложки SiC после взаимодействия оксидной композиции с подложкой из карбида кремния.
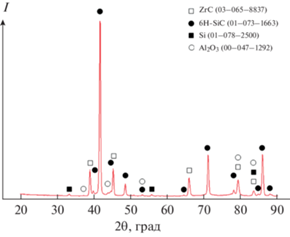
С целью проведения более подробного рентгенофазового анализа область контакта оксидной композиции Al2O3−(t + m)ZrO2(Y2O3) и прилегающую область пропитки расплавом механически отделяли (откалыванием частичек в глубину до 1 мм) от подложки SiC и измельчали. Согласно РФА, в приготовленных порошках идентифицированы следующие фазы: 6H-SiC, Al2O3, t-ZrO2, ZrC, Si, Al2Y4O9, Al3.21Si0.47 (рис. 8). Фазы 6H-SiC, Si и Al2O3, t-ZrO2 являются исходными компонентами подложки и оксидной композиции соответственно. Очевидно, что наличие в области контакта образовавшихся продуктов ZrС, Al2Y4O9, Al3.21Si0.47 обусловлено протеканием различных (последовательно-параллельных) окислительно-восстановительных реакций SiC с расплавом оксидной композиции сложного состава.
Рис. 8.
Дифрактограмма порошка, полученного измельчением приповерхностной области взаимодействия композиции Al2O3−(t + m)ZrO2(Y2O3) с подложкой SiC.
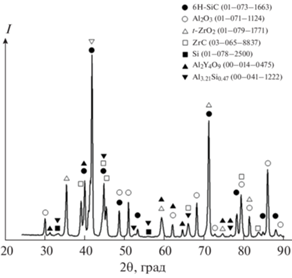
Известно, что карбид кремния окисляется при высоких температурах в атмосфере кислорода с образованием тонкой пленки диоксида кремния и оксидов углерода согласно следующим реакциям [16]:
(1)
${\text{SiC + 2}}{{{\text{O}}}_{2}} \to {\text{Si}}{{{\text{O}}}_{{\text{2}}}}{\text{ + C}}{{{\text{O}}}_{{\text{2}}}}{\text{,}}$(2)
$2{\text{SiC + 3}}{{{\text{O}}}_{2}} \to {\text{2Si}}{{{\text{O}}}_{{\text{2}}}}{\text{ + 2CO}}.$В ряде работ по спеканию карбида кремния рассмотрены также возможные реакции образования различных соединений в результате взаимодействия с различными оксидными спекающими добавками. Например, в [34] в спеченных при 1950°С образцах карбидокремниевой керамики, содержащей 30 мас. % иттрий-алюминиевого граната (YAG), основными присутствующими фазами являются AlYO3 и SiC, обнаружены также фазы оксикарбида алюминия (Al4O4C и Al2OC) в различных количествах со следами SiO2. В [47 ] исследованы фазовые взаимоотношения в тройной системе SiC−ZrO2−CaO и показано, что ZrO2 реагирует с SiC и CaO с образованием ZrC и силиката кальция посредством серии твердофазных реакций. Таким образом, можно предположить, что обнаруженные в образцах после проведения эксперимента продукты реакции ZrС, Al2Y4O9, Al3.21Si0.47 образуются при взаимодействии SiC с компонентами оксидной композициии Al2O3−(t + + m)ZrO2(Y2O3), в том числе с учетом реакций (1) и (2), в результате следующих реакций:
(3)
${\text{Zr}}{{{\text{O}}}_{{\text{2}}}}{\text{ + CO = ZrC + }}{{{\text{O}}}_{{\text{2}}}}{\text{,}}$(4)
$3{\text{Zr}}{{{\text{O}}}_{{\text{2}}}}{\text{\; + \;4SiC}}~\,\, \to \,\,~{\text{3ZrC\; + \;4SiO\; + \;C}}{{{\text{O}}}_{{\text{2}}}}{\text{,}}$(5)
$\begin{gathered} 5{\text{Si}}{{{\text{C}}}_{{{\text{тв}}}}}{\text{ + 3A}}{{{\text{l}}}_{{\text{2}}}}{{{\text{O}}}_{{\text{3}}}}_{{{\text{тв}}}} \to 5{\text{C}}{{{\text{O}}}_{{\text{г}}}}{\text{ + 2S}}{{{\text{i}}}_{{{\text{распл}}}}}{\text{ + }} \\ {\text{ + 3A}}{{{\text{l}}}_{{{\text{распл}}}}}{\text{ + 3Si}}{{{\text{O}}}_{{\text{г}}}}{\text{ + A}}{{{\text{l}}}_{{\text{2}}}}{{{\text{O}}}_{{\text{г}}}}{\text{ + A}}{{{\text{l}}}_{{\text{г}}}}{\text{.}} \\ \end{gathered} $Присутствие фазы Al3.21Si90.47 согласуется с данными [28] об образовании расплавов металлических алюминия и кремния при взаимодействии Al2O3 с SiC по реакции (5) в атмосфере аргона (как и в нашем эксперименте). При этом металлический алюминий может также взаимодействовать с остаточным кремнием в исходной подложке SiC, полученного методом реакционного спекания (рис. 6). Наличие в продуктах взаимодействия фазы Al2Y4O9 можно связать (учитывая отсутствие других соединений иттрия, в частности карбидов) с формированием оксида иттрия при взаимодействии (t + m)ZrO2(Y2O3) с SiC и CO по реакциям (3), (4) и его последующем взаимодействии с оксидом алюминия.
ЗАКЛЮЧЕНИЕ
Взаимодействие керамических образцов реакционно-связанного SiC с оксидной композицией Al2O3−(t + m)ZrO2(Y2O3) изучено контактным методом в интервале температур 1000−1860°С в атмосфере аргона. В ходе эксперимента по данным визуальных наблюдений и фоторегистрации в режиме реального времени изменения размеров и формы образцов композиции Al2O3−(t + m)ZrO2(Y2O3) на керамической подложке SiC установлено, что взаимодействие композиции с подложкой происходит в интервале температур 1720–1860°С и сопровождается ее полным расплавлением и проникновением (пропиткой) в подложку. При этом оксидная композиция Al2O3−(t + m)ZrO2(Y2O3) растекается по поверхности подложки из карбида кремния, частично пропитывает области вокруг контакта с подложкой и распределяется по границам зерен карбида кремния. Согласно РФА области взаимодействия оксидной композиции с SiC непосредственно на подложке и поверхностного слоя глубиной <1 мм (отделенного скалыванием), в области контакта выявлены (помимо фаз 6H-SiC, Si и Al2O3, t-ZrO2, являющихся соответственно исходными компонентами подложки и оксидной композиции) продукты реакции ZrС, Al2Y4O9, Al3.21Si0.47, образующиеся вследствие ряда окислительно-восстановительных реакций с участием оксидного расплава и оксида углерода.
Список литературы
Шевченко В.Я., Баринов С.М. Техническая керамика. M.: Наука, 1993. 187 с.
Андрианов Н.Т. и др. Химическая технология керамики: учеб. пособие для вузов / Под ред. Гузмана И.Я. М.: ООО Риф “Стройматериалы”, 2012. 496 с.
Schwetz K.A. // Handbook of Ceramic Hard Materials. 2000. P. 683.
Фролова М.Г., Лысенков А.С., Титов Д.Д. и др. // Журн. неорган. химии. 2021. Т. 66. № 8. С. 1086. https://doi.org/10.1134/S0036023621080052
Saddow S.E. Advances in Silicon Carbide. Processing and Applications. London: Artech House Inc., 2004. 435 p.
Katoh Y., Snead L.L., Szlufarska I. et al. // Curr. Opin. Solid State Mater. Sci. 2012. V. 16. P. 143. https://doi.org/10.1016/j.cossms.2012.03.005
Christin F. // Adv. Eng. Mater. 2002. V. 4. P. 903. https://doi.org/10.1002/adem.200290001
Ji S., Zhang Z., Wang F. // CES Transactions on Electrical Machines and Systems. 2017. V. 1. P. 254. https://doi.org/10.23919/TEMS.2017.8086104
Casady J.B., Johnson R.W. // Solid-State Electron. 1996. V. 39. P. 1409. https://doi.org/10.1016/0038-1101(96)00045-7
Neher R., Herrmann M., Brandt K. et al. // J. Eur. Ceram. Soc. 2011. V. 31. P. 175. https://doi.org/10.1016/j.jeurceramsoc.2010.09.002
Zhitnyuk S.V., Golovchenko I.A., Makarov N.A. et al. // Glass Ceram. 2013. V. 70. P. 247. https://doi.org/10.1007/s10717-013-9554-1
Abilev M., Zhilkashinova A., Pavlov A. et al. // Silicon. 2023. https://doi.org/10.1007/s12633-023-02318-5
Кхин Маунг Сое. Композиционная керамика на основе карбида кремния с эвтектическими добавками в системах Al2O3–TiO2–MnO, Al2O3–MnO–SiO2, MgO–SiO2, Al2O3(MgO)–MgO–SiO2. Дис. … канд. техн. наук. М., 2019. 110 с.
Житнюк С.В. // Тр. ВИАМ. 2019. № 3. С. 79.
Житнюк С.В. Керамика на основе карбида кремния, модифицированная добавками эвтектического состава. Дисс. … канд. тех. наук. РХТУ им. Д.И. Менделеева. М., 2014. 174 с.
Фролова М.Г., Каргин Ю.Ф., Лысенков А.С. и др. // Неорган. материалы. 2020. Т. 56. № 9. С. 1039. https://doi.org/10.1134/S0020168520090058
Perevislov S.N., Lysenkov A.S., Titov D.D. et al // Glass Ceram. 2019. V. 75. P. 400. https://doi.org/10.1007/s10717-019-00094-6
Perevislov S.N., Tomkovich M.V., Lysenkov A.S. // Refract. Ind. Ceram. 2019. V. 59. P. 522. https://doi.org/10.1007/s11148-019-00265-6
Перевислов С.Н., Чупов В.Д., Томкович М.В. // Вопросы материаловедения. 2011. № 1. С. 123.
Grande T., Sommerset H., Hagen E. et al. // J. Am. Ceram. Soc. 1997. V. 80. P. 1047.
Перевислов С.Н. // Перспективные материалы. 2013. № 10. С. 47.
Noviyanto A., Yoon D.-H. // Curr. Appl. Phys. 2013. V. 1. P. 287. https://doi.org/10.1016/j.cap.2012.07.027
Tomkovich M.V., Perevislov S.N., Panteleev I.B. et al. // Refract. Ind. Ceram. 2020. V. 60. P. 445. https://doi.org/10.17073/1683-4518-2019-9-31-41
Фролова М.Г., Леонов А.В., Каргин Ю.Ф. и др. // Материаловедение. 2017. № 12. С. 32.
Zawrah M.F., Shaw L. // Ceram. Int. 2004. V. 30. P. 721. doi.org/https://doi.org/10.1016/j.ceramint.2003.07.017
Fei Y., Song X., Du L. et al. // Ceram. Int., Part A. 2022. V. 19. P. 27324. https://doi.org/10.1016/j.ceramint.2022.04.326
Baud S., Thévenot F., Pisch A. et al. // J. Eur. Ceram. Soc. 2003. V. 23. P. 1. https://doi.org/10.1016/S0955-2219(02)00067-5
Baud S., Thévenot F., Chatillon C. // J. Eur. Ceram. Soc. 2003. V. 23. P. 9. https://doi.org/10.1016/S0955-2219(02)00068-7
Baud S., Thévenot F., Chatillon C. // J. Eur. Ceram. Soc. 2003. V. 23. P. 19. https://doi.org/10.1016/S0955-2219(02)00069-9
Baud S., Thévenot F., Chatillon C. // J. Eur. Ceram. Soc. 2003. V. 23. P. 29. https://doi.org/10.1016/S0955-2219(02)00070-5
Ihle J., Herrmann M., Adler J. // J. Eur. Ceram. Soc. 2005. V. 25. P. 987. https://doi.org/10.1016/j.jeurceramsoc.2004.04.015
Ihle J., Herrmann M., Adler J. // J. Eur. Ceram. Soc. 2005. V. 25. P. 1005. https://doi.org/10.1016/j.jeurceramsoc.2004.04.017
Grande T., Sommerset H., Hagen E. et al. // J. Am. Ceram. Soc. 1997. V. 80. № 4. P. 1047.
Baud S., Thévenot F., Pisch A. et al. // J. Eur. Ceram. Soc. 2003. V. 23. P. 1. https://doi.org/10.1016/S0955-2219(02)00067-5
Gadalla A., Almasry M., Kongkachuichay P. // J. Mater. Res. 1992. V. 7. P. 2585.
Samanta A.K., Dharguupta K.K., Ghatak S. // Ceram. Int. 2001. V. 27. P. 123. https://doi.org/10.1016/S0272-8842(00)00050-X
Keppeler M., Reichert H.-G., Broadley J.M. et al. // J. Eur. Ceram. Soc. 1998. V. 18. P. 521. https://doi.org/10.1016/S0955-2219(97)00163-5
Can A., Herrmann M., McLachlan D.S. et al. // J. Eur. Ceram. Soc. 2006. V. 26. P. 1707. https://doi.org/10.1016/j.jeurceramsoc.2005.03.253
Borrero-López O., Ortiz A.L., Guiberteau F. et al. // J. Eur. Ceram. Soc. 2007. V. 27. P. 3351. https://doi.org/10.1016/j.jeurceramsoc.2007.02.190
Gomez E., Echeberria J., Iturriza I. et al. // J. Eur. Ceram. Soc. V. 24. P. 2895. https://doi.org/10.1016/j.jeurceramsoc.2003.09.002
Симоненко Е.П., Симоненко Н.П., Нагорнов И.А. и др. // Журн. неорган. химии. 2020. Т. 65. № 9. С. 1274. https://doi.org/10.31857/S0044457X20090202
Lyubushkin R.A., Sirota V.V., Ivanov O.N. // Glass Phys. Chem. 2012. V. 38. P. 137. https://doi.org/10.1134/S1087659611060101
Ayash S., Alshoufi K., Soukieh M. et al. // J. Fusion Energy. 2016. V. 35. P. 567. https://doi.org/10.1007/s10894-016-0071-4
Oelgardt C., Anderson J., Heinrich J.G. et al. // J. Eur. Ceram. Soc. 2010. V. 30. P. 649. https://doi.org/10.1016/j.jeurceramsoc.2009.09.011
Dyatlova Ya., Ordanyan S.S., Osmakov A. et al. // Adv. Sci. Technol. 2010. V. 65. P. 11. https://doi.org/10.4028/www.scientific.net/AST.65.11
Lakiza S.N., Lopato L.M., Shevchenko A.V. // Powder Metall. Met. Ceram. 1995. V. 33. P. 595.
Дополнительные материалы отсутствуют.
Инструменты
Журнал неорганической химии