Проблемы машиностроения и надежности машин, 2019, № 1, стр. 92-97
ИССЛЕДОВАНИЕ ВЛИЯНИЯ ИЗНОСА ПОДВИЖНЫХ СОПРЯЖЕНИЙ НА ОТКАЗ ПОГРУЖНЫХ ЭЛЕКТРОПРИВОДНЫХ ЛОПАСТНЫХ НАСОСОВ ДЛЯ ДОБЫЧИ НЕФТИ
Н. И. Смирнов 1, *, Е. Е. Григорян 2
1 Институт машиноведения им. А.А. Благонравова РАН
г. Москва, Россия
2 ООО “РЕАМ-РТИ”
МО, г. Балашиха, Россия
* E-mail: smir1947@yandex.ru
Поступила в редакцию 21.03.2018
Аннотация
Рассматриваются условия возникновения отказа функционирования и параметрического отказа установок электроприводных лопастных насосов для добычи нефти, обусловленных износом. Показано, что при износе радиальных сопряжений вибрация корпуса установки может увеличиваться в 10–15 раз. Выявили, что величина утечки через радиальные уплотнения разных ступеней радиального типа практически не зависит от производительности ступеней. Рекомендуется применение износостойких подшипников и уменьшение зазоров в осевых сопряжениях.
Постановка задачи и ее актуальность. В процессе многолетней эксплуатации месторождений с применением различных методов увеличения нефтеотдачи (гидроразрывы, кислотные обработки и т.д.) происходит изменение условий работы насосов [1]. Оно заключается в увеличении содержания абразивных частиц в пластовой жидкости (свыше 500 мг/л), в проявлении различных видов коррозии, повышенном газосодержании (до 300 м3/м3) и т.д. [2, 3]. В результате усиливаются процессы изнашивания деталей и узлов установок, вибрация, которые влияют на возникновение параметрических отказов, отказов функционирования и увеличение энергопотребления. Параметрические отказы заключаются в деградации напорно-расходной характеристики (НРХ) насоса, отказы функционирования – в разрушении деталей установок электроприводных насосов.
При анализе отказов электроприводных насосов в основном применяют методы математической статистики по результатам промысловой эксплуатации [4–6], которые должны проводиться совместно с изучением физических причин, вызывающих те или иные их виды [7]. Цель настоящей статьи состояла в исследовании влияния износа подвижных сопряжений на возникновение отказа функционирования и параметрического отказа.
Основная часть. Установка электроприводного лопастного насоса – машина роторного типа, имеющая нехарактерное для обычных роторных машин отношение длины к диаметру, которое в сотни раз выше. Насосная часть изнашивается в процессе эксплуатации, в результате чего увеличивается динамика системы. Все эти обстоятельства принципиально отличают электроприводной лопастной насос от других типов.
Исследование влияния износа сопряжений на динамику электроприводного лопастного насоса. Интерес к исследованию вибрации такого насоса возник в 90-е годы для объяснения причин усталостного разрушения узлов установки и насосно-компрессорных труб (“полет”) [8, 9]. Не было понятно влияние износа подвижных сопряжений на изменение вибрации и вероятность возникновения отказа функционирования. В работе [10] проведен расчет напряженно-деформированного состояния фланцевых соединений насоса при равномерном износе радиальных сопряжений с использованием численных методов. Однако расчетные методы для таких роторных систем разработаны недостаточно полно, так как работа насоса происходит в условиях информационной неопределенности по ряду параметров. Например, невозможно исчерпывающим образом сформулировать краевые условия, которые оказывают определяющее воздействие на динамику установки. Не известны точно условия опирания установки в скважине. Поэтому при исследовании сложных динамических процессов приходится полагаться на опыт. В работах [11, 12] исследование вибрационных параметров проводили на коротких сборках насосных ступеней с моделированием износа путем проточки радиальных сопряжений. Однако, невозможно точно смоделировать вибрационное состояние реальной установки на короткой модели [13].
Для выяснения степени влияния износа радиальных сопряжений на изменение динамики были проведены испытания насосных секций пятого габарита производительностью 25–320 м3/сут на специально разработанном стенде. Насосная секция перекачивала модельную жидкость, состоящую из водопроводной воды и кварцевого песка различной концентрации, по замкнутому контуру. На корпусе устанавливали восемь акселерометров для измерения вибрации в двух плоскостях. В конце опыта измеряли износ всех подвижных сопряжений и промежуточных подшипников.
Испытания более 30 насосных секций показали, что виброскорость монотонно увеличивалась на протяжении опыта (рис. 1). В зависимости от конструктивных особенностей насосной секции, в частности наличия износостойких промежуточных подшипников и степени износа сопряженных узлов стенда характер кинетики вибрации и распределения ее по длине секции может различаться. Однако основные закономерности износа и вибрации сохраняются. Наиболее сильно влияет на изменение динамики износ радиальных сопряжений. При увеличении зазора вследствие износа приблизительно до 1.2 мм виброскорость увеличивается до 40, …, 50 мм/с (рис. 2). Износ осевых сопряжений до полного разрушения антифрикционных колец приводит к увеличению виброскорости лишь до 8, …, 12 мм/с. Величина виброскорости новых насосов составляет 2.5, …, 4.0 мм/с.
Рис. 1.
Кинетика виброскорости, измеренной в вертикальной плоскости в различных точках корпуса с промежутками через 1000 мм: точки 1 и 4 – концы корпуса; точки 2, 3 – середина корпуса; 1 – уровень вибрации т. 1, 2 – вибрация т. 2, 3 – уровень вибрации т. 3, 4 – уровень вибрации т. 4.
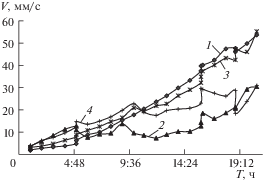
Рис. 2.
Изменение виброскорости насосной секции в зависимости от износа радиальных сопряжений (квадрат – эксперимент; треугольник – эксплуатация).
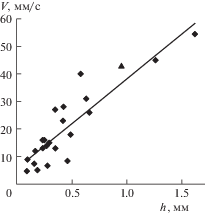
Наиболее часто в процессе изнашивания реализуется асимметричная форма износа ступицы рабочего колеса и практически равномерная форма износа ответной поверхности направляющего аппарата. Такая форма износа радиальных сопряжений обусловлена синхронной прецессией вала [14]. Другой тип – асинхронная прецессия встречается на практике существенно реже. Ей соответствует равномерный износ и ступицы рабочего колеса и отверстия аппарата. Таким образом, форма изгиба и траектория вращения вала насосной секции определяет форму износа радиальных сопряжений. Это необходимо учитывать в расчетах на износостойкость рабочих органов, подшипников электроприводных насосов и при разработке методики испытаний на износ.
Влияние изнашивания на параметрический отказ электроприводных насосов. Насосные секции являются наиболее изнашиваемыми механизмами установки, так как их узлы трения работают в пластовой жидкости, содержащей в той или иной степени твердые частицы (кварц, проппант и др.) и коррозионно-активные элементы (H2S, HCl). Для возникновения отказа наиболее опасен износ подвижных сопряжений (радиальных и осевых), а также “промыв” корпуса направляющего аппарата и газосепаратора. Радиальные подвижные сопряжения рабочих ступеней выполняют двойственную функцию, являясь с одной стороны опорами вала, а с другой стороны – уплотнениями (рис. 3). Во втором случае их износ может привести к параметрическому отказу.
Рис. 3.
Схема насосной сборки: 1 – рабочее колесо, 2 – направляющий аппарат, 3 – осевое сопряжение с большой шайбой, 4 – осевое сопряжение с малой шайбой, 5 – радиальное сопряжение.
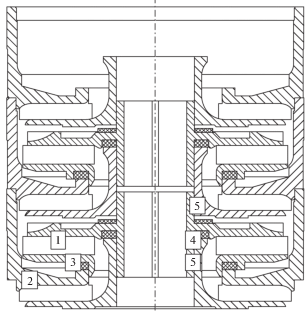
Для исследования деградации НРХ и наступления параметрического отказа вследствие износа подвижных сопряжений были проведены опыты с распространенными типами рабочих ступеней ВННД 5-80 и ВННД 5-125 на стенде ОАО “ОКБ БН КОННАС”, который позволяет регистрировать изменение напора рабочих ступеней с высокой точностью. Частота вращения вала стенда 3000 об/мин (синхронная). НРХ рабочих ступеней приведены к частоте вращения 2910 об/мин.
Номинальный напор рабочих ступеней имеет значение 6.2 м. В опытах использовали сборку, состоящую их семи рабочих ступеней и восьми направляющих аппаратов. Отверстие 5 направляющего аппарата 2 (рис. 3) растачивали под определенный размер зазора в сопряжении 0.45; 0.7; 0.95; 1.35 и 1.75 мм. Начальный диаметральный зазор имел величину 0.25 мм. Предварительно проводили приработку рабочих ступеней в течение 2.5 часа. Для каждой величины зазора строили графики напорно-расходной характеристики (НРХ) рабочей ступени (рис. 4) и рассчитывали утечку q в межступенном уплотнении по формуле [15]
где μ – коэффициент расхода, D – диаметр ступицы рабочего колеса, мм, δ – зазор в щели, мм, ΔP – перепад давлений на щели, м.Рис. 4.
Напорно-расходная характеристика рабочей ступени 5-80: 1 – К.П.Д., 2 – напор, 3 – мощность; сплошная линия – номинальные значения; штриховая линия – значения изношенной НС.
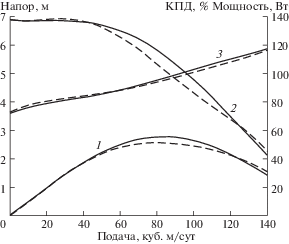
Для расчета коэффициента расхода использовали известную зависимость [15]:
где λ – коэффициент расхода через гладкую щель, который можно принять равным 0.035 [15]; l – длина межступенного уплотнения, мм.Для выбранных типов рабочих ступеней размеры сопряжений имеют значения: l = = 19 мм, D = 20.8 мм. Величину перепада давления ΔP на основании результатов балансовых испытаний центробежных ступеней, проведенных ОАО “ОКБ БН КОННАС” [16], выбрали равной 0.25 от номинального напора, т.е. 1.55 м.
В результате проведенных опытов выявлено, что при изменении расхода от максимального значения до нуля (открытая задвижка – закрытая задвижка) рабочее колесо “всплывает” (рис. 4), т.е. в осевых сопряжениях 3 и 4 (рис. 3) возникают зазоры, падает напор ступени. “Всплытие” рабочего колеса приводит к более интенсивному попаданию абразивных частиц, содержащихся в пластовой жидкости, в область подвижных сопряжений и в зазор между нижним диском рабочего колеса и верхним диском направляющего аппарата. В результате могут интенсифицироваться процессы абразивного износа сопряжений и эрозионного (гидроабразивного) износа направляющего аппарата. При изменении расхода от нуля до максимального значения (закрытая задвижка–открытая задвижка) в диапазоне рабочей части НРХ (рис. 4) рабочее колесо находится в нижнем (рабочем) положении с минимальными значениями зазоров и утечек в осевых сопряжениях. Эти результаты следует учитывать при проведении испытаний насосов, которые следует вести от закрытой задвижки к открытой.
При изготовлении рабочей ступени технологически сложно обеспечить одновременно плотное прилегание антифрикционных шайб рабочего колеса к буртам направляющего аппарата. Вследствие этого в осевом сопряжении 4 (рис. 3) имеется гарантированный зазор. Утечка в межступенном уплотнении ВННД 5-125 без шайбы изменялась в зависимости от зазора от 1.9 до 10.2 м3/сут, для ВННД 5-80 от 1.896 до 10.139 м3/сут. Принято, что условие наступления параметрического отказа – снижение подачи на 20% в номинальном режиме. Для рассматриваемых случаев величина утечки равна ~25 м3/сут и 17 м3/сут, что соответствует диаметральному зазору, равному ~2.3 мм и 1.6 мм. При этом изменение напора в номинальной точке для ВННД 5-80 составило величину 0.04–0.16 м, для ВННД 5-125 составило 0.04–0.14 м.
Обсуждение результатов исследований. Результаты исследований показали, что износ подвижных сопряжений рабочей ступени влияет на динамику электроприводных лопастных насосов – происходит увеличение амплитуды поперечных колебаний корпуса. Изменение виброскорости V в зависимости от износа h можно оценить зависимостью V = 32.6h + 5.5, полученной для насосных секций с номинальной длиной 4000 мм. Для оценки уровня вибрации установки, состоящей из нескольких насосных секций, электродвигателя, других компонентов, эти результаты можно использовать как оценочные. Анализ отказов электроприводных насосов по критерию прочности (разрушение фланцево-болтового соединения), снабженных погружной телеметрией, показал, что уровень вибрации в этих случаях составлял величину 60–100 мм/с. Причем, износ осевых сопряжений в существенно меньшей степени влияет на амплитуду поперечных колебаний корпуса. Можно лишь ожидать усиления крутильных колебаний вала установки при полном износе антифрикционных шайб рабочего колеса.
Износ подвижных сопряжений приводит к увеличению радиальных зазоров в сопряжениях. Вследствие этого увеличиваются утечки через них и происходит деградация НРХ. Показано, что при увеличении диаметральных зазоров до 1.6–2.3 мм возможен параметрический отказ для рабочей ступени производительностью 125 и 85 м3/сут. Необходимо учитывать, что параметрический отказ установки произойдет в случае, если такие величины зазоров будут у каждой рабочей ступени. На практике величина зазоров вследствие износа имеет различные значения по длине насоса.
Выводы. Наибольшее влияние на вероятность возникновения отказа функционирования электроприводного лопастного насоса по критерию прочности оказывает износ радиальных сопряжений, в результате которого увеличивается амплитуда поперечных колебаний корпуса установки.
Вибрация изношенной в процессе эксплуатации установки может увеличиваться в 10–15 раз. Существенное снижение ее величины возможно достичь путем использования износостойких подшипников.
Величина утечки через одинаковые конструктивно радиальные уплотнения разных ступеней радиального типа практически не зависит от производительности ступеней.
Для снижения вероятности параметрического отказа насоса необходимо обеспечить гарантированное прилегание малой шайбы в осевом сопряжении 4 (рис. 3).
Работа выполнена при финансовой поддержке Министерства образования и науки РФ в рамках Федеральной целевой программы “Исследования и разработки по приоритетным направлениям развития научно-технологического комплекса России на 2014–2020 годы”. Соглашение о предоставлении субсидии № 14.607.21.0191 от 26.09.2017 г., проект RFMEFI60717X0191.
Список литературы
ГОСТ 56830-2015 “Нефтяная и газовая промышленность. Установки скважинные электроприводных лопастных насосов. Общие технические требования”. Москва, 2016.
Кудрявцев И.А. Совершенствование технологии добычи нефти в условиях интенсивного выноса мехпримесей (на примере Самотлорского месторождения) // Автореф. дисс. на соиск. уч. ст. к.т.н. Тюмень. ск. ГНГУ, 2004. 23 с.
Уразаков К.Р. и др. Особенности насосной добычи нефти на месторождениях Западной Сибири. М.: ВНИИОЭНГ. 1997. 56 с.
Атнагулов А.Р., Ишемгужин И.Е. Прогнозирование наработки на отказ электроцентробежного насоса перед спуском в скважину и оценка его остаточного ресурса при эксплуатации // Нефтяное хозяйство. 2010. № 6. С. 102–105.
Перельман О.М. и др. Методика опредлеения надежности погружного оборудования и опыт ее применения // Технологии ТЭК. 2005. № 3. С. 66–73.
Пономарев Р.Н. и др. Влияние технологических факторов на аварийность установок погружных центробежных насосов // Нефтяное хозяйство. 2006. № 7. С. 102–104.
Бабаев С.Г. Надежность нефтепромыслового оборудования. М.: Недра. 1987. 264 с.
Пчелинцев Ю.В. Полеты насосов //М.: ОАО “ВНИИОЭНГ” 2003. 392 с.
Ганиев Р.Ф., Низамов Х.Н., Дербуков Е.И. Волновая стабилизация и предупреждение аварий на трубопроводах. М.: Изд-во МГТУ им. Н.Э. Баумана, 1996. 260 с.
Смирнов Н.И., Смирнов Н.Н. Расчетно-экспериментальный метод повышения ресурса УЭЦН // Управление качеством в нефтегазовом комплексе. 2006. № 1. С. 30–34.
Пахаруков Ю.В. и др. Результаты экспериментальных исследований радиальной вибрации при использовании амортизаторов ступеней центробежного электронасоса // Нефтяное хозяйстов. 2011. № 01. С. 99–101.
Бочарников В.Ф., Пахаруков Ю.В. Вибрации и разрушения в погружных центробежных электронасосах для добычи нефти. Тюмень: Тюм ГНГУ. 2005. 141 с.
Кальменс В.Я. Обеспечение вибронадежности роторных машин на основе методов подобия и моделирования. СПб.: СЗПИ. 1992. 373 с.
Смирнов Н.И., Смирнов Н.Н., Мухамадеев К.Г. Исследования и пути повышения ресурса УЭЦН // Химическое и нефтегазовое машиностроение. 2000. № 3. С. 13–16.
Михайлов А.К., Малюшенко В.В. Лопастные насосы. Теория, расчет и конструирование. М.: “Машиностроение”. 1977.
Агеев Ш.Р., Дружинин Е.Ю., Григорян Е.Е. Балансовые испытания ступеней погружных лопастных насосов для добычи нефти // Бурение и нефть. 2016. № 7–8. С. 46–51.
Дополнительные материалы отсутствуют.
Инструменты
Проблемы машиностроения и надежности машин