Проблемы машиностроения и надежности машин, 2019, № 3, стр. 65-73
ВЛИЯНИЕ СТРУКТУРНЫХ ИЗМЕНЕНИЙ НА СОПРОТИВЛЕНИЕ ХРУПКОМУ РАЗРУШЕНИЮ МЕТАЛЛА РЕССОРЫ АВТОМОБИЛЯ КАМАЗ ПРИ ЭКСПЛУАТАЦИИ В УСЛОВИЯХ СЕВЕРА
С. П. Яковлева 1, 2, *, И. И. Буслаева 1, С. Н. Махарова 2, А. И. Левин 1
1 Якутский научный центр СО РАН
г. Якутск, Россия
2 Институт физико-технических проблем Севера им. В.П. Ларионова СО РАН
г. Якутск, Россия
* E-mail: spyakovleva@yandex.ru
Поступила в редакцию 28.12.2017
Принята к публикации 18.02.2019
Аннотация
Для обеспечения надежности элементов конструкций и деталей техники требуется изучение накопления структурных повреждений и их влияния на свойства материалов с учетом условий функционирования. С целью выявления взаимосвязи структурных изменений и сопротивления материала хрупкому разрушению исследованы уровень и вид повреждений структуры, ударная вязкость, микромеханизмы разрушения металла рессоры автомобиля КАМАЗ после эксплуатации в условиях Севера. В статье использованы методы оптической и электронной микроскопии; проведено структурно-статистическое исследование параметров микротвердости и пористости, по которым оценивали структурную поврежденность. Получены новые данные о накоплении усталостных повреждений и их влиянии на сопротивление металла рессоры хрупкому разрушению при работе в зоне холодного климата. Результаты можно использовать для повышения ресурса упругих элементов автотехники.
Потеря несущей способности и разрушение технических объектов обычно обусловлены образованием в материале локальных повреждений структуры, накопление и слияние которых приводит к зарождению и развитию микро- и макротрещин [1–3]. Практически все свойства металлов являются структурно-чувствительными, структурные особенности контролируют и сопротивление разрушению. Это определяет важное научно-прикладное значение изучения накопления структурной поврежденности и ее влияния на свойства металлов и сплавов в различных условиях эксплуатации, в том числе на холоде. Для приобретающих в последнее время особую актуальность вопросов безопасности работы техники и технических систем на Севере и в Арктике [4], фактор низких температур воздуха является одним из основных.
Поскольку в большинстве случаев детали машин испытывают повторные и знакопеременные нагрузки, во избежание перехода усталостных трещин к спонтанному распространению по механизму хрупкого разрушения, одним из основных требований к металлу является сохранение хладостойкости в течение всего периода эксплуатации. Надо отметить, что для деталей автотранспорта, работающего на северных территориях, процессы циклического упрочнения (разупрочнения), накопления усталостных повреждений и их влияния на сопротивление материала хрупкому разрушению остаются малоизученными. Кроме того, недостаточно исследована взаимосвязь структурного состояния и механизмов разрушения для многоцикловой усталости.
В число деталей, лимитирующих надежность грузовых автомобилей при эксплуатации в условиях Якутии, входят элементы подвески, причем в холодное время года долговечность рессор почти в два раза ниже, чем летом [5, 6]. В ранее проведенном исследовании усталостного разрушения рессоры передней подвески грузового автомобиля КАМАЗ [7] были рассмотрены основные виды структурных повреждений материала. Цель настоящей статьи – изучить влияние структурной поврежденности, сформировавшейся в металле листовой рессоры автомобиля КАМАЗ при работе в дорожно-климатических условиях Севера, на сопротивление металла хрупкому разрушению.
Объект, методика и методы исследования. Исследование проведено на претерпевшем усталостное разрушение [7] стандартном коренном листе рессоры передней подвески грузового автомобиля КАМАЗ-44108, что позволило изучить поврежденность, внесенную в материал при реальных условиях эксплуатации; поломка произошла на стадии, соответствующей нормальному износу рессор. Трещина распространилась на расстоянии ≈170 мм от переднего конца рессоры, разделив ее на короткий и длинный фрагменты (размеры рессоры 1675 × 75 × 10 мм). На рис. 1 показана часть длинного фрагмента от излома до участка с центрирующей выдавкой.
Рис. 1.
Общий вид фрагментов разрушившейся половины рессоры и их схематическое изображение: пунктиром показана ориентация образцов при вырезке из зон I, II, III с различным уровнем нагруженности.
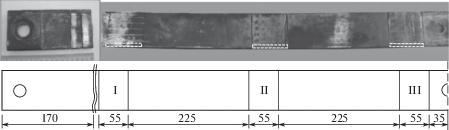
Из длинного фрагмента для изучения структуры, микромеханических свойств и последующего определения ударной вязкости были изготовлены три группы продольных образцов Шарпи (10 × 10 × 55), соответствующих зонам рессоры I, II, III с различным уровнем поврежденности (наиболее нагруженными являются места крепления рессор к мосту и к раме).
В настоящее время нет универсальных методов, позволяющих достаточно объективно и надежно оценить структурную поврежденность металла. Кроме того, поскольку рассматривается материал с уже имеющейся наработкой, то нельзя применить те подходы и критерии, которые используются при проведении испытаний на усталость. Были оценены такие показатели, как микротвердость (для характеризации микроповрежденности) и пористость (для характеризации мезоповрежденности), т.е. были выделены два типа структурной поврежденности, различающихся по масштабному уровню [8].
Микротвердость Н100 замерена на приборе “ПМТ-3” при нагрузке на индентор 0.98 Н (100 гс). Объем выборки для каждой зоны рессоры – около 1000 отпечатков. Статистический анализ проведен в программной среде EXCEL. Также для образцов всех трех групп рассчитывали коэффициент накопления структурной микроповрежденности k в соответствии с методикой, описанной в [9] и использующей массив значений Н100. Характеристики пор определяли на трех площадках по 2.0 × 1.4 мм2, наблюдаемых в оптическом микроскопе “Neophot-32”. По поперечнику поры были условно подразделены на мелкие (до 20 мкм) и крупные (наиболее крупные из наблюдавшихся не превышали 40 мкм); объемная доля мелких пор обозначена как Vм, объемная доля крупных пор – Vк, а общая пористость – Vобщ.
Испытания на ударный изгиб образцов Шарпи выполнены по ГОСТ 9454-78 при +20, –20, –60°С на маятниковом копре Amsler RKP 450 Zwick.
Методом РЭМ проведен анализ поверхностей изломов ударных образцов (использованы приборы ТМ 3030 Hitachi и JEOL JSM-6480LV). Такое исследование позволяет выявить специфику тонкого строения поверхности изломов, доминирующие микромеханизмы разрушения для ответа на вопрос о том, как достигается в материале тот или иной уровень прочности [10, 11].
Результаты и их обсуждение. Химический состав и микроструктура металла рессоры. Металл исследуемой рессоры – кремнистая рессорно-пружинная сталь 60С2 с микроструктурой бейнита, мартенсита, феррита и небольшим количеством остаточного аустенита. К особенностям строения стали следует отнести статистически распределенные округлые образования, обозначенные как пористость, которая наблюдалась при проведенном дополнительно металлографическом анализе двух таких же деталей автомобиля КАМАЗ – рессоры с наработкой и рессоры в состоянии поставки. Наличие пор в последнем случае позволяет предполагать первостепенную роль технологических причин в генезисе пористости материала. Это подтверждается результатами работы [12], в которой происхождение аналогичных образований в стали 60С2 было связано с погрешностями при выплавке, а сами они были определены как графитные включения. Здесь необходимо заметить, что ввиду незначительной прочности графита, его скопления – это по существу пустоты.
Развитие пор в исследуемой рессоре, помимо технологических факторов, обусловлено процессами деформационного порообразования [13, 14], которые могли быть стимулированы твердыми неграфитными включениями (по стехиометрическим расчетам и спектрограммам – оксидами железа). Благоприятным фактором для порообразования является вид напряженного состояния: чем ближе нагружение к одноосному, тем выше скорость роста пор [15]. Состояние металла у верхних и нижних поверхностей рессор близко к одноосному напряженному; это могло способствовать множественному порообразованию. Таким образом, справедливо предполагать, что на момент разрушения в рессоре присутствовали деформационные поры, а также имевшиеся изначально и претерпевшие некоторые изменения при эксплуатации детали “технологические” поры.
Количественный анализ структурной поврежденности металла рессоры. Усталостная прочность определяется влиянием ряда факторов (частота нагружения, концентрация напряжений, асимметрия цикла и т.д.); их интегральное воздействие, по сути, реализуется в изменениях структуры. Исследовали микроповреждения, отражаемые параметром микротвердости, и мезоскопические повреждения в виде пор.
Коэффициент k, предложенный в работе [9], характеризует относительное увеличение плотности микроповрежденности материала при эксплуатации
Вычисленные значения коэффициента k приведены в таблице 1. Там же представлены средние значения микротвердости и характеристики пористости. По результатам работы [7], металл в центре рессоры (зона III) находится на стадии упрочнения, металл зоны I существенно разуплотнен микроповреждениями; поэтому было проведено следующее ранжирование зон по возрастанию поврежденности: зона II, зона III, зона I. Из таблицы 1 видно, что зоне I не соответствует максимальное значение коэффициента k. Это расхождение может иметь следующее объяснение. Известно, что микротвердость отражает сопротивляемость металла вдавливанию индентора, зависящую от характеризующей поврежденность степени деформационного упрочнения (или разупрочнения). Если рассмотреть показатели пористости, то в зоне предразрушения I наблюдается интенсивное зарождение новых пор (для сравнения в зоне III у центра фиксации рессоры объемная доля пор возрастает преимущественно за счет роста их размера). Очевидно, что множественные мелкие поры так же, как и субструктурное разупрочнение, вносят вклад в накопление усталостной поврежденности, обуславливая системное разрыхление стали и меняя структурное состояние зоны I. Это проявляется в изменении характера распределения параметра микротвердости. Проверка статистической гипотезы нормального распределения по критерию χ2 для эмпирического распределения массива Н100 в этой зоне дала значение χ2 = 121 при рассчитанном критическом значении $\chi _{{{\text{к р }}}}^{2}$ = 16, т.е. χ2 > $\chi _{{{\text{к р }}}}^{{\text{2}}}$. Следовательно, для микротвердости металла в состоянии предразрушения отвергается гипотеза нормального распределения. Наличие множественных пор также усложняет корректную оценку параметра k на стадии предразрушения.
Таблица 1.
Коэффициент накопления микроповрежденности, средняя микротвердость и характеристики пористости металла в зонах I, II, III
Параметр | Зоны рессоры | ||
---|---|---|---|
I | II | III | |
k | 1.95 | 1.89 | 2.07 |
Н100, МПа | 3590 | 3720 | 3796 |
Vобщ= Vм + Vк/количество | 1.9/1348 | 1.8/1081 | 2.2/1021 |
Vм/количество | 1.2/1258 | 0.9/980 | 0.8/857 |
Vк/количество | 0.7/90 | 0.9/101 | 1.4/164 |
На искажение закона распределения повреждений, помимо изменений субструктуры и нарушений неразрывности материала в виде микропор, оказывают влияние структурно-фазовые превращения. Авторы [16], изучая усталостные изменения в стали 60ГС2, наблюдали разрушение пакетного мартенсита и мартенситное превращение остаточного аустенита.
Сравнивая данные для зон I и III наибольшей нагруженности рессоры, можно заметить, что при меньших значениях коэффициента k и объемной доли общей пористости Vобщ, разрушение произошло в зоне, характеризующейся: меньшим значением микротвердости (вследствие процессов разупрочнения); отклонением закона распределения микротвердости от закона Гаусса; значительным преобладанием количества мелких пор (на ≈47%); существенно меньшим количеством крупных пор (на ≈45%).
Ударная вязкость усталостно-поврежденного металла рессоры. По результатам испытаний (рис. 2) металл рессоры, несмотря на структурные повреждения, имеет достаточно хорошую вязкость разрушения при +20°C (для сравнения: обычно у стали 60С2 значения KCU+20 ≤ 300 КДж/м2). При снижении температуры ударная вязкость металла зон II и III падает весьма монотонно. Характер температурной зависимости ударной вязкости металла зоны предразрушения I несколько отличен: ее значения резко снижаются при переходе от +20°С к –20°С и далее меняются несущественно, сохраняясь на уровне KCV–60 других зон. Это указывает на бóльшую по сравнению с другими зонами начальную чувствительность зоны I к понижению температуры. С учетом неоднозначной зависимости KCV от микроповрежденности k и того факта, что наиболее значимые различия структур металла трех зон состоят в пористости, правомерно утверждение об определяющем влиянии на сопротивление металла хрупкому разрушению именно мезоповреждений.
Влияние пористости на микромеханизмы и сопротивление металла рессоры хрупкому разрушению. Микрофрактографический анализ позволил выявить некоторые особенности тонкого рельефа изломов, объясняющие характер влияния множественных пор на сопротивление металла рессоры трещинообразованию. В изломах всех ударных образцов были обнаружены вторичные трещины (рис. 3, 4, 5), микростроение которых отражает механизмы и энергоемкость развития разрушения образца в целом. По рис. 3 можно проследить, что они формировались при объединении пор, причем для зоны III этот процесс сопровождался заметной пластической деформацией (вытягиванием пор вплоть до их слияния, деформированностью стенок образующихся полостей). Негативное влияние микроповрежденности, самый высокий уровень которой зафиксирован в зоне III, было нейтрализовано возможностью протекания деформационных процессов в окрестности присутствующих в ней в большом количестве крупных пор. Деформирование материала путем вытягивания пор и при их слиянии прослеживается также в изломах образцов зон I и II, испытанных при –20°С, но заметна меньшая протяженность вторичных трещин (рис. 4). При –60°С их траектория становится более ломаной (рис. 5а, б, в), что указывает на снижение способности материала к деформации и ослабление взаимосвязанности микропроцессов деформирования соседних объемов материала. Это в большей степени характерно для зоны II, что хорошо видно на рис. 5г: поры не носят признаков существенного деформационного роста, а их объединение происходит путем растрескивания перемычек. Гладкость стенок и общий вид возникающих при этом расселин подтверждают хрупкий механизм раскрытия трещин посредством раскалывания кристаллитов. Соответственно, металл зоны II при –60°С продемонстрировал самую низкую ударную вязкость, что может быть связано с меньшим количеством крупных и мелких пор. Строго говоря, требуется рассмотрение НДС и упрочнения металла в зоне пор, необходимо учитывать их форму, ориентацию и т.д. Вопрос об образовании и характере эволюции пор в металлах при внешнем нагружении и их влиянии на свойства является одним из центральных в теории прочности. Результаты настоящей статьи показывают, что свойства металла рессоры в рассмотренных условиях эксплуатации действительно в значительной степени определяются эволюцией микропористости, обусловившей удовлетворительное сопротивление металла рессоры распространению как усталостной, так и хрупких трещин.
Рис. 3.
Объединение микропор (а – участок внутри штриховой окружности) и их развитие в расселины (б, в) в зоне III при –20°C (а, б) и при –60°C (в).
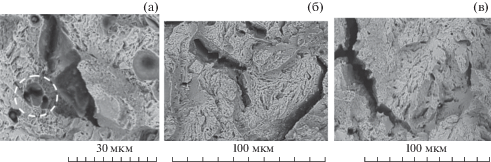
Рис. 5.
Микростроение изломов образцов металла зоны I (а, б) и зоны II (в, г), испытанных при –60°С.
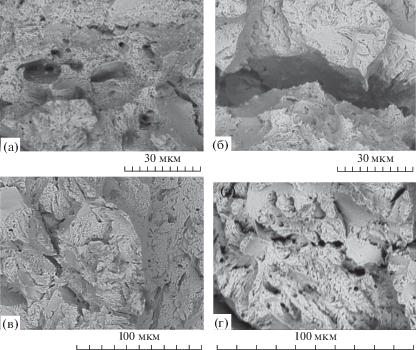
Таким образом, благодаря протеканию микродеформаций как механизма адаптации материала к нагрузкам, особенно в окрестности пор, сталь 60С2 имеет определенный иммунитет к распространению трещин. Учитывая ее применение в упругих элементах, технология изготовления должна обеспечивать высокую релаксационную способность стали, т. е. достаточное сопротивление малым пластическим деформациям с минимизацией пористости.
Выводы. Сравнение результатов структурно-статистического анализа металла зон рессоры с различным уровнем развития поврежденности при эксплуатации в условиях Севера показало, что зона предразрушения при промежуточных значениях коэффициента накопления микроповрежденности и объемной доли мезоповреждений (пор) характеризуется: а) меньшим значением микротвердости (вследствие процессов разупрочнения); б) отклонением закона распределения микротвердости от закона Гаусса; в) значительным преобладанием количества мелких (∅ ≤ 20 мкм) пор; г) меньшим количеством крупных (∅ ≤ 20…40 мкм) пор.
Усталостная поврежденность, накопленная в рессоре до наступления ее эксплуатационного разрушения, не привела к охрупчиванию металла: значения ударной вязкости указывают на удовлетворительное сопротивление стали 60С2 хрупкому разрушению при температурах климатического холода.
Температурная зависимость ударной вязкости металла рессоры в значительной степени определяется мезоповреждениями, механизм влияния которых на сопротивление хрупкому разрушению связан с возможностью протекания деформации в окрестности пор, а также при их росте и слиянии.
Обосновано требование снижения пористости для улучшения релаксационной способности стали 60С2 при применении в упругих элементах.
Конфликт интересов: Авторы заявляют, что у них нет конфликта интересов.
Список литературы
Романов А.Н. Роль структурного состояния в формировании деформационных, прочностных, трибологических и технологических свойств конструкционных материалов // Проблемы машиностроения и надежности машин. 2014. № 3. С. 69–79.
Матвиенко Ю.Г. Моделирование и критерии разрушения в современных проблемах прочности, живучести и безопасности машин // Проблемы машиностроения и надежности машин. 2014. № 3. С. 80–89.
Sangid M.D. The physics of fatigue crack initiation // International Journal of Fatigue. 2013. V. 57. P. 58–72.
Махутов Н.А., Лебедев М.П., Большаков А.М., Гаденин М.М. Научные основы анализа и снижения рисков чрезвычайных ситуаций в районах Сибири и Севера // Арктика: экология и экономика. 2013. № 4 (12). С. 1–12.
Ишков А.М., Кузьминов М.А., Зудов Г.Ю. Теория и практика надежности техники в условиях Севера / Отв. ред. В.П. Ларионов. – Якутск: ЯФ ГУ “Изд-во СО РАН”. 2004. 313 с.
Буслаева И.И., Ишков А.М., Левин А.И. Оценка работоспособности рессор грузовиков в условиях низких климатических температур // Тр. VII Евразийского симпозиума по проблемам прочности материалов и машин для регионов холодного климата. СПб.: Изд-во Политехнич. ун-та. 2014. С. 347–351.
Yakovleva S.P., Buslaeva I.I., Makharova S.N., Levin A.I. Operational Damage to the Structure and Failure of the KAMAZ Truck Spring in the Temperature–Load Conditions of the North // Journal of Machinery Manufacture and Reliability. 2017. V. 46. № 5. P. 488–493.
Волегов П.С., Грибов Д.С., Трусов П.В. Поврежденность и разрушение: обзор // Физическая мезомеханика. 2015. Т. 18. № 3. С. 11–24.
Зорин Е.Е. Разработка метода оперативной диагностики и прогнозирования остаточного ресурса, основанного на регистрации накопленной поврежденности металлом конструкции в процессе длительного нагружения // Изв. МГТУ “МАМИ”. 2013. № 1 (15). Т. 4. С. 142–148.
Клевцов Г.В., Ботвина Л.Р., Клевцова Н.А., Лимарь Л.В. Фрактодиагностика разрушения металлических материалов и конструкций. М.: МИСиС, 2007. 264 с.
Fractography of Modern Engineering Materials: Composites and Metals. V. 2. Ed. by J. E. Masters, Leslie N. Gilbertson: Fredericksburg, Virginia. 1993. 217 p.
Ермаков Б.С., Цупка С.А., Макеева Ю.К. Оценка причин разрушения упругих элементов в условиях Крайнего Севера / Тр. II Всеросс. конф. “Сварка и безопасность” (Якутск, 10‒11 окт. 2017 г.). Якутск: Цумори Пресс. 2017. 443 с.
Карзов Г.П., Марголин Б.З., Швецова В.А. Физико-механическое моделирование процессов разрушения. СПб.: Политехника. 1993. 391 с.
Bhat S., Patibandla R. Metal Fatigue and Basic Theoretical Models: A Review. Alloy Steel – Properties and Use, Dr. E.V. Morales (Ed.). INTECH Open Access Publisher. 2011. P. 203–236.
Saedi N., Ashrafizadeh F., Niroumand B. et al. Damage Mechanism and Modeling ofVoid Nucleation Process in a Ferrite-Martensite Dual Phase Steel // Engineering Fracture Mechanics. 2014. V. 127. P. 97–103.
Сучкова Е.Ю., Ивахин М.П., Громова А.В. и др. Анализ поверхности усталостного разрушения закаленной стали 60ГС2 // Фундаментальные проблемы современного материаловедения. 2005. № 1. С. 68–69.
Дополнительные материалы отсутствуют.
Инструменты
Проблемы машиностроения и надежности машин