Проблемы машиностроения и надежности машин, 2020, № 3, стр. 56-64
ВЛИЯНИЕ ПРОЧНОСТИ КОНСТРУКЦИОННЫХ МАТЕРИАЛОВ КОРПУСОВ ТВЕРДОТОПЛИВНЫХ ЗАРЯДОВ НА ЭФФЕКТИВНОСТЬ РАБОТЫ ПУЛЬСИРУЮЩИХ ВЗРЫВНЫХ УСТРОЙСТВ
В. О. Соловьев 1, *, Г. В. Москвитин 1, Н. М. Овчинников 1, М. С. Кельнер 1, М. С. Пугачев 1
1 Институт машиноведения им. А.А. Благонравова РАН
Москва, Россия
* E-mail: solovievvo@yandex.ru
Поступила в редакцию 12.03.2019
Принята к публикации 31.01.2020
Аннотация
В статье приводится анализ результатов натурных экспериментальных исследований по изучению влияния прочности конструкционных материалов тонкостенных корпусов сосредоточенных зарядов взрывчатых веществ на эффективность работы пульсирующих взрывных устройств различного целевого назначения.
В работе [1, 2] было показано, что по термодинамическим показателям режим детонационного горения топливной смеси более выгоден, чем режим дефлаграционного горения. В современных условиях, когда энергетические возможности химических топлив практически достигли своего предела, разработчики все чаще ищут новые подходы и пути повышения КПД и мощности энергосиловых установок.
В отличие от режима детонационного горения газовых смесей, детонация твердых взрывчатых веществ (ВВ) является устойчивым процессом и надежно протекает в любых средах и зарядах различной формы. С увеличением плотности ВВ возрастает скорость детонации, а, следовательно, мощность заряда и плотность выделяемой энергии, термодинамический КПД, т.е. возрастает эффективность пульсирующих взрывных устройств (ПВУ) и существенно расширяется область их применения.
Твердотопливные ПВУ – класс машин, включающий в себя автоматическую систему подачи и инициирования зарядов ВВ и совершающих полезную работу серией последовательных взрывов. К таким машинам относятся: устройства и комплексы для взрывобурения горных пород различной крепости; устройства и станки для обработки материалов или получения материалов с новыми физико-механическими свойствами; детонационные ракетные двигатели различного целевого назначения; ударно-волновые и акустические генераторы для воздействия на биообъекты.
Проведенные ранее авторами теоретические и экспериментальные исследования подтвердили эффективность применения взрывореактивных установок (ВУ) для бурения горных пород и твердотопливных детонационных ракетных двигателей (ТДРД) при оснащении их надежной системой подачи зарядов ВВ в рабочую зону с частотой до 1000 Гц и специальными высокобезопасными средствами их инициирования [3–5].
Известны созданные ранее опытные образцы, оснащенные одноразовыми отражателями и кассетами, защищенные патентами [6–8]:
1. Твердотопливные детонационные ракетные двигатели, тяга которых создается серией последовательных взрывов зарядов ВВ, размещенных в одноразовых отражателях (кассетах). После каждого взрыва очередной отражатель формирует продукты взрыва (ПВ) в направленный поток, при этом сам отражатель частично разрушается и отбрасывается от изделия [6, 7].
2. Взрывореактивные установки – безоткатные устройства, состоящие из набора одноразовых кассет, каждая из которых оснащена: отражателями с забойными зарядами ВВ (разрушающие породу на забое) и отражателями с прижимными зарядами ВВ (прижимающие изделие к забою и расширяющие скважину), при этом после направленного истечения ПВ из очередной кассеты разрушенные элементы кассеты и шлам выбрасываются из скважины ударными волнами и расширяющимися газами [4, 8].
Проведенная авторами оценка массогабаритных характеристик ПВУ показала, что для изделий калибром более 250 мм целесообразно использовать неразрушаемые многоразовые отражатели, однако, при этом возникают серьезные проблемы, связанные с живучестью конструкций, прежде всего с отражателями, находящимися в непосредственном контакте с инициируемыми зарядами ВВ.
В работе [9] была предложена концепция защиты стальных отражателей энергоаккумулирующими материалами от разрушающего воздействия ПВ при инициировании зарядов твердых ВВ на их поверхности, и приведены результаты экспериментальных исследований. В экспериментах использовались цилиндрические заряды (диаметр заряда равен их высоте) с плотностью заряжания ВВ ρ = 103 кг/м3. Заряды имели массу 6 × 10–3, 12 × 10–3 и 18 × 10–3 кг и оснащались скальным аммонитом № 3, тротилом, гексогеном, которые формовались в тонкостенных оболочках из алюминиевой фольги для исключения влияния корпуса заряда ВВ на эффект расширения ПВ на поверхности отражателя и фактор их защиты.
Использование многоразовых отражателей требует наличия высокочастотных механических систем для раздельной подачи зарядов ВВ в рабочую зону, что накладывает условия на прочностные свойства корпусов для защиты зарядов ВВ от повреждений.
Несущая способность тонкостенных корпусов для зарядов ВВ зависит не только от геометрических характеристик самих корпусов (диаметра, их высоты и толщины), мощности заряда, но и от прочностных свойств конструкционных материалов, используемых для изготовления этих корпусов.
Настоящая статья посвящена вопросам экспериментального исследования влияния величин временного сопротивления на растяжение σв конструкционных материалов корпусов твердотопливных зарядов ПВУ различного целевого назначения, изготовленных из сталей марок 3, 20, 45, 30ХГСА, 30ХГСА (закаленная), 65Г, 65Г (закаленная), а также бронзы марки БрОЦ4-3.
Для уточнения величин временного сопротивления конструкционных материалов прутков, из которых изготавливались корпуса зарядов, были проведены испытания по ГОСТ 1497-84 на сервогидравлической машине фирмы “Shimadzu”. При испытаниях использовались образцы, показанные на рис. 1.
Нагружение осуществлялось с постоянной скоростью перемещения активного захвата, которая составляла 0.02 мм/с.
Образцы устанавливались в гидравлические захваты с давлением 15 МПа. Удлинение рабочей части образцов измерялось экстензометром с базой 25 мм (рис. 1).
В процессе испытаний записывались диаграммы в координатах нагрузка – перемещение активного захвата, удлинение образца. Фотография разрушенных образцов представлена на рис. 2.
Рис. 2.
Образцы прутков, после испытаний: 1 – Сталь 65Г (закаленная); 2 – Сталь 65Г; 3 – Сталь 30ХГСА (закаленная); 4 – Сталь 30ХГСА; 5 – Сталь 45; 6 – Сталь 20; 7 – Сталь 3; 8 – Бронза БрОЦ4-3.
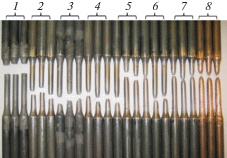
По времени возрастания и времени воздействия нагрузки на материалы выделяют три режима нагружения: статическое, квазистатическое и динамическое [10, 11]. В свою очередь динамическое нагружение можно разделить на слабое и сильное. Под динамическими нагрузками (tн max < 2L/c, αpmax < pГ) следует понимать слабое динамическое нагружение. Под сильной динамической нагрузкой понимается ударноволновое нагружение – предельный случай динамического нагружения (tн max < 2L/c, αpmax ≥ pГ), где tн max – время возрастания нагрузки до максимального значения, с; L – характерный размер элемента конструкции, м; с – скорость звука в твердом теле, м/с; α – коэффициент согласования, зависящий от особенностей нагружения и вида нагруженного состояния; pГ – упругий предел на ударной адиабате Гюгонио в ударной волне при одноосном деформированном состоянии, Па; pmax – амплитуда (или максимальное значение внешнего поверхностного давления), Па.
Для исследования слабых динамических нагружений применяется метод составных стержней Гопкинсона [10, 12–15], в том числе и для образцов, нагреваемых до 500°С, при которых прочностные свойства конструкционных сталей падают более чем в 2 раза [16].
На материалы и конструкции при ударноволновом нагружении воздействуют ударные волны и волны разрежения. Ударные волны принято описывать законами сохранения массы, импульса и энергии
где ${{D}_{{{\text{УВ}}}}}$ – скорость ударной волны, м/с; ${{\rho }_{0}}$, $\rho $ – плотность ПВ перед и за фронтом ударной волны, кг/м3; V0, V – удельный объем ПВ перед и за фронтом ударной волны, м3/кг; p0, p – давление ПВ перед и за фронтом ударной волны, Па; u0, u – массовая скорость ПВ перед и за фронтом ударной волны, м/с; E0, E – удельная энергия ВВ перед и за фронтом ударной волны, Дж/кг.Для давлений до нескольких десятков гигапаскалей уравнение состояния Ми-Грюнайзена записывается в виде
Для практических целей функцию ${{p}_{x}}({\rho })$ можно представить в виде
(3)
${{p}_{x}}(\rho ) = \frac{{{{\rho }_{0}}c_{0}^{2}}}{n}\left[ {{{{\left( {\frac{\rho }{{{{\rho }_{0}}}}} \right)}}^{n}} - 1} \right] = \frac{{{{\rho }_{0}}c_{0}^{2}}}{n}(\rho _{{{\text{сж}}}}^{n} - 1).$Упругая энергия Ex(ρ) зависит от относительного сжатия δсж = ρ/ρ0 как
(4)
${{E}_{x}}\left( {{{{\delta }}_{{{\text{сж}}}}}} \right) = \frac{{с_{0}^{2}}}{{n{{{\delta }}_{{{\text{сж}}}}}}}\left[ {1 - \frac{{n{{{\delta }}_{{{\text{сж}}}}}}}{{n - 1}} + \frac{{{\delta }_{{{\text{сж}}}}^{n}}}{{n - 1}}} \right].$Из уравнений (2)–(4) можно получить уравнение ударной адиабаты в явном виде
(5)
${{p}_{{\text{Г}}}} = \frac{{{{\rho }_{0}}с_{0}^{2}}}{n}\frac{{\left( {{{h}_{{\text{Г}}}} - \frac{{n + 1}}{{n - 1}}} \right)\delta _{{{\text{сж}}}}^{n} + \frac{{2n{{\delta }_{{{\text{сж}}}}}}}{{n - 1}} - \left( {{{h}_{{\text{Г}}}} + 1} \right)}}{{{{h}_{{\text{Г}}}} - {{\delta }_{{{\text{сж}}}}}}},$Я.Б. Зельдович предложил учитывать условия образования ударных волн разрежения, т.е. состояние вблизи критической точки фазового перехода в жидкости, где стираются различия между паром и жидкостью. Причиной образования ударных волн разрежения является фазовый переход первого рода при ударном сжатии, сопровождающийся перестройкой кристаллической решетки с уменьшением ее объема [10].
Данная область является малоизученной и требует новых уравнений состояния ВВ для последующего составления уравнений состояния нагружаемых образцов с целью уточнения расчетных моделей поведения конструкционных материалов при ударноволновом нагружении. Известны работы, проведенные в России и за рубежом по изучению деформации и разрушения металлических оболочек, оснащенных зарядами ВВ [17, 18].
Существующие расчетно-экспериментальные методы базируются на процессах стационарной детонации для определения режимов нагружения и разрушения образцов. В связи с этим в настоящее время задачи оценки прочности и живучести элементов ПВУ, подверженных ударноволновому нагружению, при нестационарных режимах детонации решаются на основе экспериментальных исследований.
Используемый нами малый оболочечный заряд разработан на основе концепции специального электродетонатора (СЭД), предполагающий переходные режимы формирования пересжатой детонации [5].
Нас интересовали процессы развития детонации малых зарядов ВВ в тонкостенных металлических корпусах толщиной до 3 мм с каналами переменного сечения диаметром от 1 до 6 мм, инициируемых электропроводным пленочным мостиком.
Для понимания процесса развития детонации в каналах малого диаметра при электрическом инициировании ТЭНа пленочным мостиком [5] были проведены оценочные эксперименты на одноканальных образцах, наружные габариты которых имели диаметр 8 мм и длину 30 мм с диаметром канала 3.2 мм и длиной канала 25 мм, оснащенных ТЭН массой 2.4 × 10–4 кг с плотностью заряжания 1200 кг/м3. Характерный разрушенный ПВ образец испытуемой конструкции из Ст45 представлен на рис. 3.
Рис. 3.
(а) – вид одноканального образца после взрыва; (б) – увеличенный фрагмент разрушенного образца с застывшим расплавом металла.
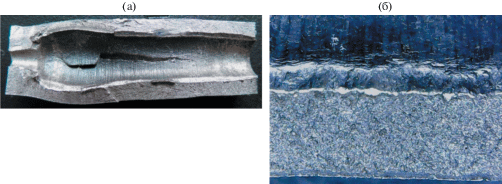
Из рис. 3а видно, что образующуюся при детонации заряда ТЭН внутреннюю полость образца можно представить в виде сопряженных геометрических фигур: бочкообразной и усеченного конуса. Видно, что раздутие канала происходило по-разному. Так, в начале бочкообразной полости диаметр увеличился в 1.8 раза, в ее середине – в 2 раза, в начале конусообразной – в 1.5 раза, а на выходе – в 1.4 раза.
Цилиндрический канал диаметром 1 мм, предназначенный для подведения электрических проводов с пленочным электропроводным мостиком к заряду ТЭНа, инициируемого взрывной машинкой ПИВ-100М, был деформирован ПВ и приобрел конусообразную форму.
Образовавшаяся после детонации полость конусообразной формы свидетельствует о том, что процесс развивался в режиме пересжатой детонации. На поверхности канала четко видны кольцеобразные, характерные для детонации, следы. Об очень высокой температуре процесса свидетельствуют застывшие капли расплавленного металла (рис. 3б). При различной плотности ТЭН температура в детонационной волне для установившегося режима детонации лежит в диапазоне 3400–4400 K [17, 19, 20].
В качестве заряда ВВ нами использовались СЭД [5], корпуса которых изготавливались из указанных ранее конструкционных материалов.
Экспериментальный стенд представлял собой массивную стальную плиту (подложку), на которую устанавливался свинцовый цилиндр диаметром 40 мм и высотой 20 мм, на плоский торец которого пластилином крепился СЭД, инициируемый взрывной машинкой ПИВ-100М (рис. 4а).
Рис. 4.
Стенды для изучения расширения ПВ на поверхности отражателей: (а) – для зарядов ВВ, размещенных в жестких корпусах (1 – жесткий корпус-отражатель; 2 – инициирующий заряд ВВ; 3 – пластилин; 4 – пробка герметизирующая; 5 – изолятор; 6 – электрические провода; 7 – основной заряд ВВ); (б) – для безкорпусных зарядов ВВ (1 – электрический детонатор ЭД-202; 2 – корпус из алюминиевой фольги; 3 – основной заряд ВВ 4 – пластилин; 5 – сборка из тонких свинцовых пластин; 6 – отражатель стальной; 7 – стол).
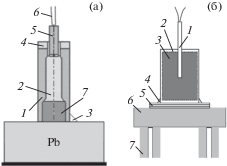
Следует отметить, что основная масса заряда СЭД (рис. 4а) имеет форму, соответствующую форме заряда, в тонкостенной оболочке из алюминиевой фольги, результаты исследований которого изложены в работе [9] (рис. 4б), диаметр основного заряда равен его высоте. СЭД оснащался ТЭН со средней плотностью заряжания 1.3 × 103 кг/м3.
Характерный вид полостей, образующихся в свинцовых цилиндрах в результате воздействия ПВ СЭД, а также фрагменты корпусов детонаторов после их срабатывания показаны на рис. 5.
Рис. 5.
Характерный вид полостей, образующихся в свинцовых цилиндрах в результате воздействия ПВ СЭД, изготовленных из различных марок стали, и их остатки.
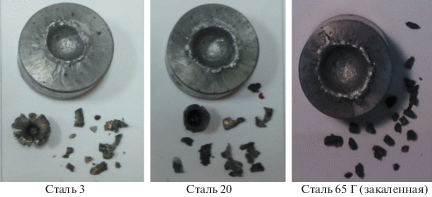
Анализ полученных экспериментальных результатов показал, что после подрыва СЭД на контактной поверхности свинцовых цилиндров, ПВ образуют полости, имеющие форму шарового или эллиптического сегмента. Было установлено, что на форму образуемой полости прямое влияние оказывает временное сопротивление материала корпуса СЭД.
По результатам экспериментов были построены графики – рис. 6, 7 и получены аналитические зависимости (6)–(8). На рис. 6 наблюдается точка максимума соотношения d/h при σв = 520 МПа, являющаяся точкой стыка двух функций. Из приведенного на рис. 6 графика видно, что при значении σв ≈ 520 МПа наблюдается разрыв функции d/h = f(σв), где d – диаметр полости, мм; h – глубина полости, мм; σв – временное сопротивление материала корпуса, МПа. Правая и левая ветви являются областями компромиссов противоречий двух факторов, а именно: развития процесса детонации (давления и температуры в ударной волне) и временного сопротивления на растяжение σв конструкционных материалов корпусов заряда ВВ.
Рис. 7.
Зависимость безразмерной величины σсV/Em от временного сопротивления σв материала корпуса СЭД.
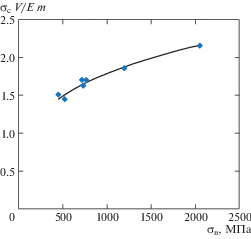
Представленная здесь безразмерная зависимость отношения диаметра полости к ее глубине d/h от временного сопротивления σв материала корпуса СЭД при σв ≤ 520 МПа выражается зависимостью (6)
при достоверности аппроксимации R2 = 0.997.Аналогичная зависимость для материалов с σв ≥ 520 МПа имеет вид (7)
при R2 = 0.957.На рис. 7 приведен график зависимости безразмерной величины σсV/Em от временного сопротивления σв материала корпуса СЭД, где σс – предел прочности на сжатие для свинца, МПа; V – объем полости в свинцовом цилиндре, м3; E – теплота взрыва ТЭНа, Дж/кг; m – масса ВВ, кг; σв – временное сопротивление материала корпуса, МПа.
Данная зависимость показывает, что c увеличением временного сопротивления материала корпуса заряда ВВ возрастает эффективность (КПД) деформации (разрушения) нагружаемого ПВ материала, которую можно выразить степенной зависимостью (8)
при R2 = 0.951.Выводы. Установлено, что при увеличении временного сопротивления материала корпуса заряда ВВ в 4 раза КПД разрушения нагружаемого образца (бризантность по свинцу) от сосредоточенного заряда возрастает в 1.5 раза, что свидетельствует о важности выбора материала корпусов для разрабатываемых зарядов (рис. 7) ПВУ различного целевого назначения.
Результаты, полученные в ходе исследований, позволяют рекомендовать использовать конструкционные материалы при проектировании корпусов зарядов с временным сопротивлением: σв < 520 МПа для изделий фугасного действия, оснащенных многоразовыми отражателями, например для ТДРД; σв > 520 МПа для изделий бризантного действия, оснащенных одноразовыми отражателями и кассетами, например для ВУ.
Список литературы
Зельдович Я.Б. К вопросу об энергетическом использовании детонационного горения // ЖТФ. 1940. Т. 10. № 17. С. 1453.
Hoffman H. Reaction-Propulsion Produced by Intermittent Detonative Combustion // German Ministry of Supply, German Research Institute for Gliding, Report ATI-52365, August 1940.
Степанов Ю.С., Соловьев В.О. Влияние основных параметров взрывореактивной установки на размеры образуемой полости в мягких горных породах // Физико-технические проблемы разработки полезных ископаемых. 1990. № 2. С. 61.
Фролов К.В., Соловьев В.О., Пацюк В.В. Об использовании взрывореактивных комплексов малого класса для разрушения горных пород и искусственных материалов // Проблемы машиностроения и надежности машин. 2001. № 5. С. 3.
Соловьев В.О., Думенко В.И. Электродетонатор и электровоспламенитель для него РФ Патент 2056034, 1992.
Bechtel R., O’Brien Ch.J. Consumable Detonation Reaction Engine and System. USA Patent 3.889.462, 1975.
Воронецкий А.В., Кутузов Б.Н., Соловьев В.О. Способ работы и устройство пульсирующего детонационного двигателя с последовательно срабатывающими кассетами. РФ Патент 2245449, 2003.
Соловьев В.О. Устройство для взрывореактивного бурения, РФ Патент 2064040, 1992.
Соловьев В.О., Кельнер М.С. Защита стальных отражателей от разрушающего воздействия продуктов детонации, использующихся в твердотопливных пульсирующих взрывных устройствах // Проблемы машиностроения и надежности машин. 2015. № 1. С. 88.
Селиванов В.В., Кобылкин И.Ф., Новиков С.А. Взрывные технологии / Под общей ред. В.В. Селиванова. М.: Изд-во МГТУ им. Н.Э. Баумана, 2008. 648 с.
Новиков С.А. Полезные взрывы. Саров: РФЯЦ-ВНИИЭФ, 2000. 293 с.
Новиков С.А., Петров В.А. Установки взрывного типа для механических испытаний материалов и конструкций: Обзор. М.: ЦНИИатоминформ, 1989.
Новиков С.А, Синицын В.А., Цой П.А. Исследование динамических диаграмм сжатия металлов при повышенных температурах // Проблемы прочности. 1980. № 11. С. 87.
Пушков В.А., Цибиков А.Н., Юрлов А.В., Окинчиц А.А., Найданова Т.Г. Результаты исследований диаграмм растяжения меди М1, алюминиевых сплавов АМГ-6 и АМц по методу составного стержня Гопкинсона с применением галтельных образцов. XI Всероссийская конференция по испытаниям и исследованиям свойств материалов “ТестМат” по тематике “Физико-механические испытания, прочность, надежность, высокотемпературные испытания” // Материалы Всероссийской конференции. Москва: ФГУП “ВИАМ”, 2019. С. 280.
Арцруни А.А., Зажилов А.А. Упрощенная методика динамических испытаний на подрыв материалов и схем защиты наземных транспортных средств. XI Всероссийская конференция по испытаниям и исследованиям свойств материалов “ТестМат” по тематике “Физико-механические испытания, прочность, надежность, высокотемпературные испытания” // Материалы Всероссийской конференции. М.: ГУП “ВИАМ”, 2019. С. 44.
Марочник сталей и сплавов / Под ред. А.С. Зубченко. 2-е изд. М.: Машиностроение, 2003. 784 с.
Физика взрыва / Под ред. Л.П. Орленко. 3-е изд. В 2 т., Т. 2. М.: Физматлит, 2004. 656 с.
Zhu J.-J., Li W.-B., Wang X.-M., Li W.-B., Zheng Y. Mid-Explosion Recovery of an Intermediate Phase of a Cylindrical Metal Shell // Combustion, Explosion, and Shock Waves. 2018. V. 54. Iss 2. P. 246.
Волков К.В., Даниленко В.В., Елин В.И. Синтез алмаза из углерода продуктов детонации // Физика горения и взрыва. 1990. Т. 26. № 3. С. 123.
Пепекин В.И., Губин С.А. Методы расчета параметров детонации взрывчатых веществ // Химическая физика. 2003. Т. 22. № 9. С. 72.
Дополнительные материалы отсутствуют.
Инструменты
Проблемы машиностроения и надежности машин