Проблемы машиностроения и надежности машин, 2020, № 1, стр. 96-102
ГРУППОВОЙ ПНЕВМОГИДРАВЛИЧЕСКИЙ ПРИВОД СИЛОВЫХ СТАНЦИЙ АВТОМАТИЧЕСКИХ ЛИНИЙ УПАКОВКИ ТИПА “FORM-FILL-SEAL”
Б. Л. Саламандра *
Институт машиноведения им. А.А. Благонравова РАН
г. Москва, Россия
* E-mail: salamandra@recuper.ru
Поступила в редакцию 26.06.2018
Принята к публикации 25.10.2019
Аннотация
В статье приводятся особенности выполнения силовых технологических операций на автоматических линиях фасовки и упаковки жидких и полужидких продуктов. Показано, что индивидуальные приводы силовых станций линии можно без ущерба для производительности заменить одним групповым пневмогидравлическим приводом. При этом можно существенно улучшить динамику процесса вырубки готовых изделий. Приводится схема пневмогидроцилиндра, в котором за счет введения дополнительной загерметизированной зоны высокого давления, соединенной с гидрокамерой регулируемым дросселем и обратным клапаном, можно изменять скорость силового хода инструмента вплоть до ползучей.
В разработках автоматических линий (АЛ) все шире применяется новая элементная база в области приводов, систем управления с программируемыми контроллерами, датчиков физических, механических величин и т.д. Эта элементная база определяет мехатронную структуру автоматических линий. Она выводит на более высокий научно-технический уровень создаваемое оборудование, повышая его надежность и существенно (в 1.5–2 раза) уменьшая стоимость. Примером такой линии является автоматическая линия для фасовки и упаковки жидких и полужидких продуктов [1, 2].
Технологическая схема линии приведена на рис. 1.
Рис 1.
Схема автоматической линии фасовки и упаковки продуктов: 1 – рулон полимерной корпусной ленты; 2 – нагреватель; 3 – станция формовки емкостей; 4 – дозатор; 5 – рулон покровной ленты с напечатанной этикеткой; 6 – станция термосварки корпусной и покровной лент; 7 – станция вырубки готовых изделий.
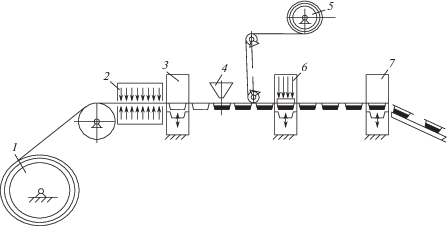
Корпусной материал 1 (термопластичный полимер – полистирол, полипропилен и т.п.) проходит через нагреватель 2, где доводится до высокопластичного состояния, и поступает на станцию формовки 3 емкостей. Далее, с помощью объемного дозатора 4 емкости заполняются продуктом, накрываются покровным материалом 5 (алюминиевой фольгой, микспапом, полимерной пленкой) с напечатанной этикеткой с одной стороны и слоем термолака с другой и поступают на станцию герметизации 6 емкостей путем термосварки корпусного и покровного материалов. Затем лента с заполненными и запечатанными емкостями поступает на станцию 7, оснащенную штампом для вырубки отдельных емкостей.
Рассматриваемая АЛ относится к классу высокопроизводительных машин-автоматов. Она работает в старт-стопном режиме с циклом в 2.5–4 с. Перемещение лент 1 и 5 на требуемый шаг 50–110 мм производится за время 0.6–0.8 с. При этом нагреватель 2 и силовые станции 4, 6 и 7 открыты. Как только заданный шаг ленты будет отработан, о чем свидетельствует сигнал датчика положения, установленного на пневмоприводе лент, контроллер выдает сигнал на закрытие нагревателя и силовых станций. Все оставшееся время цикла на закрытых станциях по локальным подпрограммам управления выполняются требуемые технологические операции. Каждая из этих операций отличается своими особенностями: 1) операция формовки емкостей на станции 4 является лимитирующей по времени, поскольку она включает несколько последовательных этапов: предварительную вытяжку разогретого полимера механическими пуансонами для усиления (увеличения толщины) донышка емкости; раздувку – для формообразования емкости и, наконец, некоторую выдержку времени – для отбора тепла полимера, контактирующего с холодной поверхностью прессформы, что способствует стабилизации формы емкости; 2) операция термосварки корпусного и покровного материалов выполняется на станции 6 при температуре 160–200°C (полистирол + микспап), усилии смыкания ≈11 кН и выдержке 0.8–1 с. Исследования показали, что качественный ленточный шов (высокая степень герметизации при легком вскрытии емкости без разрыва покровного материала) достигается на различных тепловых режимах. При этом уменьшение температуры сварки компенсируется увеличением времени выдержки при постоянном удельном давлении смыкания; 3) операция вырубки заполненных емкостей на станции 7 является самой быстрой, но отличается неблагоприятной динамикой протекания процесса. Дело в том, что при использовании пневмопривода после прохождения высеченным пуансоном ≈0.5 толщины листа происходит срез материала, нагрузка резко падает, и выходное звено с пуансонами, находясь под действием воздуха, как сильной пружины, “выстреливает”. Накопленная в этой пружине энергия гасится ударом всей подвижной массы на внутреннем или наружном упоре. Этот недостаток существенно увеличивает динамические нагрузки на конструкцию в целом и, наряду с повышенным шумом на производстве, приводит к преждевременному разрушению опорных и уплотнительных элементов. Дросселирование выходных каналов приводного пневмоцилиндра не решает данной задачи, а встраивание существующих гидроамортизаторов существенно усложняет конструкцию силовой станции.
Поскольку производительность линии определяется временем лимитирующей технологической операции, в данном случае формовкой емкостей, можно без ущерба для производительности несколько увеличить время выполнения сварки и вырубки, и производить открытие всех силовых станций одновременно после выполнения операции формовки. Некоторое увеличение времени выдержки материалов под давлением при термосварке в соответствии со свойством 2 можно скомпенсировать понижением температуры, что в свою очередь увеличит ресурс работы нагревателя.
В настоящее время каждая силовая станция имеет свой индивидуальный управляемый привод, реализованный в виде рычажного механизма – мультипликатора с пневмоцилиндром [3]. Одновременное включение силовых станций по сигналу датчика перемещения ленты и одновременное их выключение по завершении операции формовки позволяет отказаться от индивидуальных приводов, заменив их одним групповым приводом.
Групповой привод из трех гидроцилиндров, питаемых от одного гидропневмоусилителя, является одним из вариантов решения поставленной задачи. Пример такого привода, изготавливаемого фирмой Tox-Pressotechnic [4] (Германия) показан на рис. 2.
Прямой холостой и силовой ход рабочих цилиндров 1 (их может быть до 6) осуществляется подачей масла в поршневую полость цилиндра по шлангам высокого давления от пневмогидроусилителя 2. Обратный ход – подачей сжатого воздуха в штоковую полость цилиндра. Рабочий объем масла, размещаемый в пневмогидроусилителе, рассчитывается, исходя из требуемых перемещений рабочих цилиндров и диаметров их поршней. Перспективность использования подобного группового привода в рассматриваемой автоматической линии обусловлена следующими обстоятельствами: а) пневмогидроцилиндры не имеют открытой гидравлики, гидробака и гидронасоса высокого давления, что позволяет применять их в автоматах пищевого производства; б) объем масла, резервируемый для выполнения силового хода в пневмогидроусилителе, минимален, так как станции формовки и сварки работают как тиски, обеспечивая необходимое удельное давление на материал (т.е. силовой ход практически нулевой), а на станции вырубки силовой ход необходим всего лишь в пределах 3–5 мм; в) в связи с тем, что пневмогидроцилиндры имеют широкий диапазон по развиваемому усилию, можно использовать один типоразмер привода для линий разных моделей с различной площадью формования, обеспечивая требуемое удельное давление на материалы регулировкой входного давления пневмомагистрали усилительного канала пневмогидроусилителя; г) наряду с очевидными экономическими преимуществами в уменьшении трудоемкости изготовления, металлоемкости, росте унификации узлов и сокращении срока изготовления машин, переход на пневмогидравлический привод позволяет существенно улучшить технологический процесс вырубки готовых изделий. Замена рабочей среды – упругого воздуха на несжимаемую жидкость при больших коэффициентах усиления пневмогидросистемы существенно уменьшает скачки скорости пуансонов при вырубных технологических операциях. Неравномерность движения инструмента при существенно нелинейной характеристике силы резания можно практически полностью устранить путем организации в гидрокамере высокого давления усилителя специальной зоны, перетекание масла в которую осуществляется через дроссель с обратным клапаном. В результате при неизменных больших скоростях холостого хода можно изменять скорость силового хода вплоть до ползучей.
Пневмогидроцилиндры, при всем своем разнообразии [6–8] по расположению рабочего цилиндра относительно усилительного, обладают одним общим конструктивным свойством: всегда при выполнении силового хода поршень рабочего цилиндра и шток усилительного находятся в замкнутой гидрокамере и взаимодействуют через несжимаемую жидкость. Давление, которое развивается в гидрокамере, пропорционально отношению эффективных площадей поршня и штока усилительного цилиндра, которое определяет коэффициент усиления пневмогидроцилиндра и достигает величины 25 и более. В результате усилие на выходном звене рабочего цилиндра может достигать десятки тонн при давлении воздуха 6 кг/см2 [4].
На рис. 3а показана традиционная схема пневмогидроцилиндра, в котором силовой и усилительный цилиндры расположены соосно в одном корпусе. Точечным муаром показана зона, заполненная маслом. В исходном положении усилительный цилиндр, образованный поршнем 1 и штоком 2, находится в крайнем положении.
Рис 3.
(а) – схема традиционного пневмогидроцилиндра; (б), (в), (г) – схемы пневмогидроцилиндра с возможностью регулировки скорости силового хода в разных фазах движения: при быстром ходе вверх (б); при силовом ходе вверх (в); при возврате в исходное положение (г).
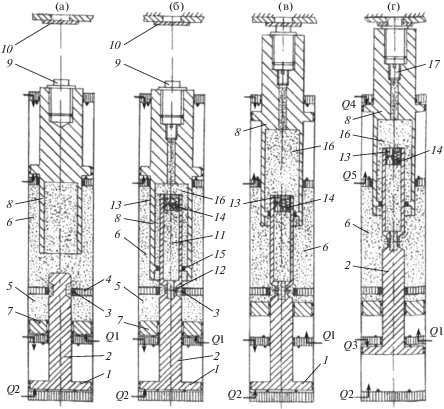
При этом канавка на штоке 2 образует зазор между штоком и уплотнением 3, установленным в перегородке 4. Зазор соединяет камеры низкого 5 и высокого 6 давления. При подаче сжатого воздуха в канал Q1 перемещается поршень 7 холостого хода, выдавливая масло через зазор из камеры 5 в камеру 6, тем самым выдвигая двухсторонний шток 8 рабочего цилиндра, несущего вырубной инструмент 9. Поскольку нагрузка отсутствует, происходит быстрый холостой ход вперед под действием давления воздуха в канале Q1. При достижении инструментом 9 обрабатываемой детали 10, что фиксируется датчиком изменения давления в канале Q1 или датчиком положения (на схеме датчики не показаны), будет подано давление воздуха в канал Q2, воздействующий на поршень 1 усилительного цилиндра. При перемещении поршня 1 его шток 2 перекроет зазор в перегородке 4, и в загерметизированной гидрокамере 6 будет возрастать давление. Максимальное давление, которое может быть достигнуто pmax = kpв, где pв – давление сжатого воздуха, а k – коэффициент усиления, равный отношению площади S1 поршня 1 к площади S2 поперечного сечения штока 2. Очевидно, что в рассматриваемой традиционной схеме нет возможности регулировать скорость силового хода, так как она определяется только взаимодействием инструмента 9 и обрабатываемой детали 10.
На рис. 3б, в, г в разных фазах движения показана новая схема пневмогидроцилиндра [5], в котором регулирование скорости силового хода осуществляется за счет разделения камеры высокого давления на две зоны, перетекание масла между которыми происходит через регулируемый дроссель с обратным клапаном. Для этого шток 2 усилительного цилиндра выполняется полым – снабженным внутренним отверстием 11, с одной стороны соединенным с камерой 6 через радиальные отверстия 12, размещенные в канавке штока 2, а с другой стороны – со стороны торца штока 2 закрытым регулируемым дросселем 13 с обратным клапаном 14. В двухстороннем штоке 8 рабочего цилиндра также выполняется сквозное отверстие, в котором устанавливается манжета 15, контактирующая с наружной поверхностью штока 2. В результате в камере 6 высокого давления выделяется закрытая зона 16.
В исходном положении (рис. 3б) при подаче давления сжатого воздуха в канал Q1 поршень 7 холостого хода, продавливая масло через зазор уплотнения 3, обеспечит в камере 6 и, соответственно, в отверстии 11 большее давление, чем в зоне 16. В результате клапан 14 откроется, и рабочий цилиндр совершит быстрый холостой ход вперед до контакта инструмента 9 с заготовкой 10 (рис. 3в), после чего, как и в традиционной схеме, производится переключение на силовой ход.
При подаче давления сжатого воздуха в канал Q2 (рис. 3г) усилительного цилиндра шток 2, перемещаясь вверх, уплотнением 3 загерметизирует камеру 6 высокого давления. Давление начнет возрастать, но всегда в силу действия силы со стороны усилительного цилиндра давление в зоне 16 будет несколько выше, чем в камере 6. Клапан 14 будет закрыт, а скорость движения инструмента 9 определится, в основном, гидросопротивлением дросселя 13. После вырубки изделия, когда усилие резания резко упадет, ситуация не изменится; обратный клапан 14 остается закрытым, и двухсторонний шток 8 рабочего цилиндра без удара, на малой скорости “сядет” на внутренний или наружный упор.
Важно отметить, что при любом относительном движении пневмоцилиндров, точнее их штоков 2 и 8, находящихся в гидрокамере, должна происходить перетечка масла между гидрозонами 6 и 16. Объем перетекаемой жидкости определяется отношением эффективных площадей штоков 2 и 8. При закрытом обратном клапане 14 и полностью затянутом дросселе 13 система лишается подвижности, и пневмогидроцилиндр “запирается”. Поэтому регулировкой дросселя можно добиться сколь угодно малой скорости силового хода.
Для выполнения обратного хода (рис. 3г) каналы Q1 и Q2 соединяем с атмосферой, а сжатый воздух подаем в каналы Q3 усилительного пневмоцилиндра и Q4 рабочего. При этом давление в гидрозоне 16 будет меньше, чем в 6, обратный клапан 14 откроется, и произойдет быстрый обратный ход в исходное положение (рис. 3б). Скорость быстрого обратного хода можно регулировать дросселированием выходного канала Q5 рабочего цилиндра.
Для возможности регулировки дросселя 13 в такой закрытой пневмогидросистеме осевое отверстие в двухстороннем штоке 8 рабочего цилиндра выполняется сквозным и со стороны рабочего инструмента заглушается пробкой 17. Это отверстие используется также наряду с другими отверстиями (на схеме не показаны) для заливки рабочей среды и удаления воздуха. Для регулировки дросселя пневмогидроцилиндр выводится в положение, в котором торец штока 2 наиболее близок к заглушенному отверстию, из штока 8 выворачивается насадка, несущая инструмент 9, удаляется заглушка 17, и через открытое отверстие стандартным длинномерным инструментом, например, отверткой, можно повернуть регулируемый элемент дросселя.
На рис. 3б, в, г дроссель 13 и обратный клапан 14 условно разделены и размещены в торце штока 8 усилительного цилиндра.
На самом деле разместить там эти два элемента достаточно непросто, так как при проектировании пневмогидроусилителя стремятся сделать диаметр штока минимальным для увеличения коэффициента усиления системы. Эту задачу можно решить, выполнив дроссель на элементах обратного клапана так, например, как показано на рис. 4. Здесь гильза 1 клапана с отверстием 2, которое перекрывается шариком 3 под действием пружины 4, запрессовывается в отверстие 5 штока. Гильза 1 на своей наружной поверхности имеет две или три продольные канавки 6.
Пружина 4 своим вторым концом опирается на торец резьбовой втулки 7, в котором выполнено сквозное отверстие 8 и профильное отверстие 9, например, внутренний шестигранник, для возможности поворота втулки. Таким образом, параллельно обратному клапану на его элементах выполнен канал перетечки жидкости, состоящий из отверстия 8, межторцевого зазора 10 и продольных канавок 6. При повороте резьбовой втулки 7 будет изменяться межторцевой зазор 10 и, соответственно, гидравлическое сопротивление дросселя.
Список литературы
Корендясев А.И. Фасовочно-упаковочная автоматическая линия – для малых форм хозяйствования // Ж. Наука – производству. 1998. № 10 (12). С. 22.
Саламандра Б.Л., Тывес Л.И., Саламандра К.Б. Новые технологические решения в построении упаковочных автоматов типа Form-Fill-Seal (FFS). Справочник // Инженерный журнал. 2009. № 1. С. 22.
Саламандра Б.Л., Тывес Л.И., Саламандра К.Б., Корендясев Г.К. Некоторые проблемы создания современных автоматических линий на примере линии упаковки типа “формовка–фасовка–укупорка–вырубка” // Ж. Проблемы машиностроения и автоматизации. 2013. № 3. С. 71.
https://de.tox-pressotechnic.com дата обращения 28.05.2018
Саламандра Б.Л. Пневмогидроцилиндр. РФ Патент 2643278, 2018.
Schuster G. Hydraulischer Druckubersetzer. DE Пaтeнт 4221638, 1992.
Todd M. Brieschke. Oil intensifier cylinder. US Пaтeнт 5526644, 1996.
Todd M. Brieschke. Air/oil intensifier having multiple sensors. US Пaтeнт 5865029, 1999.
Дополнительные материалы отсутствуют.
Инструменты
Проблемы машиностроения и надежности машин